Complete Plant Maintenance Technician Career Guide
Plant Maintenance Technicians are the unsung heroes keeping critical industrial operations running smoothly, ensuring machinery and systems function at peak efficiency. They blend mechanical, electrical, and diagnostic skills to prevent costly downtime and extend equipment life, a vital role in manufacturing and production environments. This hands-on career offers stable opportunities for those who enjoy problem-solving and working with complex machinery.
Key Facts & Statistics
Median Salary
$60,300 USD
(U.S. Bureau of Labor Statistics, May 2023)
Range: $40k - $80k+ USD, depending on experience, industry, and location.
Growth Outlook
10%
faster than average (U.S. Bureau of Labor Statistics, 2022-2032)
Annual Openings
≈33,600
openings annually (U.S. Bureau of Labor Statistics, 2022-2032)
Top Industries
Typical Education
High school diploma or equivalent, with many pursuing postsecondary vocational training, an associate's degree, or apprenticeships in industrial maintenance or a related field.
What is a Plant Maintenance Technician?
A Plant Maintenance Technician is a skilled professional responsible for ensuring the operational reliability and efficiency of machinery and systems within an industrial facility. They perform a critical role in preventing equipment failures, diagnosing complex issues, and executing timely repairs to minimize downtime and maintain continuous production. This role combines mechanical, electrical, and sometimes hydraulic expertise to keep an entire plant running smoothly.
Unlike a general mechanic who might work on vehicles, or a facilities technician focused on building infrastructure, a Plant Maintenance Technician specializes in the intricate, often heavy, industrial equipment used in manufacturing, processing, or utilities. Their work directly impacts production output, product quality, and overall operational safety, making them indispensable to any industrial enterprise.
What does a Plant Maintenance Technician do?
Key Responsibilities
- Perform routine preventative maintenance on industrial machinery and equipment following established schedules and checklists.
- Diagnose mechanical, electrical, and hydraulic issues in production equipment using schematics, multimeters, and diagnostic software.
- Repair or replace defective parts, components, and wiring, including motors, pumps, valves, and control systems.
- Conduct precise alignments of rotating machinery, ensuring optimal performance and reducing wear.
- Document all maintenance activities, repairs, and part replacements accurately in a computerized maintenance management system (CMMS).
- Collaborate with production teams to troubleshoot equipment problems and minimize downtime during operational hours.
- Adhere strictly to safety protocols, including Lockout/Tagout procedures, when working on or near machinery to prevent accidents.
Work Environment
Plant Maintenance Technicians primarily work indoors within manufacturing facilities, production plants, or industrial settings. The environment can be noisy, dusty, and may involve exposure to various temperatures, lubricants, and chemicals. This role often requires working at heights, in confined spaces, or around moving machinery.
Collaboration is essential, as technicians frequently interact with production operators, engineers, and other maintenance staff. The pace is often fast, particularly when responding to critical equipment breakdowns, which may require working irregular hours, including nights, weekends, or on-call shifts. While some planned maintenance allows for a steady pace, emergency repairs demand quick, decisive action. This role is highly hands-on and physically demanding.
Tools & Technologies
Plant Maintenance Technicians regularly use a diverse set of tools and technologies. Hand tools like wrenches, screwdrivers, and pliers are fundamental, alongside power tools such as drills, grinders, and saws. Diagnostic equipment includes multimeters for electrical testing, thermal imagers for identifying overheating components, and vibration analysis tools for predictive maintenance.
Specialized equipment often includes welding and cutting torches, hydraulic presses, and lifting devices like forklifts or hoists. Technicians also utilize computerized maintenance management systems (CMMS) such as SAP PM, Maximo, or Fiix for scheduling, tracking work orders, and managing inventory. They work with programmable logic controllers (PLCs) and human-machine interfaces (HMIs) for troubleshooting automated systems.
Plant Maintenance Technician Skills & Qualifications
Qualifications for a Plant Maintenance Technician emphasize a blend of hands-on mechanical, electrical, and hydraulic expertise, with a strong focus on practical problem-solving. Employers prioritize demonstrated ability to diagnose and repair equipment over purely academic credentials. The path into this role often begins with vocational training or an apprenticeship, which provides direct exposure to industrial machinery and systems. Formal degrees are less common unless pursuing management or specialized engineering roles within maintenance.
Requirements for a Plant Maintenance Technician vary significantly by industry sector, company size, and the complexity of the machinery involved. For example, a technician in a food processing plant needs different specialized knowledge than one in a heavy manufacturing facility or a power generation plant. Larger companies may have more formalized training programs and require specific certifications, while smaller operations might value broad adaptability and a strong generalist skillset. Geographic location also influences demand, with industrial hubs typically offering more opportunities and potentially higher skill expectations.
Practical experience and relevant certifications often hold more weight than a traditional four-year degree for this role. Certifications in areas like industrial electricity, hydraulics, pneumatics, or welding significantly enhance a candidate's value. The skill landscape for Plant Maintenance Technicians is evolving with increasing automation and digitalization; therefore, proficiency in PLC programming, basic robotics, and predictive maintenance technologies using sensor data is becoming increasingly important. Balancing traditional repair skills with an understanding of modern industrial controls and data interpretation is crucial for long-term career success in this field.
