Complete Quality Control Supervisor Career Guide
Quality Control Supervisors are the gatekeepers of excellence, ensuring products and services consistently meet rigorous standards and customer expectations. They lead teams in identifying flaws, implementing corrective actions, and optimizing processes, directly impacting a company's reputation and bottom line. This role is crucial for maintaining operational integrity and driving continuous improvement in diverse industries.
Key Facts & Statistics
Median Salary
$70,050 USD
(U.S. national median, May 2023, U.S. Bureau of Labor Statistics)
Range: $45k - $95k+ USD
Growth Outlook
1%
slower than average (U.S. Bureau of Labor Statistics, 2022-2032)
Annual Openings
≈34k
openings annually (U.S. Bureau of Labor Statistics)
Top Industries
Typical Education
Bachelor's degree in a related field such as engineering, business, or quality management, or significant experience in quality assurance roles; certifications like ASQ's Certified Quality Supervisor (CQS) are highly valued.
What is a Quality Control Supervisor?
A Quality Control Supervisor is a frontline leader responsible for ensuring products or services meet established quality standards and regulatory requirements. They oversee the daily operations of a quality control team, implementing inspection procedures, monitoring production processes, and identifying areas for quality improvement. This role ensures that products are consistent, reliable, and free from defects before reaching the customer.
Unlike a Quality Assurance Manager who focuses on the entire quality system and prevention, or a Quality Engineer who designs and optimizes quality processes, the Quality Control Supervisor is directly involved in the inspection and testing phase. They manage the hands-on verification of product quality and lead the team performing these checks, playing a critical role in defect detection and immediate corrective action on the production floor.
What does a Quality Control Supervisor do?
Key Responsibilities
- Oversee and guide a team of quality control inspectors, providing training, scheduling, and performance feedback to ensure consistent adherence to quality standards.
- Develop and implement quality control procedures and inspection plans, ensuring alignment with industry regulations and company specifications.
- Conduct regular audits of production processes and finished products, identifying non-conformances and initiating corrective actions to prevent recurrence.
- Analyze quality data and metrics to identify trends, root causes of defects, and areas for continuous improvement in manufacturing or service delivery.
- Collaborate with production, engineering, and supply chain teams to resolve quality issues, implement process changes, and improve product reliability.
- Manage calibration and maintenance schedules for all quality control equipment, ensuring accuracy and reliability of testing instruments.
- Prepare detailed quality reports for management, summarizing inspection results, non-conformance trends, and the effectiveness of corrective actions.
Work Environment
Quality Control Supervisors primarily work in manufacturing plants, production facilities, or laboratories. Their environment can range from clean rooms to factory floors, often requiring adherence to safety protocols and personal protective equipment. They spend time both in an office setting for data analysis and reporting, and on the production floor overseeing inspections and addressing issues.
The role involves significant interaction with cross-functional teams, including production managers, engineers, and line workers. The pace is often dynamic and responsive, as supervisors must quickly address emerging quality concerns. While primarily on-site, some roles in larger organizations might involve occasional travel to supplier sites or other company facilities. Work hours are typically standard business hours, but can extend during peak production periods or to resolve critical quality problems.
Tools & Technologies
Quality Control Supervisors frequently use a range of tools and technologies to monitor and improve product quality. They work with Statistical Process Control (SPC) software like Minitab or JMP to analyze data and identify trends. Quality Management Systems (QMS) such as ISO 9001 compliant platforms, MasterControl, or SAP QM modules are central to documenting procedures and managing non-conformances.
They also interact with various inspection tools, including calipers, micrometers, gauges, and coordinate measuring machines (CMMs). Data visualization tools like Tableau or Power BI help them present findings. Additionally, they utilize enterprise resource planning (ERP) systems for production data and standard office productivity suites for reporting and communication.
Quality Control Supervisor Skills & Qualifications
A Quality Control Supervisor ensures product or service quality meets established standards, regulations, and customer expectations. This role involves overseeing quality inspectors, implementing quality procedures, and analyzing data to identify areas for improvement. Requirements vary significantly based on the industry, company size, and product complexity.
For example, a QC Supervisor in pharmaceuticals needs deep knowledge of Good Manufacturing Practices (GMP) and FDA regulations. In contrast, a supervisor in automotive manufacturing focuses on ISO/TS standards and lean methodologies. Entry-level supervisors typically require a bachelor's degree and some experience, while senior roles often demand a master's degree or extensive industry-specific experience. Certifications like Six Sigma Green Belt or Black Belt, or ASQ certifications (e.g., Certified Quality Engineer, Certified Quality Auditor) add substantial value, often outweighing a master's degree in practical application.
