Complete Aluminum Pourer Career Guide
Aluminum Pourers are the skilled artisans at the heart of metal production, transforming molten aluminum into precise castings that form the foundation of countless products, from automotive parts to aerospace components. This physically demanding yet rewarding role requires exceptional precision and safety awareness, ensuring the integrity and quality of materials vital to modern manufacturing. If you are seeking a hands-on career with direct impact on essential industrial processes, this path offers stability and opportunities for mastery.
Key Facts & Statistics
Median Salary
$47,400 USD
(U.S. national median for Casting Machine Operators and Tenders, Metal and Plastic, BLS, May 2023)
Range: $35k - $60k+ USD, varying by experience, industry, and location, with potential for higher earnings through specialized skills or overtime.
Growth Outlook
0%
(little or no change) for Casting Machine Operators and Tenders, Metal and Plastic, BLS, 2022-2032
Annual Openings
≈13,000
openings annually (for Casting Machine Operators and Tenders, Metal and Plastic, BLS, May 2023)
Top Industries
Typical Education
High school diploma or equivalent, with most training occurring on-the-job, often through apprenticeships or vocational programs.
What is an Aluminum Pourer?
An Aluminum Pourer is a specialized industrial worker responsible for the precise and safe transfer of molten aluminum from furnaces into molds or casting machines. This role involves handling extremely hot liquid metal, requiring meticulous attention to detail and strict adherence to safety protocols to prevent accidents and ensure product quality.
Unlike a general foundry worker who might handle various stages of metal production, an Aluminum Pourer focuses specifically on the critical pouring phase. They ensure the metal is at the correct temperature and free of impurities before it enters the mold, directly impacting the integrity and quality of the final aluminum product, whether it's an ingot, a component for an automobile, or an aerospace part. Their expertise prevents costly defects and maintains production efficiency in high-temperature metal processing.
What does an Aluminum Pourer do?
Key Responsibilities
- Operate overhead cranes or forklifts to transport crucibles of molten aluminum safely to the pouring station.
- Skim impurities and dross from the surface of molten aluminum using specialized tools before pouring to ensure metal quality.
- Pour molten aluminum into molds or dies with precision, controlling the flow rate and temperature to prevent defects.
- Monitor furnace temperatures and metal composition, making adjustments to maintain optimal pouring conditions.
- Inspect finished castings or ingots for visual defects such as cracks, voids, or inclusions, reporting any issues.
- Clean and maintain pouring ladles, crucibles, and associated equipment to ensure operational efficiency and safety.
- Adhere strictly to safety protocols, wearing appropriate personal protective equipment and following emergency procedures for handling molten metal.
Work Environment
An aluminum pourer works in a hot, noisy, and potentially hazardous industrial environment, typically within a foundry, casting plant, or smelter. The work involves exposure to extreme heat from molten metal, fumes, and loud machinery. This role requires significant physical stamina and strength for handling equipment and enduring high temperatures.
Collaboration is essential, as pourers often work in small teams with furnace operators, mold makers, and quality control technicians, communicating constantly to ensure safe and efficient operations. Shifts can vary, often including nights, weekends, or rotating schedules, given that furnaces operate continuously. The pace is generally steady but can become intense during pouring cycles, demanding constant vigilance and quick decision-making under pressure.
Tools & Technologies
Aluminum pourers primarily use heavy industrial equipment designed for high-temperature metal handling. They operate overhead cranes, forklifts, and specialized pouring machines to move and dispense molten aluminum. Key tools include refractory-lined crucibles, pouring ladles, and skimming tools for dross removal. They also work with temperature gauges, pyrometers, and sometimes optical spectrometers to monitor metal quality.
Safety equipment is paramount, including heat-resistant personal protective equipment (PPE) such as aluminized suits, face shields, gloves, and safety boots. While less reliant on digital software than other roles, they may use basic control panels for furnace operation and communicate via two-way radios in noisy environments. Understanding material properties of various aluminum alloys is also crucial.
Aluminum Pourer Skills & Qualifications
Becoming a proficient Aluminum Pourer requires a precise blend of practical experience, specific technical skills, and a strong commitment to safety. While formal education is less critical than for other roles, on-the-job training and certifications in safety protocols are paramount. The qualification landscape for this role emphasizes hands-on competence and adherence to strict operational guidelines.
Requirements for an Aluminum Pourer vary primarily by the type of foundry, the scale of operations, and the specific casting processes utilized. Larger industrial foundries often have more formalized training programs and stricter adherence to industry certifications. Smaller operations might prioritize candidates with demonstrated experience, even if self-taught or gained through informal apprenticeships. Geographic regions with strong manufacturing sectors may have more standardized expectations, sometimes including local safety certifications.
Practical experience significantly outweighs formal degrees in this field. Employers prioritize candidates who show a deep understanding of molten metal properties, pouring techniques, and immediate safety responses. Certifications in areas like forklift operation, overhead crane operation, and specific foundry safety practices add substantial value. The skill landscape is evolving with automation, but the core pouring role still demands human judgment and precision; however, understanding automated systems is an emerging skill for future career progression.
Education Requirements
Technical Skills
- Molten Aluminum Handling: Proficient and safe manipulation of molten aluminum, including transfer from furnace to ladle and ladle to mold.
- Temperature Control: Accurate monitoring and adjustment of molten aluminum temperature to ensure optimal pour fluidity and casting quality.