Education Requirements
Technical Skills
- Industrial Electrical Systems (motor controls, VFDs, schematics, 3-phase power)
- Hydraulic and Pneumatic Systems (troubleshooting, repair, component replacement)
- Mechanical Systems (bearings, power transmission, pumps, valves, alignment)
- PLC Programming and Diagnostics (Allen-Bradley, Siemens, troubleshooting logic)
- Preventive and Predictive Maintenance Techniques (vibration analysis, thermography, oil analysis)
- Welding and Fabrication (MIG, TIG, Stick, basic metalwork)
- HVAC/R Systems (troubleshooting, repair, refrigerant handling - often specific to industry)
- Blueprint and Schematic Reading (electrical, mechanical, P&ID diagrams)
- Precision Measuring Tools (micrometers, calipers, dial indicators)
- Computerized Maintenance Management Systems (CMMS) operation
- Basic Robotics and Automation troubleshooting
- Rigging and Lifting Equipment operation and safety
Soft Skills
- Problem-solving and Analytical Thinking: Technicians must diagnose complex equipment failures, often under pressure, requiring systematic troubleshooting and logical deduction.
- Attention to Detail: Precision is critical in maintenance to ensure proper repairs, prevent errors, and adhere to safety protocols, avoiding costly reworks or further damage.
- Adaptability and Flexibility: Equipment issues are unpredictable; technicians must adjust priorities, learn new systems quickly, and work effectively in changing environments.
- Safety Consciousness: Adhering strictly to safety procedures (LOTO, confined space, hot work) is paramount to prevent accidents and protect themselves and colleagues.
- Communication and Documentation: Clearly explaining issues to supervisors, coordinating with production teams, and accurately documenting repairs and maintenance activities are essential for operational continuity.
- Teamwork and Collaboration: Working effectively with other technicians, engineers, and production staff to resolve complex problems and minimize downtime is crucial.
- Time Management and Organization: Prioritizing repairs, managing spare parts inventory, and completing tasks efficiently to minimize production interruptions are vital for productivity.
How to Become a Plant Maintenance Technician
Entering the Plant Maintenance Technician field offers multiple pathways, catering to various backgrounds and educational preferences. While some roles might favor formal education, many individuals successfully enter through vocational schools, apprenticeships, or even military service with relevant mechanical or electrical experience. The timeline to secure a first role can range from six months for targeted certifications to two to four years for comprehensive associate degrees or full apprenticeships, depending on the chosen route and prior experience.
Traditional entry often involves completing a technical program focusing on industrial maintenance, electrical systems, hydraulics, and pneumatics. However, hands-on apprenticeships, which provide paid on-the-job training alongside classroom instruction, are highly valued and often lead directly to employment upon completion. Some companies also hire mechanically inclined individuals for entry-level helper positions, providing internal training to develop their skills over time. The demand for skilled technicians varies by geographic region, with higher concentrations in industrial hubs, and larger manufacturing plants often have more structured entry programs compared to smaller facilities.
A common misconception is that this role only requires basic mechanical aptitude; in reality, modern plant maintenance demands strong diagnostic skills, an understanding of automation, and unwavering adherence to complex safety protocols. Building a practical portfolio of demonstrated troubleshooting and repair abilities, even from personal projects, greatly enhances a candidate's appeal. Networking with professionals at industry events or through trade associations is also crucial, as many positions are filled through referrals or direct connections, helping to overcome initial barriers to entry by showcasing commitment and capability.
Step 1
Step 2
Step 3
Step 4
Step 5
Step 6
Step 7
Education & Training Needed to Become a Plant Maintenance Technician
Becoming a Plant Maintenance Technician involves a blend of formal education and hands-on experience. Unlike roles requiring extensive theoretical knowledge, this field emphasizes practical skills in machinery repair, electrical systems, and preventive maintenance. While a 4-year bachelor's degree is rarely necessary, a 2-year associate's degree in Industrial Maintenance Technology or a related field provides a strong foundational understanding. These degrees typically cost between $8,000 and $25,000 and take two years to complete, offering a balance of theoretical knowledge and practical application. Vocational schools and technical colleges often provide certificate programs, which are shorter, usually 6-18 months, and cost $3,000-$15,000. These programs focus intensely on specific skills like welding, hydraulics, or electrical troubleshooting.
Employers value direct experience and certifications highly. Many companies prefer candidates with vocational training or an associate's degree, often viewing them as equally, if not more, prepared than those with broader academic degrees. Apprenticeships are another excellent pathway, combining paid on-the-job training with classroom instruction. These can last 3-5 years, providing comprehensive skill development with no upfront tuition costs, often leading directly to employment. Self-study through online courses or manufacturer-specific training can supplement formal education, but rarely replace it for entry-level positions. Continuous learning is crucial in this field; technicians must update their skills as machinery and technologies evolve, often through short courses on PLCs, robotics, or advanced diagnostics.
