Complete Ingot Caster Career Guide
Ingot casters play a crucial role in foundational industries, transforming molten metal into solid ingots—the raw material for countless products. This precise work requires deep knowledge of metallurgy and careful operation of specialized machinery, ensuring quality and structural integrity from the very first pour. It's a hands-on career vital for manufacturing, offering stable opportunities for those who master its unique demands.
Key Facts & Statistics
Median Salary
$52,260 USD
(U.S. national median, BLS, May 2023)
Range: $35k - $70k+ USD (BLS, May 2023)
Growth Outlook
1%
slower than average (BLS, 2022-2032)
Annual Openings
≈200
openings annually (BLS, 2022-2032)
Top Industries
Typical Education
High school diploma or equivalent, with significant on-the-job training or apprenticeship
What is an Ingot Caster?
An Ingot Caster is a skilled industrial professional responsible for transforming molten metal into solid, standardized blocks called ingots. These ingots serve as the foundational raw material for further processing in various manufacturing industries, including steel production, aluminum fabrication, and non-ferrous metal refining.
This role demands precision, an acute understanding of metallurgy, and strict adherence to safety protocols. Unlike a general foundry worker who might handle various casting processes, an Ingot Caster specializes specifically in the controlled pouring and solidification of metal into uniform ingot shapes, ensuring the purity and structural integrity required for subsequent manufacturing stages.
What does an Ingot Caster do?
Key Responsibilities
- Operate and monitor melting furnaces, ensuring proper temperature and metal composition for casting.
- Pour molten metal into ingot molds, carefully controlling the flow rate and fill level to prevent defects.
- Skim dross and impurities from the surface of molten metal, maintaining the purity of the final product.
- Inspect newly cast ingots for surface defects, cracks, and proper dimensions, marking any that do not meet quality standards.
- Maintain and clean casting equipment, including molds, ladles, and pouring spouts, to ensure efficient operation and product quality.
- Record production data, including melt temperatures, pour times, and ingot weights, for quality control and inventory management.
- Adhere strictly to safety protocols, wearing appropriate personal protective equipment and following lockout/tagout procedures for machinery maintenance and operation, handling molten metal safely.
Work Environment
Ingot casters work in a demanding industrial environment, typically within foundries, steel mills, or metal production plants. The workspace is often hot, noisy, and dusty due to the presence of molten metal, heavy machinery, and metal dust.
Collaboration with furnace operators, metallurgists, and quality control technicians is common. The work schedule often involves shifts, including nights and weekends, to maintain continuous production. The pace is steady and highly focused on safety and precision, as errors with molten metal can be dangerous and costly. This role requires significant physical stamina and a strong commitment to safety protocols.
Tools & Technologies
Ingot casters primarily use heavy industrial equipment. This includes induction or arc furnaces for melting metals, large ladles for transferring molten material, and various types of ingot molds (e.g., open-top, closed-bottom, split) made from cast iron or steel. They also utilize specialized tools such as skimmers, rakes, and temperature probes to manage the molten metal.
Personal protective equipment (PPE) like heat-resistant suits, gloves, safety glasses, and hard hats are essential. While the core process is traditional, some modern facilities might incorporate automated pouring systems or digital temperature monitoring tools, but manual skill remains paramount.
Ingot Caster Skills & Qualifications
Becoming an Ingot Caster involves a specialized blend of hands-on technical ability and adherence to strict safety protocols. This role is fundamental in primary metals production, directly impacting the quality and integrity of raw material ingots. Qualification structures for this position prioritize practical experience and a strong understanding of metallurgical processes over purely academic credentials.
Requirements for Ingot Casters vary by the type of metal being cast (e.g., steel, aluminum, copper), the scale of the operation, and the specific casting method employed (e.g., continuous casting, vacuum casting). Larger foundries or mills often have more formalized training programs and stricter certification requirements, while smaller operations might rely more on on-the-job training. Seniority levels dictate increasing responsibility for process optimization, troubleshooting, and potentially supervising junior casters. Entry-level positions typically require a foundational understanding of safety and basic casting principles, progressing to advanced roles that demand deep expertise in alloy properties and defect analysis.
Formal education provides a valuable theoretical foundation, but practical experience within a foundry or heavy industry environment is paramount. Many successful Ingot Casters begin as production assistants or laborers and advance through apprenticeships or internal training programs. Industry-specific certifications in areas like metallurgy, non-destructive testing, or specialized equipment operation significantly enhance a candidate's profile. The skill landscape is evolving with automation and advanced material science, requiring casters to increasingly understand automated systems and data interpretation alongside traditional manual skills. Balancing traditional casting expertise with an aptitude for new technologies is crucial for career longevity in this field.
