Complete Manual Lathe Machinist Career Guide
A Manual Lathe Machinist is a skilled artisan who transforms raw materials into precision components using traditional, hand-operated lathes. This role demands exceptional precision, problem-solving abilities, and a deep understanding of metal properties, making it vital for custom fabrication and intricate repair work. You will leverage tactile feel and keen observation to craft parts essential for industries ranging from aerospace to specialized manufacturing, offering a rewarding path for those who value craftsmanship and tangible results.
Key Facts & Statistics
Median Salary
$55,040 USD
(U.S. national median for Machinists, May 2023, BLS)
Range: $35k - $75k+ USD
Growth Outlook
1%
as fast as average (for Machinists, Tool and Die Makers, and Millwrights, BLS)
Annual Openings
≈33k
openings annually (for Machinists, Tool and Die Makers, and Millwrights, BLS)
Top Industries
Typical Education
High school diploma or equivalent, often with vocational training, apprenticeship, or significant on-the-job experience
What is a Manual Lathe Machinist?
A manual lathe machinist is a skilled tradesperson who operates and maintains traditional, hand-controlled lathes to shape metal or other materials into precise components. Unlike CNC (Computer Numerical Control) machinists who program machines, manual lathe machinists directly control the machine's movements using handwheels and levers, relying on their expertise, tactile feedback, and keen eye to achieve specified dimensions and surface finishes.
This role demands a deep understanding of metallurgy, cutting tool geometry, and measurement techniques. Manual machinists are crucial for prototyping, custom one-off parts, repair work, and situations where the flexibility and nuanced control of a human operator are preferred over automated programming. They differ significantly from CNC machinists, who focus on programming and monitoring automated processes, and from general machine operators, who may simply load and unload parts from pre-set machines without performing complex setups or adjustments.
What does a Manual Lathe Machinist do?
Key Responsibilities
- Interpret blueprints, engineering drawings, and specifications to understand part dimensions, tolerances, and material requirements.
- Set up manual lathes by selecting and installing appropriate cutting tools, chucks, and workholding devices for specific machining operations.
- Mount raw material stock onto the lathe, ensuring proper alignment and secure clamping to prevent movement during machining.
- Operate manual lathes to perform turning, facing, boring, threading, and drilling operations, using hand controls to manipulate cutting tools.
- Monitor the machining process closely, adjusting speeds, feeds, and depth of cut to achieve desired surface finishes and dimensional accuracy.
- Perform in-process inspections using precision measuring tools like calipers, micrometers, and gauges to verify part dimensions against specifications.
- Conduct routine maintenance on the lathe, including cleaning, lubrication, and minor adjustments, to ensure optimal performance and longevity.
Work Environment
A manual lathe machinist typically works in a manufacturing facility, machine shop, or fabrication plant. These environments are often noisy due to machinery operation and may involve exposure to coolants, oils, and metal shavings. The work is largely independent during machine operation but requires close collaboration with supervisors, quality control personnel, and sometimes engineers to clarify specifications or troubleshoot issues.
The schedule is usually full-time, often involving shifts in production environments. The work requires standing for extended periods and involves physical demands such as lifting heavy materials or components. Precision and attention to detail are paramount, making it a focused and methodical role. The pace of work is steady, driven by production schedules and the need for meticulous execution.
Tools & Technologies
Manual lathe machinists primarily use traditional, hand-controlled lathes, which are distinct from CNC (Computer Numerical Control) machines. Their essential tools include a variety of cutting tools, such as carbide inserts, high-speed steel tools, and form tools, specifically chosen for different materials and operations. They rely heavily on precision measuring instruments like vernier calipers, digital calipers, micrometers (inside, outside, and depth), bore gauges, and thread gauges to ensure accuracy.
Support equipment includes workholding devices like chucks, collets, and faceplates, along with various wrenches and hand tools for setup and adjustments. While less reliant on software, they must proficiently read and interpret engineering blueprints, schematics, and technical drawings, which are often created using CAD software, though the machinist's interaction is with the printed or digital output.
Manual Lathe Machinist Skills & Qualifications
A Manual Lathe Machinist navigates a qualification landscape heavily weighted towards practical experience and demonstrated proficiency rather than formal academic degrees. Employers prioritize hands-on skill, precision, and a deep understanding of metalworking principles. The ability to produce high-quality, precise parts consistently is paramount.
Requirements for a Manual Lathe Machinist vary significantly by industry sector, company size, and the complexity of parts produced. Smaller job shops might value versatility across different machine types, while larger manufacturing facilities may seek specialization in specific materials or part dimensions. Geographic location can also influence demand, with areas having strong manufacturing bases often requiring more experienced machinists. While formal education like an associate's degree or vocational training provides a strong foundation, many successful machinists enter the field through apprenticeships or on-the-job training, where practical skills are honed over years.