- Pouring Techniques: Mastery of various pouring methods (e.g., direct pour, tilt pour) for different mold types and casting requirements.
- Foundry Safety Protocols: Deep understanding and strict adherence to personal protective equipment (PPE) requirements, lockout/tagout, and emergency procedures.
- Ladle Operation: Skilled use and maintenance of pouring ladles, including preheating, slag removal, and proper material handling.
- Mold Preparation: Basic understanding of mold setup, coating application, and ensuring molds are ready for pouring.
- Slagging and Dross Removal: Efficiently removing impurities from the molten aluminum surface to prevent inclusions in castings.
- Forklift Operation: (Often required) Safe and efficient operation of forklifts for moving ingots, scrap, and finished castings.
- Overhead Crane Operation: (Often required) Competent use of overhead cranes for lifting and transporting heavy ladles of molten metal.
- Quality Inspection (Visual): Ability to visually inspect castings for immediate defects such as short pours, cold shuts, or excessive dross.
- Basic Equipment Maintenance: Performing routine checks and minor maintenance on pouring equipment and tools.
- Alloy Identification: Recognizing different aluminum alloys and their specific pouring characteristics.
Soft Skills
- Attention to Detail: Critical for monitoring molten metal temperatures, flow rates, and mold fill, ensuring casting quality and preventing defects.
- Safety Consciousness: Absolutely essential for working with molten aluminum, requiring constant vigilance to prevent accidents and adhere to strict safety protocols.
- Physical Stamina: The role demands prolonged standing, lifting, and working in hot environments, necessitating good physical endurance.
- Problem-Solving: Quickly identifying and addressing issues like uneven pour, spills, or equipment malfunctions during the casting process.
- Teamwork and Communication: Coordinating effectively with crane operators, mold setters, and other foundry personnel to ensure smooth and safe operations.
- Discipline and Adherence to Procedures: Strictly following established pouring techniques and safety guidelines to maintain consistency and minimize risks.
- Patience: Waiting for correct temperatures, precise timing of the pour, and allowing castings to cool properly.
- Adaptability: Adjusting pouring techniques based on different mold types, alloy compositions, or unexpected operational changes during a shift.
How to Become an Aluminum Pourer
Becoming an Aluminum Pourer requires a blend of specific technical skills and a strong commitment to safety within a foundry environment. Entry into this field often happens through vocational training, apprenticeships, or direct entry into entry-level foundry positions. While a formal degree is not usually required, certifications in metallurgy, welding, or industrial safety can significantly enhance a candidate's profile and accelerate their career progression.
The timeline for becoming proficient can vary. A complete beginner might spend 6-12 months gaining foundational knowledge and entry-level experience before advancing to a pourer role, often through internal promotion. Career changers with transferable skills like heavy machinery operation or manufacturing experience might transition faster, perhaps within 3-6 months. Geographic location plays a significant role, as opportunities are concentrated in regions with a strong manufacturing base and foundries, such as the Midwest and Southeast United States, or industrial zones in Europe and Asia.
Misconceptions often include believing this role is purely manual labor; it involves precise control, material science understanding, and critical decision-making. The hiring landscape values hands-on experience and a demonstrated understanding of safety protocols above all else. Companies often prefer to train from within due to the specialized nature of the work, making entry-level roles like General Laborer or Foundry Helper crucial stepping stones. Networking within local industrial communities and engaging with vocational schools can open doors to these initial opportunities.
Gain foundational knowledge in metallurgy and industrial safety by completing relevant vocational courses or certifications. Focus on understanding metal properties, melting processes, and the safe handling of molten materials. This foundational knowledge provides a critical base for understanding the pourer's responsibilities and safety protocols.
Seek entry-level positions within a foundry or manufacturing facility, such as a General Laborer, Foundry Helper, or Production Assistant. These roles allow you to learn about foundry operations, equipment, and safety procedures firsthand. Expect to spend 6-12 months in such a role, demonstrating reliability and a strong work ethic.
Develop practical skills by assisting experienced pourers and other foundry technicians, focusing on material handling, furnace operation, and mold preparation. Volunteer for tasks that expose you to the pouring process, such as preparing ladles or overseeing cooling. Showing initiative and a willingness to learn the intricacies of pouring is essential.
Obtain specialized certifications in areas like forklift operation, overhead crane operation, or specific welding techniques that are often required in a foundry setting. These certifications enhance your versatility and demonstrate a commitment to professional development, making you a more valuable candidate for advancement.
Network with experienced pourers, supervisors, and human resources personnel within your current or target foundries. Express your interest in the Aluminum Pourer role and seek mentorship to understand the specific skills and temperament required. These connections can provide invaluable insights and potentially lead to internal promotion opportunities or referrals.
Step 1
Gain foundational knowledge in metallurgy and industrial safety by completing relevant vocational courses or certifications. Focus on understanding metal properties, melting processes, and the safe handling of molten materials. This foundational knowledge provides a critical base for understanding the pourer's responsibilities and safety protocols.
Step 2
Seek entry-level positions within a foundry or manufacturing facility, such as a General Laborer, Foundry Helper, or Production Assistant. These roles allow you to learn about foundry operations, equipment, and safety procedures firsthand. Expect to spend 6-12 months in such a role, demonstrating reliability and a strong work ethic.
Step 3
Develop practical skills by assisting experienced pourers and other foundry technicians, focusing on material handling, furnace operation, and mold preparation. Volunteer for tasks that expose you to the pouring process, such as preparing ladles or overseeing cooling. Showing initiative and a willingness to learn the intricacies of pouring is essential.