The cost-benefit analysis for a Plant Maintenance Technician leans heavily towards vocational training, apprenticeships, or associate's degrees. These options offer a high return on investment due to lower costs and direct applicability to job requirements. Industry-recognized certifications, such as those from the Society for Maintenance & Reliability Professionals (SMRP) or specific equipment manufacturers, significantly enhance a technician's marketability and earning potential. Practical experience gained through internships or entry-level positions is paramount, often outweighing purely academic credentials. The educational path should align with the specific industry or machinery a technician plans to work with, as needs vary from manufacturing plants to power generation facilities.
Plant Maintenance Technician Salary & Outlook
Compensation for a Plant Maintenance Technician varies significantly based on several factors. Geographic location plays a crucial role; technicians in regions with higher costs of living or strong industrial bases often command higher salaries. For instance, salaries in metropolitan areas with extensive manufacturing or energy sectors typically exceed those in rural areas.
Experience and specialized skills also dramatically influence earning potential. Technicians with certifications in areas like PLC programming, industrial automation, or specific machinery types can secure premium compensation. Total compensation packages extend beyond base salary, frequently including overtime pay, on-call stipends, performance bonuses, and comprehensive benefits such as health insurance, retirement plans, and paid time off. Some employers also offer allowances for professional development and tool acquisition.
Industry-specific trends affect salary growth. Technicians working in highly automated or continuous operation environments, like chemical plants or power generation facilities, often see higher pay due to the critical nature of their work. Negotiating leverage comes from demonstrating a proven track record of reducing downtime, improving efficiency, and possessing in-demand technical proficiencies. While remote work is uncommon for this hands-on role, technicians may travel between plant sites. International markets present different salary structures, with the provided figures representing typical USD compensation within the United States.
Salary by Experience Level
Level | US Median | US Average |
---|---|---|
Junior Plant Maintenance Technician | $48k USD | $50k USD |
Plant Maintenance Technician | $60k USD | $62k USD |
Senior Plant Maintenance Technician | $72k USD | $75k USD |
Lead Plant Maintenance Technician | $82k USD | $85k USD |
Maintenance Supervisor | $92k USD | $95k USD |
Maintenance Manager | $105k USD | $110k USD |
Market Commentary
The job market for Plant Maintenance Technicians shows steady demand, driven by the ongoing need to maintain complex machinery and infrastructure across various industries. The Bureau of Labor Statistics projects about a 5% growth for industrial machinery mechanics, including plant maintenance technicians, from 2022 to 2032, which is about as fast as the average for all occupations. This growth translates to approximately 21,300 new jobs over the decade.
Emerging opportunities are appearing in facilities adopting advanced automation, robotics, and predictive maintenance technologies. Technicians skilled in data analysis, sensor technology, and digital twin applications are increasingly sought after. The integration of AI and IoT in plant operations is transforming the role, requiring technicians to evolve from reactive repair to proactive system management and optimization.
Supply and demand dynamics vary by region, but generally, there is a consistent demand for skilled technicians, sometimes outpacing the supply of qualified candidates, particularly those with multidisciplinary expertise. This profession is relatively recession-resistant as maintenance is essential regardless of economic cycles. Geographic hotspots for employment include manufacturing hubs, energy production zones, and large logistics centers. Future-proofing this career involves continuous learning in new industrial technologies, cybersecurity for operational technology (OT) systems, and specialized certifications in areas like mechatronics or advanced diagnostics.
Plant Maintenance Technician Career Path
Career progression for a Plant Maintenance Technician typically involves a blend of deepening technical expertise, expanding problem-solving capabilities, and developing leadership skills. Advancement often follows a dual path: an individual contributor (IC) track leading to lead technician roles, and a management track progressing into supervisory and managerial positions. Performance, specialized certifications, and continuous learning significantly influence the speed of progression.
Company size and industry sector heavily impact career paths. Larger corporations may offer more structured progression and opportunities for specialization in areas like automation or predictive maintenance. Smaller plants might require a more generalist skillset, with technicians handling a broader range of equipment. Lateral moves might involve transitioning between different types of industrial plants or specializing in specific machinery, like HVAC systems or heavy machinery.
Networking within the industry, securing advanced certifications (e.g., CMRP, specific OEM training), and demonstrating a proactive approach to problem-solving are crucial for advancement. Mentorship from experienced technicians or supervisors also provides invaluable guidance. Technicians often pivot into roles focused on reliability engineering, maintenance planning, or even facility management, leveraging their hands-on experience for strategic operational improvements.
Junior Plant Maintenance Technician
0-2 yearsKey Focus Areas
Plant Maintenance Technician
2-5 yearsKey Focus Areas
Senior Plant Maintenance Technician
5-8 yearsKey Focus Areas
Lead Plant Maintenance Technician
8-12 yearsKey Focus Areas
Maintenance Supervisor
10-15 yearsKey Focus Areas
Maintenance Manager
15+ yearsKey Focus Areas
Junior Plant Maintenance Technician
0-2 yearsPerform routine preventative maintenance tasks and assist senior technicians with repairs. Work under direct supervision, following detailed instructions for equipment checks, lubrication, and minor adjustments. Responsibilities involve ensuring basic operational readiness and maintaining cleanliness in work areas.