Certifications from organizations like the National Institute for Metalworking Skills (NIMS) are highly valued. These certifications validate specific competencies in areas such as Measurement, Materials & Safety, Job Planning, Benchwork & Layout, and Manual Machining. They serve as a recognized standard of skill. The skill landscape for manual machinists remains stable, though a foundational understanding of CNC machining principles can be beneficial for career advancement, allowing for a balance between traditional craftsmanship and modern manufacturing demands.
Education Requirements
Technical Skills
- Manual Lathe Operation (engine lathes, turret lathes)
- Blueprint Reading and Geometric Dimensioning and Tolerancing (GD&T)
- Precision Measurement Tools (micrometers, calipers, bore gauges, depth gauges)
- Tooling Selection and Setup (inserts, cutting tools, tool holders)
- Material Properties and Machinability (steel, aluminum, brass, plastics)
- Speeds and Feeds Calculation (RPM, feed rate)
- Machine Maintenance (lubrication, cleaning, minor repairs)
- Work Holding Techniques (chucks, collets, faceplates)
- Thread Cutting (single point threading, tapping)
- Surface Finish Control and Deburring
- Basic Shop Math (trigonometry, geometry for angles and dimensions)
- Inspection and Quality Control Procedures
Soft Skills
- Attention to Detail: Essential for producing parts within tight tolerances and identifying subtle imperfections, preventing costly errors.
- Problem-Solving: Required for diagnosing machine malfunctions, troubleshooting issues with part dimensions, and optimizing machining processes.
- Patience and Focus: Critical for repetitive tasks and maintaining precision over long machining cycles, especially with complex or delicate parts.
- Manual Dexterity and Hand-Eye Coordination: Fundamental for precise manipulation of machine controls, tooling setup, and part handling.
- Safety Consciousness: Paramount for adhering to strict safety protocols, operating heavy machinery responsibly, and preventing workplace accidents.
- Adaptability: Needed to adjust to different materials, part specifications, machine types, and changing production demands.
- Work Ethic and Reliability: Employers depend on machinists to meet production schedules and maintain equipment, requiring consistent effort and punctuality.
- Blueprint Reading and Interpretation: Crucial for accurately translating engineering drawings into machining operations and understanding geometric dimensioning and tolerancing (GD&T).
How to Become a Manual Lathe Machinist
Entering the Manual Lathe Machinist field offers several practical pathways, ranging from formal education to direct on-the-job training. While a vocational degree or certificate provides a strong theoretical foundation and hands-on experience, many successful machinists begin through apprenticeships or entry-level shop helper positions. Apprenticeships, often lasting 2-4 years, combine paid work with structured learning, offering a comprehensive skill set and valuable industry connections.
Timeline expectations vary significantly. A dedicated individual might secure an entry-level position within 3-6 months through a short vocational program or by actively seeking shop helper roles. A full apprenticeship or associate's degree could take 2 years. Geographic location plays a role; manufacturing hubs often have more opportunities and established training programs than smaller markets. Company size also matters; smaller job shops might offer broader exposure to different machines and tasks quickly, while larger corporations may have more structured training but slower progression.
A common misconception is that all machining is automated; however, manual lathe work remains critical for custom parts, repairs, and prototyping, especially in industries like aerospace, automotive, and specialized manufacturing. Success in this field relies heavily on precision, problem-solving, and a keen eye for detail. Networking within local manufacturing communities and engaging with experienced machinists can open doors to unadvertised opportunities and mentorship, which is invaluable for skill development and career advancement.
Step 1
Step 2
Step 3
Step 4
Step 5
Step 6
Education & Training Needed to Become a Manual Lathe Machinist
Becoming a Manual Lathe Machinist primarily involves hands-on skill development, with formal education supporting foundational knowledge. Unlike many modern manufacturing roles, a four-year university degree is rarely a direct path or prerequisite for this specific trade. Instead, vocational programs, apprenticeships, and community college certificates offer the most direct and recognized routes.
Apprenticeships, typically 3-5 years, often combine paid on-the-job training with classroom instruction, costing little to the apprentice while providing immediate income. Community college programs and vocational schools offer 6-24 month certificates or associate degrees, ranging from $5,000 to $20,000. These programs provide structured learning in blueprint reading, metallurgy, and machine operation, which are essential for safe and precise work. Self-study and informal mentorship can supplement learning, but industry employers highly value credentials from accredited programs or documented apprenticeship completion due to the precision and safety requirements of the work. Continuous learning in new materials and tooling is also important for career advancement.
The market perception of a Manual Lathe Machinist emphasizes practical experience and proven competence over academic degrees. Employers seek individuals who can demonstrate proficiency in setting up and operating manual lathes, maintaining tight tolerances, and troubleshooting. While formal programs provide a strong theoretical base, the ability to produce quality parts consistently is paramount. Educational needs vary; a beginner needs foundational training, while an experienced machinist might seek specialized courses in advanced materials or specific machining techniques. The cost-benefit analysis favors vocational training and apprenticeships, which offer high ROI through direct employment pathways and relevant skill acquisition, minimizing debt compared to longer, less directly applicable academic degrees.
