Complete Quality Control Career Guide
Quality Control professionals ensure products and services meet rigorous standards, acting as the guardians of brand reputation and customer satisfaction. They identify defects, implement corrective actions, and drive continuous improvement, playing a critical role in manufacturing, healthcare, and technology. This career offers a path to impact product excellence directly, blending analytical skills with hands-on problem-solving.
Key Facts & Statistics
Median Salary
$47,600 USD
(U.S. national median, May 2023 BLS)
Range: $30k - $75k+ USD
Growth Outlook
1%
slower than average
Annual Openings
≈69k
openings annually
Top Industries
Typical Education
High school diploma or equivalent, often with on-the-job training or an associate's degree; certifications like ASQ are highly valued.
What is a Quality Control?
A Quality Control professional is a guardian of product excellence within manufacturing and production environments. They systematically inspect, test, and monitor products at various stages of their lifecycle to ensure they meet predefined quality standards, specifications, and regulatory requirements. Their primary purpose is to identify defects, non-conformities, and deviations before products reach the customer, thereby minimizing waste, reducing rework, and protecting brand reputation.
This role differs significantly from Quality Assurance (QA) and Quality Engineering. While QA focuses on the 'process' – establishing and maintaining systems to prevent defects – Quality Control focuses on the 'product' itself, performing hands-on inspections and tests. Quality Engineers, on the other hand, design and optimize the quality systems and processes, often working on continuous improvement initiatives. The Quality Control specialist provides the critical feedback loop from the actual product to these broader quality initiatives.
What does a Quality Control do?
Key Responsibilities
- Inspect incoming raw materials and components to ensure they meet specified quality standards before production begins.
- Perform in-process checks at various stages of manufacturing to identify and address deviations from quality benchmarks.
- Conduct final product inspections, including visual checks and functional tests, to verify compliance with design specifications and customer expectations.
- Document inspection results, defects, and non-conformances accurately, maintaining detailed records for traceability and analysis.
- Collaborate with production teams to communicate quality issues and recommend corrective actions to prevent recurrence.
- Calibrate and maintain inspection equipment, ensuring all tools provide accurate measurements and reliable data.
- Assist in the investigation of customer complaints related to product quality, contributing to root cause analysis and resolution.
Work Environment
Quality Control professionals typically work in manufacturing plants, laboratories, or production facilities. Their environment can range from clean, controlled spaces to noisier factory floors, often requiring personal protective equipment (PPE).
The role involves a mix of independent inspection tasks and collaborative problem-solving with production, engineering, and supply chain teams. The pace is often steady but can become fast-paced during critical production runs or when addressing urgent quality issues. Most positions are on-site, with standard shifts, though some industries may require evening or weekend work to align with production schedules. Remote work is rare given the hands-on nature of inspections.
Tools & Technologies
Quality Control professionals regularly use a variety of tools to ensure product integrity. They operate precision measuring instruments like calipers, micrometers, gauges, and coordinate measuring machines (CMMs) for dimensional verification. They also utilize visual inspection aids such as microscopes and borescopes for detailed examination.
For data management and analysis, they often work with Statistical Process Control (SPC) software, Enterprise Resource Planning (ERP) systems like SAP or Oracle, and quality management software (QMS) such as MasterControl or ETQ Reliance. Basic office productivity suites, including Microsoft Excel and Word, are essential for documentation and reporting. Depending on the industry, they might also use specialized testing equipment for material properties, electrical performance, or chemical composition.
Quality Control Skills & Qualifications
Quality Control (QC) professionals ensure products or services meet established standards and specifications. Their work is critical for maintaining brand reputation and customer satisfaction. The qualification landscape for this role varies significantly based on the industry, company size, and the complexity of the products being inspected. For instance, QC in pharmaceuticals demands rigorous adherence to regulatory guidelines and specialized certifications, while QC in manufacturing might focus more on statistical process control and lean methodologies.
Entry-level QC positions often prioritize practical experience and a foundational understanding of quality principles. A two-year associate's degree or a relevant vocational certification can be sufficient for many roles. However, senior QC roles, particularly in highly regulated industries or those involving advanced analytics, typically require a bachelor's degree in a scientific or engineering discipline. Companies increasingly value candidates who can demonstrate hands-on experience with quality management systems and data analysis tools, sometimes even over a traditional four-year degree.
Certifications from organizations like the American Society for Quality (ASQ), such as the Certified Quality Inspector (CQI) or Certified Quality Technician (CQT), significantly enhance a candidate's marketability. These certifications validate a specific body of knowledge and practical skills. The skill landscape for QC is evolving with the adoption of automation, AI, and advanced data analytics, requiring professionals to develop competencies in interpreting complex data and utilizing digital inspection tools. Understanding the balance between broad quality assurance principles and deep expertise in specific inspection techniques is key for career progression in this field.