Education Requirements
Technical Skills
- Molten Metal Handling and Pouring Techniques
- Temperature Monitoring and Control Systems (e.g., pyrometers, thermocouples)
- Mold Preparation and Maintenance (e.g., coating, preheating, cleaning)
- Furnace Operation and Tapping Procedures
- Alloy Composition and Material Properties Knowledge
- Non-Destructive Testing (NDT) Basics (e.g., visual inspection, basic defect identification)
- Overhead Crane and Forklift Operation (certification often required)
- Safety Protocols and Personal Protective Equipment (PPE) Usage
- Basic Mechanical Troubleshooting and Equipment Maintenance
- Data Logging and Production Record Keeping
Soft Skills
- Attention to Detail: Critical for monitoring temperature, flow rates, and mold conditions to prevent defects in ingots.
- Safety Consciousness: Essential for operating heavy machinery, handling molten metal, and adhering to strict safety regulations in a high-risk environment.
- Problem-Solving: Important for quickly diagnosing and resolving issues during the casting process, such as mold failures or metal flow inconsistencies.
- Team Collaboration: Necessary for coordinating with crane operators, furnace tenders, and quality control personnel to ensure a smooth and efficient casting operation.
- Physical Stamina and Dexterity: Required for standing for long periods, handling tools, and performing precise movements in a physically demanding and often hot environment.
- Adaptability: Crucial for adjusting to changing production schedules, material specifications, and unexpected equipment malfunctions.
How to Become an Ingot Caster
Becoming an Ingot Caster involves a blend of hands-on skill, safety adherence, and a deep understanding of metallurgy. While traditional pathways often involve vocational training or apprenticeships, some individuals enter through entry-level roles within foundries and work their way up. The timeline for entry can range from a few months for those with prior manufacturing experience to over a year for complete beginners who require foundational training.
Entry strategies vary significantly by industry and company size. Large industrial operations may prefer candidates with formal certifications or extensive safety training, while smaller foundries might prioritize practical experience and a strong work ethic. Geographic location also plays a role; areas with a high concentration of manufacturing or metal processing industries will offer more opportunities. Breaking into this field often requires demonstrating reliability, a commitment to safety, and a willingness to learn on the job.
A common misconception is that this role is purely manual labor; in reality, it demands precision, attention to detail, and the ability to operate sophisticated machinery. Networking within local manufacturing communities, attending industry job fairs, and connecting with experienced casters can open doors. The hiring landscape values practical skills and a proven safety record above all else. Overcoming barriers to entry typically involves acquiring basic industrial skills and showing a strong aptitude for working in a physically demanding environment.
Step 1
Step 2
Step 3
Step 4
Step 5
Step 6
Step 7
Education & Training Needed to Become an Ingot Caster
Becoming an Ingot Caster primarily involves hands-on training and vocational education rather than traditional four-year degrees. Formal university degrees are generally not required or even beneficial for this specific role. Most Ingot Casters learn through apprenticeships or on-the-job training programs offered by foundries or metal production facilities. These pathways provide the essential practical skills and safety knowledge required for handling molten metal and operating casting machinery.
Vocational programs and certifications in metallurgy or foundry technology can significantly enhance a candidate's prospects. These programs typically range from 6 months to 2 years and can cost between $5,000 and $20,000. They cover topics like metal properties, casting processes, quality control, and industrial safety. While self-study can provide theoretical knowledge, the critical hands-on experience is irreplaceable. Employers highly value practical experience and certifications demonstrating competence in foundry operations and safety protocols.
Continuous learning in this field focuses on new casting techniques, material science advancements, and updated safety regulations. Professional development often involves specialized workshops or internal company training. The educational needs for an Ingot Caster are highly specific to the physical processes of metal casting, emphasizing practical skill over theoretical academic knowledge. Cost-benefit considerations favor direct vocational training or apprenticeships, which offer immediate skill acquisition and employment pathways, over more expensive and less relevant academic degrees.
Ingot Caster Salary & Outlook
Compensation for an Ingot Caster varies significantly based on several key factors beyond just base salary. Geographic location plays a crucial role, with higher wages often found in regions with strong heavy manufacturing or specialized metals industries, reflecting local cost of living and specific demand for skilled trades. Areas with major steel mills or aluminum smelters, for instance, generally offer better pay.
Years of experience dramatically impact earning potential. An Apprentice Ingot Caster starts at a foundational wage, which increases as they gain proficiency and move into a full Ingot Caster role. Specialization in certain metal types, like aerospace-grade alloys or rare earth metals, can also command higher compensation due to the precision and knowledge required.
Total compensation packages extend beyond hourly wages. These often include overtime pay, which can significantly boost annual earnings given the shift-based nature of foundry work. Benefits such as health insurance, retirement contributions like 401(k)s, and paid time off are standard. Some companies may offer performance bonuses tied to production targets or safety records.
