Complete Foundry Molder Career Guide
Foundry molders craft the precise molds that shape molten metal into essential components for countless industries, from automotive to aerospace. This hands-on role combines skilled craftsmanship with an understanding of metallurgy, offering a tangible impact on manufacturing. It's a career path for those who value precision work and seeing raw materials transform into critical parts, requiring both physical dexterity and an eye for detail.
Key Facts & Statistics
Median Salary
$46,920 USD
(U.S. Bureau of Labor Statistics, May 2023)
Range: $34,000 - $65,000+ USD
Growth Outlook
Annual Openings
Top Industries
Typical Education
High school diploma or equivalent; often includes on-the-job training or an apprenticeship
What is a Foundry Molder?
A Foundry Molder specializes in creating the precise sand molds and cores into which molten metal is poured to form castings. This role is fundamental to the manufacturing process in foundries, as the quality and accuracy of the mold directly determine the integrity and dimensions of the final metal product. Molders meticulously prepare the sand mixture, compact it around patterns, and assemble mold sections to create the desired cavity for the metal.
This position differs from a Foundry Melter, who focuses on melting and preparing the metal itself, or a Caster, who oversees the pouring of molten metal. The molder's expertise lies in the intricate art and science of mold construction, ensuring that the casting process has a perfect template, which is critical for producing components ranging from automotive parts to heavy machinery elements. Their skill is essential for minimizing defects and achieving high-quality metallic products.
What does a Foundry Molder do?
Key Responsibilities
- Prepare sand molds by mixing sand, binders, and water according to specifications, ensuring proper consistency and strength for casting.
- Place patterns into the prepared sand, compacting the sand around them using hand tools or automated equipment to create precise mold cavities.
- Install cores into the mold cavities to form internal features or hollow sections within the final casting, aligning them carefully to prevent defects.
- Assemble mold halves (cope and drag) accurately, securing them with clamps or weights to prevent shifting during the metal pouring process.
- Inspect finished molds for defects such as cracks, loose sand, or improper alignment, making necessary repairs to ensure casting quality.
- Operate various foundry equipment, including sand mixers, molding machines, and conveyors, adhering strictly to safety protocols.
- Clean and maintain molding equipment and work areas regularly to ensure efficient operation and a safe working environment.
Work Environment
Foundry molders typically work in industrial settings, which are often hot, noisy, and dusty environments due to the nature of metal casting. The work is physically demanding, involving lifting, bending, and standing for extended periods. Collaboration with other foundry workers, such as furnace operators and metal pourers, is essential for a smooth production flow. Shifts can vary, including day, evening, or night schedules, and some foundries operate 24/7. While the work is consistent, the pace can be fast, especially when preparing molds for active pouring schedules. Safety is a paramount concern, with strict adherence to protocols to mitigate risks associated with molten metal and heavy machinery.
Tools & Technologies
Foundry molders primarily use a range of specialized hand tools such as trowels, slickers, rammers, and mallets for shaping and compacting sand. They also operate larger machinery like sand mixers, jolt-squeeze molding machines, and automated flask handling systems. Essential safety equipment includes heat-resistant gloves, safety glasses, respirators, and protective clothing. Depending on the foundry's modernization, they might interact with basic PLC controls for automated processes or utilize pneumatic tools for compaction. Knowledge of different sand types, binders, and their properties is crucial for successful mold creation.
Foundry Molder Skills & Qualifications
Qualifications for a Foundry Molder emphasize practical, hands-on experience and a strong understanding of casting processes. Formal education often takes a secondary role compared to demonstrated skill and apprenticeship completion. Entry-level positions typically require a high school diploma or equivalent, with on-the-job training being crucial for skill development.
Requirements for a Foundry Molder vary significantly by the type of foundry (e.g., sand, investment, die casting), the metals being cast, and the complexity of the parts produced. Larger foundries might have more structured training programs, while smaller shops rely heavily on direct mentorship. Seniority levels dictate increasing expectations for precision, problem-solving, and the ability to work with diverse molding techniques. Certifications in specific molding processes or safety standards add considerable value, particularly in specialized foundries or those adhering to strict quality controls.
The skill landscape for Foundry Molders is evolving with increased automation and advanced materials. While traditional hand molding remains vital for certain applications, molders increasingly need to understand automated molding machines, robotic pouring, and digital pattern making. This balance between traditional craft and modern technology means continuous learning is essential for long-term career success. Practical experience consistently outweighs advanced degrees, though vocational training provides a strong foundation.
