Complete Quality Control Coordinator Career Guide
Quality Control Coordinators are the vigilant guardians of product and service excellence, ensuring everything meets rigorous standards before reaching customers. They play a critical role in minimizing defects, enhancing customer satisfaction, and protecting a company's reputation by meticulously implementing and overseeing quality assurance protocols. This essential career path offers opportunities to drive continuous improvement in diverse industries, demanding keen attention to detail and strong organizational skills.
Key Facts & Statistics
Median Salary
Range: $40k - $90k+ USD
Growth Outlook
Annual Openings
Top Industries
Typical Education
High school diploma or equivalent; some positions may prefer an associate's or bachelor's degree in a related field
What is a Quality Control Coordinator?
A Quality Control Coordinator is a critical professional responsible for ensuring that products, materials, or services meet specified quality standards before they reach the customer. This role involves meticulous inspection, testing, and monitoring of processes and outputs at various stages, from raw material intake to finished product delivery. They act as the frontline guardians of quality, identifying defects, non-conformities, and deviations from established benchmarks.
Unlike a Quality Assurance (QA) Specialist who focuses on preventing defects by improving processes, or a Quality Engineer who designs and optimizes quality systems, the Quality Control Coordinator's primary focus is on the direct inspection and verification of quality in tangible items. They implement the quality plans developed by QA and engineering teams, providing immediate feedback on product integrity and ensuring that only compliant items proceed through the production pipeline or are shipped to clients. Their work directly impacts product reliability, customer satisfaction, and brand reputation.
What does a Quality Control Coordinator do?
Key Responsibilities
- Conduct thorough inspections of incoming raw materials, in-process products, and finished goods to ensure adherence to quality standards and specifications.
- Document inspection results, identifying and recording non-conformities, defects, and deviations from established protocols.
- Collaborate with production teams to address quality issues, providing immediate feedback on defects and offering suggestions for corrective actions.
- Maintain and calibrate quality control equipment, ensuring all tools provide accurate and reliable measurements for testing and inspection.
- Assist in the investigation of customer complaints related to product quality, tracing issues back to their root cause within the production process.
- Participate in the development and revision of standard operating procedures (SOPs) and quality control checklists to improve consistency and efficiency.
- Prepare detailed quality reports summarizing inspection data, trends, and corrective actions for management review.
Work Environment
A Quality Control Coordinator typically works in a manufacturing facility, laboratory, or warehouse setting. The environment can range from clean rooms to more industrial spaces, often requiring the use of personal protective equipment (PPE). They spend significant time on the production floor, interacting closely with machine operators and production supervisors. The work often involves a mix of standing, walking, and sitting at a desk for documentation. While primarily an individual contributor, the role demands strong collaboration with production, engineering, and supply chain teams. The pace is generally steady but can become fast-paced when addressing critical quality issues or during peak production periods. Work hours are usually standard business hours, but some roles may require shift work or occasional overtime to cover production cycles.
Tools & Technologies
Quality Control Coordinators regularly use a variety of precision measurement tools such as calipers, micrometers, gauges, and optical comparators to assess product dimensions and tolerances. They also operate specialized testing equipment specific to their industry, which might include tensile testers, hardness testers, or environmental chambers. Software for data collection and analysis, such as Microsoft Excel, Google Sheets, or dedicated Quality Management Systems (QMS) like MasterControl or ETQ Reliance, are essential for documenting findings and generating reports. They also utilize enterprise resource planning (ERP) systems like SAP or Oracle for tracking materials and production batches, ensuring traceability throughout the quality process.
Quality Control Coordinator Skills & Qualifications
A Quality Control Coordinator ensures products or services meet established quality standards and regulatory requirements. This role focuses on implementing and monitoring quality procedures, inspecting materials and processes, and documenting compliance. It is distinct from a Quality Assurance Manager, who designs broader quality systems, or a Quality Engineer, who focuses on process improvement and statistical analysis. The Coordinator's role is hands-on and operational, focused on the execution of quality protocols.
Requirements for a Quality Control Coordinator vary significantly based on the industry. In manufacturing, a strong understanding of production processes and specific industry standards (e.g., ISO, GMP, FDA regulations) is paramount. For service-based industries, the focus shifts to process adherence, customer feedback loops, and service level agreements. Larger companies often have more formalized requirements, including specific certifications, while smaller businesses might prioritize practical experience and adaptability.
Formal education provides a strong foundation, especially in science or engineering fields. However, practical experience within a relevant industry often carries equal or greater weight, particularly for entry-level and mid-career positions. Certifications like ASQ's Certified Quality Inspector (CQI) or Certified Quality Technician (CQT) significantly enhance a candidate's profile, demonstrating a commitment to quality principles. The skill landscape for this role is evolving, with increasing emphasis on data analysis for defect trending and digital tools for quality management systems.
