Complete Maintenance Engineer Career Guide
Maintenance engineers are the unsung heroes of industry, ensuring complex machinery and systems operate smoothly and efficiently to prevent costly downtime. They blend engineering principles with hands-on problem-solving, optimizing performance and extending equipment lifespans in diverse sectors. This vital role offers a stable career path for those who enjoy diagnosing issues, implementing solutions, and continuously improving operational reliability.
Key Facts & Statistics
Median Salary
$99,040 USD
(U.S. Bureau of Labor Statistics, May 2023)
Range: $65,000 - $130,000+ USD
Growth Outlook
6%
as fast as average (U.S. Bureau of Labor Statistics, 2022-2032)
Annual Openings
≈11,800
openings annually (U.S. Bureau of Labor Statistics, 2022-2032)
Top Industries
Typical Education
Bachelor's degree in Mechanical, Electrical, or Industrial Engineering; some roles may accept an Associate's degree with extensive experience and certifications.
What is a Maintenance Engineer?
A Maintenance Engineer is a specialized professional responsible for ensuring the reliability, efficiency, and safety of industrial machinery, equipment, and systems. They design, implement, and manage maintenance strategies to prevent failures, optimize performance, and extend the lifespan of critical assets within an organization. Their core purpose is to minimize downtime, reduce operational costs, and uphold safety standards, directly impacting productivity and profitability.
This role distinguishes itself from a general maintenance technician, who primarily executes repairs, by focusing on the strategic planning, analytical assessment, and continuous improvement of maintenance processes. While a technician reacts to immediate issues, a maintenance engineer proactively identifies systemic problems, develops long-term solutions, and integrates engineering principles into maintenance practices. They often bridge the gap between technical execution and strategic business objectives, applying engineering knowledge to complex operational challenges.
What does a Maintenance Engineer do?
Key Responsibilities
- Conduct routine inspections of machinery and equipment to identify potential issues before they cause breakdowns.
- Develop and implement preventive maintenance schedules and procedures to extend asset lifespan and minimize downtime.
- Diagnose complex mechanical, electrical, and hydraulic problems using diagnostic tools and technical manuals.
- Perform corrective maintenance and repairs on industrial equipment, ensuring compliance with safety standards and operational specifications.
- Collaborate with production teams to coordinate maintenance activities, minimizing disruption to manufacturing processes.
- Analyze equipment performance data and maintenance records to identify trends and recommend improvements.
- Procure necessary spare parts and materials, managing inventory levels to support ongoing maintenance operations and project work.
Work Environment
Maintenance engineers typically work in industrial settings such as manufacturing plants, power stations, or large commercial facilities. The environment can be dynamic, often involving exposure to noise, varying temperatures, and moving machinery. They spend a significant portion of their time on the factory floor or in equipment rooms, directly interacting with machinery, but also have office time for planning, analysis, and documentation.
Collaboration with production operators, technicians, and other engineering disciplines is constant. The pace of work can be highly variable; routine tasks fill scheduled hours, but urgent breakdowns demand immediate, high-pressure responses, sometimes requiring irregular hours or on-call availability. While some roles are site-specific, others might involve travel between multiple facilities.
Tools & Technologies
Maintenance engineers regularly use a variety of specialized tools and diagnostic equipment, including multimeters, oscilloscopes, thermal imaging cameras, and vibration analyzers. They work extensively with Computerized Maintenance Management Systems (CMMS) such as SAP PM, Maximo, or Fiix, for scheduling, tracking work orders, and managing inventory. Proficiency with CAD software like AutoCAD or SolidWorks is often necessary for reviewing schematics and designing modifications.
They also utilize enterprise resource planning (ERP) systems for procurement and inventory management, and various data analysis tools like Microsoft Excel or specialized statistical software for performance tracking. Experience with programmable logic controllers (PLCs) and industrial control systems (ICS) is crucial for troubleshooting automated machinery. Safety equipment, including lockout/tagout devices and personal protective equipment (PPE), is fundamental to their daily work.
Maintenance Engineer Skills & Qualifications
Maintenance Engineers play a crucial role in ensuring the reliability and efficiency of industrial operations. Their qualifications are a blend of formal education, practical hands-on experience, and specialized certifications. Entry-level positions often require a bachelor's degree in an engineering discipline, while senior roles demand extensive experience, sometimes coupled with a master's degree or professional engineering licensure.
Requirements for Maintenance Engineers vary significantly by industry sector, company size, and geographic location. For instance, a Maintenance Engineer in a highly regulated pharmaceutical plant needs strong adherence to GMP (Good Manufacturing Practices) and validation protocols, whereas one in a heavy manufacturing plant prioritizes robust mechanical and hydraulic system expertise. Smaller companies might seek generalists, while larger corporations often look for specialists in areas like predictive maintenance or robotics. Geographic differences can also influence the emphasis on specific certifications or local safety regulations.
Formal education provides foundational knowledge, but practical experience is paramount for Maintenance Engineers. Certifications in specific equipment, safety protocols, or maintenance methodologies (like Lean or Six Sigma) add significant value and can sometimes compensate for less traditional educational backgrounds. The field is rapidly evolving with the integration of IoT, AI, and advanced analytics for predictive maintenance. Therefore, continuous learning in these emerging technologies is becoming a 'must-have' rather than a 'nice-to-have' for long-term career success, shifting the balance from reactive to proactive maintenance strategies.