Key Focus Areas
Develop foundational skills in safety protocols, tool usage, and basic troubleshooting. Learn to interpret blueprints, schematics, and technical manuals. Focus on understanding the plant's specific machinery and maintenance procedures. Build a strong work ethic and attention to detail.
Plant Maintenance Technician
2-5 yearsExecute complex repairs and preventative maintenance independently. Troubleshoot equipment malfunctions, diagnose root causes, and implement corrective actions. Participate in equipment installation and calibration. Provide guidance to junior technicians and collaborate with operations teams.
Key Focus Areas
Master a wide range of maintenance tasks, including mechanical, electrical, and hydraulic systems. Gain proficiency in diagnostics and advanced troubleshooting. Pursue certifications in specific equipment or safety areas. Develop independent problem-solving and decision-making abilities.
Senior Plant Maintenance Technician
5-8 yearsServe as a subject matter expert for specific plant systems or equipment. Lead complex diagnostic and repair efforts, often handling critical or high-risk machinery. Initiate and implement improvements to maintenance processes and safety standards. Act as a technical resource for the team.
Key Focus Areas
Develop expertise in specialized systems or machinery within the plant. Focus on optimizing maintenance procedures, reducing downtime, and implementing predictive maintenance techniques. Enhance communication skills for effective collaboration with engineering and production departments. Mentor and train less experienced technicians.
Lead Plant Maintenance Technician
8-12 yearsCoordinate and oversee the daily activities of a small team of technicians on specific projects or shifts. Assign tasks, monitor progress, and ensure adherence to safety and quality standards. Provide on-the-job training and technical guidance. Act as a primary point of contact for operational issues related to maintenance.
Key Focus Areas
Cultivate strong leadership and organizational skills. Focus on project management, team coordination, and advanced problem resolution. Develop a deeper understanding of plant operations and how maintenance impacts overall efficiency. Begin exploring maintenance software and data analysis for decision-making.
Maintenance Supervisor
10-15 yearsManage a team of maintenance technicians, overseeing daily operations, scheduling, and resource allocation. Ensure all maintenance activities comply with safety regulations and company policies. Conduct performance reviews, identify training needs, and foster a culture of continuous improvement. Report on team metrics and project status.
Key Focus Areas
Develop supervisory and team management skills, including scheduling, performance evaluation, and conflict resolution. Learn budgeting principles and resource allocation for maintenance operations. Focus on improving team efficiency and implementing best practices in maintenance management. Gain deeper insights into regulatory compliance.
Maintenance Manager
15+ yearsOversee the entire maintenance department, including strategic planning, budgeting, and personnel management. Develop and implement comprehensive maintenance programs to maximize asset reliability and minimize downtime. Collaborate with senior leadership on capital expenditure planning and operational improvements. Responsible for department performance and safety records.
Key Focus Areas
Master strategic planning, budgeting, and long-term asset management. Develop strong leadership, communication, and negotiation skills. Focus on integrating maintenance strategies with overall plant production goals and financial objectives. Explore advanced maintenance technologies and lean principles.
Job Application Toolkit
Ace your application with our purpose-built resources:
Plant Maintenance Technician Resume Examples
Proven layouts and keywords hiring managers scan for.
View examplesPlant Maintenance Technician Cover Letter Examples
Personalizable templates that showcase your impact.
View examplesTop Plant Maintenance Technician Interview Questions
Practice with the questions asked most often.
View examplesPlant Maintenance Technician Job Description Template
Ready-to-use JD for recruiters and hiring teams.
View examplesGlobal Plant Maintenance Technician Opportunities
Plant Maintenance Technicians find demand across various global industrial sectors, including manufacturing, energy, and infrastructure. This role involves maintaining complex machinery and systems, a universal need in industrialized economies. International job markets for this profession remain stable as of 2025, driven by ongoing industrialization and infrastructure development. Different countries have varying safety standards and equipment types, requiring adaptability. Professionals consider international opportunities for specialized experience or better economic prospects. Some international certifications, like certain ISO standards or trade-specific credentials, can enhance global mobility.
Global Salaries
Salary ranges for Plant Maintenance Technicians vary significantly by region and industrial sector. In North America, specifically the United States, annual salaries typically range from $55,000 to $80,000 USD, with higher figures in regions with significant industrial bases. Canadian salaries are comparable, often between $50,000 and $75,000 CAD (approximately $37,000-$55,000 USD), reflecting a similar cost of living.
Europe presents diverse compensation. In Germany, a technician might earn €40,000 to €60,000 (approximately $43,000-$65,000 USD) annually, with strong social benefits like extensive vacation and healthcare. The UK sees salaries from £30,000 to £45,000 (approximately $38,000-$57,000 USD). Southern and Eastern European countries generally offer lower nominal salaries but often align with lower living costs, maintaining purchasing power.
