Complete Metal Milling Machine Operator Career Guide
Metal Milling Machine Operators are precision craftspeople who transform raw metal into intricate components vital for everything from aerospace to medical devices. You'll master advanced machinery to cut, shape, and finish parts with extreme accuracy, solving complex production challenges daily. This hands-on career offers stable opportunities for those who enjoy working with technology and have an eye for detail, building essential products that power modern industries.
Key Facts & Statistics
Median Salary
$47,690 USD
(U.S. Bureau of Labor Statistics, May 2023)
Range: $35k - $65k+ USD, varying by experience and specialization
Growth Outlook
5%
as fast as average (U.S. Bureau of Labor Statistics, 2022-2032)
Annual Openings
≈17,000
openings annually (U.S. Bureau of Labor Statistics, 2022-2032)
Top Industries
Typical Education
High school diploma or equivalent, often with on-the-job training, vocational school, or an apprenticeship
What is a Metal Milling Machine Operator?
A Metal Milling Machine Operator is a skilled tradesperson who sets up, operates, and maintains milling machines to cut and shape metal parts according to precise specifications.
This role is distinct from a general machinist, as it specializes specifically in milling operations, which involve rotating multi-point cutting tools to remove material from a workpiece. Unlike a lathe operator who works with rotating workpieces, a milling machine operator works with stationary workpieces, creating complex shapes, slots, and holes. They are crucial in manufacturing, producing components for aerospace, automotive, medical, and various other industries that rely on high-precision metal parts.
What does a Metal Milling Machine Operator do?
Key Responsibilities
- Set up metal milling machines by selecting and installing appropriate cutting tools, fixtures, and work holding devices according to blueprints and job specifications.
- Load raw material, such as metal blocks or sheets, onto the machine and ensure it is securely clamped for precise cutting operations.
- Program machine controls, inputting G-code or using CAM software to define tool paths, cutting speeds, and feed rates to achieve the desired part geometry.
- Monitor machine operations closely, observing tool wear, cutting conditions, and material removal to ensure product quality and machine efficiency.
- Perform routine maintenance on milling machines, including cleaning, lubricating, and making minor adjustments to ensure optimal performance and extend machine lifespan.
- Inspect finished parts using precision measuring instruments like calipers, micrometers, and gauges to verify dimensional accuracy and surface finish against design specifications.
- Troubleshoot and resolve minor machine malfunctions or program errors that may occur during production to minimize downtime and maintain workflow.
Work Environment
Metal Milling Machine Operators typically work in manufacturing plants, machine shops, or production facilities. The environment can be noisy due to machinery operation and may require personal protective equipment like safety glasses, hearing protection, and steel-toed boots.
The work is often performed independently at a machine, but collaboration with supervisors, quality control technicians, and maintenance staff is common. Schedules often involve fixed shifts, including day, evening, or night shifts, and sometimes weekends, depending on production demands.
The pace is steady and detail-oriented, requiring focus and precision. The role is primarily hands-on, involving standing, lifting, and repetitive motions.
Tools & Technologies
Metal Milling Machine Operators primarily work with Computer Numerical Control (CNC) milling machines, including vertical milling machines (VMCs) and horizontal milling machines (HMCs).
They use a variety of cutting tools such as end mills, face mills, drills, and reamers. Precision measuring instruments like micrometers, calipers, height gauges, and bore gauges are essential for quality control. Operators also utilize hand tools for setup and maintenance.
Software includes machine control interfaces and potentially Computer-Aided Manufacturing (CAM) software for generating tool paths from Computer-Aided Design (CAD) models, along with basic shop floor control systems for tracking production.
Metal Milling Machine Operator Skills & Qualifications
A Metal Milling Machine Operator requires a specific blend of practical experience, precision, and safety awareness. Employers prioritize hands-on experience with CNC (Computer Numerical Control) or manual milling machines. The depth of experience needed often depends on the complexity of the parts being machined and the type of industry. For instance, aerospace or medical device manufacturing demands a higher level of precision and proven experience compared to general fabrication shops.
Formal education can provide a strong foundation, but practical experience often carries more weight. Many operators begin with vocational training or apprenticeships, which combine classroom learning with on-the-job training. Certifications, particularly in CNC operation, CAD/CAM software, or specific machining techniques, significantly enhance a candidate's marketability. These certifications validate specialized skills and demonstrate a commitment to professional development.
The skill landscape for Metal Milling Machine Operators is evolving with increasing automation. While manual machining skills remain valuable, proficiency in CNC programming and operation is becoming essential. Operators must continuously adapt to new machine technologies and software updates. Balancing foundational mechanical aptitude with digital literacy is crucial for long-term career success in this field.
Education Requirements
Technical Skills
- CNC Milling Machine Operation (setup, loading, tool changes, offsets)
- Blueprint and Technical Drawing Interpretation (GD&T, tolerances, finishes)
- Precision Measurement Tools (calipers, micrometers, height gauges, bore gauges)
- G-Code and M-Code Programming (editing, basic troubleshooting, understanding commands)
- Machine Tooling and Inserts (selection, care, application)
- Material Properties and Machinability (metals like aluminum, steel, brass, titanium)
- Preventative Maintenance (cleaning, lubrication, basic diagnostics)
- Fixture and Workholding Setup (vise, clamps, chucks)
- Quality Control Procedures (in-process inspection, first-piece inspection)
- CAM Software (e.g., Mastercam, Fusion 360, GibbsCAM) - basic understanding and program loading
- Manual Milling Machine Operation (if applicable to the specific role)
- Deburring and Finishing Techniques
Soft Skills
- Attention to Detail: Essential for precise measurements, identifying material flaws, and ensuring product specifications are met, preventing costly errors.
