Complete Boring Mill Operator for Metal Career Guide
Boring Mill Operators for Metal are critical to precision manufacturing, shaping raw metal into components with exacting specifications for industries from aerospace to energy. This specialized role demands meticulous attention to detail and a deep understanding of machinery, directly impacting the quality and functionality of complex industrial parts. You'll operate advanced equipment, ensuring components meet tight tolerances, making this a rewarding path for those who value precision and hands-on technical skill.
Key Facts & Statistics
Median Salary
$47,440 USD
(U.S. Bureau of Labor Statistics, May 2022)
Range: $35k - $70k+ USD (Varies by experience, location, and industry)
Growth Outlook
1%
slower than average (U.S. Bureau of Labor Statistics, 2022-2032)
Annual Openings
≈23,200
openings annually (U.S. Bureau of Labor Statistics, 2022-2032)
Top Industries
Typical Education
High school diploma or equivalent; often combined with on-the-job training, vocational school, or an apprenticeship
What is a Boring Mill Operator for Metal?
A Boring Mill Operator for Metal is a highly skilled machinist who specializes in operating large, precision machine tools known as boring mills. These machines are designed to enlarge and refine existing holes or create new, highly accurate cylindrical cavities in large, often heavy, metal workpieces. The operator ensures that these holes meet extremely tight dimensional tolerances and surface finish requirements, which are critical for the functionality of complex machinery, engines, and structural components.
This role differs from a general Machinist or CNC Operator by its specific focus on boring operations and the handling of significantly larger and heavier parts. While a CNC Operator might work on a variety of smaller milling or turning machines, a Boring Mill Operator's expertise lies in the intricacies of large-scale boring, including fixture design, tool selection for deep holes, and managing the unique challenges of machining massive metal castings or fabrications. They are crucial for industries requiring precision in heavy manufacturing, such as aerospace, energy, and heavy equipment.
What does a Boring Mill Operator for Metal do?
Key Responsibilities
- Interpret complex blueprints and engineering drawings to understand precise dimensions, tolerances, and machining requirements for large metal components.
- Set up horizontal or vertical boring mills by selecting and installing appropriate cutting tools, fixtures, and workholding devices, ensuring secure clamping of heavy workpieces.
- Program machine controls (CNC) or manually adjust machine settings for feed rates, spindle speeds, and depth of cut to achieve specified finishes and dimensions.
- Monitor the machining process closely, listening for unusual sounds, observing chip formation, and adjusting parameters as needed to prevent tool wear or workpiece damage.
- Perform in-process inspections using precision measuring tools like micrometers, calipers, and bore gauges to verify that machined features meet tight tolerances.
- Conduct routine maintenance on the boring mill, including lubrication, cleaning, and minor troubleshooting, to ensure optimal performance and longevity.
- Document machining operations, including setup sheets, inspection results, and any deviations or issues encountered during the production run.
Work Environment
Boring Mill Operators typically work in manufacturing plants, machine shops, or heavy industrial facilities. The environment is often noisy due to machinery, and safety gear, including hearing protection and safety glasses, is mandatory. They frequently stand for long periods and may lift or maneuver heavy components with assistance. Collaboration occurs with other machinists, quality control inspectors, and supervisors. Work schedules often involve standard shifts, but overtime or rotating shifts are common in facilities with continuous production. The pace is steady and precise, requiring high concentration and attention to detail, as errors can be costly.
Tools & Technologies
Boring Mill Operators primarily use large horizontal and vertical boring mills, which can be manual, semi-automatic, or Computer Numerical Control (CNC) machines. Their toolkit includes a wide array of specialized cutting tools such as boring bars, inserts, reamers, and milling cutters, chosen based on the material and desired finish. Precision measuring instruments like micrometers, bore gauges, calipers, depth gauges, and optical comparators are essential for quality control. They also work with overhead cranes or forklifts for material handling of heavy workpieces. Software for CNC programming (CAM software) and machine control interfaces are critical for modern operations, along with enterprise resource planning (ERP) systems for tracking production.
Boring Mill Operator for Metal Skills & Qualifications
A Boring Mill Operator for Metal operates specialized machinery to enlarge and precisely finish holes in metal workpieces. These roles demand a blend of technical acumen, meticulous attention to detail, and practical experience. Qualification expectations for this position vary significantly based on the employer's industry, the complexity of the parts produced, and the level of automation present in the shop.
Entry-level operators often begin with vocational training or an apprenticeship, focusing on foundational machining principles and safety. More senior positions, particularly in aerospace, defense, or heavy machinery manufacturing, require extensive experience with diverse materials, advanced tooling, and complex blueprints. Certifications, such as those from the National Institute for Metalworking Skills (NIMS) in Boring, add substantial value, demonstrating validated competency beyond basic experience. While formal degrees are less common, continuous learning through manufacturer-specific training on new machinery or advanced machining techniques is crucial.
