Complete Quality Coordinator Career Guide
Quality Coordinators are the backbone of operational excellence, meticulously ensuring products, services, and processes meet stringent standards and regulatory requirements. You'll drive continuous improvement, identify inefficiencies, and implement solutions that directly enhance customer satisfaction and organizational reputation. This role offers a unique blend of analytical problem-solving and cross-functional collaboration, making it vital across diverse industries.
Key Facts & Statistics
Median Salary
$79,160 USD
(U.S. national median, BLS, May 2023)
Range: $48k - $120k+ USD
Growth Outlook
7%
as fast as average (BLS, 2022-2032)
Annual Openings
≈17,800
openings annually (BLS, 2022-2032)
Top Industries
Typical Education
Bachelor's degree in a related field (e.g., business, engineering, quality management), often with relevant certifications like Six Sigma or ASQ
What is a Quality Coordinator?
A Quality Coordinator is a professional who supports the implementation and maintenance of an organization's quality management system. This role ensures that products, services, and processes consistently meet established quality standards, regulatory requirements, and customer expectations. They act as a central point for quality-related documentation, data, and corrective actions, helping to embed a culture of continuous improvement across the organization.
This role differs from a Quality Inspector, who primarily performs checks on products or processes, and a Quality Engineer, who typically designs and optimizes quality processes. A Quality Coordinator focuses more on the systemic aspects of quality assurance, coordinating efforts, managing documentation, and facilitating compliance rather than hands-on testing or engineering solutions. Their core purpose is to ensure the integrity and effectiveness of the entire quality system.
What does a Quality Coordinator do?
Key Responsibilities
- Develop and update quality management system documentation, including policies, procedures, and work instructions, to ensure compliance with industry standards.
- Conduct internal audits and inspections of processes and products, identifying non-conformances and opportunities for improvement.
- Track and analyze quality performance data, such as defect rates and customer feedback, to identify trends and report on key metrics.
- Coordinate corrective and preventive actions (CAPAs) by collaborating with relevant departments to resolve quality issues and prevent recurrence.
- Facilitate quality training sessions for employees on new procedures, quality standards, and best practices.
- Manage document control systems, ensuring all quality-related records are accurately maintained and accessible.
- Support external audits and regulatory inspections by preparing necessary documentation and assisting auditors with information requests.
Work Environment
Quality Coordinators typically work in office settings, often within manufacturing plants, healthcare facilities, or corporate environments. Their work involves a mix of independent desk work, data analysis, and highly collaborative tasks with various departments like production, engineering, and customer service. The pace can be steady, but it often becomes fast-paced when responding to quality issues or preparing for audits. While most work occurs during standard business hours, urgent issues or audit preparations may require extended hours. Remote work is possible for some administrative and data analysis tasks, but on-site presence is often necessary for audits, inspections, and direct collaboration.
Tools & Technologies
Quality Coordinators frequently use specialized Quality Management System (QMS) software like MasterControl, EtQ Reliance, or Veeva QualityOne to manage documentation, audits, and CAPAs. They also utilize spreadsheet software such as Microsoft Excel for data analysis and tracking, along with presentation tools like PowerPoint for reporting. For communication and collaboration, they rely on Microsoft Outlook, Teams, or Slack. Depending on the industry, they might use statistical analysis software like Minitab for process capability studies or enterprise resource planning (ERP) systems like SAP for integrated data management.
Quality Coordinator Skills & Qualifications
The Quality Coordinator role is central to maintaining and improving an organization's quality management systems. This position requires a blend of administrative rigor, analytical thinking, and effective communication. Requirements for Quality Coordinators vary significantly based on the industry, company size, and specific regulatory environment.
For instance, a Quality Coordinator in a pharmaceutical company will face much stricter regulatory compliance demands than one in a general manufacturing setting. Small companies might expect a Quality Coordinator to handle a broader range of tasks, including some aspects of quality assurance or control, while larger organizations often have more specialized roles. Seniority also plays a role; an entry-level coordinator might focus on data entry and document control, whereas a senior coordinator could lead internal audits and manage corrective actions. Practical experience often holds more weight than formal education, especially for those with a proven track record in quality processes.
Certifications like ASQ's Certified Quality Improvement Associate (CQIA) or Certified Quality Auditor (CQA) significantly enhance a Quality Coordinator's profile, demonstrating a commitment to professional standards. Many professionals enter this field through alternative pathways, such as internal promotions from production or administrative roles, leveraging their operational knowledge. The skill landscape evolves with new technologies, particularly in data analytics and automation, making proficiency in these areas increasingly valuable. Balancing foundational quality principles with emerging digital tools is key for career progression.
Education Requirements
Technical Skills
- Quality Management Systems (QMS) Software: Proficiency with platforms like MasterControl, EtQ Reliance, or similar systems for document control, CAPA management, and audit tracking.