Education Requirements
Technical Skills
- Mechanical Systems Troubleshooting and Repair (e.g., hydraulics, pneumatics, rotating equipment, pumps, conveyors)
- Electrical Systems Diagnostics (e.g., motor controls, PLCs, sensors, industrial wiring, power distribution)
- Preventive and Predictive Maintenance Techniques (e.g., vibration analysis, thermography, oil analysis, ultrasonic testing)
- Computerized Maintenance Management Systems (CMMS) operation and administration (e.g., SAP PM, Maximo, Fiix)
- Root Cause Analysis (RCA) and Failure Mode and Effects Analysis (FMEA) methodologies
- Blueprint and Schematic Reading (mechanical, electrical, P&ID diagrams)
- Industrial Control Systems (ICS) and Programmable Logic Controllers (PLCs) programming and troubleshooting (e.g., Siemens, Rockwell Automation)
- Knowledge of relevant safety regulations and standards (e.g., OSHA, Lockout/Tagout, confined space entry)
- Reliability Centered Maintenance (RCM) principles and implementation
- Data analysis and statistical process control for maintenance optimization
- Knowledge of Lean Manufacturing and Six Sigma principles as applied to maintenance operations
- Basic metallurgy and material science for component selection and failure analysis
Soft Skills
- Problem-solving and Analytical Thinking: Maintenance Engineers must diagnose complex equipment failures by analyzing symptoms, data, and historical records to identify root causes and implement effective, lasting solutions.
- Attention to Detail: Precision is critical in maintenance to prevent errors that could lead to further breakdowns, safety hazards, or production losses. This includes meticulously following procedures and documenting work.
- Communication and Documentation: Clear verbal and written communication is essential for conveying technical information to technicians, management, and cross-functional teams, as well as for creating comprehensive maintenance reports and procedures.
- Adaptability and Resilience: Equipment failures are often unpredictable, requiring Maintenance Engineers to quickly adapt to changing priorities, work under pressure, and remain composed during critical breakdowns.
- Team Collaboration and Leadership: Often working with maintenance technicians, operators, and other engineers, the ability to collaborate, delegate tasks, and provide technical guidance is vital for efficient repairs and project execution.
- Proactive Planning and Organization: Effective maintenance involves anticipating potential issues, scheduling preventive maintenance, and managing resources efficiently to minimize downtime and optimize asset performance.
- Safety Consciousness: A deep commitment to safety protocols and procedures is paramount to protect themselves, their team, and the operational environment from hazards associated with industrial machinery.
- Continuous Learning and Improvement: The industrial landscape constantly evolves with new technologies and methodologies. Maintenance Engineers must actively seek to learn new skills and apply continuous improvement principles to maintenance processes.
How to Become a Maintenance Engineer
Breaking into the Maintenance Engineer field involves several pathways, from vocational training to university degrees, each with varying timelines and advantages. A complete beginner might spend 1-2 years acquiring foundational skills through a technical diploma or apprenticeship, while someone transitioning from a related trade like an electrician or mechanic could leverage existing skills to enter faster, perhaps in 6-12 months after targeted upskilling. University graduates in engineering disciplines, such as Mechanical or Electrical Engineering, often find entry-level roles within 3-6 months of graduation, though practical experience through internships is crucial.
Entry strategies vary significantly by industry and company size. Large manufacturing plants or corporations may prefer candidates with formal engineering degrees and certifications, offering structured graduate programs. Smaller companies or local facilities might prioritize hands-on experience and vocational qualifications. Geographic location also plays a role; industrial hubs will have more opportunities and potentially more specialized roles. Misconceptions include believing that only a four-year degree guarantees entry; many successful maintenance engineers start with vocational training and apprenticeships, gaining hands-on experience that is highly valued.
Networking within industrial communities, attending trade shows, and connecting with seasoned professionals can open doors to mentorship and job opportunities. The hiring landscape values a blend of theoretical knowledge and practical problem-solving abilities. Overcoming barriers often involves demonstrating a strong aptitude for diagnostics, repair, and continuous learning, often through personal projects or volunteer work that showcases mechanical or electrical proficiency.
Acquire foundational technical skills through a relevant educational program. Consider a vocational diploma in industrial maintenance, an associate's degree in engineering technology, or a bachelor's degree in mechanical or electrical engineering. This step provides the theoretical knowledge and basic practical skills necessary for understanding complex machinery and systems, typically taking 1-4 years depending on the chosen path.
Gain hands-on practical experience through internships, apprenticeships, or entry-level technician roles. Seek opportunities in manufacturing, facilities management, or industrial settings where you can work alongside experienced technicians and engineers. This practical exposure, often lasting 6-12 months, helps bridge the gap between theoretical knowledge and real-world application, building confidence and problem-solving abilities.
Develop specialized skills and obtain relevant certifications. Focus on areas like PLC programming, hydraulic systems, pneumatic systems, welding, or specific machinery operation, depending on your career interests and industry demands. Certifications from organizations like SMRP (CMRP) or specific vendor training can significantly enhance your resume and demonstrate expertise, usually requiring a few months of dedicated study and practice.
Build a professional network within the maintenance and engineering community. Attend industry conferences, local trade association meetings, and online forums to connect with professionals, learn about emerging technologies, and uncover potential job opportunities. Networking helps you gain insights into industry trends and can lead to mentorship and direct referrals, accelerating your job search.
Prepare a targeted resume and cover letter that highlights your technical skills, practical experience, and problem-solving capabilities. Tailor each application to the specific requirements of the job description, using keywords from the posting. Include any projects or experiences where you successfully diagnosed and resolved equipment issues, demonstrating your value to potential employers.
Actively search for entry-level Maintenance Engineer positions and prepare for technical interviews. Look for roles such as Junior Maintenance Engineer, Maintenance Technician, or Reliability Technician, as these often serve as stepping stones. Practice explaining your technical knowledge and problem-solving approach to common maintenance scenarios, focusing on how you would diagnose and repair equipment failures.
Step 1
Acquire foundational technical skills through a relevant educational program. Consider a vocational diploma in industrial maintenance, an associate's degree in engineering technology, or a bachelor's degree in mechanical or electrical engineering. This step provides the theoretical knowledge and basic practical skills necessary for understanding complex machinery and systems, typically taking 1-4 years depending on the chosen path.
Step 2
Gain hands-on practical experience through internships, apprenticeships, or entry-level technician roles. Seek opportunities in manufacturing, facilities management, or industrial settings where you can work alongside experienced technicians and engineers. This practical exposure, often lasting 6-12 months, helps bridge the gap between theoretical knowledge and real-world application, building confidence and problem-solving abilities.
