Complete Drill Press Operator for Metal Career Guide
Drill press operators are precision craftspeople essential to manufacturing, meticulously shaping metal components that form the backbone of industries from automotive to aerospace. You will use specialized machinery to create precise holes and features, ensuring parts meet exact specifications for complex assemblies. This role offers a tangible impact on product quality and a stable career path for those who value hands-on work and attention to detail.
Key Facts & Statistics
Median Salary
$46,650 USD
(U.S. national median, Source: BLS, May 2023)
Range: $35k - $65k+ USD
Growth Outlook
1%
as fast as average (Source: BLS, 2022-2032)
Annual Openings
≈33k
openings annually (Source: BLS, 2022-2032)
Top Industries
Typical Education
High school diploma or equivalent; on-the-job training is common, with some opting for vocational training or an associate's degree in machining.
What is a Drill Press Operator for Metal?
A Drill Press Operator for Metal is a skilled manufacturing professional who precisely creates holes and performs related operations in metal workpieces using a drill press machine. This role involves interpreting engineering blueprints, setting up the machine with appropriate tools and settings, and operating it to achieve exact specifications for depth, diameter, and location.
Unlike a general machinist who might operate a variety of machines like lathes, mills, and grinders, a Drill Press Operator specializes specifically in drilling, boring, reaming, and tapping operations. Their expertise lies in understanding the nuances of drilling different metal types, maintaining drill press equipment, and ensuring hole quality. This specialization is crucial for industries requiring high-volume, accurate hole production in metal components.
What does a Drill Press Operator for Metal do?
Key Responsibilities
- Set up and adjust drill press machines, including selecting correct drill bits, speeds, and feed rates based on material specifications and blueprint requirements.
- Load raw metal workpieces onto the drill press table, securing them with clamps, vises, or fixtures to ensure stability and precise drilling.
- Operate manual or automated drill presses to bore holes, tap threads, countersink, or ream metal parts, closely monitoring the drilling process for accuracy.
- Inspect finished parts for dimensional accuracy, hole quality, and surface finish using precision measuring tools such as calipers, micrometers, and gauges.
- Perform routine maintenance on drill press machines, including cleaning, lubricating, and replacing worn drill bits or other components to ensure optimal performance.
- Interpret engineering blueprints, schematics, and work orders to understand hole locations, depths, diameters, and other critical specifications for each part.
- Maintain a clean and organized work area, adhering to all safety protocols and using personal protective equipment to prevent accidents and injuries.
Work Environment
Drill press operators typically work in manufacturing plants, machine shops, or fabrication facilities. These environments are often noisy due to machinery operation and may involve exposure to metal shavings, coolants, and lubricants. The work is usually performed standing for extended periods, and it requires physical dexterity and strength to handle metal workpieces.
Collaboration occurs with other machinists, welders, and production supervisors to ensure parts meet specifications and production schedules. Shifts can vary, including day, evening, or night shifts, and overtime may be required to meet production demands. The pace of work is steady, driven by production quotas and the need for precision.
Tools & Technologies
Drill press operators primarily use various types of drill press machines, including manual, automatic, and CNC-controlled models. They work with a wide assortment of drill bits, reamers, taps, and countersinks, selecting the appropriate tool for each task.
Precision measuring instruments are essential, such as calipers, micrometers, depth gauges, and bore gauges, to verify hole specifications and overall part accuracy. Operators also utilize hand tools for setup and maintenance, including wrenches and screwdrivers. Safety equipment like safety glasses, gloves, and ear protection are mandatory for daily operations.
Drill Press Operator for Metal Skills & Qualifications
A Drill Press Operator for Metal plays a crucial role in manufacturing, shaping raw metal into precision components. Qualifications for this role are primarily practical, emphasizing hands-on experience and a strong understanding of machining principles. Formal education often takes a backseat to demonstrated competency and a proven track record in a machine shop environment.
Requirements for this position vary based on the complexity of the parts, the type of machinery used (manual vs. CNC), and the industry sector. For instance, aerospace or medical device manufacturing demands higher precision and stricter quality control, requiring more experienced operators. Smaller job shops might prioritize versatility across different machines, while larger production facilities may seek specialists in high-volume drilling operations.
While a high school diploma is standard, vocational training or apprenticeships significantly enhance a candidate's appeal. Certifications in machining or specific equipment operation add substantial value, particularly in a competitive market. The skill landscape is evolving with increasing automation; operators must adapt to working with CNC drill presses and understanding basic programming, even if their primary role remains manual operation. Maintaining a balance between traditional mechanical aptitude and emerging digital literacy is vital for long-term career viability.
