Complete Iron Pourer Career Guide
Iron pourers are the artisans of the foundry, transforming raw metal into essential components for countless industries. This hands-on role involves working with molten iron, demanding precision, strength, and an unwavering commitment to safety. You will be shaping the future of manufacturing, crafting everything from automotive parts to heavy machinery components.
Key Facts & Statistics
Median Salary
$48,740 USD
(U.S. Bureau of Labor Statistics, May 2023)
Range: $35k - $65k+ USD, depending on experience and location
Growth Outlook
1%
slower than average (U.S. Bureau of Labor Statistics, 2022)
Annual Openings
≈3,200
openings annually (U.S. Bureau of Labor Statistics, 2022)
Top Industries
Typical Education
High school diploma or equivalent, often with on-the-job training or a vocational program in metal casting or welding.
What is an Iron Pourer?
An Iron Pourer is a highly skilled and specialized industrial professional responsible for the critical step of transferring molten iron into molds to create castings. They manage the flow of extremely hot liquid metal, ensuring it fills the mold cavities correctly and solidifies into the desired shape without defects. This role demands meticulous attention to detail, precision, and an unwavering commitment to safety given the inherent hazards of working with molten materials.
This position differs significantly from a general 'foundry worker' or 'caster.' While a foundry worker might handle various tasks like mold preparation, shakeout, or finishing, the Iron Pourer focuses exclusively on the delicate and dangerous art of pouring. Unlike a 'caster' who might work with various metals like aluminum or steel, an Iron Pourer specializes specifically in iron, understanding its unique metallurgical properties and pouring characteristics.
What does an Iron Pourer do?
Key Responsibilities
- Operate and monitor induction furnaces to melt scrap metal and raw materials, ensuring the molten iron reaches the precise temperature and chemical composition required for casting.
- Skim dross and impurities from the surface of molten iron using specialized tools, maintaining the purity of the metal before pouring into molds.
- Transport ladles of molten iron from the furnace to the pouring area, often using overhead cranes or forklifts, ensuring safe and precise handling of extremely hot material.
- Carefully pour molten iron into sand molds or permanent molds, controlling the flow rate and ensuring complete filling without defects like cold shuts or misruns.
- Monitor the pouring process closely for any anomalies, such as spills, splashes, or mold integrity issues, and react quickly to prevent accidents or quality deviations.
- Maintain a clean and organized work area, disposing of slag and spent molding materials properly to ensure a safe and efficient foundry environment.
- Conduct routine inspections of pouring equipment, ladles, and personal protective equipment to identify and report any wear or damage that could compromise safety or operational efficiency.
Work Environment
Iron pourers work in industrial foundries, which are typically hot, noisy, and dusty environments. The work involves exposure to extreme heat, fumes, and molten metal, making safety protocols critically important. It is a physically demanding role, requiring strength, stamina, and excellent hand-eye coordination.
Collaboration with furnace operators, mold makers, and quality control technicians is essential for a smooth casting process. The pace of work is often fast and consistent, especially during pouring cycles, with strict adherence to production schedules. Shifts can vary, including day, evening, or night shifts, and often involve overtime to meet production demands. Safety is the absolute top priority in this high-risk environment.
Tools & Technologies
Iron pourers utilize a range of heavy industrial equipment and safety gear. They operate induction furnaces or cupola furnaces for melting, along with overhead cranes, forklifts, or specialized pouring machines for material handling. Essential tools include refractory-lined ladles of various sizes for transporting molten metal, skimming tools for impurity removal, and pyrometers or thermal cameras for temperature verification.
Safety equipment is paramount, including heat-resistant personal protective equipment (PPE) such as aluminized suits, face shields, gloves, and safety boots. They also work with mold-making equipment and sand preparation systems indirectly, understanding how mold quality impacts the pour. Understanding material science principles, especially metallurgy and the properties of cast iron, is crucial for success.
Iron Pourer Skills & Qualifications
Iron Pourers require a highly specialized skill set that blends traditional craftsmanship with a deep understanding of metallurgy and foundry operations. Qualifications for this role are primarily built on hands-on experience and demonstrated competency, rather than extensive formal education. While larger, more automated foundries might prioritize candidates with some technical training, smaller, artisanal operations often value apprenticeships and on-the-job learning above all else.
The importance of certifications and licenses varies significantly by region and specific foundry regulations. For instance, some jurisdictions may require specific safety certifications for handling molten metal or operating heavy machinery. The skill landscape is evolving with advancements in automation and safety protocols; however, the core competencies of safely handling molten iron and understanding its properties remain paramount. Practical experience often outweighs formal degrees for entry-level positions, though vocational training can accelerate career progression. Senior-level Iron Pourers are distinguished by their ability to troubleshoot complex pouring issues, manage teams, and implement advanced safety procedures.
Alternative pathways into this field are common, with many successful Iron Pourers starting as general foundry laborers and progressing through internal training programs. Self-taught individuals are rare given the inherent dangers and specialized equipment involved. The balance between breadth and depth of skills leans heavily towards deep expertise in pouring techniques, temperature control, and safety protocols. Misconceptions often include underestimating the physical demands and the critical need for precision and attention to detail required in every pour. Prioritizing rigorous safety training and gaining extensive practical experience are essential for anyone entering this field.
Education Requirements
Technical Skills
- Molten Metal Handling: Safe and precise manipulation of ladles, crucibles, and pouring mechanisms for molten iron.