The skill landscape for Boring Mill Operators evolves with advancements in CNC technology and automation. Operators increasingly need strong computer literacy to program and monitor machines, moving beyond purely manual operations. Practical experience consistently outweighs formal degrees for this role, though a structured apprenticeship provides the most direct and respected pathway into the profession. Understanding material properties, tool wear, and precision measurement remains paramount, ensuring the operator can troubleshoot and maintain tight tolerances.
Education Requirements
Technical Skills
- Blueprint Reading and GD&T (Geometric Dimensioning and Tolerancing): Interpreting complex engineering drawings, understanding symbols, and applying GD&T principles for precise measurements.
- Manual and CNC Boring Mill Operation: Setting up, operating, and monitoring horizontal and vertical boring mills, including understanding different machine types and their capabilities.
- Tooling Selection and Setup: Choosing appropriate boring bars, inserts, and cutting tools based on material, bore size, and surface finish requirements.
- Precision Measurement Tools: Proficient use of micrometers, calipers, bore gauges, depth gauges, and CMMs (Coordinate Measuring Machines) for verifying dimensions.
- Material Science Knowledge: Understanding the properties of various metals (e.g., steel, aluminum, cast iron, exotic alloys) and how they react to machining processes.
- Machine Maintenance and Troubleshooting: Performing routine preventative maintenance, identifying common mechanical or electrical issues, and making minor repairs.
- Feeds and Speeds Calculation: Determining optimal cutting parameters (feed rate, spindle speed, depth of cut) for different materials and tooling to ensure efficiency and quality.
- Workholding and Fixturing: Securely clamping and aligning workpieces on the machine table using various fixtures, vises, and clamps to prevent movement during operation.
- Basic CNC Programming (G-code/M-code): Reading and understanding G-code and M-code for CNC boring mills, with the ability to make minor program edits at the machine interface.
- Surface Finish Control: Achieving specified surface roughness requirements through proper tooling, speeds, feeds, and coolant application.
- Coolant and Lubrication Management: Selecting and managing appropriate coolants and lubricants to extend tool life, improve surface finish, and dissipate heat.
Soft Skills
- Attention to Detail: Essential for maintaining extremely tight tolerances, reading complex blueprints, and detecting minute imperfections in finished parts.
- Problem-Solving: Crucial for diagnosing machine malfunctions, troubleshooting issues with part dimensions, and adjusting parameters to achieve desired outcomes.
- Spatial Reasoning: Important for visualizing 3D parts from 2D blueprints, planning tool paths, and understanding how machine movements affect the workpiece.
- Safety Consciousness: Paramount for operating heavy machinery, handling sharp tools, and working with hazardous materials while adhering to strict safety protocols.
- Adaptability: Necessary for switching between different types of boring operations, working with various materials, and learning new machine control interfaces.
- Mechanical Aptitude: Fundamental for understanding how machines work, performing basic maintenance, and making precise adjustments to tools and fixtures.
- Patience: Required for repetitive tasks, meticulous setup procedures, and fine-tuning operations to achieve precision without rushing.
How to Become a Boring Mill Operator for Metal
Becoming a Boring Mill Operator for Metal involves a blend of hands-on skill and precision. Entry pathways range from formal apprenticeships and vocational training programs to on-the-job learning. A complete beginner might spend 6-12 months gaining foundational knowledge before seeking an entry-level position, while someone with prior manufacturing experience could transition within 3-6 months.
Geographic location significantly impacts opportunities; manufacturing hubs in the Midwest or Southeast United States, for example, offer more openings than areas with less industrial activity. Larger corporations often seek candidates with formal training or certifications, while smaller job shops might prioritize practical experience and a willingness to learn. Understanding these nuances helps in tailoring your approach.
A common misconception is that this role is purely manual; in reality, it increasingly involves interpreting blueprints, operating CNC controls, and performing quality checks. Building a strong foundational understanding of machining principles and safety protocols is crucial, and networking with experienced operators or local machine shop owners can open doors that formal applications might not.
Step 1
Step 2
Step 3
Step 4
Step 5
Step 6
Step 7
Education & Training Needed to Become a Boring Mill Operator for Metal
Becoming a Boring Mill Operator for Metal involves a blend of formal training and practical experience. While a four-year degree is not typically required, vocational schools, community colleges, and apprenticeships offer structured pathways. These programs typically focus on blueprint reading, precision measurement, machine setup, and safe operation of boring mills. Costs for vocational programs range from $5,000 to $20,000 for a certificate, taking 6 to 18 months to complete. Apprenticeships often span 3-5 years, providing paid on-the-job training and related classroom instruction, making them a cost-effective and highly regarded option.
