Complete Manual Machinist Career Guide
Manual machinists are skilled artisans who precisely shape metal and other materials using traditional, hand-operated machine tools like lathes, mills, and grinders. They are crucial in custom fabrication, prototyping, and repair work, where computer numerical control (CNC) machines might be less efficient or suitable. This role demands exceptional precision, problem-solving abilities, and a deep understanding of material properties, offering a hands-on career path vital to manufacturing and specialized industries.
Key Facts & Statistics
Median Salary
$55,270 USD
(U.S. national median for Machinists, BLS, May 2023)
Range: $38k - $75k+ USD (varies by experience, industry, and location)
Growth Outlook
13%
much faster than average for Machinists (BLS, 2022-2032)
Annual Openings
≈33
.2k openings annually for Machinists (including Manual and CNC), (BLS, 2022-2032)
Top Industries
Typical Education
High school diploma or equivalent; many learn through apprenticeships, vocational programs, or on-the-job training. Certifications can enhance career prospects.
What is a Manual Machinist?
A Manual Machinist is a skilled craftsperson who operates traditional, non-computerized machine tools to cut, shape, and form metal or other materials into precise components. They rely on their expertise, hand-eye coordination, and deep understanding of mechanics and materials to produce custom parts, prototypes, or repair existing machinery. This role demands meticulous attention to detail and a strong mechanical aptitude.
Unlike CNC (Computer Numerical Control) Machinists who program machines to execute automated tasks, Manual Machinists directly control the movements of their machines using handwheels and levers. This distinction means they are highly sought after for one-off jobs, intricate repairs, and situations where human judgment and adaptability are critical, offering a unique blend of craftsmanship and precision engineering.
What does a Manual Machinist do?
Key Responsibilities
- Interpret engineering blueprints and technical drawings to determine material specifications and machining sequences.
- Set up and operate conventional machine tools such as lathes, milling machines, grinders, and drill presses.
- Monitor machine operations to detect malfunctions or out-of-tolerance machining, making adjustments as necessary.
- Perform precise measurements using calipers, micrometers, and gauges to ensure parts meet strict quality standards.
- Select appropriate cutting tools, coolants, and speeds for various materials like metals and plastics.
- Conduct regular maintenance on machines, including cleaning, lubrication, and minor repairs, to ensure optimal performance.
Work Environment
Manual machinists typically work in workshops, manufacturing plants, or job shops. The environment can be noisy due to machinery and may involve exposure to coolants and metal shavings. They often work independently on specific tasks but may collaborate with engineers or other machinists on complex projects. The work is hands-on and requires standing for long periods. Safety is paramount, requiring personal protective equipment like safety glasses and steel-toed boots. Work schedules are usually standard day shifts, though some roles may involve overtime or occasional weekend work based on production demands.
Tools & Technologies
Manual machinists primarily use conventional machine tools such as engine lathes, vertical and horizontal milling machines, surface grinders, and drill presses. They rely on precision measuring instruments like micrometers, calipers, height gauges, and bore gauges to verify dimensions. Essential hand tools include wrenches, screwdrivers, and various files. They also use cutting fluids, lubricants, and various types of cutting inserts and drill bits. While not directly operating CNC machines, an understanding of basic CAD/CAM principles can be beneficial for interpreting complex drawings.
Manual Machinist Skills & Qualifications
A Manual Machinist's qualifications prioritize hands-on practical experience and a deep understanding of metalworking principles over formal academic degrees. Employers highly value demonstrable skill in operating conventional machine tools, interpreting blueprints, and maintaining precision tolerances. The pathway into this trade often includes vocational training, apprenticeships, or extensive on-the-job experience.
Requirements for a Manual Machinist vary significantly based on the industry and the complexity of the parts produced. Smaller job shops might seek generalists capable of operating various machines, while larger manufacturing facilities may require specialization in specific equipment or materials. Seniority brings expectations of greater independence, troubleshooting abilities, and mentoring junior machinists. Geographical location can also influence demand; regions with strong manufacturing sectors will have more opportunities and potentially higher skill expectations.
While certifications like NIMS (National Institute for Metalworking Skills) can significantly enhance a candidate's resume, they are typically supplementary to proven practical ability. The skill landscape for manual machinists is stable but evolving, with increasing integration of digital readouts and a foundational understanding of CNC programming becoming beneficial, even if direct CNC operation is not a primary duty. This role requires a balance of traditional craftsmanship and an openness to modern measurement and quality control techniques.
