Complete Sheet Metal Installer Career Guide
Sheet metal installers are the unsung heroes behind the scenes, fabricating and installing vital metal components that ensure buildings function efficiently and safely. This hands-on career offers a direct path to a skilled trade, providing essential services for HVAC systems, roofing, and architectural elements across diverse structures. You'll solve unique structural challenges daily, contributing to the integrity and energy efficiency of commercial and residential spaces.
Key Facts & Statistics
Median Salary
$57,690 USD
(U.S. national median, May 2023 BLS data)
Range: $38k - $89k+ USD
Growth Outlook
1%
slower than average
Annual Openings
≈9
.6k openings annually
Top Industries
Typical Education
High school diploma or equivalent; most learn through apprenticeships or on-the-job training.
What is a Sheet Metal Installer?
A Sheet Metal Installer is a skilled tradesperson specializing in the fabrication, assembly, and installation of sheet metal products. These professionals primarily work with thin gauge metal sheets to create and put in place components for various systems, most commonly heating, ventilation, and air conditioning (HVAC) ductwork, but also roofing elements, gutters, downspouts, and architectural trim.
This role differs significantly from a general construction worker or a welder. While a welder focuses primarily on joining metal using heat, a sheet metal installer possesses expertise in the entire lifecycle of sheet metal components, from interpreting blueprints and precise measuring to cutting, bending, forming, and finally installing and sealing these intricate systems. They ensure that all installations meet specific building codes and performance standards, playing a critical role in a building's energy efficiency and climate control.
What does a Sheet Metal Installer do?
Key Responsibilities
- Interpret blueprints, schematics, and construction drawings to determine the layout, dimensions, and type of sheet metal required for installations.
- Measure, cut, bend, and shape sheet metal using hand tools, power tools, and specialized machinery such as brakes, shears, and rolls.
- Assemble and install HVAC ducts, exhaust systems, rain gutters, and other sheet metal components in residential, commercial, or industrial buildings.
- Fasten sheet metal parts together using various methods, including welding, soldering, riveting, bolting, and crimping, to ensure secure and airtight connections.
- Inspect completed installations for proper fit, alignment, and functionality, making adjustments or repairs as needed to meet specifications and building codes.
- Maintain a safe work environment by following all safety protocols, using personal protective equipment, and properly operating tools and equipment.
- Collaborate with other tradespeople, such as plumbers, electricians, and carpenters, to coordinate work and ensure project completion.
Work Environment
Sheet metal installers typically work on construction sites, in existing buildings undergoing renovation, or in fabrication shops. The work environment can vary significantly from day to day, ranging from indoor spaces with climate control to outdoor settings exposed to various weather conditions. The job often involves working at heights, in confined spaces, or in dusty and noisy environments.
Collaboration is constant, as installers work closely with other construction trades, project managers, and supervisors. The pace of work is often fast, driven by project deadlines. Installers usually work full-time hours, and overtime may be required to meet project schedules. The role requires physical stamina and the ability to lift heavy materials, often involving repetitive tasks and standing for long periods.
Tools & Technologies
Sheet metal installers utilize a wide array of tools and equipment to perform their duties effectively. Hand tools include tin snips, hammers, punches, and measuring tapes. Power tools frequently used are drills, grinders, saws, and portable shears. Specialized machinery on job sites or in fabrication shops includes press brakes for bending, squaring shears for cutting, and roll-forming machines for shaping.
Installers also work with various fastening equipment such as welding machines (TIG, MIG, stick), soldering irons, rivet guns, and specialized crimping tools. Personal protective equipment (PPE) like safety glasses, gloves, hard hats, and respirators are essential for safety. They also use scaffolding, lifts, and ladders to access elevated work areas.
Sheet Metal Installer Skills & Qualifications
A Sheet Metal Installer's qualifications are primarily built on practical experience and certifications, with formal education playing a supporting role. Entry-level positions often require a high school diploma and a strong aptitude for hands-on work, leading into apprenticeships. Senior installers demonstrate extensive on-the-job experience and advanced certifications.
Requirements for Sheet Metal Installers vary significantly by industry sector. Commercial construction demands proficiency with larger ductwork and structural components, while residential work focuses on HVAC systems and smaller gauge materials. Industrial settings, such as manufacturing plants or shipyards, require specialized knowledge of heavy-gauge metals, welding techniques, and often specific safety protocols.