Education Requirements
Technical Skills
- Quality Management Systems (e.g., ISO 9001, AS9100, IATF 16949) adherence and documentation
- Inspection tools and measurement equipment (calipers, micrometers, gauges, CMMs)
- Statistical Process Control (SPC) charting and basic data interpretation
- Non-conformance reporting and Corrective and Preventive Action (CAPA) processes
- Blueprint and technical drawing interpretation (GD&T preferred)
- Good Manufacturing Practices (GMP) and regulatory compliance (e.g., FDA, OSHA) where applicable
- Microsoft Office Suite (Excel for data tracking, Word for reports)
- Quality control software and databases for data entry and analysis
- Root cause analysis methodologies (e.g., 5 Whys, Fishbone diagrams)
- Sampling plans and inspection techniques (AQL, 100% inspection)
Soft Skills
- Attention to Detail: Crucial for identifying subtle defects, discrepancies, and non-conformances in products, processes, or documentation.
- Problem-Solving: Essential for investigating root causes of quality issues and proposing corrective actions to prevent recurrence.
- Organizational Skills: Important for managing inspection schedules, documentation, samples, and equipment efficiently.
- Communication Skills: Necessary for clearly reporting findings, explaining quality standards to production teams, and collaborating with various departments.
- Integrity and Objectivity: Vital for unbiased assessment of quality, ensuring standards are met without compromise or favoritism.
- Adaptability: Helps in adjusting to changing production schedules, new product specifications, or evolving quality standards and regulations.
- Documentation Accuracy: Critical for maintaining precise records of inspections, tests, and corrective actions, which are often required for compliance and audits.
- Time Management: Allows for efficient prioritization of tasks, ensuring inspections and reports are completed on schedule, especially in fast-paced environments.
How to Become a Quality Control Coordinator
Breaking into a Quality Control Coordinator role involves diverse pathways, from direct entry with relevant certifications to leveraging existing experience in related fields. The timeline varies significantly; a complete beginner might need 6-12 months to acquire foundational knowledge and certifications, while someone transitioning from a manufacturing or administrative role could secure a position within 3-6 months. Direct entry often suits those with technical associate's degrees or specific vocational training.
Many companies, especially in regulated industries like pharmaceuticals, food, or aerospace, prioritize candidates with a demonstrated understanding of quality systems and documentation. Smaller companies or startups might be more flexible, valuing strong organizational skills and attention to detail over formal qualifications. Networking within industry associations and attending local manufacturing or quality management events provides valuable insights into regional hiring trends and specific company needs.
A common misconception is that a science degree is always mandatory; while beneficial, many roles emphasize process adherence, data analysis, and documentation rather than deep scientific expertise. Focus on building a portfolio of practical skills in data management, standard operating procedure (SOP) development, and regulatory compliance. This practical experience, even from volunteer work or internships, often outweighs theoretical knowledge alone.
Step 1
Step 2
Step 3
Step 4
Step 5
Step 6
Step 7
Education & Training Needed to Become a Quality Control Coordinator
Becoming a Quality Control Coordinator often involves a blend of formal education and practical experience, with varied pathways leading to the role. Four-year degrees in fields like Chemistry, Biology, Engineering, or Quality Management provide a strong theoretical foundation, typically costing $40,000 to $100,000+ and requiring four years of full-time study. These programs are highly valued by larger corporations and industries with strict regulatory compliance, such as pharmaceuticals or aerospace, as they demonstrate a comprehensive understanding of scientific principles and quality systems.
Alternative learning paths, such as professional certifications and specialized online courses, offer more focused and time-efficient routes. Certifications like ASQ's Certified Quality Inspector (CQI) or Certified Quality Technician (CQT) can be completed in 6 to 18 months, with costs ranging from $500 to $5,000, including study materials and exam fees. These options are often preferred by individuals with some prior industry experience or those seeking to transition into quality control from related operational roles. Employers increasingly recognize these certifications as proof of specialized knowledge and commitment to quality standards.
Continuous learning remains critical for Quality Control Coordinators due to evolving industry regulations and technological advancements. Many professionals pursue advanced certifications or short courses in areas like Lean Six Sigma or ISO standards to enhance their skill sets and career prospects. While theoretical knowledge is important, practical experience through internships, entry-level quality assurance roles, or on-the-job training is equally vital. This hands-on experience allows coordinators to apply their knowledge in real-world scenarios, troubleshoot issues, and develop the critical thinking skills necessary for effective quality management. The specific educational needs for a Quality Control Coordinator can vary significantly based on the industry; for instance, a coordinator in food manufacturing may require different specialized training than one in medical devices.