Education Requirements
Technical Skills
- Manual Lathe Operation (turning, facing, threading, boring)
- Manual Milling Machine Operation (vertical and horizontal, indexing, slotting)
- Blueprint Reading and Geometric Dimensioning and Tolerancing (GD&T)
- Precision Measurement Tools (calipers, micrometers, height gauges, bore gauges)
- Material Properties and Selection (steel, aluminum, brass, plastics)
- Tooling Selection and Sharpening (end mills, drills, inserts)
- Machine Setup and Fixturing
- Shop Math and Trigonometry for Machining
- Basic Machine Maintenance and Troubleshooting
- Surface Grinding and Finishing Techniques
- CNC Machine Basics and G-Code Interpretation (for setup and understanding)
Soft Skills
- Attention to Detail: Essential for ensuring parts meet precise specifications and identifying minute imperfections.
- Problem-Solving: Crucial for diagnosing machine issues, optimizing machining processes, and correcting part deviations.
- Patience and Precision: Required for meticulous setup, careful operation, and achieving tight tolerances on complex parts.
- Mechanical Aptitude: Important for understanding how machines work, their components, and how to maintain them.
- Safety Consciousness: Paramount for operating heavy machinery, handling sharp tools, and working with hazardous materials safely.
- Blueprint Reading and Interpretation: Necessary to accurately translate engineering drawings into physical components.
- Adaptability: Valued for adjusting to different materials, machine types, and varying project requirements.
- Communication: Important for collaborating with engineers, supervisors, and other machinists to ensure project success and resolve issues.
How to Become a Manual Machinist
Breaking into manual machining involves a blend of traditional training and hands-on skill development. While a formal apprenticeship or vocational school program is a common and highly recommended path, individuals can also enter through entry-level shop helper positions, learning on the job. The timeline for entry varies; a dedicated vocational program might take 1-2 years, while an apprenticeship could extend to 3-5 years, offering paid experience throughout. Learning on the job can take longer, typically 2-3 years to gain basic proficiency.
Geographic location significantly influences opportunities; manufacturing hubs in the Midwest or Southeast often have more openings and established training programs than smaller markets. Larger corporations might prefer candidates with formal certifications, while smaller job shops may prioritize demonstrated hands-on experience and a strong work ethic. Understanding these nuances helps in choosing the most effective entry strategy for your situation.
A common misconception is that manual machining is obsolete due to CNC technology. In reality, manual machinists are crucial for prototyping, custom one-off parts, repair work, and intricate tasks where CNC programming is inefficient or impossible. Networking with experienced machinists, joining local manufacturing associations, and seeking mentorship can open doors to unadvertised opportunities and provide invaluable insights into the trade's demands and rewards.
Step 1
Step 2
Step 3
Step 4
Step 5
Step 6
Education & Training Needed to Become a Manual Machinist
Becoming a Manual Machinist primarily involves hands-on training and practical experience, rather than formal four-year degrees. While some community colleges offer associate's degrees in Machining Technology, these programs often focus on a broader scope, including CNC operation. The most direct and employer-preferred pathways for manual machining are often vocational school programs, apprenticeships, or on-the-job training. Vocational programs typically last 6-18 months and can cost between $5,000 and $20,000, covering foundational skills in blueprint reading, measurement, and operating lathes, mills, and grinders. Apprenticeships, which combine paid work with structured learning, are highly valued for manual machining, often lasting 3-5 years. These programs are generally free to the apprentice, offering a direct route to skilled employment.
Employer acceptance of credentials varies. Many traditional machine shops prioritize demonstrated practical skills and experience over academic degrees. A vocational certificate or completion of a recognized apprenticeship program holds significant weight. Self-study, combined with personal projects and seeking entry-level shop helper positions, can also be a viable path, though it requires significant self-discipline and networking. This approach might cost less than $1,000 for tools and materials but could take 1-2 years to build proficiency. Continuous learning in manual machining involves staying updated on new materials, tooling advancements, and precision techniques. This often happens through vendor workshops, industry seminars, or mentorship within the workplace.
The educational needs for a manual machinist are highly specific to the type of work and the required precision. For instance, working on aerospace components demands a higher level of precision and material knowledge than general fabrication. Practical experience consistently outweighs theoretical knowledge in this field, making hands-on training paramount. Emerging trends might include basic CAD/CAM understanding for interpreting drawings, but the core skills of manual operation remain essential. Investing in quality vocational training or securing an apprenticeship offers a strong return on investment, providing direct pathways to employment and skill mastery. Look for programs with strong industry partnerships and access to a variety of manual machines for hands-on practice.