- Temperature Control and Measurement: Accurately reading and adjusting iron temperatures using pyrometers and understanding the impact of temperature on casting quality.
- Mold Preparation and Integrity Checks: Ensuring molds (sand, ceramic, or permanent) are properly prepared, sealed, and free of defects before pouring.
- Pouring Techniques: Mastery of various pouring methods (e.g., direct pour, tilt pour, pressure pour) to achieve desired casting properties and minimize defects.
- Furnace Operation and Tapping: Basic understanding of cupola, induction, or electric arc furnace operation, including tapping procedures and metal transfer.
- Slag Management: Identifying, separating, and safely handling slag during and after the pouring process.
- Personal Protective Equipment (PPE) Usage: Proficiently wearing, maintaining, and understanding the limitations of specialized heat-resistant gear, face shields, and respirators.
- Emergency Procedures and Safety Protocols: Rapid response to spills, equipment failures, and other emergencies; strict adherence to lockout/tagout and other safety regulations.
- Material Science Fundamentals: Basic knowledge of iron metallurgy, including different iron types (e.g., gray, ductile), their properties, and solidification characteristics.
- Casting Defect Identification: Recognizing common casting defects (e.g., shrinkage, porosity, cold shuts) and understanding their causes related to pouring.
Soft Skills
- Attention to Detail: Critical for ensuring precise pour rates, temperature control, and mold integrity, directly impacting the quality and safety of each casting.
- Safety Consciousness: Paramount in an environment dealing with molten metal; requires constant vigilance and adherence to strict safety protocols to prevent serious injury.
- Physical Stamina and Endurance: The role involves prolonged standing, heavy lifting, and working in high-heat environments, demanding significant physical resilience.
- Problem-Solving: Essential for quickly identifying and rectifying issues during the pour, such as misruns, cold shuts, or equipment malfunctions.
- Teamwork and Communication: Requires seamless coordination with crane operators, mold makers, and other foundry personnel to execute pours safely and efficiently.
- Discipline and Adherence to Procedures: Follows strict operational guidelines, pouring schedules, and quality control measures without deviation.
- Adaptability: Adjusts quickly to changing conditions, such as unexpected temperature fluctuations or equipment issues, maintaining control of the pour.
- Stress Management: Manages high-pressure situations effectively, especially when dealing with large volumes of molten metal and tight production deadlines, ensuring calm and precise execution under duduress.
How to Become an Iron Pourer
Entering the iron pouring field offers multiple pathways, from direct entry as a labor hand to formal apprenticeships. A complete beginner can expect to spend 3-6 months gaining foundational safety knowledge and basic shop skills before advancing to more specialized tasks. Career changers with transferable skills like heavy machinery operation or welding might accelerate this timeline, potentially securing entry-level positions within a few weeks if they demonstrate a strong work ethic and willingness to learn.
Traditional entry often involves starting as a general laborer or foundry assistant, learning on the job. Non-traditional paths might include vocational training programs focused on metallurgy or industrial arts, though these are less common specifically for iron pouring. Geographic location significantly impacts opportunities; major industrial regions with a history of manufacturing will have more foundries and thus more openings than smaller, less industrialized areas. Company size also matters; larger foundries may have structured training programs, while smaller shops might offer more direct, hands-on mentorship.
A common misconception is that this field requires extensive formal education; practical experience and a strong safety mindset are often more valued. While some foundries appreciate certifications in safety or specific equipment, they primarily seek individuals who are reliable, physically capable, and committed to learning the trade. Networking within the local industrial community or attending regional trade shows can open doors to unadvertised positions and mentorship opportunities, which are crucial in a trade-focused environment.
Research foundry operations and safety protocols to build foundational knowledge. Understand the basics of metal casting, different types of iron, and the significant safety hazards involved in working with molten metal. This initial research will help you speak confidently about your interest and commitment to safety during interviews.
Obtain relevant safety certifications, such as OSHA 10 or 30, and consider first aid/CPR training. Many foundries prioritize safety above all else, and having these certifications demonstrates a proactive approach to workplace well-being. This step can often be completed within a few weeks through online or in-person courses.
Seek entry-level labor or assistant positions at local foundries or manufacturing plants. These roles, such as general labor, sand mixer, or shakeout operator, provide invaluable hands-on experience with foundry processes and expose you to the working environment. Expect to learn the physical demands and operational flow of a busy foundry.
Develop core practical skills by observing experienced pourers and assisting with various tasks. Focus on understanding furnace operation, ladle preparation, pouring techniques, and quality control. This practical learning phase, often lasting 6-12 months, is essential for building the muscle memory and judgment required for safe and effective iron pouring.
Build a professional network by connecting with experienced foundry workers, supervisors, and industry professionals. Attend local industrial trade events or join relevant online forums to gain insights into hiring practices and potential job openings. These connections can lead to mentorship opportunities and referrals for more specialized roles.
Prepare a resume that highlights your safety certifications, any hands-on labor experience, and your strong work ethic and attention to detail. Emphasize your physical capabilities, reliability, and willingness to learn and adhere to strict safety guidelines. Tailor your application to specific foundry requirements, showcasing your understanding of the job's demands.
Apply for Iron Pourer or Molten Metal Handler trainee positions and prepare for practical interviews. Be ready to discuss your safety knowledge, demonstrate your understanding of foundry processes, and show your commitment to the physically demanding and high-stakes environment. Successful candidates will convey a serious dedication to the trade.