Step 3
Develop specialized skills and obtain relevant certifications. Focus on areas like PLC programming, hydraulic systems, pneumatic systems, welding, or specific machinery operation, depending on your career interests and industry demands. Certifications from organizations like SMRP (CMRP) or specific vendor training can significantly enhance your resume and demonstrate expertise, usually requiring a few months of dedicated study and practice.
Step 4
Build a professional network within the maintenance and engineering community. Attend industry conferences, local trade association meetings, and online forums to connect with professionals, learn about emerging technologies, and uncover potential job opportunities. Networking helps you gain insights into industry trends and can lead to mentorship and direct referrals, accelerating your job search.
Step 5
Prepare a targeted resume and cover letter that highlights your technical skills, practical experience, and problem-solving capabilities. Tailor each application to the specific requirements of the job description, using keywords from the posting. Include any projects or experiences where you successfully diagnosed and resolved equipment issues, demonstrating your value to potential employers.
Step 6
Actively search for entry-level Maintenance Engineer positions and prepare for technical interviews. Look for roles such as Junior Maintenance Engineer, Maintenance Technician, or Reliability Technician, as these often serve as stepping stones. Practice explaining your technical knowledge and problem-solving approach to common maintenance scenarios, focusing on how you would diagnose and repair equipment failures.
Education & Training Needed to Become a Maintenance Engineer
Becoming a Maintenance Engineer requires a blend of theoretical knowledge and practical skills. Formal university degrees, such as a Bachelor's in Mechanical Engineering, Electrical Engineering, or Industrial Engineering, provide a strong foundational understanding of systems and analysis. These 4-year programs typically cost $40,000-$100,000+ for in-state tuition at public universities, and significantly more for private institutions. While comprehensive, the time commitment is substantial, and graduates often need additional on-the-job training to bridge the gap between theory and practical application.
Alternative pathways include vocational training programs, associate's degrees in maintenance technology, or specialized certifications. These options range from 6 months to 2 years, with costs varying from $5,000 to $25,000. They focus heavily on hands-on skills like troubleshooting, repair, and preventive maintenance. Employers often highly value these practical credentials, especially for entry-level or technician-focused roles, as they indicate immediate readiness for fieldwork. Companies increasingly accept a mix of formal education and practical certifications.
Continuous learning is crucial for Maintenance Engineers. The field evolves with new technologies like predictive analytics, IoT, and automation. Professional development courses, manufacturer-specific training, and certifications in areas like Lean Manufacturing or Six Sigma enhance career progression and earning potential. Self-study through online platforms and industry forums also plays a vital role in staying current. The cost-benefit analysis often favors a balanced approach: a solid technical foundation combined with targeted, ongoing skill development. Practical experience remains paramount; certifications and degrees complement, rather than replace, hands-on work and problem-solving abilities.
Maintenance Engineer Salary & Outlook
Compensation for a Maintenance Engineer varies significantly based on multiple factors. Geographic location plays a crucial role, with higher salaries typically found in areas with a high cost of living or strong industrial presence, such as major manufacturing hubs or energy sectors. Conversely, rural areas or regions with lower industrial density may offer more modest compensation.
Years of experience dramatically influence earning potential. Entry-level engineers start at a foundational salary, which grows substantially with demonstrated expertise in specific equipment, systems, or process optimization. Specialization areas like reliability engineering, automation systems, or specific industry knowledge (e.g., aerospace, pharmaceuticals) can command premium compensation.
Total compensation extends beyond base salary. Many roles include performance-based bonuses, especially in production-driven environments. Benefits packages, encompassing health insurance, retirement contributions like 401(k) matching, and paid time off, form a significant part of the overall value. Some companies also offer allowances for professional development or certifications, enhancing long-term career growth.
Industry-specific trends also impact salary. High-tech manufacturing or highly regulated industries often offer more competitive packages due to the complexity and critical nature of their operations. Remote work for Maintenance Engineers is less common but can impact salary ranges if a role allows for strategic oversight or predictive maintenance analysis from a distance. Salary figures provided typically refer to the US market, while international compensation varies widely based on local economic conditions and labor laws.
Salary by Experience Level
Level | US Median | US Average |
---|---|---|
Junior Maintenance Engineer | $65k USD | $70k USD |
Maintenance Engineer | $85k USD | $88k USD |
Senior Maintenance Engineer | $102k USD | $105k USD |
Lead Maintenance Engineer | $115k USD | $120k USD |
Maintenance Supervisor | $98k USD | $100k USD |
Maintenance Manager | $130k USD | $135k USD |
Director of Maintenance | $165k USD | $170k USD |
Market Commentary
The job market for Maintenance Engineers shows stable demand, driven by the continuous need for operational efficiency and asset longevity across various industries. Projections indicate a steady growth outlook, particularly as industries adopt advanced manufacturing techniques and smart factory concepts. The Bureau of Labor Statistics projects a modest growth for industrial engineers, a category that often includes maintenance engineers, reflecting consistent demand rather than rapid expansion.
Emerging opportunities lie in predictive maintenance, leveraging IoT sensors, data analytics, and artificial intelligence to anticipate equipment failures before they occur. This shift from reactive to proactive maintenance requires engineers with strong analytical skills and a grasp of digital technologies. Roles are evolving to include more data interpretation, automation integration, and strategic planning, rather than just hands-on repair.
The supply and demand dynamics are generally balanced, though specialized skills in areas like robotics, advanced PLCs, or specific industry certifications can create a higher demand for qualified candidates. Economic shifts, such as increased investment in infrastructure or renewed domestic manufacturing, can further boost job availability. However, economic downturns might see a temporary slowdown in new capital projects, impacting some roles.
Future-proofing this career involves continuous learning in automation, data science, and cybersecurity as it pertains to operational technology. While some routine tasks may become automated, the strategic oversight, problem-solving, and system integration aspects of the Maintenance Engineer role remain critical and largely resistant to full automation. Geographic hotspots for this role include states with significant manufacturing, energy production, or logistics industries, such as Texas, California, Michigan, and Pennsylvania.
