Complete Maintenance Mechanic Career Guide
Maintenance mechanics are the unsung heroes who keep our world running, ensuring everything from factory machinery to building systems operates smoothly and safely. They diagnose complex issues, perform critical repairs, and implement preventative measures, directly impacting productivity and operational efficiency across countless industries. This hands-on career offers stable demand and the satisfaction of solving tangible problems daily.
Key Facts & Statistics
Median Salary
$59,990 USD
(U.S. national median, May 2023, U.S. Bureau of Labor Statistics)
Range: $38k - $80k+ USD
Growth Outlook
1%
as fast as average (U.S. Bureau of Labor Statistics)
Annual Openings
≈110k
openings annually (U.S. Bureau of Labor Statistics)
Top Industries
Typical Education
High school diploma or equivalent, often supplemented by vocational training or an apprenticeship
What is a Maintenance Mechanic?
A Maintenance Mechanic is a skilled professional responsible for the upkeep, repair, and troubleshooting of industrial machinery and mechanical systems within a facility. Their primary objective is to ensure that production equipment operates efficiently and reliably, minimizing downtime and extending the lifespan of assets. This role is crucial for operational continuity and overall productivity.
Unlike a general handyman who handles a broader range of facility issues, or an electrician who focuses solely on electrical systems, a Maintenance Mechanic specializes in the mechanical aspects of complex equipment. They possess a deep understanding of hydraulics, pneumatics, power transmission, and precision alignment, applying this knowledge to diagnose failures and implement effective, lasting repairs.
What does a Maintenance Mechanic do?
Key Responsibilities
- Inspect and diagnose mechanical issues on industrial equipment and machinery by observing operation, listening for unusual sounds, and using testing instruments.
- Perform preventive maintenance tasks, including lubrication, filter changes, belt adjustments, and cleaning, following established schedules and procedures.
- Repair or replace defective parts, components, or systems using hand tools, power tools, and specialized equipment to restore machinery to optimal working order.
- Read and interpret blueprints, schematics, and technical manuals to understand equipment design and facilitate accurate troubleshooting and repairs.
- Fabricate or modify parts using welding, machining, or other shop tools when off-the-shelf replacements are unavailable or impractical.
- Maintain accurate records of maintenance activities, including repairs performed, parts used, and time spent, to track equipment history and inform future planning.
- Collaborate with production operators and engineers to identify recurring problems and implement solutions that improve equipment reliability and operational efficiency.
Work Environment
Maintenance mechanics typically work in industrial settings such as manufacturing plants, factories, warehouses, or commercial facilities. The environment can be noisy, dusty, and may involve working in confined spaces, at heights, or around moving machinery. The pace is often dynamic, with urgent repair needs arising unexpectedly, requiring quick problem-solving.
Collaboration with production teams, engineers, and other maintenance personnel is frequent. While some roles offer a standard day shift, many maintenance positions require rotating shifts, on-call availability, or weekend work to ensure continuous operation. Work-life balance can vary depending on the industry and the criticality of the machinery.
Tools & Technologies
Maintenance mechanics regularly use a wide array of hand tools such as wrenches, screwdrivers, and pliers, alongside power tools like drills, grinders, and impact drivers. They operate specialized diagnostic equipment including multimeters, vibration analyzers, and thermal imaging cameras to pinpoint issues. For repairs and fabrication, they often work with welding equipment (MIG, TIG, stick), lathes, milling machines, and various cutting tools.
Beyond physical tools, they utilize computerized maintenance management systems (CMMS) like SAP PM, Maximo, or Fiix for scheduling, work order management, and inventory tracking. They also interpret technical drawings, hydraulic schematics, and electrical diagrams, often relying on digital versions or CAD software for detailed views.
Maintenance Mechanic Skills & Qualifications
The Maintenance Mechanic role requires a blend of practical experience, technical knowledge, and problem-solving abilities. Qualifications for this position are highly practical, often prioritizing hands-on experience and certifications over traditional academic degrees, especially for entry to mid-level roles. Companies value demonstrable competence in diagnosing and repairing equipment.
Requirements vary significantly by industry and company size. Manufacturing plants, for instance, demand expertise in specific production machinery, while commercial buildings require proficiency with HVAC, plumbing, and electrical systems. Larger organizations may seek candidates with specialized certifications in areas like hydraulics or pneumatics, whereas smaller businesses often prefer generalists capable of handling a broader range of tasks. Geographic location can also influence requirements, with some regions having stronger union presences that impact training and certification pathways.
Formal education, such as an associate's degree in industrial maintenance or a vocational certificate, provides a strong foundation. However, many successful maintenance mechanics enter the field through apprenticeships, on-the-job training, or military experience, which are highly valued for their practical exposure. Certifications from organizations like the Society for Maintenance & Reliability Professionals (SMRP) or specific equipment manufacturers can significantly enhance a candidate's profile, signaling specialized expertise and commitment to the profession. The field is evolving with increasing integration of automation and predictive maintenance technologies, making skills in PLCs, sensor technology, and data interpretation increasingly critical alongside traditional mechanical and electrical proficiencies.