Step 4
Obtain specialized certifications in areas like forklift operation, overhead crane operation, or specific welding techniques that are often required in a foundry setting. These certifications enhance your versatility and demonstrate a commitment to professional development, making you a more valuable candidate for advancement.
Step 5
Network with experienced pourers, supervisors, and human resources personnel within your current or target foundries. Express your interest in the Aluminum Pourer role and seek mentorship to understand the specific skills and temperament required. These connections can provide invaluable insights and potentially lead to internal promotion opportunities or referrals.
Education & Training Needed to Become an Aluminum Pourer
Becoming an Aluminum Pourer primarily involves hands-on training and specific certifications rather than traditional degree programs. While a high school diploma or GED is often a prerequisite, formal university education is not typically required for this role. Vocational schools and community colleges sometimes offer industrial technology or metallurgy programs that provide foundational knowledge, but most specialized skills are acquired through on-the-job training or apprenticeships within foundries or casting plants.
Alternative learning paths focus on practical skills. Apprenticeships, lasting 1-3 years, provide structured training under experienced pourers, covering safety, metallurgy, temperature control, and mold preparation. These programs often include paid work experience, making them a cost-effective entry point. Certifications in industrial safety, forklift operation, or specific casting processes, such as those from the American Foundry Society (AFS), enhance employability. These certifications typically range from a few hundred to a few thousand dollars and can be completed in days to weeks.
Employers highly value practical experience and a strong safety record. While a four-year engineering degree might cost $40,000-$100,000+, and a two-year associate's degree $10,000-$20,000, direct entry and apprenticeship models require minimal upfront educational costs. Self-study of safety protocols and material properties can supplement hands-on learning. Continuous professional development, especially in new casting technologies or advanced safety practices, remains important throughout an Aluminum Pourer's career, often provided through employer-sponsored training or industry workshops.
Aluminum Pourer Salary & Outlook
Compensation for an Aluminum Pourer varies significantly based on several factors, reflecting the specialized and often demanding nature of the work. Geographic location plays a crucial role; areas with a high concentration of aluminum foundries or manufacturing plants tend to offer higher wages due to demand and potentially higher costs of living. For instance, salaries in industrial hubs of the Midwest or Southeast United States may differ from those in less industrialized regions.
Years of experience directly influence earning potential, with highly skilled and experienced pourers commanding premium rates. Specialization in certain casting techniques or materials, along with certifications in safety or specific machinery operation, can also lead to increased compensation. Total compensation often extends beyond base salary to include overtime pay, which is common in foundry work, production bonuses, and comprehensive benefits packages. These benefits typically include health insurance, retirement contributions like 401(k) plans, and sometimes profit-sharing.
Industry-specific trends, such as demand from the automotive, aerospace, or construction sectors, drive salary growth. Companies facing labor shortages for skilled pourers often offer more competitive wages and sign-on bonuses. While remote work is not applicable to this hands-on role, understanding local market dynamics and negotiating based on proven expertise, safety record, and production efficiency can significantly improve compensation. International markets also employ Aluminum Pourers, but the figures provided here are specific to USD in the United States.
Salary by Experience Level
Level | US Median | US Average |
---|---|---|
Junior Aluminum Pourer | $38k USD | $40k USD |
Aluminum Pourer | $46k USD | $48k USD |
Senior Aluminum Pourer | $55k USD | $57k USD |
Lead Aluminum Pourer | $63k USD | $65k USD |
Casting Supervisor | $75k USD | $78k USD |
Market Commentary
The job market for Aluminum Pourers is stable, driven by consistent demand from manufacturing sectors that rely on aluminum casting. Industries such as automotive, aerospace, construction, and consumer goods require a steady supply of cast aluminum components, ensuring ongoing opportunities for skilled pourers. While the overall manufacturing sector experiences fluctuations, the fundamental need for cast metals provides a resilient base for this profession.
Future growth in this field is projected to remain steady, with modest increases driven by advancements in casting technology and the increasing use of lightweight aluminum in new applications. Automation and robotics are impacting some aspects of foundry work, but the specialized skill and precision required for aluminum pouring often necessitates human oversight and expertise, especially for complex or high-precision castings. This role is less susceptible to full automation compared to other manufacturing tasks.
Supply and demand dynamics show a consistent need for experienced pourers, as the skills are often learned through apprenticeships or on-the-job training and require significant practical experience. There can be shortages of highly skilled candidates in certain regions, leading to competitive wages. Geographic hotspots for this role align with major industrial and manufacturing centers. Continuous learning, particularly in new casting techniques, safety protocols, and the operation of advanced pouring equipment, will be crucial for career longevity and advancement in this evolving industry.
Aluminum Pourer Career Path
Career progression for an Aluminum Pourer involves a clear ladder of increasing responsibility, skill, and safety expertise within the foundry or casting environment. Progression heavily relies on demonstrated proficiency, adherence to safety protocols, and the ability to handle more complex casting operations. Individuals can advance through individual contributor roles or eventually transition into supervisory positions.
Advancement speed depends on several factors: an individual's performance, consistent demonstration of advanced techniques, and a proactive approach to learning new casting methods. Company size and the specific casting processes used also influence career paths; larger operations may offer more specialized roles or faster advancement opportunities. Geographic location can also play a role, with more foundries in certain regions providing greater demand for skilled pourers.