- Problem-Solving: Critical for diagnosing machine malfunctions, troubleshooting production issues, and optimizing machining parameters for efficiency and quality.
- Safety Consciousness: Paramount for adhering to strict safety protocols, operating heavy machinery responsibly, and maintaining a safe work environment to prevent accidents.
- Mechanical Aptitude: Important for understanding how machines work, performing basic maintenance, and interpreting mechanical drawings and schematics.
- Adaptability: Necessary to adjust to new machine models, software updates, and varying production demands or material properties.
- Communication: Key for collaborating with supervisors, engineers, and fellow operators, reporting issues, and understanding work orders accurately.
- Patience: Required when setting up complex jobs, waiting for long machining cycles, or troubleshooting intricate problems.
- Time Management: Important for prioritizing tasks, meeting production deadlines, and efficiently managing machine uptime and material flow.
How to Become a Metal Milling Machine Operator
Becoming a Metal Milling Machine Operator involves various pathways, each with its own timeline and benefits. Some enter through vocational training programs, which can take 6-12 months, providing hands-on skills quickly. Others start as apprentices, learning on the job over 2-4 years, often while earning a wage.
Entry strategies vary significantly by company size and industry. Larger manufacturing firms might prefer candidates with formal certifications or apprenticeship completions, while smaller job shops might be more open to training someone with mechanical aptitude from scratch. Geographic location also plays a role; industrial hubs often have more opportunities and established training pipelines.
A common misconception is that this field only requires brute strength; in reality, precision, attention to detail, and a strong understanding of machine mechanics are paramount. While a formal degree is not always essential, demonstrating practical skills through projects or previous mechanical work is crucial. Networking with experienced operators and shop owners can also uncover unadvertised opportunities and mentorship.
Develop foundational mechanical aptitude and math skills. Focus on understanding basic physics, geometry, and algebra, which are crucial for interpreting blueprints and machine settings. Consider taking introductory courses in shop math or enrolling in a community college program for mechanical basics; this stage can take 1-3 months.
Gain hands-on experience with tools and materials. Seek opportunities to work with hand tools, power tools, and various metals, even through personal projects or volunteer work. Familiarize yourself with different types of metal, their properties, and safe handling procedures to build practical familiarity over 3-6 months.
Complete a specialized vocational program or apprenticeship. Enroll in a certified machining program that covers CNC operation, manual milling, blueprint reading, and G-code programming. Alternatively, seek an entry-level apprenticeship with a local machine shop to learn directly from experienced operators; this phase typically lasts 6 months to 2 years.
Obtain relevant certifications to validate your skills. Pursue certifications like the NIMS (National Institute for Metalworking Skills) credentials in Measurement, Materials & Safety, Job Planning, Benchwork & Layout, and Milling. These certifications demonstrate a standardized level of competency to potential employers and can take 2-6 months to prepare for and pass.
Build a portfolio of practical projects and documented experience. Showcase any parts you have machined, detailing the processes, tools used, and challenges overcome. Include photos, blueprints, and a brief explanation of your role in each project, even if they are from school or personal initiatives.
Network within the manufacturing industry and prepare for job applications. Attend local manufacturing trade shows, join online forums for machinists, and connect with professionals on LinkedIn. Tailor your resume to highlight your practical skills, certifications, and any hands-on experience, even if it's from personal projects or volunteer work.
Apply for entry-level or apprentice operator positions and excel in interviews. Focus on demonstrating your eagerness to learn, attention to detail, and commitment to safety. Be prepared to discuss your understanding of machine operation principles and how you approach problem-solving during a practical assessment or shop tour.
Step 1
Develop foundational mechanical aptitude and math skills. Focus on understanding basic physics, geometry, and algebra, which are crucial for interpreting blueprints and machine settings. Consider taking introductory courses in shop math or enrolling in a community college program for mechanical basics; this stage can take 1-3 months.
Step 2
Gain hands-on experience with tools and materials. Seek opportunities to work with hand tools, power tools, and various metals, even through personal projects or volunteer work. Familiarize yourself with different types of metal, their properties, and safe handling procedures to build practical familiarity over 3-6 months.
Step 3
Complete a specialized vocational program or apprenticeship. Enroll in a certified machining program that covers CNC operation, manual milling, blueprint reading, and G-code programming. Alternatively, seek an entry-level apprenticeship with a local machine shop to learn directly from experienced operators; this phase typically lasts 6 months to 2 years.
Step 4
Obtain relevant certifications to validate your skills. Pursue certifications like the NIMS (National Institute for Metalworking Skills) credentials in Measurement, Materials & Safety, Job Planning, Benchwork & Layout, and Milling. These certifications demonstrate a standardized level of competency to potential employers and can take 2-6 months to prepare for and pass.
Step 5
Build a portfolio of practical projects and documented experience. Showcase any parts you have machined, detailing the processes, tools used, and challenges overcome. Include photos, blueprints, and a brief explanation of your role in each project, even if they are from school or personal initiatives.