Manual Machinist Salary & Outlook
Compensation for a Manual Machinist varies significantly based on several factors, reflecting the precision and specialized skills required in this trade. Geographic location plays a crucial role; areas with strong manufacturing or aerospace industries, like the Midwest, parts of the Northeast, and California, typically offer higher wages due to demand and cost of living. Conversely, regions with lower industrial density or living expenses may show lower earning potential.
Experience levels dramatically influence a machinist's salary. An apprentice starts with foundational learning, while a master machinist commands premium compensation due to years of expertise, ability to work with complex materials, and proficiency with diverse machinery. Specializations, such as working with exotic alloys, precision grinding, or operating specific types of manual lathes and mills, also lead to higher pay.
Beyond base salary, total compensation packages often include overtime pay, which can significantly boost annual earnings given the project-based nature of much machining work. Some companies offer performance bonuses, particularly for meeting tight deadlines or achieving exceptional quality control. Benefits like health insurance, retirement plans (401k), and paid time off are standard. Larger manufacturing firms or those in high-demand sectors might also provide allowances for professional development or tool acquisition.
Industry-specific trends drive salary growth. The resurgence of domestic manufacturing and the need for custom, low-volume parts often produced manually can increase demand for skilled machinists. Negotiating leverage comes from proven precision, a strong portfolio of completed work, and certifications in specific machining processes. While remote work is not typical for this hands-on role, machinists with advanced CAD/CAM knowledge or supervisory skills might find some hybrid opportunities in planning or design phases. International markets also require skilled machinists, though direct salary comparisons need careful consideration of local economic conditions and currency values against the USD figures provided.
Salary by Experience Level
Level | US Median | US Average |
---|---|---|
Apprentice Manual Machinist | $35k USD | $38k USD |
Junior Manual Machinist | $45k USD | $47k USD |
Manual Machinist | $56k USD | $58k USD |
Senior Manual Machinist | $69k USD | $72k USD |
Lead Manual Machinist | $82k USD | $85k USD |
Master Machinist | $95k USD | $98k USD |
Market Commentary
The job market for Manual Machinists, while evolving, shows stable demand driven by specific industry needs. While automated CNC machining has grown, manual machinists remain indispensable for prototyping, custom one-off parts, specialized repairs, and intricate work where human touch and precision are paramount. Industries such as aerospace, defense, medical device manufacturing, and high-precision tooling continue to seek skilled manual machinists.
The U.S. Bureau of Labor Statistics projects employment for machinists and tool and die makers to show little or no change from 2022 to 2032, indicating a stable but not rapidly growing field. However, this overall projection masks specific demand for manual expertise. Many experienced machinists are nearing retirement, creating a skill gap that new entrants can fill. This supply-demand dynamic for highly skilled manual machinists can lead to competitive wages and job security for those with proven abilities.
Emerging opportunities for manual machinists often involve hybrid roles, where traditional skills are combined with digital literacy. Understanding CAD/CAM software for interpreting designs or setting up initial cuts, even if the final machining is manual, is increasingly valuable. The demand for custom fabrication and specialized components, particularly in advanced manufacturing and R&D, ensures the continued relevance of manual precision. Automation and AI primarily impact high-volume, repetitive tasks, leaving complex, low-volume, or unique projects to manual experts.
Geographic hotspots for manual machinists align with manufacturing hubs, including states like Michigan, Ohio, Pennsylvania, California, and Texas. Economic resilience for this profession comes from its role in essential industries like defense and medical, which often remain stable even during economic downturns. Future-proofing involves continuous learning, staying updated on new materials, and embracing quality control methodologies to maintain high standards of precision and efficiency.
Manual Machinist Career Path
Career progression for a Manual Machinist typically involves a clear ladder from entry-level apprenticeship to master craftsman. Advancement hinges on developing precision, problem-solving skills, and deep material knowledge through hands-on experience. Performance, the complexity of projects undertaken, and continuous learning directly influence advancement speed.
Progression often follows an individual contributor (IC) track, emphasizing technical mastery. However, leadership opportunities emerge at senior levels, allowing a shift into management or mentorship roles. Company size and industry sector also shape career paths; smaller job shops might offer faster advancement through diverse projects, while large manufacturing plants might provide more specialized but slower progression.