Education Requirements
Technical Skills
- Sand preparation and mixing (e.g., green sand, no-bake, shell molding).
- Pattern making and repair (understanding of wood, metal, or plastic patterns).
- Core making (e.g., sand cores, shell cores, cold box cores).
- Molding machine operation (e.g., jolt-squeeze, high-pressure, automated molding lines).
- Metal pouring techniques and temperature control.
- Casting defect identification and mitigation (e.g., misruns, shrinks, porosity, sand inclusions).
- Use of hand tools and precision measuring instruments (e.g., calipers, micrometers, rulers).
- Basic metallurgy principles relevant to common casting alloys (e.g., iron, steel, aluminum, brass).
- Foundry safety protocols and equipment operation (e.g., PPE, hoist operation, lockout/tagout).
- Blueprint and technical drawing interpretation for mold construction.
- Maintenance and cleaning of molding equipment and tools.
- Shakeout and preliminary casting cleaning processes.
Soft Skills
- Attention to Detail: Critical for ensuring mold integrity, precise measurements, and defect prevention in castings.
- Problem-Solving: Important for diagnosing and resolving issues with mold defects, material inconsistencies, and equipment malfunctions.
- Physical Stamina: Essential for handling heavy materials, operating machinery, and performing repetitive tasks in a hot, demanding environment.
- Safety Consciousness: Crucial for adhering to strict safety protocols, operating hazardous machinery, and preventing workplace accidents.
- Team Collaboration: Necessary for coordinating with pattern makers, furnace operators, and finishing teams to ensure efficient production flow.
- Adaptability: Important for adjusting to different molding techniques, material properties, and production schedules.
- Patience: Required for the meticulous and often repetitive tasks involved in preparing molds and ensuring quality.
- Instruction Following: Essential for accurately executing complex molding instructions and adhering to quality standards and specifications.
How to Become a Foundry Molder
Breaking into the Foundry Molder field offers both traditional and non-traditional entry points. Many individuals begin through vocational training programs or apprenticeships, which provide hands-on experience and direct industry connections. For those without prior experience, entry-level positions often involve starting as a laborer or assistant, learning the craft on the job over several months to a couple of years.
Geographic location significantly impacts opportunities; areas with robust manufacturing and heavy industry, such as the Midwest or parts of the South in the United States, typically have more foundries. Smaller, specialized foundries might offer more direct mentorship, while larger operations could provide structured training programs. The hiring landscape values practical skills and a strong work ethic more than formal academic degrees.
Misconceptions often include believing that all foundry work is entirely automated or that physical strength is the only requirement. While physical stamina is important, precision, attention to detail, and a deep understanding of metallurgy and mold properties are crucial. Networking within local industrial communities and seeking out experienced mentors can accelerate career progression, opening doors to opportunities not widely advertised.
Step 1
Step 2
Step 3
Step 4
Step 5
Step 6
Step 7
Education & Training Needed to Become a Foundry Molder
Becoming a Foundry Molder involves a blend of practical skills and specialized knowledge, which educational pathways reflect. Unlike many professions, a four-year university degree is rarely a prerequisite for this hands-on role. Instead, the educational ecosystem for Foundry Molders heavily favors vocational training, apprenticeships, and on-the-job experience. These pathways typically cost significantly less and require shorter time commitments compared to traditional academic routes.
Vocational programs and community college courses, often lasting 6 months to 2 years, provide foundational knowledge in metallurgy, casting processes, and safety. These programs might cost between $3,000 and $15,000. Apprenticeships, a highly valued route, combine paid on-the-job training with classroom instruction, lasting 2 to 4 years. Apprenticeships offer the benefit of earning a wage while learning and often lead directly to employment with the sponsoring company. Self-study and short online courses can supplement learning but are insufficient on their own for entry into the field.
Employers highly value hands-on experience and demonstrated competence in foundry operations. While a formal certificate or degree can provide a structured entry point, practical skills gained through apprenticeships or extensive on-the-job training often carry more weight. Continuous learning in areas like new molding technologies, materials science, and advanced safety protocols remains crucial throughout a molder's career. The educational path should align with specific employer needs and the type of casting processes involved, as requirements can vary between sand casting, die casting, or investment casting operations.