Manual Lathe Machinist Salary & Outlook
Compensation for a Manual Lathe Machinist varies significantly based on several key factors. Geographic location plays a major role, with higher salaries typically found in regions with strong manufacturing sectors and a higher cost of living, such as parts of the Northeast, Midwest, and West Coast. In contrast, areas with lower demand or cost of living will reflect lower earning potentials.
Experience dramatically influences pay. Entry-level machinists earn less, while those with extensive experience, specialized skills like precision machining for aerospace, or the ability to work with exotic materials command premium rates. Total compensation often extends beyond base salary to include overtime pay, production bonuses, and comprehensive benefits packages. These benefits frequently cover health insurance, retirement plans like 401(k)s, and sometimes even tool allowances or tuition reimbursement for advanced training.
Industry-specific demands also shape compensation. Machinists in industries like aerospace, defense, or medical device manufacturing typically earn more due to the precision and critical nature of their work compared to those in general manufacturing. Company size and union affiliation can also impact wages and benefits. While remote work is not applicable to this hands-on role, a machinist's ability to operate diverse machinery or program CNC equipment in addition to manual lathes can increase their negotiation leverage. Salary figures presented are primarily for the United States, acknowledging that international markets will have their own distinct economic conditions and pay scales.
Salary by Experience Level
Level | US Median | US Average |
---|---|---|
Apprentice Manual Lathe Machinist | $35k USD | $38k USD |
Junior Manual Lathe Machinist | $45k USD | $47k USD |
Manual Lathe Machinist | $56k USD | $58k USD |
Senior Manual Lathe Machinist | $69k USD | $72k USD |
Lead Manual Lathe Machinist | $82k USD | $85k USD |
Master Machinist (Lathe Specialist) | $92k USD | $95k USD |
Market Commentary
The job market for Manual Lathe Machinists shows a nuanced demand. While there's a broader industry shift towards CNC (Computer Numerical Control) machining, a persistent need for skilled manual lathe operators remains, particularly for custom, low-volume, repair, or specialized prototype work. This demand is driven by industries requiring high precision and adaptability without the need for extensive programming setups, such as aerospace, defense, automotive prototyping, and custom fabrication shops.
The Bureau of Labor Statistics projects slower than average growth for machinists overall, but the specific niche of manual lathe operation benefits from a skilled labor shortage. Many experienced manual machinists are nearing retirement, creating a vacuum that new talent is not fully filling. This imbalance between supply and demand for highly skilled manual operators can lead to competitive wages for qualified candidates.
Future-proofing for manual machinists involves embracing hybrid skills. Those who can operate both manual and CNC equipment, troubleshoot complex mechanical issues, and understand metrology principles will be highly sought after. While automation impacts some aspects of manufacturing, the dexterity, problem-solving, and hands-on intuition of a manual lathe machinist are difficult to fully replicate by machines, especially for unique or challenging projects. Geographic hotspots for these roles align with major manufacturing hubs, particularly in states like Michigan, Ohio, Texas, California, and parts of the Southeast where industrial activity is strong.
Manual Lathe Machinist Career Path
Career progression for a Manual Lathe Machinist emphasizes the continuous development of precision machining skills, material science knowledge, and problem-solving abilities. Advancement typically follows a path from foundational learning to highly specialized expertise, marked by increasing autonomy and complexity in work.
Progression can occur within an individual contributor (IC) track, leading to master-level specialization, or can branch into a leadership track, involving team supervision and project management. Factors influencing advancement speed include consistent demonstration of accuracy, efficiency, and the ability to work with diverse materials and complex blueprints. Company size and industry also play a role; smaller job shops might offer faster progression through varied tasks, while larger manufacturing facilities might require deeper specialization in specific processes or materials.
Lateral movement often involves cross-training on other machine types, such as milling machines, or moving into quality control or CAD/CAM programming roles. Networking within the local manufacturing community and pursuing certifications in advanced machining techniques or metrology can significantly enhance career prospects. Mentorship from experienced machinists is crucial, providing hands-on knowledge transfer and accelerating skill acquisition.
Apprentice Manual Lathe Machinist
0-2 yearsKey Focus Areas
Junior Manual Lathe Machinist
2-4 yearsKey Focus Areas
Manual Lathe Machinist
4-7 yearsKey Focus Areas
Senior Manual Lathe Machinist
7-10 yearsKey Focus Areas
Lead Manual Lathe Machinist
10-15 yearsKey Focus Areas
Master Machinist (Lathe Specialist)
15+ yearsKey Focus Areas
Apprentice Manual Lathe Machinist
0-2 yearsOperate under direct supervision, performing basic turning operations on a manual lathe. Responsibilities include loading and unloading materials, starting and stopping the machine, and making simple cuts. Tasks are highly structured with immediate oversight from experienced machinists. Impact is limited to individual task completion.