The skill landscape for Sheet Metal Installers is evolving with the increased adoption of digital fabrication and advanced machinery. Installers now benefit from understanding CAD/CAM software for precise cutting and bending. While traditional craftsmanship remains vital, a willingness to adapt to new technologies like laser cutters and automated bending machines adds significant value. Certifications in welding, safety, and specific equipment operation are often more critical than a traditional degree, demonstrating immediate competency and adherence to industry standards.
Education Requirements
Technical Skills
- Blueprint Reading and Interpretation (architectural, mechanical, shop drawings)
- Sheet Metal Fabrication (cutting, bending, forming, seaming)
- HVAC Ductwork Installation (rigid, flexible, spiral ducts, fittings)
- Soldering and Brazing Techniques (copper, aluminum)
- Welding (MIG, TIG, Stick for various metals like steel, stainless steel, aluminum)
- Fastening Techniques (riveting, screwing, bolting, sealant application)
- Measuring Tools Proficiency (tape measures, calipers, squares, levels)
- Power Tool Operation (shears, brakes, grinders, drills, saws)
- Safety Equipment Usage (fall protection, respirators, lockout/tagout)
- Troubleshooting and Repair of Sheet Metal Systems
- Material Handling and Rigging (hoists, lifts, scaffolding)
- Basic Electrical Knowledge (for HVAC control wiring)
Soft Skills
- Attention to Detail: Installers must ensure precise measurements and accurate cuts to prevent rework and ensure system efficiency.
- Problem-Solving: Identifying and resolving issues on-site, such as unexpected structural obstacles or material discrepancies, is crucial.
- Physical Stamina and Dexterity: The role demands prolonged standing, bending, lifting heavy materials, and working in confined spaces.
- Team Collaboration: Installers often work as part of a crew, requiring effective communication and coordination to complete projects safely and efficiently.
- Adherence to Safety Protocols: Strictly following safety guidelines and using personal protective equipment protects oneself and the team from hazards.
- Adaptability: Adjusting to changing blueprints, site conditions, or project timelines is common in construction environments.
- Time Management: Efficiently completing tasks within project deadlines and managing material flow on the job site is essential.
- Work Ethic and Reliability: Consistently showing up on time, being prepared, and maintaining a strong work ethic are fundamental for project success and team trust.
How to Become a Sheet Metal Installer
Entering the sheet metal installer field typically involves a blend of hands-on training and formal education. While some individuals find entry-level positions directly with contractors, the most robust and respected pathway is often through an apprenticeship. Apprenticeships offer structured learning, paid on-the-job experience, and lead to journeyman status, which is highly valued across the industry.
Timeline expectations vary; a direct entry helper position might take a few weeks to secure, but an apprenticeship can span 3-5 years. Geographic location significantly impacts opportunities; major construction hubs or areas with strong manufacturing sectors will have more openings than rural regions. Company size also matters, with larger firms or union shops more likely to offer apprenticeships, while smaller contractors might prefer hiring experienced installers or offer less structured on-the-job training.
A common misconception is that this field only requires brute strength; in reality, it demands precision, problem-solving, and a strong understanding of blueprints and safety protocols. Building a foundation in basic math, blueprint reading, and safety is crucial, regardless of your chosen entry route. Networking with local contractors and union representatives can open doors and provide insights into specific local requirements and hiring practices.
Step 1
Step 2
Step 3
Step 4
Step 5
Step 6
Step 7
Education & Training Needed to Become a Sheet Metal Installer
Becoming a Sheet Metal Installer primarily involves hands-on training and vocational education, rather than traditional four-year degrees. Formal degree programs are generally not required or even available for this specialized trade. Instead, aspiring installers often pursue apprenticeships, vocational school programs, or certifications from industry associations.
Apprenticeships are the most common and highly regarded pathway, typically lasting 4-5 years. They combine paid on-the-job training with classroom instruction, leading to a journey-level certification. These programs usually cost minimal tuition, often covered by sponsoring unions or contractors, while apprentices earn an increasing wage. Vocational schools and community colleges offer shorter, more focused programs, usually 6-18 months, costing $5,000-$20,000. These provide foundational skills, making graduates more competitive for entry-level positions or apprenticeships. Self-study is less common for this hands-on role, but online courses can supplement knowledge.
Employers highly value practical experience and certifications from recognized bodies like the National Center for Construction Education and Research (NCCER) or local union training centers. Continuous learning is essential, focusing on new materials, techniques, and safety standards. Specialized skills in areas like HVAC ductwork, architectural sheet metal, or custom fabrication can significantly enhance career prospects and earnings. The educational needs vary by the complexity of projects and the specific industry sector. Practical experience remains paramount for career advancement, often outweighing theoretical knowledge alone.