Step 1
Research foundry operations and safety protocols to build foundational knowledge. Understand the basics of metal casting, different types of iron, and the significant safety hazards involved in working with molten metal. This initial research will help you speak confidently about your interest and commitment to safety during interviews.
Step 2
Obtain relevant safety certifications, such as OSHA 10 or 30, and consider first aid/CPR training. Many foundries prioritize safety above all else, and having these certifications demonstrates a proactive approach to workplace well-being. This step can often be completed within a few weeks through online or in-person courses.
Step 3
Seek entry-level labor or assistant positions at local foundries or manufacturing plants. These roles, such as general labor, sand mixer, or shakeout operator, provide invaluable hands-on experience with foundry processes and expose you to the working environment. Expect to learn the physical demands and operational flow of a busy foundry.
Step 4
Develop core practical skills by observing experienced pourers and assisting with various tasks. Focus on understanding furnace operation, ladle preparation, pouring techniques, and quality control. This practical learning phase, often lasting 6-12 months, is essential for building the muscle memory and judgment required for safe and effective iron pouring.
Step 5
Build a professional network by connecting with experienced foundry workers, supervisors, and industry professionals. Attend local industrial trade events or join relevant online forums to gain insights into hiring practices and potential job openings. These connections can lead to mentorship opportunities and referrals for more specialized roles.
Step 6
Prepare a resume that highlights your safety certifications, any hands-on labor experience, and your strong work ethic and attention to detail. Emphasize your physical capabilities, reliability, and willingness to learn and adhere to strict safety guidelines. Tailor your application to specific foundry requirements, showcasing your understanding of the job's demands.
Step 7
Apply for Iron Pourer or Molten Metal Handler trainee positions and prepare for practical interviews. Be ready to discuss your safety knowledge, demonstrate your understanding of foundry processes, and show your commitment to the physically demanding and high-stakes environment. Successful candidates will convey a serious dedication to the trade.
Education & Training Needed to Become an Iron Pourer
The Iron Pourer role primarily relies on hands-on training and practical experience, rather than formal academic degrees. While university degrees are not typically required, vocational schools and apprenticeships provide structured pathways. These specialized programs often cover metallurgy, safety protocols, and casting techniques essential for working with molten metal. Costs for vocational programs range from $5,000 to $15,000 and usually take 6 months to 2 years to complete. Apprenticeships, often unpaid initially, offer on-the-job learning and can last 3 to 5 years, leading to journeyman status.
Employers highly value demonstrated practical skills and a strong understanding of safety, making hands-on experience paramount. Certifications in specific casting processes or safety standards, like OSHA certifications, significantly enhance a candidate's marketability. Self-study, while possible for theoretical knowledge, cannot replace the supervised practical training needed for this hazardous role. Continuous learning focuses on new casting technologies, material science advancements, and updated safety regulations, often provided through industry workshops or employer-sponsored training.
The educational needs vary by the foundry's specialization; for instance, art foundries may emphasize different techniques than industrial ones. Gaining initial experience, even in entry-level foundry support roles, is a common and effective way to progress into an Iron Pourer position. The industry recognizes experience and specific certifications over general academic credentials for this role.
Iron Pourer Salary & Outlook
Compensation for an Iron Pourer varies significantly based on several critical factors beyond just base salary. Geographic location plays a substantial role, as areas with a higher concentration of foundries or industrial activity, like the Midwest or parts of the Southeast U.S., may offer more competitive wages due to demand. The cost of living in these regions also influences pay scales.
Years of experience dramatically impact earning potential, with seasoned Iron Pourers commanding higher rates. Specialization in particular types of iron or casting processes, along with certifications in safety or advanced foundry techniques, can also lead to premium compensation. Total compensation packages often include overtime pay, which is common in foundry work, along with health insurance, retirement plans, and sometimes production bonuses.
Industry-specific trends, such as the demand from manufacturing, automotive, or construction sectors, directly influence salary growth. Larger foundries or those producing highly specialized components may offer better pay and benefits compared to smaller operations. Remote work is not applicable for this hands-on role. While figures are presented in USD, international markets have their own distinct wage structures driven by local industrial demand and labor costs.
Salary by Experience Level
Level | US Median | US Average |
---|---|---|
Iron Pourer | $48k USD | $50k USD |
Senior Iron Pourer | $60k USD | $62k USD |
Lead Iron Pourer | $72k USD | $75k USD |
Foundry Supervisor | $85k USD | $88k USD |
Market Commentary
The job market for Iron Pourers is experiencing a steady demand, largely driven by the foundational role of cast iron in various industries, including automotive, heavy machinery, and infrastructure. While not a high-growth sector, the skilled nature of the work ensures consistent opportunities. Projections indicate a stable outlook, with some regional growth tied to manufacturing reshoring efforts and infrastructure spending.
Technological advancements, such as automation in material handling and robotic pouring systems, are emerging. These technologies aim to improve safety and efficiency rather than entirely replace skilled pourers. Instead, they require pourers to adapt to operating and monitoring advanced equipment, evolving the role. The supply of new, skilled Iron Pourers is often limited, creating a demand-supply imbalance that favors experienced workers.
This profession is relatively recession-resistant due to the ongoing need for cast components in essential industries. Geographic hotspots for Iron Pourers typically align with industrial manufacturing hubs. Future-proofing in this career involves continuous learning in new foundry technologies, safety protocols, and quality control systems. The direct, physical nature of the work means it is less susceptible to full automation compared to other manufacturing roles, but embracing new tools remains key.
