Complete Sheet Metal Mechanic Career Guide
Sheet metal mechanics are the skilled artisans who transform raw metal into precision products, fabricating and installing components critical for everything from HVAC systems to aircraft. This hands-on career offers a tangible impact, combining technical expertise with problem-solving to build essential infrastructure. It is a vital trade, requiring meticulous attention to detail and offering steady demand across diverse sectors.
Key Facts & Statistics
Median Salary
$57,210 USD
Range: $35k - $90k+ USD
Growth Outlook
1%
as fast as average (2022-2032)
Annual Openings
≈17,400
openings annually
Top Industries
Typical Education
High school diploma or equivalent, often followed by an apprenticeship or vocational training
What is a Sheet Metal Mechanic?
A Sheet Metal Mechanic is a skilled tradesperson who fabricates, assembles, installs, and repairs products made from thin sheets of metal, such as stainless steel, galvanized iron, or aluminum. They transform raw sheets into precise components for a wide range of applications, including HVAC ducts, aircraft parts, roofing, industrial machinery, and architectural elements.
This role differs significantly from a general welder or fabricator. While a welder focuses primarily on joining metal pieces, and a general fabricator might work with thicker materials or various processes, a Sheet Metal Mechanic specializes in the intricate shaping, bending, and joining of thinner gauge metals to create specific forms and systems. Their expertise lies in understanding metal properties and precision forming techniques rather than just the joining process.
What does a Sheet Metal Mechanic do?
Key Responsibilities
- Interpret blueprints, schematics, and engineering drawings to determine layout and sequence of operations for sheet metal fabrication.
- Measure, cut, bend, and form sheet metal components using hand tools, power tools, and specialized machinery like press brakes and shears.
- Assemble and install sheet metal parts and structures, often involving welding, riveting, bolting, or soldering techniques.
- Inspect finished products for quality assurance, ensuring they meet specifications, tolerances, and industry standards.
- Perform routine maintenance and calibration on fabrication equipment to ensure optimal performance and safety.
- Troubleshoot and repair existing sheet metal installations, identifying defects and implementing corrective actions.
- Collaborate with engineers, welders, and other tradespeople to ensure seamless integration of sheet metal components into larger projects.
Work Environment
Sheet metal mechanics typically work in fabrication shops, industrial settings, construction sites, or manufacturing plants. The environment can be noisy due due to machinery and often requires wearing personal protective equipment (PPE) like safety glasses, gloves, and hearing protection. Work often involves standing for long periods, bending, lifting, and working in confined spaces or at heights.
Collaboration with other trades, such as welders, plumbers, and electricians, is common on larger projects. While some work is indoors, outdoor work is frequent on construction sites. The pace can be fast, especially when meeting project deadlines. While traditional roles are on-site, some specialized design or planning roles might incorporate remote work for blueprint review, but the hands-on nature of the job requires physical presence.
Tools & Technologies
Sheet metal mechanics rely on a diverse set of tools and technologies. Hand tools include tin snips, punches, hammers, and measuring devices like calipers and micrometers. Power tools commonly used are grinders, drills, and specialized cutting tools.
Key machinery involves press brakes for bending, shears for cutting, and roll-forming machines. Welding equipment, such as TIG and MIG welders, is essential for joining metal pieces. They also use various soldering and riveting tools. Knowledge of CAD/CAM software for interpreting designs and sometimes for operating CNC machinery becomes increasingly important in modern fabrication shops.
Sheet Metal Mechanic Skills & Qualifications
A Sheet Metal Mechanic fabricates, assembles, installs, and repairs sheet metal products and equipment, primarily in construction, manufacturing, or aerospace. Qualifications for this role emphasize practical experience and specific certifications over extensive formal education. The field highly values demonstrable hands-on skill and adherence to safety and quality standards.
Requirements for a Sheet Metal Mechanic vary significantly by industry and seniority. Entry-level positions often require a high school diploma and completion of an apprenticeship or vocational program. Senior roles, particularly in aerospace or precision manufacturing, demand advanced certifications, extensive experience with complex blueprints, and expertise in specialized welding or fabrication techniques. Company size also plays a role; larger companies might seek more specialized skills, while smaller shops value versatility across different tasks.
Formal apprenticeships are the most common and respected pathway into this trade, providing structured on-the-job training combined with classroom instruction. While a college degree is not typically required, vocational school programs or community college courses in sheet metal fabrication or welding can provide a strong foundation. Certifications in specific welding processes, safety protocols, or equipment operation significantly enhance employability and earning potential. The skill landscape evolves with new materials and automated machinery, requiring continuous learning in areas like CAD/CAM and robotic welding systems.