Sheet Metal Installer Salary & Outlook
Compensation for a Sheet Metal Installer varies significantly based on several key factors. Geographic location plays a crucial role, with higher wages typically found in metropolitan areas and regions with strong construction or manufacturing sectors due to increased demand and higher cost of living. Conversely, rural areas may offer lower salaries.
Years of experience and specialized skills also dramatically impact earning potential. Entry-level installers earn less, while those with extensive experience, certifications in specialized welding or HVAC systems, and a proven track record of complex installations command premium compensation. Union membership often leads to higher wages and comprehensive benefits packages compared to non-union roles.
Total compensation extends beyond base salary to include overtime pay, which is common in project-based work, and sometimes project completion bonuses. Benefits packages frequently cover health insurance, retirement plans like 401(k)s, and paid time off. Some companies also offer allowances for tools or professional development to maintain certifications.
Industry-specific trends, such as the demand in commercial construction versus residential, influence salary growth. Economic conditions and the volume of new construction projects directly affect the availability of work and negotiation leverage for installers. While salary figures are typically quoted in USD, international markets present their own distinct pay scales, influenced by local labor laws, economic stability, and construction activity.
Salary by Experience Level
Level | US Median | US Average |
---|---|---|
Apprentice Sheet Metal Installer | $42k USD | $45k USD |
Sheet Metal Installer | $62k USD | $65k USD |
Senior Sheet Metal Installer | $77k USD | $80k USD |
Lead Sheet Metal Installer | $92k USD | $95k USD |
Sheet Metal Foreman | $105k USD | $110k USD |
Market Commentary
The job market for Sheet Metal Installers shows a stable outlook, driven primarily by ongoing demand in the construction and manufacturing sectors. The U.S. Bureau of Labor Statistics projects about a 4% growth for sheet metal workers between 2022 and 2032, which is about as fast as the average for all occupations. This translates to roughly 3,900 new job openings each year, arising from both growth and the need to replace workers who exit the labor force.
Demand is particularly strong in commercial and industrial construction, including the installation of HVAC systems, roofing, and architectural sheet metal. The push for energy efficiency in buildings also creates opportunities for installers skilled in fabricating and installing more advanced, sealed ductwork and ventilation systems. Emerging opportunities include specialized work in cleanroom construction for industries like semiconductors and pharmaceuticals, requiring precise installation techniques.
The supply of skilled Sheet Metal Installers often struggles to keep pace with demand, especially for those with specialized welding or blueprint reading capabilities. This imbalance can lead to competitive wages and better job security for qualified individuals. Automation and AI have a limited direct impact on the hands-on installation aspect of the role, though prefabrication using automated machinery may streamline some workshop processes, shifting some tasks from on-site to off-site fabrication.
This profession is somewhat cyclical, tied to the overall health of the construction industry, but essential maintenance and renovation work provide a baseline level of stability. Geographic hotspots for employment include major urban centers and areas experiencing significant infrastructure development. Continuous training in new materials, safety protocols, and advanced installation techniques is crucial for long-term career viability.
Sheet Metal Installer Career Path
Career progression for a Sheet Metal Installer typically involves a hands-on journey from foundational learning to supervisory roles. This path emphasizes the continuous acquisition of specialized skills, adherence to safety protocols, and the development of leadership capabilities. Advancement often hinges on demonstrated proficiency, reliability, and a commitment to quality craftsmanship.
Individual contributor (IC) tracks focus on mastering installation techniques and becoming highly efficient and accurate. Management/leadership tracks involve overseeing projects, managing teams, and ensuring project completion on time and within budget. Factors influencing advancement speed include consistent high performance, the willingness to specialize in complex systems like HVAC or architectural sheet metal, and participation in ongoing training. Company size and industry also play a role; larger construction firms or specialized fabrication shops might offer more structured advancement paths than smaller, general contractors.
Lateral movement opportunities exist into related trades like welding, HVAC service, or even project coordination. Networking within the construction industry, seeking mentorship from experienced installers, and maintaining a strong reputation for precision and problem-solving significantly aid career growth. Key milestones include obtaining journeyman certification, mastering complex blueprints, and successfully leading installation crews. Professionals might also transition into roles like estimating, quality control, or safety management, leveraging their practical experience.
Apprentice Sheet Metal Installer
1-3 yearsKey Focus Areas
Sheet Metal Installer
3-5 years total experienceKey Focus Areas
Senior Sheet Metal Installer
5-8 years total experienceKey Focus Areas
Lead Sheet Metal Installer
8-12 years total experienceKey Focus Areas
Sheet Metal Foreman
12+ years total experienceKey Focus Areas
Apprentice Sheet Metal Installer
1-3 yearsWorks under direct supervision, assisting experienced installers with basic tasks. Carries materials, prepares work areas, and performs simple measurements and cuts. Focuses on learning fundamental installation methods and site safety. Has minimal decision-making authority.