The field is evolving with increased automation and data analytics. Supervisors must now integrate digital tools for real-time monitoring and predictive quality. Practical experience, especially hands-on work with quality systems and process improvement initiatives, often holds more weight than formal education alone. Alternative paths, such as vocational training combined with significant on-the-job experience and certifications, are increasingly accepted, particularly in skilled trades or manufacturing environments. Understanding this balance helps individuals prioritize their learning and development efforts effectively.
Education Requirements
Technical Skills
- Quality Management Systems (QMS) implementation and maintenance (e.g., ISO 9001, AS9100, IATF 16949, GMP)
- Statistical Process Control (SPC) and data analysis using tools like Minitab or JMP
- Root Cause Analysis (RCA) methodologies (e.g., 5 Whys, Fishbone Diagrams, FMEA)
- Inspection and testing techniques, including proficiency with measurement tools and equipment
- Lean Manufacturing and Six Sigma principles for process optimization and defect reduction
- Non-conformance management and Corrective and Preventive Action (CAPA) systems
- Auditing principles and conducting internal/external quality audits
- Data visualization and reporting tools (e.g., Excel, Power BI, Tableau) for quality metrics
- Blueprint reading and Geometric Dimensioning & Tolerancing (GD&T) interpretation
- Calibration processes and equipment management
- Regulatory compliance specific to industry (e.g., FDA, OSHA, EPA)
- Supplier Quality Management and incoming material inspection protocols
Soft Skills
- Leadership and Team Management: Directing and motivating quality control teams, fostering a culture of quality, and managing performance.
- Problem-Solving and Analytical Thinking: Identifying root causes of quality issues, developing effective corrective actions, and making data-driven decisions.
- Communication and Reporting: Clearly articulating quality standards, findings, and improvement plans to diverse stakeholders, including production, management, and external auditors.
- Attention to Detail: Meticulously reviewing products, processes, and documentation to ensure compliance with stringent quality specifications.
- Adaptability and Continuous Improvement: Adjusting to changing production demands, new technologies, and evolving quality standards, while promoting ongoing process enhancements.
- Conflict Resolution and Negotiation: Addressing disagreements regarding quality standards or non-conformances with production teams or suppliers constructively.
- Ethical Conduct and Integrity: Upholding strict ethical standards in quality assessments and reporting, especially in regulated industries.
- Time Management and Prioritization: Effectively managing multiple quality control tasks, audits, and deadlines in a fast-paced environment and allocating resources efficiently to critical areas of the quality process or product inspection.
How to Become a Quality Control Supervisor
Entering the Quality Control Supervisor field involves diverse pathways, from direct industry experience to specialized education. Individuals with a background in manufacturing, science, or engineering often transition into this role, leveraging their understanding of production processes and quality standards. A complete beginner might spend 1-2 years building foundational knowledge and gaining entry-level QC experience before moving into a supervisory capacity.
Career changers or those from related fields, like laboratory technicians or production leads, can often accelerate this timeline to 6-12 months by focusing on specific quality management certifications. The hiring landscape varies significantly by industry; for instance, pharmaceuticals and aerospace have stringent regulatory requirements, demanding more specialized knowledge than consumer goods. Smaller companies might offer quicker advancement due to broader responsibilities, while larger corporations often require more formal credentials and extensive experience.
Overcoming barriers often involves demonstrating a strong grasp of quality methodologies, even if direct supervisory experience is limited. Networking within industry associations and seeking mentorship from experienced QC professionals can open doors and provide invaluable insights into specific sector demands. Focus on building a robust understanding of regulatory compliance and process improvement, as these are critical skills for any aspiring supervisor.
Step 1
Step 2
Step 3
Step 4
Step 5
Step 6
Education & Training Needed to Become a Quality Control Supervisor
Becoming a Quality Control Supervisor involves a blend of formal education and practical experience, with educational needs varying significantly by industry and company size. Formal four-year degrees in fields like Engineering, Quality Management, or Business Administration provide a strong theoretical foundation. These bachelor's degrees typically cost between $40,000 and $100,000 or more and require four years of full-time study. They are often preferred for roles in highly regulated industries such as pharmaceuticals, aerospace, or advanced manufacturing, where a deep understanding of statistical process control, lean manufacturing, and regulatory compliance is critical.
Alternative pathways, such as associate's degrees, specialized certifications, or professional training courses, offer more focused and often quicker entry into the field. Associate's degrees, costing $10,000-$25,000 over two years, provide a solid technical base. Industry-recognized certifications like the ASQ Certified Quality Supervisor (CQS) or Certified Quality Engineer (CQE) are highly valued. These certifications often require a combination of experience and passing a rigorous exam, with preparation courses ranging from a few hundred to a few thousand dollars and completion times from 6 to 18 months. Employers widely accept these credentials, especially when combined with relevant work experience, as they demonstrate a commitment to professional standards.