Foundry Molder Salary & Outlook
Compensation for a Foundry Molder reflects a blend of specialized manual skill, experience, and the specific demands of the casting industry. Geographic location significantly impacts earnings, with areas boasting a higher concentration of manufacturing and heavy industry, such as the Midwest or parts of the Southeast United States, often offering more competitive wages due to localized demand and cost of living differences. International markets also vary, with US figures generally representing a strong benchmark for skilled trades.
Years of experience are a primary driver of salary progression, as molders gain proficiency in complex casting techniques and materials. Specialization in certain types of molding, like sand, investment, or die casting, or expertise with specific metals, can command higher pay. Total compensation extends beyond base salary to include overtime pay, which is common in manufacturing, and comprehensive benefits packages covering health, dental, and vision. Many companies also offer retirement plans like 401(k)s, and some provide profit-sharing or performance bonuses based on production targets or quality metrics.
Industry-specific trends, such as the demand from automotive, aerospace, or heavy equipment sectors, directly influence salary growth. Companies with advanced automation or specialized product lines may offer premium compensation for skilled molders. Negotiating leverage comes from demonstrated expertise, a clean safety record, and the ability to work with diverse molding processes. Remote work is not applicable to this hands-on role, so geographic location remains a fixed element in salary considerations.
Salary by Experience Level
Level | US Median | US Average |
---|---|---|
Apprentice Foundry Molder | $36k USD | $38k USD |
Foundry Molder | $45k USD | $47k USD |
Senior Foundry Molder | $54k USD | $56k USD |
Lead Foundry Molder | $62k USD | $65k USD |
Foundry Supervisor | $75k USD | $78k USD |
Market Commentary
The job market for Foundry Molders is undergoing a period of transformation, driven by both traditional manufacturing demands and technological advancements. While some areas of foundry work are increasingly automated, the core skills of a Molder remain critical for intricate designs, quality control, and troubleshooting. The demand for castings in sectors like automotive, aerospace, defense, and heavy machinery continues to provide a stable base for employment. However, domestic production competition and outsourcing can influence job availability.
Growth in this field is projected to be relatively stable, with the Bureau of Labor Statistics indicating little to no change in employment for metal and plastic machine workers, including molders, over the next decade. This stability means that job openings often arise from the need to replace retiring workers or those who leave the occupation. Emerging opportunities lie in specializations involving new alloys, advanced composite materials, or precision casting techniques for high-tech applications. Companies investing in modernizing their foundries and adopting lean manufacturing principles are often seeking skilled molders who can adapt to new processes and machinery.
The supply and demand dynamics for skilled molders can vary regionally; some areas experience shortages of experienced talent, particularly those proficient in traditional, highly skilled molding methods. Future-proofing this career involves continuous learning, embracing new technologies like 3D printing for mold creation, and understanding digital controls for automated equipment. While not recession-proof, the essential nature of castings for various industries provides a degree of resilience. Geographic hotspots for employment remain concentrated in industrial states like Ohio, Pennsylvania, Michigan, and Wisconsin, where foundries are integral to the manufacturing ecosystem.
Foundry Molder Career Path
Career progression for a Foundry Molder unfolds through a hands-on journey, building expertise from basic molding techniques to advanced supervisory roles. Advancement hinges on mastering various molding processes, understanding metallurgy, and demonstrating consistent quality and efficiency. Both individual contributor (IC) and management tracks exist, with the latter requiring leadership and operational planning skills.
Advancement speed depends on performance, the complexity of castings produced, and the adoption of new technologies like automated molding systems. Larger foundries may offer more specialized roles and clearer promotion paths compared to smaller operations. Lateral moves might involve specializing in specific molding types (e.g., sand, investment, die casting) or moving into related areas like pattern making or quality control within the same industry.
Networking within the foundry community, pursuing certifications in specific molding techniques, and continuous learning about new materials and processes are crucial for career growth. Foundry professionals often pivot into roles such as quality assurance, process improvement, or even sales of foundry equipment, leveraging their deep operational knowledge.