Key Focus Areas
Mastering tool identification and safe handling. Learning basic sheet metal fabrication techniques, including cutting, bending, and forming. Understanding and following safety regulations and procedures. Developing strong communication skills for working with experienced installers.
Sheet Metal Installer
3-5 years total experiencePerforms independent installation tasks under general supervision. Responsible for accurate measurements, precise cuts, and secure installations. Participates in project planning and contributes to problem-solving. Works with other trades and adheres to project timelines.
Key Focus Areas
Developing proficiency in various installation techniques, including ductwork, roofing, and architectural elements. Interpreting complex blueprints and schematics accurately. Improving problem-solving skills for on-site challenges. Beginning to mentor new apprentices and share knowledge.
Senior Sheet Metal Installer
5-8 years total experienceHandles complex and critical installation projects with minimal supervision. Acts as a subject matter expert, troubleshooting difficult issues and ensuring work meets high standards. Collaborates with project managers and other trades to ensure seamless integration. Mentors and guides less experienced team members.
Key Focus Areas
Refining expertise in complex installations and specialized sheet metal systems. Taking initiative in identifying and resolving installation challenges. Providing technical guidance to junior installers. Understanding project specifications and quality control standards.
Lead Sheet Metal Installer
8-12 years total experienceDirects the daily activities of a small crew of installers on specific project segments. Assigns tasks, monitors progress, and ensures work quality and safety compliance. Acts as the primary point of contact for project managers regarding crew progress and issues. Makes on-site decisions to maintain project flow.
Key Focus Areas
Developing strong leadership and team coordination skills. Improving project management capabilities, including scheduling and resource allocation. Enhancing communication and conflict resolution skills. Taking ownership of project segments and ensuring team productivity.
Sheet Metal Foreman
12+ years total experienceManages multiple sheet metal installation projects or large, complex phases of a single project. Oversees multiple crews, ensuring adherence to blueprints, schedules, and budget. Responsible for quality control, safety enforcement, and team performance. Liaises with clients, general contractors, and suppliers.
Key Focus Areas
Mastering comprehensive project planning, budgeting, and resource management. Developing advanced leadership, delegation, and motivational skills. Understanding contractual obligations and client relations. Focusing on overall project profitability and safety culture.
Job Application Toolkit
Ace your application with our purpose-built resources:
Sheet Metal Installer Resume Examples
Proven layouts and keywords hiring managers scan for.
View examplesSheet Metal Installer Cover Letter Examples
Personalizable templates that showcase your impact.
View examplesTop Sheet Metal Installer Interview Questions
Practice with the questions asked most often.
View examplesSheet Metal Installer Job Description Template
Ready-to-use JD for recruiters and hiring teams.
View examplesGlobal Sheet Metal Installer Opportunities
The Sheet Metal Installer role is globally consistent, involving the fabrication, assembly, and installation of sheet metal products. Demand remains stable across industrial, commercial, and residential construction sectors worldwide. Regulatory differences impact material specifications and safety standards, but core skills are universally transferable. Professionals often seek international opportunities for higher wages or specialized projects, with some countries recognizing vocational training for mobility.
Global Salaries
Sheet Metal Installer salaries vary significantly by region and cost of living. In North America, a skilled installer in the United States earns between $45,000 and $70,000 USD annually, while in Canada, salaries range from $50,000 to $75,000 CAD (approximately $37,000-$55,000 USD). These figures often include benefits like health insurance and retirement plans, which are common in these markets.
European salaries show considerable diversity. In Germany, installers typically earn €35,000 to €55,000 (around $38,000-$60,000 USD), often with strong social security benefits. The UK sees ranges of £30,000 to £45,000 (about $38,000-$57,000 USD). Scandinavian countries, like Norway, offer higher wages, often exceeding $65,000 USD, but with a much higher cost of living. Taxes and social contributions significantly impact take-home pay across Europe.
Asia-Pacific markets offer lower nominal wages but good purchasing power. Australia provides salaries from $60,000 to $85,000 AUD (roughly $40,000-$57,000 USD), with a high cost of living. In some Middle Eastern countries, like UAE, salaries can be $30,000 to $50,000 USD, often tax-free, but with fewer long-term residency benefits. Experience and specialized certifications, such as welding or HVAC system knowledge, can command higher compensation globally.