Industry-specific trends, such as demand for new alloys or fluctuations in raw material prices, influence overall company profitability and, consequently, salary growth. Larger companies or those with advanced casting technologies may offer more competitive wages and benefits. Remote work is not applicable to this hands-on role; however, the stability of the manufacturing sector in a given area directly correlates with job security and pay.
Salary by Experience Level
Level | US Median | US Average |
---|---|---|
Apprentice Ingot Caster | $38k USD | $40k USD |
Ingot Caster | $52k USD | $55k USD |
Senior Ingot Caster | $65k USD | $68k USD |
Lead Ingot Caster | $75k USD | $78k USD |
Casting Supervisor | $90k USD | $95k USD |
Market Commentary
The job market for Ingot Casters remains stable, driven by continuous demand for primary metals in manufacturing, construction, and infrastructure development. While overall growth might not be rapid, the skilled nature of the work ensures consistent opportunities. Projections suggest a steady demand, particularly as older, experienced casters retire, creating openings for new talent.
Technological advancements in casting, such as automation in material handling and quality control systems, are influencing the role. Ingot Casters must increasingly adapt to operating and monitoring sophisticated machinery, rather than solely manual processes. This shift emphasizes skills in diagnostics, maintenance, and computer-aided manufacturing, future-proofing the profession against full automation.
Supply and demand dynamics show a consistent need for skilled tradespeople in heavy industry. There is often a shortage of properly trained and experienced casters, leading to competitive wages for qualified individuals. This imbalance means that those with specialized training or certifications in specific casting techniques or materials are highly sought after.
The profession's economic resilience is tied to the broader manufacturing sector. While sensitive to economic downturns, the fundamental need for raw metal products provides a baseline of stability. Geographic hotspots for Ingot Casters include the industrial Midwest, the Southeast, and parts of the Pacific Northwest in the United States, where major foundries and metal processing plants are concentrated. Continuous learning in new casting technologies and safety protocols is essential for career advancement.
Ingot Caster Career Path
Career progression for an Ingot Caster involves a clear path from foundational training to supervisory leadership, deeply rooted in hands-on experience and specialized knowledge of metallurgy and casting processes. Advancement often depends on demonstrating meticulous attention to detail, adherence to safety protocols, and a consistent ability to produce high-quality ingots. This field emphasizes practical skills over academic degrees, though certifications in safety, metallurgy, or specific casting technologies can accelerate progression.
Advancement typically occurs through an individual contributor (IC) track, where casters deepen their technical expertise and take on more complex casting operations. A management track emerges at the Lead Ingot Caster stage, where individuals begin overseeing teams and optimizing production. Company size and type significantly influence career paths; larger foundries or integrated steel mills offer more structured progression and specialized roles, while smaller operations might require a broader skill set.
Factors influencing advancement speed include consistent performance, a proactive approach to learning new casting techniques, and a strong safety record. Lateral moves often involve specializing in different metal alloys or casting methods, enhancing versatility within the broader metals industry. Networking within the foundry community, participating in industry safety seminars, and mentoring junior casters also contribute to reputation and open doors for leadership roles.
Apprentice Ingot Caster
0-2 yearsKey Focus Areas
Ingot Caster
2-5 years total experienceKey Focus Areas
Senior Ingot Caster
5-8 years total experienceKey Focus Areas
Lead Ingot Caster
8-12 years total experienceKey Focus Areas
Casting Supervisor
12+ years total experienceKey Focus Areas
Apprentice Ingot Caster
0-2 yearsOperate under direct supervision, assisting experienced casters with preparing molds, pouring molten metal, and cooling ingots. Responsibilities include cleaning equipment, transporting materials, and observing casting procedures. Decisions are limited to immediate task execution, with no independent authority.
Key Focus Areas
Develop a strong understanding of foundry safety regulations and material handling. Master basic casting techniques and equipment operation. Focus on precise measurement, temperature control, and mold preparation. Learn to identify and report common casting defects.
Ingot Caster
2-5 years total experiencePerform independent casting operations for standard ingots, adhering to strict quality and safety standards. Manage the pouring process, temperature regulation, and mold preparation with minimal oversight. Contribute to production schedules and ensure material availability.
Key Focus Areas
Refine skills in various casting methods and metal types. Develop problem-solving abilities for minor casting issues. Understand the properties of different alloys and their impact on casting. Focus on efficiency, waste reduction, and consistent quality output.
Senior Ingot Caster
5-8 years total experienceLead casting operations for specialized or high-value ingots, often involving unique alloys or intricate molds. Provide technical guidance to less experienced casters and troubleshoot complex casting issues. Take responsibility for quality assurance checks and process improvements on the casting line.