Education Requirements
Technical Skills
- Blueprint and technical drawing interpretation, including GD&T (Geometric Dimensioning and Tolerancing)
- Measurement tools proficiency (calipers, micrometers, depth gauges, protractors)
- Drill bit selection and sharpening (understanding material compatibility and optimal cutting angles)
- Machine setup and adjustment (speed, feed rate, depth stops, clamping mechanisms)
- Material handling and securing workpieces (using vises, clamps, jigs)
- Lubrication and coolant application (understanding types and proper use)
- Preventive machine maintenance and cleaning
- Basic metallurgy (understanding properties of different metals like steel, aluminum, brass)
- Quality control and inspection procedures (identifying burrs, out-of-spec holes)
- Troubleshooting common drilling issues (chatter, breakage, overheating)
- Knowledge of safety procedures and lockout/tagout protocols
- Basic CNC drill press operation (for automated or semi-automated machines)
Soft Skills
- Attention to Detail: Critical for ensuring precise hole placement, depth, and diameter, preventing costly errors and material waste.
- Problem-Solving: Operators must identify and troubleshoot issues like drill bit wear, material inconsistencies, or machine malfunctions.
- Safety Consciousness: Essential for adhering to strict safety protocols, operating heavy machinery responsibly, and preventing workplace injuries.
- Manual Dexterity and Hand-Eye Coordination: Necessary for accurately positioning workpieces, manipulating controls, and handling tools with precision.
- Work Ethic and Reliability: Consistent attendance and dedication are vital for maintaining production schedules and contributing to team output.
- Adaptability: Operators must adjust to different metal types, drill bits, machine settings, and production demands.
- Communication: Clear communication with supervisors and fellow operators is important for reporting issues, coordinating tasks, and ensuring smooth workflow.
- Patience: Achieving precise results often requires careful, deliberate work, especially with complex or delicate materials.
How to Become a Drill Press Operator for Metal
Becoming a Drill Press Operator for metal involves precision, safety, and a keen eye for detail, rather than just brute strength. Entry into this field can range from a few weeks of dedicated self-study and on-the-job training to several months in a vocational program or apprenticeship. Many smaller fabrication shops prioritize practical aptitude and a willingness to learn over formal degrees, offering entry-level roles that provide direct training.
Traditional entry routes often involve vocational school programs in machining or manufacturing, providing a structured learning environment. However, a significant number of operators enter through hands-on experience, starting as shop assistants or production helpers and learning directly from experienced machinists. Larger corporations might prefer candidates with some formal training, while smaller custom shops often value immediate availability and a strong work ethic.
The hiring landscape for these roles remains steady, driven by ongoing manufacturing needs. Overcoming entry barriers typically involves demonstrating basic math skills, an understanding of measurement tools, and an unwavering commitment to workplace safety. Networking with local manufacturing businesses and attending industry job fairs can open doors that online applications might not, showcasing your enthusiasm and hands-on readiness.
Step 1
Step 2
Step 3
Step 4
Step 5
Step 6
Step 7
Education & Training Needed to Become a Drill Press Operator for Metal
Becoming a Drill Press Operator for Metal typically involves hands-on training rather than formal degree programs. Most employers prioritize practical experience, safety knowledge, and the ability to read blueprints and precision measurements. While a four-year degree is unnecessary, vocational programs or apprenticeships offer structured learning, often costing $5,000-$15,000 and taking 6-18 months. These programs teach machine operation, material properties, and safety protocols. Self-study and on-the-job training are also common, with initial roles often requiring 3-6 months of supervised work to gain proficiency.
Employer acceptance of credentials varies. Larger manufacturing companies may prefer candidates with vocational certifications, signaling a foundational understanding of machining principles. Smaller shops might value direct work experience and a proven ability to learn quickly on the job. Continuous learning focuses on mastering new machinery, tooling, and advanced machining techniques, which can lead to roles as CNC operators or machinists. This ongoing development often happens through employer-sponsored training or short courses.
The cost-benefit analysis for a drill press operator favors practical, shorter-term training. Investing in a vocational certificate or an apprenticeship provides a clear path to employment without the significant time and financial commitment of a degree. Industry-specific certifications, such as those from the National Institute for Metalworking Skills (NIMS), demonstrate competence and can enhance job prospects, particularly in shops with high-precision requirements. Theoretical knowledge supports practical skills, but hands-on application remains paramount for success in this role.