Lateral moves often involve specializing in particular materials, machine types, or precision levels, such as aerospace components or medical devices. Networking within the industry, seeking mentorship from experienced machinists, and pursuing certifications in advanced machining techniques or CAD/CAM software significantly bolster career trajectory. Milestones include mastering complex setups, achieving zero-defect production runs, and successfully troubleshooting intricate machining challenges. Some machinists transition into quality control, tool and die making, or even machine design.
Apprentice Manual Machinist
1-2 yearsKey Focus Areas
Junior Manual Machinist
2-4 years total experienceKey Focus Areas
Manual Machinist
4-7 years total experienceKey Focus Areas
Senior Manual Machinist
7-10 years total experienceKey Focus Areas
Lead Manual Machinist
10-15 years total experienceKey Focus Areas
Master Machinist
15+ years total experienceKey Focus Areas
Apprentice Manual Machinist
1-2 yearsOperates under direct supervision, performing basic machining tasks. Assists experienced machinists with machine setup, material loading, and part inspection. Focuses on learning fundamental machine functions, shop safety, and quality control procedures. Produces simple components with guidance.
Key Focus Areas
Develop foundational safety practices, machine operation basics, and blueprint reading. Focus on understanding material properties, tool selection, and measurement techniques. Build a strong work ethic and attention to detail. Practical application of classroom knowledge is crucial.
Junior Manual Machinist
2-4 years total experienceOperates various manual machines with moderate supervision. Performs routine setups, executes machining operations, and conducts in-process quality checks. Works on moderately complex parts, often requiring multiple operations. Troubleshoots minor machine adjustments and tool wear issues.
Key Focus Areas
Refine machine operation skills, focusing on achieving tighter tolerances and improved surface finishes. Learn to interpret more complex blueprints and perform basic machine maintenance. Develop independent problem-solving skills for minor machining issues. Begin understanding production efficiency.
Manual Machinist
4-7 years total experienceIndependently sets up and operates a wide range of manual machines for complex projects. Makes critical decisions regarding machining processes, tooling, and workholding. Responsible for producing high-precision components to exact specifications. Provides technical guidance to less experienced machinists.
Key Focus Areas
Master advanced machining techniques, including complex geometries and unconventional materials. Develop expertise in fixture design, tool path optimization, and machine calibration. Hone troubleshooting skills for challenging production problems. Mentor junior machinists and contribute to process improvements.
Senior Manual Machinist
7-10 years total experienceLeads the most challenging machining operations, often involving custom tooling or innovative methods. Responsible for ensuring the highest quality and efficiency on critical components. Provides expert technical advice, troubleshoots persistent issues, and optimizes production workflows. May oversee a small team or specific machine area.
Key Focus Areas
Specialize in high-precision machining, exotic materials, or specific machine types. Lead complex projects, optimizing processes for efficiency and quality. Develop strong analytical skills for root cause analysis of machining defects. Begin contributing to design-for-manufacturability discussions.
Lead Manual Machinist
10-15 years total experienceOversees a team of machinists, coordinating workloads and ensuring production targets are met. Acts as the primary technical expert for complex machining challenges and new project implementations. Mentors and trains junior staff, develops standard operating procedures, and contributes to equipment selection decisions. Ensures adherence to safety and quality standards across the shop.
Key Focus Areas
Cultivate strong leadership and communication skills. Focus on project management, team coordination, and training development. Develop expertise in lean manufacturing principles and continuous improvement methodologies. Contribute to strategic planning for machine shop capabilities.
Master Machinist
15+ years total experiencePossesses the highest level of technical expertise and often acts as a consultant for the most challenging or innovative projects. Develops new machining techniques, designs specialized tooling, and resolves critical production bottlenecks. Provides strategic input on equipment acquisition and shop capabilities. May lead R&D efforts or serve as a master trainer for the entire organization.
Key Focus Areas
Achieve unparalleled expertise in all facets of manual machining, including advanced metallurgy, machine design principles, and complex problem-solving. Drive innovation in machining processes and lead research into new technologies. Serve as the ultimate authority on technical issues.
Job Application Toolkit
Ace your application with our purpose-built resources:
Manual Machinist Cover Letter Examples
Personalizable templates that showcase your impact.
View examplesManual Machinist Job Description Template
Ready-to-use JD for recruiters and hiring teams.