Remote Work
International remote work for a Sheet Metal Installer is generally not feasible due to the hands-on nature of the job. The role requires physical presence on construction sites, in workshops, or manufacturing facilities to perform tasks like cutting, bending, assembling, and installing metal components. This essential on-site requirement limits true remote opportunities.
However, some related functions, such as project management, CAD design for sheet metal, or estimation, can be performed remotely. These roles, while adjacent, are distinct from the direct installation work. Digital nomad visas or remote work policies do not typically apply to this trade. Employers hiring internationally for this role expect physical relocation. Salary expectations remain tied to the geographic location of the physical work, with no geographic arbitrage for the installation aspect.
Visa & Immigration
Sheet Metal Installers seeking international work often pursue skilled worker visas. Countries like Canada, Australia, and Germany have specific pathways for tradespeople. For example, Canada's Express Entry system or Provincial Nominee Programs target skilled trades, requiring a valid job offer, language proficiency, and credential assessment. Australia's skilled migration visas also list this occupation, often requiring a skills assessment by a relevant authority.
In 2025, typical requirements include relevant vocational training, several years of documented experience, and English or the local language proficiency (e.g., German for Germany). Visa processing times vary from a few months to over a year. Some countries, particularly those with labor shortages in construction, may offer faster processing. Intra-company transfers are rare for this role unless part of a larger, specialized project team. Pathways to permanent residency usually involve maintaining employment and meeting specific residency duration requirements. Family visas allow dependents to accompany the primary applicant, subject to financial and health checks. Understanding country-specific licensing or certification needs is crucial before applying.
2025 Market Reality for Sheet Metal Installers
Understanding current market conditions is critical for sheet metal installers to navigate career paths effectively. The industry has seen shifts post-pandemic, with supply chain issues and fluctuating material costs impacting project timelines.
Broader economic factors, like interest rates and inflation, directly influence construction spending, affecting job availability. Market realities vary significantly by experience level, geographic region, and the size of contracting companies, influencing job security and earning potential. This analysis provides an honest assessment of current hiring realities.
Current Challenges
Sheet metal installers face increased competition for stable, full-time roles, especially in regions with slower construction growth. Economic uncertainty can delay large commercial projects, directly impacting job availability.
Skill gaps persist in advanced fabrication or specialized welding, making it harder for some to secure higher-paying jobs. The physical demands and safety risks of the role also present ongoing challenges.
Growth Opportunities
Opportunities for sheet metal installers are strong in specialized areas like custom fabrication for architectural projects and advanced HVAC system installation. Demand for installers with certifications in specific welding techniques or CAD software proficiency is growing.
Underserved markets exist in regions undergoing significant industrial expansion or infrastructure upgrades. Installers who cross-train in related trades, such as pipefitting or electrical work, gain a competitive edge. The increasing focus on energy efficiency in buildings also creates niches for installers familiar with airtight ductwork and sustainable material installation.
Market corrections can open opportunities for installers willing to relocate to high-growth areas. Investing in continuous training, especially in new materials and installation technologies, positions professionals for better roles. Sectors like data centers, healthcare facilities, and renewable energy plants consistently require skilled sheet metal work.
Current Market Trends
Demand for skilled sheet metal installers remains steady in 2025, driven by ongoing infrastructure projects and commercial construction. However, residential demand fluctuates with interest rates and housing starts. The industry sees a consistent need for new construction and renovation work.
Automation in fabrication shops affects some aspects of the trade, but on-site installation still requires manual expertise. Employers increasingly seek installers with diverse skills, including HVAC system integration and precision measurement. Salary trends show moderate growth, particularly for those with certifications in specialized areas like welding or blueprint reading.
Geographically, strong markets include urban centers with active commercial development and regions investing heavily in renewable energy infrastructure. Remote work is not applicable here, making local market conditions paramount. Seasonal hiring patterns are typical, with increased activity during warmer months for outdoor projects.
Emerging Specializations
The sheet metal installation trade is experiencing a significant transformation, driven by advancements in fabrication technologies, material science, and building energy efficiency standards. These shifts are creating entirely new specialization opportunities that professionals can pursue to enhance their careers.
Early positioning in these emerging areas is crucial for professionals aiming for career advancement and premium compensation in 2025 and beyond. Specializing in next-generation techniques and materials allows installers to command higher rates and secure roles on cutting-edge projects.
While established specializations remain vital, focusing on emerging areas offers a strategic advantage. These new niches often transition from niche to mainstream within five to ten years, creating a substantial increase in job opportunities. Understanding this timeline helps professionals assess the risk and reward of investing in new skill sets.