Iron Pourer Career Path
Career progression for an Iron Pourer typically follows a hands-on, skill-based trajectory within a foundry environment. Advancement relies heavily on demonstrated proficiency in safety protocols, pouring techniques, and equipment operation, along with a growing understanding of metallurgical properties. Professionals often progress from mastering basic tasks to handling more complex pours and eventually leading teams.
Individual contributor (IC) tracks focus on refining pouring expertise and becoming a subject matter expert in specific casting types or alloys. Management tracks involve supervising pour teams, optimizing production processes, and ensuring quality control. Factors influencing advancement include consistent performance, adherence to stringent safety standards, willingness to learn new casting methods, and the ability to mentor others. Company size and the type of castings produced also affect career paths; larger foundries might offer more specialized roles or faster progression into supervisory positions.
Lateral movement opportunities exist into related roles like quality control, furnace operation, or pattern making, requiring additional training. Networking within the foundry industry, though less formal than in other fields, involves gaining recognition for reliability and skill. Continuous learning about new materials, automation, and safety regulations marks significant progression. Career pivots might lead to roles in metallurgy, industrial safety, or even equipment maintenance, leveraging the deep understanding of molten metal and heavy machinery.
Iron Pourer
0-2 yearsPerforms routine iron pouring operations under direct supervision. Focuses on safely transferring molten iron from ladles into molds, ensuring proper fill and temperature. Primarily responsible for executing specific pouring instructions. Works as part of a pouring crew, contributing to daily production targets. Decisions are typically limited to immediate task execution.
Key Focus Areas
Mastering fundamental pouring techniques, including ladle handling and mold filling. Strict adherence to all safety regulations and personal protective equipment (PPE) protocols. Developing an understanding of different iron types and their pouring characteristics. Learning to identify common casting defects and their causes. Building strong teamwork and communication skills with fellow pourers and furnace operators.
Senior Iron Pourer
2-5 yearsExecutes complex iron pouring tasks with minimal supervision, handling diverse mold types and challenging pour conditions. Provides guidance and training to less experienced pourers, ensuring consistent quality and safety. Troubleshoots minor pouring issues independently and assists in maintaining equipment. Takes on more critical or specialized pouring assignments.
Key Focus Areas
Refining advanced pouring techniques for complex molds and various alloys. Proactively identifying and resolving pouring-related issues to prevent defects. Mentoring new or junior pourers on best practices and safety. Deepening knowledge of furnace operation, metal treatments, and quality control procedures. Contributing to process improvement initiatives and efficiency gains.
Lead Iron Pourer
5-8 yearsLeads a specific pouring station or a small team of pourers, overseeing all pouring operations for their assigned area. Ensures production targets are met while maintaining stringent quality and safety standards. Acts as the primary point of contact for technical issues during pouring. Responsible for initial training and ongoing performance feedback for team members.
Key Focus Areas
Developing leadership skills, including team coordination, scheduling, and conflict resolution. Optimizing pouring schedules and material flow for maximum efficiency. Implementing and enforcing advanced safety protocols and emergency procedures. Collaborating with metallurgy and engineering teams on new casting designs or material specifications. Training and certifying pourers on new equipment or techniques.
Foundry Supervisor
8+ years total experienceManages all iron pouring operations across the entire foundry floor, overseeing multiple pour teams and stations. Responsible for the overall safety, quality, and productivity of the pouring department. Develops and implements operational policies and procedures. Makes critical decisions regarding production flow, staffing, and equipment utilization. Reports directly to plant management and plays a key role in strategic planning.
Key Focus Areas
Cultivating strong managerial and supervisory capabilities, including performance management and team development. Strategic planning for production schedules, resource allocation, and budget management. Driving continuous improvement initiatives across the foundry floor, focusing on safety, quality, and efficiency. Building strong relationships with other departments, including maintenance, quality control, and engineering. Staying current with industry advancements in casting technology and safety regulations.
Iron Pourer
0-2 yearsPerforms routine iron pouring operations under direct supervision. Focuses on safely transferring molten iron from ladles into molds, ensuring proper fill and temperature. Primarily responsible for executing specific pouring instructions. Works as part of a pouring crew, contributing to daily production targets. Decisions are typically limited to immediate task execution.
Key Focus Areas
Mastering fundamental pouring techniques, including ladle handling and mold filling. Strict adherence to all safety regulations and personal protective equipment (PPE) protocols. Developing an understanding of different iron types and their pouring characteristics. Learning to identify common casting defects and their causes. Building strong teamwork and communication skills with fellow pourers and furnace operators.
Senior Iron Pourer
2-5 yearsExecutes complex iron pouring tasks with minimal supervision, handling diverse mold types and challenging pour conditions. Provides guidance and training to less experienced pourers, ensuring consistent quality and safety. Troubleshoots minor pouring issues independently and assists in maintaining equipment. Takes on more critical or specialized pouring assignments.
Key Focus Areas
Refining advanced pouring techniques for complex molds and various alloys. Proactively identifying and resolving pouring-related issues to prevent defects. Mentoring new or junior pourers on best practices and safety. Deepening knowledge of furnace operation, metal treatments, and quality control procedures. Contributing to process improvement initiatives and efficiency gains.
Lead Iron Pourer
5-8 yearsLeads a specific pouring station or a small team of pourers, overseeing all pouring operations for their assigned area. Ensures production targets are met while maintaining stringent quality and safety standards. Acts as the primary point of contact for technical issues during pouring. Responsible for initial training and ongoing performance feedback for team members.