Continuous learning is crucial for an Aluminum Pourer. This includes mastering new pouring techniques, understanding different aluminum alloys, and becoming proficient with updated safety equipment and regulations. Networking within the industry, while less formal than in other fields, can involve sharing knowledge with experienced pourers and supervisors to gain insights into best practices. Career pivots might involve moving into quality control, maintenance, or even specialized roles in metallurgy within the broader manufacturing sector.
Junior Aluminum Pourer
0-2 yearsOperate under direct supervision, assisting experienced pourers with routine casting tasks. Learn to prepare molds, handle ladles, and pour molten aluminum following strict safety guidelines. Responsibilities involve precise measurements and careful observation of pouring temperatures. Impact is on the quality of individual casts, with minimal decision-making authority.
Key Focus Areas
Develop foundational pouring techniques and understand basic safety protocols. Focus on consistent, accurate pouring and learning to identify common casting defects. Familiarize with different aluminum alloys and their properties. Gain proficiency in equipment setup and basic maintenance.
Aluminum Pourer
2-5 yearsPerform independent pouring operations for a variety of products with moderate supervision. Responsible for ensuring molten aluminum meets specific temperature and composition requirements before pouring. May train junior pourers on basic tasks and assist with equipment calibration. Directly impacts production quotas and quality standards for assigned casting runs.
Key Focus Areas
Master advanced pouring techniques for various mold types and casting complexities. Enhance problem-solving skills related to common pouring issues and material reactions. Develop a deeper understanding of thermal dynamics and metallurgy. Focus on efficiency and minimizing material waste.
Senior Aluminum Pourer
5-8 yearsLead pouring teams on specific casting projects, often involving intricate designs or specialized alloys. Provide technical guidance and troubleshoot complex pouring challenges on the floor. Responsible for quality assurance checks and ensuring adherence to all safety regulations for the pouring station. Acts as a key resource for operational problem-solving.
Key Focus Areas
Specialize in complex or high-precision casting methods. Develop strong leadership skills for guiding junior team members and troubleshooting advanced issues. Focus on process optimization and identifying areas for improved safety and efficiency. Begin to understand production scheduling and material logistics.
Lead Aluminum Pourer
8-12 yearsOversee multiple pouring stations or a specific section of the casting floor. Assign tasks to pourers, monitor production schedules, and ensure all safety and quality standards are met. Responsible for training new staff, conducting performance reviews, and implementing process improvements. Has significant input on material ordering and equipment upgrades.
Key Focus Areas
Develop comprehensive operational oversight and team management skills. Focus on strategic planning for pouring operations, including resource allocation and workflow optimization. Cultivate strong communication and conflict resolution abilities. Gain expertise in advanced safety management systems and regulatory compliance.
Casting Supervisor
12+ yearsManage all aspects of the casting department's operations, including pouring, mold preparation, and quality control. Develop and implement production plans, manage budgets, and ensure regulatory compliance. Leads a team of pourers and lead pourers, overseeing their training, development, and performance. Makes critical decisions impacting overall plant efficiency and output.
Key Focus Areas
Acquire strong leadership and managerial competencies, including budgeting, strategic planning, and cross-departmental collaboration. Focus on continuous improvement methodologies and lean manufacturing principles. Develop robust analytical skills for production data and trend analysis. Enhance decision-making for large-scale operational challenges.
Junior Aluminum Pourer
0-2 yearsOperate under direct supervision, assisting experienced pourers with routine casting tasks. Learn to prepare molds, handle ladles, and pour molten aluminum following strict safety guidelines. Responsibilities involve precise measurements and careful observation of pouring temperatures. Impact is on the quality of individual casts, with minimal decision-making authority.
Key Focus Areas
Develop foundational pouring techniques and understand basic safety protocols. Focus on consistent, accurate pouring and learning to identify common casting defects. Familiarize with different aluminum alloys and their properties. Gain proficiency in equipment setup and basic maintenance.
Aluminum Pourer
2-5 yearsPerform independent pouring operations for a variety of products with moderate supervision. Responsible for ensuring molten aluminum meets specific temperature and composition requirements before pouring. May train junior pourers on basic tasks and assist with equipment calibration. Directly impacts production quotas and quality standards for assigned casting runs.
Key Focus Areas
Master advanced pouring techniques for various mold types and casting complexities. Enhance problem-solving skills related to common pouring issues and material reactions. Develop a deeper understanding of thermal dynamics and metallurgy. Focus on efficiency and minimizing material waste.
Senior Aluminum Pourer
5-8 yearsLead pouring teams on specific casting projects, often involving intricate designs or specialized alloys. Provide technical guidance and troubleshoot complex pouring challenges on the floor. Responsible for quality assurance checks and ensuring adherence to all safety regulations for the pouring station. Acts as a key resource for operational problem-solving.
Key Focus Areas
Specialize in complex or high-precision casting methods. Develop strong leadership skills for guiding junior team members and troubleshooting advanced issues. Focus on process optimization and identifying areas for improved safety and efficiency. Begin to understand production scheduling and material logistics.
Lead Aluminum Pourer
8-12 yearsOversee multiple pouring stations or a specific section of the casting floor. Assign tasks to pourers, monitor production schedules, and ensure all safety and quality standards are met. Responsible for training new staff, conducting performance reviews, and implementing process improvements. Has significant input on material ordering and equipment upgrades.