Quality Control Coordinator Salary & Outlook
Compensation for a Quality Control Coordinator varies significantly based on several factors. Geographic location plays a major role, with higher salaries typically found in metropolitan areas and regions with a strong manufacturing or pharmaceutical presence due to higher cost of living and specialized industry demand. For example, a coordinator in California or New Jersey may earn considerably more than one in a lower cost-of-living state.
Years of experience, specific industry knowledge (e.g., FDA regulations in pharma, ISO standards in manufacturing), and specialized skill sets in areas like lean manufacturing or Six Sigma dramatically influence earning potential. Total compensation packages often extend beyond base salary to include performance bonuses, profit-sharing, and comprehensive benefits. These benefits typically cover health insurance, retirement contributions (401k matching), and sometimes professional development allowances for certifications.
Industry-specific trends, such as increased regulatory scrutiny or technological advancements in quality assurance, drive salary growth for skilled professionals. Negotiation leverage comes from demonstrating a proven track record of improving quality metrics, reducing defects, and implementing efficient control processes. Remote work for this role is less common due to the hands-on nature, but some administrative or documentation aspects might offer limited flexibility. International markets also present different salary scales, with the provided figures reflecting the U.S. Dollar context.
Salary by Experience Level
Level | US Median | US Average |
---|---|---|
Junior Quality Control Coordinator | $48k USD | $50k USD |
Quality Control Coordinator | $60k USD | $62k USD |
Senior Quality Control Coordinator | $75k USD | $78k USD |
Quality Control Supervisor | $85k USD | $88k USD |
Quality Control Manager | $102k USD | $105k USD |
Director of Quality Control | $140k USD | $145k USD |
Market Commentary
The job market for Quality Control Coordinators shows stable demand, primarily driven by the continuous need for product safety, regulatory compliance, and process efficiency across various industries. Manufacturing, pharmaceuticals, food and beverage, and medical devices are key sectors. The U.S. Bureau of Labor Statistics projects a moderate growth outlook for quality control inspectors and related roles, aligning with general industrial growth and increased emphasis on quality assurance.
Emerging opportunities for Quality Control Coordinators involve integrating new technologies like AI-powered inspection systems, automated quality checks, and advanced data analytics for predictive quality. Professionals skilled in these areas, along with traditional quality management systems, will find enhanced career prospects. The demand for meticulous record-keeping and adherence to evolving international standards also reinforces the role's importance.
Supply and demand dynamics are relatively balanced, but there is a growing need for candidates with strong analytical skills and a solid understanding of digital quality tools. Automation and AI are unlikely to fully replace this role; instead, they will transform it, shifting focus from manual inspection to overseeing automated processes and interpreting data. This makes the profession relatively resilient and less susceptible to economic downturns compared to some other industrial roles.
Geographic hotspots for Quality Control Coordinators remain concentrated in industrial hubs and areas with robust R&D and manufacturing sectors. Continuous learning in areas like statistical process control, quality management software, and industry-specific certifications is crucial for long-term career viability.
Quality Control Coordinator Career Path
Career progression for a Quality Control Coordinator often begins with foundational tasks and advances through increasing levels of responsibility, technical expertise, and leadership. Professionals can choose between an individual contributor (IC) track, focusing on deep specialization and technical mastery, or a management track, which involves leading teams and shaping departmental strategy.
Advancement speed depends on several factors, including individual performance, the specific industry (e.g., pharmaceutical, manufacturing, food safety), company size, and economic conditions. Larger organizations may offer more structured paths and specialized roles, while smaller companies might provide broader exposure to various quality functions. Lateral moves are common, allowing professionals to gain experience in different aspects of quality assurance, regulatory affairs, or even production operations.
Continuous learning, staying updated on industry regulations, and acquiring relevant certifications (e.g., Six Sigma, ASQ certifications) are crucial for progression. Networking within professional organizations and seeking mentorship from experienced quality professionals significantly aids career growth. Some professionals may pivot into roles like process improvement specialists, auditors, or consultants as their expertise deepens.
Junior Quality Control Coordinator
0-2 yearsKey Focus Areas
Quality Control Coordinator
2-4 yearsKey Focus Areas
Senior Quality Control Coordinator
4-7 yearsKey Focus Areas
Quality Control Supervisor
7-10 yearsKey Focus Areas
Quality Control Manager
10-15 yearsKey Focus Areas
Director of Quality Control
15+ yearsKey Focus Areas
Junior Quality Control Coordinator
0-2 yearsPerforms routine quality checks and inspections on raw materials, in-process goods, or finished products under direct supervision. Documents findings accurately and maintains detailed records. Identifies non-conforming products and escalates issues to senior staff. Works closely with team members to ensure compliance with established quality standards.
Key Focus Areas
Develop a strong understanding of quality control principles, standard operating procedures (SOPs), and basic laboratory or inspection techniques. Focus on accuracy, attention to detail, and efficient execution of assigned tasks. Build foundational knowledge of industry-specific regulations and documentation requirements.