Step 6
Network within the manufacturing industry and prepare for job applications. Attend local manufacturing trade shows, join online forums for machinists, and connect with professionals on LinkedIn. Tailor your resume to highlight your practical skills, certifications, and any hands-on experience, even if it's from personal projects or volunteer work.
Step 7
Apply for entry-level or apprentice operator positions and excel in interviews. Focus on demonstrating your eagerness to learn, attention to detail, and commitment to safety. Be prepared to discuss your understanding of machine operation principles and how you approach problem-solving during a practical assessment or shop tour.
Education & Training Needed to Become a Metal Milling Machine Operator
Becoming a skilled Metal Milling Machine Operator involves a blend of formal training and hands-on experience. While a four-year degree is not typically required, specialized vocational programs, apprenticeships, and certifications are highly valued. These pathways equip operators with the necessary knowledge of machine operation, blueprint reading, precision measurement, and material properties.
Vocational school programs, ranging from 6 months to 2 years, often cost between $5,000 and $25,000, and provide a strong foundation in CNC machining and manual milling. Apprenticeships, which combine paid on-the-job training with classroom instruction, can last 3-5 years. They often cost less for the apprentice, with employers sometimes covering tuition for related technical instruction. Industry certifications, like those from NIMS (National Institute for Metalworking Skills), are crucial for demonstrating competency and can be earned through various programs or self-study, typically costing a few hundred to a couple of thousand dollars per certification.
Employers highly regard practical experience and industry-recognized certifications. While some basic roles might accept candidates with only a high school diploma and on-the-job training, advancement to more complex or CNC-driven milling operations usually requires formal education or an apprenticeship. Continuous learning is essential, especially with the rapid evolution of CNC technology and automation in manufacturing. Many operators pursue additional certifications in advanced machining techniques or specific software to enhance their skills and career prospects.
Metal Milling Machine Operator Salary & Outlook
Compensation for a Metal Milling Machine Operator varies significantly based on several factors beyond just the base hourly wage. Geographic location plays a crucial role; operators in regions with high manufacturing demand or a higher cost of living, such as the Northeast or parts of the Midwest, typically command higher salaries than those in areas with a lower cost of living.
Experience and specialized skills also dramatically influence earning potential. Operators proficient in advanced CNC programming, multi-axis milling, or working with exotic materials often receive premium compensation. Total compensation packages frequently include overtime pay, production bonuses, and shift differentials, particularly for night or weekend shifts. Comprehensive benefits, including health insurance, retirement plans like 401(k)s, and paid time off, are standard in many manufacturing companies.
Company size and industry sector can also impact pay. Larger manufacturing firms or those in high-precision industries like aerospace or medical devices generally offer more competitive salaries and benefits than smaller job shops. Remote work is not applicable for this hands-on role. While these figures focus on the USD market, international markets will show different pay scales based on local economic conditions and labor market dynamics.
Salary by Experience Level
Level | US Median | US Average |
---|---|---|
Junior Metal Milling Machine Operator | $35k USD | $38k USD |
Metal Milling Machine Operator | $45k USD | $47k USD |
Senior Metal Milling Machine Operator | $53k USD | $56k USD |
Lead Metal Milling Machine Operator | $62k USD | $65k USD |
CNC Milling Specialist | $68k USD | $72k USD |
Market Commentary
The job market for Metal Milling Machine Operators shows a stable outlook, driven by ongoing demand in various manufacturing sectors. The Bureau of Labor Statistics projects little to no change in employment for machinists and tool and die makers, which includes milling machine operators, through 2032. Despite this, a consistent need for skilled operators exists due to retirements and the increasing complexity of manufacturing processes.
Technological advancements, particularly in Computer Numerical Control (CNC) machinery and automation, are reshaping the role. Operators with strong CNC programming, setup, and troubleshooting skills are in high demand, as these abilities are essential for optimizing production and maintaining quality. The adoption of advanced robotics and AI in manufacturing plants means operators must continuously update their skills to work alongside these technologies, ensuring future relevance.
While some tasks may become automated, the need for human oversight, precision setup, quality control, and problem-solving remains critical. Industries like aerospace, automotive, medical device manufacturing, and defense continue to be significant employers. Geographic hotspots for this role align with major manufacturing hubs in states like Michigan, Ohio, Texas, and California. The supply of highly skilled operators often lags behind demand, creating opportunities for those with specialized expertise and a commitment to continuous learning in evolving machining technologies.
Metal Milling Machine Operator Career Path
Career progression for a Metal Milling Machine Operator typically involves a journey from foundational machine operation to advanced technical expertise and leadership. This path emphasizes hands-on experience, precision, and continuous learning. Operators can advance through individual contributor (IC) tracks, focusing on specialized technical skills, or move into leadership roles, guiding teams and optimizing processes.
Advancement speed depends on several factors: an operator's demonstrated precision and efficiency, their willingness to learn new technologies like CNC programming, and the size and type of manufacturing company. Larger companies with diverse machinery often offer more structured advancement opportunities. Specialization in complex materials or advanced machining techniques also accelerates progression.
Lateral movement opportunities exist within manufacturing, such as transitioning to CAD/CAM programming, quality control, or machine maintenance. Continuous skill development, including certifications in specific machining processes or CAD/CAM software, is crucial. Networking within the manufacturing industry and seeking mentorship from experienced operators or engineers also plays a significant role in identifying new opportunities and accelerating growth.