View examplesGlobal Manual Machinist Opportunities
Manual machinists find consistent demand globally, particularly in manufacturing hubs and industries requiring custom parts or repair. This profession translates well across borders due to universal principles of metalworking and machine operation. Global demand remains stable for skilled manual machinists, especially where precision and craftsmanship are paramount. Cultural differences impact workshop practices and safety standards, while regulatory environments dictate equipment certifications. Professionals seek international roles for higher wages, diverse industry exposure, and skill development, with no specific international certifications universally required beyond local qualifications.
Global Salaries
Manual machinist salaries vary significantly by region and industrial demand. In North America, a manual machinist earns between $45,000 and $70,000 USD annually in the United States, and $40,000 to $65,000 CAD in Canada. These figures reflect a high cost of living in major industrial cities. European salaries range from €30,000 to €50,000 per year in Germany, known for its precision engineering, and £25,000 to £40,000 in the United Kingdom. Scandinavian countries offer similar ranges but with higher income taxes.
Asia-Pacific markets present diverse compensation. In Australia, manual machinists make between A$55,000 and A$80,000. Japan offers ¥3.5 million to ¥5.5 million annually (approximately $24,000-$37,000 USD), often balanced by lower living costs outside major cities. Latin America, such as Mexico, sees salaries from $10,000 to $20,000 USD, with significantly lower purchasing power. Middle Eastern countries, particularly the UAE, offer tax-free salaries from $25,000 to $45,000 USD, often including housing allowances.
Salary structures also differ. North America and Europe often include comprehensive health benefits and paid time off. Other regions may offer fewer benefits, with higher base pay or specific allowances. Tax implications vary widely; for example, high earners in Germany face steeper progressive taxes compared to flat tax rates in some Middle Eastern countries. Experience and specialized skills, like working with exotic materials or complex geometries, consistently command higher compensation globally, improving international pay scales.
Remote Work
Manual machinists have extremely limited international remote work opportunities. This role inherently requires hands-on operation of machinery and physical presence in a workshop or factory setting. The nature of precision manufacturing, material handling, and quality control necessitates on-site work.
Digital nomad opportunities are not applicable to manual machinists. The profession does not lend itself to working from different locations without the necessary equipment. Companies hiring manual machinists globally always require their physical presence. Therefore, salary expectations for this role are tied to the local job market where the work is performed, with no geographic arbitrage potential. Equipment, internet requirements, and workspace setup for a manual machinist are strictly industrial and cannot be replicated remotely.
Visa & Immigration
Manual machinists often qualify for skilled worker visas in countries with manufacturing needs. Popular destinations include Germany (Skilled Immigration Act), Canada (Express Entry, Provincial Nominee Programs), and Australia (Skilled Nominated Visa). Requirements for these visas typically involve demonstrating relevant experience and qualifications, often with a job offer.
Education credential recognition for vocational training in manual machining is crucial. Some countries, like Germany, require formal recognition of foreign qualifications. Visa timelines vary; a skilled worker visa can take 3-12 months. Language requirements are common, particularly for European countries; for instance, German language proficiency may be necessary for employment. Pathways to permanent residency exist in many nations, often after several years of continuous skilled employment.
Profession-specific advantages are rare, but strong demand for skilled trades can expedite processing in some regions. Practical considerations include obtaining dependent visas for family members. Secure a job offer before applying for a visa, as many immigration pathways are employer-sponsored or points-based systems favoring those with confirmed employment.
2025 Market Reality for Manual Machinists
Understanding current market realities is crucial for manual machinists to navigate evolving career paths. The profession has seen significant shifts since 2023, driven by post-pandemic reshoring efforts and the accelerating integration of automation and AI in manufacturing.
Broader economic factors, such as industrial output and investment in new technologies, directly impact job availability for machinists. Market realities vary considerably by experience level, with highly skilled artisans finding more niche opportunities, and by geographic region, as some areas retain more traditional manufacturing. This analysis provides an honest assessment of current hiring conditions and strategic considerations for manual machinists.
Current Challenges
Manual machinists face significant challenges from automation and CNC technology. Increased competition for specialized manual roles means fewer openings. Economic slowdowns can also reduce manufacturing demand, impacting job availability. The need for highly precise work limits entry-level opportunities, demanding extensive experience.
Growth Opportunities
Despite challenges, strong opportunities exist for manual machinists specializing in niche areas like aerospace, medical device manufacturing, or custom tooling. These sectors value precision, custom work, and the ability to handle unique materials that automated machines may struggle with. Experienced manual machinists proficient in complex setups, prototyping, or repair work find consistent demand.