Key Focus Areas
Develop comprehensive operational oversight and team management skills. Focus on strategic planning for pouring operations, including resource allocation and workflow optimization. Cultivate strong communication and conflict resolution abilities. Gain expertise in advanced safety management systems and regulatory compliance.
Casting Supervisor
12+ yearsManage all aspects of the casting department's operations, including pouring, mold preparation, and quality control. Develop and implement production plans, manage budgets, and ensure regulatory compliance. Leads a team of pourers and lead pourers, overseeing their training, development, and performance. Makes critical decisions impacting overall plant efficiency and output.
Key Focus Areas
Acquire strong leadership and managerial competencies, including budgeting, strategic planning, and cross-departmental collaboration. Focus on continuous improvement methodologies and lean manufacturing principles. Develop robust analytical skills for production data and trend analysis. Enhance decision-making for large-scale operational challenges.
Job Application Toolkit
Ace your application with our purpose-built resources:
Aluminum Pourer Cover Letter Examples
Personalizable templates that showcase your impact.
View examplesAluminum Pourer Job Description Template
Ready-to-use JD for recruiters and hiring teams.
View examplesGlobal Aluminum Pourer Opportunities
An Aluminum Pourer's role involves precise control over molten aluminum in casting and smelting operations globally. This highly specialized manual skill is in steady demand within industrial sectors worldwide. Regulatory differences impact safety standards and production methods across countries, but core pouring techniques remain consistent. Professionals often seek international opportunities for advanced technology exposure or higher earning potential. No specific international certifications exist, but vocational training and practical experience are universally valued.
Global Salaries
Salaries for Aluminum Pourers vary significantly by region, reflecting industrial output and cost of living. In North America, particularly the US and Canada, annual salaries range from $45,000 to $70,000 USD. Experienced pourers in unionized facilities may earn more. European countries like Germany and France offer €35,000 to €55,000 (approx. $38,000-$60,000 USD), with strong social benefits packages. Scandinavia often provides higher wages but also faces a higher cost of living.
In Asia-Pacific, specifically Australia, salaries can be $50,000 to $75,000 AUD (approx. $33,000-$50,000 USD). However, China and India, while major producers, generally have lower nominal wages for this role, though purchasing power might be comparable locally. Latin American countries like Brazil or Mexico typically offer $15,000 to $30,000 USD equivalent. These figures reflect base pay; overtime and shift differentials often increase take-home pay, particularly in regions with high industrial demand.
Benefit structures differ widely. North America might offer private health insurance and 401k plans, while Europe emphasizes public healthcare and generous vacation time. Taxes also vary, impacting net income. Experience directly affects compensation, as skilled pourers minimize waste and ensure quality. No international pay scales standardize this role, but industry demand drives regional remuneration.
Remote Work
International remote work opportunities for an Aluminum Pourer are virtually nonexistent. This role requires direct, hands-on interaction with molten metal and heavy machinery within a manufacturing facility. The core duties cannot be performed off-site. Digital nomad lifestyles are not compatible with this profession due to its physical and location-specific nature.
Some related roles, such as quality control or supervisory positions within the metals industry, might offer limited hybrid or remote administrative tasks. However, the pourer's specific skill set is tied to the physical production line. Companies hiring for this field exclusively seek on-site personnel. Therefore, geographic arbitrage or international remote work policies are not applicable to the Aluminum Pourer position itself.
Visa & Immigration
For Aluminum Pourers seeking international work, skilled worker visas are the primary pathway. Countries like Canada, Australia, and Germany have specific programs for trades and skilled manufacturing roles. Requirements typically include proof of vocational training or extensive experience, often five years or more. Some nations may require a job offer from an employer before visa application.
Education credential recognition for this specific trade is less complex than for professional degrees but practical assessments may occur. Language requirements vary; for instance, German proficiency aids employment in Germany, while English is standard for Canada or Australia. Visa processing times range from several months to over a year, depending on the country and visa type. Employers often sponsor these visas, simplifying the process.
Pathways to permanent residency exist in many countries for skilled workers after a period of employment. Family visas are usually available for spouses and dependents. No profession-specific fast-track programs are common for Aluminum Pourers. Practical considerations include adapting to new safety standards and workplace cultures. A clean criminal record is essential for all immigration applications.
2025 Market Reality for Aluminum Pourers
Understanding current market conditions is vital for aluminum pourers. The industry has seen considerable shifts from 2023 to 2025, influenced by post-pandemic supply chain adjustments and the ongoing push for automation. Broader economic factors, such as manufacturing output and material costs, directly impact job availability and stability in this specialized field.
Market realities for pourers vary significantly by experience level, as seasoned professionals are often in higher demand for complex operations. Geographic location, particularly proximity to major foundries and manufacturing hubs, also plays a critical role. Company size matters too; larger operations might offer more consistent work, while smaller custom shops may have specialized needs. This analysis provides an honest assessment of current market realities for aluminum pourers.
Current Challenges
Aluminum pourers face significant challenges from automation and increased demand for efficiency. Foundries seek highly skilled operators, limiting entry-level roles. Economic slowdowns directly impact manufacturing output, reducing available pouring shifts.
Competition for stable, well-paying positions remains high, especially for those with experience. Safety regulations are stricter, requiring continuous training and adherence, which can be demanding. Timelines for securing roles can extend as employers thoroughly vet candidates for precision and reliability.