Junior Metal Milling Machine Operator
0-2 yearsOperates conventional metal milling machines under direct supervision, performing routine cutting and shaping tasks. Follows detailed instructions to load materials, set up basic tooling, and monitor machine performance. Primarily responsible for producing simple parts and ensuring quality through basic measurement tools.
Key Focus Areas
Developing foundational machine operation skills, including safe machine startup and shutdown, basic material handling, and understanding blueprint readings. Focus on learning to identify common machining errors and performing basic preventative maintenance. Accuracy and adherence to safety protocols are paramount.
Metal Milling Machine Operator
2-5 yearsIndependently operates a range of metal milling machines, including both conventional and introductory CNC models. Performs complex setups, adjusts machine parameters for optimal performance, and conducts in-process quality checks. Responsible for producing precision parts to specifications with minimal oversight.
Key Focus Areas
Mastering various milling techniques, including advanced tooling selection and fixture setup. Developing troubleshooting skills for common machine issues and improving efficiency in part production. Beginning to interpret complex blueprints and understand geometric dimensioning and tolerancing (GD&T).
Senior Metal Milling Machine Operator
5-8 yearsExecutes highly complex milling operations, often involving challenging geometries or exotic materials. Troubleshoots advanced machine malfunctions and optimizes existing programs to enhance production efficiency and reduce scrap. Provides guidance to less experienced operators and contributes to shop floor organization and safety standards.
Key Focus Areas
Refining expertise in complex machining operations, including multi-axis milling and advanced material applications. Developing problem-solving skills for intricate production challenges and optimizing machine programs for efficiency and quality. Mentoring junior operators and contributing to process improvement initiatives.
Lead Metal Milling Machine Operator
8-12 yearsOversees a small team of milling machine operators, ensuring production schedules are met and quality standards are maintained. Assigns tasks, provides technical guidance, and conducts performance reviews. Responsible for identifying and implementing process improvements, managing material flow, and ensuring compliance with safety regulations.
Key Focus Areas
Leading and coordinating milling operations, including scheduling, resource allocation, and workflow optimization. Developing strong communication and leadership skills to motivate teams and manage production targets. Contributing to the development of new machining processes and training programs.
CNC Milling Specialist
12+ years total experience, with 3+ years as a LeadServes as the primary technical expert for all CNC milling operations. Designs and optimizes complex CNC programs, develops custom tooling solutions, and troubleshoots the most challenging production issues. Collaborates with engineering and design teams to improve part manufacturability and implement new technologies for enhanced efficiency and precision.
Key Focus Areas
Mastering advanced CNC programming, including CAM software proficiency and G-code optimization. Developing expertise in DFM (Design for Manufacturability) principles and integrating automation into milling processes. Staying current with industry trends, new materials, and cutting-edge machining technologies.
Junior Metal Milling Machine Operator
0-2 yearsOperates conventional metal milling machines under direct supervision, performing routine cutting and shaping tasks. Follows detailed instructions to load materials, set up basic tooling, and monitor machine performance. Primarily responsible for producing simple parts and ensuring quality through basic measurement tools.
Key Focus Areas
Developing foundational machine operation skills, including safe machine startup and shutdown, basic material handling, and understanding blueprint readings. Focus on learning to identify common machining errors and performing basic preventative maintenance. Accuracy and adherence to safety protocols are paramount.
Metal Milling Machine Operator
2-5 yearsIndependently operates a range of metal milling machines, including both conventional and introductory CNC models. Performs complex setups, adjusts machine parameters for optimal performance, and conducts in-process quality checks. Responsible for producing precision parts to specifications with minimal oversight.
Key Focus Areas
Mastering various milling techniques, including advanced tooling selection and fixture setup. Developing troubleshooting skills for common machine issues and improving efficiency in part production. Beginning to interpret complex blueprints and understand geometric dimensioning and tolerancing (GD&T).
Senior Metal Milling Machine Operator
5-8 yearsExecutes highly complex milling operations, often involving challenging geometries or exotic materials. Troubleshoots advanced machine malfunctions and optimizes existing programs to enhance production efficiency and reduce scrap. Provides guidance to less experienced operators and contributes to shop floor organization and safety standards.
Key Focus Areas
Refining expertise in complex machining operations, including multi-axis milling and advanced material applications. Developing problem-solving skills for intricate production challenges and optimizing machine programs for efficiency and quality. Mentoring junior operators and contributing to process improvement initiatives.
Lead Metal Milling Machine Operator
8-12 yearsOversees a small team of milling machine operators, ensuring production schedules are met and quality standards are maintained. Assigns tasks, provides technical guidance, and conducts performance reviews. Responsible for identifying and implementing process improvements, managing material flow, and ensuring compliance with safety regulations.
Key Focus Areas
Leading and coordinating milling operations, including scheduling, resource allocation, and workflow optimization. Developing strong communication and leadership skills to motivate teams and manage production targets. Contributing to the development of new machining processes and training programs.
CNC Milling Specialist
12+ years total experience, with 3+ years as a LeadServes as the primary technical expert for all CNC milling operations. Designs and optimizes complex CNC programs, develops custom tooling solutions, and troubleshoots the most challenging production issues. Collaborates with engineering and design teams to improve part manufacturability and implement new technologies for enhanced efficiency and precision.