Quality Control Coordinator
2-4 yearsConducts a variety of quality control tests and inspections with minimal supervision, interpreting results against specifications. Troubleshoots basic quality deviations and recommends initial corrective actions. Collaborates with production to resolve immediate quality concerns. Contributes to the review and update of quality documentation.
Key Focus Areas
Refine technical skills and expand knowledge of complex testing methodologies or inspection protocols. Develop problem-solving abilities for identifying root causes of quality issues. Improve communication skills for interacting with production teams and documenting corrective actions. Begin understanding data analysis for trend identification.
Senior Quality Control Coordinator
4-7 yearsExecutes complex quality control procedures, analyzes data to identify trends, and proposes solutions for recurring quality issues. Provides technical guidance and training to junior coordinators. Participates in investigations of significant quality deviations and non-conformances. Leads small projects aimed at improving testing efficiency or accuracy.
Key Focus Areas
Master advanced quality control techniques and statistical process control (SPC). Develop strong analytical skills for identifying patterns and recommending process improvements. Cultivate mentoring skills by guiding junior team members. Take initiative in optimizing testing procedures and contributing to quality system enhancements.
Quality Control Supervisor
7-10 yearsOversees the daily operations of a quality control team or specific testing area, ensuring adherence to schedules and quality standards. Trains and mentors QC coordinators, manages workload distribution, and conducts performance reviews. Investigates and resolves complex quality issues, implementing corrective and preventive actions. Reports on team performance and quality metrics to management.
Key Focus Areas
Develop leadership and team management skills, including scheduling, performance feedback, and conflict resolution. Enhance understanding of departmental budgeting and resource allocation. Focus on process optimization and implementing best practices within the QC lab or inspection area. Build cross-functional communication and collaboration skills.
Quality Control Manager
10-15 yearsManages the entire quality control department, setting objectives, developing strategies, and ensuring compliance with all relevant regulations and standards. Leads a team of supervisors and coordinators, overseeing hiring, training, and performance management. Drives continuous improvement projects and implements new QC technologies or methodologies. Responsible for departmental budget and resource planning.
Key Focus Areas
Cultivate strategic planning and departmental management capabilities, including budget management and technology adoption. Develop strong analytical skills for interpreting quality data and driving continuous improvement initiatives. Focus on regulatory compliance expertise and preparing for audits. Enhance stakeholder management and communication for executive reporting.
Director of Quality Control
15+ yearsProvides strategic direction and leadership for all quality control and assurance functions across the organization. Develops and implements the company's overarching quality strategy and policies. Ensures regulatory compliance and represents the company during external audits. Oversees quality system development, continuous improvement initiatives, and manages relationships with key regulatory bodies. A key member of the senior leadership team.
Key Focus Areas
Develop executive leadership skills, including organizational strategy, risk management, and long-range planning for quality systems. Focus on integrating quality control with overall business objectives and supply chain management. Cultivate strong negotiation and influencing skills for cross-departmental and external stakeholder engagement. Drive a culture of quality excellence across the organization.
Job Application Toolkit
Ace your application with our purpose-built resources:
Quality Control Coordinator Resume Examples
Proven layouts and keywords hiring managers scan for.
View examplesQuality Control Coordinator Cover Letter Examples
Personalizable templates that showcase your impact.
View examplesTop Quality Control Coordinator Interview Questions
Practice with the questions asked most often.
View examplesQuality Control Coordinator Job Description Template
Ready-to-use JD for recruiters and hiring teams.
View examplesGlobal Quality Control Coordinator Opportunities
A Quality Control Coordinator ensures product or service standards are met globally. This role involves implementing quality systems, conducting inspections, and analyzing data across international supply chains and manufacturing sites.
Global demand remains strong, particularly in industries like pharmaceuticals, food production, and automotive, as regulatory compliance tightens. International certifications such as ISO 9001 are highly valued, facilitating mobility.
Global Salaries
Global salaries for a Quality Control Coordinator vary significantly by region, industry, and experience. In North America, particularly the U.S. and Canada, salaries typically range from $50,000 to $75,000 USD annually. A Quality Control Coordinator in Germany or the UK can expect €40,000 to €60,000 (approximately $43,000-$65,000 USD), while in Japan, this role might command ¥4,500,000 to ¥7,000,000 (around $30,000-$47,000 USD).
When considering purchasing power, a lower nominal salary in a country with a lower cost of living, like Mexico (MXN 250,000-450,000 or $15,000-$27,000 USD), can offer similar or better purchasing power than a higher salary in a more expensive city. Salary structures also differ; European countries often include more robust benefits like extended paid vacation and universal healthcare, which can offset lower base pay.