Growth Opportunities
Despite automation, strong opportunities exist for aluminum pourers specializing in complex or high-precision casting. Foundries that produce specialized alloys or intricate components still rely heavily on skilled manual pourers. Roles focused on quality control, material analysis, and operating advanced pouring machinery are emerging as growth areas.
Pourers who can demonstrate proficiency in reading technical specifications, understanding metallurgical reactions, and operating robotic assists gain a significant competitive edge. Opportunities are strong in sectors like defense manufacturing, custom art foundries, and high-performance automotive parts. These areas require a level of precision and adaptability that automation has not fully replicated yet. Investing in certifications for advanced material handling or quality assurance can open new doors. Strategic career moves might involve targeting companies that prioritize custom work over mass production, or those heavily involved in emerging technologies requiring unique metal compositions.
Current Market Trends
Hiring for aluminum pourers shows stable demand, particularly in regions with strong automotive, aerospace, and construction sectors. Foundries are investing in modernization, impacting the specific skills required from pourers. Manual pouring roles are increasingly supported by robotic systems, shifting pourers' duties towards oversight and precision finishing rather than purely physical labor.
Economic conditions directly influence metal production. A robust manufacturing sector drives higher demand for pourers, while downturns lead to reduced shifts or temporary layoffs. Generative AI and automation are not directly replacing pourers but are enhancing quality control and material handling processes, making precision and adaptability crucial for pourers. Employers now seek pourers with a keen eye for detail, understanding of metallurgical properties, and the ability to work with advanced monitoring equipment. Salary trends for experienced pourers remain competitive, but entry-level wages can be stagnant due to the availability of automated alternatives. Geographic variations are significant; states with large industrial bases like Michigan, Ohio, and Alabama have more consistent opportunities. Seasonal patterns are less pronounced, but demand can fluctuate with major industrial contracts or economic cycles.
Emerging Specializations
The field of aluminum pouring is undergoing a quiet but significant transformation, driven by advancements in material science, automation, and environmental regulations. These changes are creating novel specialization opportunities beyond traditional pouring techniques. Understanding these emerging areas allows professionals to strategically position themselves for career advancement in 2025 and beyond.
Early positioning in these future-oriented specializations often leads to premium compensation and accelerated career growth. As new technologies become industry standards, those with specialized skills will be highly sought after. While established pouring methods remain crucial, a balanced approach involves recognizing the potential of emerging areas for long-term career resilience.
Many emerging areas, particularly those involving advanced robotics or specialized alloys, are currently gaining traction and will likely become mainstream within the next five to ten years, creating substantial job opportunities. Pursuing these cutting-edge specializations involves a calculated risk, as some technologies may evolve differently than anticipated. However, the potential for significant professional reward and leadership in a transforming industry often outweighs these considerations.
Embracing these shifts allows aluminum pourers to evolve their expertise, moving into roles that demand higher technical proficiency and problem-solving capabilities. This strategic adaptation ensures continued relevance and opens doors to innovative processes and materials that define the future of metal casting.
Automated Pouring Systems Operator
As the industry moves towards greater efficiency and safety, robotic pouring systems are becoming more prevalent. This specialization involves programming, calibrating, and overseeing automated pouring robots to achieve precise and consistent metal flow. Professionals in this area ensure optimal performance, troubleshoot technical issues, and integrate robotic systems with overall production lines. It requires a deep understanding of both metallurgy and robotic operation to maintain high-quality outputs.
Specialty Alloy Pouring Technician
The demand for lightweight and high-strength aluminum alloys in aerospace and automotive industries is rising. This specialization focuses on pouring advanced, custom-blended aluminum alloys with specific properties, such as those with enhanced heat resistance or superior tensile strength. It requires meticulous control over temperature, purity, and pouring speed to meet stringent material specifications. Understanding the unique characteristics of each alloy and its application is critical.
Eco-Conscious Pouring Specialist
Sustainability and resource efficiency are driving the demand for specialized pouring techniques that minimize waste and maximize material recovery. This involves optimizing pouring processes to reduce dross formation, minimize scrap, and efficiently utilize recycled aluminum. Professionals in this area implement lean manufacturing principles, analyze material flow, and develop innovative methods for more environmentally responsible casting. They ensure compliance with evolving environmental regulations.
Digital Pouring Process Analyst
The integration of digital twins and real-time data analytics is revolutionizing manufacturing processes. This specialization involves utilizing sensors and software to monitor pouring parameters in real-time, creating digital models of the pouring process. Professionals analyze this data to predict defects, optimize flow rates, and ensure consistent quality. They leverage data insights to make proactive adjustments and improve overall operational efficiency. This requires strong analytical and technical skills.
In-Process Quality Assurance Pourer
With increasing quality demands, particularly in critical applications, advanced inspection and non-destructive testing (NDT) methods are integrated directly into the pouring workflow. This specialization focuses on implementing and interpreting real-time NDT techniques, such as ultrasonic testing or thermal imaging, during or immediately after the pour. Professionals ensure structural integrity and detect internal defects instantaneously, preventing costly rework. This requires a keen eye for detail and understanding of testing equipment.
Pros & Cons of Being an Aluminum Pourer
Making an informed career decision requires understanding both the positive aspects and the inherent challenges of a profession. The experience of an aluminum pourer, like many specialized roles, can vary significantly based on the specific company, the type of foundry, and individual personality. Factors such as company culture, safety standards, and the level of automation in a facility greatly influence daily work life. Additionally, the pros and cons may evolve at different career stages; for instance, initial physical demands might be more pronounced for new entrants, while experienced pourers might focus more on precision and efficiency. What one person considers a benefit, such as a predictable routine, another might view as a drawback, like repetitive tasks. This assessment provides an honest, balanced perspective to help set realistic expectations for this demanding but essential role.