Maintenance Engineer Career Path
Career progression for a Maintenance Engineer typically follows a structured path, emphasizing hands-on technical expertise, problem-solving capabilities, and a gradual transition into leadership and strategic planning. Professionals advance by mastering complex systems, optimizing operational efficiency, and demonstrating strong analytical skills to minimize downtime.
Advancement speed depends on several factors, including individual performance, the complexity of the assets managed, and the industry sector—for example, manufacturing, utilities, or facilities management. Larger organizations often provide more defined individual contributor (IC) tracks leading to specialized expert roles, alongside management/leadership tracks. Smaller companies may offer quicker progression but with a broader range of responsibilities.
Lateral moves are common, allowing engineers to specialize in areas like reliability engineering, asset management, or specific equipment types. Continuous learning, certifications in areas like Lean Six Sigma or vibration analysis, and active networking within industry associations significantly influence career trajectory. Mentorship also plays a crucial role in developing leadership and strategic thinking for higher-level positions.
Junior Maintenance Engineer
0-2 yearsPerforms routine preventive maintenance, assists with corrective repairs under direct supervision, and learns to operate and maintain various types of industrial equipment. Documents maintenance activities and contributes to maintaining a safe work environment. Works on individual tasks or as part of a small team.
Key Focus Areas
Develop foundational understanding of mechanical, electrical, and hydraulic systems. Learn to use maintenance software and diagnostic tools. Focus on safety protocols, basic troubleshooting, and effective communication with senior team members. Gain practical experience with preventive and corrective maintenance tasks.
Maintenance Engineer
2-5 yearsExecutes complex preventive and corrective maintenance tasks independently. Diagnoses and resolves equipment malfunctions, often taking the lead on specific repair projects. Collaborates with production teams to schedule maintenance and minimize operational disruption. Provides guidance to junior team members.
Key Focus Areas
Enhance diagnostic and troubleshooting skills for complex equipment failures. Specialize in specific machinery or systems. Improve efficiency in maintenance tasks, contributing to reduced downtime. Develop stronger problem-solving abilities and effective communication with operations teams.
Senior Maintenance Engineer
5-8 yearsActs as a technical expert, leading complex repairs and critical maintenance projects. Conducts root cause analyses for recurring failures and implements sustainable solutions. Designs and optimizes preventive maintenance schedules. Mentors junior engineers and contributes to training programs.
Key Focus Areas
Master advanced troubleshooting and root cause analysis techniques. Develop skills in reliability engineering and predictive maintenance technologies. Mentor junior engineers and lead small maintenance projects. Focus on optimizing maintenance procedures and improving asset longevity.
Lead Maintenance Engineer
7-10 yearsLeads a team of maintenance engineers and technicians on specific projects or shifts. Responsible for planning, coordinating, and executing maintenance activities to meet operational goals. Troubleshoots critical issues, allocates resources, and ensures adherence to safety and quality standards. Provides technical guidance and support.
Key Focus Areas
Develop strong leadership and project management skills. Focus on optimizing team efficiency and resource allocation for maintenance activities. Gain expertise in maintenance planning, scheduling, and budgeting. Improve cross-functional collaboration and communication abilities.
Maintenance Supervisor
8-12 yearsManages a team of maintenance personnel, overseeing daily operations, scheduling, and performance. Ensures maintenance activities align with production targets and safety regulations. Conducts performance reviews, identifies training needs, and implements continuous improvement initiatives. Responsible for team-level budget adherence.
Key Focus Areas
Enhance team leadership, motivation, and performance management skills. Develop expertise in maintenance KPIs, budget management, and continuous improvement methodologies. Focus on developing team members and fostering a strong safety culture. Improve strategic planning for daily operations.
Maintenance Manager
12-18 yearsOversees the entire maintenance department, developing and executing maintenance strategies that support business objectives. Manages departmental budgets, asset reliability programs, and capital projects. Leads continuous improvement efforts and ensures compliance with all regulatory requirements. Responsible for staff development and departmental performance metrics.
Key Focus Areas
Develop strategic planning, financial management, and leadership skills at a departmental level. Focus on asset lifecycle management, capital expenditure planning, and vendor negotiations. Improve cross-departmental collaboration and contribute to broader organizational objectives. Gain expertise in maintenance software implementation.
Director of Maintenance
18+ yearsProvides executive leadership for all maintenance and reliability functions across an organization or multiple sites. Develops long-term maintenance strategies, technological roadmaps, and capital investment plans. Responsible for overall asset performance, operational uptime, and strategic resource allocation. Represents maintenance at the executive level and drives organizational change.
Key Focus Areas
Master executive leadership, organizational strategy, and enterprise-level asset management. Focus on long-term capital planning, technological innovation, and risk management across multiple facilities or business units. Develop strong communication and influencing skills for executive stakeholders.
Junior Maintenance Engineer
0-2 yearsPerforms routine preventive maintenance, assists with corrective repairs under direct supervision, and learns to operate and maintain various types of industrial equipment. Documents maintenance activities and contributes to maintaining a safe work environment. Works on individual tasks or as part of a small team.
Key Focus Areas
Develop foundational understanding of mechanical, electrical, and hydraulic systems. Learn to use maintenance software and diagnostic tools. Focus on safety protocols, basic troubleshooting, and effective communication with senior team members. Gain practical experience with preventive and corrective maintenance tasks.
Maintenance Engineer
2-5 yearsExecutes complex preventive and corrective maintenance tasks independently. Diagnoses and resolves equipment malfunctions, often taking the lead on specific repair projects. Collaborates with production teams to schedule maintenance and minimize operational disruption. Provides guidance to junior team members.
Key Focus Areas
Enhance diagnostic and troubleshooting skills for complex equipment failures. Specialize in specific machinery or systems. Improve efficiency in maintenance tasks, contributing to reduced downtime. Develop stronger problem-solving abilities and effective communication with operations teams.
Senior Maintenance Engineer
5-8 yearsActs as a technical expert, leading complex repairs and critical maintenance projects. Conducts root cause analyses for recurring failures and implements sustainable solutions. Designs and optimizes preventive maintenance schedules. Mentors junior engineers and contributes to training programs.