- ISO Standards Knowledge: Familiarity with ISO 9001:2015 principles and requirements; understanding of industry-specific standards like ISO 13485 (medical devices) or AS9100 (aerospace) as applicable.
- Document Control: Expertise in managing, updating, and archiving controlled documents, including procedures, work instructions, and records, ensuring version control and accessibility.
- Data Entry and Management: Accurate and efficient input of quality data into databases or spreadsheets, maintaining data integrity for analysis.
- Microsoft Office Suite: Advanced proficiency in Excel for data analysis and reporting, Word for document creation, PowerPoint for presentations, and Outlook for communication.
- Root Cause Analysis Tools: Basic understanding and application of tools like 5 Whys, Fishbone diagrams, or Pareto charts to support investigations.
- Audit Preparation and Support: Ability to assist in preparing for internal and external audits, compiling necessary documentation, and tracking audit findings.
- Corrective and Preventive Action (CAPA) Processes: Understanding the lifecycle of CAPA, including initiation, investigation, implementation, and verification.
- Statistical Process Control (SPC) Basics: Fundamental knowledge of SPC concepts and charts for monitoring process performance, especially in manufacturing environments.
- Regulatory Compliance Knowledge: Awareness of specific industry regulations (e.g., FDA, GMP, GxP) pertinent to the organization's products or services.
Soft Skills
- Attention to Detail: Essential for reviewing documents, identifying discrepancies, and ensuring accuracy in quality records and reports.
- Organizational Skills: Crucial for managing multiple quality documents, schedules, audit findings, and corrective action plans efficiently.
- Communication Skills: Necessary for clearly conveying quality requirements, audit findings, and procedural changes to diverse stakeholders, both verbally and in writing.
- Problem-Solving Abilities: Important for assisting in the identification of root causes for non-conformities and contributing to effective corrective and preventive actions.
- Adaptability: Valuable for navigating evolving regulations, new quality standards, and changes in organizational processes or priorities.
- Interpersonal Skills: Helps in building rapport with colleagues across departments, facilitating cooperation during audits, and encouraging adherence to quality procedures.
- Initiative: Demonstrating proactive engagement in identifying areas for improvement and taking ownership of quality-related tasks.
- Time Management: Key for prioritizing tasks, meeting deadlines for documentation, audit schedules, and reporting requirements.
How to Become a Quality Coordinator
Breaking into a Quality Coordinator role involves navigating various pathways, from traditional education to direct industry experience. A common misconception is that a science or engineering degree is always mandatory; however, many successful Quality Coordinators come from diverse backgrounds like business administration, public health, or even liberal arts, especially if they possess strong organizational and analytical skills.
The timeline for entry can range from 3-6 months for someone with related experience or a relevant degree, to 1-2 years for a complete beginner who needs to build foundational knowledge and practical skills. Entry strategies also vary significantly by industry. For instance, highly regulated sectors like pharmaceuticals or medical devices often prefer candidates with specific industry certifications, while manufacturing or service industries might prioritize practical experience in process improvement or data analysis.
Networking and informational interviews are crucial for understanding specific industry nuances and often lead to unadvertised opportunities. Smaller companies or startups may offer more entry-level positions where you can quickly gain broad experience, whereas larger corporations might have structured training programs but higher competition. Overcoming barriers often involves demonstrating transferable skills from previous roles, such as attention to detail, documentation, problem-solving, and communication, even without direct 'quality' experience.
Step 1
Step 2
Step 3
Step 4
Step 5
Step 6
Education & Training Needed to Become a Quality Coordinator
Becoming a Quality Coordinator involves navigating a diverse educational landscape, blending formal education with practical skill development. While a bachelor's degree in a relevant field like Business Administration, Healthcare Administration, or Public Health is often preferred, it is not always strictly mandatory. These four-year degrees typically cost $40,000-$100,000+ and provide a strong theoretical foundation in quality management principles, regulatory compliance, and statistical analysis. Completion usually takes four years of full-time study.
Alternative pathways, such as specialized certifications and online courses, offer more focused and time-efficient routes. Professional certifications like those from the American Society for Quality (ASQ) range from $500-$2,000, requiring 6-18 months of dedicated self-study or online course work. These certifications are highly valued by employers, demonstrating a commitment to industry best practices and specific knowledge areas. Bootcamps specifically for quality coordination are rare; instead, focus on broader quality management or process improvement bootcamps, which can cost $5,000-$15,000 and last 8-16 weeks.
Employers generally perceive formal degrees as providing a broader understanding, while certifications signal specialized expertise. The most effective approach often combines a foundational degree with targeted certifications. Continuous learning is crucial in this field due to evolving regulations and quality standards. Practical experience gained through internships or entry-level roles is also paramount. Educational needs vary significantly by industry (e.g., healthcare, manufacturing) and the complexity of the quality systems involved. Investing in education for this role offers a strong return, as it opens doors to stable positions focused on process improvement and compliance, both critical functions for any organization.