Education Requirements
Technical Skills
- Quality Management System (QMS) adherence (e.g., ISO 9001, AS9100, ISO 13485)
- Statistical Process Control (SPC) and data analysis using tools like Minitab or Excel
- Interpretation of blueprints, schematics, and technical drawings (GD&T)
- Proficiency with measurement tools (calipers, micrometers, gauges, CMM)
- Non-destructive testing (NDT) methods (e.g., visual inspection, dye penetrant, ultrasonic) specific to industry
- Root cause analysis methodologies (e.g., 5 Whys, Fishbone diagrams)
- Knowledge of industry-specific regulations and standards (e.g., FDA, GMP, IPC)
- Calibration procedures and equipment maintenance
- Computer literacy for data entry, reporting, and using QMS software
- Basic understanding of manufacturing processes relevant to the product
Soft Skills
- Attention to Detail: Essential for identifying minute defects or deviations from specifications, which can significantly impact product quality and safety.
- Problem-Solving: Important for analyzing root causes of defects and contributing to corrective and preventive actions, improving overall quality processes.
- Communication Skills: Necessary for clearly documenting findings, explaining non-conformances to production teams, and collaborating on quality improvements.
- Integrity: Critical for maintaining objectivity and upholding quality standards without compromise, even under pressure.
- Organization Skills: Key for managing inspection schedules, maintaining detailed records, and ensuring traceability of inspected products.
- Adaptability: Important for adjusting to new product designs, changing quality standards, and evolving inspection technologies.
- Teamwork: Essential for collaborating effectively with production, engineering, and supply chain teams to resolve quality issues and implement improvements.
How to Become a Quality Control
Entering the Quality Control field offers diverse pathways, ranging from formal education to on-the-job training and certifications. A complete beginner might spend 6-12 months acquiring foundational knowledge and certifications, while someone transitioning from a related field like manufacturing or lab work could find a role within 3-6 months. Traditional routes often involve an associate's or bachelor's degree in a science or engineering discipline, but many companies prioritize practical experience and specific QC certifications over a four-year degree, especially for entry-level technician roles.
Entry strategies can vary significantly by industry and company size. For example, highly regulated industries like pharmaceuticals or aerospace often demand stricter adherence to formal qualifications and specific industry standards, while smaller manufacturing operations might be more open to candidates with strong problem-solving skills and a willingness to learn. Geographic location also plays a role; major industrial hubs will have more opportunities than smaller markets. Misconceptions exist that QC is merely about 'finding mistakes'; instead, it involves meticulous process adherence, data analysis, and contributing to continuous improvement.
Networking within industry associations and seeking mentorship from experienced QC professionals can significantly accelerate a job search. The hiring landscape values candidates who can demonstrate attention to detail, analytical thinking, and a commitment to quality standards. Overcoming entry barriers often involves highlighting transferable skills from previous roles, such as process adherence, documentation, and critical observation, even if direct QC experience is limited.
Step 1
Step 2
Step 3
Step 4
Step 5
Step 6
Step 7
Education & Training Needed to Become a Quality Control
A career in Quality Control (QC) requires a blend of theoretical understanding and practical application. Educational pathways range from vocational training and certifications to associate's and bachelor's degrees. Formal two-year associate's degrees in quality assurance or manufacturing technology often cost $5,000-$20,000 and provide a strong foundational understanding of QC principles, statistical process control, and inspection methods. Four-year bachelor's degrees in engineering, industrial technology, or supply chain management, costing $40,000-$100,000+, offer a broader theoretical base and are often preferred for supervisory or more technical QC roles, requiring about four years of study.
Alternatively, professional certifications are highly valued in the QC field and often carry significant weight with employers. Organizations like the American Society for Quality (ASQ) offer certifications such as Certified Quality Inspector (CQI) or Certified Quality Technician (CQT). These certifications typically involve self-study or short courses (6-18 months) and exam fees ranging from $200-$600, with preparatory courses adding $500-$2,000. While not a substitute for a degree in all cases, they demonstrate specialized knowledge and a commitment to professional standards. Many employers recognize these certifications as proof of competency, particularly for entry-level and mid-level QC positions.
Continuous learning is crucial in Quality Control due to evolving industry standards, technologies, and methodologies. Specialized workshops on Lean Six Sigma, ISO standards, or specific inspection techniques further enhance a professional's skill set. These shorter courses can cost from a few hundred to several thousand dollars. The optimal educational investment depends on the target industry (e.g., pharmaceuticals, manufacturing, software), the specific QC specialization (e.g., product testing, process auditing), and career aspirations. Practical experience gained through internships or on-the-job training complements formal education, as hands-on skills in using measurement tools and interpreting data are paramount for success in Quality Control.
Quality Control Salary & Outlook
Compensation for Quality Control (QC) professionals depends on several factors beyond just base salary. Geographic location significantly impacts earnings, with higher salaries in major metropolitan areas or regions with a strong manufacturing or pharmaceutical presence due to higher cost of living and specialized industry demand. For example, salaries in California or the Northeast often exceed those in the Midwest.