Drill Press Operator for Metal Salary & Outlook
Compensation for a Drill Press Operator for Metal depends on several key factors. Geographic location significantly impacts earnings, with higher wages often found in areas with a strong manufacturing base or higher cost of living. For instance, salaries in industrial hubs like the Midwest or Southeast United States may differ from those in the Northeast or West Coast.
Years of experience, specific certifications, and the ability to operate advanced CNC (Computer Numerical Control) drill presses or perform complex setups create dramatic salary variations. Operators with expertise in precision machining or working with specialized metals can command higher pay. Total compensation extends beyond base salary to include overtime pay, production bonuses, and benefits packages, which often cover health insurance, retirement contributions like 401(k)s, and sometimes even tool allowances.
Industry-specific trends, such as demand from aerospace, automotive, or general fabrication sectors, drive salary growth. Companies offering advanced training or opportunities to cross-train on other machinery may also offer better compensation. Remote work is not applicable for this hands-on role, but the ability to work shifts, including nights or weekends, can often lead to higher hourly rates. Salary figures are primarily based on the USD market, with international variations subject to local labor laws and economic conditions.
Salary by Experience Level
Level | US Median | US Average |
---|---|---|
Junior Drill Press Operator | $36k USD | $38k USD |
Drill Press Operator | $44k USD | $46k USD |
Senior Drill Press Operator | $53k USD | $55k USD |
Lead Drill Press Operator | $60k USD | $62k USD |
Machining Supervisor | $72k USD | $75k USD |
Market Commentary
The job market for Drill Press Operators for Metal shows steady demand, driven by the ongoing need for manufactured goods across various industries. While some traditional machining tasks face automation, skilled operators capable of complex setups, quality control, and troubleshooting remain essential. The U.S. Bureau of Labor Statistics projects a slight decline in overall machining occupations, but the need for specialized manual and CNC operators persists.
Emerging opportunities include roles in precision manufacturing for medical devices, aerospace components, and custom fabrication, which require high levels of accuracy and specialized material handling. The supply of highly skilled operators is often tight, creating a demand-supply imbalance that can favor experienced candidates. This imbalance is particularly noticeable for those proficient with modern CNC equipment and advanced tooling.
Future-proofing in this role involves continuous learning in CNC programming, advanced metrology, and understanding new materials. While automation handles repetitive tasks, human oversight for complex operations, maintenance, and quality assurance remains critical. This profession is tied to manufacturing cycles, making it somewhat cyclical but generally recession-resistant for skilled individuals as essential goods production continues. Geographic hotspots include industrial corridors in states like Michigan, Ohio, Texas, and parts of California, where manufacturing activity is concentrated.
Drill Press Operator for Metal Career Path
Career progression for a Drill Press Operator for Metal typically begins with hands-on foundational work and advances through increasing levels of machine mastery, precision, and leadership. Advancement pathways often involve a clear distinction between becoming a highly skilled individual contributor (IC) focusing on complex operations and materials, or transitioning into a management/leadership track overseeing teams and production lines.
Factors influencing advancement speed include demonstrated precision, efficiency, safety adherence, and the ability to troubleshoot machine issues. Specialization in particular materials, complex geometries, or advanced drilling techniques can accelerate progression. Company size also plays a role; smaller shops might offer quicker advancement to supervisory roles due to flatter hierarchies, while larger manufacturers may have more structured, but slower, progression paths with more opportunities for diverse machine training.
Continuous learning through certifications in advanced machining, CAD/CAM software, or lean manufacturing principles marks significant progression. Networking within the manufacturing community and seeking mentorship from experienced machinists or supervisors can open doors to new opportunities. Lateral moves might involve training on other types of machining equipment, such as lathes or milling machines, broadening a professional's overall manufacturing skillset. Common career pivots include becoming a Quality Control Inspector, a Tool and Die Maker, or a Manufacturing Trainer.
Junior Drill Press Operator
0-2 yearsKey Focus Areas
Drill Press Operator
2-5 yearsKey Focus Areas
Senior Drill Press Operator
5-8 yearsKey Focus Areas
Lead Drill Press Operator
8-12 yearsKey Focus Areas
Machining Supervisor
12+ yearsKey Focus Areas
Junior Drill Press Operator
0-2 yearsOperate drill press machines under direct supervision, performing routine drilling tasks on metal components. Follow clear instructions and blueprints for hole specifications, depths, and tolerances. Responsible for loading and unloading materials, maintaining a clean work area, and reporting any machine malfunctions or quality issues. Work involves minimal decision-making authority.