Apprentice Foundry Molder
1-2 yearsKey Focus Areas
Foundry Molder
2-4 years total experienceKey Focus Areas
Senior Foundry Molder
5-8 years total experienceKey Focus Areas
Lead Foundry Molder
8-12 years total experienceKey Focus Areas
Foundry Supervisor
12+ years total experienceKey Focus Areas
Apprentice Foundry Molder
1-2 yearsAssist experienced molders with preparing molds, cleaning castings, and maintaining equipment. Work under direct supervision, performing routine tasks such as mixing sand, setting cores, and basic flask assembly. Impact is primarily on task completion and supporting the efficiency of the molding line.
Key Focus Areas
Develop foundational skills in sand preparation, core making, and basic pattern placement. Learn safety protocols and proper handling of molten metal and molding equipment. Understand different types of molding sand and their properties. Focus on precision, attention to detail, and following instructions accurately.
Foundry Molder
2-4 years total experienceIndependently prepare and assemble molds for various castings, ensuring adherence to specifications. Operate molding machines and equipment with proficiency. Responsible for the quality of individual molds and contributing to production targets. Collaborate with pattern makers and melt shop personnel.
Key Focus Areas
Master various molding techniques including green sand, dry sand, and possibly shell molding. Improve efficiency and accuracy in mold assembly and core setting. Develop a strong understanding of casting defects and their causes, learning to identify and prevent common issues. Begin to troubleshoot minor molding problems independently.
Senior Foundry Molder
5-8 years total experienceLead the setup and execution of challenging molding projects, often involving custom or intricate designs. Provide technical guidance to other molders, ensuring quality standards are met. May oversee a small team or specific molding station. Decisions impact casting quality and production schedules for specific product lines.
Key Focus Areas
Specialize in complex molding techniques, large-scale castings, or advanced materials. Mentor and train junior molders on best practices and safety procedures. Contribute to process improvement initiatives, identifying areas for increased efficiency or reduced waste. Develop problem-solving skills for intricate molding challenges.
Lead Foundry Molder
8-12 years total experienceDirect and coordinate the daily activities of a team of molders, ensuring production targets are met and quality standards are maintained. Responsible for training, safety compliance, and performance of the molding team. Troubleshoot complex production issues and implement corrective actions. Authority extends to workflow management and minor disciplinary actions.
Key Focus Areas
Develop leadership and team coordination skills, assigning tasks and managing workflow for a molding team. Understand production scheduling and resource allocation within the molding department. Focus on optimizing overall molding processes for efficiency, quality, and cost-effectiveness. Participate in cross-functional planning meetings.
Foundry Supervisor
12+ years total experienceOversee the entire molding department, managing personnel, resources, and production schedules to meet organizational goals. Responsible for departmental budget, safety compliance, quality control, and continuous process improvement. Make strategic decisions regarding equipment upgrades, staffing, and production methods. Directly impacts the foundry's overall productivity and profitability.
Key Focus Areas
Acquire strong operational management skills, including budgeting, inventory control, and strategic planning for the molding department. Develop leadership capabilities in talent development, performance management, and conflict resolution. Gain expertise in lean manufacturing principles and continuous improvement methodologies within a foundry setting. Understand broader foundry operations.
Job Application Toolkit
Ace your application with our purpose-built resources:
Foundry Molder Cover Letter Examples
Personalizable templates that showcase your impact.
View examplesFoundry Molder Job Description Template
Ready-to-use JD for recruiters and hiring teams.
View examplesGlobal Foundry Molder Opportunities
Foundry molders are essential globally, transforming raw materials into critical components across manufacturing, automotive, and aerospace industries. Their specialized skills in pattern creation, sand molding, and metal casting are in consistent demand in industrialized nations. International opportunities arise from differing industrial capacities and technological advancements between regions. Cultural nuances impact workplace safety protocols and material handling, while regulatory frameworks dictate environmental compliance and quality control standards. Molders often seek international roles for advanced training or better compensation.
Global Salaries
Foundry molder salaries vary significantly by region and industrial development. In North America, a molder earns between $45,000 and $70,000 USD annually. For instance, in the United States, an experienced molder might earn $60,000, while in Canada, the range is C$55,000-C$85,000 (approximately $40,000-$62,000 USD). These figures reflect higher living costs and strong industrial demand.
European salaries differ, with molders in Germany earning €35,000-€55,000 (about $38,000-$60,000 USD) and in the UK, £28,000-£45,000 (approximately $35,000-$56,000 USD). Scandinavian countries offer higher wages but also higher living expenses. In contrast, Asia-Pacific, particularly China and India, offers lower nominal salaries, often ranging from $10,000-$25,000 USD, though purchasing power can be higher locally.