Quality Coordinator Salary & Outlook
Compensation for a Quality Coordinator varies significantly based on several factors, reflecting the role's critical function in maintaining standards and compliance. Geographic location plays a substantial role, with areas having a higher cost of living or a strong presence of industries requiring stringent quality control, such as manufacturing, pharmaceuticals, or aerospace, typically offering higher salaries. Major metropolitan areas or specialized industry hubs often command premium compensation.
Years of experience, specific industry knowledge, and specialized certifications (e.g., Six Sigma, ISO 9001 auditor) directly impact earning potential. A Quality Coordinator specializing in complex regulatory environments or possessing advanced data analysis skills often commands higher pay. Total compensation extends beyond base salary to include performance bonuses, profit-sharing, and comprehensive benefits packages. These benefits frequently encompass health insurance, retirement plans like 401(k) matching, and allowances for continuous professional development, enhancing overall career value.
Industry-specific trends also drive salary growth. For instance, a growing emphasis on supply chain quality or product safety in certain sectors can increase demand and subsequently, compensation. Remote work options, while offering flexibility, can influence salary ranges, sometimes aligning with the employee's lower cost of living rather than the company's headquarters. While these figures primarily reflect the U.S. market, international variations can be substantial, often tied to local economic conditions and industry maturity.
Salary by Experience Level
Level | US Median | US Average |
---|---|---|
Junior Quality Coordinator | $52k USD | $55k USD |
Quality Coordinator | $65k USD | $68k USD |
Senior Quality Coordinator | $78k USD | $82k USD |
Quality Supervisor | $90k USD | $95k USD |
Quality Manager | $110k USD | $115k USD |
Quality Assurance Manager | $128k USD | $135k USD |
Market Commentary
The job market for Quality Coordinators shows stable demand, driven by an increasing global emphasis on product safety, regulatory compliance, and process efficiency across various industries. Projections suggest a steady growth outlook, particularly in sectors like healthcare, manufacturing, and technology, where quality assurance is paramount. The role is evolving, with a greater need for professionals skilled in data analytics, automation tools, and Lean Six Sigma methodologies to optimize quality processes.
Emerging opportunities for Quality Coordinators include roles focused on digital quality management systems and integration of AI-driven quality checks. The supply of qualified candidates generally meets demand, though specialized areas, such as those requiring specific regulatory expertise (e.g., FDA, aerospace standards), may experience higher demand for niche skills. This profession demonstrates a degree of recession resistance as quality control remains essential even during economic downturns to prevent costly errors and maintain consumer trust.
Geographic hotspots for Quality Coordinators include industrial centers and regions with significant pharmaceutical, medical device, or automotive manufacturing. Remote work opportunities are expanding, particularly for roles that involve documentation, data analysis, and virtual audits, allowing for greater location flexibility. Future-proofing this career involves continuous learning in new quality standards, technology adoption, and cross-functional collaboration skills, ensuring adaptability in an evolving industrial landscape.
Quality Coordinator Career Path
Career progression for a Quality Coordinator involves a clear path from entry-level support to strategic leadership, focusing on process improvement and quality assurance. Professionals can pursue an individual contributor (IC) track, becoming highly specialized experts in quality systems, or transition into management roles, leading teams and departments. Performance, continuous learning, and the ability to drive measurable improvements significantly influence advancement speed.
Company size and industry sector also shape career trajectories. Smaller organizations might offer broader responsibilities earlier, while larger corporations often provide more structured paths and opportunities for specialization. Lateral moves into related fields like regulatory affairs, operations management, or even product development are common, leveraging a strong understanding of quality processes. Networking within industry associations and seeking mentorship from experienced quality professionals are crucial for identifying new opportunities and gaining insights.
Key milestones include obtaining certifications like ASQ Certified Quality Engineer (CQE) or Six Sigma Green/Black Belt, which validate expertise and enhance career prospects. Developing a reputation for analytical rigor and effective problem-solving accelerates progression. While traditional paths lead to management, some highly experienced Quality Assurance Managers transition into consulting or senior leadership roles focused on organizational excellence and strategic quality initiatives across an enterprise.
Junior Quality Coordinator
0-2 yearsKey Focus Areas
Quality Coordinator
2-4 yearsKey Focus Areas
Senior Quality Coordinator
4-7 yearsKey Focus Areas
Quality Supervisor
6-9 years total experienceKey Focus Areas
Quality Manager
8-12 years total experienceKey Focus Areas
Quality Assurance Manager
12+ years total experienceKey Focus Areas
Junior Quality Coordinator
0-2 yearsSupports the quality department by collecting data, performing basic inspections, and maintaining quality records. Works under direct supervision, assisting in the implementation of quality checks. Helps identify non-conforming products and documents findings, contributing to initial problem identification.
Key Focus Areas
Develop foundational knowledge of quality control methods, data collection, and basic statistical analysis. Focus on mastering company-specific quality procedures and documentation. Build strong communication skills for interacting with production teams and understanding their challenges.