Key Focus Areas
Specialize in complex alloy casting or advanced molding techniques. Mentor junior casters, sharing best practices and troubleshooting guidance. Develop a deeper understanding of metallurgical principles and quality control processes. Focus on process optimization and defect prevention.
Lead Ingot Caster
8-12 years total experienceOversee a shift or a specific section of the casting floor, ensuring production targets are met efficiently and safely. Coordinate team members, assign tasks, and manage workflow. Responsible for daily operational decisions, quality control, and initial incident response.
Key Focus Areas
Develop leadership skills, including team coordination, scheduling, and performance monitoring. Focus on advanced process optimization, identifying bottlenecks and implementing solutions. Gain expertise in equipment maintenance scheduling and inventory management for casting materials.
Casting Supervisor
12+ years total experienceManage all aspects of the ingot casting department, including personnel, equipment, safety, and production targets. Develop and implement operational strategies to enhance efficiency, reduce costs, and improve product quality. Responsible for budgeting, training, and performance reviews for the entire casting team.
Key Focus Areas
Cultivate strategic planning skills for long-term production goals and resource allocation. Master team management, conflict resolution, and continuous improvement methodologies. Develop strong communication skills for reporting to upper management and collaborating with other departments.
Job Application Toolkit
Ace your application with our purpose-built resources:
Global Ingot Caster Opportunities
An Ingot Caster's role involves pouring molten metal into molds, a critical step in primary metal production. This profession is fundamental to heavy industries globally, including steel, aluminum, and precious metals. Demand remains steady in industrialized nations and emerging economies, driven by infrastructure and manufacturing needs. Regulatory differences impact safety standards and environmental compliance across regions. Professionals consider international roles for specialized projects or better earning potential in resource-rich countries. No specific international certifications exist; experience and company-specific training are paramount.
Global Salaries
Global salaries for Ingot Casters vary significantly based on industry, company size, and country's economic development. In North America, particularly the United States, an Ingot Caster can expect to earn between $45,000 and $70,000 USD annually. Canadian salaries are comparable, ranging from $40,000 to $65,000 CAD ($30,000-$50,000 USD). These figures often include comprehensive benefits like health insurance, retirement plans, and paid vacation.
In Europe, salaries differ widely. In Germany, an Ingot Caster might earn €35,000 to €55,000 ($38,000-$60,000 USD), often with strong union protections and benefits. The UK offers £28,000 to £45,000 ($35,000-$57,000 USD). Eastern European countries, like Poland, offer lower wages, typically €15,000 to €25,000 ($16,000-$27,000 USD), but with a lower cost of living. Purchasing power parity ensures that even lower nominal wages can provide a decent standard of living in these regions.
Asia-Pacific markets present diverse compensation. In Australia, salaries range from AUD $60,000 to $85,000 ($40,000-$57,000 USD), often with generous superannuation (pension) contributions. China's manufacturing hubs offer RMB 80,000 to 150,000 ($11,000-$21,000 USD), often with company-provided housing or subsidies. India's salaries are lower, typically INR 250,000 to 500,000 ($3,000-$6,000 USD), reflecting a much lower cost of living.
Latin American countries like Brazil might offer BRL 30,000 to 60,000 ($6,000-$12,000 USD). Tax implications and take-home pay vary significantly; some countries have higher social security contributions, impacting net income. Experience and specialized skills in casting rare metals or specific alloys can command higher compensation globally. International pay scales are not standardized; individual company policies and local labor laws dictate remuneration.
Remote Work
International remote work opportunities for an Ingot Caster are virtually non-existent. This role is inherently hands-on, requiring direct presence in a foundry or manufacturing plant to operate machinery and supervise casting processes. Physical proximity to molten metal and heavy equipment is always necessary.
Digital nomad lifestyles or working from different countries are not applicable to this profession. The nature of the work, involving specialized industrial equipment and strict safety protocols, precludes any form of remote execution. Therefore, considerations for international remote work policies, time zone collaboration, or digital nomad visas do not apply to Ingot Casters.
All employment for an Ingot Caster requires on-site presence. Companies hiring in this field expect full-time, in-person commitment. This role does not involve tasks that can be performed off-site, such as data analysis or project management. Equipment requirements are industrial, not personal, further cementing the on-site necessity.
Visa & Immigration
Ingot Casters seeking international work typically apply for skilled worker visas. Popular destinations include Canada, Australia, Germany, and the United States, given their robust manufacturing sectors. Requirements usually involve a job offer from an employer in the destination country, demonstrating a need for the specific skill set.