Years of experience, specific industry knowledge, and the complexity of products or processes being controlled drive salary variations. Specialization in areas like analytical chemistry, microbiology, or specific regulatory frameworks (e.g., FDA, ISO) commands higher pay. Total compensation packages frequently include performance bonuses, profit-sharing, or stock options, particularly at senior and management levels. Comprehensive benefits, such as health insurance, retirement contributions (401k matching), and professional development allowances, add substantial value.
Industry-specific trends also influence salary growth. For instance, the highly regulated pharmaceutical and biotech sectors typically offer higher compensation than general manufacturing due to the stringent quality requirements and critical nature of their products. Remote work options, while less common for hands-on QC roles, can impact salary ranges by allowing companies to source talent from lower-cost regions, potentially influencing geographic arbitrage. Salary negotiation leverage comes from demonstrating a proven track record of reducing defects, improving efficiency, and ensuring regulatory compliance. While specific figures are provided in USD, international markets will have their own distinct salary structures based on local economic conditions and industry maturity.
Salary by Experience Level
Level | US Median | US Average |
---|---|---|
Junior Quality Control Specialist | $50k USD | $55k USD |
Quality Control Specialist | $65k USD | $70k USD |
Senior Quality Control Specialist | $85k USD | $88k USD |
Quality Control Supervisor | $100k USD | $105k USD |
Quality Control Manager | $120k USD | $125k USD |
Director of Quality Control | $155k USD | $165k USD |
Market Commentary
The job market for Quality Control professionals remains stable, driven by an enduring need for product safety, reliability, and regulatory compliance across various industries. Manufacturing, pharmaceuticals, biotechnology, food and beverage, and automotive sectors consistently demand skilled QC personnel. Current trends show increased adoption of automation and data analytics in QC processes, shifting the role from manual inspection to more analytical and process-improvement-focused tasks.
The growth outlook for Quality Control roles is projected to be steady, aligning with the overall growth in manufacturing and R&D. While specific percentages vary by industry, the Bureau of Labor Statistics indicates consistent demand for quality assurance professionals. Emerging opportunities lie in specializations related to advanced manufacturing technologies, such as additive manufacturing (3D printing), and in roles focused on data integrity and validation for automated systems. The supply of qualified candidates is generally balanced with demand, though highly specialized roles, particularly in biotech or advanced materials, may experience shortages.
Future-proofing this career involves continuous learning in areas like Lean Six Sigma, statistical process control (SPC), and quality management systems (QMS) software. AI and machine learning tools are increasingly used for predictive quality and defect detection, requiring QC professionals to adapt and manage these technologies rather than being replaced by them. This profession is relatively recession-resistant, as quality standards and regulatory requirements persist regardless of economic cycles. Geographic hotspots for QC roles include established industrial hubs and emerging biotech clusters, with remote work being less prevalent for roles requiring physical presence in labs or on production floors.
Quality Control Career Path
Career progression for Quality Control professionals typically involves a clear path from hands-on inspection and testing to strategic leadership in quality assurance. Advancement often hinges on a blend of meticulous attention to detail, strong analytical skills, and a deep understanding of industry-specific regulations and standards. Professionals can pursue either an individual contributor (IC) track, becoming highly specialized experts, or a management track, leading teams and shaping organizational quality policies.
Advancement speed depends on several factors, including sustained high performance, the ability to implement process improvements, and a proactive approach to learning new technologies or methodologies. Company size and industry also play a significant role; larger corporations may offer more structured paths and diverse opportunities, while smaller firms might provide broader exposure to various quality aspects. Specialization in areas like Six Sigma, Lean manufacturing, or specific regulatory compliance can accelerate progression, opening doors to more complex and impactful roles.
Lateral movement opportunities within quality control are common, allowing professionals to transition between different product lines, manufacturing processes, or even into related fields like regulatory affairs or process engineering. Networking with industry peers, seeking mentorship, and building a reputation for reliability and expertise are crucial for opening new pathways. Continuous learning through certifications, workshops, and staying current with evolving quality standards marks significant career milestones and supports sustained growth.
Junior Quality Control Specialist
0-2 yearsKey Focus Areas
Quality Control Specialist
2-4 yearsKey Focus Areas
Senior Quality Control Specialist
4-7 yearsKey Focus Areas
Quality Control Supervisor
7-10 years total experience, 2-3 years in a leadership roleKey Focus Areas
Quality Control Manager
10-15 years total experience, 3-5 years in a managerial roleKey Focus Areas
Director of Quality Control
15+ years total experience, 5+ years in senior managementKey Focus Areas
Junior Quality Control Specialist
0-2 yearsPerform routine inspections and tests on raw materials, in-process products, or finished goods. Document findings accurately and identify basic non-conformances. Work under direct supervision, following established procedures. Contribute to maintaining a clean and organized work environment.
Key Focus Areas
Develop foundational understanding of quality standards, inspection techniques, and documentation protocols. Master basic statistical process control tools and data entry. Focus on meticulous observation and adherence to instructions. Build strong communication skills for reporting findings.