Continuous learning is essential for Quality Control Supervisors to stay current with evolving industry standards, technologies, and regulatory changes. This includes advanced courses in Six Sigma, Lean principles, or specific quality management software. The cost-benefit of different educational investments depends on career aspirations; a degree provides broad career mobility, while certifications offer targeted skill enhancement. Practical experience, including a strong understanding of production processes and problem-solving, often holds equal or greater weight than theoretical knowledge alone. Geographic availability of programs varies, but many certification preparation courses and advanced training modules are available online, offering flexibility for working professionals.
Quality Control Supervisor Salary & Outlook
Compensation for a Quality Control Supervisor varies significantly, influenced by numerous factors beyond just base salary. Geographic location plays a crucial role; areas with a higher cost of living or strong manufacturing presence, such as California or the Northeast, typically offer higher wages to attract talent. Conversely, regions with lower living costs may see slightly reduced salary figures, though demand for skilled supervisors remains consistent.
Experience levels, specialized industry knowledge, and specific skill sets dramatically affect earning potential. A supervisor with expertise in advanced analytical techniques or regulatory compliance for specialized industries like pharmaceuticals or aerospace commands premium compensation. Total compensation often extends beyond the base salary, including performance bonuses, profit-sharing, and comprehensive benefits packages. These benefits typically cover health insurance, retirement contributions like 401(k) matching, and professional development allowances for certifications or advanced training.
Industry-specific compensation trends are also vital. Highly regulated industries or those with complex production processes often pay more due to the critical nature of quality assurance. Company size also matters; larger corporations with more extensive operations and greater revenue typically offer more competitive salaries and benefits than smaller firms. Remote work opportunities for Quality Control Supervisors are less common due to the hands-on nature of the role, but some companies may offer hybrid models, which can impact local salary expectations. While the figures provided are in USD, international markets present their own unique salary structures and economic factors, making direct comparisons challenging.
Salary by Experience Level
Level | US Median | US Average |
---|---|---|
Junior Quality Control Supervisor | $55k USD | $60k USD |
Quality Control Supervisor | $70k USD | $75k USD |
Senior Quality Control Supervisor | $85k USD | $90k USD |
Quality Control Manager | $100k USD | $105k USD |
Director of Quality Control | $128k USD | $135k USD |
Market Commentary
The job market for Quality Control Supervisors shows steady demand, driven by increasing regulatory scrutiny and the global emphasis on product safety and efficiency. This role is critical across various sectors, including manufacturing, food and beverage, pharmaceuticals, and automotive. Projections indicate a stable growth outlook, with the Bureau of Labor Statistics forecasting a 3-5% increase in related roles over the next decade. This growth is slightly below the average for all occupations, reflecting the established nature of quality assurance functions.
Emerging opportunities for Quality Control Supervisors often involve integrating new technologies. The adoption of automation, AI-driven inspection systems, and advanced data analytics is transforming quality control processes. Supervisors who can implement and manage these technologies, ensuring data integrity and process optimization, will find enhanced career prospects. The demand for meticulous quality assurance remains high, fueled by consumer expectations for defect-free products and stringent industry standards. Companies are increasingly investing in robust quality management systems to minimize recalls and enhance brand reputation.
Supply and demand dynamics for this role are generally balanced. While there is a consistent need for qualified professionals, the pool of candidates with the necessary blend of technical expertise, leadership skills, and regulatory knowledge can be limited. Future-proofing this career involves continuous learning in areas like Lean Six Sigma, ISO standards, and digital quality management tools. This role is relatively recession-resistant, as quality control remains essential even during economic downturns to maintain product standards and reduce waste. Geographic hotspots for Quality Control Supervisors align with major industrial and manufacturing centers, particularly in the Midwest and Southeast United States, where production facilities are concentrated.
Quality Control Supervisor Career Path
Career progression for a Quality Control Supervisor involves a blend of technical mastery, leadership development, and strategic thinking. Professionals typically begin by mastering operational aspects before moving into roles that require managing teams and processes. Advancement often distinguishes between individual contributor (IC) paths, focusing on deep technical expertise and process optimization, and management tracks, which emphasize team leadership and strategic oversight of quality systems.
Factors influencing advancement speed include consistent high performance, the ability to implement and improve quality systems, and effective team leadership. Specialization in areas such as Lean Six Sigma, specific industry regulations, or advanced analytical techniques can accelerate progression. Company size significantly impacts career paths; larger corporations may offer more structured advancement and specialized roles, while smaller companies might provide broader responsibilities and faster movement into management.
Lateral moves are common, allowing professionals to gain experience in different product lines, manufacturing processes, or regulatory environments. Continuous learning, including certifications in quality management (e.g., ASQ certifications), plays a crucial role. Networking within industry associations and mentorship from experienced quality leaders also provides significant advantages for career growth and identifying new opportunities.