Key Focus Areas
Develop foundational understanding of machine components, safety protocols, and basic cutting tool selection. Focus on accurate measurement techniques using calipers and micrometers. Learn to interpret simple blueprints and perform routine machine maintenance tasks. Building a strong work ethic and attention to detail is paramount.
Junior Manual Lathe Machinist
2-4 yearsPerform moderately complex machining operations with reduced supervision. Responsibilities include setting up the lathe for multiple operations, selecting appropriate tooling, and performing quality checks on finished parts. Works on components requiring tighter tolerances and more intricate designs. Contributes to project timelines through efficient part production.
Key Focus Areas
Refine turning, facing, and boring techniques with increased independence. Master various cutting tool geometries and their applications for different materials. Begin to understand material properties and their impact on machining. Develop skills in troubleshooting minor machine issues and performing more complex setups.
Manual Lathe Machinist
4-7 yearsOperate manual lathes independently, producing complex, high-precision components from various materials. Interpret advanced engineering drawings and apply critical thinking to determine optimal machining strategies. Responsible for the entire machining process from setup to final inspection. Often collaborates with engineers on part design and manufacturability.
Key Focus Areas
Achieve high proficiency in all standard lathe operations, including threading, tapering, and knurling. Develop strong problem-solving skills for unexpected machining challenges. Understand advanced G-code concepts for potential future CNC integration. Focus on optimizing machining processes for efficiency and quality.
Senior Manual Lathe Machinist
7-10 yearsHandle the most challenging and critical manual lathe projects, often involving prototypes or highly specialized components. Provide technical guidance and support to other machinists on complex setups and difficult materials. Make independent decisions regarding machining methodologies and quality control standards. Direct impact on project success and product quality.
Key Focus Areas
Master advanced machining techniques for exotic materials and extremely tight tolerances. Develop expertise in jig and fixture design for complex parts. Cultivate strong mentoring skills, guiding junior machinists through challenging operations. Begin to evaluate and recommend new tooling or machining processes.
Lead Manual Lathe Machinist
10-15 yearsOversee a team of manual lathe machinists, managing workflow, assigning tasks, and ensuring production targets are met. Troubleshoot complex machining problems across multiple machines and provide expert guidance. Responsible for training new machinists and maintaining safety standards within the lathe section. Influences departmental efficiency and output directly.
Key Focus Areas
Develop leadership and project management skills, including scheduling and resource allocation. Focus on process improvement and lean manufacturing principles. Cultivate strong communication skills to liaise effectively between the shop floor, engineering, and management. Understand cost implications of machining processes.
Master Machinist (Lathe Specialist)
15+ yearsServe as the ultimate authority and technical expert for all manual lathe operations within an organization. Design highly specialized tooling and fixtures for unprecedented machining challenges. Consult on complex engineering projects, providing critical input on manufacturability and precision. Their decisions have a significant, long-term impact on the company's capabilities and competitive edge.
Key Focus Areas
Achieve unparalleled expertise in all aspects of manual lathe machining, including material science and advanced metrology. Focus on innovation in machining processes, contributing to R&D or advanced manufacturing initiatives. Develop strategic thinking to advise on equipment procurement and long-term production planning.
Job Application Toolkit
Ace your application with our purpose-built resources:
Manual Lathe Machinist Resume Examples
Proven layouts and keywords hiring managers scan for.
View examplesManual Lathe Machinist Cover Letter Examples
Personalizable templates that showcase your impact.
View examplesTop Manual Lathe Machinist Interview Questions
Practice with the questions asked most often.
View examplesManual Lathe Machinist Job Description Template
Ready-to-use JD for recruiters and hiring teams.
View examplesGlobal Manual Lathe Machinist Opportunities
Manual Lathe Machinists find global demand, particularly in manufacturing hubs across Europe, Asia, and North America. This profession maintains its relevance for specialized, low-volume, or repair work, where automation is not feasible. Cultural differences impact workshop practices and safety standards. Regulatory differences influence machinery certifications and operational protocols. Professionals often seek international opportunities for higher wages, better working conditions, or specialized projects. Some international certifications, like ISO 9001 adherence, can facilitate global mobility.
Global Salaries
Manual Lathe Machinist salaries vary significantly by region and industrial demand. In North America, a machinist might earn USD 45,000-70,000 annually in the USA, or CAD 50,000-80,000 in Canada. These figures reflect a higher cost of living, with strong purchasing power in industrial states and provinces.
Europe offers diverse salary landscapes. In Germany, a skilled machinist can expect EUR 35,000-55,000 (approximately USD 38,000-60,000), while in the UK, salaries range from GBP 28,000-45,000 (approximately USD 35,000-56,000). Scandinavian countries like Sweden might offer SEK 300,000-450,000 (USD 28,000-42,000), but with a much higher cost of living. Benefits packages in Europe often include extensive vacation time and comprehensive healthcare.