Quality Control Specialist
2-4 yearsConduct a variety of complex quality inspections and tests, interpreting specifications and blueprints. Investigate deviations and non-conformances, recommending corrective actions. Operate with greater autonomy, making decisions within defined parameters. Collaborate with production teams to resolve immediate quality concerns.
Key Focus Areas
Enhance proficiency in advanced testing equipment and analytical software. Develop problem-solving skills for root cause analysis of quality issues. Understand and apply relevant industry regulations and quality management systems. Begin to mentor junior colleagues and participate in process improvement initiatives.
Senior Quality Control Specialist
4-7 yearsLead critical quality inspections and audits, often involving complex products or processes. Act as a subject matter expert, providing guidance on quality standards and best practices. Independently analyze quality data, identify trends, and propose process improvements. Train junior staff and contribute significantly to quality documentation and system enhancements.
Key Focus Areas
Master advanced statistical analysis for trend identification and predictive quality. Lead complex investigations and implement robust corrective and preventive actions (CAPA). Develop expertise in specific product lines or manufacturing processes. Cultivate strong cross-functional collaboration and communication skills to influence quality culture.
Quality Control Supervisor
7-10 years total experience, 2-3 years in a leadership roleOversee the daily operations of a team of Quality Control Specialists, ensuring adherence to schedules and quality protocols. Review and approve inspection reports, managing escalated non-conformances. Implement and enforce quality procedures, contributing to standard operating procedure (SOP) development. Provide direct supervision and training to team members.
Key Focus Areas
Develop leadership and team management skills, including scheduling, performance feedback, and conflict resolution. Understand budgetary constraints and resource allocation for quality operations. Enhance knowledge of advanced quality methodologies like Six Sigma or Lean. Focus on fostering a proactive quality mindset within the team.
Quality Control Manager
10-15 years total experience, 3-5 years in a managerial roleManage the overall quality control function for a department or product line, setting objectives and strategies. Develop, implement, and maintain quality control programs and procedures. Lead internal and external audits, ensuring compliance with regulatory requirements. Recruit, train, and develop quality control staff, managing departmental budgets.
Key Focus Areas
Master quality management system (QMS) implementation and continuous improvement. Develop strategic thinking for long-term quality planning and risk management. Cultivate strong stakeholder management and negotiation skills. Focus on driving organizational quality culture and compliance.
Director of Quality Control
15+ years total experience, 5+ years in senior managementProvide strategic leadership for the entire quality control and assurance function across the organization. Define the long-term vision and strategy for quality, ensuring alignment with business goals. Oversee all quality systems, regulatory compliance, and continuous improvement initiatives. Represent the company on quality matters to external stakeholders, including regulatory agencies and customers.
Key Focus Areas
Develop executive leadership skills, including strategic planning, organizational development, and change management. Cultivate an in-depth understanding of global quality regulations and market trends. Focus on innovation in quality assurance and driving competitive advantage through superior quality. Build strong relationships with executive leadership and external regulatory bodies.
Job Application Toolkit
Ace your application with our purpose-built resources:
Quality Control Cover Letter Examples
Personalizable templates that showcase your impact.
View examplesQuality Control Job Description Template
Ready-to-use JD for recruiters and hiring teams.
View examplesGlobal Quality Control Opportunities
Quality Control professionals ensure product and process standards globally. This role translates across manufacturing, pharma, and tech, with consistent demand for defect prevention and regulatory compliance worldwide.
International job markets in 2025 show strong growth, driven by supply chain complexity and increased global quality regulations. Cultural differences impact quality perceptions, while international certifications like ISO 9001 facilitate global mobility.
Professionals consider international opportunities for specialized industry exposure and diverse regulatory environments.
Global Salaries
Quality Control salaries vary significantly by region and industry. In North America, an experienced Quality Control specialist can expect to earn between $55,000 and $80,000 USD annually. For example, in the US, salaries average around $65,000 USD, while in Canada, they typically range from CAD 50,000 to CAD 75,000 ($37,000-$55,000 USD).
Europe presents a diverse landscape. In Germany, a Quality Control professional might earn €40,000-€60,000 ($43,000-$65,000 USD), reflecting a higher cost of living. In Eastern Europe, such as Poland, salaries are lower, typically €20,000-€35,000 ($22,000-$38,000 USD), offering greater purchasing power locally. UK salaries average £30,000-£45,000 ($38,000-$57,000 USD).
Asia-Pacific markets, like Singapore, offer competitive pay, ranging from SGD 45,000-SGD 70,000 ($33,000-$52,000 USD), but with a high cost of living. In India, salaries are considerably lower, INR 400,000-INR 800,000 ($5,000-$10,000 USD), though purchasing power remains strong for local expenses. Latin America sees lower compensation, with Brazil offering BRL 40,000-BRL 70,000 ($8,000-$14,000 USD).