Education Requirements
Technical Skills
- Mechanical Systems Repair (pumps, motors, gearboxes, conveyors)
- Hydraulics and Pneumatics Troubleshooting and Repair
- Electrical Systems Diagnostics (motors, controls, wiring, sensors)
- Blueprint and Schematic Reading (mechanical, electrical, hydraulic)
- Preventive and Predictive Maintenance Techniques
- Welding and Fabrication (MIG, TIG, stick)
- PLC (Programmable Logic Controller) Basic Troubleshooting
- Precision Measurement Tools (micrometers, calipers, gauges)
- Lockout/Tagout (LOTO) Procedures and Safety Protocols
- Bearing Installation and Alignment
- Basic Machining Operations (lathe, mill)
- CMMS (Computerized Maintenance Management System) Software Usage
Soft Skills
- Problem-Solving: Maintenance mechanics must efficiently diagnose complex mechanical, electrical, or hydraulic issues, often under pressure, to minimize downtime.
- Attention to Detail: Precision in identifying faulty components, following schematics, and performing repairs ensures safety and equipment longevity.
- Adaptability: Equipment failures are unpredictable; mechanics must quickly adjust to new problems and prioritize tasks effectively in dynamic environments.
- Safety Consciousness: Adherence to safety protocols (LOTO, confined space entry) is paramount to prevent accidents and ensure compliance.
- Communication: Clear communication with supervisors, operators, and team members about equipment status, repair progress, and preventive maintenance needs is essential.
- Time Management: Efficiently managing repair schedules, prioritizing critical breakdowns, and completing tasks within deadlines are crucial for operational continuity.
- Manual Dexterity: The role requires fine motor skills and hand-eye coordination for working with small parts, tools, and intricate machinery components.
How to Become a Maintenance Mechanic
Entering the Maintenance Mechanic field offers diverse pathways, from traditional apprenticeships to vocational training and self-taught routes. A complete beginner might spend 6-12 months acquiring foundational skills through a trade school or entry-level certification, while someone transitioning from a related field, like automotive repair, could find a role within 3-6 months. The timeline also depends on the specific industry; manufacturing facilities often have structured training programs, whereas smaller companies might prefer hands-on experience over formal credentials.
Geographic location significantly impacts opportunities. Industrial hubs and areas with strong manufacturing or logistics sectors will have more openings and potentially more varied entry-level positions. In contrast, smaller markets might require a broader skill set or a willingness to start in general labor roles before specializing. Many mistakenly believe a four-year degree is essential, but practical skills, problem-solving ability, and a strong work ethic often outweigh academic credentials in this trade.
Building a network within local industrial sectors and engaging with experienced mechanics through informational interviews can open doors to unadvertised opportunities. Mentorship is crucial for accelerating skill development and understanding industry nuances. The hiring landscape values hands-on proficiency and a demonstrated ability to learn and adapt to new machinery and systems. Overcoming barriers often involves proving mechanical aptitude and reliability, even if formal experience is limited.
Step 1
Step 2
Step 3
Step 4
Step 5
Step 6
Step 7
Education & Training Needed to Become a Maintenance Mechanic
The Maintenance Mechanic field offers diverse educational pathways, ranging from formal vocational programs to on-the-job training. Formal degrees, such as Associate of Applied Science in Industrial Maintenance or Mechatronics, typically take two years and can cost between $8,000 and $25,000 at community colleges. These programs provide a strong theoretical foundation in electrical, mechanical, and hydraulic systems, often including practical lab work.
Alternative paths include vocational school certificates, which usually last 6-12 months and cost $3,000-$15,000. Apprenticeships, combining paid on-the-job training with classroom instruction, are highly valued by employers. These can last 3-5 years, often with minimal direct cost to the apprentice beyond tools. Employer acceptance of credentials varies; while some roles prefer a degree, many prioritize hands-on experience and certifications. Continuous learning is crucial, as technology in industrial equipment evolves rapidly.
Specialization in areas like HVAC, robotics, or specific machinery types significantly influences educational needs. Entry-level roles might favor apprenticeships, while senior positions or specialized maintenance often benefit from advanced certifications or a degree. Practical experience often outweighs theoretical knowledge for many employers, but a strong educational base accelerates skill acquisition. Industry-specific certifications, like those from the National Center for Construction Education and Research (NCCER) or the Manufacturing Skill Standards Council (MSSC), are highly regarded for validating specific competencies.
Maintenance Mechanic Salary & Outlook
Compensation for a Maintenance Mechanic varies significantly based on several factors beyond just base salary. Geographic location plays a crucial role, with higher wages typically found in metropolitan areas and regions with a high concentration of manufacturing or industrial facilities, reflecting both a higher cost of living and increased demand for skilled trades. Conversely, rural areas may offer lower salaries.