Employers highly value hands-on experience and certifications. Many companies prefer candidates with formal training or those who have completed a recognized apprenticeship. Self-study, while possible for foundational knowledge, does not replace the practical skills gained in a structured environment. Continuous learning is crucial, especially with advancements in CNC (Computer Numerical Control) technology, requiring operators to adapt to new machinery and software. Specialized certifications in CNC operation or specific boring mill types can significantly enhance career prospects and earning potential.
The demand for skilled Boring Mill Operators remains steady, particularly in manufacturing sectors that require precision machining. Educational needs vary; entry-level positions might accept vocational graduates, while more complex operations often seek experienced operators with advanced training or certifications. The balance between theoretical knowledge from coursework and practical application gained through apprenticeships or on-the-job training is key to success in this role. Investing in quality training directly impacts job security and career progression within the metalworking industry.
Boring Mill Operator for Metal Salary & Outlook
Compensation for Boring Mill Operators depends on several critical factors beyond basic experience. Geographic location significantly impacts earning potential; areas with a high concentration of manufacturing, such as the Midwest or parts of the Southeast, often offer higher wages due to demand and a higher cost of living. Conversely, regions with less industrial activity may see lower compensation.
Years of experience, specialized skills in operating specific types of boring mills (e.g., horizontal, vertical, CNC), and proficiency with complex materials or tight tolerances create substantial salary variations. Operators capable of programming CNC machines or performing advanced setups command premium compensation. Total compensation often extends beyond base salary to include overtime pay, production bonuses, shift differentials, and comprehensive benefits packages. These benefits typically encompass health insurance, retirement plans like 401(k)s, and sometimes even professional development allowances for certifications or advanced training.
Industry-specific trends also drive salary growth. Industries requiring precision machining, such as aerospace, defense, or medical device manufacturing, generally offer higher pay due to the stringent quality requirements and critical nature of the work. Company size and unionization can also influence pay scales, with larger companies or unionized environments often providing more structured and competitive compensation. Remote work is not applicable to this hands-on role, so geographic arbitrage opportunities are limited. While these figures are in USD, international markets may vary significantly based on local industrial demand and economic conditions.
Salary by Experience Level
Level | US Median | US Average |
---|---|---|
Junior Boring Mill Operator | $38k USD | $42k USD |
Boring Mill Operator | $52k USD | $55k USD |
Senior Boring Mill Operator | $65k USD | $68k USD |
Lead Boring Mill Operator | $75k USD | $78k USD |
Boring Mill Supervisor | $85k USD | $88k USD |
Market Commentary
The job market for Boring Mill Operators remains stable, driven by the ongoing demand for precision machined components across various industries. Manufacturing sectors like aerospace, automotive (especially in specialized parts), defense, and heavy machinery continue to rely on skilled operators for critical production. Projections indicate a modest but consistent demand, as the need for custom and high-tolerance parts persists, even with advancements in automation.
Automation and CNC technology are transforming the role rather than eliminating it. Operators now require stronger programming, troubleshooting, and setup skills. This shift creates a demand for operators who can manage complex machinery and integrate with digital workflows. The supply of highly skilled operators is often tight, particularly those proficient with advanced CNC boring mills, leading to a competitive environment for employers seeking top talent.
Emerging opportunities exist in facilities adopting advanced manufacturing techniques, including additive manufacturing (3D printing) that still requires post-processing with traditional machining. Geographic hotspots for this role include established manufacturing hubs in the Midwest (Ohio, Michigan, Indiana), the Southeast (Georgia, Alabama), and parts of Texas. This profession is relatively recession-resistant due to its foundational role in producing essential industrial components. Future-proofing involves continuous learning in CNC programming, CAD/CAM software, and advanced metrology to adapt to evolving industry standards and technologies.
Boring Mill Operator for Metal Career Path
Career progression for a Boring Mill Operator in metal fabrication typically involves a hands-on journey from foundational machine operation to advanced programming, precision machining, and eventually, leadership roles. This path emphasizes continuous skill development, particularly in interpreting complex blueprints, machine setup, and quality control. Advancing requires a deep understanding of metallurgy and precision tolerances.
Progression offers distinct pathways: remaining an individual contributor (IC) who masters increasingly complex machining tasks, or transitioning into management/leadership. Performance, a willingness to learn new technologies like CNC programming, and specialization in certain materials or highly precise components significantly influence advancement speed. Company size also plays a role; larger operations may have more structured advancement paths and specialized roles, while smaller shops might offer broader experience across different machines and materials.