Professionals can gain a competitive advantage by acquiring hybrid skills. Learning basic CNC programming, CAD/CAM software, or metrology enhances their value. Employers seek individuals who can bridge the gap between traditional craftsmanship and modern manufacturing processes. Underserved markets often include smaller, highly specialized fabrication shops or R&D facilities that require unique, one-off components. Strategic career moves involve targeting industries that prioritize bespoke manufacturing over mass production. Investing in certifications for specific materials or advanced machining techniques can also open doors. The demand for skilled troubleshooters who understand machine mechanics and material science remains robust, even as automation expands.
Current Market Trends
Hiring for manual machinists shows a bifurcated trend in 2025. Demand remains strong for highly skilled, experienced professionals capable of complex, one-off, or prototype work. These roles often require deep material knowledge and the ability to troubleshoot intricate setups without extensive digital aids. However, entry-level and less specialized manual machining positions are declining.
The integration of advanced CNC machines and automation continues to shift the landscape. Many manufacturers now prioritize machinists who can program, set up, and operate automated equipment, reducing the need for purely manual operators. This trend puts pressure on traditional manual machinists to upskill or specialize. Economic conditions, including fluctuating manufacturing output and supply chain adjustments, directly influence the number of available manual machining jobs. Layoffs in some sectors, particularly those adopting more automation, reflect this shift.
Employers increasingly seek manual machinists with hybrid skills, including basic CAD/CAM understanding or the ability to work alongside robotics. Salary trends for highly skilled manual machinists are stable or seeing modest increases due to their specialized value, but general manual machinist salaries face downward pressure from automation. Market saturation exists at the lower skill levels. Geographically, stronger demand persists in regions with custom fabrication, aerospace, defense, or precision tooling industries, where manual dexterity and problem-solving remain critical. Remote work is generally not applicable to this hands-on role.
Emerging Specializations
The manufacturing landscape is undergoing a significant transformation, driven by advancements in automation, materials science, and digital fabrication. These shifts are creating novel specialization opportunities for Manual Machinists, moving beyond traditional roles. Early positioning in these emerging areas is crucial for career advancement, offering pathways to roles with premium compensation and enhanced career growth.
While established machining specializations remain valuable, focusing on cutting-edge areas can provide a distinct advantage. These emerging fields often represent the intersection of traditional craftsmanship with advanced technology, enabling a Manual Machinist to expand their capabilities significantly. Many of these specializations are poised to become mainstream within the next three to five years, creating a substantial number of job opportunities.
Embracing these new areas involves a balance of risk and reward. While it requires investment in new skills and adaptive learning, the potential for higher demand, better pay, and more engaging work is substantial. Professionals who proactively acquire skills in these niche, future-oriented fields will be well-positioned to lead the next generation of precision manufacturing.
Advanced Composites Machining Specialist
Rapid Prototyping & Custom Fabrication Machinist
Robotics & Automation Component Machinist
Industrial Component Restoration Machinist
Pros & Cons of Being a Manual Machinist
Understanding both the advantages and challenges of a career is crucial before making a commitment. This assessment provides a realistic overview of being a Manual Machinist, helping you set appropriate expectations. Career experiences can vary significantly based on the specific company, the industry sector, and the types of projects undertaken. What one individual finds appealing, another might see as a drawback, depending on their personal values and lifestyle preferences. Additionally, the day-to-day realities and the balance of pros and cons can shift at different stages of a machinist's career, from an apprentice to a seasoned professional. This honest evaluation aims to prepare you for the genuine benefits and the real-world demands of this skilled trade.
Pros
- Manual machinists experience high job satisfaction from creating tangible products and seeing projects through from raw material to finished precision components.
- This role offers significant intellectual stimulation through problem-solving, requiring machinists to interpret blueprints, plan machining operations, and troubleshoot issues with complex parts.
- Manual machining provides a strong sense of craftsmanship and mastery, as it relies heavily on a machinist's individual skill, judgment, and experience rather than automated processes.
- There is consistent demand for skilled manual machinists across various industries, including manufacturing, aerospace, automotive, and custom fabrication, ensuring good job security.
- The skills learned as a manual machinist are highly transferable and foundational, providing an excellent base for transitioning into CNC machining, tool and die making, or even engineering roles.
- Entry into manual machining often involves apprenticeships or vocational training, which are typically more affordable and hands-on than traditional four-year degrees, leading to quicker entry into the workforce.
- Manual machinists often work standard daytime hours in a shop environment, providing a predictable schedule and generally good work-life balance compared to some other industrial roles.