Key Focus Areas
Master advanced troubleshooting and root cause analysis techniques. Develop skills in reliability engineering and predictive maintenance technologies. Mentor junior engineers and lead small maintenance projects. Focus on optimizing maintenance procedures and improving asset longevity.
Lead Maintenance Engineer
7-10 yearsLeads a team of maintenance engineers and technicians on specific projects or shifts. Responsible for planning, coordinating, and executing maintenance activities to meet operational goals. Troubleshoots critical issues, allocates resources, and ensures adherence to safety and quality standards. Provides technical guidance and support.
Key Focus Areas
Develop strong leadership and project management skills. Focus on optimizing team efficiency and resource allocation for maintenance activities. Gain expertise in maintenance planning, scheduling, and budgeting. Improve cross-functional collaboration and communication abilities.
Maintenance Supervisor
8-12 yearsManages a team of maintenance personnel, overseeing daily operations, scheduling, and performance. Ensures maintenance activities align with production targets and safety regulations. Conducts performance reviews, identifies training needs, and implements continuous improvement initiatives. Responsible for team-level budget adherence.
Key Focus Areas
Enhance team leadership, motivation, and performance management skills. Develop expertise in maintenance KPIs, budget management, and continuous improvement methodologies. Focus on developing team members and fostering a strong safety culture. Improve strategic planning for daily operations.
Maintenance Manager
12-18 yearsOversees the entire maintenance department, developing and executing maintenance strategies that support business objectives. Manages departmental budgets, asset reliability programs, and capital projects. Leads continuous improvement efforts and ensures compliance with all regulatory requirements. Responsible for staff development and departmental performance metrics.
Key Focus Areas
Develop strategic planning, financial management, and leadership skills at a departmental level. Focus on asset lifecycle management, capital expenditure planning, and vendor negotiations. Improve cross-departmental collaboration and contribute to broader organizational objectives. Gain expertise in maintenance software implementation.
Director of Maintenance
18+ yearsProvides executive leadership for all maintenance and reliability functions across an organization or multiple sites. Develops long-term maintenance strategies, technological roadmaps, and capital investment plans. Responsible for overall asset performance, operational uptime, and strategic resource allocation. Represents maintenance at the executive level and drives organizational change.
Key Focus Areas
Master executive leadership, organizational strategy, and enterprise-level asset management. Focus on long-term capital planning, technological innovation, and risk management across multiple facilities or business units. Develop strong communication and influencing skills for executive stakeholders.
Job Application Toolkit
Ace your application with our purpose-built resources:
Maintenance Engineer Resume Examples
Proven layouts and keywords hiring managers scan for.
View examplesMaintenance Engineer Cover Letter Examples
Personalizable templates that showcase your impact.
View examplesTop Maintenance Engineer Interview Questions
Practice with the questions asked most often.
View examplesMaintenance Engineer Job Description Template
Ready-to-use JD for recruiters and hiring teams.
View examplesGlobal Maintenance Engineer Opportunities
Maintenance Engineers are globally in high demand across manufacturing, energy, and infrastructure sectors. This role focuses on optimizing asset performance and ensuring operational reliability, a critical need worldwide. International opportunities arise from diverse industrial landscapes and varying regulatory environments. Professionals seeking international roles often find their skills highly transferable, especially with certifications like CMRP or CMMS proficiency. Cultural nuances impact safety standards and operational protocols, but core engineering principles remain universal.
Global Salaries
Maintenance Engineer salaries vary significantly by region and industrial sector. In North America, particularly the US, a Maintenance Engineer earns between $70,000 and $100,000 USD annually. Canada offers similar ranges, from CAD $65,000 to CAD $95,000. These figures reflect a high cost of living in major industrial hubs.
European salaries differ by country. In Germany, a Maintenance Engineer might earn €55,000 to €80,000 (approximately $60,000-$87,000 USD). The UK offers £40,000 to £60,000 (around $50,000-$75,000 USD). Northern European countries generally offer higher compensation, but also have higher living costs and tax burdens. Southern Europe typically has lower salaries and living expenses.
Asia-Pacific markets like Australia and Singapore present competitive salaries, often ranging from AUD $80,000 to AUD $110,000 (around $55,000-$75,000 USD) and SGD $60,000 to SGD $90,000 (about $45,000-$67,000 USD), respectively. These regions often have lower personal income taxes. In contrast, Latin America, such as Brazil or Mexico, sees Maintenance Engineers earning between $25,000 and $45,000 USD, which offers strong purchasing power due to lower living costs.
Salary structures also include varying benefits. North America often provides robust health insurance and retirement plans. Europe emphasizes generous vacation time and public healthcare. Tax implications significantly affect take-home pay; for instance, high-tax European countries reduce net income more than lower-tax Asian nations. Experience and specialized certifications, like Six Sigma or Lean Manufacturing, significantly enhance earning potential globally.
Remote Work
Purely remote work for Maintenance Engineers is generally limited due to the hands-on nature of the role. Most positions require physical presence for equipment inspection, repair, and operational oversight. However, hybrid models are emerging where planning, data analysis, and predictive maintenance monitoring occur remotely. This allows engineers to manage multiple sites or collaborate with international teams.
Digital nomad opportunities are less common, but some specialized consulting roles in maintenance strategy or CMMS implementation can be fully remote. Legal and tax implications for international remote work are complex, requiring careful consideration of tax residency and employer compliance. Companies hiring internationally often establish local entities or use employer of record services.
Time zone differences impact international team collaboration, necessitating flexible working hours. Platforms like SAP PM, Maximo, or Infor EAM facilitate remote data analysis and task management. Equipment and internet requirements for remote work are typically standard, focusing on reliable connectivity and secure access to industrial systems.
Visa & Immigration
Maintenance Engineers often qualify for skilled worker visas in many countries. Popular destinations include Canada, Australia, Germany, and the UK, which value engineering expertise. Requirements typically involve a recognized engineering degree, relevant work experience, and sometimes professional registration or licensing. For instance, Engineers Australia or Engineers Canada assess credentials.