Asia-Pacific markets present lower nominal salaries but often a lower cost of living. In Australia, machinists earn AUD 60,000-90,000 (USD 40,000-60,000). Japan offers JPY 3.5-5.5 million (USD 23,000-37,000). China's salaries vary widely, but experienced machinists in manufacturing zones might earn CNY 80,000-150,000 (USD 11,000-21,000). Latin America generally offers lower compensation, with Brazil paying BRL 40,000-70,000 (USD 8,000-14,000). Tax implications and take-home pay differ greatly, with some European countries having higher deductions than North America or Asia. International experience and specialized skills, like working with specific materials or complex geometries, can boost compensation globally.
Remote Work
International remote work for Manual Lathe Machinists is extremely limited, as the role is inherently hands-on and requires specialized machinery. Machining tasks demand physical presence at a workshop or manufacturing facility. Therefore, digital nomad opportunities are not applicable to this profession.
Some related tasks, like CAD/CAM programming or technical drawing, might be performed remotely if a machinist also possesses those skills. However, the core function of operating a manual lathe cannot be done outside a physical workshop. Companies typically do not hire manual machinists for international remote work. Any remote aspect would involve administrative or design-related duties, not the actual machining process.
Visa & Immigration
Manual Lathe Machinists often qualify for skilled worker visas in countries with manufacturing needs. Popular destinations include Germany, Canada, Australia, and the USA. Requirements typically involve a job offer, relevant work experience, and sometimes trade certifications. For example, Canada's Express Entry system or Australia's skilled migration programs may include this occupation, often requiring skills assessments.
Credential recognition is crucial; some countries require formal trade qualifications or apprenticeships to be recognized. Visa timelines vary, from a few months in Canada to longer periods for US H-2B visas. Language requirements may apply, especially for integration into the workplace and community. German skilled worker visas often require basic German language proficiency. Pathways to permanent residency exist in countries like Canada and Australia after several years of skilled employment. Family visas for dependents are usually available alongside the primary applicant's visa. Some countries may offer expedited processing for occupations on high-demand lists, benefiting skilled trades like machining.
2025 Market Reality for Manual Lathe Machinists
Understanding current market conditions is paramount for any Manual Lathe Machinist aiming for career longevity and success. The manufacturing landscape has transformed significantly between 2023 and 2025, driven by post-pandemic reshoring efforts and the accelerated adoption of automation and AI in production. These shifts, alongside broader economic factors impacting industrial output, directly influence the availability and nature of machining roles.
Market realities for manual machinists vary considerably by experience level, as highly skilled craftsmen remain in demand for specialized tasks while entry-level manual roles face more competition from automated processes. Geographic location and the size of the manufacturing operation also play a critical role, with some regions and smaller shops preserving traditional machining needs more readily. This analysis provides an honest assessment, preparing you for the realities of this evolving trade.
Current Challenges
Manual Lathe Machinists face a shrinking pool of dedicated manual work as CNC machines handle more standard production, intensifying competition for specialized or repair-focused roles. Economic shifts and supply chain adjustments sometimes delay projects, creating inconsistent demand. Many employers now seek hybrid skills, expecting manual machinists to also operate or understand CNC programming, creating a skill gap for those focused solely on traditional methods. Finding roles that do not require CNC experience can take longer, especially for entry-level candidates.
Growth Opportunities
Despite automation, several strong opportunities exist for Manual Lathe Machinists. Niche areas like custom fabrication, aerospace repair, medical device prototyping, and specialized tooling production still show robust demand for manual expertise. These fields require the unique problem-solving and adaptive skills of a human operator, which automation cannot replicate.
Professionals can gain a significant advantage by developing hybrid skills. Learning to read and interpret G-code, understanding basic CAD/CAM software, or familiarizing themselves with metrology tools used in conjunction with CNC machines can make them more versatile and appealing to employers. Opportunities also emerge in smaller, specialized machine shops or R&D facilities that value precision craftsmanship over mass production. Focusing on industries with high-value, low-volume production, such as defense contracting or scientific instrument manufacturing, can lead to stable and well-paying roles. Investing in certifications for specific materials or advanced machining techniques, even manual ones, also strengthens a candidate's position. Strategic career moves involve targeting companies that prioritize quality and customization, or those with extensive legacy equipment requiring expert repair, rather than focusing solely on large-scale production facilities.
Current Market Trends
The market for Manual Lathe Machinists in 2025 shows a nuanced demand. While high-volume production increasingly relies on Computer Numerical Control (CNC) machines for efficiency and precision, a persistent need exists for skilled manual machinists in specific niches. These include prototyping, custom one-off parts, repair work, specialized tooling, and situations where the flexibility and tactile feedback of a human operator are crucial over automated processes. Employers often seek individuals who can troubleshoot complex issues or perform intricate operations that even advanced CNC machines struggle with. The demand is not for mass production, but for precision craftsmanship.