Embracing these cutting-edge specializations involves a commitment to continuous learning, but it also offers significant potential for career growth and stability in a rapidly evolving industry.
BIM-Integrated Sheet Metal Installation
Building Information Modeling (BIM) integration is becoming critical for sheet metal installers. This involves working with digital 3D models to precisely plan, coordinate, and execute installations, minimizing errors and material waste. Installers need to understand how to interpret and contribute to BIM workflows, ensuring seamless integration of sheet metal components within larger building systems. This specialization bridges the gap between digital design and physical construction.
High-Performance HVAC & Envelope Installation
The growing emphasis on sustainable building practices and energy efficiency is creating demand for installers specializing in advanced HVAC ductwork and envelope systems. This includes working with high-performance insulation, air-sealing techniques, and specialized duct materials designed to reduce energy consumption. Installers in this area ensure that sheet metal components contribute optimally to a building's thermal performance and indoor air quality.
Modular & Prefabricated Sheet Metal Assembly
Modular and prefabricated construction methods are gaining traction, requiring sheet metal installers to adapt to off-site assembly and on-site integration of large pre-fabricated modules. This specialization involves understanding standardized component assembly, precise alignment techniques for modular units, and working efficiently within a controlled factory environment before transportation and final installation. The focus shifts from piece-by-piece assembly to integrating larger, pre-built sections.
Robotic & Automated Installation Support
Advanced robotic and automated tools are increasingly being used in both fabrication and on-site installation of sheet metal. Installers specializing in this area learn to operate and maintain robotic cutting, bending, and even some assembly equipment. They also troubleshoot automated systems, ensuring efficient and precise production and installation. This role combines traditional craftsmanship with technological oversight.
Smart Building Systems Integration (Sheet Metal)
The increasing complexity of building systems requires specialized installers who can integrate sheet metal components with smart building technologies. This includes installing ductwork with embedded sensors for air quality monitoring, ventilation systems connected to building management systems (BMS), and sheet metal enclosures for smart infrastructure. Installers in this area need a foundational understanding of how these systems communicate and interact.
Pros & Cons of Being a Sheet Metal Installer
Making informed career choices requires a thorough understanding of both the potential benefits and the inherent challenges of a profession. The experience within any career field, including that of a Sheet Metal Installer, can vary significantly based on factors such as the specific company, the industry sector (e.g., HVAC, construction, manufacturing), the type of projects undertaken, and individual personality or preferences. For example, what one person considers a challenging physical aspect, another might view as an engaging, active workday. Furthermore, the pros and cons can evolve at different stages of a career, from an apprentice learning the ropes to a seasoned journeyman. This assessment aims to provide a realistic and balanced perspective to help individuals set appropriate expectations for a career as a Sheet Metal Installer.
Pros
- There is consistent demand for skilled sheet metal installers across various industries, including construction, HVAC, and manufacturing, providing good job security and diverse employment opportunities.
- Many entry-level positions offer apprenticeships or on-the-job training, allowing individuals to earn a wage while acquiring valuable skills without requiring a four-year college degree.
- The work is often hands-on and involves tangible results, providing a sense of accomplishment and satisfaction from seeing a project completed from raw materials to a finished installation.
- Skilled sheet metal installers typically command competitive hourly wages, and with experience and specialized certifications, earning potential can increase significantly.
- The job often involves working in different locations and on various projects, which provides variety and prevents the monotony of a typical office job.
- Developing expertise in sheet metal installation creates a foundation for specialization in areas such as welding, fabrication, or CAD design, offering multiple avenues for career growth and skill diversification.
- Working as part of a team on construction sites or in fabrication shops fosters strong camaraderie and a supportive work environment among colleagues.
Cons
- The work involves physically demanding tasks, including lifting heavy sheets of metal, working in awkward positions, and repetitive motions, which can lead to musculoskeletal injuries over time.
- Sheet metal installers often work in environments with loud noise, dust, fumes, and extreme temperatures, requiring strict adherence to safety protocols and the use of personal protective equipment.
- Many projects operate on tight deadlines, especially in construction, which can lead to periods of long hours, early starts, or weekend work to ensure timely completion.
- The job requires precision and attention to detail; even minor errors in measurement or installation can lead to significant re-work, material waste, and project delays.
- Employment can be sensitive to economic downturns or seasonal changes in the construction industry, potentially leading to periods of reduced work or layoffs if new projects are scarce.
- Career advancement into supervisory or project management roles may require additional training, certifications, or a significant amount of on-the-job experience, making progression slower for some.