Educational credential recognition is less critical for Ingot Casters than for licensed professions; practical experience and employer-specific training are more valued. Some countries may require proof of vocational training or apprenticeships. Visa timelines vary from a few months to over a year, depending on the country and visa type.
Canada's Express Entry system or Australia's skilled migration programs are common pathways, often requiring an English language test like IELTS. Germany's skilled immigration law may facilitate entry with a recognized vocational qualification and a job offer. The U.S. generally requires employer sponsorship for H-2B or other temporary worker visas.
Pathways to permanent residency or citizenship can exist after several years of continuous skilled employment, depending on the country's immigration policies. Family visas for spouses and dependents are generally available once the primary applicant secures a work visa. There are no specific fast-track programs unique to Ingot Casters; they follow general skilled worker immigration rules.
2025 Market Reality for Ingot Casters
Understanding current market conditions is critical for ingot casters. This insight helps professionals navigate a transforming industry and plan strategic career moves. The period from 2023 to 2025 has seen significant shifts, driven by post-pandemic supply chain adjustments and the accelerating impact of automation and AI.
Broader economic factors, such as industrial output and global trade, directly influence demand for raw materials like ingots. Market realities vary considerably by experience level, as advanced roles are more resilient to automation. Geographic location and the size of the foundry also play a large part in job availability. This analysis provides an honest assessment of these dynamics, setting realistic expectations for those in the field.
Current Challenges
Ingot casters face significant challenges from automation. Modern foundries increasingly use robotic systems, reducing manual labor demand. Competition remains high for fewer specialized roles, especially in regions with declining heavy industry.
Economic downturns directly affect manufacturing output, leading to reduced shifts or layoffs. Acquiring the precise skills for advanced casting machinery can also be difficult.
Growth Opportunities
Despite automation, specialized opportunities exist for ingot casters with advanced technical skills. Foundries need professionals who can operate, monitor, and maintain complex automated casting systems, including those integrated with AI for process optimization. Roles focused on quality control, material analysis, and troubleshooting advanced machinery are seeing increased demand.
Professionals can gain a competitive edge by pursuing certifications in industrial automation, robotics, or advanced materials science. Underserved markets, particularly in regions with growing aerospace or defense manufacturing, may offer more stable opportunities. Strategic career moves involve transitioning from manual casting to roles overseeing highly automated lines or specializing in niche metals like superalloys.
Investing in training for data analysis or predictive maintenance for casting equipment can also create significant advantages. Certain sectors, such as those producing high-performance alloys for specialized applications, remain robust. Timing educational investments to align with emerging technological needs can position casters for long-term success in this evolving field.
Current Market Trends
Hiring for ingot casters shows a steady decline in 2025, continuing a trend from 2023. Automation in foundries means fewer manual casting positions exist, with demand shifting towards operators of advanced machinery. Economic conditions, particularly in sectors like automotive and construction, directly influence metal demand and, consequently, casting activity.
The integration of AI in process control and quality assurance systems is transforming the role. Employers now seek casters with strong technical aptitude for monitoring and troubleshooting automated lines, rather than purely physical labor. Salary trends reflect this shift; highly skilled operators of advanced systems see stable wages, while traditional manual casting roles face wage stagnation due to reduced demand and increased competition.
Geographically, opportunities are concentrating in regions with specialized metal production or aerospace industries, while areas dependent on traditional manufacturing see significant reductions. Remote work is impossible for this hands-on role. Cyclical demand tied to industrial production schedules can also lead to seasonal fluctuations in hiring.
Emerging Specializations
The field of metal casting, particularly for ingot production, is experiencing significant transformation driven by advancements in materials science, automation, and sustainability. These technological shifts are creating entirely new specialization opportunities for ingot casters. Understanding these emerging areas allows professionals to strategically position themselves for career advancement in 2025 and beyond.
Early positioning in these cutting-edge specializations often leads to premium compensation and accelerated career growth. As new processes become standard, the demand for skilled professionals in these niche areas outpaces supply, creating a competitive advantage. While established casting methods remain vital, focusing on emerging areas offers a pathway to becoming an indispensable expert.
Many emerging areas, initially niche, typically transition to mainstream operations within three to five years, creating substantial job opportunities. Pursuing these specializations involves a balance of risk and reward. While requiring investment in new skills and knowledge, the potential for significant professional development and long-term career security in a transforming industry is considerable.
Advanced Microstructure Ingot Caster
Advanced ingot casting techniques are emerging, focusing on producing ingots with highly specific microstructures and enhanced mechanical properties for high-performance applications in aerospace and medical industries. This involves precise control over solidification rates, cooling curves, and atmospheric conditions within the casting environment. These methods move beyond traditional bulk material production, requiring a deeper understanding of metallurgical principles.