Junior Quality Control Supervisor
0-2 yearsKey Focus Areas
Quality Control Supervisor
2-4 yearsKey Focus Areas
Senior Quality Control Supervisor
4-7 yearsKey Focus Areas
Quality Control Manager
7-12 yearsKey Focus Areas
Director of Quality Control
12+ yearsKey Focus Areas
Junior Quality Control Supervisor
0-2 yearsOversee specific segments of the quality control process, ensuring products meet established standards. Directly supervise a small team of QC technicians, providing immediate guidance and troubleshooting. Verify adherence to testing protocols and documentation requirements for assigned tasks. Work under close supervision from a Quality Control Supervisor.
Key Focus Areas
Develop a strong understanding of quality control principles, standard operating procedures (SOPs), and relevant industry regulations. Learn to operate and calibrate QC equipment accurately. Practice basic data analysis and reporting. Focus on attention to detail and adherence to protocols.
Quality Control Supervisor
2-4 yearsManage daily operations of a quality control section, supervising a team of QC technicians and junior supervisors. Ensure all testing and inspection activities comply with quality standards and regulatory requirements. Conduct investigations into non-conformance issues and implement corrective actions. Report on team performance and quality metrics to management.
Key Focus Areas
Master advanced statistical process control (SPC) techniques and root cause analysis. Enhance leadership skills, including conflict resolution and performance feedback. Develop strong communication skills for presenting data and process improvements. Begin identifying areas for process optimization.
Senior Quality Control Supervisor
4-7 yearsLead a larger or more complex quality control department, overseeing multiple teams and processes. Design and implement quality control procedures and standards to enhance product quality and efficiency. Play a key role in internal and external audits, ensuring compliance. Train and mentor new supervisors and contribute to strategic planning for the QC department.
Key Focus Areas
Cultivate strong analytical and problem-solving skills for complex quality challenges. Develop project management capabilities for implementing quality improvement initiatives. Focus on mentoring and developing junior supervisors and technicians. Gain deeper knowledge of regulatory compliance and audit preparation.
Quality Control Manager
7-12 yearsOversee the entire quality control function for a specific plant or business unit. Develop and implement quality management systems (QMS) and strategies aligned with organizational goals. Manage departmental budgets, resources, and personnel. Serve as a primary point of contact for regulatory agencies and lead major quality initiatives.
Key Focus Areas
Develop strategic planning and budget management skills for the quality department. Enhance cross-functional collaboration and stakeholder management abilities. Focus on continuous improvement methodologies (e.g., Lean Six Sigma) and their application. Cultivate strong leadership and team-building skills across multiple teams.
Director of Quality Control
12+ yearsProvide strategic direction and leadership for all quality control and assurance activities across the organization. Establish long-term quality objectives and policies that support overall business strategy. Represent the company on quality matters to executive leadership, boards, and external stakeholders. Build and lead a high-performing quality organization, fostering a culture of continuous improvement and excellence.
Key Focus Areas
Master executive-level communication and presentation skills. Develop expertise in global quality standards and regulatory landscapes. Focus on organizational leadership, change management, and talent development across the quality function. Drive innovation in quality assurance and control processes.
Job Application Toolkit
Ace your application with our purpose-built resources:
Quality Control Supervisor Resume Examples
Proven layouts and keywords hiring managers scan for.
View examplesQuality Control Supervisor Cover Letter Examples
Personalizable templates that showcase your impact.
View examplesTop Quality Control Supervisor Interview Questions
Practice with the questions asked most often.
View examplesQuality Control Supervisor Job Description Template
Ready-to-use JD for recruiters and hiring teams.
View examplesGlobal Quality Control Supervisor Opportunities
A Quality Control Supervisor ensures products meet quality standards across various industries globally. This role involves inspecting processes and outputs, often leading small teams. Global demand remains strong, particularly in manufacturing, pharmaceuticals, and food production, due to increasing regulatory scrutiny and supply chain complexity. International opportunities exist in developing economies expanding their industrial bases. Understanding international certifications like ISO 9001 is crucial for global mobility. Cultural differences in quality perception and regulatory frameworks directly impact this profession worldwide.
Global Salaries
Salaries for Quality Control Supervisors vary significantly by region and industry. In North America, particularly the US, a supervisor earns between $60,000 and $85,000 USD annually. Canadian supervisors typically see $55,000 to $75,000 CAD (approx. $40,000-$55,000 USD). These figures often include comprehensive benefits packages like health insurance and retirement plans. In Western Europe, such as Germany, salaries range from €45,000 to €65,000 (approx. $48,000-$70,000 USD). The UK offers £35,000 to £50,000 (approx. $44,000-$63,000 USD). These European salaries often come with strong social welfare benefits and generous vacation time.