Cons
- The work environment in a machine shop can be noisy, dirty, and sometimes hot, requiring constant use of hearing protection, safety glasses, and other personal protective equipment.
- Manual machining involves repetitive motions and standing for long periods, which can lead to physical fatigue, back strain, or other musculoskeletal issues over time.
- There is a constant risk of injury from moving machine parts, sharp tools, and hot metal chips, demanding unwavering attention to safety protocols and machine operation.
- The job requires significant physical strength and dexterity for lifting heavy raw materials and finished parts, as well as for precise manual adjustments.
- Opportunities for career advancement within manual machining itself can be limited, often leading to supervisory roles or transitioning to CNC programming, which requires new skills.
- Mastering manual machining skills takes years of hands-on experience and apprenticeship, as formal education alone does not substitute for practical expertise.
- Pay scales for manual machinists, while stable, may not offer the same high-end earning potential as specialized CNC programming or engineering roles, especially without additional skills.
Frequently Asked Questions
Manual Machinists face unique challenges blending traditional craftsmanship with modern precision demands. This section addresses key questions about entering this skilled trade, from acquiring hands-on experience to understanding career stability and the physical demands of the role.
What are the typical entry requirements to become a Manual Machinist?
Most manual machinists learn through apprenticeships, vocational programs, or on-the-job training. While not strictly required, a high school diploma or GED is usually preferred. Strong mechanical aptitude, attention to detail, and good hand-eye coordination are more critical than formal degrees. Many successful machinists start as shop helpers and learn from experienced mentors.
How long does it take to become a skilled Manual Machinist from scratch?
Becoming a proficient manual machinist can take 2-5 years, depending on the training path. Apprenticeships typically last 3-4 years, combining classroom instruction with extensive on-the-job experience. Vocational programs might be shorter, 6-18 months, but often require additional hands-on experience to become fully job-ready. Continuous learning is essential, as mastering complex setups and materials takes time.
What are the salary expectations for a Manual Machinist, both entry-level and experienced?
Starting salaries for entry-level manual machinists often range from $35,000 to $45,000 annually, varying by region and employer. Experienced machinists with specialized skills and a proven track record can earn $55,000 to $75,000 or more per year. Overtime opportunities are common, which can significantly increase overall earnings. Benefits packages usually include health insurance and retirement plans.
What are the physical demands and safety considerations of this job?
Manual machining involves working with heavy machinery, sharp tools, and often metal dust or coolants. Safety is paramount, requiring strict adherence to protocols and personal protective equipment. The work can be physically demanding, involving standing for long periods, lifting, and repetitive motions. Maintaining focus and precision for extended periods is also crucial for quality work.
Is the Manual Machinist role still in demand with the prevalence of CNC technology?
Despite the rise of CNC machines, the demand for skilled manual machinists remains steady, especially for custom work, repairs, prototyping, and small batch production. Manual machinists possess unique problem-solving skills and an understanding of material properties that automated machines cannot fully replicate. Job security is generally good for those with diverse skills and a willingness to adapt.
What are the typical career advancement opportunities for a Manual Machinist?
Career growth for manual machinists can include specializing in complex materials, precision grinding, or tool and die making. Many advance to lead machinist roles, shop supervisors, or production managers. Some transition into CNC programming or machine repair, leveraging their foundational knowledge. Entrepreneurship, starting a custom machine shop, is also a viable path for highly experienced individuals.
What is the typical work-life balance and work environment like for a Manual Machinist?
Work-life balance for manual machinists varies by employer. Most positions are full-time, often with standard day shifts. However, some shops operate on multiple shifts, and overtime might be necessary to meet production deadlines. The work is typically performed on-site in a workshop or factory setting, limiting remote work options. Weekend work is less common but can occur during peak periods.
Related Careers
Explore similar roles that might align with your interests and skills:
Lathe Machinist
A growing field with similar skill requirements and career progression opportunities.
Explore career guideMachinist
A growing field with similar skill requirements and career progression opportunities.
Explore career guideManual Lathe Machinist
A growing field with similar skill requirements and career progression opportunities.
Explore career guidePrecision Machinist
A growing field with similar skill requirements and career progression opportunities.
Explore career guideProduction Machinist
A growing field with similar skill requirements and career progression opportunities.
Explore career guideAssess your Manual Machinist readiness
Understanding where you stand today is the first step toward your career goals. Our Career Coach helps identify skill gaps and create personalized plans.