Experience, specialized skills, and certifications directly influence earning potential. Mechanics with expertise in specific machinery, advanced diagnostic tools, or specialized trades like HVAC, electrical, or hydraulics often command premium compensation. Total compensation packages frequently include overtime pay, which can substantially boost earnings, along with health insurance, retirement plans like 401(k)s, and tool allowances. Some companies also offer performance bonuses or profit-sharing.
Industry-specific trends also affect pay. For instance, mechanics in highly automated or continuous-operation industries, such as pharmaceuticals or advanced manufacturing, often earn more due to the critical nature of their work and the complexity of equipment. Negotiating leverage comes from demonstrating a proven track record of reducing downtime, improving efficiency, and possessing diverse, in-demand technical skills. While remote work is uncommon for this hands-on role, travel to various sites might be required, sometimes with additional compensation. International markets also show variations, with the provided figures specific to the United States Dollar (USD) context.
Salary by Experience Level
Level | US Median | US Average |
---|---|---|
Junior Maintenance Mechanic | $42k USD | $45k USD |
Maintenance Mechanic | $55k USD | $58k USD |
Senior Maintenance Mechanic | $68k USD | $72k USD |
Lead Maintenance Mechanic | $80k USD | $85k USD |
Maintenance Supervisor | $90k USD | $95k USD |
Maintenance Manager | $110k USD | $115k USD |
Market Commentary
The job market for Maintenance Mechanics shows consistent demand, driven by the ongoing need to maintain and repair machinery across various industries. The Bureau of Labor Statistics projects stable growth for industrial machinery mechanics, including maintenance mechanics, at around 8% from 2022 to 2032, which is about as fast as the average for all occupations. This growth is fueled by increasing automation in manufacturing, logistics, and power generation, which requires skilled technicians to keep complex systems operational.
Emerging opportunities exist in facilities adopting smart factory technologies, predictive maintenance systems, and robotics. Mechanics who can interpret data from sensors, troubleshoot network-connected equipment, and work with programmable logic controllers (PLCs) are increasingly valuable. There is a persistent supply-demand imbalance, with a shortage of qualified, skilled trades professionals, particularly those proficient in modern industrial technologies. This shortage often translates to competitive wages and job security for experienced mechanics.
Future-proofing this career involves continuous learning in areas like industrial automation, mechatronics, and data analytics for maintenance. While some routine tasks might be automated, the core role of diagnosing complex issues and performing hands-on repairs remains highly resistant to full automation. Geographic hotspots for this role include major industrial hubs and regions with significant manufacturing, warehousing, or energy infrastructure. The profession is generally recession-resistant as maintenance is critical regardless of economic cycles, ensuring operational continuity for businesses.
Maintenance Mechanic Career Path
Career progression for a Maintenance Mechanic typically involves a clear ladder of increasing technical expertise, autonomy, and leadership responsibilities. Individuals often start with foundational tasks, gradually taking on more complex systems and supervisory duties. Advancement hinges on demonstrated mechanical aptitude, problem-solving skills, and a commitment to continuous learning.
Progression can follow an individual contributor (IC) track, where mechanics become highly specialized experts in specific equipment or systems, or a management track, leading teams and overseeing operations. Factors influencing advancement speed include performance, acquisition of specialized certifications (e.g., HVAC, welding, electrical), and the complexity of the machinery involved. Larger organizations or those with highly automated processes often offer more structured advancement paths and specialized roles.
Lateral movement opportunities exist into related roles like industrial electrician, HVAC technician, or even into facilities management. Networking with peers and mentors, along with active participation in industry associations, enhances career prospects. Continuous skill development, particularly in automation, predictive maintenance technologies, and safety protocols, remains crucial for sustained growth and opens doors to alternative pathways in engineering support or technical training.
Junior Maintenance Mechanic
0-2 yearsKey Focus Areas
Maintenance Mechanic
2-5 yearsKey Focus Areas
Senior Maintenance Mechanic
5-8 yearsKey Focus Areas
Lead Maintenance Mechanic
8-12 yearsKey Focus Areas
Maintenance Supervisor
10-15 yearsKey Focus Areas
Maintenance Manager
15+ yearsKey Focus Areas
Junior Maintenance Mechanic
0-2 yearsPerforms routine preventative maintenance tasks and assists senior mechanics with repairs. Works under direct supervision, following detailed instructions for equipment checks, lubrication, and basic component replacements. Learns to identify potential issues and reports findings accurately. Impact is primarily on individual task completion and adherence to safety protocols.
Key Focus Areas
Develop foundational mechanical and electrical troubleshooting skills. Learn to safely operate and maintain basic hand and power tools. Focus on understanding equipment manuals and standard operating procedures. Build strong communication skills for reporting issues and collaborating with senior mechanics.