Tax implications also vary widely; for example, Scandinavian countries have higher income taxes but offer extensive social welfare. Asia-Pacific regions, like Australia, see salaries from AUD 60,000 to AUD 85,000 ($40,000-$57,000 USD). Experience and specialized industry knowledge (e.g., medical devices) significantly impact compensation, making international experience valuable for career progression and higher pay scales.
Remote Work
The potential for a Quality Control Coordinator to work fully remotely is limited due to the hands-on nature of inspections and direct oversight of production processes. However, hybrid models are becoming more common, allowing for remote data analysis, documentation, and virtual team meetings.
Legal and tax implications for international remote work are complex, requiring careful consideration of host country regulations and permanent establishment risks. Companies often prefer to hire locally for roles requiring on-site presence, even if some tasks can be done remotely. Digital nomad opportunities exist for roles focused purely on compliance documentation or supplier quality audits that can be conducted virtually.
Some global companies with distributed manufacturing or supply chains may offer limited international remote positions for experienced coordinators managing specific aspects of quality control remotely. Salary expectations for international remote work might be adjusted based on the employee's location and cost of living rather than the employer's headquarters.
Visa & Immigration
Quality Control Coordinators often qualify for skilled worker visas in many countries, particularly those with strong manufacturing or regulated industries. Common destinations include Germany, Canada, Australia, and the UK, which have specific points-based or employer-sponsored visa systems.
Requirements typically include relevant educational qualifications, such as a bachelor's degree in engineering or a related science, and several years of experience. Professional certifications like ASQ (American Society for Quality) are highly beneficial for credential recognition. The typical visa timeline can range from 3 to 12 months, depending on the country and visa type.
Many countries offer pathways to permanent residency for skilled workers after several years of employment. Language proficiency, often demonstrated through tests like IELTS or Goethe-Zertifikat, is a common requirement, especially for non-English speaking countries. Some countries may also offer intra-company transfer visas for employees moving within a multinational corporation.
2025 Market Reality for Quality Control Coordinators
Understanding the current job market for Quality Control Coordinators is crucial for effective career planning. Market conditions have evolved significantly since 2023, influenced by post-pandemic shifts in supply chains and the rapid integration of AI across industries.
Broader economic factors like inflation and consumer demand directly impact production volumes, thereby affecting the need for quality oversight. Market realities for Quality Control Coordinators vary by experience level, with entry-level roles facing more competition than specialized senior positions. Geographic region and company size also play a role, as larger manufacturers or companies in regulated sectors often have more structured quality departments. This analysis provides an honest assessment of current hiring conditions.
Current Challenges
Quality Control Coordinator roles face increased competition, particularly at entry levels, as companies seek more experienced candidates. Economic uncertainty prompts leaner team structures, reducing the number of available positions. Automation and AI tools also shift expectations, requiring coordinators to manage systems rather than just manual checks, creating a skill mismatch for some.
Remote work normalization means a broader pool of applicants for each opening. Companies now expect coordinators to handle more complex data analysis and integrate AI-driven insights, which presents a challenge for those without updated analytical skills.
Growth Opportunities
Despite market shifts, strong demand persists for Quality Control Coordinators with expertise in data analytics, automation, and regulatory compliance. Emerging opportunities lie in roles that involve managing AI-powered quality systems, validating machine learning models for production defects, and ensuring data integrity in automated environments.
Professionals can gain a competitive advantage by acquiring certifications in Six Sigma, Lean Manufacturing, or specific quality management software. Developing skills in Python or R for data analysis, and understanding industrial IoT applications, also provides significant leverage. Underserved markets include smaller manufacturing firms adopting new technologies, or specialized niches like biotech startups that require rigorous quality protocols from inception.
Strategic career moves might involve transitioning from traditional manufacturing to sectors like medical devices or advanced materials, where quality control remains paramount and often more complex. Companies in these areas are actively seeking coordinators who can adapt to evolving standards and integrate new technologies. Investing in continuous learning, particularly in AI-driven quality assurance or process optimization, positions candidates for future growth and leadership within quality departments.
Current Market Trends
Hiring for Quality Control Coordinators remains steady in highly regulated industries like pharmaceuticals, food production, and aerospace, driven by strict compliance needs. However, other sectors show a shift towards automation and AI-driven quality assurance, impacting the demand for purely manual oversight roles. Companies increasingly seek coordinators who can manage automated systems and interpret data, rather than just perform checks.
The integration of generative AI and advanced analytics is redefining the Quality Control Coordinator role. Employers now prioritize candidates who understand data integrity, can troubleshoot automated QA processes, and contribute to predictive quality models. This means a move away from routine inspection tasks towards more analytical and oversight responsibilities. Layoffs in broader tech sectors have not severely impacted this role directly, but the emphasis on efficiency means fewer, more skilled coordinators are hired.