Lateral movement often involves cross-training on other machine types like lathes or grinders, or moving into quality assurance or tooling design. Networking within the local manufacturing community, continuous learning through certifications in advanced machining techniques, and demonstrating a consistent commitment to safety and quality are crucial for long-term career growth. Experienced operators may also transition into training roles or technical sales for machine tool manufacturers.
Junior Boring Mill Operator
0-2 yearsKey Focus Areas
Boring Mill Operator
2-5 yearsKey Focus Areas
Senior Boring Mill Operator
5-8 yearsKey Focus Areas
Lead Boring Mill Operator
8-12 yearsKey Focus Areas
Boring Mill Supervisor
12+ yearsKey Focus Areas
Junior Boring Mill Operator
0-2 yearsOperate boring mills under direct supervision, primarily performing repetitive tasks or assisting more experienced operators. Responsibilities include loading and unloading materials, basic machine setup, and deburring finished parts. Works with pre-programmed machines and performs initial quality checks on machined components.
Key Focus Areas
Develop foundational knowledge of boring mill operation, including safety protocols, basic machine components, and material handling. Focus on tool identification, proper clamping techniques, and reading basic schematics. Learn to perform routine machine maintenance and contribute to a clean, organized workspace.
Boring Mill Operator
2-5 yearsIndependently operate boring mills to produce parts according to specifications, often working from detailed blueprints. Responsibilities include selecting appropriate tooling, setting machine parameters, and conducting in-process quality control. May assist in training junior operators and contribute to process improvement initiatives.
Key Focus Areas
Master advanced machine setup, including complex fixturing and tool path optimization. Develop strong blueprint reading skills, including understanding GD&T (Geometric Dimensioning and Tolerancing). Begin to troubleshoot minor machine issues and perform quality inspections using precision measuring tools. Focus on increasing efficiency and reducing scrap.
Senior Boring Mill Operator
5-8 yearsLead complex machining projects, interpreting challenging blueprints and devising optimal machining strategies. Independently program and set up machines for intricate operations, often involving multi-axis movements. Troubleshoots advanced machine malfunctions and implements corrective actions. Acts as a subject matter expert for specific machining techniques.
Key Focus Areas
Specialize in complex machining projects, including exotic materials or tight tolerance requirements. Develop strong problem-solving skills for intricate machining challenges. Begin to mentor junior and mid-level operators, sharing expertise and best practices. Focus on optimizing machining processes for efficiency and cost reduction.
Lead Boring Mill Operator
8-12 yearsOversee a small team of operators, coordinating daily machining schedules and ensuring project deadlines are met. Provides technical guidance, resolves complex operational issues, and conducts initial quality audits. Participates in capacity planning and recommends new tooling or equipment to improve production capabilities.
Key Focus Areas
Develop strong leadership and communication skills, focusing on team coordination and project management. Gain expertise in advanced CAD/CAM software for programming complex parts. Focus on continuous improvement methodologies, such as Lean Manufacturing or Six Sigma, to enhance overall shop efficiency. Cultivate strong relationships with engineering and quality teams.
Boring Mill Supervisor
12+ yearsManage the entire boring mill department, overseeing all operations, personnel, and equipment. Responsible for departmental budgeting, scheduling, and ensuring adherence to safety and quality standards. Implements process improvements, evaluates new technologies, and collaborates with other departments to meet production goals. Leads performance reviews and professional development for the team.
Key Focus Areas
Develop comprehensive managerial skills, including performance management, budgeting, and resource allocation. Focus on strategic planning for shop operations, including equipment acquisition and process optimization. Cultivate strong interpersonal skills for team motivation and conflict resolution. Gain a deeper understanding of overall business objectives and how machining operations contribute to them.
Job Application Toolkit
Ace your application with our purpose-built resources:
Boring Mill Operator for Metal Resume Examples
Proven layouts and keywords hiring managers scan for.
View examplesBoring Mill Operator for Metal Cover Letter Examples
Personalizable templates that showcase your impact.
View examplesTop Boring Mill Operator for Metal Interview Questions
Practice with the questions asked most often.
View examplesBoring Mill Operator for Metal Job Description Template
Ready-to-use JD for recruiters and hiring teams.
View examplesGlobal Boring Mill Operator for Metal Opportunities
Boring Mill Operators for metal find global demand in manufacturing and heavy industry. This specialized role involves precision machining of large metal components, essential for sectors like aerospace, automotive, and energy across North America, Europe, and Asia. Regulatory standards for precision and safety vary, impacting operational procedures. Professionals seek international roles for higher wages, advanced machinery exposure, and diverse project experience. International certifications in CNC operation or specific machinery can enhance global mobility.