Maintenance Mechanic
2-5 yearsConducts independent troubleshooting, repair, and preventative maintenance on various industrial equipment and systems. Exercises independent judgment in diagnosing failures and executing corrective actions. Collaborates with production teams to minimize downtime. Decisions directly impact equipment uptime and operational efficiency.
Key Focus Areas
Master diagnostics and repair for a wider range of mechanical, electrical, and hydraulic systems. Acquire proficiency in reading blueprints and schematics. Develop independent problem-solving abilities and time management. Pursue certifications in specific areas like welding, basic PLC programming, or specialized machinery maintenance.
Senior Maintenance Mechanic
5-8 yearsServes as a subject matter expert for complex equipment and system repairs, often handling the most challenging breakdowns. Provides technical guidance and training to less experienced mechanics. Proactively identifies and implements improvements to maintenance procedures. Decisions have a significant impact on long-term equipment performance and team efficiency.
Key Focus Areas
Specialize in complex systems such as robotics, advanced automation, or intricate fluid power. Develop advanced diagnostic techniques and root cause analysis skills. Begin mentoring junior staff and contribute to training materials. Focus on optimizing maintenance processes and improving equipment reliability.
Lead Maintenance Mechanic
8-12 yearsActs as a working supervisor, coordinating daily maintenance activities for a small team of mechanics. Assigns tasks, monitors progress, and ensures compliance with safety and quality standards. Provides on-the-job training and technical support. Makes immediate operational decisions to resolve maintenance issues and optimize team output.
Key Focus Areas
Cultivate strong leadership and communication skills, including delegating tasks and providing constructive feedback. Develop project management capabilities for overseeing maintenance projects. Focus on scheduling, resource allocation, and optimizing workflow for a small team. Understand key performance indicators (KPIs) for maintenance.
Maintenance Supervisor
10-15 yearsManages a team of maintenance mechanics, overseeing daily operations, scheduling, and performance reviews. Responsible for departmental safety compliance and training programs. Develops and implements preventative maintenance schedules. Decisions impact team productivity, budget adherence, and overall facility reliability.
Key Focus Areas
Strengthen leadership, team management, and conflict resolution skills. Develop expertise in preventative and predictive maintenance strategies. Learn budgeting, inventory management, and vendor relations. Focus on strategic planning for maintenance operations and continuous improvement initiatives.
Maintenance Manager
15+ yearsDirects all maintenance operations for a facility or a specific division, including budget management, strategic planning, and capital project oversight. Leads continuous improvement initiatives and implements advanced maintenance technologies. Manages relationships with key vendors and contractors. Decisions significantly influence operational costs, asset longevity, and overall organizational profitability.
Key Focus Areas
Master strategic planning, financial management, and human resources aspects of maintenance. Develop strong analytical skills for performance metrics and long-term asset management. Cultivate cross-functional collaboration and stakeholder management. Focus on integrating maintenance goals with broader organizational objectives.
Job Application Toolkit
Ace your application with our purpose-built resources:
Maintenance Mechanic Resume Examples
Proven layouts and keywords hiring managers scan for.
View examplesMaintenance Mechanic Cover Letter Examples
Personalizable templates that showcase your impact.
View examplesTop Maintenance Mechanic Interview Questions
Practice with the questions asked most often.
View examplesMaintenance Mechanic Job Description Template
Ready-to-use JD for recruiters and hiring teams.
View examplesGlobal Maintenance Mechanic Opportunities
A Maintenance Mechanic's skills are universally valuable, adapting across diverse industrial sectors worldwide. Global demand for skilled mechanics remains consistent, driven by the need to maintain essential machinery and infrastructure. This role faces cultural differences in safety standards and regulatory compliance, which vary significantly by country. Professionals seek international opportunities for higher wages, specialized projects, or exposure to advanced technologies. International certifications, like specific trade licenses or ISO standards, can enhance global mobility for mechanics.
Global Salaries
Global salaries for Maintenance Mechanics vary greatly by region, reflecting economic conditions and industry demand. In North America, particularly the United States, annual salaries range from $50,000 to $75,000 USD, with higher figures in metropolitan areas or specialized industries. Canadian mechanics typically earn C$55,000 to C$80,000 annually. European salaries show significant diversity; a mechanic in Germany might earn €40,000 to €60,000 per year, while in the UK, the range is £30,000 to £45,000. These figures reflect a higher purchasing power in Western Europe compared to some other regions.
Asia-Pacific offers varied compensation. Australian mechanics earn A$60,000 to A$85,000 annually, while in Southeast Asia, salaries can be lower, perhaps $15,000 to $30,000 USD equivalent in countries like Thailand or Vietnam, but with a much lower cost of living. In the Middle East, particularly the UAE, salaries for expatriate mechanics can range from $35,000 to $60,000 USD, often tax-free, alongside benefits like housing allowances, significantly impacting take-home pay. Latin American countries, like Brazil, offer R$40,000 to R$70,000 (approximately $8,000 to $14,000 USD) annually, where the cost of living is considerably lower.