Asia-Pacific markets present diverse ranges. In Australia, a supervisor earns around $70,000 to $95,000 AUD (approx. $47,000-$64,000 USD). Japan offers ¥5,000,000 to ¥7,500,000 (approx. $32,000-$48,000 USD), often with significant allowances. These Asian salaries reflect varying costs of living; purchasing power can differ greatly even with lower nominal figures. For instance, a salary in Japan might offer better purchasing power for local goods compared to a higher nominal salary in a more expensive US city. In Latin America, like Mexico, salaries are typically lower, around $18,000 to $30,000 USD, but cost of living is also considerably less. Tax implications and take-home pay differ by country; for example, European countries often have higher income taxes but provide more public services. International experience and specialized certifications, like Six Sigma or Lean Manufacturing, can significantly boost compensation across all regions.
Remote Work
The Quality Control Supervisor role has limited international remote work potential. This position fundamentally requires on-site presence to inspect products, monitor processes, and manage physical teams within manufacturing or production facilities. While some administrative or data analysis tasks might be performed remotely, the core responsibilities demand physical proximity to the production line. Therefore, true digital nomad opportunities are rare for this specific role.
Some companies with international operations might employ a supervisor in one country to oversee quality standards for a specific product line, coordinating with remote teams on data. However, this is typically an intra-company arrangement rather than a fully remote, borderless role. Salary expectations for such hybrid roles would likely align with the local market where the supervisor is physically based. Equipment needs include standard office setups and secure access to company systems, but the primary requirement remains access to the physical production environment.
Visa & Immigration
Quality Control Supervisors often qualify for skilled worker visas in many countries. Popular destinations like Canada, Australia, Germany, and the UK have specific immigration pathways for roles in manufacturing and industrial quality. Requirements typically include a relevant bachelor's degree or significant professional experience, often 3-5 years. Professional licensing is generally not required for this role, but industry-specific certifications (e.g., ASQ certifications) are beneficial. Education credential recognition is usually straightforward via evaluation services.
Visa application timelines vary, from a few months to over a year, depending on the country and specific program. For instance, Canada's Express Entry system can be relatively fast for eligible candidates. Language requirements, such as IELTS for English-speaking countries or Goethe-Institut exams for Germany, are often mandatory. Some countries, particularly those with labor shortages in specific manufacturing sectors, may offer fast-track programs. Pathways to permanent residency often exist after several years of continuous employment. Family visas for spouses and dependents are generally available, allowing them to accompany the primary visa holder.
2025 Market Reality for Quality Control Supervisors
Understanding the current market realities for Quality Control Supervisors is critical for career success. The landscape has significantly evolved from 2023 to 2025, driven by post-pandemic shifts in supply chains and the rapid integration of AI into manufacturing and production processes.
Broader economic factors, such as inflation and consumer demand fluctuations, directly influence production volumes and, consequently, the need for stringent quality oversight. Market realities also vary by experience level, with senior supervisors in higher demand, and by geographic region, as industrial hubs offer more opportunities. Company size also plays a role, with larger enterprises often having more structured quality departments. This analysis provides an honest assessment to help you navigate these complex dynamics.
Current Challenges
Quality Control Supervisors face increased competition, particularly from internal promotions and candidates with strong automation expertise. Economic uncertainty prompts companies to optimize existing teams rather than expand. Skill gaps exist where supervisors lack advanced data analytics or AI integration knowledge for quality systems. Remote work normalization expands the applicant pool, intensifying competition, especially for roles requiring on-site presence. Job searches can take longer as companies conduct more thorough, multi-stage interviews.
Growth Opportunities
Despite market shifts, strong demand exists for Quality Control Supervisors who specialize in advanced manufacturing, biopharmaceuticals, and high-tech electronics. These sectors prioritize precision and compliance, creating consistent opportunities. Emerging roles include 'AI Quality Lead' or 'Automated Inspection Supervisor,' focusing on managing AI-driven quality systems and optimizing data pipelines for quality insights.
Professionals can gain a competitive edge by pursuing certifications in AI for manufacturing, advanced data analytics, or specific industry compliance standards like ISO 13485 for medical devices. Underserved markets, particularly in regions experiencing industrial reshoring or expansion, often present better opportunities for qualified candidates. Supervisors with a proven track record in implementing lean manufacturing principles or reducing scrap rates using data-driven methods are highly sought after.
Market corrections can create opportunities for strategic career moves, as companies streamline operations and seek efficient quality leaders. Sectors like aerospace and defense, food safety, and renewable energy remain robust despite broader economic challenges, offering stable career paths. Investing in continuous learning, especially in AI-powered quality tools and automation, can significantly enhance long-term career prospects for Quality Control Supervisors.
Current Market Trends
Hiring for Quality Control Supervisors in 2025 shows a nuanced demand. While essential for compliance and product integrity, companies are increasingly seeking supervisors who can implement advanced quality management systems and integrate automation. The manufacturing, pharmaceutical, and food processing sectors maintain consistent demand, but roles in tech or consumer goods are becoming more specialized.