Global Salaries
Salaries for Boring Mill Operators vary significantly by region and experience. In North America, particularly the USA and Canada, annual salaries range from USD 50,000 to USD 80,000. Experienced operators in high-demand areas can earn up to USD 95,000. European countries like Germany and Switzerland offer EUR 45,000 to EUR 65,000 (approximately USD 48,000 to USD 70,000), reflecting strong manufacturing sectors and high living costs.
Asia-Pacific markets, such as Australia and Japan, provide AUD 60,000 to AUD 90,000 (around USD 40,000 to USD 60,000) and JPY 4 million to JPY 6 million (approximately USD 27,000 to USD 40,000) respectively. These figures often include comprehensive benefits like health insurance, retirement plans, and paid leave, which might be more extensive in Europe. Latin American countries like Mexico or Brazil typically offer lower ranges, from USD 15,000 to USD 30,000, but with a significantly lower cost of living.
Purchasing power parity indicates that lower nominal salaries in some regions can still provide a good quality of life. Tax implications also differ; for instance, European countries generally have higher income tax rates than the USA, affecting take-home pay. International experience with advanced boring mill technologies often translates into higher compensation, as employers value specialized skills. Some multinational corporations may offer standardized pay scales for intra-company transfers, adjusting for local cost of living.
Remote Work
Remote work potential for a Boring Mill Operator is very limited due to the hands-on nature of the job. Operators must be physically present to set up, operate, and monitor large machinery, and perform quality checks on metal components. The role requires direct interaction with heavy equipment and materials.
However, some aspects might involve remote collaboration. For example, programming for CNC boring mills can sometimes happen remotely, but the actual execution and oversight always require on-site presence. Digital nomad opportunities are not applicable for this role. Employers typically do not hire Boring Mill Operators for international remote work due to the specialized equipment and safety protocols involved. Salary expectations are tied to on-site work; geographic arbitrage is not a factor. Companies do not commonly list international remote positions for this profession. Essential requirements include physical access to the boring mill, specialized tools, and a factory environment.
Visa & Immigration
Boring Mill Operators seeking international work typically apply for skilled worker visas. Countries like Canada (through Express Entry), Australia (Skilled Nominated Visa), and Germany (Job Seeker or Skilled Immigration Act) often have pathways for skilled trades. Requirements usually include demonstrating professional experience, relevant certifications, and often a job offer from an employer. Education credential recognition is crucial; applicants may need to have their trade qualifications assessed.
Specific requirements for 2025 vary by country. Germany requires vocational training equivalence. Canada assesses skills based on the National Occupational Classification (NOC) system. The typical visa timeline ranges from 6 to 18 months. Language tests, such as IELTS for English-speaking countries or Goethe-Zertifikat for Germany, are frequently mandatory. Some countries offer fast-track programs for in-demand trades. Pathways to permanent residency and citizenship exist through continuous skilled employment. Practical considerations include securing family visas for dependents and understanding local labor laws.
2025 Market Reality for Boring Mill Operator for Metals
Understanding the current market realities for Boring Mill Operators is vital for career success. This role has seen unique shifts since 2023, influenced by post-pandemic supply chain adjustments and the accelerating integration of advanced manufacturing technologies.
Broader economic factors, such as industrial output and infrastructure spending, directly impact job availability. Market conditions vary by experience level; entry-level positions are scarce, while experienced operators are highly sought after. Geographic location and the presence of heavy industry significantly influence local demand. This analysis provides an honest assessment of these dynamics, helping operators navigate the current landscape.
Current Challenges
Finding experienced Boring Mill Operators remains a significant challenge. The aging workforce and a limited pipeline of new talent create a skills gap. Economic shifts can impact manufacturing output, leading to fluctuating demand for operators. Competition for skilled individuals is high among specialized fabrication shops.
Growth Opportunities
Opportunities for Boring Mill Operators are strong in niche manufacturing sectors requiring extreme precision and large-scale component fabrication. Industries like aerospace, defense, heavy equipment manufacturing, and energy infrastructure consistently seek experienced operators.
Specializing in complex geometries, exotic materials, or large-format boring operations creates distinct advantages. Operators who can program advanced CNC boring mills or integrate digital metrology tools into their workflow are particularly valuable. Companies are willing to invest in operators who demonstrate a blend of traditional machining expertise and modern technological proficiency.
Underserved markets exist in regions with new industrial investments or where an older workforce is retiring rapidly, creating talent vacuums. Strategic career moves involve targeting companies with long-term contracts in stable sectors. Investing in certifications for advanced machining techniques or specific control systems can significantly enhance marketability, allowing operators to command higher wages and secure stable positions.