Salary structures also differ. In some countries, comprehensive benefits packages, including health insurance, pension contributions, and generous vacation time, supplement the base salary. Other regions might offer higher base pay with fewer additional benefits. Tax implications vary widely; for instance, high-income tax rates in some European countries contrast with lower rates or no income tax in parts of the Middle East. Experience and specific technical certifications directly influence compensation across all regions, as employers value proven expertise and specialized skills.
Remote Work
For a Maintenance Mechanic, direct international remote work opportunities are extremely limited. The role inherently requires on-site presence to inspect, diagnose, and repair machinery. However, some ancillary functions, like remote diagnostics, technical support, or even training development, might be performed remotely. These are generally supplementary to the core hands-on responsibilities.
Digital nomad opportunities for this specific trade are not applicable, as the job cannot be performed from a laptop in a different country. Employers rarely hire Maintenance Mechanics for fully remote international positions. Any remote tasks would typically be part of a hybrid local role. Therefore, salary expectations for a Maintenance Mechanic are almost entirely tied to the geographic location of the physical work site. This role does not lend itself to geographic arbitrage through remote work.
Visa & Immigration
Maintenance Mechanics seeking international work often use skilled worker visas. Countries like Canada (Express Entry), Australia (Skilled Nominated Visa), and Germany (Skilled Immigration Act) have specific pathways for tradespeople. Requirements typically include recognized trade qualifications, several years of experience, and a job offer from an employer in the destination country. Education credential recognition is crucial; applicants often need their qualifications assessed by relevant bodies in the target country to ensure they meet local standards. Some countries also require specific professional licensing or certifications.
Visa application timelines vary, from a few months to over a year, depending on the country and visa type. English or local language proficiency tests, like IELTS for English-speaking countries or Goethe-Zertifikat for Germany, are frequently mandatory. For instance, Canada's Express Entry system awards points for language ability. Spouses and dependents can usually be included in visa applications, allowing families to relocate together. Some countries, particularly those with aging workforces or specific industry needs, may offer fast-track processing for highly skilled trades like Maintenance Mechanics. Permanent residency pathways often become available after several years of continuous skilled employment in the host country, demonstrating integration and contribution to the economy.
2025 Market Reality for Maintenance Mechanics
Understanding current market realities is crucial for any maintenance mechanic aiming for career success. The field has undergone significant shifts in recent years, particularly between 2023 and 2025. Post-pandemic supply chain disruptions highlighted the importance of resilient industrial operations, increasing the need for robust maintenance. The ongoing AI revolution impacts machinery diagnostics and predictive maintenance, changing core job responsibilities.
Broader economic factors, such as inflation and industrial investment levels, directly influence job availability and compensation in this profession. Market realities for maintenance mechanics vary considerably based on experience level, with senior technicians in high demand. Geographic regions also play a role; manufacturing hubs offer different opportunities than logistics centers. Company size matters too, as large corporations often have more specialized roles than smaller businesses. This analysis provides an honest assessment of these realities.
Current Challenges
Maintenance mechanics face increased competition for specialized roles, especially those requiring advanced automation or robotics skills. Many entry-level positions are saturated, making it harder for new technicians to gain initial experience. Economic uncertainty can lead companies to delay equipment upgrades, reducing demand for new installations and associated maintenance. The rapid evolution of industrial technology creates a persistent skill gap for mechanics not continuously updating their expertise. Job searches can extend several months for highly desirable positions in competitive regions.
Growth Opportunities
Despite challenges, strong demand exists for maintenance mechanics specializing in automation, robotics, and advanced electrical systems. Emerging opportunities include roles focused on predictive maintenance analytics, where mechanics interpret sensor data to prevent failures, and technicians for additive manufacturing equipment. Professionals can gain an advantage by pursuing certifications in industrial controls, mechatronics, or specific OEM equipment. Underserved markets often include specialized food processing plants, advanced material manufacturing, and large-scale data centers, which require highly skilled, continuously available maintenance staff.
Proficiency in programmable logic controllers (PLCs), human-machine interfaces (HMIs), and industrial networking provides a significant competitive edge in the current market. Experience with AI-powered diagnostic tools or augmented reality (AR) for troubleshooting also sets candidates apart. Market corrections might create opportunities for mechanics to transition into more stable, essential industries like pharmaceuticals or utilities, which tend to be less volatile. Investing in training for new technologies now positions mechanics for long-term career growth and increased earning potential.
Current Market Trends
Demand for skilled maintenance mechanics remains steady, though evolving. Hiring patterns show a strong preference for mechanics with cross-functional skills, particularly in industrial automation and robotics. Companies increasingly seek technicians who can troubleshoot complex PLC systems alongside traditional mechanical and electrical faults. The integration of predictive maintenance technologies, powered by AI and IoT sensors, is reshaping the role, shifting focus from reactive repairs to proactive system management. Economic conditions, while stable, encourage efficiency, driving demand for mechanics who can minimize downtime and optimize asset performance.