Education Requirements
Technical Skills
- Blueprint Reading and Interpretation (including orthographic and isometric projections)
- Precision Measuring Tools (calipers, micrometers, protractors, squares)
- Sheet Metal Fabrication Techniques (shearing, bending, rolling, forming, flanging)
- Welding Processes (TIG, MIG, Stick welding for various metals like aluminum, stainless steel, mild steel)
- Fastening Methods (riveting, bolting, soldering, brazing, adhesive bonding)
- Use of Hand and Power Tools (snips, hammers, drills, grinders, nibblers, brakes, shears)
- HVAC Ductwork Installation and Repair (for Mechanics specializing in HVAC systems)
- Layout and Pattern Development (flat pattern layout from 3D designs)
- Material Science Knowledge (understanding properties of various metals and alloys)
- Shop Math and Geometry (calculations for angles, radii, and material allowances)
- Quality Control and Inspection Procedures
- Basic CAD/CAM Software Operation (for interpreting designs or operating CNC machinery)
Soft Skills
- Attention to Detail: Critical for precise measurements, accurate cuts, and ensuring components fit correctly to meet strict specifications.
- Problem-Solving: Essential for identifying issues with blueprints, material properties, or installation challenges and devising effective solutions.
- Spatial Reasoning: Necessary to visualize how flat patterns will form three-dimensional objects and how components will integrate into larger structures.
- Safety Consciousness: Paramount for working with heavy machinery, sharp materials, and hazardous processes; strict adherence to safety protocols is non-negotiable.
- Team Collaboration: Often works as part of a team on larger projects, requiring effective communication and coordination with other tradespeople.
- Adaptability: Required to work with various materials, tools, and project requirements, often shifting tasks or adjusting methods based on site conditions or client needs.
- Work Ethic: The role often involves physically demanding tasks, requiring stamina, reliability, and a commitment to completing tasks efficiently and to high standards.
How to Become a Sheet Metal Mechanic
Becoming a Sheet Metal Mechanic involves several pathways, primarily through apprenticeships, vocational training programs, or direct entry with relevant experience. Apprenticeships offer a structured learning environment, combining on-the-job training with classroom instruction, typically lasting 3-5 years. Vocational programs provide foundational skills and certifications in a shorter timeframe, usually 6-18 months, which can then lead to entry-level positions or further apprenticeships.
The timeline for entry varies significantly: a complete beginner pursuing an apprenticeship might take 3-5 years to become fully qualified, while someone with prior mechanical aptitude or related construction experience could transition into an entry-level role within 6-12 months after targeted training. Geographic location plays a role, with more opportunities in areas with strong manufacturing, construction, or HVAC industries. Larger corporations and union shops often prefer formal apprenticeships, while smaller businesses might hire based on demonstrated practical skills and a willingness to learn.
A common misconception is that this field only involves heavy, dirty work; in reality, it requires precision, mathematical skills, and the ability to interpret complex blueprints. Overcoming entry barriers often means proving mechanical aptitude and a strong work ethic, even without formal qualifications initially. Networking with local contractors, union representatives, and vocational school instructors can open doors to opportunities not widely advertised, helping candidates understand specific hiring needs and secure mentorship.
Step 1
Step 2
Step 3
Step 4
Step 5
Step 6
Education & Training Needed to Become a Sheet Metal Mechanic
Becoming a Sheet Metal Mechanic primarily involves hands-on training and vocational education, rather than traditional four-year degrees. Formal degree programs are rare; instead, individuals typically pursue apprenticeships, vocational school certificates, or specialized associate's degrees. Apprenticeships often last 3-5 years, providing extensive on-the-job training combined with classroom instruction. These programs can be highly cost-effective, with apprentices often earning wages while learning, and may cost $1,000-$5,000 in fees and tools over the entire duration. Vocational certificates and associate's degrees usually take 6 months to 2 years, costing between $5,000 and $25,000, depending on the institution and program length. These programs offer foundational knowledge in blueprint reading, fabrication, and safety.
Employers highly value practical experience and certifications from recognized trade organizations or vocational schools. While self-study can supplement learning, it rarely replaces structured training for this hands-on role. The market perception favors candidates with completed apprenticeships or strong vocational backgrounds, as these paths demonstrate direct applicability of skills. Continuous learning in areas like new materials, advanced welding techniques, and specialized software (e.g., CAD/CAM) is crucial for career advancement, especially for those moving into supervisory or design roles. Educational needs vary; entry-level positions prioritize core fabrication and safety, while advanced roles might require certifications in specific welding types or advanced manufacturing processes.