Latin American countries like Mexico might offer $15,000-$30,000 USD. Beyond base pay, international compensation often includes varying benefits like health insurance, pension contributions, and vacation days, which impact take-home pay. Tax structures also differ; for example, European countries generally have higher income taxes than many parts of North America. Experience directly affects compensation across all regions; a molder with decades of specialized experience commands significantly more.
Remote Work
Direct remote work for a foundry molder is not feasible due to the hands-on nature of the job, which requires physical presence in a manufacturing facility. Molders operate heavy machinery, pour molten metal, and handle intricate molds, tasks impossible to perform remotely. The role demands immediate interaction with materials, equipment, and safety protocols on the factory floor.
However, related roles like process optimization, quality control analysis, or technical training within the foundry industry might offer some remote components. These roles would typically involve data analysis, virtual collaboration, or instructional design, not the core molding tasks. Digital nomad opportunities are nonexistent for active molders. Employers in this field do not generally hire for international remote work in this specific capacity, as the work is fundamentally location-dependent.
Visa & Immigration
Foundry molders seeking international work often utilize skilled worker visas. Countries like Germany, Canada, and Australia have specific pathways for tradespeople. Germany's Skilled Immigration Act simplifies entry for professionals with recognized vocational training. Canada's Express Entry system and Provincial Nominee Programs consider foundry experience under specific NOC codes, requiring credential assessment.
Australia's skilled migration visas, such as the Skilled Nominated (subclass 190) or Skilled Regional (subclass 491) visas, may be options, often requiring a skills assessment by Trades Recognition Australia. Education credential recognition is crucial; vocational qualifications from one country may need formal assessment for equivalence. Some countries might require language proficiency, particularly for integration into the workforce and community, though often not for the visa itself.
Visa timelines vary, typically ranging from a few months to over a year depending on the country and visa type. Employers sometimes sponsor visas, especially for highly skilled molders. Permanent residency pathways exist for skilled workers who integrate into the labor market for several years. Family visas are generally available for dependents of skilled visa holders.
2025 Market Reality for Foundry Molders
Understanding the current market realities for foundry molders is critical for career longevity and strategic planning. The landscape has evolved significantly post-pandemic, with shifts in manufacturing priorities and the accelerating impact of automation and AI.
Broader economic factors, such as industrial output and supply chain stability, directly influence demand for casting processes. Market conditions also vary by experience level, with highly skilled molders in specialized areas experiencing different pressures than entry-level workers. Geographic location and the size of manufacturing facilities further dictate the available opportunities, making a localized understanding essential for setting realistic career expectations.
Current Challenges
Foundry molders face significant challenges, including the increasing automation of repetitive molding tasks, which reduces demand for manual labor. Competition for specialized roles remains high, particularly for those requiring advanced pattern-making skills. Economic downturns in manufacturing sectors directly impact job availability, leading to reduced hiring.
Newer materials and additive manufacturing processes also present a challenge, potentially displacing traditional molding techniques. Job seekers must demonstrate adaptability and a willingness to learn new technologies to remain competitive.
Growth Opportunities
Despite market shifts, specific opportunities exist for foundry molders. Strong demand persists for those specializing in lost-wax casting, investment casting, or sand molding for large, intricate components used in aerospace, defense, and heavy machinery. These areas often require a human touch and expertise that automation cannot fully replicate.
Emerging opportunities include roles focused on quality assurance, where molders ensure the integrity and precision of automated casting processes. Expertise in defect analysis, material handling for exotic alloys, and advanced finishing techniques also provides a competitive edge. Molders who can adapt to new materials and work collaboratively with engineers on rapid prototyping projects find a niche.
Professionals can position themselves advantageously by acquiring certifications in specific casting methods or metallurgy, demonstrating proficiency with quality control software, or gaining experience in foundries adopting Industry 4.0 technologies. Underserved markets often exist in smaller, specialized foundries catering to niche product lines that demand high-precision, custom work. Investing in continuous learning about new casting technologies or materials can open doors to more advanced and secure positions.
Current Market Trends
The market for foundry molders shows a nuanced demand in 2025. While core manufacturing sectors continue to rely on traditional casting, the industry increasingly integrates automation and advanced robotics. This shifts demand from purely manual labor towards molders who can operate and maintain sophisticated machinery, or specialize in complex, custom molds that automation struggles with.