Employer requirements now emphasize digital literacy and data interpretation alongside hands-on mechanical aptitude. Many roles demand familiarity with CMMS (Computerized Maintenance Management Systems) for work order tracking and historical analysis. Salary trends indicate a premium for mechanics proficient in advanced diagnostics, cybersecurity for OT (Operational Technology) systems, and specialized equipment like vision systems or collaborative robots. Market saturation appears in generalist roles, while specialists in niche manufacturing or advanced logistics find strong demand. Geographic variations are significant; industrial hubs and growing distribution centers show robust demand, while older manufacturing regions may see slower growth. Remote work is rare for this hands-on role, but some companies offer hybrid roles for supervisory or planning functions. Seasonal hiring for plant shutdowns or upgrade cycles remains a consistent pattern.
Emerging Specializations
The role of a Maintenance Mechanic is evolving rapidly, driven by advancements in automation, data analytics, and sustainable industrial practices. Traditional mechanical skills remain foundational, but new specialization opportunities are emerging that demand a blend of technical expertise and digital literacy. Understanding these shifts helps professionals strategically position themselves for future career growth and enhanced earning potential.
Early positioning in these emerging areas is crucial for career advancement, particularly looking towards 2025 and beyond. Professionals who proactively acquire skills in next-generation maintenance technologies often command premium compensation and experience faster career progression. These specialized roles address complex challenges that traditional mechanics may not be equipped to handle.
While established specializations offer stability, pursuing emerging areas can unlock significant opportunities. Many cutting-edge fields are still developing, creating a high demand for skilled individuals with fewer competitors. These areas typically transition from niche to mainstream within five to ten years, creating a surge in job opportunities once widespread adoption occurs.
Embracing these cutting-edge specializations involves a balance of risk and reward. The risk lies in investing time and resources into fields that are still maturing, but the reward is significant. Being an early adopter establishes expertise and leadership in areas that will define the future of industrial maintenance, leading to substantial long-term career benefits.
Predictive Maintenance Technician
Predictive Maintenance Technicians use IoT sensors and data analytics platforms to monitor equipment health in real-time. This specialization shifts maintenance from reactive or time-based to condition-based, allowing for interventions before failures occur. It significantly reduces downtime and extends asset lifespan, making it critical for operational efficiency in modern industries.
Robotics and Automation Maintenance Specialist
Robotics and Automation Maintenance Specialists focus on the upkeep, troubleshooting, and repair of industrial robots, automated guided vehicles (AGVs), and complex automated systems. As factories become increasingly automated, these mechanics ensure the continuous operation of highly integrated production lines. This role requires understanding both mechanical and control system aspects of robotics.
Industrial Cybersecurity Mechanic
Industrial Cybersecurity Mechanics specialize in protecting operational technology (OT) systems within industrial environments from cyber threats. This involves securing networked machinery, PLCs, and SCADA systems from unauthorized access or malicious attacks. They ensure the integrity and availability of critical infrastructure, preventing costly disruptions and maintaining safety.
Renewable Energy Equipment Mechanic
Renewable Energy Equipment Mechanics focus on the maintenance and repair of systems like wind turbines, solar arrays, and energy storage units. With the global shift towards sustainable energy, demand for skilled mechanics who can keep these complex installations operating efficiently is surging. This specialization requires understanding unique mechanical and electrical challenges of green technologies.
Augmented Reality (AR) Assisted Maintenance Technician
Augmented Reality (AR) Assisted Maintenance Technicians utilize AR headsets and software to overlay digital information onto physical equipment, guiding complex repairs and diagnostics. This specialization enhances efficiency by providing real-time schematics, step-by-step instructions, and remote expert assistance. It significantly reduces human error and speeds up troubleshooting in the field.
Pros & Cons of Being a Maintenance Mechanic
Making informed career decisions requires understanding both the benefits and challenges of a profession. The experience of a Maintenance Mechanic can vary significantly based on the industry, company culture, and specific equipment managed. Pros and cons may also shift across different career stages, with early career professionals focusing on skill acquisition and senior mechanics on problem-solving or mentorship. What one person considers a benefit, such as hands-on problem-solving, another might see as a challenge, such as dealing with unexpected breakdowns. This assessment provides an honest, balanced view to help set realistic expectations for anyone considering a career as a Maintenance Mechanic.
Pros
- Maintenance mechanics are consistently in high demand across nearly all industries, including manufacturing, facilities management, and transportation, ensuring strong job security.
- The role offers significant hands-on problem-solving opportunities, providing intellectual satisfaction from diagnosing and fixing complex mechanical and electrical issues.
- Maintenance mechanics develop a diverse skill set, including electrical, hydraulic, pneumatic, and mechanical expertise, making their skills highly transferable across various sectors.