Current Market Trends
Demand for skilled Boring Mill Operators remains steady in 2025, driven by ongoing infrastructure projects and specialized manufacturing needs. Companies seek operators capable of handling complex, large-scale components, often requiring precision beyond standard CNC milling. The shift towards automation in other machining areas has not fully replaced the need for human expertise in intricate boring operations.
Economic conditions in 2024 saw some cautious hiring, but 2025 shows renewed investment in heavy machinery and custom fabrication, bolstering demand. Generative AI primarily assists in design and programming, but human operators still manage the physical setup, tool changes, and real-time adjustments crucial for large boring mills. This preserves a critical human element in the process.
Employers increasingly look for operators with strong blueprint reading skills, advanced metrology knowledge, and the ability to troubleshoot complex machining issues. Experience with various materials, from high-strength alloys to composites, also provides a competitive edge. Salary trends show a slight upward trajectory for highly skilled operators, reflecting the specialized nature of the role and the persistent talent shortage.
Geographically, demand concentrates in regions with heavy industries, aerospace, defense, and large-scale energy sectors. Remote work is not applicable here, as the role requires hands-on machine operation. Seasonal patterns are less pronounced than in other sectors, with demand tied more to long-term project cycles and industrial investment.
Emerging Specializations
The landscape for Boring Mill Operators is evolving, driven by advancements in automation, materials science, and digital integration within manufacturing. Understanding these shifts creates new specialization opportunities. Early positioning in these emerging areas is crucial for career advancement in 2025 and beyond, allowing operators to become indispensable assets in modern production environments.
Specializing in cutting-edge techniques often commands premium compensation and offers accelerated career growth. While established machining practices remain foundational, embracing new technologies opens doors to roles with greater complexity and strategic importance. The timeline for these emerging areas to become mainstream and create significant job opportunities varies, but many are already gaining traction, moving from niche applications to broader industry adoption.
Pursuing emerging specializations involves a strategic risk-reward calculation. It requires continuous learning and adaptability, but the reward is a future-proof career with enhanced market value. Balancing the pursuit of these forward-looking areas with a solid understanding of traditional operations ensures a robust and adaptable skill set, positioning operators for long-term success in an increasingly sophisticated manufacturing sector.
Robotics-Integrated Boring Mill Operator
Advanced Materials Boring Specialist
IoT & Data-Driven Boring Mill Operator
Hybrid Manufacturing Boring Specialist
Precision Metrology Boring Mill Operator
Pros & Cons of Being a Boring Mill Operator for Metal
Making informed career decisions requires a thorough understanding of both the benefits and challenges of a specific profession. The experience of a Boring Mill Operator for Metal can vary significantly based on the company's size, the industry served, the type of machinery used, and the specific projects undertaken.
Pros and cons may also shift as an operator gains more experience, moving from entry-level tasks to more complex operations. What one individual considers an advantage, such as a highly structured work environment, another might view as a disadvantage. This assessment aims to provide an honest, balanced perspective to help individuals set realistic expectations for a career in this specialized machining field.
Pros
- Boring mill operators possess a highly specialized skill set in precision machining, ensuring consistent demand for their expertise across various manufacturing industries.
- This role offers the satisfaction of producing tangible, high-precision metal components essential for various applications, from aerospace to heavy machinery.
- Many companies provide on-the-job training and apprenticeships, allowing individuals to enter this field without a four-year degree and develop valuable skills.
- Experienced boring mill operators can achieve competitive wages, especially those with advanced skills in CNC programming or working with exotic metals.
- The work often involves problem-solving, such as optimizing machine settings or identifying material inconsistencies, which provides intellectual stimulation.
- Working as a boring mill operator often provides a stable work environment, as precision machining is a fundamental requirement in many industrial sectors regardless of economic shifts.
- Operators contribute directly to the production process, seeing the immediate results of their work and understanding their critical role in the manufacturing supply chain.
Cons
- Boring mill operators often work with heavy, sharp metal parts and powerful machinery, which poses significant risks of injury if safety protocols are not strictly followed.
- The work environment in a machine shop can be noisy due to machinery operation and often involves exposure to coolants, lubricants, and metal dust, necessitating personal protective equipment.
- Operating complex boring mills requires continuous attention to detail, precision, and repetitive tasks, which can lead to mental fatigue over long shifts.
- While there is demand, the role can be physically demanding, requiring standing for long periods, lifting heavy workpieces, and repetitive movements that may contribute to musculoskeletal issues.