Key Focus Areas
Developing leadership skills, including team coordination, scheduling, and conflict resolution. Optimizing pouring schedules and material flow for maximum efficiency. Implementing and enforcing advanced safety protocols and emergency procedures. Collaborating with metallurgy and engineering teams on new casting designs or material specifications. Training and certifying pourers on new equipment or techniques.
Foundry Supervisor
8+ years total experienceManages all iron pouring operations across the entire foundry floor, overseeing multiple pour teams and stations. Responsible for the overall safety, quality, and productivity of the pouring department. Develops and implements operational policies and procedures. Makes critical decisions regarding production flow, staffing, and equipment utilization. Reports directly to plant management and plays a key role in strategic planning.
Key Focus Areas
Cultivating strong managerial and supervisory capabilities, including performance management and team development. Strategic planning for production schedules, resource allocation, and budget management. Driving continuous improvement initiatives across the foundry floor, focusing on safety, quality, and efficiency. Building strong relationships with other departments, including maintenance, quality control, and engineering. Staying current with industry advancements in casting technology and safety regulations.
Job Application Toolkit
Ace your application with our purpose-built resources:
Global Iron Pourer Opportunities
Iron pourers find consistent demand globally, especially in regions with strong manufacturing and infrastructure development. This specialized trade requires direct, hands-on foundry work, limiting its remote nature. International opportunities often arise in countries investing heavily in industrial expansion or maintaining legacy foundries. Cultural differences may impact workplace safety standards and team dynamics, while regulatory variations dictate environmental compliance. Professionals consider international roles for higher wages, skill development, or access to advanced foundry technology. No specific international certifications exist; practical experience and skill validation are key.
Global Salaries
Salaries for iron pourers vary significantly by region, reflecting local industrial strength and cost of living. In North America, particularly the US and Canada, experienced iron pourers earn between $45,000 and $70,000 USD annually. Major industrial states or provinces often offer the higher end of this range. European countries like Germany and the UK offer salaries from €35,000 to €55,000 (approximately $38,000 to $60,000 USD), with Germany generally providing better benefits due to its strong manufacturing sector. These figures account for higher living costs in Western Europe.
In Asia-Pacific, countries such as Australia and South Korea present opportunities. Australian iron pourers might see AUD 50,000 to AUD 75,000 (about $33,000 to $50,000 USD), while South Korea offers KRW 35,000,000 to KRW 55,000,000 (roughly $26,000 to $40,000 USD). These regions typically have lower purchasing power parity than North America or Western Europe for similar nominal wages. Latin American markets like Brazil and Mexico offer lower nominal salaries, often ranging from $15,000 to $25,000 USD, though local purchasing power can be relatively higher. Compensation structures vary; some countries include robust healthcare and pension plans, while others rely more on direct wages.
Tax implications significantly affect take-home pay. For instance, European countries generally have higher income taxes but often compensate with extensive social security benefits. Experience and specialized skills, like working with specific alloys or advanced pouring techniques, can command higher compensation internationally. There are no standardized international pay scales for this trade; compensation depends on local industrial agreements and individual negotiation.
Remote Work
International remote work opportunities for iron pourers are virtually non-existent. The role demands direct physical presence in a foundry environment, working with molten metal and heavy machinery. This hands-on nature makes it impossible to perform remotely. Digital nomad lifestyles do not apply to this profession.
Some related roles, such as metallurgy engineers or foundry managers, might have limited remote components for planning or administrative tasks, but the core function of an iron pourer requires on-site engagement. Companies do not typically hire iron pourers for international remote work. Any international role would involve relocation and on-site employment.
Visa & Immigration
Skilled worker visas are the primary pathway for iron pourers seeking international employment. Countries with significant manufacturing sectors, such as Germany, Canada, Australia, and the US, may offer opportunities. Requirements often include proof of relevant experience, a job offer from a local employer, and sometimes a skills assessment. For instance, Canada's Express Entry system or Australia's skilled migration programs may consider foundry workers, though specific
2025 Market Reality for Iron Pourers
Understanding the current market for iron pourers is crucial for career planning in this specialized trade. The industry has navigated post-pandemic supply chain disruptions and adapted to new manufacturing demands. Broad economic factors, such as industrial output and infrastructure spending, directly influence job availability and stability.
Market realities for iron pourers vary significantly. Experienced pourers with a proven safety record find more opportunities than entry-level candidates. Geographic location is paramount, as jobs are concentrated in regions with active foundries. Company size also matters, with larger foundries often offering more stable employment and benefits, while smaller operations may have more flexible roles. This analysis provides an honest assessment of current conditions.
Current Challenges
Iron pourers face significant challenges, primarily due to the physically demanding and hazardous nature of the work. Automation in foundries, while not fully displacing pourers, reduces the total number of manual pouring stations. Competition for skilled roles is rising as fewer new entrants consider this demanding trade.
Economic downturns directly impact manufacturing and construction, leading to reduced demand for castings. Finding roles requires specific certifications and a willingness to relocate to areas with active foundries.
Growth Opportunities
Despite challenges, strong opportunities exist for skilled iron pourers, particularly those with a focus on safety and efficiency. Foundries serving the automotive, heavy equipment, and infrastructure sectors consistently seek experienced personnel. Emerging opportunities are appearing in specialized alloy casting and additive manufacturing support roles, where traditional pouring skills complement new technologies.