Economic conditions, particularly in manufacturing and aerospace, directly influence the availability of manual lathe positions. When these sectors experience growth or face complex maintenance needs, demand for manual machinists strengthens. However, any slowdown in capital expenditure or factory output can lead to fewer new projects and, consequently, fewer openings. The integration of technology means that while manual skills are valued, employers increasingly prefer candidates who also possess foundational knowledge of CAD/CAM software or can interpret CNC programs, even if they primarily operate manual equipment. Salary trends for highly skilled manual machinists performing specialized work remain stable, often commanding good rates due to their unique expertise. However, positions requiring only basic manual operation may see stagnant wages due to the overall shift towards automation. Geographic variations are significant; areas with strong legacy manufacturing, heavy industry, or specialized repair shops show more consistent demand. Conversely, regions dominated by modern, automated factories may have fewer manual lathe opportunities. Remote work is not applicable to this hands-on role. Seasonal patterns are less pronounced than cyclical industry demands.
Emerging Specializations
The field of manual machining is evolving significantly, driven by advancements in materials science, automation, and precision engineering. While traditional manual lathe skills remain foundational, new specialization opportunities are emerging that integrate these core abilities with cutting-edge technologies. Professionals who strategically position themselves in these nascent areas can unlock substantial career advancement and often command premium compensation in 2025 and beyond.
Understanding these future-oriented paths allows machinists to proactively acquire relevant skills, moving beyond conventional roles into high-demand niches. Early positioning in emerging specializations provides a distinct competitive advantage, as these areas tend to experience rapid growth before becoming mainstream. This foresight enables machinists to become pioneers in new methodologies, securing roles that offer greater complexity, responsibility, and financial rewards.
However, pursuing emerging areas involves a balance between innovation and established expertise. While the potential for growth and higher earning is significant, some emerging fields require substantial investment in new tools and training. The timeline for these specializations to generate widespread job opportunities can vary, typically ranging from three to five years for significant market penetration. Evaluating the risk and reward of specializing in cutting-edge areas requires careful consideration of industry trends and personal career goals, ensuring a strategic and impactful career trajectory.
Advanced Composites Machinist
This specialization involves the precise machining of advanced composite materials like carbon fiber and Kevlar, which are increasingly used in aerospace, automotive, and medical industries. Manual lathe machinists in this area must understand how these materials behave differently under cutting stress compared to metals. The demand for lightweight, high-strength components is driving this niche, requiring precise material handling and specialized cutting techniques.
Robotics Component Machinist
This area focuses on machining components for robotics and automation systems, including intricate parts for robotic arms, end-effectors, and automated assembly lines. As industries worldwide increase automation, the need for custom, high-precision mechanical parts for these systems grows. Manual lathe machinists here produce prototypes and low-volume specialized components that automated CNC machines cannot efficiently create.
Exotic Alloy Machinist
This specialization involves working with exotic and superalloys, such as Inconel, Titanium, and Hastelloy, which are critical in demanding environments like jet engines, power generation, and chemical processing. These materials are notoriously difficult to machine due to their hardness and heat resistance, requiring specific tooling, slower speeds, and unique cooling strategies. The aerospace and energy sectors are driving the demand for these specialized skills.
Medical Device Components Machinist
This niche focuses on producing highly precise components for medical devices, surgical instruments, and laboratory equipment. These parts often have extremely tight tolerances and intricate geometries, sometimes requiring biocompatible materials. Manual lathe machinists in this field contribute to critical healthcare innovations, where precision and material integrity are paramount for patient safety and device functionality.
Custom Industrial Parts Fabricator
This specialization centers on creating bespoke or highly customized parts for industrial machinery and specialized equipment. Unlike mass production, this involves unique, often one-off components that require a deep understanding of mechanical function and material stress. Manual lathe machinists in this area solve complex engineering problems by fabricating custom solutions that integrate with existing systems or new prototypes.
Pros & Cons of Being a Manual Lathe Machinist
Understanding both the advantages and challenges of a career is crucial before making a commitment. A career as a Manual Lathe Machinist offers a unique blend of craftsmanship and technical skill. However, experiences can vary significantly based on the specific industry, company culture, and the types of projects undertaken. What one person views as an advantage, such as hands-on work, another might see as a challenge due to its physical demands. These pros and cons may also shift at different career stages; for instance, the initial learning curve might be a significant challenge, while later, the satisfaction of creating precision parts becomes a major pro. This assessment provides an honest, balanced perspective to help you set appropriate expectations for this specialized trade.
Pros
- Manual lathe machining offers a high degree of hands-on craftsmanship, allowing machinists to directly shape raw materials into precise components using their skill and intuition.
- There is strong demand for skilled manual machinists in specialized industries like aerospace, prototyping, and custom fabrication, where unique or low-volume parts are frequently required.
- The work provides immediate, tangible results; machinists can see and hold the precision parts they create, which offers a deep sense of accomplishment and satisfaction.
- Manual machining allows for significant problem-solving and improvisation, as machinists must often adapt techniques and tools on the fly to achieve exact specifications for unique or complex parts.
- Entry into this trade can be achieved through vocational training, apprenticeships, or on-the-job learning, often requiring less formal education than many other skilled trades or engineering roles.