- Advancement opportunities for a dedicated boring mill operator may be limited to lead operator roles or moving into programming/supervisory positions, which requires additional training.
- Troubleshooting machine malfunctions or unexpected material behaviors under tight deadlines can create high-pressure situations, requiring quick and accurate problem-solving.
- Some projects may require working irregular hours, including evenings, nights, or weekends, especially when production deadlines are tight or specialized parts are needed quickly by clients.
Frequently Asked Questions
Boring Mill Operators for Metal face distinct challenges around precision, material handling, and machine setup. This section addresses common questions about entering this specialized trade, from mastering large-scale machining techniques to ensuring safety and career stability in manufacturing.
What are the typical entry requirements or educational paths to become a Boring Mill Operator?
Most Boring Mill Operators gain skills through vocational training, apprenticeships, or on-the-job experience. While a formal degree is not always required, completing a machining or manufacturing program from a technical school provides a strong foundation in blueprint reading, metallurgy, and CNC programming. Apprenticeships offer comprehensive hands-on training, typically lasting 3-4 years, which prepares you for complex operations and safety protocols specific to large-scale boring mills.
How long does it take to become proficient enough to work as a Boring Mill Operator?
The timeline to become job-ready as an entry-level Boring Mill Operator varies. If you enroll in a vocational program, it might take 6-12 months. An apprenticeship typically takes 3-4 years, but you earn wages while learning and gain significant experience. Self-taught individuals or those with prior machining experience might transition faster, but demonstrating proficiency with large machines and complex setups is crucial for employers.
What are the salary expectations for a Boring Mill Operator, both entry-level and experienced?
Starting salaries for entry-level Boring Mill Operators typically range from $18 to $25 per hour, depending on location, employer, and prior experience. Experienced operators with expertise in complex setups or CNC programming can earn $28 to $35+ per hour. Overtime opportunities are common in manufacturing, which can significantly increase annual earnings. Benefits packages, including health insurance and retirement plans, are also standard.
What is the typical work-life balance like, considering potential shifts or overtime?
The work-life balance for a Boring Mill Operator often involves working set shifts, which can include evenings or weekends, especially in facilities with 24/7 operations. The work is physically demanding, requiring standing for long periods and lifting. While the job is consistent, opportunities for remote work are non-existent due to the nature of operating heavy machinery. You should expect a structured work environment focused on production schedules.
Is the job of a Boring Mill Operator secure, or is it at risk from automation?
Job security for skilled Boring Mill Operators remains strong, especially for those proficient with CNC machines and complex materials. As manufacturing evolves, the demand for operators who can program and troubleshoot advanced boring mills increases. While some automation impacts routine tasks, the need for human oversight, setup, and precision finishing ensures a steady demand for skilled professionals in this specialized trade.
What are the career advancement opportunities for a Boring Mill Operator?
Career growth for a Boring Mill Operator can lead to several advanced roles. You might specialize in complex materials or highly precise operations, becoming a lead operator or trainer. Opportunities also exist to move into supervisory positions, quality control, or machine programming. Some operators transition into maintenance roles, leveraging their understanding of machine mechanics. Continuous learning, especially in CNC advancements, is key to progression.
What are the biggest challenges or frustrations faced by Boring Mill Operators?
The most significant challenge for Boring Mill Operators is maintaining extreme precision on large-scale parts, often with tight tolerances. This requires meticulous attention to detail, strong problem-solving skills, and a deep understanding of tooling and material properties. Ensuring safety around heavy machinery and managing chip evacuation are also constant considerations. Adapting to new machine technologies and programming languages is another ongoing challenge.
Can Boring Mill Operators work remotely, or is it strictly an on-site role?
As a Boring Mill Operator, your work is inherently location-dependent, requiring you to be physically present to operate the machinery. Remote work is not an option for this role. Job opportunities are concentrated in areas with strong manufacturing sectors, particularly industries that produce large metal components like aerospace, heavy equipment, and energy. You may need to relocate to find the best career opportunities in specific manufacturing hubs.
Related Careers
Explore similar roles that might align with your interests and skills:
Bore Mill Operator for Plastic
A growing field with similar skill requirements and career progression opportunities.
Explore career guideDrill Press Operator for Metal
A growing field with similar skill requirements and career progression opportunities.
Explore career guideHorizontal Boring Mill Operator for Metal
A growing field with similar skill requirements and career progression opportunities.
Explore career guideJig Boring Machine Operator
A growing field with similar skill requirements and career progression opportunities.
Explore career guideMetal Milling Machine Operator
A growing field with similar skill requirements and career progression opportunities.
Explore career guideAssess your Boring Mill Operator for Metal readiness
Understanding where you stand today is the first step toward your career goals. Our Career Coach helps identify skill gaps and create personalized plans.