Salary trends for Quality Control Coordinators are stable but show modest growth for those with strong data analysis and automation experience. Market saturation exists at the entry level, where competition is high for roles requiring basic inspection skills. Geographic variations are notable: manufacturing hubs in the Midwest and South continue to have consistent demand, while roles in technology-centric regions often require a stronger emphasis on software quality assurance. Remote work opportunities are growing but are often reserved for senior coordinators capable of managing distributed teams and advanced systems.
Emerging Specializations
The field of quality control is undergoing a significant transformation, driven by advancements in automation, data analytics, and artificial intelligence. These technological shifts are creating entirely new specialization opportunities for Quality Control Coordinators, moving beyond traditional inspection roles to more strategic, data-driven functions. Professionals who proactively position themselves in these emerging areas will find enhanced career trajectories and often command premium compensation in 2025 and beyond.
Early positioning in these cutting-edge specializations provides a distinct advantage, allowing professionals to become pioneers and subject matter experts in rapidly evolving niches. While established quality control practices remain essential, focusing on emerging areas offers a pathway to leadership roles and significant influence within an organization's operational excellence initiatives. The balance involves understanding foundational quality principles while actively integrating new technologies and methodologies.
Many emerging areas, particularly those involving AI and advanced analytics, are currently in a growth phase, expected to become mainstream and generate substantial job opportunities within the next three to five years. Pursuing these specializations involves a calculated risk, as some technologies may evolve differently than anticipated. However, the potential for high reward, including increased demand and specialized compensation, often outweighs these considerations for ambitious professionals seeking to shape the future of quality.
AI-Driven Quality Assurance Specialist
This specialization focuses on integrating and overseeing AI-driven quality inspection systems. Quality Control Coordinators in this role manage the calibration, training, and performance monitoring of AI models used for defect detection, predictive maintenance, and process optimization. They ensure the AI systems accurately identify quality issues and continuously improve their detection capabilities, moving quality control from reactive to proactive.
Sustainable Manufacturing Quality Coordinator
This area involves developing and implementing quality control protocols for products and processes that incorporate sustainable materials or energy-efficient designs. Professionals ensure compliance with environmental regulations and green manufacturing standards, verifying that products meet both performance and ecological criteria. They track the environmental impact of material choices and production methods, ensuring sustainability claims are verifiable.
IoT Data Quality Analyst
With the rise of IoT devices in manufacturing, this specialization focuses on collecting, analyzing, and acting upon real-time quality data from connected sensors and equipment. Quality Control Coordinators in this role manage IoT data streams to monitor process parameters, identify anomalies, and trigger immediate corrective actions. They ensure data integrity and leverage insights for continuous process improvement and defect prevention.
Blockchain Traceability Quality Specialist
This specialization applies blockchain technology to create immutable and transparent supply chain quality records. Quality Control Coordinators in this field verify product provenance, track material quality from source to consumer, and ensure the integrity of quality certifications. They manage the secure recording of quality checkpoints on a distributed ledger, enhancing trust and traceability throughout the product lifecycle.
Robotics and Automation Quality Coordinator
This role focuses on ensuring the quality and reliability of products and systems designed for human-machine interaction, particularly in robotics and advanced automation. Quality Control Coordinators evaluate the user experience, safety protocols, and functional performance of automated systems. They ensure seamless integration and reliable operation, minimizing errors and enhancing overall system efficiency.
Pros & Cons of Being a Quality Control Coordinator
Understanding both the advantages and challenges of a career is crucial before making a commitment. This assessment provides a realistic overview of the Quality Control Coordinator role, helping you set appropriate expectations. Career experiences can vary significantly based on company culture, industry sector, and your specific responsibilities within the quality department. What one person considers a benefit, another might see as a drawback, depending on their personal values and work style. Moreover, the pros and cons may shift at different stages of your career, from an entry-level position to a more senior coordination role. This honest evaluation aims to prepare you for the real-world aspects of this profession.
Pros
Strong job stability across various industries, as demand for quality assurance remains constant in manufacturing, pharmaceuticals, food production, and many other sectors.
Direct impact on product quality and customer satisfaction, providing a tangible sense of accomplishment by ensuring that goods meet high standards before reaching consumers.
Develops meticulous attention to detail and analytical skills, which are highly transferable and valued in many other professional roles.
Opportunities to work with diverse products and processes, offering exposure to different aspects of an industry's operations and supply chain.
Generally offers predictable work schedules, as quality control tasks are often integrated into standard production hours, leading to a stable work-life balance.
Provides a clear understanding of production workflows and compliance requirements, building a foundational knowledge crucial for broader operational roles.
Entry-level positions are often accessible with vocational training or an associate's degree, making it a viable career path without extensive higher education.
Cons
Repetitive tasks can lead to monotony, as many daily duties involve checking the same specifications or performing similar inspections repeatedly.