Economic conditions within heavy industry and automotive sectors directly influence hiring. A slowdown in these areas can lead to reduced production and fewer openings for molders. However, defense, aerospace, and specialized industrial equipment sectors often maintain steady demand for high-precision casting, creating pockets of stability.
Generative AI and advanced simulation software are not directly replacing molders but are influencing design and process optimization. This means molders need to understand how digital models translate to physical molds and troubleshoot effectively. Employers increasingly look for molders with a strong understanding of material science, quality control, and an ability to work with CAD/CAM systems, even if they are not designing the molds themselves.
Salary trends for experienced, skilled molders remain stable, particularly for those with expertise in complex alloys or large-scale industrial components. Entry-level positions face more saturation and competition, especially as some basic molding tasks become automated. Geographically, opportunities concentrate in regions with strong manufacturing bases, particularly the Midwest and parts of the Southeast in the U.S., and industrial hubs globally. Remote work is generally not applicable to this hands-on role.
Emerging Specializations
Technological advancements and evolving industrial demands are creating new specialization opportunities for Foundry Molders. Understanding these future-oriented career paths allows professionals to position themselves effectively for significant opportunities in 2025 and beyond.
Early positioning in emerging areas often commands premium compensation and accelerated career growth. As new processes and materials gain traction, expertise in these cutting-edge fields becomes highly valued, differentiating individuals from those with traditional skill sets.
While established specializations remain vital, pursuing emerging areas offers a strategic advantage. It requires a balance, as some cutting-edge fields may take time—typically 3-5 years—to become mainstream and generate a significant volume of job opportunities.
There are inherent risks in specializing in nascent areas, such as the potential for slower adoption or shifts in technological direction. However, the rewards of being at the forefront of innovation, including leadership roles and higher earning potential, often outweigh these considerations.
Additive Manufacturing Molder
Sustainable Molding Specialist
Automated Molding Systems Technician
Advanced Materials Molder
Smart Molding Process Analyst
Pros & Cons of Being a Foundry Molder
Understanding both the advantages and challenges of a career is crucial for making informed decisions. Career experiences vary significantly based on company culture, industry sector, specific specialization, and individual preferences. What one person views as a benefit, another might see as a drawback, and these perceptions can shift at different career stages. This assessment provides an honest, balanced overview of the foundry molder profession, helping you set appropriate expectations. It covers financial, lifestyle, intellectual, and long-term prospects, acknowledging that real-world experiences can differ based on specific circumstances and entry paths.
Pros
There is a consistent demand for skilled foundry molders in manufacturing, offering good job security as foundries are essential for producing metal components across various industries.
Entry into this career often requires vocational training or an apprenticeship, allowing individuals to start working and earning sooner compared to professions requiring extensive university degrees.
The work provides a tangible sense of accomplishment, as molders create the foundational forms for essential metal products, seeing the direct results of their precise and skilled efforts.
Molders develop specialized skills in pattern making, sand preparation, and casting techniques, which are valuable and transferable within the broader manufacturing and metallurgy sectors.
Many foundries offer competitive wages and benefits, including health insurance, retirement plans, and opportunities for overtime, recognizing the physically demanding and specialized nature of the work.
There are opportunities for continuous learning and skill refinement, as new materials, molding techniques, and automation technologies are introduced, allowing molders to expand their expertise.
For individuals who enjoy hands-on, physically active work and the satisfaction of working with raw materials to create finished products, this role provides a fulfilling daily experience.
Cons
The work environment in a foundry is often hot, noisy, and dirty, requiring constant exposure to high temperatures, dust, and fumes, which can be physically demanding and uncomfortable over long shifts.
Foundry molding is a physically demanding job that involves heavy lifting, bending, and repetitive motions, leading to potential strain injuries, back problems, and fatigue over time.
Molding operations carry inherent safety risks, including exposure to molten metal, heavy machinery, and airborne particulates, necessitating strict adherence to safety protocols and the consistent use of personal protective equipment (PPE) to prevent accidents.
The work can be monotonous and repetitive, as molders often perform the same tasks repeatedly throughout the day, which may not appeal to individuals seeking varied or intellectually stimulating work.