The integration of AI and machine learning tools in quality assurance is a major trend. Employers now prioritize candidates who understand how to leverage predictive analytics for defect prevention, automate inspection processes, and manage AI-driven quality monitoring systems. This shifts the focus from reactive problem-solving to proactive quality enhancement. Economic conditions, especially supply chain disruptions and inflation, pressure companies to reduce waste and improve efficiency, making robust quality control even more critical. However, some sectors experience hiring freezes or cautious expansion.
Employer requirements have evolved. Beyond traditional quality methodologies like Six Sigma or Lean, supervisors now need proficiency in data visualization, statistical process control software, and sometimes even basic programming for automation scripts. Salaries are generally stable but show upward movement for those with advanced tech skills or experience in highly regulated industries. Market saturation is low for highly skilled, tech-savvy supervisors, but moderate for those with only traditional experience. Geographic variations persist; areas with strong manufacturing bases, such as the Midwest or Southeast US, offer more opportunities, though remote supervision roles are rare.
Emerging Specializations
The landscape for Quality Control Supervisors is evolving rapidly, driven by advanced technologies and shifting industry paradigms. This evolution creates distinct new specialization opportunities beyond traditional quality assurance. Understanding these emerging areas allows professionals to strategically position themselves for future career advancement, commanding premium compensation and accelerated growth in 2025 and beyond.
Early positioning in these cutting-edge fields offers a significant advantage. As these specializations mature, they will become mainstream, creating a substantial number of job opportunities. However, those who develop expertise now will be at the forefront of innovation and demand. This forward-looking approach balances the risk of investing in new areas with the substantial rewards of being an early adopter.
While established quality control practices remain vital, focusing exclusively on them limits future potential. The true growth lies in integrating emerging technologies and methodologies into quality processes. This strategic shift ensures that Quality Control Supervisors are not merely overseeing current standards but are actively shaping the future of operational excellence and product integrity.
AI-Driven Predictive Quality Analyst
This specialization focuses on integrating artificial intelligence and machine learning models into quality control processes. AI-driven systems can predict defects, identify anomalies in real-time, and optimize inspection schedules with unprecedented accuracy. Quality Control Supervisors specializing in AI will manage the deployment, calibration, and continuous improvement of these intelligent systems, moving from reactive defect detection to proactive quality prediction.
Additive Manufacturing Quality Lead
This area involves overseeing quality in additive manufacturing environments, where products are built layer by layer. Unlike traditional manufacturing, 3D printing introduces unique quality challenges related to material properties, layer adhesion, and geometric precision. A supervisor in this niche ensures that printed parts meet stringent specifications, developing new inspection protocols and validation methods for complex geometries and novel materials.
Sustainable Product Quality Specialist
This specialization addresses the quality assurance of products and processes within a circular economy framework, focusing on sustainability, recyclability, and resource efficiency. Quality Control Supervisors in this role ensure that products not only meet performance standards but also adhere to environmental impact metrics throughout their lifecycle. They will develop and implement quality standards for material sourcing, waste reduction, and end-of-life product management.
Data Quality and Integrity Supervisor
This area focuses on ensuring the quality and integrity of data used in manufacturing and quality systems. As operations become more data-driven, the accuracy, consistency, and reliability of data are paramount for effective decision-making and automated processes. Supervisors in this role will establish data quality standards, implement validation procedures, and oversee data governance frameworks to prevent errors from impacting production quality.
Automation and Robotics Quality Assurance Lead
This emerging field involves managing quality control processes in highly automated and robotic manufacturing environments. As robots and automated systems perform more tasks, supervisors need to ensure the quality of robotic operations, calibrate automated inspection systems, and troubleshoot issues arising from human-robot collaboration. This role requires overseeing both product quality and the operational quality of the automation itself.
Pros & Cons of Being a Quality Control Supervisor
Understanding the full spectrum of a career, including both its advantages and challenges, is crucial for making informed decisions. Career experiences vary significantly based on company culture, industry sector, specific specialization, and individual preferences. The pros and cons of a role like Quality Control Supervisor may also shift at different career stages, from early responsibilities to senior leadership. What one person views as a benefit, another might see as a drawback, depending on their personal values and lifestyle priorities. This assessment provides an honest, balanced perspective to help set realistic expectations for this profession.
Pros
Strong job security and consistent demand across various manufacturing and production industries, as quality control is essential for product safety and regulatory compliance.
Opportunity to make a significant impact on product quality and customer satisfaction by ensuring adherence to standards and preventing defects.
Intellectual stimulation from problem-solving and root cause analysis, as supervisors investigate deviations and implement corrective actions to improve processes.
Leadership and team management experience is gained by overseeing quality control technicians and inspectors, developing their skills and coordinating daily operations.
Diverse work environments are possible, ranging from pharmaceuticals and food processing to automotive and electronics, offering varied technical challenges and learning opportunities.
Clear pathways for professional development through certifications in quality management (e.g., Six Sigma, Lean Manufacturing) can enhance expertise and career prospects.