Key Focus Areas
Develop strong foundational skills in machine setup, tool selection, and basic drilling operations. Focus on safety protocols, proper material handling, and understanding blueprints for simple parts. Learn to identify common drilling issues and perform basic machine maintenance. Gain familiarity with different metal types and their drilling characteristics.
Drill Press Operator
2-5 yearsOperate drill press machines independently, producing components to precise specifications with minimal supervision. Interpret complex blueprints and work orders, making decisions on tooling and setup adjustments for optimal output. Responsible for quality checks of finished parts, basic machine calibration, and maintaining production schedules. May assist in training junior operators.
Key Focus Areas
Master various drilling techniques, including tapping, reaming, and counterboring. Focus on optimizing machine speeds and feeds for different materials and hole requirements. Develop advanced blueprint reading skills, including GD&T (Geometric Dimensioning and Tolerancing). Begin troubleshooting minor machine issues and performing more complex setups independently.
Senior Drill Press Operator
5-8 yearsServe as a subject matter expert for drill press operations, handling the most complex and critical drilling tasks with high precision. Provide technical guidance and support to other operators, assisting with difficult setups and troubleshooting advanced machine issues. Responsible for maintaining strict quality standards and contributing to process improvement initiatives. May lead small, specialized production runs.
Key Focus Areas
Expertise in advanced machining techniques, including working with exotic alloys and complex part geometries. Focus on process optimization, reducing cycle times, and minimizing material waste. Develop strong problem-solving skills for complex machining challenges. Begin mentoring and providing technical guidance to less experienced operators. Understanding of lean manufacturing principles.
Lead Drill Press Operator
8-12 yearsLead a team of drill press operators, overseeing daily production activities, ensuring adherence to schedules, and maintaining quality standards. Responsible for assigning tasks, monitoring operator performance, and providing on-the-job training and mentorship. Troubleshoot complex production issues and coordinate with other departments to optimize workflow. May participate in equipment selection.
Key Focus Areas
Develop strong leadership and communication skills, effectively delegating tasks and providing constructive feedback. Focus on production scheduling, workflow optimization, and resource allocation. Gain expertise in identifying and implementing continuous improvement opportunities. Understand basic supervisory responsibilities, including performance reviews and conflict resolution.
Machining Supervisor
12+ yearsOversee all machining operations within a specific department or shift, including drill press, milling, and lathe operations. Manage a team of lead operators and machinists, responsible for scheduling, performance management, and ensuring production targets are met efficiently and safely. Implement continuous improvement initiatives and contribute to strategic planning for the manufacturing floor.
Key Focus Areas
Master production planning, resource management, and departmental budgeting. Focus on strategic oversight of machining operations, identifying opportunities for technological upgrades and process automation. Develop strong interpersonal skills for team leadership, performance management, and cross-departmental collaboration. Understanding of overall manufacturing goals and business objectives.
Job Application Toolkit
Ace your application with our purpose-built resources:
Drill Press Operator for Metal Resume Examples
Proven layouts and keywords hiring managers scan for.
View examplesDrill Press Operator for Metal Cover Letter Examples
Personalizable templates that showcase your impact.
View examplesTop Drill Press Operator for Metal Interview Questions
Practice with the questions asked most often.
View examplesDrill Press Operator for Metal Job Description Template
Ready-to-use JD for recruiters and hiring teams.
View examplesGlobal Drill Press Operator for Metal Opportunities
Drill press operators for metal find opportunities globally, particularly in manufacturing hubs across Asia, Europe, and North America. This role involves precision machining, a skill consistently in demand for industrial production. Regulatory differences primarily affect safety standards and equipment certifications. Professionals seek international work for better wages or specialized industry exposure. No specific international certifications exist, but vocational training recognition helps mobility.
Global Salaries
Salaries for drill press operators vary significantly by region and cost of living. In North America, specifically the United States, annual wages typically range from $35,000 to $55,000 USD. Canadian operators earn CAD 40,000 to CAD 60,000 annually, roughly $29,000 to $44,000 USD, often with comprehensive benefits.
European salaries differ widely. In Germany, a major manufacturing economy, operators can expect €30,000 to €45,000 per year ($32,000 to $48,000 USD). The UK offers £25,000 to £35,000 ($31,000 to $44,000 USD). These figures reflect higher purchasing power in Germany due to strong social benefits and lower cost of living outside major cities compared to the US.
Asia-Pacific markets present diverse compensation. Australian operators might earn AUD 50,000 to AUD 70,000 ($33,000 to $46,000 USD). In contrast, China's manufacturing sector pays CNY 60,000 to CNY 100,000 ($8,500 to $14,000 USD), with a much lower cost of living. Experience and specific machine expertise directly impact earning potential globally.