The cost-benefit analysis for a Sheet Metal Mechanic strongly favors vocational training and apprenticeships due to their direct career applicability and lower financial burden compared to academic degrees. These pathways typically lead to faster entry into the workforce and immediate skill utilization. Quality standards for programs often involve accreditation by organizations like the National Center for Construction Education and Research (NCCER) or specific union affiliations. These accreditations ensure programs meet industry-recognized competencies. The blend of theoretical knowledge from classroom settings and extensive practical experience gained through hands-on work is paramount for success in this precise trade.
Sheet Metal Mechanic Salary & Outlook
Compensation for a Sheet Metal Mechanic is influenced by several factors, reflecting the specialized skills required in this trade. Geographic location significantly impacts earnings; major metropolitan areas or regions with high demand for construction and manufacturing often offer higher wages due to increased cost of living and specific project needs. Conversely, rural areas may see lower compensation.
Years of experience dramatically affect earning potential. An Apprentice Sheet Metal Mechanic earns less than a seasoned professional, who brings advanced fabrication, installation, and repair expertise. Specializations such as HVAC system installation, aerospace component fabrication, or precision welding can command premium pay.
Total compensation packages extend beyond base salary. These often include health insurance, retirement plans like 401(k)s, and paid time off. Some roles may offer overtime pay, project-based bonuses, or tool allowances. Union membership can also influence wage rates and benefits, often providing structured pay scales and comprehensive packages.
Industry-specific trends, such as growth in infrastructure projects or aerospace manufacturing, drive salary growth. Companies involved in complex, high-stakes projects typically offer better compensation. Negotiating leverage comes from demonstrated proficiency, certifications, and a strong safety record. While remote work is not typical for this hands-on role, travel to various job sites is common, and per diem rates might apply for out-of-town assignments. Salary figures presented are in USD, acknowledging international variations where compensation structures and living costs differ significantly.
Salary by Experience Level
Level | US Median | US Average |
---|---|---|
Apprentice Sheet Metal Mechanic | $42k USD | $45k USD |
Sheet Metal Mechanic | $59k USD | $62k USD |
Senior Sheet Metal Mechanic | $72k USD | $75k USD |
Lead Sheet Metal Mechanic | $85k USD | $88k USD |
Sheet Metal Supervisor | $100k USD | $105k USD |
Market Commentary
The job market for Sheet Metal Mechanics shows steady demand, driven by ongoing needs in construction, manufacturing, and aerospace industries. The U.S. Bureau of Labor Statistics projects employment for sheet metal workers to grow 5 percent from 2022 to 2032, about as fast as the average for all occupations. This growth translates to approximately 16,300 new openings over the decade, primarily to replace workers who exit the labor force.
Demand drivers include new commercial and residential construction, infrastructure upgrades, and the maintenance of existing HVAC systems. The aerospace sector also contributes significantly, requiring skilled mechanics for aircraft fabrication and repair. Emerging opportunities exist in sustainable building practices and energy-efficient HVAC systems, which require specialized sheet metal work for advanced air distribution and ventilation.
Supply and demand dynamics vary by region. Some areas face a shortage of skilled tradespeople, leading to competitive wages and incentives for qualified Sheet Metal Mechanics. Conversely, areas with declining manufacturing might see less demand. Automation and AI have limited direct impact on the hands-on fabrication and installation aspects of this role, making it relatively recession-resistant compared to other professions. However, computer-aided design (CAD) and automated cutting tools are becoming more prevalent, requiring mechanics to adapt and develop digital literacy.
Geographic hotspots for this role include major urban centers with robust construction sectors, states with significant aerospace industries, and regions with large manufacturing bases. Continuous learning in areas like advanced welding techniques, blueprint reading, and building codes ensures long-term career viability and enhances earning potential.
Sheet Metal Mechanic Career Path
Career progression for a Sheet Metal Mechanic typically unfolds through a structured path, emphasizing hands-on skill acquisition, safety adherence, and increasing responsibility. Advancement often begins with a formal apprenticeship, moving into journeyman status, and then into more specialized or supervisory roles. This field offers distinct individual contributor (IC) tracks focused on highly skilled fabrication and installation, alongside management/leadership tracks that oversee teams and projects.
Advancement speed depends on several factors, including consistent performance, the complexity of projects undertaken, and the specific industry—aerospace, construction, or manufacturing each have unique demands. Specialization in areas like HVAC systems, aircraft fabrication, or architectural metalwork can accelerate progression and open doors to niche opportunities. Company size also influences career paths; larger corporations may offer more structured advancement and diverse project types, while smaller shops might provide broader skill development across various tasks.
Lateral movement opportunities exist within the broader metalworking trades, such as moving into welding, machining, or quality control. Networking within industry associations and mentorship from experienced mechanics are crucial for identifying these opportunities and gaining insights into best practices. Continuous learning, often through certifications in areas like welding, CAD, or specific safety protocols, marks significant milestones and is essential for sustained growth and adapting to new technologies in metal fabrication.