Common visa categories include the Canadian Express Entry (Federal Skilled Worker Program), Australian Skilled Independent Visa (Subclass 189), German Blue Card, and UK Skilled Worker Visa. Each requires specific points for age, education, language proficiency (IELTS or TOEFL), and work experience. The application process usually involves credential assessment, English language testing, and submitting a comprehensive application, often taking several months.
Intra-company transfers are also common for large multinational corporations. Pathways to permanent residency exist in countries like Canada and Australia after a few years of skilled employment. Language requirements vary; Germany often requires B1/B2 German, while English-speaking countries test English proficiency. Family visas are usually available for spouses and dependent children.
2025 Market Reality for Maintenance Engineers
Understanding current market conditions is vital for maintenance engineers. The field has evolved significantly from 2023 to 2025, driven by post-pandemic reshoring efforts and the accelerating AI revolution.
Broader economic factors, such as supply chain stability and industrial investment, directly influence job availability and project scope. Market realities vary considerably based on an engineer's experience level, the specific industry (e.g., manufacturing, energy, data centers), and the geographic region. This analysis provides an honest assessment of these dynamics, helping engineers navigate a complex and changing landscape.
Current Challenges
Maintenance engineers face increasing competition, especially for roles requiring specialized automation or predictive maintenance skills. Many entry-level positions are becoming harder to secure due to a preference for experienced candidates.
Economic uncertainty causes some companies to delay equipment upgrades, reducing demand for new maintenance strategies. Keeping up with rapid technological changes, particularly in AI-driven diagnostics, requires continuous learning.
Growth Opportunities
Strong opportunities exist for maintenance engineers specializing in predictive maintenance, robotics, and industrial automation. Roles focused on implementing and managing AI-driven diagnostic systems are rapidly emerging and highly sought after.
Engineers who can analyze large datasets from machinery, optimize asset performance, and integrate smart technologies gain a significant competitive advantage. Focusing on sectors like renewable energy, advanced manufacturing, and data centers offers better prospects, as these industries continue to invest heavily in infrastructure and automation.
Upskilling in machine learning, IoT, and data analytics can open doors to specialized, higher-paying roles. Consider certifications in specific automation platforms or predictive software. These strategic career moves can make maintenance engineers indispensable, even amidst broader market shifts.
Current Market Trends
Demand for maintenance engineers remains steady, but hiring patterns are shifting. Companies prioritize proactive and predictive maintenance, moving away from reactive approaches. This means engineers need strong analytical skills to interpret data from IoT sensors and smart machinery.
AI integration significantly impacts the field. Generative AI tools assist in troubleshooting, while machine learning algorithms predict equipment failures. This changes employer requirements, favoring engineers who can implement and manage these advanced systems, not just repair them.
Economic conditions show a mixed impact. While some manufacturing sectors experienced slowdowns, essential infrastructure and highly automated facilities continue robust hiring. Salary trends for engineers with expertise in Industry 4.0 technologies and AI-powered predictive maintenance are rising, reflecting a skill premium.
Market saturation exists at the basic repair level, but a shortage of engineers proficient in data analytics, robotics, and complex automation systems persists. Geographic variations are notable; dense industrial regions and data center hubs show stronger demand. Remote work is rare for this hands-on role, though remote monitoring and diagnostic support are increasing.
Emerging Specializations
The field of Maintenance Engineering is undergoing a significant transformation, driven by rapid advancements in digital technologies and a growing emphasis on sustainability. Traditional reactive maintenance models are giving way to proactive, data-driven strategies, creating entirely new specialization opportunities. Professionals who position themselves early in these emerging areas can secure a considerable advantage, often commanding premium compensation and accelerated career growth.
Understanding these future-oriented paths is crucial for career advancement from 2025 onwards. Specializing in cutting-edge areas allows engineers to become indispensable assets, leading innovation rather than merely adapting to it. While established specializations remain vital, exploring nascent fields offers the chance to define new industry standards and solve complex, evolving problems.
Many emerging areas, particularly those at the intersection of engineering and data science, are poised to become mainstream within the next three to five years, creating a significant number of job opportunities. Pursuing these specializations involves a balance of risk and reward. Early adopters face the challenge of pioneering new methods and technologies, but they also reap the benefits of being at the forefront of industry evolution, shaping the future of maintenance and asset management.
Predictive Maintenance Engineer
Predictive Maintenance Engineers specialize in leveraging machine learning and advanced analytics to forecast equipment failures before they occur. This involves integrating sensor data from industrial assets with sophisticated algorithms to identify patterns indicative of impending issues, moving beyond traditional scheduled maintenance. Their work significantly reduces downtime, optimizes operational efficiency, and extends asset lifecycles, making them critical for modern, cost-efficient operations.
Digital Twin Maintenance Engineer
Digital Twin Maintenance Engineers create and manage virtual replicas of physical assets and systems. These digital twins allow for real-time monitoring, simulation of operational scenarios, and predictive analysis without impacting the physical asset. This specialization enables precise fault diagnosis, optimized maintenance scheduling, and virtual testing of repair strategies, offering unprecedented control and foresight in asset management.
Robotics and Automation Maintenance Engineer
Robotics and Automation Maintenance Engineers focus on the upkeep, programming, and troubleshooting of robotic systems and automated machinery within industrial environments. As automation becomes ubiquitous across manufacturing and logistics, ensuring the continuous operation and optimal performance of these complex systems is paramount. This specialization involves both mechanical and software diagnostics, ensuring high uptime and efficiency.
Sustainable Asset Lifecycle Engineer
Sustainable Asset Lifecycle Engineers specialize in optimizing the environmental impact and resource efficiency of industrial assets throughout their entire lifecycle, from design to decommissioning. This involves implementing strategies for energy conservation, waste reduction, material reuse, and carbon footprint minimization within maintenance operations. Their role is increasingly critical as industries face stricter environmental regulations and greater pressure for eco-friendly practices.