Skills Gap Analysis
Get a detailed assessment of your current skills versus Manual Machinist requirements. Our AI Career Coach identifies specific areas for improvement with personalized recommendations.
See your skills gapCareer Readiness Assessment
Evaluate your overall readiness for Manual Machinist roles with our AI Career Coach. Receive personalized recommendations for education, projects, and experience to boost your competitiveness.
Assess your readinessSimple pricing, powerful features
Upgrade to Himalayas Plus and turbocharge your job search.
Himalayas
Himalayas Plus
Himalayas Max
Find your dream job
Sign up now and join over 100,000 remote workers who receive personalized job alerts, curated job matches, and more for free!
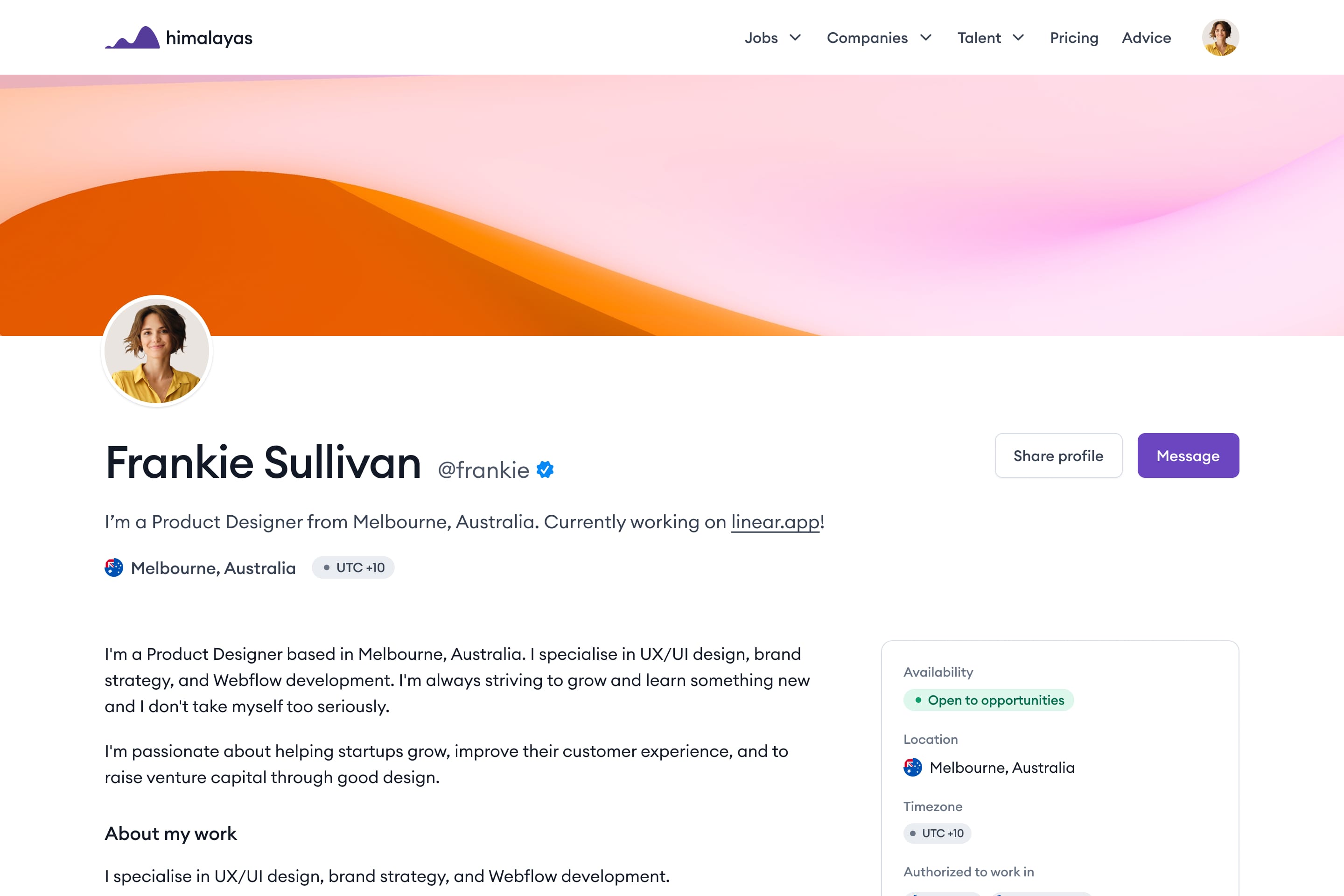