- The work is rarely monotonous, as each day brings new challenges, different types of equipment breakdowns, and varied maintenance tasks to address.
- Many entry-level positions can be secured with vocational training or apprenticeships, offering a practical path to a well-paying career without requiring a four-year university degree.
- Directly seeing the impact of your work, such as restoring a broken production line or ensuring a building's systems run smoothly, provides a strong sense of accomplishment and purpose.
- Opportunities for specialization exist, allowing mechanics to become experts in specific types of machinery or systems, which can lead to higher earning potential and more focused roles.
Cons
- The work environment can be physically demanding, requiring heavy lifting, bending, climbing, and working in confined or awkward spaces, which can lead to fatigue and potential injuries over time.
- Maintenance mechanics often work irregular hours, including nights, weekends, and holidays, and are frequently on call for emergency repairs, which can disrupt personal life and social plans.
- Exposure to hazardous materials, loud machinery, and dangerous equipment is common, necessitating strict adherence to safety protocols and the constant use of personal protective equipment.
- Diagnosing complex mechanical, electrical, and hydraulic issues can be mentally challenging, requiring strong problem-solving skills under pressure to minimize downtime.
- The job requires continuous learning to keep up with new technologies, equipment, and safety regulations, meaning ongoing training and skill updates are essential.
- The repetitive nature of some tasks, such as routine inspections or preventative maintenance, can sometimes lead to monotony or a feeling of stagnation for individuals seeking constant novelty.
- Career progression beyond a senior mechanic role often requires additional certifications, specialized training, or a shift into supervisory or management positions, which may not appeal to everyone.
Frequently Asked Questions
Maintenance Mechanics face unique challenges balancing technical expertise with practical problem-solving in industrial settings. This section addresses the most common questions about entering this trade, from acquiring essential skills to understanding the demanding work environment and career growth potential.
What are the basic educational or certification requirements to become a Maintenance Mechanic?
You typically need a high school diploma or GED. Many successful Maintenance Mechanics complete vocational training programs, an associate's degree in industrial maintenance, or an apprenticeship. These programs provide hands-on experience with electrical systems, hydraulics, pneumatics, and precision tools, which are crucial for the job.
How long does it take to become job-ready as a Maintenance Mechanic, starting from scratch?
It usually takes 1-2 years for vocational training or an associate's degree, followed by on-the-job experience. Apprenticeships often last 3-4 years, combining classroom instruction with extensive practical work. You can become job-ready for entry-level positions within a year if you commit to a focused training program.
What are the typical salary expectations for an entry-level Maintenance Mechanic, and how does it grow with experience?
Starting salaries for Maintenance Mechanics can range from $40,000 to $55,000 annually, depending on location, industry, and specific skills. Experienced mechanics with specialized certifications in areas like PLC programming or welding can earn significantly more, often exceeding $70,000 per year. Overtime opportunities also significantly boost earning potential.
What is the typical work-life balance like for a Maintenance Mechanic, considering potential on-call duties?
Work-life balance varies but often involves irregular hours, including evenings, weekends, and on-call shifts, especially in industries that operate 24/7. This role requires adaptability to emergency repairs, which can disrupt personal plans. However, many positions offer stable schedules once you gain experience, and some companies provide generous time off.
Is the Maintenance Mechanic role a secure career path, or is it at risk from automation?
Job security for Maintenance Mechanics is generally strong. Industries rely on operational machinery, creating a constant demand for skilled professionals to prevent breakdowns and perform routine maintenance. As automation increases, the need for mechanics who can troubleshoot complex systems and robots also grows, ensuring steady employment.
What are the common career advancement opportunities for Maintenance Mechanics?
Career growth paths include specializing in areas like robotics, HVAC, or electrical systems. You can advance to lead mechanic, maintenance supervisor, or even maintenance manager roles. Some mechanics transition into roles like field service technician, where they work on equipment for multiple clients, or into training and instruction.
What is the typical day-to-day work environment like, and what are the physical demands of the job?
The work environment is often hands-on and physically demanding, requiring lifting, bending, and working in various conditions, including loud, hot, or dirty spaces. It's a problem-solving role that requires quick thinking and mechanical aptitude. Safety is a top priority, and you must adhere strictly to protocols to prevent injuries.
Can Maintenance Mechanics work remotely, or is it strictly an on-site position?
Remote work is not typical for Maintenance Mechanics because the job requires direct interaction with physical machinery and equipment on-site. However, some senior roles or specialized positions might involve remote monitoring of systems or virtual technical support, but the core function remains hands-on and location-dependent.
Related Careers
Explore similar roles that might align with your interests and skills:
Industrial Maintenance Mechanic
A growing field with similar skill requirements and career progression opportunities.
Explore career guideIndustrial Mechanic
A growing field with similar skill requirements and career progression opportunities.
Explore career guideMaintenance Engineer
A growing field with similar skill requirements and career progression opportunities.