A sense of accomplishment comes from ensuring products meet high standards, contributing directly to a company's reputation and bottom line.
Cons
High-pressure environment, especially when production targets conflict with quality standards, leading to difficult decisions and potential conflicts with other departments.
Repetitive tasks are common in ensuring compliance with established procedures, which can become monotonous over time for some individuals.
Limited career progression opportunities in some organizations exist, as the Quality Control Supervisor role often represents a senior technical position without a clear management track above it.
Exposure to hazardous materials or loud machinery is a possibility depending on the industry, which requires strict adherence to safety protocols and can pose health risks.
Requires continuous learning and adaptation to new technologies, regulations, and quality standards, which demands ongoing professional development outside of work hours.
Dealing with non-conforming products or processes can be frustrating and time-consuming, requiring detailed investigation and root cause analysis under tight deadlines.
Work-life balance can be challenging during peak production periods or when quality issues arise, often requiring extended hours to resolve problems and ensure product integrity.
Frequently Asked Questions
Quality Control Supervisors face distinct challenges balancing team leadership with strict adherence to quality standards. This section addresses key questions about entering this role, from required certifications and leadership skills to managing compliance and fostering a culture of continuous improvement.
What are the typical educational and experience requirements to become a Quality Control Supervisor?
Most Quality Control Supervisor roles require a bachelor's degree in a relevant field like engineering, science, or operations management. Many also seek candidates with certifications such as ASQ Certified Quality Engineer (CQE) or Certified Quality Manager (CQM). Significant prior experience in quality assurance or a related production environment, often 3-5 years, is also a common prerequisite for this leadership position.
How long does it typically take to transition into a Quality Control Supervisor role from an entry-level position?
Transitioning into a Quality Control Supervisor role usually takes 2-4 years if you already have a relevant degree and entry-level quality experience. This timeframe allows you to gain hands-on experience, understand quality systems, and develop leadership skills. Obtaining industry certifications like ASQ certifications can accelerate this process by demonstrating specialized knowledge and commitment to the field.
What are the salary expectations for a Quality Control Supervisor, and how do they vary?
Salaries for Quality Control Supervisors vary significantly based on industry, location, and company size. Entry-level supervisors might expect to earn between $60,000 and $80,000 annually. Experienced supervisors in high-demand industries or large corporations can command salaries ranging from $80,000 to over $110,000, often with additional benefits and bonuses tied to performance and quality metrics.
What is the typical work-life balance like for a Quality Control Supervisor?
The work-life balance for a Quality Control Supervisor can be variable, often depending on the industry and production schedules. While many roles are standard Monday-Friday, 9-to-5, some manufacturing or production environments may require evening, weekend, or on-call availability, especially during critical production phases or audits. The role demands attention to detail and problem-solving, which can sometimes extend beyond regular hours during peak periods.
Is the job outlook for Quality Control Supervisors stable, or is it a high-demand field?
Job security for Quality Control Supervisors is generally strong because quality assurance remains critical across all manufacturing and service industries. As companies increasingly focus on efficiency, customer satisfaction, and regulatory compliance, the demand for skilled quality professionals who can lead teams and implement robust systems grows. The field is less susceptible to automation than some production roles, as it requires human judgment and leadership.
What are the typical career advancement opportunities for a Quality Control Supervisor?
Career growth for Quality Control Supervisors can lead to various senior roles. Common paths include advancing to Quality Manager, Senior Quality Manager, or even Director of Quality. Some supervisors transition into roles in process improvement, such as Lean Six Sigma Black Belt, or move into operations management. Continuous learning and certifications in advanced quality methodologies can significantly enhance these opportunities.
What are the biggest challenges unique to a Quality Control Supervisor role?
A significant challenge for Quality Control Supervisors involves balancing production demands with strict quality standards, often requiring difficult decisions that impact timelines or costs. They also face the challenge of motivating and training their teams to adhere to protocols consistently, managing non-conformances, and implementing corrective actions effectively. Staying updated with evolving regulations and industry best practices is another continuous challenge.
Are there remote work opportunities for Quality Control Supervisors?
Remote work opportunities for Quality Control Supervisors are limited compared to many other roles, as the position often requires direct oversight of production processes, physical inspections, and hands-on team leadership. While some administrative tasks or data analysis can be done remotely, the core responsibilities typically necessitate an on-site presence. Hybrid models might exist where some planning or reporting can be done off-site, but frequent on-site presence is usually required.
Related Careers
Explore similar roles that might align with your interests and skills:
Quality Assurance Supervisor
A growing field with similar skill requirements and career progression opportunities.
Explore career guideQuality Control Coordinator
A growing field with similar skill requirements and career progression opportunities.
Explore career guideQuality Control Inspector
A growing field with similar skill requirements and career progression opportunities.
Explore career guideQuality Control Technician
A growing field with similar skill requirements and career progression opportunities.