Apprentice Sheet Metal Mechanic
0-4 yearsKey Focus Areas
Sheet Metal Mechanic
4-8 years total experienceKey Focus Areas
Senior Sheet Metal Mechanic
8-12 years total experienceKey Focus Areas
Lead Sheet Metal Mechanic
12-15 years total experienceKey Focus Areas
Sheet Metal Supervisor
15+ years total experienceKey Focus Areas
Apprentice Sheet Metal Mechanic
0-4 yearsWorks under direct supervision to learn and assist with various sheet metal fabrication and installation tasks. Responsibilities include material handling, basic cutting, forming, and fastening. Performs tasks with minimal decision-making authority, focusing on learning and following instructions precisely.
Key Focus Areas
Mastering fundamental safety protocols, tool identification, and basic sheet metal processes like measuring, cutting, and bending. Developing proficiency in reading blueprints and technical drawings. Building a strong work ethic and attention to detail under direct supervision.
Sheet Metal Mechanic
4-8 years total experienceIndependently performs complex sheet metal fabrication, installation, and repair tasks based on blueprints and specifications. Makes decisions regarding material usage, sequencing of operations, and adherence to quality standards. May provide guidance to apprentices and collaborate with other trades.
Key Focus Areas
Refining precision in fabrication and installation techniques. Developing problem-solving skills for on-site challenges and complex assemblies. Gaining expertise in various types of metals and their specific handling requirements. Pursuing certifications in specialized welding or advanced fabrication methods.
Senior Sheet Metal Mechanic
8-12 years total experienceHandles highly complex and specialized sheet metal projects, often involving custom fabrication, intricate repairs, or critical installations. Acts as a subject matter expert, diagnosing difficult issues and proposing innovative solutions. Provides technical guidance to a team and ensures project compliance with stringent quality and safety regulations.
Key Focus Areas
Enhancing diagnostic and troubleshooting skills for intricate systems. Specializing in advanced fabrication techniques, such as precision welding, CAD/CAM integration, or complex HVAC ductwork. Mentoring junior mechanics and contributing to process improvements. Expanding knowledge of relevant building codes or aerospace standards.
Lead Sheet Metal Mechanic
12-15 years total experienceDirects the daily activities of a team of sheet metal mechanics and apprentices on specific projects. Oversees project execution, ensuring adherence to schedules, budgets, and quality standards. Acts as the primary point of contact for project-related issues and coordinates with other trades or departments. Makes decisions on project priorities and task assignments.
Key Focus Areas
Developing strong leadership and communication skills to manage project workflow and personnel. Focusing on project planning, resource allocation, and timeline management. Improving conflict resolution and team motivation abilities. Understanding cost control and material efficiency.
Sheet Metal Supervisor
15+ years total experienceManages the overall operations of a sheet metal department or multiple project teams. Responsible for hiring, training, and performance management of staff. Develops and implements operational policies, safety protocols, and quality control procedures. Oversees departmental budgets, resource planning, and ensures project profitability and client satisfaction.
Key Focus Areas
Cultivating strategic planning, budget management, and performance evaluation skills. Focusing on long-term team development, training programs, and departmental efficiency. Building strong relationships with clients, vendors, and senior management. Staying current with industry innovations and regulatory changes.
Job Application Toolkit
Ace your application with our purpose-built resources:
Sheet Metal Mechanic Resume Examples
Proven layouts and keywords hiring managers scan for.
View examplesSheet Metal Mechanic Cover Letter Examples
Personalizable templates that showcase your impact.
View examplesTop Sheet Metal Mechanic Interview Questions
Practice with the questions asked most often.
View examplesSheet Metal Mechanic Job Description Template
Ready-to-use JD for recruiters and hiring teams.
View examplesGlobal Sheet Metal Mechanic Opportunities
Sheet Metal Mechanics find strong global demand, particularly in aviation, manufacturing, and construction sectors across industrialized nations. This role involves fabricating, assembling, installing, and repairing sheet metal products and structures. While core skills are universal, regional building codes and material specifications vary significantly. Professionals consider international roles for higher wages, specialized projects, and diverse cultural experiences. Certifications like FAA A&P (Airframe and Powerplant) or equivalent national licenses greatly enhance global mobility for aviation mechanics.
Global Salaries
Sheet Metal Mechanic salaries vary significantly by region and industry. In North America, particularly the United States, annual salaries range from $50,000 to $80,000 USD, with higher figures in aerospace hubs like Seattle or Wichita. Canadian salaries are comparable, often between CAD 55,000 and CAD 75,000. These figures reflect a strong purchasing power due to a stable economy.