Asia-Pacific markets, such as Australia, offer AUD 65,000 to AUD 95,000 (approximately $43,000-$63,000 USD) for experienced technicians, particularly in mining or large-scale manufacturing. In emerging economies like Southeast Asia, salaries can range from $15,000 to $30,000 USD, but this reflects a much lower cost of living. Middle Eastern countries, especially in oil and gas, offer competitive tax-free salaries, often $40,000 to $70,000 USD, plus housing and transport allowances.
Tax implications and take-home pay differ greatly. Countries like Germany have higher income taxes but robust social security. Gulf states often have no income tax. Experience and specialized skills, such as robotics or PLC programming, significantly boost international compensation. Some multinational companies use global pay scales, but local market adjustments are common.
Remote Work
International remote work for a Plant Maintenance Technician is generally not feasible due to the hands-on nature of the role. This profession requires physical presence to inspect, diagnose, repair, and maintain machinery and systems on-site within industrial plants. The core duties cannot be performed remotely.
However, some peripheral activities might involve remote elements. For example, a technician might participate in virtual training sessions, review digital schematics, or consult with engineering teams remotely. Digital nomad opportunities are virtually non-existent for this specific role. Companies hiring Plant Maintenance Technicians prioritize on-site presence and typically do not offer global remote hiring options for the core function.
Any remote work for this role would involve administrative tasks or theoretical planning, not the actual maintenance work. Salary expectations are tied to the physical location of the plant. Equipment needs are standard tools and safety gear, not remote setup. Internet requirements are minimal beyond basic communication tools.
Visa & Immigration
Plant Maintenance Technicians often qualify for skilled worker visas in many industrialized nations. Popular destinations include Canada, Australia, and Germany, which have specific immigration pathways for skilled trades. Requirements typically include relevant vocational qualifications, several years of experience, and sometimes an employer sponsorship. Many countries require skills assessments to recognize foreign credentials.
For instance, Canada's Express Entry system or Provincial Nominee Programs target skilled trades with specific points for experience and language proficiency. Australia's Skilled Migration program also lists maintenance roles. Germany offers a skilled immigration law, often requiring a recognized qualification and a job offer. Visa timelines vary, typically from 6 to 18 months, depending on the country and specific program.
Language proficiency in English, German, or the local language is often a requirement, demonstrated through standardized tests. Pathways to permanent residency exist in many countries after several years of skilled employment. Intra-company transfers are also possible for technicians working for multinational corporations. Practical considerations include family visas and dependent rights, which are usually part of skilled worker visa packages.
2025 Market Reality for Plant Maintenance Technicians
Understanding current market realities is crucial for Plant Maintenance Technicians. This knowledge helps set realistic expectations for career progression and skill development. The field has evolved significantly between 2023 and 2025, driven by post-pandemic reshoring initiatives and the rapid acceleration of automation and AI in manufacturing.
Broader economic factors, such as supply chain stability and energy costs, directly influence plant operations and thus the demand for maintenance staff. Market realities also vary by experience level; senior technicians with specialized skills in robotics or predictive analytics often find more opportunities than entry-level candidates. Location and company size also play a role, with large, modern facilities typically offering more advanced roles. This analysis provides an honest assessment of current conditions.
Current Challenges
Plant Maintenance Technicians face increased competition for specialized roles, particularly those requiring advanced automation or robotics skills. Economic uncertainty can delay capital investments in new plants or upgrades, slowing hiring. Some entry-level positions see saturation as training programs graduate more candidates than immediate openings, requiring longer job search timelines.
A notable skill gap exists in predictive maintenance technologies. Many employers seek technicians proficient with AI-driven diagnostic tools, a skill set not universally present among candidates. This creates a barrier for those without up-to-date training. The normalization of remote work does not apply here, meaning geographic relocation often remains a necessity for securing roles in specific industrial hubs.
Growth Opportunities
Strong demand persists for Plant Maintenance Technicians skilled in industrial automation and robotics. Emerging roles in predictive maintenance and data-driven fault analysis offer significant opportunities. Technicians who can interpret sensor data and utilize AI-powered diagnostic software are highly sought after, often commanding better salaries and more stable positions.
Professionals can gain a competitive advantage by pursuing certifications in PLC programming, industrial network protocols, and specialized equipment like collaborative robots. Underserved markets exist in regions experiencing manufacturing expansion or those with aging infrastructure requiring modernization, particularly in the Midwest and Southeast. Specific skills in energy efficiency systems and sustainable manufacturing processes also provide a distinct edge.
While economic adjustments might slow some hiring, the ongoing need to maintain complex, expensive machinery ensures a baseline demand for skilled technicians. Sectors like pharmaceuticals, food processing, and advanced materials manufacturing remain robust, offering consistent opportunities. Investing in training for new technologies now can position technicians for long-term career resilience and growth, making strategic educational investments vital.