- Working at heights is a common requirement, especially in commercial or industrial installations, which can be a significant challenge for individuals with a fear of heights or balance issues, despite safety measures being in place by companies and organizations to prevent injuries, falls, and fatalities.
Frequently Asked Questions
Becoming a Sheet Metal Installer involves hands-on skill and precision, but many prospective professionals wonder about the physical demands, necessary training, and career progression. This section addresses the most common questions about entering this trade, from apprenticeship pathways to job stability and salary expectations.
What is the typical path to becoming a Sheet Metal Installer, and do I need a specific degree?
Most Sheet Metal Installers learn through a formal apprenticeship, which typically lasts 3-5 years. These programs combine paid on-the-job training with classroom instruction, covering blueprint reading, safety, welding, and specific sheet metal fabrication techniques. While not strictly required, some vocational high school programs or pre-apprenticeship courses can provide a valuable head start and foundational knowledge.
How long does it realistically take to become a skilled Sheet Metal Installer?
The time to become job-ready depends on your chosen training path. A full apprenticeship can take 3-5 years to complete, after which you qualify as a journeyman. You will earn wages throughout the apprenticeship, increasing as you gain more experience. Entry-level helper positions might be available with minimal training, but these roles serve as stepping stones to a formal apprenticeship for long-term career growth.
What are the salary expectations for a Sheet Metal Installer, and do benefits typically come with the job?
Sheet Metal Installers can earn a competitive wage, especially after completing an apprenticeship. Starting salaries for apprentices are lower but increase significantly each year. Journeyman installers can expect to earn a good living, with potential for higher pay based on experience, specialization (e.g., HVAC, architectural), and location. Union membership often includes comprehensive benefits packages, which adds to overall compensation.
What is the typical work-life balance like, considering the physical demands and project deadlines?
The work-life balance for Sheet Metal Installers can vary. Projects often have deadlines, which may lead to longer hours, including evenings or weekends, especially during peak construction seasons. However, regular overtime is typically compensated. The work is physically demanding, requiring strength and stamina, but also offers the satisfaction of seeing tangible results from your efforts. Many find the variety of projects and the hands-on nature of the work appealing.
Is the job market for Sheet Metal Installers stable, or is it prone to fluctuations?
Job security for Sheet Metal Installers is generally strong, driven by consistent demand in construction, manufacturing, and HVAC industries. As buildings are constructed, renovated, and maintained, skilled installers remain essential. While economic downturns can affect construction, the need for maintenance and specialized fabrication often provides stability. Specializing in areas like HVAC or custom fabrication can further enhance long-term job prospects.
What are the potential career advancement opportunities for a Sheet Metal Installer?
Career growth opportunities for Sheet Metal Installers are robust. After becoming a journeyman, you can advance to foreman or supervisor roles, managing teams and projects. Specialization in specific areas like welding, CAD design for fabrication, or advanced HVAC systems can open up new opportunities. Some experienced installers transition into estimating, project management, or even start their own contracting businesses.
What are the biggest challenges and safety concerns specific to working as a Sheet Metal Installer?
The primary challenges include the physical demands of the job, working in various weather conditions, and adhering to strict safety protocols. Installers often work at heights, in confined spaces, or with heavy machinery. Maintaining a high level of precision while working quickly is also crucial. However, comprehensive safety training and proper equipment are standard, and continuous learning helps address evolving techniques and materials.
Can Sheet Metal Installers work remotely, or is it primarily an on-site role?
Sheet Metal Installers primarily work on-site at construction projects, manufacturing facilities, or client locations. This means remote work is generally not an option for the installation aspect of the job. However, some roles in design, estimating, or project management within the sheet metal industry might offer more flexibility. The nature of the work requires physical presence to fabricate, transport, and install materials.
Related Careers
Explore similar roles that might align with your interests and skills:
Sheet Metal Mechanic
A growing field with similar skill requirements and career progression opportunities.
Explore career guideSheet Metal Worker
A growing field with similar skill requirements and career progression opportunities.
Explore career guideAir Conditioning Sheet Metal Installer
A growing field with similar skill requirements and career progression opportunities.
Explore career guideHeating, Ventilation, and Air Conditioning (HVAC) Sheet Metal Installer
A growing field with similar skill requirements and career progression opportunities.
Explore career guideSheet Metal Duct Installer
A growing field with similar skill requirements and career progression opportunities.
Explore career guideAssess your Sheet Metal Installer readiness
Understanding where you stand today is the first step toward your career goals. Our Career Coach helps identify skill gaps and create personalized plans.