Advancement opportunities for a foundry molder may be limited to supervisory roles or specialized molding techniques, requiring additional training or education to progress significantly within the industry.
Work schedules often involve shift work, including nights and weekends, to maintain continuous production, which can disrupt personal life and make it challenging to maintain a consistent routine.
Foundry work can be subject to economic downturns or changes in manufacturing demand, potentially leading to periods of reduced work hours or job instability if production slows.
Frequently Asked Questions
Foundry Molders face distinct challenges around precision, safety, and physical demands. This section addresses the most common questions about entering this role, from mastering molding techniques to understanding the work environment and career progression.
What does a Foundry Molder actually do day-to-day?
Foundry molders create sand molds or patterns for casting metal parts. This involves preparing sand mixtures, compacting them around patterns, and ensuring the mold's integrity before molten metal is poured. The role requires significant attention to detail, physical stamina, and adherence to strict safety protocols to produce high-quality castings.
What qualifications or training do I need to become a Foundry Molder?
Entry into foundry molding often requires a high school diploma or GED. Many employers prefer candidates with vocational training in metalworking, industrial arts, or a related field. Apprenticeships are common and provide hands-on training alongside experienced molders, covering techniques, safety, and equipment operation. Some roles may also benefit from certifications in specific molding processes.
How long does it typically take to become a skilled Foundry Molder?
The time to become job-ready for an entry-level foundry molder position can vary. With an apprenticeship, it typically takes 2-4 years to gain comprehensive skills and experience. If starting with vocational training, you might find entry-level work sooner, but continued on-the-job learning is essential for proficiency. The learning curve involves mastering various molding techniques, material properties, and safety procedures.
What are the working conditions and physical demands of this job?
The work environment for a foundry molder is often hot, noisy, and dusty due to the nature of metal casting. Safety is paramount, requiring personal protective equipment like respirators, safety glasses, and heat-resistant clothing. The job is physically demanding, involving lifting, bending, and standing for long periods. Shifts can include nights or weekends, depending on production schedules.
Is the Foundry Molder role a secure career, or is it at risk from automation?
Job security for foundry molders is generally stable, especially for skilled professionals. While automation impacts some aspects of manufacturing, the demand for custom or complex metal parts often requires human expertise in molding. The industry's reliance on specific skills ensures a consistent need for experienced molders. Economic downturns can affect demand, but essential industries still require castings.
What are the typical salary expectations for a Foundry Molder?
Starting salaries for entry-level foundry molders typically range from $35,000 to $45,000 annually, depending on location and company. Experienced molders with specialized skills or leadership responsibilities can earn $50,000 to $70,000 or more. Overtime opportunities are often available, which can significantly increase earning potential. Benefits packages usually include health insurance, retirement plans, and paid time off.
What are the career growth opportunities for a Foundry Molder?
Career advancement for a foundry molder can lead to several roles. Skilled molders might specialize in complex casting techniques or become pattern makers. Opportunities also exist to move into supervisory positions, overseeing molding teams or production lines. Some molders transition into quality control, ensuring casting integrity, or into maintenance roles for foundry equipment. Continuous learning and a strong work ethic support progression.
Can Foundry Molders work remotely, or is it always an on-site position?
Foundry molding is primarily an on-site role due to the specialized equipment and materials involved. Remote work is not feasible for the hands-on production aspects. However, some administrative or supervisory roles within a foundry might offer hybrid options. The nature of the work requires direct presence in the facility to ensure proper molding processes and safety standards.
Related Careers
Explore similar roles that might align with your interests and skills:
Mold Maker
A growing field with similar skill requirements and career progression opportunities.
Explore career guideGreen Sand Molder
A growing field with similar skill requirements and career progression opportunities.
Explore career guideIngot Caster
A growing field with similar skill requirements and career progression opportunities.
Explore career guideIron Pourer
A growing field with similar skill requirements and career progression opportunities.
Explore career guideSand Molder
A growing field with similar skill requirements and career progression opportunities.
Explore career guideAssess your Foundry Molder readiness
Understanding where you stand today is the first step toward your career goals. Our Career Coach helps identify skill gaps and create personalized plans.
Skills Gap Analysis
Get a detailed assessment of your current skills versus Foundry Molder requirements. Our AI Career Coach identifies specific areas for improvement with personalized recommendations.