Cyber-Physical Systems Maintenance Engineer
Cyber-Physical Systems Maintenance Engineers focus on securing and maintaining the operational integrity of interconnected industrial control systems (ICS) and operational technology (OT) networks. With the convergence of IT and OT, these professionals protect critical infrastructure from cyber threats that could disrupt maintenance operations or cause system failures. Their expertise ensures the resilience and reliability of smart factories and connected assets.
Pros & Cons of Being a Maintenance Engineer
Making informed career decisions requires a thorough understanding of both the benefits and challenges associated with a specific profession. A career as a Maintenance Engineer offers unique rewards and significant hurdles. Be aware that experiences can vary considerably based on the industry sector, company culture, specific equipment managed, and the individual's role within a maintenance team. The pros and cons may also shift as one progresses from an entry-level position to a senior or management role. What one person views as a pro, such as hands-on problem-solving, another might see as a con, like unpredictable work demands. This assessment aims to provide a realistic overview to help set appropriate expectations.
Pros
- Maintenance engineers are consistently in high demand across various industries, including manufacturing, energy, and infrastructure, ensuring strong job security and diverse employment opportunities. This widespread need provides stability, even during economic fluctuations.
- The role offers significant intellectual stimulation through complex problem-solving, requiring analytical thinking to diagnose equipment malfunctions and design effective repair or preventative solutions. Each new breakdown presents a unique technical challenge to overcome.
- Maintenance engineers gain hands-on experience with a wide array of machinery, systems, and technologies, building a versatile skill set applicable across different industrial settings. This practical knowledge is highly valued and transferable.
- The work environment often involves direct interaction with operational teams, production staff, and other engineers, fostering a collaborative atmosphere. This teamwork allows for knowledge sharing and collective problem-solving, which can be very rewarding.
- Maintenance engineering provides clear pathways for career advancement into senior technical roles, maintenance management, or even broader operational leadership positions. Professional certifications and advanced degrees can further accelerate this progression.
- The profession offers a direct impact on operational efficiency, safety, and cost savings within an organization, providing a strong sense of accomplishment. Seeing equipment run smoothly due to your intervention is a tangible reward.
- Salaries for experienced maintenance engineers are generally competitive, reflecting the critical nature of their work and the specialized skills required. This financial compensation supports a comfortable lifestyle and long-term financial planning.
Cons
- Maintenance engineers often work irregular hours, including evenings, weekends, and holidays, due to the 24/7 operational needs of facilities. This unpredictable schedule can make it difficult to maintain a consistent personal life and plan social activities.
- The role requires continuous learning and adaptation to new technologies, equipment, and industry standards, demanding a commitment to ongoing professional development. Falling behind on new skills can impact career progression and job effectiveness.
- Maintenance engineers frequently work in physically demanding and potentially hazardous environments, such as factories, power plants, or construction sites. Exposure to noise, extreme temperatures, heavy machinery, and hazardous materials is common, increasing the risk of accidents or health issues.
- The job involves problem-solving under pressure, especially during critical equipment failures or system breakdowns that impact production or safety. This high-stakes environment can lead to significant stress and burnout, particularly when deadlines are tight.
- Career progression can sometimes be limited to senior engineering roles or management positions within maintenance departments, requiring additional qualifications or significant leadership experience. Lateral moves into other engineering disciplines may also be challenging without retraining.
- Budget constraints and resource limitations are common in maintenance departments, forcing engineers to find creative solutions with fewer resources. This can add frustration and pressure when trying to implement necessary repairs or upgrades.
- Maintenance engineers often deal with repetitive tasks like routine inspections, preventative maintenance schedules, and documenting repairs. While essential, this can lead to monotony and a lack of intellectual stimulation for those who prefer constant novelty.
Frequently Asked Questions
Maintenance Engineers face unique challenges balancing technical expertise with proactive problem-solving to ensure operational efficiency. This section addresses common questions about entering this field, from essential qualifications and daily responsibilities to career progression and work-life considerations specific to this vital role.
What educational qualifications do I need to become a Maintenance Engineer?
Most Maintenance Engineer roles require a bachelor's degree in engineering, typically mechanical, electrical, industrial, or manufacturing engineering. Some entry-level positions or those in specific industries might accept an associate's degree with significant relevant experience or specialized certifications. Practical experience gained through internships or co-op programs is highly valued.
What does a typical day look like for a Maintenance Engineer?
The day-to-day work involves a mix of hands-on technical tasks, planning, and analysis. You will troubleshoot equipment failures, implement preventive maintenance schedules, analyze data to predict potential issues, and optimize machinery performance. Collaboration with production teams, technicians, and management is frequent, ensuring minimal downtime and continuous improvement.
What are the salary expectations for a Maintenance Engineer, especially for someone starting out?
Entry-level Maintenance Engineers can expect salaries that vary based on industry, location, and specific company. With experience, certifications, and specialization in areas like reliability engineering or automation, earning potential significantly increases. Mid-career professionals often see substantial salary growth as they take on more complex projects and leadership responsibilities.
What are the common career paths and opportunities for advancement for a Maintenance Engineer?
Career progression for Maintenance Engineers can lead to senior engineering roles, maintenance management, reliability engineering, or even broader operational leadership positions. Specializing in areas like Six Sigma, Lean Manufacturing, or specific industrial equipment can open doors to highly specialized and well-compensated roles. Continuous learning and professional development are key to advancement.
What is the typical work-life balance like, considering the nature of the role?
Work-life balance can vary depending on the industry and specific company. In some manufacturing environments, you might be on call for critical equipment failures, or work extended hours during major shutdowns or upgrades. However, many roles offer standard business hours, with a focus on proactive planning to minimize emergencies. It is important to clarify on-call expectations during interviews.
Is the job market for Maintenance Engineers stable, and is there a growing demand?
The field has strong job security due to the critical need for operational efficiency across almost all industries that rely on machinery, from manufacturing to energy and logistics. As technology advances, the demand for Maintenance Engineers with skills in automation, data analytics, and predictive maintenance continues to grow. Companies constantly seek to minimize downtime and optimize assets.