Latin America offers lower wages, with Mexico paying MXN 90,000 to MXN 150,000 ($5,000 to $8,500 USD) annually. Taxation and benefit structures vary, impacting take-home pay. For instance, European countries often have higher taxes but provide universal healthcare and generous vacation time, which can offset lower nominal salaries compared to the US.
Remote Work
Drill press operation is a hands-on, on-site role. It requires direct interaction with machinery and physical materials, making international remote work impossible for this profession. There are no digital nomad opportunities specific to a drill press operator.
Employers in this field do not typically offer international remote work. The nature of the job demands physical presence in a manufacturing facility. Salary expectations are tied to the local labor market where the physical work occurs. Companies hiring for this role focus on local recruitment or skilled migration, not remote arrangements. Equipment and workspace setup are entirely facility-dependent.
Visa & Immigration
Skilled worker visas are the primary pathway for drill press operators seeking international employment. Countries like Canada, Australia, and Germany have specific programs for skilled trades. Requirements often include proof of relevant vocational training or apprenticeships and several years of experience.
Canada's Federal Skilled Trades Program or Provincial Nominee Programs frequently list machining roles. Germany's skilled immigration law facilitates entry for non-EU workers with recognized qualifications. Australia's skilled occupation lists sometimes include metal machinists. Education credential recognition is crucial; applicants often need assessments confirming their qualifications meet local standards.
Visa application timelines vary, from a few months to over a year, depending on the country and specific program. Language proficiency tests, typically in English or the destination country's official language, are often required. While no fast-track programs exist solely for drill press operators, their inclusion on skilled occupation lists in some countries can expedite the process. Family visas are generally available for accompanying dependents once the primary applicant secures their work visa.
2025 Market Reality for Drill Press Operator for Metals
Understanding current market conditions is crucial for drill press operators. The manufacturing landscape has evolved significantly from 2023 to 2025, influenced by post-pandemic supply chain adjustments and increasing automation. Broader economic factors, such as industrial output fluctuations, directly impact job availability in this field.
Market realities for drill press operators vary by experience level, from entry-level positions often facing automation threats to experienced operators who can adapt to new technologies. Geographic location and the size of manufacturing operations also play a critical role, with custom shops behaving differently from large production facilities. This analysis provides an honest assessment of current hiring realities for this specific trade.
Current Challenges
Finding entry-level drill press operator positions is harder due to automation and a shrinking manufacturing base in some regions. Competition increases as fewer companies hire for manual roles, preferring multi-skilled technicians. Economic slowdowns directly reduce manufacturing output, leading to fewer available shifts or temporary layoffs.
The push for higher productivity means employers expect operators to manage multiple machines or handle more complex setups, often without significant pay increases. This can create a skill gap if training is not readily available for older operators. Job search timelines for specialized roles can extend to several months, especially in areas with fewer metal fabrication shops.
Growth Opportunities
Despite automation, strong opportunities exist for drill press operators specializing in complex, custom, or low-volume precision work where CNC programming is not cost-effective. Niche sectors like aerospace component manufacturing, medical device fabrication, and specialized tool and die making continue to value manual precision and expertise.
Operators who cross-train on other manual machines, such as lathes or mills, or gain basic CNC operation and setup skills, significantly enhance their employability. Companies increasingly seek multi-skilled technicians who can adapt to diverse tasks. Learning to interpret advanced blueprints and implementing lean manufacturing principles also provides a competitive edge.
Underserved markets often include smaller, independent fabrication shops or regions with strong local industries that require custom metalwork. Strategic career moves might involve seeking roles in prototyping, repair, or specialized fabrication over high-volume production. Investing in certifications for specific materials or precision techniques can also open doors to more advanced and stable positions, particularly as economic conditions stabilize.
Current Market Trends
Demand for skilled drill press operators in metal fabrication remains steady but is not growing significantly as of 2025. Many companies are investing in CNC machining centers, which automate drilling tasks, reducing the need for dedicated manual drill press operators. However, custom shops, prototyping facilities, and repair operations still require manual precision and experienced hands.
Hiring patterns show a preference for operators who understand blueprints, can perform basic machine maintenance, and possess strong quality control skills. Employers increasingly seek individuals capable of operating other manual machines or assisting with CNC setup, rather than just a standalone drill press. The integration of basic automation and robotics in some drill press operations means operators now need to monitor automated processes or perform more complex, less repetitive tasks.