Current Market Trends
Hiring for Plant Maintenance Technicians remains steady but increasingly specialized as of 2025. Demand centers on technicians proficient with automated systems, robotics, and smart factory technologies. The widespread integration of generative AI in manufacturing processes, while not directly replacing technicians, shifts the focus from reactive repairs to predictive maintenance and system optimization. Technicians now need to interpret data from AI-powered diagnostic tools and maintain complex, interconnected machinery.
Economic conditions influence hiring, with expansion in sectors like renewable energy and advanced manufacturing driving new plant construction and subsequent technician demand. Conversely, traditional heavy industries might see slower growth. Employer requirements now heavily emphasize mechatronics skills, PLC programming, and data analysis capabilities alongside traditional mechanical and electrical aptitudes. Companies seek adaptable technicians who can troubleshoot both hardware and software issues. Salary trends show a premium for those with advanced certifications in automation and digital maintenance platforms. Market saturation is minimal for highly skilled technicians, though generalist roles might see more applicants. Geographic demand varies significantly; industrial corridors and regions with new manufacturing facilities offer more opportunities than older, declining industrial zones. Seasonal hiring is less pronounced than cyclical industry investments.
Emerging Specializations
The field of plant maintenance is undergoing a significant transformation, driven by advancements in automation, data analytics, and sustainable practices. These technological shifts are not merely incremental; they are creating entirely new specialization opportunities for Plant Maintenance Technicians. Understanding these emerging areas allows professionals to strategically position themselves for the next generation of industrial operations.
Early positioning in these cutting-edge specializations is crucial for career advancement from 2025 onwards. Professionals who acquire expertise in these future-oriented niches will find themselves in high demand, often commanding premium compensation and experiencing accelerated career growth. While established maintenance specializations remain vital, the highest growth potential lies in areas integrating new technologies and methodologies.
Many emerging areas, particularly those involving advanced predictive analytics or robotics, are moving from niche applications to mainstream adoption. This transition means significant job opportunities are likely to materialize within the next three to five years, rather than a distant future. Pursuing these specializations involves a balance of risk and reward; early adopters gain a competitive advantage, but must commit to continuous learning in rapidly evolving fields.
Predictive Maintenance & IoT Integration Specialist
Predictive maintenance leverages sensor data, machine learning, and advanced analytics to forecast equipment failures before they occur. Plant Maintenance Technicians specializing in this area interpret data from IoT devices, identify patterns indicative of impending issues, and schedule interventions precisely. This shift from reactive or preventive maintenance significantly reduces downtime and operational costs, making it a critical skill for modern industrial facilities.
Industrial Robotics & Automation Technician
Robotics and automation are increasingly integrated into plant operations, from automated guided vehicles (AGVs) to collaborative robots (cobots) performing repetitive tasks. Plant Maintenance Technicians in this specialization focus on the installation, calibration, troubleshooting, and repair of these advanced robotic systems. They ensure the seamless operation and optimal performance of automated machinery within the plant environment, supporting production efficiency.
Sustainable Plant Systems Technician
Sustainable operations and energy efficiency are growing priorities for industrial plants, driven by environmental regulations and cost savings. This specialization involves maintaining systems designed to reduce energy consumption, optimize waste management, and support renewable energy integration within the plant. Plant Maintenance Technicians in this field work with energy monitoring systems, efficient HVAC, and specialized eco-friendly equipment, ensuring compliance and operational sustainability.
Operational Technology (OT) Cybersecurity Technician
Cybersecurity for Operational Technology (OT) is a critical and rapidly expanding area, as industrial control systems become more interconnected. Plant Maintenance Technicians specializing in OT cybersecurity protect the plant's operational networks and equipment from cyber threats. They are responsible for implementing security protocols, monitoring for vulnerabilities, and responding to incidents that could impact production or safety, bridging the gap between IT and physical plant operations.
AR/VR Maintenance Support Specialist
Augmented Reality (AR) and Virtual Reality (VR) are transforming training, troubleshooting, and remote assistance in plant maintenance. Technicians specializing in AR/VR applications utilize these technologies for real-time equipment diagnostics, guided repair procedures, and immersive training simulations. They help integrate AR/VR tools into daily workflows, improving efficiency, safety, and knowledge transfer across the maintenance team, especially in complex or hazardous environments.
Pros & Cons of Being a Plant Maintenance Technician
Understanding both the advantages and challenges of any career is crucial before making a commitment. A Plant Maintenance Technician's experience can vary significantly based on the industry, company culture, specific equipment, and individual aptitude. Factors such as the age of the facility, the level of automation, and the company's investment in preventative maintenance all influence daily realities. What one person considers a benefit, like hands-on problem-solving, another might find a challenge due to the physical demands. These assessments can also shift throughout a career, as early-career technicians focus on learning, while senior technicians might prioritize mentorship or specialized projects. This balanced overview aims to provide a realistic perspective on what to expect in this essential industrial role.
Pros
There is consistent high demand for skilled Plant Maintenance Technicians across various industries like manufacturing, energy, and food processing, ensuring strong job security.