- Manual machinists possess a highly specialized and valuable skill set that is not easily automated, making them indispensable for certain types of precision work and repairs.
- The ability to create custom, one-off parts makes the role crucial for research and development, enabling innovation across various industries by producing critical prototypes and components.
Cons
- The work environment can be physically demanding, requiring prolonged standing, heavy lifting, and exposure to noise, coolant, and metal shavings, which can lead to fatigue or respiratory issues over time.
- Repetitive tasks are common when producing multiple identical parts, which can lead to monotony and a lack of intellectual stimulation for some individuals, despite the precision required.
- Advancement opportunities within manual machining are often limited compared to CNC machining or engineering roles, as the focus remains on hands-on operation rather than programming or design.
- Job security can be less stable than in more automated fields, as companies may prioritize investments in CNC technology, potentially reducing the demand for purely manual operators.
- Income potential often plateaus after gaining experience, as manual machinists typically earn less than CNC machinists or those in higher-skilled manufacturing roles that require programming knowledge.
- There is a risk of injury from operating heavy machinery, sharp tools, and fast-moving parts, necessitating constant vigilance and strict adherence to safety protocols to prevent accidents.
- Manual machinists must often work to tight deadlines, especially when producing custom parts or prototypes, which can create pressure and require efficient, error-free work to meet production schedules and client expectations.
Frequently Asked Questions
Manual Lathe Machinists face distinct challenges balancing precision craftsmanship with physical demands. This section addresses the most common questions about entering this traditional, yet vital, trade, from mastering hands-on skills to understanding job stability and career progression in a modern manufacturing landscape.
What are the typical entry requirements or qualifications to become a Manual Lathe Machinist?
While a formal degree is not always required, most successful Manual Lathe Machinists complete a vocational training program, an apprenticeship, or a combination of on-the-job training. These programs typically cover blueprint reading, material properties, precision measurement, and safe machine operation. Employers highly value practical experience and a strong understanding of machining principles.
How long does it typically take to become a skilled Manual Lathe Machinist from scratch?
Becoming proficient enough to work independently as a Manual Lathe Machinist usually takes 1-3 years. An apprenticeship can last 3-4 years, providing comprehensive training. If you pursue vocational training, you might spend 6-12 months in a program, followed by 1-2 years of entry-level shop experience to build speed and accuracy. Continuous learning is essential throughout your career.
What are the salary expectations for a Manual Lathe Machinist, especially for new entrants versus experienced professionals?
Entry-level Manual Lathe Machinists can expect to earn a modest hourly wage, which increases significantly with experience and specialized skills. Experienced machinists with expertise in complex parts or exotic materials often command higher rates. Salary varies based on industry, location, and the specific demands of the job, but skilled machinists generally find stable, well-paying work.
What is the typical work-life balance like for a Manual Lathe Machinist, and is remote work an option?
The work-life balance for a Manual Lathe Machinist can vary. Many roles are full-time, often with standard day shifts, but some manufacturing environments may require evening or weekend shifts, or overtime, especially when production deadlines are tight. The work itself is hands-on and requires focus, but it typically does not involve extensive travel or remote work.
Is there strong job security and demand for Manual Lathe Machinists in today's manufacturing landscape?
The demand for skilled Manual Lathe Machinists remains steady, particularly for custom work, repairs, and prototypes where CNC machines may not be cost-effective or adaptable. While CNC technology has automated some tasks, the ability to operate manual machines with precision and troubleshoot complex issues makes manual machinists valuable. Job security is generally good for those with strong practical skills.
What are the potential career growth and advancement opportunities for a Manual Lathe Machinist?
Manual Lathe Machinists can advance by specializing in complex materials, precision grinding, or tooling. Career progression often involves moving into supervisory roles, becoming a lead machinist, or transitioning into CNC programming and operation. Some machinists also open their own shops, providing custom machining services. Continuous learning and adapting to new technologies are key for advancement.
What are some of the biggest challenges or common difficulties faced by Manual Lathe Machinists?
One significant challenge is the physical demand of the job, which often involves standing for long periods, lifting materials, and working with machinery. Another is maintaining extreme precision, as even tiny errors can scrap a part. Staying updated with new materials and techniques, as well as adhering to strict safety protocols, are also ongoing considerations in this field.
Are the skills learned as a Manual Lathe Machinist transferable to other roles or industries?
The core skills of a Manual Lathe Machinist, such as precision measurement, material science, and hands-on problem-solving, are highly transferable. These skills can be applied to other machining disciplines like milling, grinding, or even transitioning into quality control, design, or engineering technician roles. Understanding the fundamentals of manufacturing provides a strong base for various technical careers.
Related Careers
Explore similar roles that might align with your interests and skills:
Cnc Lathe Machinist
A growing field with similar skill requirements and career progression opportunities.
Explore career guideLathe Machinist
A growing field with similar skill requirements and career progression opportunities.