AI-Driven Process Optimization Caster
The integration of artificial intelligence and machine learning is revolutionizing ingot casting. This specialization involves developing and implementing AI models to predict and optimize casting parameters, detect defects in real-time, and enhance overall process efficiency. Ingot casters in this role work with data scientists to refine algorithms that improve yield, reduce waste, and ensure consistent quality, moving towards predictive manufacturing.
Sustainable Casting Specialist
Sustainability is a growing concern in metal production, leading to the emergence of specializations focused on eco-friendly casting. This involves optimizing energy consumption during melting and casting, minimizing material waste through improved yield, and implementing closed-loop recycling systems for metal scrap. Ingot casters in this area contribute directly to reducing the environmental footprint of metal manufacturing.
Additive Manufacturing Feedstock Caster
Additive manufacturing, particularly large-scale metal 3D printing, is influencing ingot production by requiring specialized ingots or preforms optimized for these new processes. This specialization focuses on casting metals with specific compositions, purities, and geometries that serve as feedstock for advanced additive manufacturing systems. It bridges traditional casting with future manufacturing paradigms.
Ultra-High Purity Ingot Production Specialist
The demand for ultra-high purity metals, essential for semiconductor, electronics, and specialized medical device industries, is creating a distinct specialization. This involves stringent control over impurities, vacuum melting techniques, and specialized casting environments to produce ingots with impurity levels measured in parts per billion. This area requires meticulous attention to detail and advanced contamination control.
Pros & Cons of Being an Ingot Caster
Making a career choice requires a thorough understanding of both the positive aspects and the inherent difficulties. Career experiences can vary significantly based on company culture, the specific industry sector, your area of specialization, and individual preferences or personality. The pros and cons of a role like Ingot Caster may also shift at different career stages, from early entry to more senior levels. What one person considers a benefit, another might see as a challenge, depending on their personal values and lifestyle preferences. This assessment aims to provide an honest, balanced perspective to help you approach this career path with realistic expectations.
Pros
- Ingot Casters often earn competitive wages, especially in unionized plants or facilities with high demand for their specialized skills, providing a stable income. Job security tends to be strong in the metals industry, as the foundational demand for raw metal ingots remains consistent across manufacturing and construction sectors. This role provides a clear, hands-on opportunity to work with fundamental industrial processes, offering a sense of tangible accomplishment in producing essential materials. Training for an Ingot Caster is typically provided on-the-job, often through apprenticeships, which allows entry into the field without requiring a four-year degree or significant upfront educational costs. The work often involves a strong team environment, as successful casting operations rely heavily on coordinated efforts and communication among crew members. For individuals who enjoy physical work and operating heavy machinery, the daily tasks of an Ingot Caster can be engaging and satisfying. Directly contributing to the initial stage of metal production means playing a vital role in the supply chain for numerous industries, offering a sense of importance and contribution.
- Ingot Casters often earn competitive wages, especially in unionized plants or facilities with high demand for their specialized skills, providing a stable income.
- Job security tends to be strong in the metals industry, as the foundational demand for raw metal ingots remains consistent across manufacturing and construction sectors.
- This role provides a clear, hands-on opportunity to work with fundamental industrial processes, offering a sense of tangible accomplishment in producing essential materials.
- Training for an Ingot Caster is typically provided on-the-job, often through apprenticeships, which allows entry into the field without requiring a four-year degree or significant upfront educational costs.
- The work often involves a strong team environment, as successful casting operations rely heavily on coordinated efforts and communication among crew members.
- For individuals who enjoy physical work and operating heavy machinery, the daily tasks of an Ingot Caster can be engaging and satisfying.
Cons
- The work environment for an Ingot Caster is often extremely hot, noisy, and dirty, requiring constant exposure to molten metal and heavy machinery. This can lead to physical discomfort and potential long-term health issues if proper safety protocols are not strictly followed. The job involves significant physical demands, including standing for long periods, lifting heavy tools, and operating equipment in high-temperature conditions, which can be physically exhausting. Ingot Casters typically work in shifts, which often include nights, weekends, and holidays, disrupting personal life and making it challenging to maintain a consistent schedule. Safety risks are inherent in working with molten metal and heavy industrial equipment; despite stringent precautions, accidents can occur, leading to serious injuries. The work can be highly repetitive and monotonous, as the core tasks of pouring, cooling, and handling ingots remain largely consistent, which may not appeal to those seeking varied intellectual challenges. Career advancement opportunities for an Ingot Caster within the casting plant might be limited without further specialized training or moving into supervisory or engineering roles. Exposure to fumes and particulates from the casting process, even with ventilation, can pose respiratory risks over time, emphasizing the need for diligent use of personal protective equipment.