Professionals can gain an advantage by pursuing certifications in advanced safety procedures, metallurgy, or specific pouring techniques. Underserved markets often align with regions experiencing industrial revitalization or where older foundries face a shortage of skilled labor. Acquiring skills in automated pouring system operation or quality control software can also enhance a pourer's marketability.
Market corrections can create opportunities for those willing to relocate or adapt to new industry demands. Strategic career moves include specializing in niche casting processes or targeting foundries that produce high-value, custom components. The consistent need for infrastructure repair and new industrial development ensures a baseline demand for cast iron products, providing ongoing opportunities in this essential trade.
Current Market Trends
Hiring for iron pourers shows steady demand in sectors reliant on heavy machinery, automotive components, and infrastructure. Foundries are investing in safer, more ergonomic equipment, but the core skill of precise molten metal handling remains crucial. The industry is seeing a generational shift; many experienced pourers are retiring, creating openings.
Economic indicators, particularly in manufacturing and construction, directly influence job availability. A strong housing market or increased infrastructure spending often boosts demand for cast iron products, in turn driving pourer recruitment. Conversely, slowdowns can lead to reduced shifts or hiring freezes.
Technology, especially advanced robotics and AI-driven quality control, influences the pourer's role by automating auxiliary tasks and enhancing safety monitoring. However, the nuanced skill of manually pouring molten iron, adjusting for temperature and flow, is not yet fully replicable by machines, preserving the need for human expertise. Employers increasingly seek pourers with a deeper understanding of metallurgical properties and safety protocols, not just physical capability.
Salary trends for experienced pourers are stable, often with good benefits, reflecting the specialized skill and risk involved. Entry-level positions face more saturation, but experienced pourers find consistent work. Geographic variations are pronounced; states with robust manufacturing bases, like Michigan, Ohio, and Pennsylvania, have stronger markets than those with fewer heavy industries. Seasonal patterns are less influential than overall economic cycles, though construction-related demand can fluctuate.
Emerging Specializations
The field of iron pouring, while deeply rooted in traditional craftsmanship, faces significant transformation through technological advancements and evolving industry demands. Understanding these shifts is crucial for professionals seeking to advance their careers beyond established practices. New specialization opportunities are emerging, driven by innovations in automation, material science, and environmental sustainability.
Early positioning in these nascent areas offers substantial career benefits for 2025 and beyond. Professionals who adapt to these emerging specializations can command premium compensation and experience accelerated career growth, as their unique skills become highly sought after. These cutting-edge roles often involve integrating traditional pouring expertise with advanced digital or material knowledge.
While established specializations remain vital, a strategic balance involves exploring these future-oriented niches. Many emerging areas, particularly those involving automation or advanced metallurgy, are on a trajectory to become mainstream within the next five to ten years, creating a significant number of job opportunities. Specializing in these cutting-edge fields involves a calculated risk, as some technologies may not fully mature. However, the potential for high reward, through increased demand and compensation, often outweighs these considerations, positioning professionals at the forefront of the industry.
Automated Pouring System Operator
Automated Pouring System Operator is an emerging specialization focusing on the oversight and management of robotic and automated iron pouring lines. These systems require skilled individuals to program, monitor, and troubleshoot complex machinery, ensuring precision and efficiency beyond manual capabilities. This role blends traditional metallurgical knowledge with advanced controls engineering, optimizing production cycles and maintaining consistent quality in high-volume foundry operations.
High-Purity Iron Production Technician
Additive Manufacturing Iron Specialist involves expertise in preparing and pouring iron for 3D printing processes, particularly for large-scale industrial components. This specialization requires a deep understanding of iron's rheological properties at high temperatures and its interaction with various binder jetting or wire arc additive manufacturing (WAAM) techniques. Professionals in this area ensure the integrity and specific metallurgical properties of iron for complex, bespoke designs that cannot be achieved through traditional casting.
Sustainable Iron Pouring Technologist
Sustainable Iron Pouring Technologist focuses on developing and implementing eco-friendly practices within the iron pouring process. This includes optimizing furnace efficiency to reduce energy consumption, managing and recycling foundry waste streams, and exploring alternative, lower-carbon iron production methods. Professionals in this area help foundries meet stringent environmental regulations and reduce their carbon footprint, contributing to a greener industrial future.
Advanced Alloy Pouring Specialist
Advanced Alloy Pouring Specialist concentrates on the precise pouring and handling of novel iron alloys, including those with enhanced properties like high strength, corrosion resistance, or specific thermal characteristics. This role demands an acute understanding of how different alloying elements influence melt behavior and solidification, requiring meticulous control over pouring temperatures, rates, and atmospheric conditions. This specialization supports industries requiring components with extreme performance demands.
Digital Twin & Simulation Pouring Analyst
Digital Twin & Simulation Pouring Analyst utilizes advanced software to create virtual models of the iron pouring process. This specialization involves simulating melt flow, solidification, and potential defect formation before physical casting occurs, optimizing mold designs and pouring parameters. Professionals in this role leverage data analytics and computational fluid dynamics to predict outcomes, reduce material waste, and enhance casting quality and efficiency.
Pros & Cons of Being an Iron Pourer
Making informed career decisions requires understanding both the appealing benefits and the genuine challenges of a profession. The experience of an iron pourer can vary significantly based on the specific foundry, the type of iron being cast, and the individual's role within the pouring team. Factors like company culture, safety standards, and production demands also play a crucial role in shaping the daily work life.