European salaries differ by country. In Germany, mechanics can expect €35,000 to €55,000 (approximately $38,000-$60,000 USD), while in the UK, salaries range from £28,000 to £45,000 (about $35,000-$57,000 USD). Northern European countries like Sweden offer higher pay, but also a higher cost of living. Benefits packages in Europe often include comprehensive healthcare and generous vacation time, which can offset slightly lower base salaries compared to the US.
Asia-Pacific markets, such as Australia, offer AUD 60,000 to AUD 85,000 (around $40,000-$57,000 USD) for experienced mechanics. Middle Eastern countries, especially those with large aviation or construction projects like UAE or Qatar, provide competitive, tax-free salaries ranging from $45,000 to $70,000 USD, often including housing allowances. Latin American salaries are generally lower, typically $15,000 to $30,000 USD, reflecting a lower cost of living and different economic structures. Experience and specialized skills, such as aviation or HVAC, significantly influence compensation globally.
Remote Work
Direct remote work for a Sheet Metal Mechanic is extremely limited. The core duties involve hands-on fabrication, installation, and repair of physical materials, which requires on-site presence. Therefore, traditional remote work models are not applicable to this role.
However, some related functions, like design, CAD modeling for sheet metal components, or project management, can be performed remotely. These roles typically belong to engineers or project managers, not directly to a Sheet Metal Mechanic. Digital nomad opportunities are virtually non-existent for this specific hands-on trade. International remote work policies from employers are not relevant for this position due to its physical nature. Salary expectations for this role are always tied to a physical location and the local cost of labor.
Visa & Immigration
Sheet Metal Mechanics seeking international work typically apply for skilled worker visas. Popular destinations include Canada, Australia, Germany, and the United States, all of which have specific programs for skilled trades. Requirements generally include a recognized trade qualification, often equivalent to an apprenticeship or vocational degree. Some countries, like Australia, require a skills assessment to verify qualifications.
For aviation-focused roles, an FAA A&P license or EASA Part-66 license is often a significant advantage, sometimes a mandatory requirement. Visa application timelines vary, from a few months in Canada to over a year for some US visas. Language proficiency tests, such as IELTS for English-speaking countries or Goethe-Zertifikat for Germany, are frequently required. Employers often sponsor these visas, especially for specialized roles or in regions with labor shortages. Some countries offer pathways to permanent residency for skilled trades, such as Canada's Federal Skilled Trades Program. Family members can typically join the primary visa holder on dependent visas, subject to specific country regulations.
2025 Market Reality for Sheet Metal Mechanics
Understanding current market conditions is crucial for any Sheet Metal Mechanic. The industry has seen shifts in recent years, influenced by post-pandemic material costs and advancements in fabrication technology. Broader economic factors, such as construction spending and manufacturing output, directly shape job availability.
Market realities for Sheet Metal Mechanics vary significantly by experience level, geographic region, and the specific industry sector (e.g., aerospace, HVAC, general construction). This analysis provides an honest assessment, helping mechanics and aspiring professionals navigate the real hiring landscape as of 2025 and strategically plan their careers.
Current Challenges
Competition for experienced sheet metal mechanics remains high, especially for specialized roles in aerospace or HVAC. Market saturation affects entry-level positions without certifications. Economic uncertainty can delay large construction projects, impacting demand. Remote work normalization does not apply here, so geographic relocation for better opportunities is often necessary. The push for pre-fabricated components also reduces on-site fabrication needs.
Growth Opportunities
Areas experiencing strong demand for sheet metal mechanics include aerospace manufacturing, specialized HVAC system installation, and infrastructure projects like bridge and tunnel construction. Emerging opportunities exist in precision fabrication for advanced manufacturing sectors and in custom architectural metalwork.
Mechanics can position themselves advantageously by acquiring certifications in specialized welding techniques (e.g., TIG, MIG for exotic metals), CAD/CAM software proficiency, and advanced blueprint reading. Underserved markets often appear in regions with new industrial development or significant infrastructure upgrades. Specific skills in complex material handling (e.g., titanium, composites) or experience with automated machinery provide a competitive edge. Sectors like defense contracting and medical equipment manufacturing maintain consistent demand. Investing in specialized training now can lead to more stable and higher-paying roles, even as the market evolves.
Current Market Trends
Hiring for sheet metal mechanics shows steady demand, driven by infrastructure projects, manufacturing, and maintenance needs. The market seeks skilled professionals who can work with diverse materials and complex designs. Recent shifts include increased use of CAD/CAM software for precision fabrication and a growing emphasis on energy-efficient HVAC systems. Economic conditions, while stable, mean fewer speculative new builds and more focus on renovation and repair.