The role offers a high degree of hands-on problem-solving, where technicians directly diagnose and repair mechanical, electrical, and hydraulic systems, providing immediate gratification from fixing tangible issues.
Plant Maintenance Technicians typically earn competitive wages, often with opportunities for overtime pay due to the critical nature of their work and the need for continuous plant operation.
This career path provides continuous learning opportunities as technicians work with diverse machinery, advanced automation, and new technologies, constantly expanding their skill set.
The work is dynamic and rarely monotonous, as technicians face a variety of challenges daily, from routine preventative maintenance to unexpected emergency repairs on complex systems.
This role offers a clear sense of purpose and contribution, as technicians are directly responsible for ensuring the operational efficiency and safety of critical industrial equipment, preventing costly downtime.
Many companies provide comprehensive benefits packages, including health insurance, retirement plans, and paid time off, reflecting the value placed on skilled maintenance personnel.
Cons
The work environment often includes exposure to noise, vibrations, dust, chemicals, and extreme temperatures, which can be physically demanding and pose health risks over time.
Maintenance emergencies can occur at any time, requiring Plant Maintenance Technicians to be on-call or work irregular hours, including nights, weekends, and holidays, disrupting personal life.
This role carries inherent safety risks due to working with heavy machinery, electrical systems, pressurized equipment, and hazardous materials, demanding constant vigilance and adherence to safety protocols.
While some troubleshooting is routine, complex equipment failures can be highly stressful, requiring technicians to diagnose obscure problems quickly under pressure to minimize costly downtime.
The job is physically demanding, involving frequent lifting, climbing, bending, kneeling, and working in confined spaces or at heights, which can lead to fatigue and strain.
Career advancement opportunities for Plant Maintenance Technicians can be limited primarily to supervisory roles or specialized technical positions, requiring additional training and certifications.
Ongoing training is necessary to keep up with new machinery, automation technologies, and safety regulations, requiring a commitment to continuous learning outside of regular work hours.
Frequently Asked Questions
Plant Maintenance Technicians face distinct challenges ensuring operational continuity and equipment longevity. This section addresses the most common questions about entering this hands-on role, from required mechanical aptitude to on-the-job problem-solving in an industrial environment.
What are the typical educational and certification requirements to become a Plant Maintenance Technician?
Most Plant Maintenance Technician roles require a high school diploma or GED, along with vocational training or an associate's degree in industrial maintenance, mechatronics, or a related technical field. Many employers also value certifications in specific areas like hydraulics, pneumatics, or electrical systems. Practical experience gained through apprenticeships or internships significantly boosts your employability.
How long does it take to become job-ready as a Plant Maintenance Technician if I'm starting from scratch?
Gaining entry-level job readiness usually takes 1-2 years if you pursue a vocational program or associate's degree. Apprenticeships, which combine on-the-job training with classroom instruction, can last 3-4 years but provide paid experience. Self-taught individuals might take longer, focusing on hands-on projects and gaining certifications to prove their skills.
What is the typical salary range for a Plant Maintenance Technician, including entry-level and experienced roles?
Entry-level Plant Maintenance Technicians can expect to earn between $40,000 and $55,000 annually, depending on location, industry, and specific skills. Experienced technicians with specialized knowledge or certifications can earn $60,000 to $80,000 or more. Overtime pay is often available due to the critical nature of the role, especially during breakdowns or scheduled maintenance.
What is the job security and market demand like for Plant Maintenance Technicians?
The job outlook for Plant Maintenance Technicians is stable, with consistent demand across various industries like manufacturing, energy, and logistics. As plants modernize, the need for skilled technicians who can maintain complex automated systems remains high. Job security is generally strong because these roles are essential for keeping operations running efficiently and safely.
What is the typical work-life balance for a Plant Maintenance Technician, considering shifts or on-call duties?
Work-life balance can vary, as maintenance roles sometimes require working shifts, on-call duty, or responding to emergency breakdowns outside of regular hours. While many positions offer standard hours, be prepared for occasional flexibility. The physical demands of the job, including lifting, climbing, and working in various industrial environments, also factor into daily life.
What are the career advancement opportunities for a Plant Maintenance Technician?
Career growth paths include specializing in particular equipment (e.g., PLCs, robotics, HVAC), becoming a lead technician, or moving into supervisory roles. Many technicians also advance into maintenance planning, reliability engineering, or facility management. Continuous learning and obtaining advanced certifications are key to unlocking these opportunities.
What does a typical day look like for a Plant Maintenance Technician, and what are the working conditions?
The job involves hands-on troubleshooting, repairing machinery, performing preventative maintenance, and ensuring equipment operates safely. You will work with mechanical, electrical, hydraulic, and pneumatic systems. Expect to use a variety of tools, read technical schematics, and often work in environments that can be noisy, hot, or involve heights or confined spaces.
Related Careers
Explore similar roles that might align with your interests and skills:
Industrial Maintenance Technician
A growing field with similar skill requirements and career progression opportunities.
Explore career guideMaintenance Engineer
A growing field with similar skill requirements and career progression opportunities.