Pros
- Aluminum pourers often earn a competitive hourly wage, reflecting the specialized skills, physical demands, and hazardous nature of working with molten metals, often including overtime opportunities.
- There is a consistent demand for skilled aluminum pourers in manufacturing and industrial sectors, providing good job security for those with the necessary expertise and experience.
- The role provides a clear, tangible sense of accomplishment, as pourers directly contribute to the creation of essential metal products from raw materials, seeing the immediate result of their work.
- The work environment fosters strong camaraderie among colleagues due to the team-oriented nature of foundry operations and the shared experience of working in challenging conditions.
- Entry into this career often does not require an advanced degree; instead, it relies on on-the-job training, apprenticeships, and vocational certifications, making it accessible to individuals seeking direct employment.
- Pourers develop a highly specialized skill set in metallurgy, temperature control, and material handling, which is valuable and not easily automated, ensuring the ongoing relevance of the role.
- Many foundries offer comprehensive benefits packages, including health insurance, retirement plans, and paid time off, which are attractive given the nature of industrial work.
Cons
- Working in an aluminum foundry exposes pourers to extreme heat, often exceeding 100 degrees Fahrenheit, which creates a physically demanding and uncomfortable environment.
- Aluminum pourers face significant safety risks from molten metal splashes, intense radiant heat, and potential burns, necessitating constant vigilance and strict adherence to safety protocols.
- The work involves repetitive physical tasks, such as lifting ladles and manipulating pouring mechanisms, which can lead to musculoskeletal strain and fatigue over time.
- Exposure to fumes and particulate matter from the melting process, even with ventilation, poses long-term respiratory health concerns for workers in this environment.
- Shift work, including nights and weekends, is common in foundry operations to maintain continuous production, which can disrupt personal life and sleep patterns.
- The job requires a high degree of focus and precision, as errors in pouring can lead to defective products, safety incidents, or significant material waste, adding mental pressure.
- Career progression for an aluminum pourer within the foundry often requires cross-training into other specialized roles or moving into supervisory positions, which may not always be readily available or desired by all individuals, limiting vertical mobility in the pouring specific role itself, though horizontal mobility within the foundry is common and often encouraged to train in different areas like casting or furnace operation.
Frequently Asked Questions
Aluminum Pourers face unique challenges balancing precision with intense heat and safety protocols. This section addresses the most common questions about entering this demanding role, from mastering the pouring process to understanding the physical requirements and safety measures in a foundry environment.
What qualifications or experience do I need to become an Aluminum Pourer?
Entry-level Aluminum Pourer positions usually require a high school diploma or GED. Employers prioritize candidates with a strong work ethic, attention to detail, and a commitment to safety. While not always mandatory, prior experience in manufacturing, construction, or any role involving heavy machinery or hot materials can be a significant advantage. Some employers may offer apprenticeships or on-the-job training programs.
How long does it take to become competent enough to work independently as an Aluminum Pourer?
Becoming proficient as an Aluminum Pourer typically involves several months of intensive on-the-job training under experienced supervisors. This period focuses on mastering pouring techniques, understanding metal properties, and rigorously adhering to safety protocols. While you can start earning relatively quickly, achieving a high level of skill and independence in handling molten metal can take 6-12 months or more of continuous practice and learning.
What are the typical working conditions and physical demands of an Aluminum Pourer role?
The work environment for an Aluminum Pourer is characterized by extreme heat, noise, and potential hazards. You will consistently work near furnaces and molten metal, requiring constant vigilance and strict adherence to safety procedures, including wearing extensive personal protective equipment (PPE). The job demands significant physical stamina, as it involves standing for long periods, lifting, and repetitive movements in a hot, industrial setting.
What are the salary expectations for an entry-level and experienced Aluminum Pourer?
Aluminum Pourers typically earn competitive wages, reflecting the demanding nature and specialized skills required for the role. Entry-level salaries might start in the range of $35,000 to $45,000 annually. With experience, specialized skills, and increased responsibility, experienced pourers can earn $50,000 to $65,000 or more, especially with overtime or shift differentials. Geographic location and the specific company also influence pay rates.
How does the Aluminum Pourer role impact work-life balance, especially with shift work?
The work-life balance for an Aluminum Pourer can vary. Many foundries operate on shifts, including nights and weekends, to maintain continuous production, which can impact personal scheduling. Overtime is often available, which can boost earnings but also extend working hours. While the job is physically demanding during shifts, companies generally ensure proper breaks and adherence to labor laws to prevent burnout.
What are the potential career advancement opportunities for an Aluminum Pourer?
Career growth for an Aluminum Pourer often involves advancing to lead pourer, supervisor, or foreman roles within the foundry. Opportunities also exist to specialize in quality control, metallurgy, or safety management, leveraging your direct experience with molten metal. Some pourers transition into equipment maintenance or training roles, sharing their expertise with new hires. Continuous learning and a strong safety record are key to advancement.
How significant are the safety risks, and what measures are in place to protect Aluminum Pourers?