Technology, particularly automated cutting and bending machines, influences the role. Mechanics now require proficiency in operating advanced machinery and interpreting digital blueprints. Employer requirements increasingly favor certifications in welding, safety, and specific material handling. Salaries for experienced, certified mechanics remain competitive, while entry-level wages reflect the need for initial training. Geographic demand is strongest in areas with significant manufacturing, aerospace, or large-scale commercial construction. Cyclical trends often align with construction seasons, with increased hiring in spring and summer.
Emerging Specializations
The field of sheet metal fabrication is undergoing significant transformation, driven by advancements in automation, material science, and sustainability initiatives. These evolving trends are creating distinct new specialization opportunities for skilled sheet metal mechanics. Understanding these future-oriented paths allows professionals to strategically position themselves for career advancement in 2025 and beyond.
Early positioning in emerging areas often commands premium compensation and accelerated career growth. As new technologies become integral to manufacturing processes, the demand for specialized expertise in these niches intensifies. While established specializations remain vital, focusing on cutting-edge areas can unlock unparalleled opportunities for innovation and leadership within the industry.
Emerging specializations typically take several years to move from nascent concepts to mainstream adoption where a significant number of job opportunities arise. Mechanics who invest in acquiring these new skills now will be at the forefront of this shift, ready to meet future industry demands. Pursuing these cutting-edge areas involves a balance of risk and reward, offering substantial long-term benefits for those willing to adapt and learn.
Automated Fabrication Systems Specialist
The increasing adoption of robotics and advanced CNC machinery in sheet metal fabrication requires mechanics with specialized skills in automated system integration and maintenance. This involves understanding robotic programming, sensor calibration, and the interface between design software and machine operations. These specialists ensure seamless production workflows and troubleshoot complex automated systems.
Advanced Materials Fabrication Technician
The demand for lightweight, high-strength materials like composites and advanced alloys is growing across aerospace, automotive, and renewable energy sectors. Sheet metal mechanics specializing in these materials work with unique forming, joining, and finishing techniques that differ significantly from traditional steel or aluminum. This includes precision bonding, specialized welding, and advanced heat treatment processes.
Additive Manufacturing Post-Processing Mechanic
As additive manufacturing, particularly metal 3D printing, becomes more prevalent for complex parts, sheet metal mechanics can specialize in post-processing and finishing these components. This involves precision grinding, heat treatment, surface finishing, and quality inspection of 3D-printed metal parts to meet stringent industry standards. They bridge the gap between digital design and physical product.
Sustainable Metal Reclamation Specialist
Sustainability initiatives are driving the need for expertise in the repair, refurbishment, and repurposing of existing sheet metal structures and components, rather than always fabricating new ones. This specialization focuses on advanced repair techniques, material reclamation, and methods to extend the lifespan of metal parts, reducing waste and energy consumption. It requires diagnostic and corrective fabrication skills.
Smart Structures Integration Mechanic
The integration of smart sensors and IoT devices directly into sheet metal structures for real-time performance monitoring is an emerging area. Mechanics specializing here would embed, test, and maintain these integrated electronic components during the fabrication process. This ensures the structural integrity and functionality of smart metal assemblies in diverse applications, from smart buildings to industrial machinery.
Pros & Cons of Being a Sheet Metal Mechanic
Making an informed career decision requires a clear understanding of both the benefits and challenges associated with a specific profession. A career in sheet metal mechanics, like any other field, offers distinct advantages alongside genuine difficulties.
Experiences can vary significantly based on the industry sector, such as aerospace, HVAC, or construction, and the specific company culture. The pros and cons may also shift at different career stages, from an apprentice learning foundational skills to a seasoned veteran managing complex projects. What one person views as a benefit, such as hands-on work, another might see as a challenge. This assessment aims to provide a realistic overview to help individuals set appropriate expectations.
Pros
- Sheet metal mechanics possess highly specialized and tangible skills, creating a consistent demand for their expertise across various industries like construction, manufacturing, and aerospace.
- Many sheet metal mechanic roles offer stable employment, particularly in maintenance or large-scale manufacturing, providing reliable work and income.
- The work involves hands-on fabrication and problem-solving, offering a strong sense of accomplishment when a project is completed and a tangible product is created.
- This career often provides opportunities for skill development and advancement, with pathways to becoming a lead mechanic, supervisor, or specializing in areas like welding or CAD design.
- Many positions offer competitive wages, especially for experienced and certified professionals, along with benefits packages that include health insurance and retirement plans.
- Sheet metal mechanics often work as part of a team, collaborating with engineers, welders, and other tradespeople, which can foster a strong sense of camaraderie and shared purpose.
- There are diverse work environments available, ranging from large factory floors to smaller custom fabrication shops or on-site construction projects, allowing for varied experiences.