Quality Coordinator
2-4 yearsExecutes quality control procedures, conducts inspections, and performs audits to ensure compliance with standards. Analyzes quality data to identify trends and potential issues, recommending corrective actions. Collaborates with production and engineering to implement quality improvements, operating with moderate autonomy.
Key Focus Areas
Enhance problem-solving skills, root cause analysis, and corrective action planning. Gain proficiency in quality management systems (e.g., ISO 9001). Develop presentation skills to communicate quality data and findings to various stakeholders.
Senior Quality Coordinator
4-7 yearsLeads complex quality investigations, develops and refines quality control processes, and performs internal audits. Serves as a subject matter expert, interpreting quality standards and guiding teams on compliance. Drives continuous improvement projects, influencing operational changes and training junior coordinators.
Key Focus Areas
Master advanced statistical process control (SPC) and lean manufacturing principles. Develop project management skills for leading quality improvement initiatives. Begin mentoring junior staff and contribute to the development of new quality procedures.
Quality Supervisor
6-9 years total experienceOversees a small team of Quality Coordinators, assigning tasks, providing guidance, and monitoring performance. Ensures daily quality operations run smoothly, troubleshooting issues and making immediate decisions. Implements departmental goals and contributes to the development of quality strategies, reporting to a Quality Manager.
Key Focus Areas
Cultivate leadership and team management skills, including performance feedback and conflict resolution. Develop a deeper understanding of regulatory requirements specific to the industry. Focus on strategic planning for quality initiatives and resource allocation.
Quality Manager
8-12 years total experienceManages the overall quality control function for a specific product line or area, ensuring compliance with all internal and external standards. Develops, implements, and maintains quality management systems, leading audit preparations. Directs a team of supervisors and coordinators, making key hiring and performance decisions, and reports to a Quality Assurance Manager.
Key Focus Areas
Develop strong business acumen, financial literacy, and strategic planning capabilities. Focus on cross-functional collaboration and stakeholder management across departments. Gain expertise in risk management and compliance frameworks.
Quality Assurance Manager
12+ years total experienceProvides strategic direction for the entire quality assurance department, overseeing all quality systems, policies, and procedures. Drives the organization's quality vision, setting long-term goals and ensuring regulatory compliance across all operations. Manages a large team of managers and professionals, playing a critical role in executive decision-making and driving significant business impact.
Key Focus Areas
Master organizational change management and advanced strategic leadership. Develop executive communication and negotiation skills. Focus on building a culture of quality and continuous improvement across the entire organization.
Job Application Toolkit
Ace your application with our purpose-built resources:
Quality Coordinator Resume Examples
Proven layouts and keywords hiring managers scan for.
View examplesQuality Coordinator Cover Letter Examples
Personalizable templates that showcase your impact.
View examplesTop Quality Coordinator Interview Questions
Practice with the questions asked most often.
View examplesQuality Coordinator Job Description Template
Ready-to-use JD for recruiters and hiring teams.
View examplesGlobal Quality Coordinator Opportunities
A Quality Coordinator ensures adherence to quality standards and regulatory requirements across various industries globally. This role involves implementing quality management systems, conducting audits, and managing documentation. International demand for skilled Quality Coordinators remains steady across manufacturing, pharmaceuticals, and technology sectors, driven by global supply chains and stringent compliance needs. Cultural nuances affect quality implementation, particularly in highly regulated markets. Professionals often seek international roles for diverse industry exposure and career advancement. Certifications like ISO 9001 Lead Auditor or Six Sigma Green Belt significantly enhance global mobility.
Global Salaries
Salaries for Quality Coordinators vary significantly by region and industry. In North America, a Quality Coordinator in the US can expect to earn between $55,000 and $75,000 USD annually, while in Canada, the range is typically C$50,000 to C$70,000. These figures reflect a higher cost of living in major cities.
European salaries differ, with Western European countries like Germany offering €40,000 to €60,000 (approximately $43,000-$65,000 USD). The UK sees salaries from £30,000 to £45,000 (about $38,000-$57,000 USD). Southern and Eastern Europe generally offer lower compensation but also have a lower cost of living.
In the Asia-Pacific region, a Quality Coordinator in Australia might earn A$60,000 to A$80,000 (around $40,000-$53,000 USD), whereas in Singapore, it ranges from S$45,000 to S$65,000 (about $33,000-$48,000 USD). India offers competitive salaries relative to its cost of living, often Rs 400,000 to Rs 800,000 (approximately $4,800-$9,600 USD) for experienced professionals. Latin American countries like Brazil typically offer R$40,000 to R$70,000 (around $8,000-$14,000 USD).
Salary structures also differ, with North America often including performance bonuses and comprehensive health benefits. European countries may offer more generous vacation time and public healthcare. Tax implications vary by country, affecting take-home pay. Experience and specialized industry knowledge significantly influence compensation globally, with highly regulated sectors often paying more.