Pros and cons may also shift across different career stages; for instance, the physical demands might be more manageable early on, while the long-term health considerations become more prominent later. What one person views as a challenge, such as a physically demanding role, another might see as a benefit, like staying active. This assessment provides an honest, balanced perspective to help set realistic expectations for anyone considering a career as an iron pourer.
Pros
- Iron pourers often earn a competitive wage, particularly with experience and specialized skills, reflecting the hazardous and skilled nature of the work.
- There is consistent demand for skilled iron pourers in the manufacturing and heavy industry sectors, providing good job security in areas with active foundries.
- The work offers a clear sense of accomplishment, as pourers directly contribute to creating tangible products, from engine blocks to artistic castings.
- The role requires and builds a strong sense of teamwork and camaraderie, as pourers rely heavily on their colleagues for safety and efficient operations.
- Foundries often provide comprehensive training for safety procedures and specialized pouring techniques, allowing individuals to develop valuable, hands-on skills.
- For those who enjoy a physically active and hands-on job, the daily tasks of an iron pourer provide a dynamic alternative to sedentary office work.
- Opportunities exist to learn about metallurgy, casting processes, and quality control, which can open doors to other roles within the foundry industry.
Cons
- Iron pourers work in extremely hot environments, facing radiant heat from molten metal and furnaces, which requires constant hydration and can be physically draining over long shifts.
- This role involves significant exposure to fumes, dust, and particulate matter from the melting and pouring processes, necessitating strict adherence to respiratory protection and ventilation protocols.
- The work is physically demanding, requiring heavy lifting, prolonged standing, and repetitive motions, which can lead to musculoskeletal strain and fatigue over time.
- There is a high risk of severe burns, eye injuries, and other accidents due to handling molten metal and operating heavy machinery, making safety vigilance paramount.
- Work schedules often include irregular hours, night shifts, and weekend work, especially in foundries operating continuously to meet production demands.
- The job can be monotonous and repetitive, as the core tasks of preparing molds, tapping furnaces, and pouring metal remain largely consistent day-to-day.
- Career progression for an iron pourer can be limited within the direct pouring role itself, often requiring further training or specialization to advance into supervisory or technical positions within the foundry.
Frequently Asked Questions
Iron Pourers face unique challenges balancing intense physical demands with precision and safety. This section addresses the most common questions about entering this specialized trade, from mastering the pouring process to understanding the significant safety protocols and the physical toll of the work.
What are the entry requirements to become an Iron Pourer?
You typically do not need a specific college degree to become an Iron Pourer. Most professionals enter the field through on-the-job training, apprenticeships, or vocational programs. Employers prioritize practical skills, a strong work ethic, and adherence to safety procedures over academic credentials. However, a high school diploma or GED is usually a minimum requirement, and some foundational knowledge in metallurgy or welding can be beneficial.
How long does it take to become a skilled Iron Pourer?
Becoming proficient enough to work independently as an Iron Pourer can take 1-3 years. Initial training focuses on safety protocols, equipment operation, and understanding metal properties. You start by assisting experienced pourers, gradually taking on more responsibility. True mastery of the pouring process, including judging temperature and flow, develops over several years of consistent practice and varied experiences in different casting scenarios.
What are the typical salary expectations for an Iron Pourer?
Salaries for Iron Pourers vary based on experience, location, and the type of foundry. Entry-level positions typically start lower, often ranging from $18-$25 per hour. Experienced and highly skilled Iron Pourers, especially those in specialized foundries or leadership roles, can earn $30-$40 per hour or more, plus benefits. Overtime opportunities are also common due to the nature of foundry work, which can significantly increase annual income.
What is the typical work-life balance like for an Iron Pourer?
The work-life balance for an Iron Pourer can be demanding due to the physical nature of the job and often non-traditional hours. Shifts can be long, and some foundries operate 24/7, requiring night or weekend work. The environment is hot and noisy, which adds to the physical strain. However, many pourers appreciate the tangible results of their labor and the camaraderie within foundry teams. Maintaining physical fitness and prioritizing recovery are crucial for longevity in this role.
Is the job of an Iron Pourer secure, or is it at risk from automation?
Job security for skilled Iron Pourers remains relatively stable despite advancements in automation. While some tasks may be automated, the nuanced skill of judging molten metal and ensuring precise pours often requires human expertise. The demand for cast iron products in industries like construction, automotive, and machinery ensures a consistent need for skilled pourers. Experienced professionals with a strong safety record are highly valued and sought after in the industry.
What are the career advancement opportunities for an Iron Pourer?
Career growth for an Iron Pourer often involves specializing in particular types of casting, becoming a lead pourer, or moving into supervisory roles. With additional training and experience, you could advance to a foundry supervisor, quality control inspector, or even a foundry manager. Some pourers also transition into related roles like pattern making, mold design, or maintenance within the same industry. Continuing education in metallurgy or lean manufacturing can also open new doors.
What are the main safety concerns and risks in this role?
The primary safety concerns include extreme heat, molten metal splashes, heavy lifting, and exposure to fumes and dust. Iron Pourers must wear extensive personal protective equipment (PPE), including heat-resistant suits, face shields, and respirators. Foundries implement strict safety protocols, including emergency procedures and ventilation systems. Continuous training in safety is mandatory, and adherence to these rules is paramount to prevent serious injury.
Can Iron Pourers work remotely, or is it strictly an on-site job?