See your skills gapCareer Readiness Assessment
Evaluate your overall readiness for Foundry Molder roles with our AI Career Coach. Receive personalized recommendations for education, projects, and experience to boost your competitiveness.
Assess your readinessSimple pricing, powerful features
Upgrade to Himalayas Plus and turbocharge your job search.
Himalayas
Himalayas Plus
Himalayas Max
Find your dream job
Sign up now and join over 100,000 remote workers who receive personalized job alerts, curated job matches, and more for free!
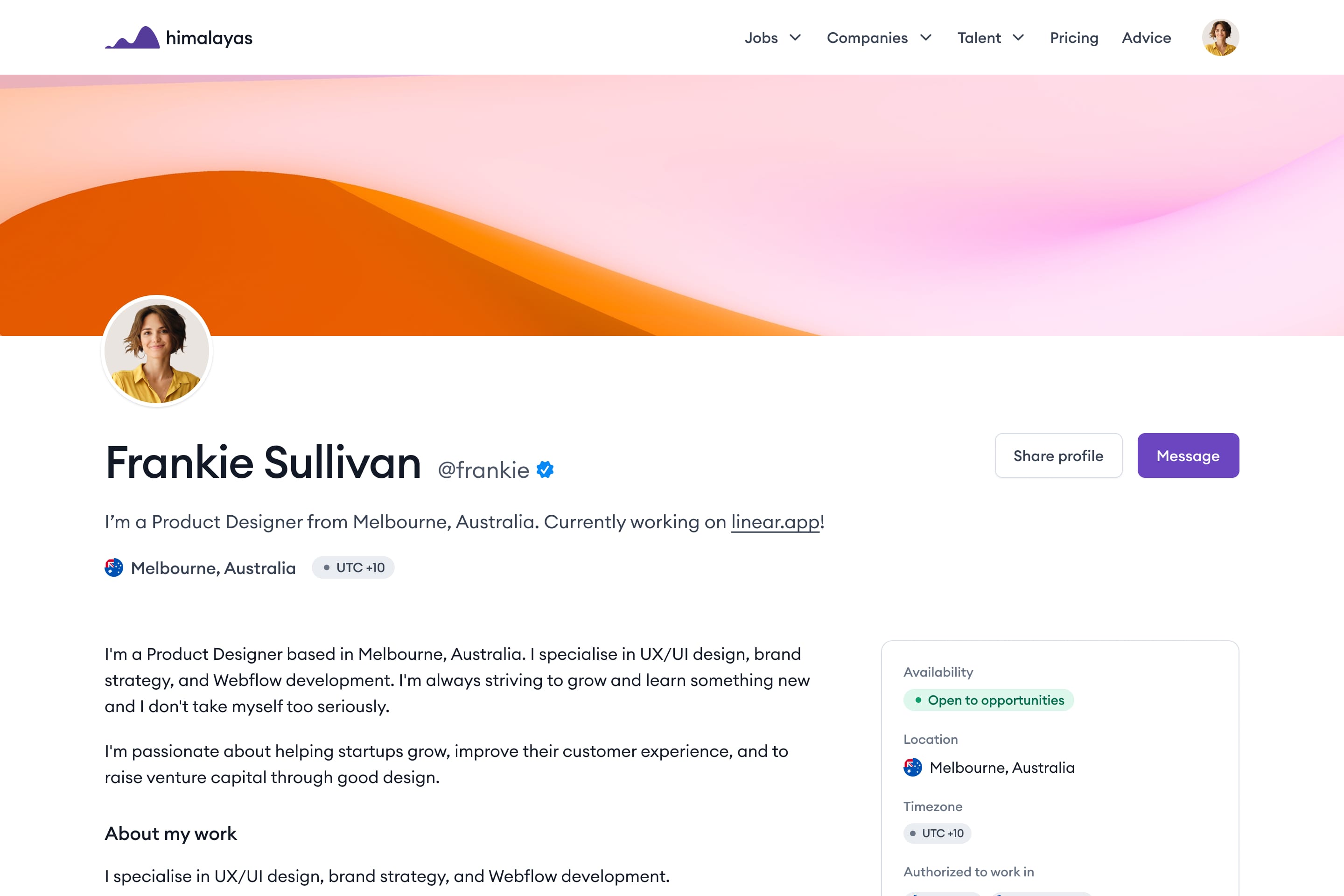