- The work environment for an Ingot Caster is often extremely hot, noisy, and dirty, requiring constant exposure to molten metal and heavy machinery. This can lead to physical discomfort and potential long-term health issues if proper safety protocols are not strictly followed.
- The job involves significant physical demands, including standing for long periods, lifting heavy tools, and operating equipment in high-temperature conditions, which can be physically exhausting.
- Ingot Casters typically work in shifts, which often include nights, weekends, and holidays, disrupting personal life and making it challenging to maintain a consistent schedule.
- Safety risks are inherent in working with molten metal and heavy industrial equipment; despite stringent precautions, accidents can occur, leading to serious injuries.
- The work can be highly repetitive and monotonous, as the core tasks of pouring, cooling, and handling ingots remain largely consistent, which may not appeal to those seeking varied intellectual challenges.
- Career advancement opportunities for an Ingot Caster within the casting plant might be limited without further specialized training or moving into supervisory or engineering roles.
Frequently Asked Questions
Ingot Casters face unique challenges balancing precision with safety in extreme environments. This section addresses the most common questions about entering this specialized role, from mastering the casting process to managing the demanding physical and environmental conditions.
What are the basic educational and experience requirements to become an Ingot Caster?
Entry into an Ingot Caster role typically requires a high school diploma or GED. Many employers prefer candidates with vocational training in metallurgy, welding, or industrial manufacturing. Practical experience in a heavy industrial setting, even in a different capacity, can significantly strengthen your application. Specific certifications in safety protocols, such as OSHA, are also highly valued.
How long does it take to become a skilled Ingot Caster, and what does the training involve?
The path to becoming a proficient Ingot Caster usually involves on-the-job training and apprenticeships, which can last from several months to a couple of years. During this period, you learn the intricacies of metal pouring, temperature control, mold preparation, and safety procedures under the guidance of experienced casters. The speed of progression depends on your aptitude and the complexity of the casting operations.
What are the typical working conditions and physical demands of an Ingot Caster?
Ingot Casters work in hot, noisy, and potentially hazardous environments due to molten metal and heavy machinery. Expect shifts that may include nights, weekends, and holidays, as casting operations often run continuously. The work is physically demanding, requiring strength, stamina, and the ability to stand for long periods while wearing extensive personal protective equipment. Safety is paramount, and strict adherence to protocols is essential.
What are the salary expectations for an Ingot Caster, both entry-level and experienced?
Starting salaries for Ingot Casters vary by region and company, but typically range from $35,000 to $50,000 annually. With experience, specialized skills, and supervisory roles, earnings can increase significantly, often reaching $60,000 to $80,000 or more. Overtime opportunities are common due to the nature of continuous operations, which can boost overall income.
What are the long-term career growth and advancement opportunities for an Ingot Caster?
Career growth for an Ingot Caster often involves moving into supervisory roles, such as Lead Caster or Shift Supervisor, overseeing casting teams and operations. Opportunities also exist to specialize in quality control, process improvement, or even move into maintenance or engineering support roles within the plant. Continuous learning about new casting technologies and materials can open further advancement paths.
Is the Ingot Caster role secure, or is it at risk from automation?
The demand for Ingot Casters is tied to the manufacturing and metals industries. While some automation is increasing, skilled casters remain crucial for quality control and problem-solving in complex casting processes. Job security is generally stable in established metal production facilities, though it can fluctuate with economic cycles impacting industrial output. Specialization in rare or high-value metals can also enhance job security.
What are the main safety risks involved, and how are they managed in this role?
The primary safety concerns include burns from molten metal, heat stress, exposure to fumes, and risks from heavy machinery. Companies implement rigorous safety protocols, including mandatory personal protective equipment (PPE) like fire-resistant clothing, helmets, and specialized footwear. Regular safety training, emergency procedures, and strict adherence to operational guidelines are critical to mitigating these risks effectively.
How transferable are the skills learned as an Ingot Caster to other industries or roles?
While the core skills of an Ingot Caster are highly specialized and often location-dependent on casting plants, there is some transferability. The discipline, precision, and understanding of material properties gained can be valuable in other heavy industrial or manufacturing roles, such as welding, fabrication, or quality assurance in a related industry. However, direct remote work is not feasible for this hands-on position.
Related Careers
Explore similar roles that might align with your interests and skills:
Aluminum Pourer
A growing field with similar skill requirements and career progression opportunities.
Explore career guideFoundry Molder
A growing field with similar skill requirements and career progression opportunities.
Explore career guideIron Pourer
A growing field with similar skill requirements and career progression opportunities.
Explore career guideMolten Iron Pourer
A growing field with similar skill requirements and career progression opportunities.
Explore career guideWhite Metal Caster
A growing field with similar skill requirements and career progression opportunities.