Explore career guideMaintenance Mechanic
A growing field with similar skill requirements and career progression opportunities.
Explore career guideMaintenance Technician
A growing field with similar skill requirements and career progression opportunities.
Explore career guidePlant Technician
A growing field with similar skill requirements and career progression opportunities.
Explore career guideAssess your Plant Maintenance Technician readiness
Understanding where you stand today is the first step toward your career goals. Our Career Coach helps identify skill gaps and create personalized plans.
Skills Gap Analysis
Get a detailed assessment of your current skills versus Plant Maintenance Technician requirements. Our AI Career Coach identifies specific areas for improvement with personalized recommendations.
See your skills gapCareer Readiness Assessment
Evaluate your overall readiness for Plant Maintenance Technician roles with our AI Career Coach. Receive personalized recommendations for education, projects, and experience to boost your competitiveness.
Assess your readinessSimple pricing, powerful features
Upgrade to Himalayas Plus and turbocharge your job search.
Himalayas
Himalayas Plus
Himalayas Max
Find your dream job
Sign up now and join over 100,000 remote workers who receive personalized job alerts, curated job matches, and more for free!
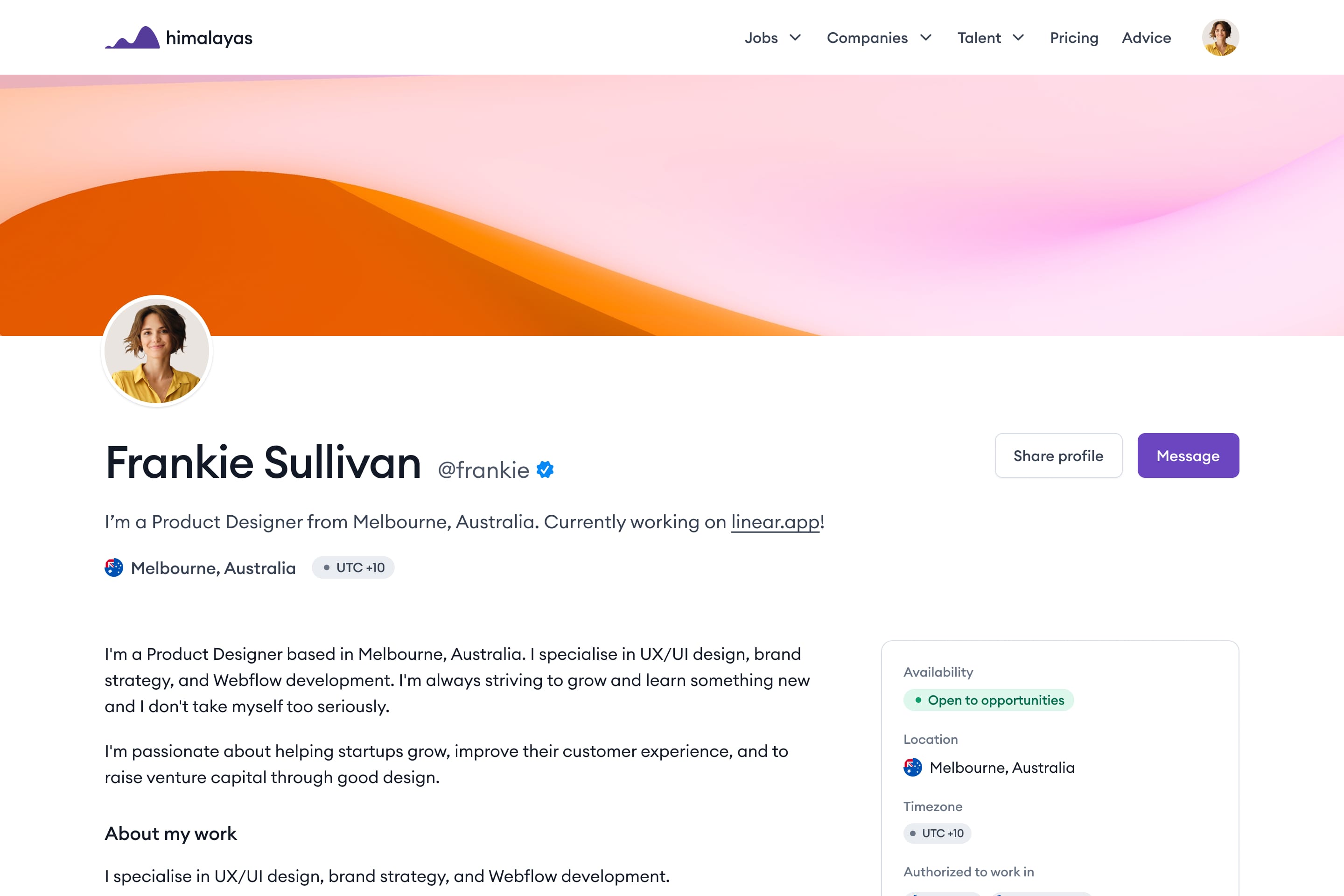