Cons
- The work environment often involves exposure to loud noises, sparks, fumes, and sharp materials, necessitating strict adherence to safety protocols and the constant use of personal protective equipment.
- The job often requires working in awkward positions, such as bending, kneeling, or reaching overhead for extended periods, which can lead to physical strain and fatigue over time.
- Many projects operate under tight deadlines, especially in manufacturing or construction, which can create high-pressure situations and the need for efficient, accurate work.
- The demand for specific sheet metal skills can fluctuate with economic cycles and industry-specific projects, potentially leading to periods of reduced work or job insecurity.
- Continuous learning is necessary to adapt to new materials, tools, and fabrication techniques, requiring ongoing training and skill development to remain competitive.
- Some roles, especially in construction or field service, may require travel to different job sites or working outdoors in various weather conditions.
- The work often involves repetitive tasks, which can become monotonous for some individuals despite the precision and skill required for each operation.
Frequently Asked Questions
Sheet Metal Mechanics face distinct challenges in precision, safety, and adapting to evolving materials and technologies. This section addresses the most common questions about entering this trade, from the necessary hands-on skills to career stability and potential for specialization within the field.
What are the typical entry requirements and qualifications to become a Sheet Metal Mechanic?
Most Sheet Metal Mechanic roles require completing a formal apprenticeship program, which typically lasts 3-5 years. These programs combine on-the-job training with classroom instruction, covering blueprint reading, welding, fabrication techniques, and safety protocols. Some entry-level positions might be available for those with vocational training or a strong mechanical aptitude, but apprenticeships are the most common and recommended path.
How long does it take to become a fully qualified Sheet Metal Mechanic?
Becoming a fully qualified Sheet Metal Mechanic through an apprenticeship can take between three to five years. This timeline includes thousands of hours of practical work experience and hundreds of hours of technical instruction. For individuals starting with no prior experience, this structured path provides comprehensive skills development and industry certification upon completion.
What are the salary expectations for a Sheet Metal Mechanic, both entry-level and experienced?
Starting salaries for apprentice Sheet Metal Mechanics are lower than journey-level mechanics, but they increase progressively as you gain experience and skills. Journey-level mechanics can expect competitive wages, often ranging from $45,000 to $70,000 annually, depending on location, industry (e.g., construction, manufacturing, aerospace), and union affiliation. Overtime opportunities can significantly boost earnings in this field.
What is the typical work-life balance like for a Sheet Metal Mechanic?
The work-life balance for Sheet Metal Mechanics can vary based on the specific project and employer. Construction and manufacturing roles might involve early mornings, long shifts, and occasional weekend work, especially when meeting project deadlines. However, many positions offer consistent daytime hours. It's a physically demanding job, requiring stamina and strength, but it often provides a clear separation between work and personal time once the workday ends.
Is the job market for Sheet Metal Mechanics stable, and what are the long-term prospects?
Job security for skilled Sheet Metal Mechanics is generally strong. Demand exists across various sectors, including HVAC installation, architectural building, aircraft manufacturing, and industrial fabrication. While economic downturns can affect the construction sector, the diverse applications of sheet metal work provide resilience. Modernization efforts in manufacturing and infrastructure also contribute to ongoing demand for skilled tradespeople.
What are the common career growth opportunities for an experienced Sheet Metal Mechanic?
Sheet Metal Mechanics have several avenues for career growth. After gaining experience, you can specialize in areas like welding, CAD/CAM programming for fabrication, or advanced HVAC systems. Opportunities also exist to move into supervisory roles, project management, or even start your own fabrication business. Continuous learning through certifications and advanced training can open doors to higher-paying and more complex roles.
What are the biggest challenges or unique aspects of being a Sheet Metal Mechanic?
Working as a Sheet Metal Mechanic involves unique challenges, including working with heavy machinery, exposure to loud noises, and handling sharp materials, necessitating strict adherence to safety protocols. Precision is paramount, as errors in fabrication can lead to costly rework or structural issues. Adapting to new technologies, such as automated bending machines and laser cutters, also requires ongoing learning and skill development.
Related Careers
Explore similar roles that might align with your interests and skills:
Sheet Metal Worker
A growing field with similar skill requirements and career progression opportunities.
Explore career guideHeating, Ventilation, and Air Conditioning (HVAC) Sheet Metal Installer
A growing field with similar skill requirements and career progression opportunities.
Explore career guideSheet Metal Fabricator
A growing field with similar skill requirements and career progression opportunities.
Explore career guideSheet Metal Installer
A growing field with similar skill requirements and career progression opportunities.
Explore career guideSheet Metal Roofer
A growing field with similar skill requirements and career progression opportunities.