Salary trends for experienced operators show modest increases, but entry-level wages remain stagnant due to automation. Market saturation exists at the basic operational level, while skilled operators capable of intricate work or diverse machine operation find more consistent opportunities. Geographic variations are significant; areas with strong aerospace, defense, or heavy machinery manufacturing still have demand, while regions with declining traditional manufacturing see fewer openings. Remote work is not applicable for this hands-on role.
Emerging Specializations
The manufacturing landscape is undergoing significant transformation, creating new specialization opportunities even for skilled roles like Drill Press Operators. Advancements in automation, smart factory integration, and precision material processing are reshaping traditional tasks and demanding new proficiencies. Understanding these shifts and positioning oneself in emerging areas is crucial for career advancement in 2025 and beyond.
Early positioning in these evolving specializations often leads to premium compensation and enhanced career growth. As new technologies become more prevalent, demand for operators skilled in these specific niches outpaces the general workforce. This creates a competitive advantage for those who invest in acquiring relevant, forward-looking skills.
While established specializations remain important, pursuing emerging areas offers a strategic advantage. These cutting-edge fields typically transition from niche applications to mainstream adoption within a three to five-year timeframe, generating a significant number of job opportunities. Embracing these areas involves a balance of risk and reward; while initial demand might be lower, the long-term potential for stable, high-value employment is substantial.
Robotic Drill Cell Operator
This specialization focuses on operating drill presses integrated with robotic arms or collaborative robots (cobots). Operators program the robot's movements, load/unload parts, monitor automated drilling processes, and troubleshoot robotic anomalies. The role shifts from manual drilling to overseeing and optimizing automated drilling cells, ensuring high precision and throughput while maintaining safety protocols in a human-robot collaborative environment.
Smart Drill Press Data Monitor
With the rise of Industry 4.0, drill presses are increasingly equipped with advanced sensors and network capabilities. A Digital Twin Data Operator specializes in monitoring real-time data streams from these smart machines, including spindle speed, feed rate, vibration, and tool wear. They use this data to predict maintenance needs, optimize drilling parameters for efficiency, and identify potential quality issues before they arise, often working with digital twin models of the equipment.
Advanced Material Drilling Specialist
Advanced materials like composites, ceramics, and superalloys require specialized drilling techniques due to their unique properties. A Composite & Advanced Material Drilling Specialist understands the specific challenges these materials present, such as delamination, heat generation, and tool wear. They select appropriate tooling, optimize drilling parameters, and implement specialized cooling or vacuum systems to achieve precise holes without material degradation.
Additive Manufacturing Post-Process Drilling Technician
This role focuses on operating and maintaining drill presses specifically configured for additive manufacturing post-processing. As 3D-printed metal parts often require precise drilling for final assembly or feature creation, this operator specializes in handling complex geometries and materials unique to additive processes. They ensure high accuracy in drilling features into parts produced by technologies like DMLS or Binder Jetting, often involving intricate fixturing.
Micro-Drilling & Medical Device Specialist
Precision drilling for micro-components or medical devices demands extreme accuracy and specialized equipment. A Micro-Drilling & Precision Components Operator works with high-precision drill presses, often under magnification, to create holes with tolerances in the micron range. This specialization requires meticulous attention to detail, expertise in handling delicate parts, and proficiency with highly sensitive measurement tools for quality control.
Pros & Cons of Being a Drill Press Operator for Metal
Choosing a career path requires a thorough understanding of both its appealing aspects and its inherent difficulties. The experience of working as a Drill Press Operator for Metal can vary significantly based on the specific manufacturing environment, the types of parts being produced, and the overall company culture. Factors like shift patterns, the level of automation involved, and the emphasis on safety can all influence daily life. Furthermore, what one person considers a benefit, another might see as a challenge, depending on their personal preferences and career aspirations. This assessment aims to provide a realistic overview, helping individuals set appropriate expectations and determine if this role aligns with their skills and lifestyle.
Pros
Steady demand for skilled operators exists in manufacturing sectors, offering good job security as metal fabrication remains a fundamental industry.
Entry into this role often requires only a high school diploma and on-the-job training, making it accessible without extensive higher education or certifications.
The work provides a tangible sense of accomplishment, as operators directly contribute to the creation of precise components used in various products and industries.
Operators develop practical, hands-on mechanical skills and a strong understanding of metal properties and machining principles, which are valuable in manufacturing.
Work schedules are often predictable, typically involving fixed shifts (day, evening, or night), which can aid in personal planning and work-life balance.
Many facilities offer opportunities to learn about other machining operations, such as milling or turning, potentially leading to skill diversification and higher-paying roles.