Salary structures also differ, with North American packages often including comprehensive health benefits and retirement plans. European countries typically have robust social security and generous vacation time. Tax implications vary; for instance, higher income tax rates in Western Europe may reduce take-home pay compared to some Asian markets. Experience and specialized education, like Six Sigma certification, significantly influence compensation globally.
Remote Work
International remote work for Quality Control professionals is less common than for purely digital roles, as many tasks require on-site presence, especially in manufacturing or lab settings. However, roles focusing on documentation, process auditing, or supplier quality management can offer remote potential.
Legal and tax implications for international remote work are complex, requiring careful consideration of permanent establishment rules and social security contributions. Time zone differences can pose challenges for real-time collaboration with global teams.
Digital nomad opportunities exist for Quality Control consultants or auditors who manage multiple international projects. Countries like Portugal and Estonia offer specific remote work visas. Employer policies vary; some global companies are adopting hybrid models, allowing remote work for administrative quality functions. Salary expectations for remote roles often align with the employer's country of origin, impacting geographic arbitrage opportunities. Reliable internet and a dedicated home office are essential.
Visa & Immigration
Quality Control professionals seeking international work often utilize skilled worker visas. Countries like Germany (EU Blue Card), Canada (Express Entry), and Australia (Skilled Nominated Visa) are popular destinations. Requirements typically include a relevant bachelor's degree in engineering or science, several years of experience, and a job offer from a local employer.
Credential recognition is crucial; applicants may need to have their educational qualifications assessed by a designated authority. Professional licensing is generally not required for Quality Control roles, but industry-specific certifications (e.g., ASQ certifications) enhance eligibility. Typical visa timelines range from 3 to 12 months, depending on the country and visa type.
Pathways to permanent residency exist in many skilled worker programs, usually after several years of continuous employment. Language proficiency (e.g., IELTS for English-speaking countries, Goethe-Institut for German) is often a requirement. Some countries prioritize specific manufacturing or pharmaceutical expertise, potentially offering faster processing. Family visas for spouses and dependents are generally available alongside the primary applicant's visa.
2025 Market Reality for Quality Controls
Understanding current market conditions is critical for anyone pursuing a Quality Control career. The landscape has shifted significantly between 2023 and 2025, influenced by post-pandemic supply chain recalibrations and the rapid integration of AI into industrial processes.
Broader economic factors, such as inflation and consumer demand shifts, directly impact production volumes and, consequently, the need for QC professionals. Market realities also vary by experience level; entry-level roles face different dynamics than senior or specialized positions. Geographic region and company size further dictate specific opportunities and challenges, making a tailored understanding essential for effective career planning.
Current Challenges
Quality Control faces increased competition, particularly for entry-level roles, as companies automate more routine tasks, expecting higher analytical skills. Economic uncertainty pushes companies to streamline operations, often leading to leaner QC teams and higher output expectations per individual. This creates skill gaps, as many candidates lack proficiency in advanced statistical analysis or automated testing tools. Job searches can extend due to the volume of applicants and the specialized nature of current demands.
Growth Opportunities
Despite challenges, strong demand exists for Quality Control professionals specializing in automation, data analytics, and AI integration. Roles like 'Automation QC Engineer,' 'Data-Driven Quality Analyst,' or 'AI-Assisted Quality Assurance Specialist' are emerging with significant growth. Professionals can gain an advantage by acquiring certifications in predictive analytics, machine learning for quality, or advanced statistical software. These skills transform them from inspectors to strategic partners.
Underserved markets include small to medium-sized enterprises (SMEs) that are just beginning their digital transformation journeys and require expertise to implement new quality systems. Furthermore, niche industries such as specialized medical device manufacturing or advanced materials production continue to show robust demand for highly skilled QC talent. Focusing on sectors resilient to economic downturns, like pharmaceuticals or essential goods, can also provide stability. Strategic career moves now involve investing in upskilling to align with automation and data-centric quality paradigms, ensuring long-term relevance and higher earning potential.
Current Market Trends
Hiring for Quality Control (QC) roles as of 2025 shows a nuanced demand. While foundational QC remains crucial, the market increasingly favors candidates proficient in automated testing, data analytics, and process optimization rather than purely manual inspection. The integration of AI and machine learning into manufacturing and service delivery reshapes QC; predictive quality assurance models now augment traditional checks, shifting roles from reactive fault detection to proactive prevention.
Economic conditions exert pressure on QC departments. Companies seek to maximize efficiency, often leading to consolidation of roles or increased expectations for fewer staff. This impacts job availability, with a stronger emphasis on multi-skilled professionals. Technology trends, especially the rise of industrial IoT and advanced sensor technology, generate vast datasets. QC professionals now analyze this data to identify trends, predict failures, and improve processes, moving beyond simple pass/fail assessments.