Remote Work
The potential for remote work for Quality Coordinators depends on the industry and the specific tasks. Roles heavily reliant on on-site audits or physical process control are less suitable for full remote work. However, managing documentation, developing quality procedures, and conducting virtual audits can be done remotely.
Legal and tax implications for international remote work require careful consideration. Companies must understand local labor laws and tax regulations for employees in different countries. Time zone differences can impact collaboration with international teams, requiring flexible working hours.
Digital nomad visas are emerging in countries like Portugal and Spain, offering pathways for remote professionals. Some global companies have policies supporting international remote hiring for roles that do not require physical presence. Remote work can influence salary expectations, with some companies adjusting pay based on the employee's location and local cost of living. Platforms like LinkedIn and specific industry job boards often list remote Quality Coordinator positions. A reliable internet connection and a dedicated home workspace are essential for success.
Visa & Immigration
Quality Coordinators often qualify for skilled worker visas in many countries. Popular destinations include Canada (Express Entry), Australia (Skilled Nominated Visa), Germany (EU Blue Card), and the UK (Skilled Worker visa). Requirements typically include a relevant bachelor's degree, professional experience, and a job offer from a sponsoring employer.
Credential recognition is crucial; applicants may need to have their educational qualifications assessed by a designated body. Professional licensing is generally not required for Quality Coordinators, but industry-specific certifications are beneficial. Visa timelines vary, ranging from a few months to over a year, depending on the country and visa type.
Many countries offer pathways to permanent residency after several years of skilled work. Language proficiency tests, such as IELTS for English-speaking countries or Goethe-Zertifikat for Germany, are often mandatory. Some countries prioritize occupations in demand, which can offer faster processing or additional points in immigration systems. Family visas for spouses and dependents are typically available, allowing families to relocate together.
2025 Market Reality for Quality Coordinators
Understanding the current market realities for Quality Coordinators is crucial for strategic career planning. The landscape has evolved rapidly between 2023 and 2025, driven by post-pandemic operational shifts and the accelerating impact of AI.
Broader economic factors, such as inflation and supply chain volatility, directly influence hiring budgets and the strategic importance companies place on quality assurance. Market realities for Quality Coordinators also vary significantly by experience level, with entry-level roles facing more competition than senior positions. Geographic location and company size further dictate specific opportunities and challenges. This analysis provides an honest assessment, preparing job seekers for practical hiring realities.
Current Challenges
Quality Coordinators face increased competition, especially at entry levels, as companies seek more experienced candidates who can immediately implement complex quality systems. Economic uncertainty leads some organizations to consolidate roles, expecting a single coordinator to handle broader responsibilities. Additionally, the rapid integration of AI and automation tools means coordinators must quickly adapt their skill sets to manage new digital quality processes, creating a gap for those without updated technical proficiencies.
Growth Opportunities
Despite challenges, strong demand exists for Quality Coordinators proficient in data analytics and AI-driven quality tools. Emerging roles focus on managing automated inspection systems and validating AI model outputs for quality control. Professionals who can analyze large datasets to identify quality trends and predict potential failures are highly valued.
Strategic positioning involves acquiring certifications in advanced quality methodologies like Lean Six Sigma or specific industry standards such as AS9100 or ISO 13485. These credentials provide a competitive edge. Underserved markets often include small to medium-sized manufacturing operations that are just beginning to implement formal quality management systems, or niche industries with strict regulatory requirements.
Expertise in specific software platforms for quality management (e.g., eQMS systems) or statistical process control (SPC) also offers significant advantages. Market corrections can create opportunities as companies restructure, prioritizing efficiency and defect reduction, placing a premium on skilled quality professionals. Sectors like medical devices, aerospace, and advanced manufacturing continue to show robust demand for dedicated Quality Coordinators.
Current Market Trends
The market for Quality Coordinators in 2025 shows steady demand, though hiring patterns have shifted significantly. Companies increasingly seek coordinators with strong data analysis skills and experience with digital quality management systems, moving beyond traditional manual processes. Post-pandemic supply chain disruptions continue to highlight the critical need for robust quality control, maintaining a baseline demand.
Generative AI and automation are reshaping the role. Instead of purely manual inspections, coordinators now often manage AI-powered defect detection systems and analyze output from automated testing. This demands a blend of traditional quality assurance knowledge with technological fluency. Organizations are also consolidating roles, expecting coordinators to contribute to process improvement initiatives and regulatory compliance, rather than just oversight.
Salary trends for Quality Coordinators remain stable, with slight increases for those demonstrating expertise in data analytics, AI integration, and lean methodologies. Market saturation is noticeable at the entry level, where competition for foundational roles is high. However, experienced coordinators with specialized certifications in areas like Six Sigma or ISO standards find ample opportunities. Geographically, manufacturing hubs and highly regulated industries like pharmaceuticals and aerospace exhibit stronger demand, though remote work for some documentation and system management tasks is becoming more normalized.