Skills Gap Analysis
Get a detailed assessment of your current skills versus Sheet Metal Installer requirements. Our AI Career Coach identifies specific areas for improvement with personalized recommendations.
See your skills gapCareer Readiness Assessment
Evaluate your overall readiness for Sheet Metal Installer roles with our AI Career Coach. Receive personalized recommendations for education, projects, and experience to boost your competitiveness.
Assess your readinessSimple pricing, powerful features
Upgrade to Himalayas Plus and turbocharge your job search.
Himalayas
Himalayas Plus
Himalayas Max
Find your dream job
Sign up now and join over 100,000 remote workers who receive personalized job alerts, curated job matches, and more for free!
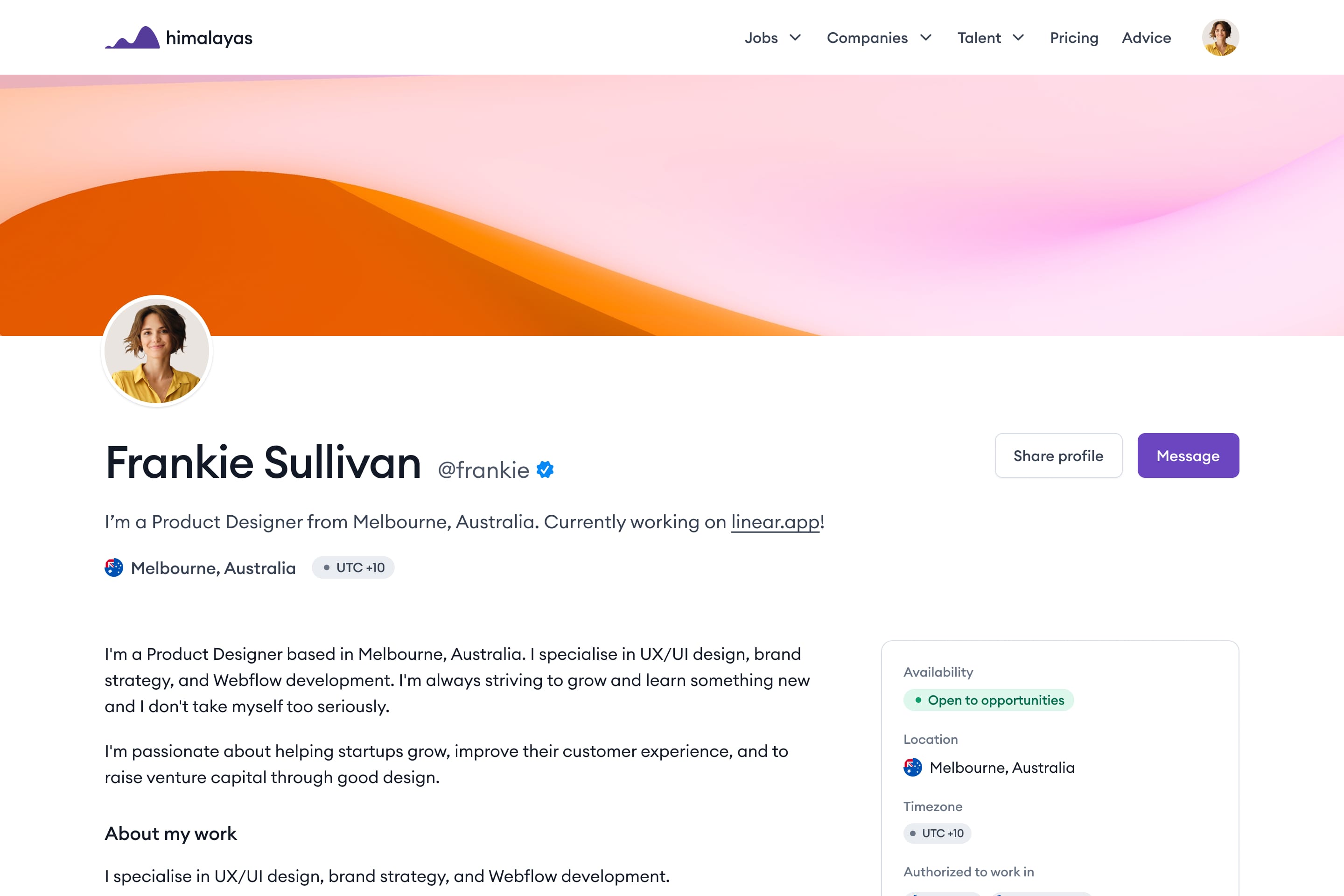