High pressure to identify defects accurately, as missing even minor flaws can lead to significant financial losses or safety issues for the company.
Limited direct career progression within the Quality Control Coordinator role itself, often requiring a move into management or a specialized quality assurance position for advancement.
Exposure to potentially hazardous environments or materials depending on the industry, which may require strict adherence to safety protocols and the use of personal protective equipment.
Dealing with resistance from production teams, as quality checks can sometimes be perceived as slowing down processes or critiquing their work, leading to interpersonal challenges.
Requires meticulous attention to detail for extended periods, which can be mentally fatiguing and demands sustained focus throughout the workday.
Can be blamed for issues outside their control, especially if a defect is discovered later in the production chain, leading to stress and accountability pressures.
Frequently Asked Questions
Quality Control Coordinators face distinct challenges balancing meticulous attention to detail with effective communication across teams. This section addresses key questions about entering this role, from mastering quality standards to navigating cross-departmental responsibilities and ensuring product integrity.
What are the typical educational and experience requirements to become a Quality Control Coordinator?
Entry into a Quality Control Coordinator role often requires a high school diploma or equivalent, but many employers prefer an associate's or bachelor's degree in a relevant field like science, engineering, or business administration. Experience in manufacturing, production, or a related quality assurance role is also highly valued. Certifications such as ASQ Certified Quality Inspector (CQI) or Certified Quality Technician (CQT) can significantly boost your qualifications and demonstrate a commitment to quality principles.
How long does it take to become job-ready for a Quality Control Coordinator position, especially if I'm new to the field?
The timeline to become job-ready as a Quality Control Coordinator varies based on your existing background. If you have a relevant degree and some foundational experience, you could transition into an entry-level role within a few months. For those starting from scratch, pursuing an associate's degree or relevant certifications might take 1-2 years. Gaining practical experience through internships or entry-level production roles can also accelerate your readiness.
What are the salary expectations for a Quality Control Coordinator, and how do they grow with experience?
Salaries for Quality Control Coordinators vary by industry, location, and experience, but typically range from $40,000 to $65,000 annually. Entry-level positions might start closer to $35,000, while those with several years of experience, specialized knowledge, or certifications can earn upwards of $70,000. Larger companies and industries with stringent quality requirements often offer higher compensation.
What is the typical work-life balance like for a Quality Control Coordinator?
The work-life balance for a Quality Control Coordinator can be quite stable, often adhering to standard business hours. However, roles in manufacturing or production environments might involve occasional evening or weekend shifts, especially when addressing urgent quality issues or during peak production times. The role demands precision and attention to detail, which can be mentally engaging, but typically does not require extensive overtime.
Is the Quality Control Coordinator role in high demand, and what are the job security prospects?
The job market for Quality Control Coordinators is generally stable and growing, driven by increasing regulatory demands and a global focus on product quality and safety. Industries such as manufacturing, pharmaceuticals, food and beverage, and automotive consistently need skilled quality professionals. Automation might change some tasks, but the need for human oversight and problem-solving in quality control remains strong, ensuring good job security.
What are the typical career advancement opportunities for a Quality Control Coordinator?
Career growth for a Quality Control Coordinator can lead to various advanced roles. You might advance to Quality Assurance Specialist, Quality Engineer, or Quality Manager positions, which involve more strategic planning, process improvement, and team leadership. Specializing in areas like Six Sigma or Lean Manufacturing can also open doors to continuous improvement roles. Many also transition into compliance or regulatory affairs.
Can Quality Control Coordinators work remotely, or is it primarily an on-site role?
While some administrative aspects of the Quality Control Coordinator role might be performed remotely, the core responsibilities often require a physical presence. You need to be on-site to inspect products, monitor production lines, and interact directly with manufacturing teams. Hybrid models are becoming more common, allowing for some remote work for documentation and analysis, but full-time remote opportunities are less frequent due to the hands-on nature of the job.
What are the biggest challenges or common pain points for someone in a Quality Control Coordinator role?
A key challenge for Quality Control Coordinators involves balancing strict adherence to quality standards with production schedules and cost considerations. You must effectively communicate deficiencies without disrupting operations and often need to mediate between production and management. Adapting to new technologies, maintaining up-to-date knowledge of industry regulations, and ensuring consistent application of quality processes across diverse teams are also significant aspects of the role.
Related Careers
Explore similar roles that might align with your interests and skills:
Quality Assurance Coordinator
A growing field with similar skill requirements and career progression opportunities.
Explore career guideQuality Control
A growing field with similar skill requirements and career progression opportunities.
Explore career guideQuality Control Manager
A growing field with similar skill requirements and career progression opportunities.
Explore career guideQuality Control Specialist
A growing field with similar skill requirements and career progression opportunities.