Key Focus Areas
Mastering advanced CNC programming, including CAM software proficiency and G-code optimization. Developing expertise in DFM (Design for Manufacturability) principles and integrating automation into milling processes. Staying current with industry trends, new materials, and cutting-edge machining technologies.
Job Application Toolkit
Ace your application with our purpose-built resources:
Metal Milling Machine Operator Resume Examples
Proven layouts and keywords hiring managers scan for.
View examplesMetal Milling Machine Operator Cover Letter Examples
Personalizable templates that showcase your impact.
View examplesTop Metal Milling Machine Operator Interview Questions
Practice with the questions asked most often.
View examplesMetal Milling Machine Operator Job Description Template
Ready-to-use JD for recruiters and hiring teams.
View examplesGlobal Metal Milling Machine Operator Opportunities
Metal Milling Machine Operators find global demand in manufacturing hubs. This role translates consistently across countries, focusing on precision machining. Global demand for skilled operators remains stable, especially in automotive, aerospace, and general fabrication industries. Cultural and regulatory differences primarily affect workplace safety standards and training methodologies. Operators consider international roles for better pay, advanced technology exposure, or new cultural experiences. International certifications like ISO standards or specific machine operation licenses enhance global mobility.
Global Salaries
Salaries for Metal Milling Machine Operators vary significantly by region and industrial output. In North America, particularly the US, operators earn between $40,000 and $65,000 annually (approx. 37,000-60,000 EUR). Experienced operators in high-tech sectors may exceed this. In Europe, Germany offers strong compensation, with salaries typically ranging from 35,000 EUR to 55,000 EUR (approx. $38,000-$60,000 USD). Scandinavian countries also offer competitive pay, often with better benefits and vacation time.
Asia-Pacific countries like Japan and South Korea provide salaries from 3,500,000 JPY to 5,500,000 JPY (approx. $23,000-$37,000 USD) and 40,000,000 KRW to 60,000,000 KRW (approx. $30,000-$45,000 USD) respectively, though cost of living can be higher. Latin American nations, such as Mexico, offer lower nominal salaries, generally $10,000-$20,000 USD, but purchasing power parity can make these roles viable.
Salary structures internationally include varying benefit packages. European countries often have robust social security, healthcare, and longer paid holidays. North American packages may include private health insurance and retirement plans. Tax implications differ greatly; for example, Nordic countries have higher income taxes but extensive social services. Experience and specific machine certifications, like CNC programming expertise, significantly impact compensation in any country. There are no global standardized pay scales, but multinational corporations sometimes offer consistent internal frameworks.
Remote Work
Metal Milling Machine Operators perform hands-on work with machinery; therefore, direct remote work for this role is not feasible. The nature of the job requires physical presence at a manufacturing facility to operate and monitor equipment. There are no digital nomad opportunities directly for machine operation.
However, some related functions, like CAD/CAM programming or production planning, might offer remote possibilities. These are distinct roles from direct machine operation. International remote work policies for operators do not exist due to the practical requirements of the job. Salary expectations are tied to the physical location of the manufacturing plant. Companies do not hire international remote operators for this specific role. Equipment, internet, and workspace setup are irrelevant for the core operational tasks.
Visa & Immigration
Common visa categories for Metal Milling Machine Operators include skilled worker visas. Countries like Canada, Australia, and Germany actively seek skilled tradespeople. For example, Canada's Express Entry system or Australia's Skilled Migration program often list machining roles. Germany's skilled immigration law also facilitates entry for qualified operators, often requiring a recognized vocational qualification.
Education credential recognition is crucial; many countries assess foreign qualifications against their national standards. Professional licensing is not typically required for operators, but specific machine certifications are valuable. Visa timelines vary, from a few months to over a year, depending on the country and application backlog. Language requirements are common, particularly for European countries like Germany (Goethe-Zertifikat) or Canada (IELTS/CELPIP).
Pathways to permanent residency exist in several countries for skilled workers after a few years of employment. Some countries may offer profession-specific advantages if there is a critical shortage. Practical considerations include proving sufficient funds and securing an employer-sponsored job offer. Family visas for spouses and dependents are generally available once the primary applicant secures their work visa.
2025 Market Reality for Metal Milling Machine Operators
Understanding current market conditions is crucial for Metal Milling Machine Operators to navigate career paths effectively. The manufacturing sector, significantly impacted by post-pandemic shifts and the accelerating AI revolution, continues to transform.
Broader economic factors like supply chain stability and industrial investment directly influence job availability and the types of skills employers prioritize. Market realities for milling operators vary by experience level, with entry-level roles facing more competition than specialized positions, and by geographic region where manufacturing density differs. This analysis provides an honest assessment of current hiring realities.
Current Challenges
Metal Milling Machine Operators face increased competition due to automation and a focus on multi-skilled technicians. Entry-level roles, in particular, see saturation as companies invest in advanced CNC systems that require fewer manual operators. Economic uncertainty can lead to reduced manufacturing output, directly impacting hiring for these roles.
The demand for operators with basic, single-machine experience is declining. Companies seek individuals who can program, set up, and troubleshoot complex machines, creating a skill gap for those without advanced training. Job searches for traditional milling operator roles can extend for several months as employers become more selective.