Explore career guideQuality Supervisor
A growing field with similar skill requirements and career progression opportunities.
Explore career guideAssess your Quality Control Supervisor readiness
Understanding where you stand today is the first step toward your career goals. Our Career Coach helps identify skill gaps and create personalized plans.
Skills Gap Analysis
Get a detailed assessment of your current skills versus Quality Control Supervisor requirements. Our AI Career Coach identifies specific areas for improvement with personalized recommendations.
See your skills gapCareer Readiness Assessment
Evaluate your overall readiness for Quality Control Supervisor roles with our AI Career Coach. Receive personalized recommendations for education, projects, and experience to boost your competitiveness.
Assess your readinessSimple pricing, powerful features
Upgrade to Himalayas Plus and turbocharge your job search.
Himalayas
Himalayas Plus
Himalayas Max
Find your dream job
Sign up now and join over 100,000 remote workers who receive personalized job alerts, curated job matches, and more for free!
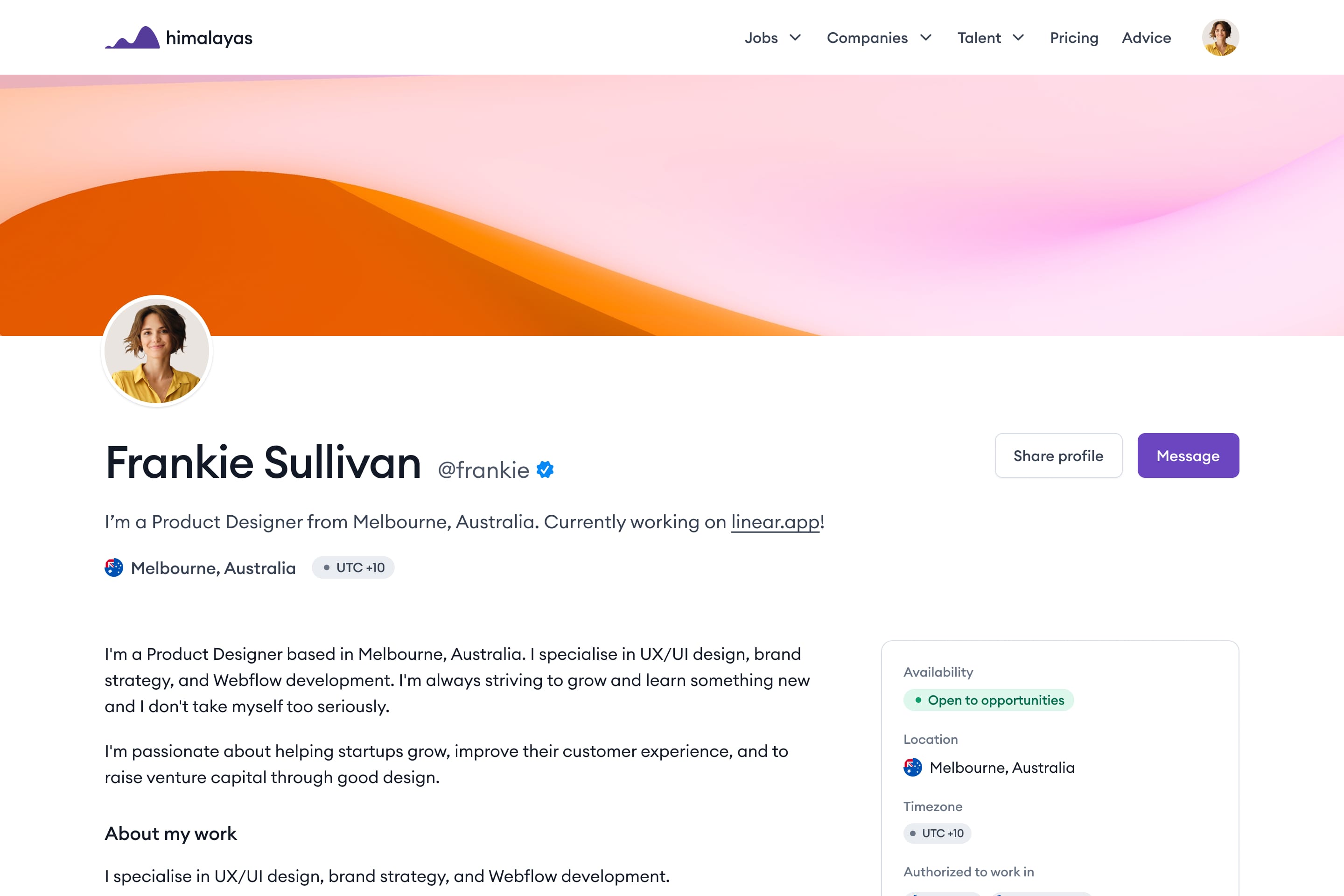