Skills Gap Analysis
Get a detailed assessment of your current skills versus Boring Mill Operator for Metal requirements. Our AI Career Coach identifies specific areas for improvement with personalized recommendations.
See your skills gapCareer Readiness Assessment
Evaluate your overall readiness for Boring Mill Operator for Metal roles with our AI Career Coach. Receive personalized recommendations for education, projects, and experience to boost your competitiveness.
Assess your readinessSimple pricing, powerful features
Upgrade to Himalayas Plus and turbocharge your job search.
Himalayas
Himalayas Plus
Himalayas Max
Find your dream job
Sign up now and join over 100,000 remote workers who receive personalized job alerts, curated job matches, and more for free!
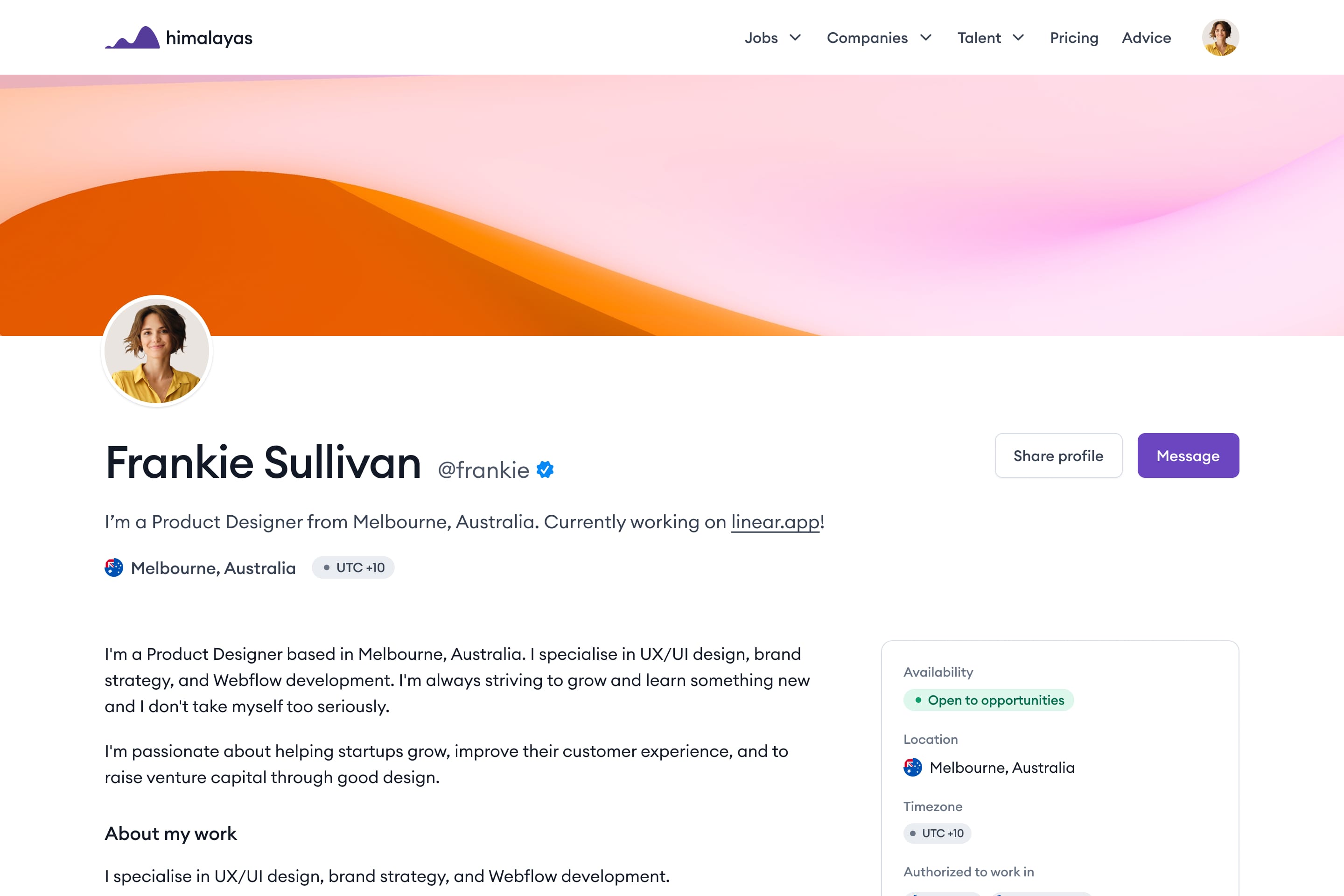