Safety is paramount for an Aluminum Pourer. Foundries implement rigorous safety protocols, including extensive training on PPE usage, emergency procedures, and safe handling of molten materials. You will learn to identify and mitigate risks associated with heat, fumes, and splashes. Adhering to these strict rules and maintaining constant awareness is crucial for your personal safety and the safety of your colleagues in this high-risk environment.
Related Careers
Explore similar roles that might align with your interests and skills:
Ingot Caster
A growing field with similar skill requirements and career progression opportunities.
Explore career guideIron Pourer
A growing field with similar skill requirements and career progression opportunities.
Explore career guideMolten Iron Pourer
A growing field with similar skill requirements and career progression opportunities.
Explore career guideSteel Pourer
A growing field with similar skill requirements and career progression opportunities.
Explore career guideTin Pourer
A growing field with similar skill requirements and career progression opportunities.
Explore career guideAssess your Aluminum Pourer readiness
Understanding where you stand today is the first step toward your career goals. Our Career Coach helps identify skill gaps and create personalized plans.
Skills Gap Analysis
Get a detailed assessment of your current skills versus Aluminum Pourer requirements. Our AI Career Coach identifies specific areas for improvement with personalized recommendations.
See your skills gapCareer Readiness Assessment
Evaluate your overall readiness for Aluminum Pourer roles with our AI Career Coach. Receive personalized recommendations for education, projects, and experience to boost your competitiveness.
Assess your readinessSimple pricing, powerful features
Upgrade to Himalayas Plus and turbocharge your job search.
Himalayas
Himalayas Plus
Himalayas Max
Find your dream job
Sign up now and join over 100,000 remote workers who receive personalized job alerts, curated job matches, and more for free!
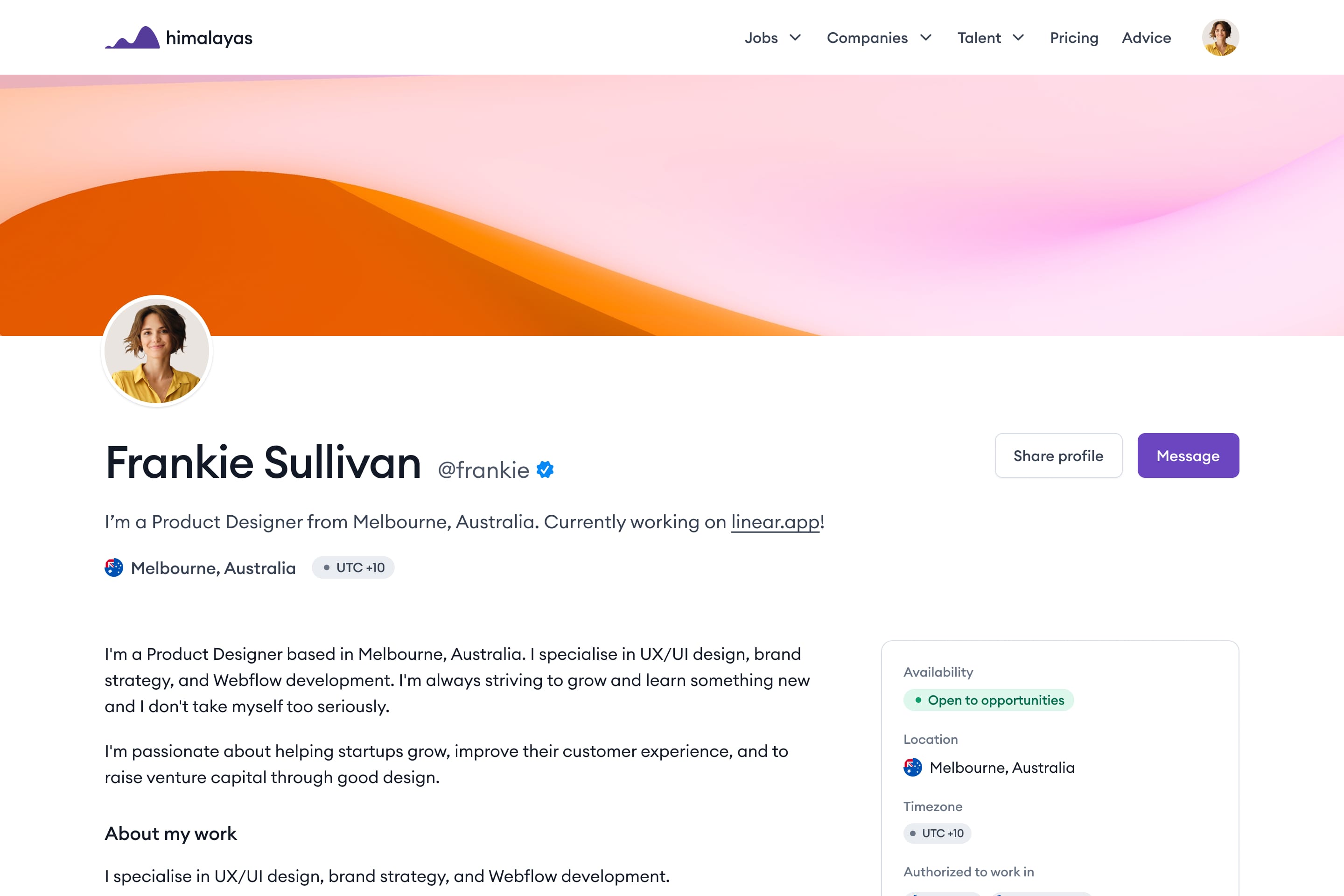