Emerging Specializations
The role of a Quality Coordinator is evolving significantly, driven by rapid advancements in technology, increasingly complex regulatory landscapes, and a heightened focus on data-driven decision-making. These shifts are creating entirely new specialization opportunities that demand a forward-looking perspective.
Early positioning in these emerging areas is crucial for career advancement from 2025 onwards. Professionals who proactively develop expertise in these nascent fields often command premium compensation and experience accelerated career growth, distinguishing themselves from those in more established specializations. While traditional quality coordination skills remain foundational, embracing these new domains offers a strategic advantage.
Many emerging areas, particularly those at the intersection of quality and advanced analytics or sustainability, are moving from niche interests to mainstream requirements. This transition typically takes 3-5 years for significant job opportunities to materialize, offering a window for professionals to gain expertise. Pursuing cutting-edge specializations involves a balance of risk and reward; while the initial investment in learning new skills may be substantial, the potential for long-term career resilience and leadership is considerable.
Understanding these future-oriented career paths allows Quality Coordinators to strategically align their skill development with upcoming industry demands, ensuring they are well-prepared for the next generation of opportunities.
Data Quality Assurance Coordinator
This specialization focuses on ensuring the quality and integrity of data used in decision-making and automated processes. As organizations increasingly rely on large datasets for everything from product development to operational efficiency, the Quality Coordinator specializing in Data Quality Assurance ensures that data is accurate, consistent, and reliable. This involves setting data quality standards, implementing validation rules, and monitoring data pipelines for anomalies, which is critical for maintaining robust quality management systems.
Sustainability Quality Coordinator
With the growing emphasis on environmental, social, and governance (ESG) factors, this role focuses on integrating sustainability principles into quality management systems. A Sustainability Quality Coordinator ensures that products, processes, and supply chains meet both traditional quality standards and emerging environmental and social responsibility benchmarks. This involves auditing for sustainable practices, tracking environmental impact metrics, and ensuring compliance with green certifications, thereby extending the scope of quality beyond traditional metrics.
AI/Predictive Quality Coordinator
This specialization applies advanced analytics and machine learning techniques to predict and prevent quality issues. An AI/Predictive Quality Coordinator uses statistical models and AI algorithms to analyze vast amounts of operational data, identifying patterns that indicate potential defects or failures before they occur. This proactive approach moves quality control from reactive inspection to predictive intervention, significantly reducing waste and improving efficiency across manufacturing or service delivery processes.
Regulatory Compliance Quality Coordinator
This emerging area focuses on ensuring the quality and reliability of software and systems in highly regulated or safety-critical environments. A Regulatory Compliance Quality Coordinator specializes in validating that software development processes, medical devices, or financial systems adhere strictly to industry-specific regulations and international standards. This requires deep understanding of compliance frameworks, risk management, and meticulous documentation practices to prevent costly non-compliance issues.
Cybersecurity Quality Coordinator
This role centers on ensuring the quality and security of products and processes within the context of cyber threats and digital vulnerabilities. A Cybersecurity Quality Coordinator integrates cybersecurity best practices into the quality management system, focusing on securing data, intellectual property, and operational technology from cyber-attacks. This involves assessing system vulnerabilities, ensuring secure coding practices, and developing incident response plans to maintain product integrity and customer trust in an increasingly connected world.
Pros & Cons of Being a Quality Coordinator
Making informed career decisions requires a realistic understanding of both the benefits and challenges associated with a particular field. A Quality Coordinator role, like any profession, offers distinct advantages alongside genuine difficulties that impact daily work life. It is important to recognize that individual experiences can vary significantly based on the specific industry, company culture, team dynamics, and personal aptitude. Furthermore, the emphasis on certain pros and cons may shift as one progresses from an entry-level position to a more senior or specialized role within quality assurance. What one person views as a positive aspect, such as meticulous attention to detail, another might find a drawback if they prefer less structured tasks. This assessment provides an honest look at the typical realities of being a Quality Coordinator, helping prospective candidates set appropriate expectations.
Pros
- Quality Coordinators play a crucial role in ensuring product or service integrity, providing a strong sense of purpose and direct contribution to organizational reputation and customer satisfaction.
- The position offers diverse learning opportunities by interacting with various departments, from production and engineering to sales and customer service, providing a holistic view of business operations.
- Developing strong analytical and problem-solving skills is central to this role, as Quality Coordinators regularly investigate root causes of issues and implement corrective actions, enhancing critical thinking abilities.
- Many industries require Quality Coordinators, leading to stable job security and consistent demand across sectors such as manufacturing, healthcare, pharmaceuticals, and technology, offering good career mobility.
- The role involves developing expertise in industry-specific quality standards and regulatory compliance, making individuals highly valuable assets in environments where adherence to strict guidelines is paramount.
- Quality Coordinators often work collaboratively with cross-functional teams to implement improvements, fostering teamwork and interpersonal skills through project-based work and process optimization initiatives.