Explore career guideAssess your Sheet Metal Mechanic readiness
Understanding where you stand today is the first step toward your career goals. Our Career Coach helps identify skill gaps and create personalized plans.
Skills Gap Analysis
Get a detailed assessment of your current skills versus Sheet Metal Mechanic requirements. Our AI Career Coach identifies specific areas for improvement with personalized recommendations.
See your skills gapCareer Readiness Assessment
Evaluate your overall readiness for Sheet Metal Mechanic roles with our AI Career Coach. Receive personalized recommendations for education, projects, and experience to boost your competitiveness.
Assess your readinessSimple pricing, powerful features
Upgrade to Himalayas Plus and turbocharge your job search.
Himalayas
Himalayas Plus
Himalayas Max
Find your dream job
Sign up now and join over 100,000 remote workers who receive personalized job alerts, curated job matches, and more for free!
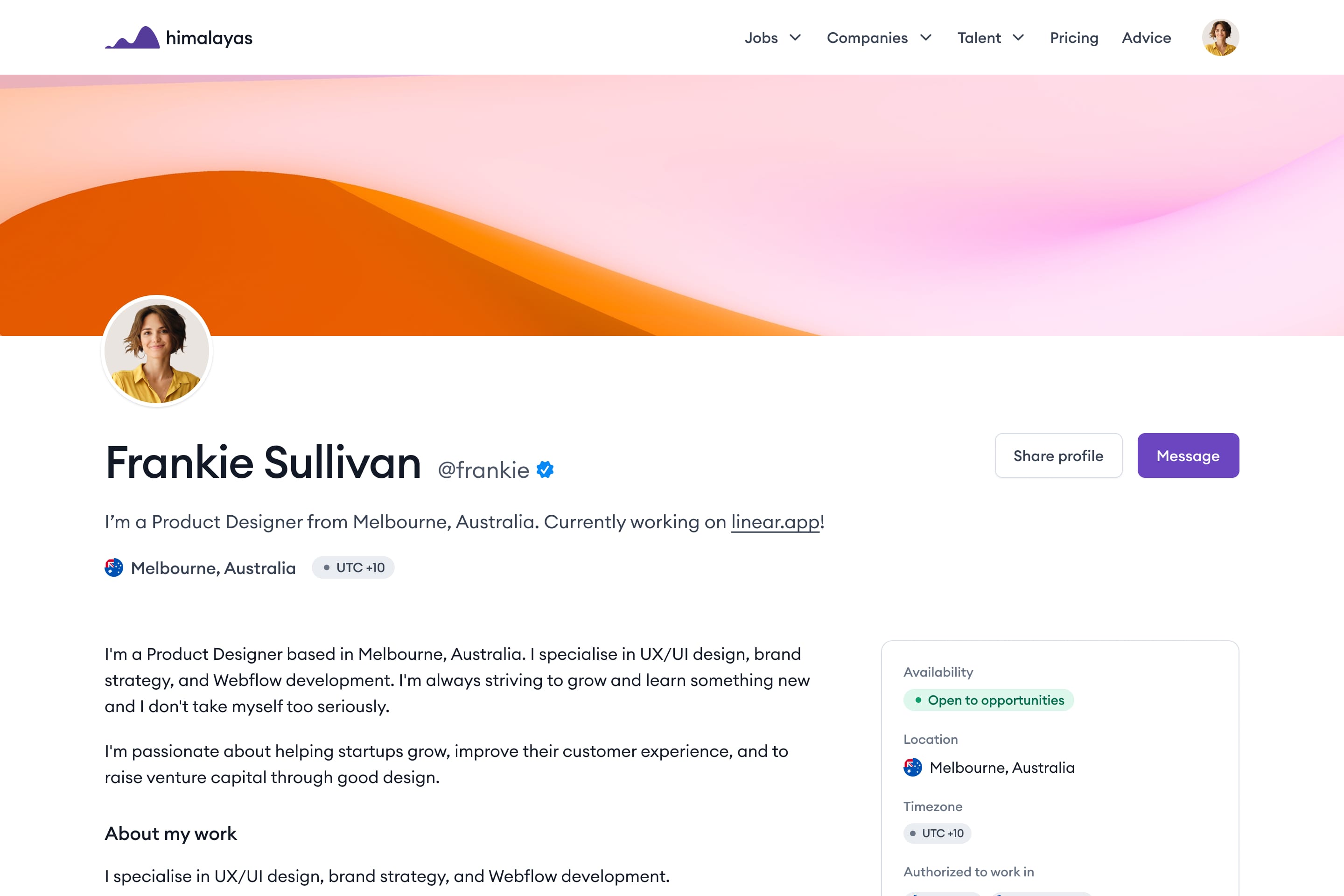