Employer requirements have evolved. Many companies now demand certifications in Lean, Six Sigma, or specific automated testing platforms. Proficiency in statistical process control (SPC) software is often a prerequisite. Salary trends for basic QC roles remain stable but show upward movement for those with advanced automation, data analysis, or AI integration skills. Market saturation exists at the entry-level for manual inspection roles, but a shortage of skilled automation QC specialists persists. Geographic variations are notable; manufacturing hubs and technology centers show stronger demand for advanced QC roles, while remote work is less common for hands-on production QC.
Emerging Specializations
The Quality Control profession is undergoing a significant transformation, driven by rapid advancements in automation, artificial intelligence, and data analytics. These technological shifts are not merely optimizing existing processes; they are fundamentally reshaping the demand for specific skills and creating entirely new specialization opportunities. Professionals who proactively identify and position themselves within these emerging areas will find themselves at a distinct advantage as early adopters.
Early positioning in these future-oriented specializations is crucial for career advancement from 2025 onwards. Such roles often command premium compensation and offer accelerated career growth paths, as the supply of skilled professionals in these niche areas is still developing. While established quality control practices remain vital, the greatest opportunities for impact and innovation lie in understanding and integrating next-generation methodologies.
Many emerging areas, particularly those involving advanced data analysis or specialized compliance, move from nascent concepts to mainstream demand within a three to five-year timeframe. This allows professionals to build expertise as the market matures, ensuring a strong foundation for future roles. Pursuing cutting-edge specializations involves a calculated risk, as not all trends fully materialize, but the potential rewards—in terms of influence, compensation, and career trajectory—often outweigh these considerations for forward-thinking individuals.
Data Quality Control Specialist
This specialization focuses on ensuring the quality and integrity of data used in decision-making and automated processes. As organizations increasingly rely on large datasets and AI-driven insights, the quality of this foundational data becomes paramount. A Data Quality Control Specialist designs and implements robust data validation, cleansing, and monitoring protocols to prevent errors and ensure compliance with data governance standards.
Automation & Robotics QC Engineer
With the proliferation of automated manufacturing processes, robotics, and smart systems, ensuring the quality of these complex, interconnected systems is a new challenge. An Automation & Robotics QC Engineer focuses on the reliability, precision, and safety of automated production lines and robotic applications. This involves validating sensor accuracy, robotic arm repeatability, and the overall performance of integrated automation solutions.
AI/ML Model Quality Analyst
This role addresses the critical need for quality assurance in software and systems incorporating artificial intelligence and machine learning. An AI/ML Model Quality Analyst ensures that AI models are unbiased, perform accurately, and maintain their predictive power over time. This involves developing testing methodologies for model performance, data drift detection, and ethical AI compliance.
Supply Chain Quality & Traceability Specialist
As supply chains become more globalized and interconnected, the need for robust quality control across the entire network intensifies. A Supply Chain Quality & Traceability Specialist ensures product quality from raw material sourcing through final delivery, leveraging digital tools for real-time monitoring and traceability. This specialization focuses on mitigating risks, ensuring compliance, and maintaining quality standards across diverse suppliers and logistics partners.
Sustainability & Green QC Auditor
This specialization focuses on ensuring that products and processes meet stringent environmental and sustainability standards. A Sustainability & Green QC Auditor evaluates manufacturing processes, material sourcing, and product lifecycle impacts against environmental regulations and corporate sustainability goals. This involves assessing carbon footprints, waste reduction initiatives, and the use of eco-friendly materials, ensuring compliance and promoting sustainable practices.
Pros & Cons of Being a Quality Control
Making informed career choices requires a thorough understanding of both the benefits and challenges associated with a profession. The experience in any career, including Quality Control, can vary significantly based on factors such as company culture, the specific industry sector, the level of specialization, and individual preferences. What one person considers an advantage, another might see as a drawback, depending on their personal values and lifestyle priorities. Furthermore, the pros and cons of a role can evolve as one progresses through different career stages, from entry-level to senior positions. This assessment aims to provide a realistic and balanced perspective on the Quality Control field, helping prospective professionals set appropriate expectations.
Pros
- Quality Control professionals play a crucial role in ensuring product safety and reliability, providing a strong sense of purpose and contribution to customer satisfaction and brand reputation.
- Demand for Quality Control personnel remains consistent across diverse industries, including manufacturing, pharmaceuticals, food processing, and technology, offering good job security and varied employment opportunities.
- The role provides opportunities to develop strong analytical and problem-solving skills as you investigate defects, identify root causes, and implement corrective actions.
- Quality Control often involves working with various departments, such as production, engineering, and supply chain, offering a holistic view of the operational process and fostering cross-functional collaboration.
- Entry into Quality Control often does not require extensive formal education; many positions are accessible with vocational training, an associate's degree, or even relevant certifications and on-the-job experience.
- Many Quality Control environments offer predictable work schedules, especially in industries with standard operating hours, which can contribute to a stable work-life balance.
- For those who enjoy meticulous work and attention to detail, the precise nature of Quality Control tasks, such as inspection, testing, and documentation, can be highly satisfying.
Cons
- Quality Control roles often involve repetitive tasks, such as inspecting numerous items or running the same tests repeatedly, which can lead to monotony and reduced job satisfaction over time.