Explore career guideMaintenance Specialist
A growing field with similar skill requirements and career progression opportunities.
Explore career guideMaintenance Technician
A growing field with similar skill requirements and career progression opportunities.
Explore career guideAssess your Maintenance Mechanic readiness
Understanding where you stand today is the first step toward your career goals. Our Career Coach helps identify skill gaps and create personalized plans.
Skills Gap Analysis
Get a detailed assessment of your current skills versus Maintenance Mechanic requirements. Our AI Career Coach identifies specific areas for improvement with personalized recommendations.
See your skills gapCareer Readiness Assessment
Evaluate your overall readiness for Maintenance Mechanic roles with our AI Career Coach. Receive personalized recommendations for education, projects, and experience to boost your competitiveness.
Assess your readinessSimple pricing, powerful features
Upgrade to Himalayas Plus and turbocharge your job search.
Himalayas
Himalayas Plus
Himalayas Max
Find your dream job
Sign up now and join over 100,000 remote workers who receive personalized job alerts, curated job matches, and more for free!
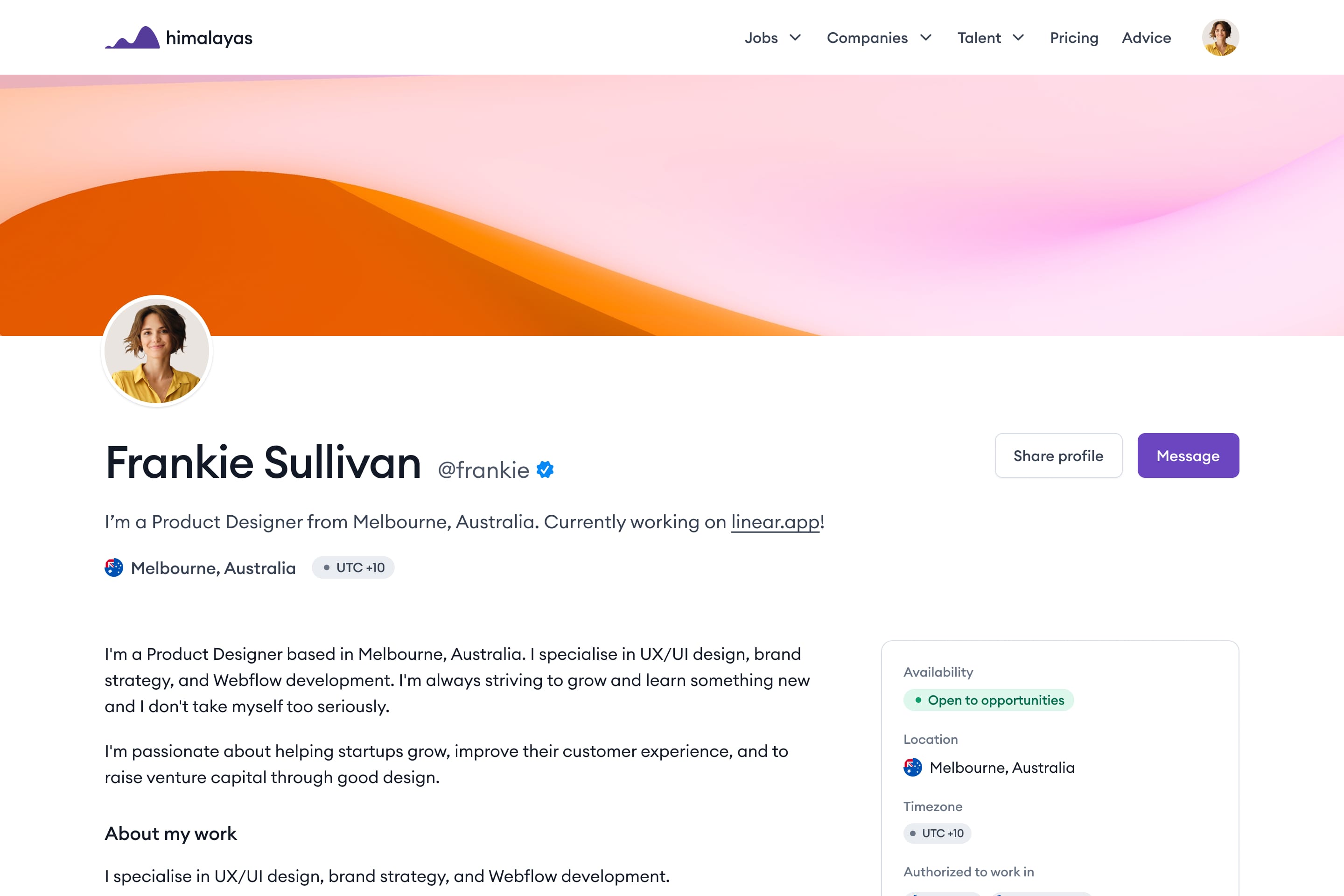