Explore career guideAssess your Ingot Caster readiness
Understanding where you stand today is the first step toward your career goals. Our Career Coach helps identify skill gaps and create personalized plans.
Skills Gap Analysis
Get a detailed assessment of your current skills versus Ingot Caster requirements. Our AI Career Coach identifies specific areas for improvement with personalized recommendations.
See your skills gapCareer Readiness Assessment
Evaluate your overall readiness for Ingot Caster roles with our AI Career Coach. Receive personalized recommendations for education, projects, and experience to boost your competitiveness.
Assess your readinessSimple pricing, powerful features
Upgrade to Himalayas Plus and turbocharge your job search.
Himalayas
Himalayas Plus
Himalayas Max
Find your dream job
Sign up now and join over 100,000 remote workers who receive personalized job alerts, curated job matches, and more for free!
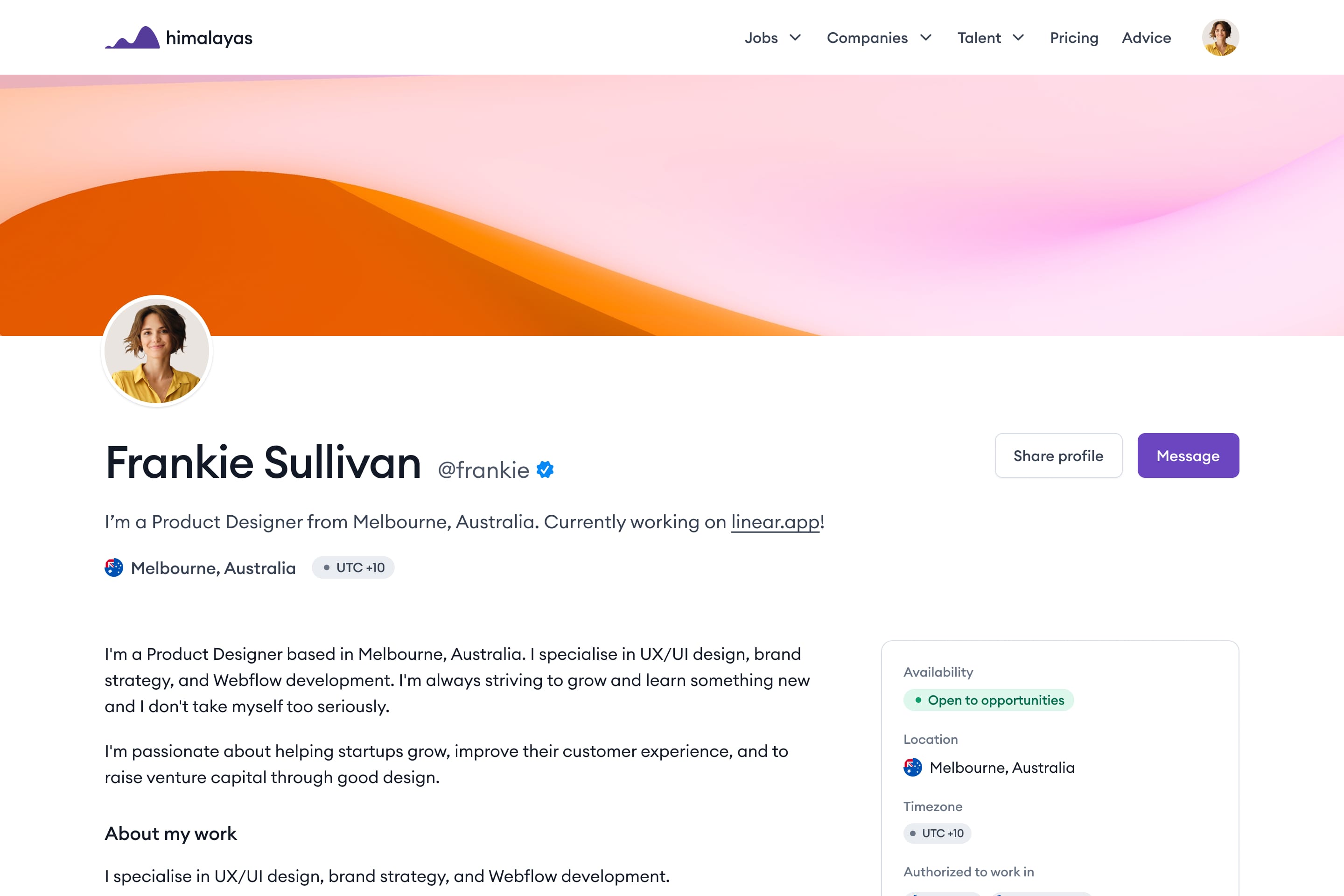