- There are clear pathways for career advancement into roles such as Quality Assurance Manager, Quality Engineer, or specialized compliance officer positions, often requiring additional certifications or experience.
Cons
- Quality Coordinators often face significant pressure to maintain high standards and resolve non-conformances quickly, which can lead to stress and demanding work periods, especially during audits or critical production issues.
- The role can involve extensive documentation and administrative tasks, such as updating quality manuals, logging incidents, and preparing reports, which some individuals may find repetitive or tedious over time.
- Interaction with other departments can sometimes be challenging, as Quality Coordinators frequently need to enforce procedures or highlight deficiencies, potentially leading to resistance or conflicts from operational teams.
- Career progression within a Quality Coordinator role might feel limited without further specialization or management training, as the position often focuses on maintaining existing systems rather than strategic development.
- Staying current with evolving industry regulations, quality standards (e.g., ISO, GMP), and best practices requires continuous learning and professional development, which demands a personal commitment outside of daily tasks.
- The impact of a Quality Coordinator's work is often preventative or reactive to issues, meaning direct recognition for their efforts can sometimes be less visible compared to roles directly involved in product creation or sales.
- Some Quality Coordinator positions, particularly in manufacturing or healthcare, may require working in environments with specific safety protocols, controlled conditions, or exposure to manufacturing noise and processes.
Frequently Asked Questions
What educational background or certifications are typically required to become a Quality Coordinator?
A bachelor's degree in a relevant field like business administration, engineering, or a specific industry discipline (e.g., healthcare, manufacturing) often serves as a strong foundation. Many Quality Coordinator roles also value certifications such as ASQ Certified Quality Improvement Associate (CQIA) or Six Sigma Yellow Belt. Practical experience in data analysis, process documentation, and cross-functional team collaboration is highly beneficial for demonstrating readiness.
How long does it typically take to transition into a Quality Coordinator role if I'm starting fresh?
Transitioning into a Quality Coordinator role can take anywhere from 6 months to 2 years, depending on your current experience and the industry. If you have a relevant degree and some foundational experience in an operational role, you might secure an entry-level position within 6-12 months. Those needing to gain specific certifications or practical quality experience might need 1-2 years of dedicated effort and learning.
What are the typical salary expectations for an entry-level Quality Coordinator?
Entry-level Quality Coordinators can expect a salary range that varies significantly by industry, location, and company size. Generally, salaries might start from around $45,000 to $55,000 annually. With a few years of experience, specialized industry knowledge, and advanced certifications, this can increase to $60,000-$75,000 or more. Researching specific industry benchmarks in your target region provides more accurate expectations.
What is the typical work-life balance like for a Quality Coordinator?
The work-life balance for a Quality Coordinator is generally good, often involving standard business hours. However, it can fluctuate based on project deadlines, audit schedules, or critical quality incidents. During peak periods, such as preparation for a major certification audit or addressing a significant non-conformance, you might experience increased demands. Most of the time, the role allows for a predictable schedule.
What is the job security and market demand like for Quality Coordinators?
The job market for Quality Coordinators remains stable and consistent, as quality assurance is a critical function across almost all industries, including manufacturing, healthcare, technology, and services. Companies continually need professionals to ensure compliance, improve processes, and maintain standards. While specific industry demands can shift, the core need for quality oversight ensures ongoing demand for these roles.
What are the typical career growth opportunities for a Quality Coordinator?
Quality Coordinators have clear paths for career growth. You can advance to Quality Specialist, Quality Engineer, or even Quality Manager roles. Specializing in areas like Lean Six Sigma, ISO standards, or specific industry regulations can open doors to senior positions. Some professionals also move into related fields like process improvement, project management, or regulatory affairs, leveraging their strong understanding of systems and compliance.
What are some common challenges or frustrations specific to the Quality Coordinator role?
A common challenge for Quality Coordinators involves gaining buy-in from different departments for quality initiatives. You often need strong communication and persuasion skills to implement changes, ensure adherence to new procedures, and encourage a culture of quality across the organization. Another challenge is managing extensive documentation and ensuring its accuracy and accessibility, which requires meticulous attention to detail.
Can Quality Coordinators realistically work remotely, or is it primarily an on-site role?
Remote work opportunities for Quality Coordinators vary significantly by industry and company. Roles focused heavily on documentation, data analysis, and virtual meetings may offer more flexibility for remote or hybrid work. However, positions in manufacturing or industries requiring hands-on inspection, facility audits, or direct interaction with physical processes often necessitate on-site presence. It's crucial to clarify remote work policies during the job search.
Related Careers
Explore similar roles that might align with your interests and skills:
Quality Assurance Coordinator
A growing field with similar skill requirements and career progression opportunities.
Explore career guideQuality Assurance Supervisor
A growing field with similar skill requirements and career progression opportunities.
Explore career guideQuality Control Coordinator
A growing field with similar skill requirements and career progression opportunities.