Growth Opportunities
Despite challenges, strong demand exists for Metal Milling Machine Operators with advanced CNC programming and setup skills. Opportunities are growing in precision manufacturing sectors like aerospace, medical devices, and custom tooling, where high-tolerance components are essential.
Specializations in 5-axis milling, advanced materials (e.g., composites, superalloys), or integrated quality control systems offer significant advantages. Professionals can position themselves by pursuing certifications in advanced CNC programming, CAD/CAM software, and GD&T. Underserved markets often include smaller, specialized machine shops that require versatile operators for diverse projects.
Operators who understand automation trends and can work alongside robotic systems, or even assist in their integration, create competitive advantages. Market corrections can create opportunities for those willing to relocate or specialize in niche manufacturing areas. Investing in continuous learning, particularly in new machine technologies and software, remains a key strategy for career advancement in this evolving field.
Current Market Trends
Hiring for Metal Milling Machine Operators shows a stable but evolving demand as of 2025. The industry prioritizes precision and efficiency, shifting requirements from purely manual operation to advanced CNC (Computer Numerical Control) proficiency. Companies seek operators capable of programming, setting up, and troubleshooting complex multi-axis milling machines.
The integration of generative AI and automation in manufacturing planning is influencing production schedules, which in turn affects the workload for milling operators. While AI won't replace operators directly, it optimizes processes, requiring operators to adapt to more complex tasks and less routine work. Economic conditions, while showing signs of recovery, still prompt manufacturers to optimize staffing, leading to a focus on highly skilled individuals rather than simply adding headcount.
Employer requirements now emphasize strong blueprint reading, GD&T (Geometric Dimensioning and Tolerancing) comprehension, and proficiency with CAM (Computer-Aided Manufacturing) software. Operators need to demonstrate problem-solving abilities and a proactive approach to machine maintenance. Salary trends for basic operators remain steady, but those with advanced CNC programming, CAM experience, and multi-machine operation skills command higher wages. Market saturation is noticeable for operators with only manual or basic CNC experience, while demand for advanced technicians remains strong.
Geographically, demand is concentrated in manufacturing hubs like the Midwest and Southeast United States, as well as parts of Germany and China. Remote work is not applicable to this hands-on role. Seasonal patterns are less pronounced, but demand can fluctuate with large-scale manufacturing contracts or industry-specific cycles, such as automotive or aerospace production.
Emerging Specializations
The manufacturing landscape is undergoing significant transformation, creating new specialization opportunities for skilled professionals. Technological advancements, particularly in automation, data analytics, and new material science, are reshaping traditional roles. For Metal Milling Machine Operators, understanding these shifts and positioning oneself early in emerging areas is crucial for career advancement.
Early adoption of these specialized skills can lead to premium compensation and accelerated career growth. While established specializations remain vital, focusing on cutting-edge areas ensures relevance and opens doors to next-generation manufacturing processes. These emerging fields, while not yet mainstream, are rapidly gaining traction and are expected to generate significant job opportunities by 2027-2029.
Pursuing these specializations involves a balance of risk and reward. The initial investment in learning new techniques and software might be higher, but the potential for long-term career stability and higher earning potential is substantial. Professionals who proactively adapt to these changes will be at the forefront of the industry's evolution.
Advanced Multi-Axis CNC Machining Specialist
This specialization focuses on operating and programming advanced 5-axis and multi-tasking CNC milling machines. These machines perform highly complex, simultaneous movements to produce intricate parts in a single setup, significantly reducing production time and improving accuracy. As industries demand more complex geometries and tighter tolerances, expertise in these sophisticated systems becomes indispensable.
Digital Twin Integration Specialist
Digital Twin Integration Specialists work with virtual models of physical milling machines and their processes. They use real-time data from sensors to simulate operations, predict maintenance needs, and optimize machining parameters in a virtual environment before execution. This reduces errors, improves efficiency, and allows for predictive maintenance, making production lines more robust and agile.
Hybrid Additive/Subtractive Machine Operator
This area involves operating milling machines specifically adapted for additive manufacturing post-processing, or hybrid machines that combine additive and subtractive capabilities. Operators manage the milling of 3D-printed parts to achieve final dimensions, surface finishes, and critical tolerances that additive processes alone cannot provide. This bridges the gap between rapid prototyping and high-precision manufacturing.
Automated Milling Cell Technician
Automation and Robotics Integration focuses on setting up, programming, and overseeing robotic arms or automated systems that load, unload, and inspect parts on milling machines. This specialization moves beyond manual operation to managing an automated cell, troubleshooting robotic sequences, and optimizing the interaction between the robot and the milling machine for continuous, lights-out manufacturing.
Sustainable Machining Process Specialist
Sustainable Machining Process Optimization involves adjusting milling parameters, selecting tools, and managing coolants to minimize energy consumption, reduce waste, and extend tool life. This specialization focuses on eco-friendly manufacturing practices, including dry machining, minimum quantity lubrication (MQL), and material recycling, aligning with growing industry demands for sustainability.
Pros & Cons of Being a Metal Milling Machine Operator
Making informed career decisions requires a clear understanding of both the benefits and challenges of a specific profession. A career as a Metal Milling Machine Operator offers distinct advantages, but it also comes with genuine difficulties that prospective individuals should consider.