Explore career guideQuality Coordinator
A growing field with similar skill requirements and career progression opportunities.
Explore career guideAssess your Quality Control Coordinator readiness
Understanding where you stand today is the first step toward your career goals. Our Career Coach helps identify skill gaps and create personalized plans.
Skills Gap Analysis
Get a detailed assessment of your current skills versus Quality Control Coordinator requirements. Our AI Career Coach identifies specific areas for improvement with personalized recommendations.
See your skills gapCareer Readiness Assessment
Evaluate your overall readiness for Quality Control Coordinator roles with our AI Career Coach. Receive personalized recommendations for education, projects, and experience to boost your competitiveness.
Assess your readinessSimple pricing, powerful features
Upgrade to Himalayas Plus and turbocharge your job search.
Himalayas
Himalayas Plus
Himalayas Max
Find your dream job
Sign up now and join over 100,000 remote workers who receive personalized job alerts, curated job matches, and more for free!
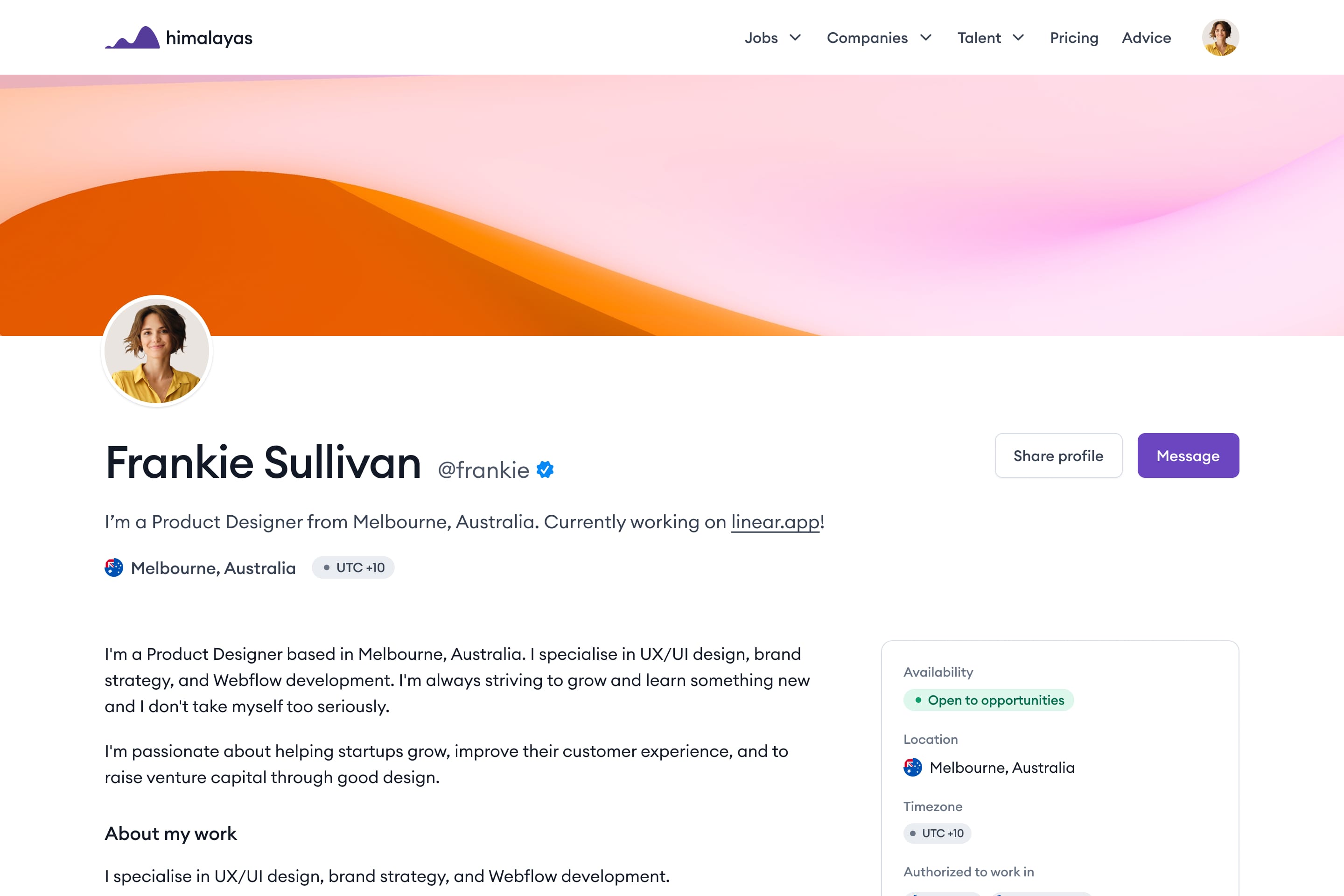