Explore career guideQuality Control Manager
A growing field with similar skill requirements and career progression opportunities.
Explore career guideQuality Supervisor
A growing field with similar skill requirements and career progression opportunities.
Explore career guideAssess your Quality Coordinator readiness
Understanding where you stand today is the first step toward your career goals. Our Career Coach helps identify skill gaps and create personalized plans.
Skills Gap Analysis
Get a detailed assessment of your current skills versus Quality Coordinator requirements. Our AI Career Coach identifies specific areas for improvement with personalized recommendations.
See your skills gapCareer Readiness Assessment
Evaluate your overall readiness for Quality Coordinator roles with our AI Career Coach. Receive personalized recommendations for education, projects, and experience to boost your competitiveness.
Assess your readinessSimple pricing, powerful features
Upgrade to Himalayas Plus and turbocharge your job search.
Himalayas
Himalayas Plus
Himalayas Max
Find your dream job
Sign up now and join over 100,000 remote workers who receive personalized job alerts, curated job matches, and more for free!
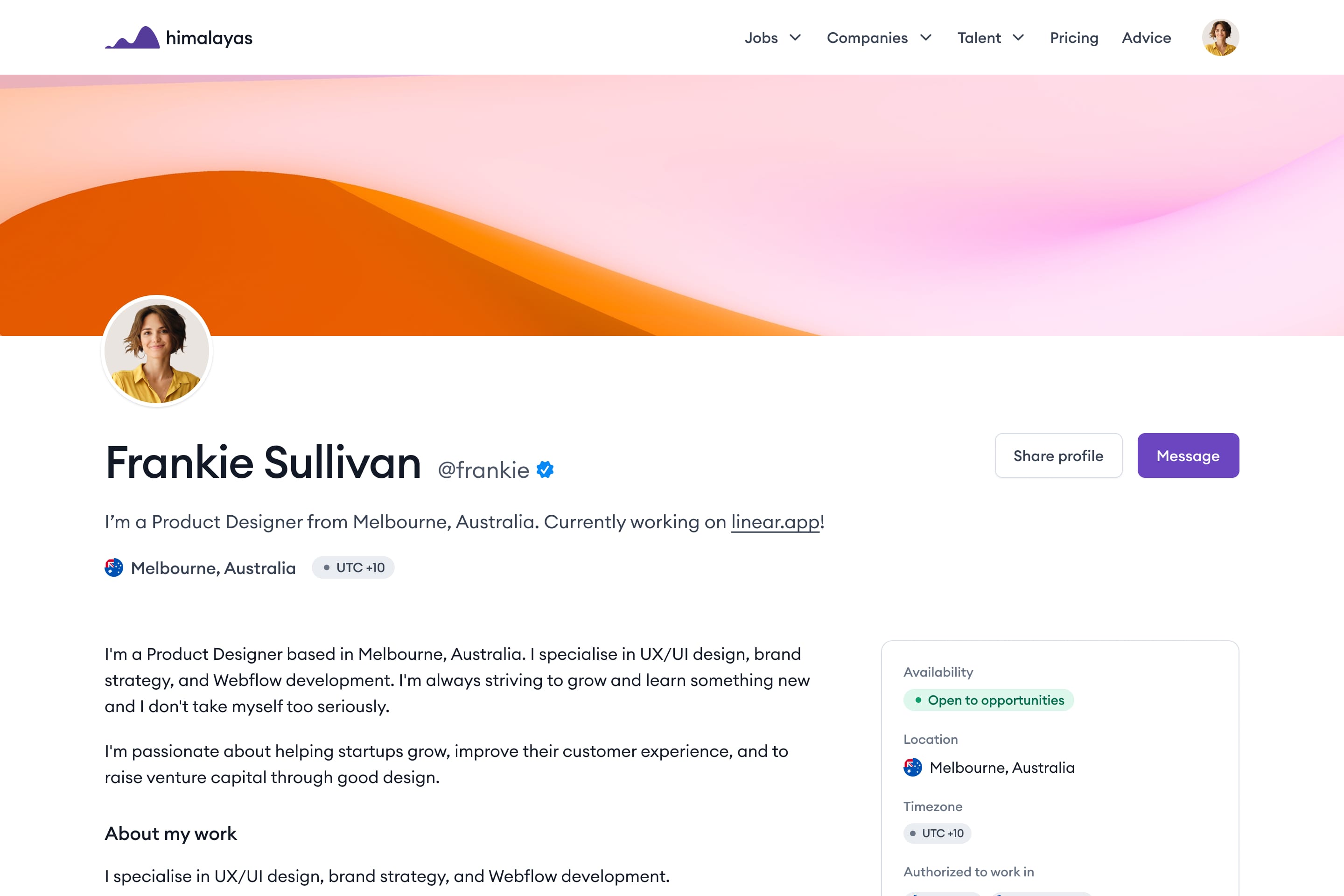