Can I transition into a Maintenance Engineer role without a traditional engineering degree?
Transitioning into this role without a traditional engineering degree is challenging but possible with a strong technical background and specific certifications. Vocational training, military experience in relevant technical fields, or an associate's degree combined with certifications like Certified Maintenance and Reliability Professional (CMRP) can provide a pathway. Demonstrating practical skills and problem-solving abilities is crucial.
How much opportunity is there for remote work or location flexibility in this career?
While some planning and data analysis tasks can be done remotely, the core of a Maintenance Engineer's job involves direct interaction with machinery and on-site problem-solving. Therefore, the role is predominantly on-site. Hybrid models might exist for roles with significant administrative or project management components, but a substantial physical presence is typically required to assess and manage equipment.
Related Careers
Explore similar roles that might align with your interests and skills:
Industrial Maintenance Technician
A growing field with similar skill requirements and career progression opportunities.
Explore career guideMaintenance Mechanic
A growing field with similar skill requirements and career progression opportunities.
Explore career guideMaintenance Specialist
A growing field with similar skill requirements and career progression opportunities.
Explore career guideMaintenance Technician
A growing field with similar skill requirements and career progression opportunities.
Explore career guidePlant Maintenance Technician
A growing field with similar skill requirements and career progression opportunities.
Explore career guideAssess your Maintenance Engineer readiness
Understanding where you stand today is the first step toward your career goals. Our Career Coach helps identify skill gaps and create personalized plans.
Skills Gap Analysis
Get a detailed assessment of your current skills versus Maintenance Engineer requirements. Our AI Career Coach identifies specific areas for improvement with personalized recommendations.
See your skills gapCareer Readiness Assessment
Evaluate your overall readiness for Maintenance Engineer roles with our AI Career Coach. Receive personalized recommendations for education, projects, and experience to boost your competitiveness.
Assess your readinessLand your dream job with Himalayas Plus
Upgrade to unlock Himalayas' premium features and turbocharge your job search.
Himalayas
Himalayas Plus
Himalayas Max
Find your dream job
Sign up now and join over 100,000 remote workers who receive personalized job alerts, curated job matches, and more for free!
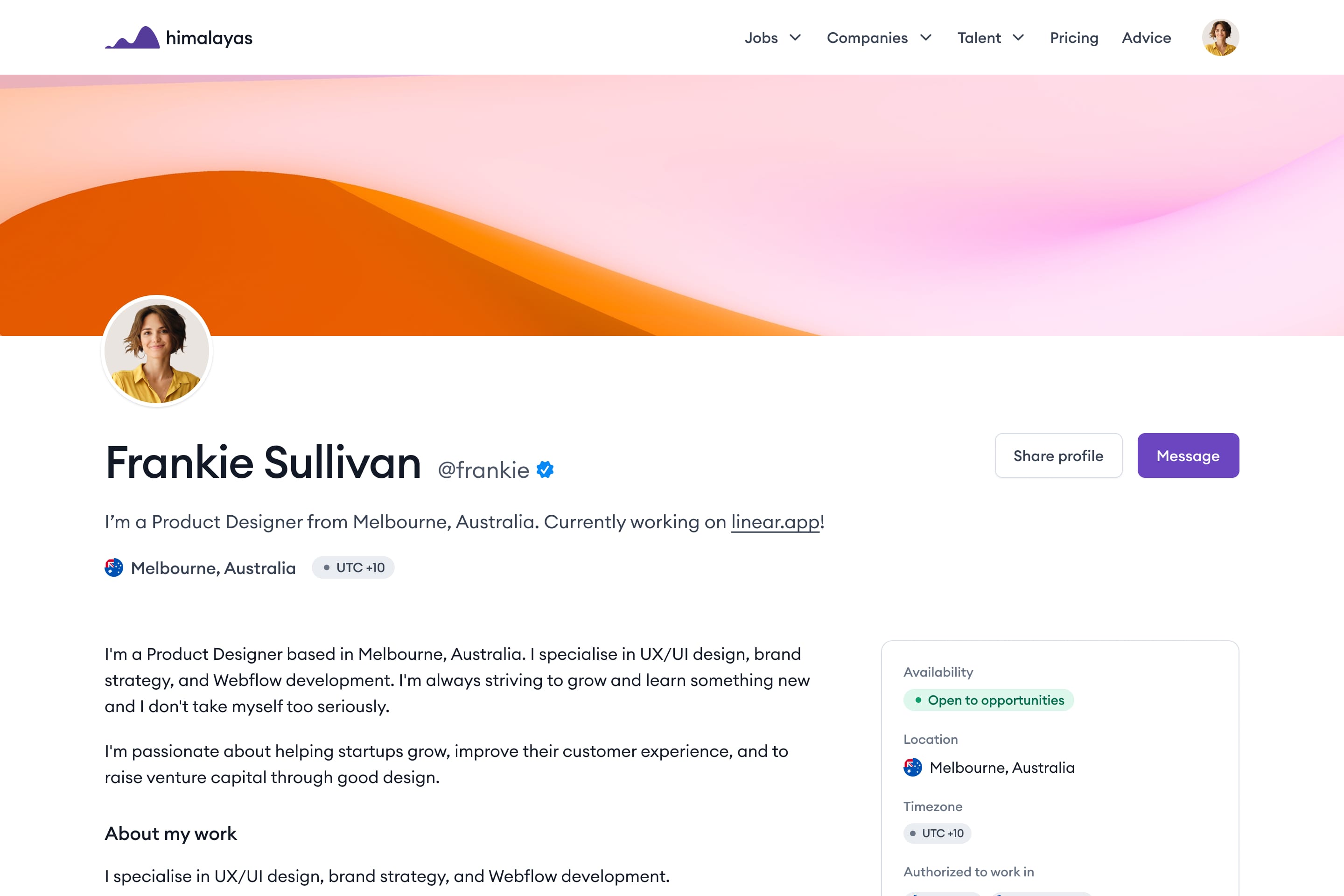