- Pressure to meet production quotas while maintaining high quality standards can create significant stress, especially when defects are discovered late in the process or when deadlines are tight.
- Exposure to hazardous materials, loud machinery, or uncomfortable working conditions is common in manufacturing or industrial settings, posing potential health and safety risks.
- Career advancement opportunities within Quality Control can be limited, often requiring additional education or a transition into management or specialized engineering roles to progress significantly.
- Investigating the root cause of defects can be a frustrating and time-consuming process, particularly when documentation is poor or when multiple variables contribute to the issue.
- Quality Control professionals often bear the primary responsibility for product failures or recalls, even when the issues stem from design or manufacturing errors outside their direct control, leading to high accountability.
- The work environment can sometimes feel isolating, as Quality Control often operates independently or within small teams, with less direct collaboration compared to other departments like production or design.
Frequently Asked Questions
Quality Control professionals face distinct challenges in ensuring product excellence and process adherence across various industries. This section addresses crucial questions about entering this role, from necessary skills and educational paths to career progression and the daily realities of maintaining high standards.
What are the essential educational requirements to become a Quality Control professional?
Entry-level Quality Control positions often require a high school diploma or GED, especially in manufacturing or production environments. However, a two-year associate's degree in a technical field, engineering technology, or a related science can significantly improve your prospects and starting salary. For more specialized or advanced roles, a bachelor's degree in engineering, chemistry, biology, or a similar scientific discipline is usually preferred or required. Certifications like ASQ's Certified Quality Inspector (CQI) or Certified Quality Technician (CQT) can also be highly beneficial.
How long does it take to become job-ready in Quality Control if I'm starting from scratch?
The timeline to become job-ready for an entry-level Quality Control role can range from a few months to two years, depending on your starting point. If you have a high school diploma, you might find entry-level positions that offer on-the-job training, allowing you to start quickly. Pursuing an associate's degree typically takes two years. If you already have some relevant technical skills, you might become job-ready faster through specific certifications or vocational training programs, which can take 3-6 months.
What are the typical salary expectations for an entry-level Quality Control position?
Starting salaries for Quality Control technicians or inspectors typically range from $35,000 to $50,000 annually, depending on the industry, location, and your specific qualifications. With a few years of experience, a bachelor's degree, or specialized certifications, salaries can climb to $55,000-$75,000 for Quality Control specialists or engineers. Senior or supervisory roles can command even higher salaries, often exceeding $80,000. Industries like pharmaceuticals, aerospace, and medical devices generally offer higher compensation.
What is the typical work-life balance like for a Quality Control professional?
The work-life balance in Quality Control can vary significantly by industry and company. In manufacturing, shifts might be common, including evenings or weekends, especially in facilities operating 24/7. Lab-based Quality Control roles often have more predictable daytime hours. While the work is usually structured, there can be periods of high pressure, particularly during audits, product launches, or when addressing critical quality issues. Overtime might be required during peak production or problem-solving phases.
Is the Quality Control field growing, and what is the job security like?
The job market for Quality Control professionals remains stable and is expected to grow, driven by increasing regulatory demands and consumer expectations for product safety and reliability. Industries like manufacturing, healthcare, food and beverage, and technology consistently need skilled Quality Control personnel. Automation might change some tasks, but the need for human oversight, problem-solving, and decision-making in quality assurance processes will continue to create demand for qualified individuals.
What are the typical career progression opportunities within Quality Control?
Career growth in Quality Control can lead to various advanced roles. After gaining experience as a Quality Control inspector or technician, you can advance to Quality Assurance Specialist, Quality Engineer, or Quality Manager. Further specialization can lead to roles in Lean Six Sigma, regulatory affairs, or supplier quality. Many professionals also transition into broader operations management or even research and development, leveraging their deep understanding of product and process integrity. Continuous learning and certifications are key to advancement.
What are some of the biggest challenges or frustrations that Quality Control professionals face regularly?
A common challenge in Quality Control is balancing the need for strict adherence to standards with production deadlines. This often requires strong communication skills to convey issues without alienating production teams. Another challenge involves staying current with evolving regulations and technologies, which necessitates continuous learning. Dealing with non-conforming products or processes can also be stressful, requiring meticulous investigation, root cause analysis, and effective problem-solving under pressure.
Can Quality Control roles be performed remotely, or are they mostly on-site?
While some administrative or documentation aspects of Quality Control might be performed remotely, the core functions of inspecting, testing, and monitoring products or processes usually require a physical presence. This means most Quality Control roles are on-site, whether in a manufacturing plant, laboratory, or production facility. However, management or auditing roles might offer more flexibility for hybrid work, allowing some remote work for reporting, planning, or virtual meetings.
Related Careers
Explore similar roles that might align with your interests and skills:
Quality Control Associate
A growing field with similar skill requirements and career progression opportunities.
Explore career guideQuality Control Coordinator
A growing field with similar skill requirements and career progression opportunities.