Experiences can vary significantly depending on the industry, the specific type of machinery, company culture, and the operator's level of experience. What one person perceives as a benefit, another might see as a drawback, based on their personal values and lifestyle preferences. This assessment aims to provide a realistic overview, helping you set appropriate expectations for this hands-on, detail-oriented role.
Pros
- Hands-on work provides a tangible sense of accomplishment, as operators directly contribute to creating precise metal components used in various industries.
- There is consistent demand for skilled metal milling machine operators across manufacturing sectors, ensuring good job security and steady employment opportunities.
- The foundational skills learned are highly transferable, allowing operators to transition to other machining roles or even into programming and quality control positions with additional training.
- Entry into this career often requires vocational training or an apprenticeship rather than a four-year degree, making it an accessible path without significant educational debt.
- Operators develop strong problem-solving skills by troubleshooting machine issues, interpreting blueprints, and adjusting parameters to achieve exact specifications.
- Many manufacturing facilities offer stable hourly wages with potential for overtime pay, providing a reliable income stream, especially for those with specialized skills.
- Modern CNC milling machines require operators to engage with digital controls and programming, offering opportunities to learn and apply technology in a practical setting.
Cons
- The work environment often includes exposure to loud noise, vibrations, and metal dust, which requires consistent use of personal protective equipment and can still pose long-term health risks without proper ventilation.
- Repetitive tasks and standing for long periods can lead to physical strain, fatigue, and an increased risk of musculoskeletal injuries, especially in older or less ergonomically optimized machines.
- Troubleshooting complex machine malfunctions or unexpected material defects can be highly stressful, requiring quick problem-solving under pressure to maintain production schedules.
- Advancement opportunities within a single company might be limited, often requiring additional certifications or a shift into programming, quality control, or supervisory roles.
- The job can be monotonous due to the repetitive nature of loading, unloading, and monitoring machines, which may not appeal to individuals seeking varied daily tasks.
- Working with heavy machinery poses inherent safety risks, including potential for cuts, crushing injuries, or entanglement if safety protocols are not rigorously followed.
- Shift work, including nights and weekends, is common in manufacturing to maximize machine uptime, which can disrupt personal life and social schedules for operators.
Frequently Asked Questions
Becoming a Metal Milling Machine Operator involves mastering precision, safety, and machine programming. This section addresses common questions about entry requirements, daily responsibilities, and career progression, helping you understand the practicalities and opportunities within this skilled trade.
What are the basic educational or training requirements to become a Metal Milling Machine Operator?
A high school diploma or GED is typically the minimum educational requirement. Many operators gain skills through vocational training programs, community college courses focusing on machining or manufacturing technology, or apprenticeships. Certifications like NIMS (National Institute for Metalworking Skills) are highly valued as they demonstrate specific competencies.
How long does it usually take to become job-ready as a Metal Milling Machine Operator if I'm starting from scratch?
Entry-level positions can often be secured within 6-12 months after completing a dedicated vocational program or starting an apprenticeship. If you are self-learning or seeking on-the-job training without prior formal education, it might take longer to build the necessary foundational skills and secure an entry-level role.
What are the typical salary expectations for an entry-level and experienced Metal Milling Machine Operator?
Starting salaries for Metal Milling Machine Operators vary by region and experience, but entry-level roles typically range from $18 to $25 per hour. With a few years of experience, specialized skills (like CNC programming), or working with complex materials, experienced operators can earn $25 to $35+ per hour. Overtime opportunities can also significantly impact overall earnings.
What is the typical work schedule and work-life balance like for a Metal Milling Machine Operator?
The work-life balance for a Metal Milling Machine Operator depends heavily on the employer and industry. Many manufacturing facilities operate on multiple shifts (day, evening, night), which can include 8-hour or 10-hour shifts. Some companies offer standard 40-hour workweeks, while others may require regular overtime, especially during peak production periods. Weekend work is also possible in some operations.
Is the job of a Metal Milling Machine Operator secure, or is it at risk from automation?
Job security for skilled Metal Milling Machine Operators is generally strong, especially for those proficient with CNC machines. Manufacturing continues to be a vital sector, and there's a consistent demand for skilled tradespeople who can operate and program complex machinery. Automation changes the nature of the work, but it also creates a need for operators who can manage these advanced systems.
What are the typical career advancement opportunities for a Metal Milling Machine Operator?
Career growth paths for Metal Milling Machine Operators include specializing in CNC programming, becoming a quality control inspector, or moving into a lead operator or shop supervisor role. Some operators transition into machine maintenance and repair, or even into sales or applications engineering for machine tool companies. Continuing education in advanced machining techniques or leadership can accelerate this progression.
What is the typical work environment like for a Metal Milling Machine Operator?
The work environment for a Metal Milling Machine Operator is typically indoors, within a manufacturing facility or machine shop. It can be noisy due to machinery, and operators are often on their feet for long periods. Safety is paramount, requiring the consistent use of personal protective equipment (PPE) like safety glasses, ear protection, and steel-toed boots. The work often involves handling heavy materials and precise measurements.
Can a Metal Milling Machine Operator work remotely, or is it strictly an on-site role?
While some administrative tasks might be performed remotely, the core work of a Metal Milling Machine Operator, which involves setting up, operating, and monitoring physical machinery, cannot be done from home. This role requires direct, hands-on interaction with the milling machines and materials in a manufacturing setting, making it an inherently on-site position.