The role is generally stable and less susceptible to automation compared to some other manufacturing tasks, as it often requires human judgment for setup and quality checks.
Cons
Repetitive motions can lead to physical strain and repetitive stress injuries over time, particularly affecting wrists, hands, and shoulders from repeated loading and unloading of parts.
Exposure to noise, metal dust, and coolant mists is common, requiring consistent use of personal protective equipment (PPE) and proper ventilation to mitigate health risks.
Limited career advancement opportunities exist within the role itself; progression typically involves moving into supervisory positions, quality control, or specialized machining roles.
The work environment can be hot, especially in facilities without adequate climate control, and often involves standing for long periods throughout the shift.
Strict adherence to safety protocols is critical, and any lapse can lead to serious injuries due to the powerful machinery and sharp tools involved.
The pay scale for drill press operators, while stable, may not offer significant upward mobility without acquiring additional skills in other machining processes or taking on leadership responsibilities.
Monotony can be a factor for some individuals, as the core tasks of loading, operating, and unloading the drill press remain consistent day-to-day.
Frequently Asked Questions
Drill Press Operators for Metal face distinct questions around safety, precision, and the physical demands of the role. This section addresses common concerns about entering this specific manufacturing position, from required training and work environment to career stability and potential for advancement.
What qualifications or education do I need to become a Drill Press Operator for Metal?
You typically do not need a formal degree to become a Drill Press Operator. Most employers look for a high school diploma or GED, strong mechanical aptitude, and a willingness to learn. Many companies offer on-the-job training, but vocational school programs in machining or manufacturing can provide a significant advantage and accelerate your learning curve.
How long does it take to become competent as a Drill Press Operator for Metal?
Entry-level Drill Press Operators can typically become proficient within a few months of hands-on training. Mastering the nuances of different materials, tooling, and complex blueprints takes longer, often 1-2 years of consistent practice. Your progress depends on the complexity of the parts you work on and the quality of your training.
What are the typical salary expectations for a Drill Press Operator for Metal?
Starting salaries for Drill Press Operators for Metal vary by region and experience, but typically range from $15 to $20 per hour. With experience and specialized skills, such as operating CNC drill presses or performing setup tasks, wages can increase to $20-$28 per hour or more. Overtime opportunities are often available in manufacturing, which can boost overall earnings.
What is the typical work environment and physical demand for this role?
The work environment for a Drill Press Operator is usually a manufacturing or machine shop floor. It can be noisy, and you will often be standing for long periods. Safety is paramount, requiring the use of personal protective equipment like safety glasses, hearing protection, and steel-toed boots. The work is hands-on and requires attention to detail and adherence to strict safety protocols.
Is the job of a Drill Press Operator for Metal secure, or is it at high risk from automation?
Job security for Drill Press Operators remains relatively stable, particularly in industries that rely on custom metal fabrication or specialized components. While automation impacts some roles, skilled operators who can set up machines, troubleshoot issues, and work with various materials continue to be in demand. Cross-training on other machinery can enhance your job security.
What are the career advancement opportunities for a Drill Press Operator for Metal?
Career growth for Drill Press Operators can lead to several advancement opportunities. You could become a Lead Operator, overseeing a team or specific production line, or move into a Machinist role, operating a wider range of precision machinery. Some operators advance to roles like Quality Control Inspector, CNC Programmer, or even Shop Foreman, especially with further training or certifications.
What are the main safety risks and how are they managed in this job?
The primary safety concerns include entanglement with rotating machinery, flying debris, and exposure to metal shavings or coolants. Operators must strictly follow lockout/tagout procedures, wear appropriate personal protective equipment, and maintain a clean and organized workspace. Continuous training on machine safety and emergency procedures is crucial to mitigate risks.
Related Careers
Explore similar roles that might align with your interests and skills:
Boring Mill Operator for Metal
A growing field with similar skill requirements and career progression opportunities.
Explore career guideMetal Milling Machine Operator
A growing field with similar skill requirements and career progression opportunities.
Explore career guideMetal Punch Press Operator
A growing field with similar skill requirements and career progression opportunities.
Explore career guideRadial Drill Press Operator for Plastic
A growing field with similar skill requirements and career progression opportunities.
Explore career guideScrew Machine Operator
A growing field with similar skill requirements and career progression opportunities.
Explore career guideAssess your Drill Press Operator for Metal readiness
Understanding where you stand today is the first step toward your career goals. Our Career Coach helps identify skill gaps and create personalized plans.