Iron Pouring is inherently a hands-on, on-site role that requires direct interaction with molten metal and heavy machinery. Therefore, remote work is not an option for an Iron Pourer. The job demands physical presence in a foundry environment. However, some administrative or supervisory roles within the foundry industry might offer hybrid or limited remote flexibility, but the core pouring duties are strictly on-site.
Related Careers
Explore similar roles that might align with your interests and skills:
Aluminum Pourer
A growing field with similar skill requirements and career progression opportunities.
Explore career guideFoundry Molder
A growing field with similar skill requirements and career progression opportunities.
Explore career guideMolten Iron Pourer
A growing field with similar skill requirements and career progression opportunities.
Explore career guideSteel Pourer
A growing field with similar skill requirements and career progression opportunities.
Explore career guideTin Pourer
A growing field with similar skill requirements and career progression opportunities.
Explore career guideAssess your Iron Pourer readiness
Understanding where you stand today is the first step toward your career goals. Our Career Coach helps identify skill gaps and create personalized plans.
Skills Gap Analysis
Get a detailed assessment of your current skills versus Iron Pourer requirements. Our AI Career Coach identifies specific areas for improvement with personalized recommendations.
See your skills gapCareer Readiness Assessment
Evaluate your overall readiness for Iron Pourer roles with our AI Career Coach. Receive personalized recommendations for education, projects, and experience to boost your competitiveness.
Assess your readinessSimple pricing, powerful features
Upgrade to Himalayas Plus and turbocharge your job search.
Himalayas
Himalayas Plus
Himalayas Max
Find your dream job
Sign up now and join over 100,000 remote workers who receive personalized job alerts, curated job matches, and more for free!
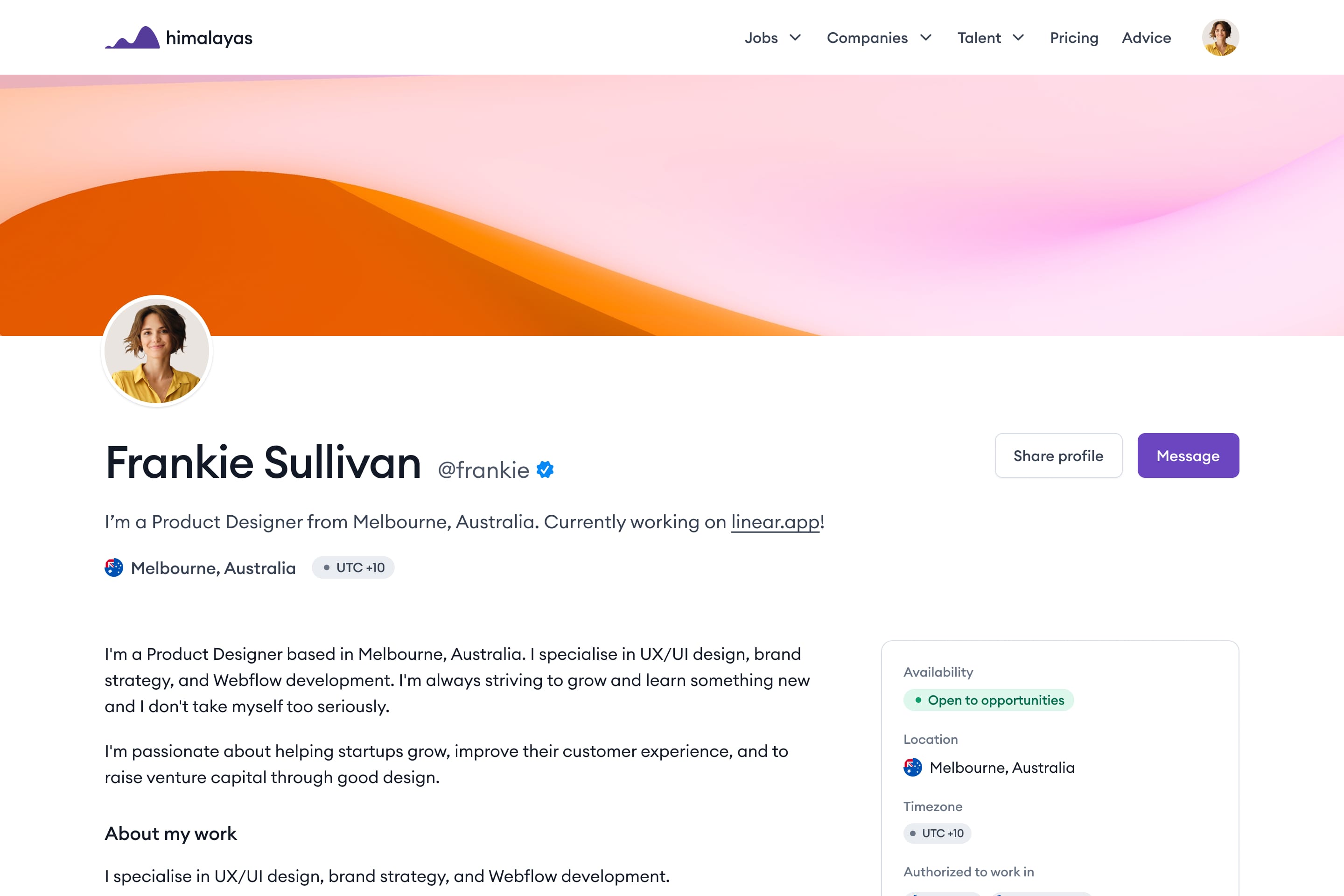