Related Careers
Explore similar roles that might align with your interests and skills:
Boring Mill Operator for Metal
A growing field with similar skill requirements and career progression opportunities.
Explore career guideComputer Numerically Controlled (CNC) Milling Machine Operator
A growing field with similar skill requirements and career progression opportunities.
Explore career guideDrill Press Operator for Metal
A growing field with similar skill requirements and career progression opportunities.
Explore career guideHorizontal Boring Mill Operator for Metal
A growing field with similar skill requirements and career progression opportunities.
Explore career guideMetal Rotary Head Milling Machine Setup Operator
A growing field with similar skill requirements and career progression opportunities.
Explore career guideAssess your Metal Milling Machine Operator readiness
Understanding where you stand today is the first step toward your career goals. Our Career Coach helps identify skill gaps and create personalized plans.
Skills Gap Analysis
Get a detailed assessment of your current skills versus Metal Milling Machine Operator requirements. Our AI Career Coach identifies specific areas for improvement with personalized recommendations.
See your skills gapCareer Readiness Assessment
Evaluate your overall readiness for Metal Milling Machine Operator roles with our AI Career Coach. Receive personalized recommendations for education, projects, and experience to boost your competitiveness.
Assess your readinessSimple pricing, powerful features
Upgrade to Himalayas Plus and turbocharge your job search.
Himalayas
Himalayas Plus
Himalayas Max
Find your dream job
Sign up now and join over 100,000 remote workers who receive personalized job alerts, curated job matches, and more for free!
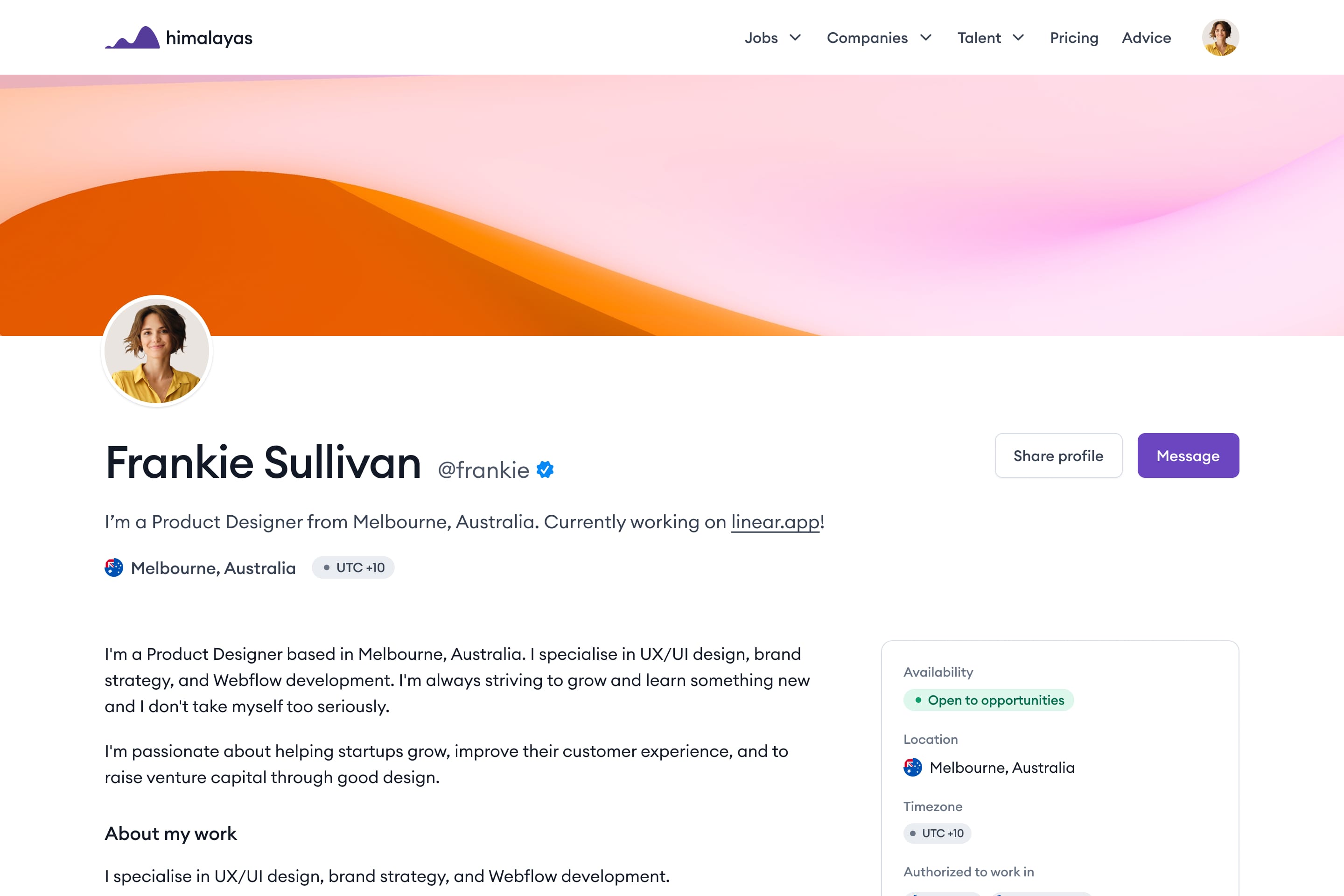