Skills Gap Analysis
Get a detailed assessment of your current skills versus Drill Press Operator for Metal requirements. Our AI Career Coach identifies specific areas for improvement with personalized recommendations.
See your skills gapCareer Readiness Assessment
Evaluate your overall readiness for Drill Press Operator for Metal roles with our AI Career Coach. Receive personalized recommendations for education, projects, and experience to boost your competitiveness.
Assess your readinessSimple pricing, powerful features
Upgrade to Himalayas Plus and turbocharge your job search.
Himalayas
Himalayas Plus
Himalayas Max
Find your dream job
Sign up now and join over 100,000 remote workers who receive personalized job alerts, curated job matches, and more for free!
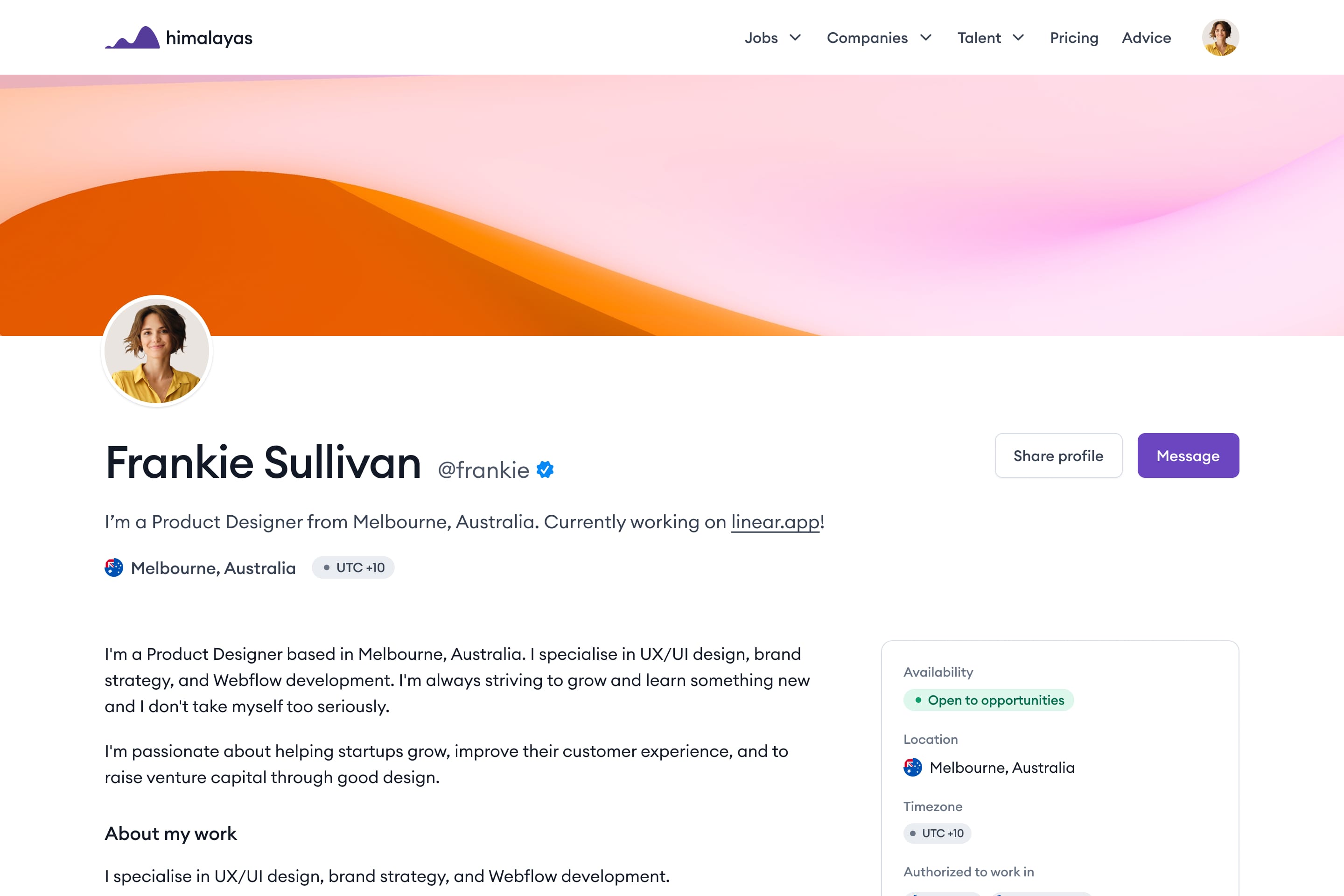