Explore career guideLathe Operator
A growing field with similar skill requirements and career progression opportunities.
Explore career guideManual Machinist
A growing field with similar skill requirements and career progression opportunities.
Explore career guideEngine Lathe Operator
A growing field with similar skill requirements and career progression opportunities.
Explore career guideAssess your Manual Lathe Machinist readiness
Understanding where you stand today is the first step toward your career goals. Our Career Coach helps identify skill gaps and create personalized plans.
Skills Gap Analysis
Get a detailed assessment of your current skills versus Manual Lathe Machinist requirements. Our AI Career Coach identifies specific areas for improvement with personalized recommendations.
See your skills gapCareer Readiness Assessment
Evaluate your overall readiness for Manual Lathe Machinist roles with our AI Career Coach. Receive personalized recommendations for education, projects, and experience to boost your competitiveness.
Assess your readinessSimple pricing, powerful features
Upgrade to Himalayas Plus and turbocharge your job search.
Himalayas
Himalayas Plus
Himalayas Max
Find your dream job
Sign up now and join over 100,000 remote workers who receive personalized job alerts, curated job matches, and more for free!
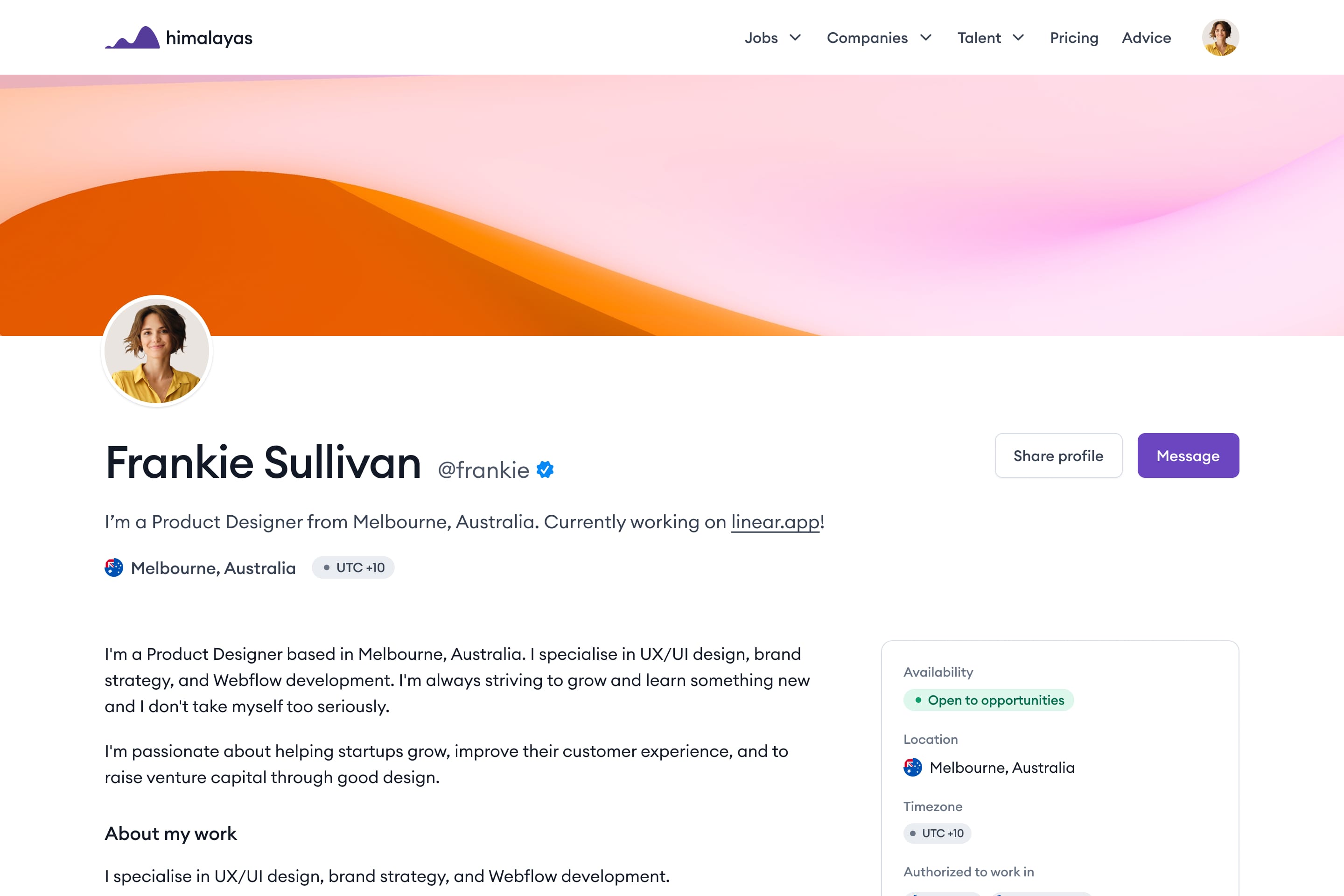