Explore career guideQuality Control Specialist
A growing field with similar skill requirements and career progression opportunities.
Explore career guideQuality Control Technician
A growing field with similar skill requirements and career progression opportunities.
Explore career guideQuality Specialist
A growing field with similar skill requirements and career progression opportunities.
Explore career guideAssess your Quality Control readiness
Understanding where you stand today is the first step toward your career goals. Our Career Coach helps identify skill gaps and create personalized plans.
Skills Gap Analysis
Get a detailed assessment of your current skills versus Quality Control requirements. Our AI Career Coach identifies specific areas for improvement with personalized recommendations.
See your skills gapCareer Readiness Assessment
Evaluate your overall readiness for Quality Control roles with our AI Career Coach. Receive personalized recommendations for education, projects, and experience to boost your competitiveness.
Assess your readinessSimple pricing, powerful features
Upgrade to Himalayas Plus and turbocharge your job search.
Himalayas
Himalayas Plus
Himalayas Max
Find your dream job
Sign up now and join over 100,000 remote workers who receive personalized job alerts, curated job matches, and more for free!
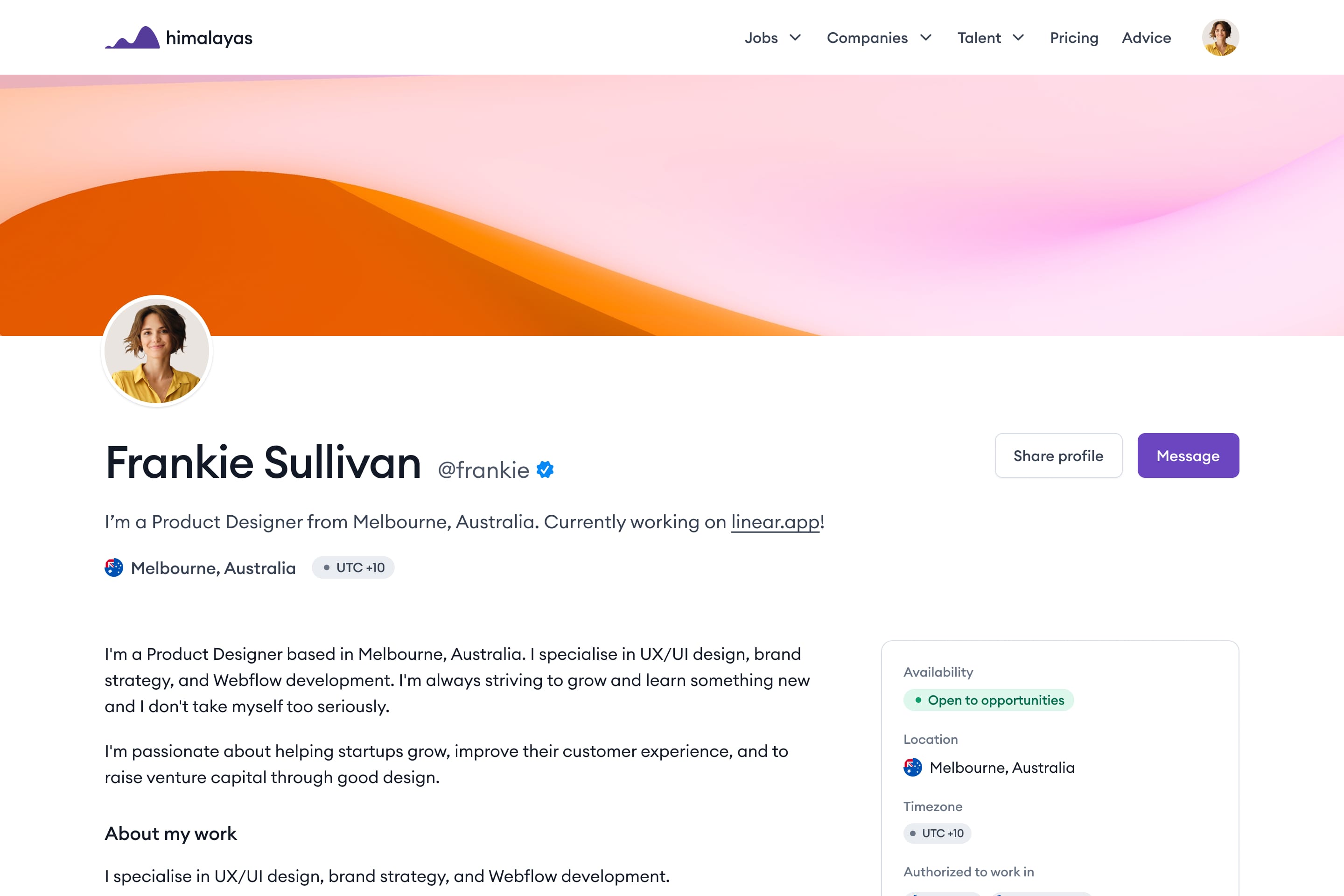