Complete Manufacturing Engineer Career Guide
Manufacturing engineers are the architects of efficiency, designing and optimizing the processes that transform raw materials into finished products. They bridge the gap between product design and mass production, ensuring quality, cost-effectiveness, and safety across diverse industries. This crucial role offers a dynamic blend of technical problem-solving and hands-on application, making it vital for global innovation and economic growth.
Key Facts & Statistics
Median Salary
$100,560 USD
(U.S. Bureau of Labor Statistics, May 2023)
Range: $70k - $140k+ USD, depending on experience and location
Growth Outlook
10%
faster than average (U.S. Bureau of Labor Statistics, 2022-2032)
Annual Openings
≈20k
openings annually (U.S. Bureau of Labor Statistics, 2022-2032)
Top Industries
Typical Education
Bachelor's degree in Manufacturing Engineering, Industrial Engineering, Mechanical Engineering, or a related field
What is a Manufacturing Engineer?
A manufacturing engineer optimizes and designs the processes and systems used to produce goods. This role focuses on improving efficiency, reducing costs, enhancing product quality, and ensuring the safety of manufacturing operations. They bridge the gap between product design and actual production, making sure that a product can be consistently and economically manufactured at scale.
Unlike a mechanical engineer who might design the product itself, or an industrial engineer who focuses on broader system efficiency across various industries, a manufacturing engineer specifically hones in on the mechanics of making things. Their expertise lies in understanding production lines, machinery, materials, and human factors to create seamless, efficient, and reliable manufacturing workflows. They are critical to bringing products from concept to market effectively.
What does a Manufacturing Engineer do?
Key Responsibilities
- Designs and optimizes manufacturing processes, layouts, and workflows to improve efficiency and reduce costs.
- Develops and implements quality control procedures to ensure products meet specified standards and reduce defects.
- Selects, specifies, and integrates new machinery and equipment into production lines, ensuring proper installation and calibration.
- Conducts time studies and process analyses to identify bottlenecks and areas for continuous improvement.
- Collaborates with product design engineers to ensure new products are manufacturable and cost-effective.
- Trains production staff on new processes, equipment operation, and safety protocols.
- Troubleshoots manufacturing issues and implements corrective actions to minimize downtime and scrap rates.
Work Environment
A manufacturing engineer typically works in a dynamic environment, often splitting time between an office setting for design and analysis work, and the factory floor or production line for observation, troubleshooting, and implementation. Collaboration is central, as they frequently work with production teams, quality control, product design, and supply chain personnel. The pace can be fast, especially when implementing new processes or resolving urgent production issues. While most work occurs on-site, some roles might involve travel to supplier facilities or other company plants. Work hours are generally standard business hours, but project deadlines or critical equipment failures may require extended or irregular shifts.
Tools & Technologies
Manufacturing engineers regularly use Computer-Aided Design (CAD) software such as SolidWorks, AutoCAD, or PTC Creo for designing fixtures, tools, and plant layouts. They also employ simulation software like Arena or FlexSim for process optimization and bottleneck analysis. For quality control, they utilize Statistical Process Control (SPC) software and metrology equipment like CMMs (Coordinate Measuring Machines). Enterprise Resource Planning (ERP) systems such as SAP or Oracle are crucial for managing production schedules and material flow. Data analysis tools like Microsoft Excel, Minitab, or specialized analytics platforms help them interpret production data and identify trends. They also work with automation technologies including PLCs (Programmable Logic Controllers), robotics, and SCADA systems.
Manufacturing Engineer Skills & Qualifications
Manufacturing Engineers bridge the gap between design and production, ensuring efficient, high-quality, and cost-effective manufacturing processes. They optimize workflows, implement new technologies, and troubleshoot production issues. Qualifications for this role prioritize a blend of theoretical knowledge and practical application.
Requirements vary significantly by seniority and industry. Entry-level positions often seek candidates with strong foundational engineering principles and a willingness to learn specific processes. Senior roles demand extensive experience in process optimization, project management, and leadership. Companies in highly regulated industries like aerospace or medical devices place a stronger emphasis on formal certifications and strict adherence to quality standards, while consumer goods manufacturing might value rapid iteration and cost reduction more.
Formal education, typically a Bachelor's degree, forms the bedrock for most Manufacturing Engineer roles. However, practical experience gained through internships, co-op programs, or technician roles significantly enhances a candidate's profile. Certifications in lean manufacturing, Six Sigma, or specific software tools are highly valued as they demonstrate specialized expertise and a commitment to continuous improvement. The field is rapidly evolving with the integration of Industry 4.0 technologies, requiring engineers to continuously update their skills in automation, data analytics, and smart manufacturing systems.
Education Requirements
Technical Skills
- Lean Manufacturing and Six Sigma methodologies (e.g., Value Stream Mapping, Kaizen, SPC)
- Process Optimization and Efficiency Analysis (e.g., cycle time reduction, OEE improvement)
- CAD/CAM software proficiency (e.g., SolidWorks, AutoCAD, CATIA) for design and simulation
- Robotics and Automation principles (e.g., PLC programming, robotic cell integration)
- Manufacturing Execution Systems (MES) and Enterprise Resource Planning (ERP) software
- Statistical Process Control (SPC) and Quality Management Systems (e.g., ISO 9001)
- Tooling and Fixture Design for production lines
- Materials science and engineering principles relevant to manufacturing processes
- Data analysis and visualization tools (e.g., Excel, Minitab, Tableau)
- Facility layout and workflow design for optimized production flow
- Additive Manufacturing (3D printing) technologies and applications
- Safety and environmental regulations (e.g., OSHA, EPA) within manufacturing operations
Soft Skills
- Problem-solving and analytical thinking: Manufacturing Engineers diagnose and resolve complex production issues, requiring a systematic approach to identify root causes and implement effective solutions.
- Attention to detail: Ensuring product quality, process consistency, and adherence to safety standards demands meticulous attention to detail in process design and execution.
- Cross-functional collaboration: This role frequently interacts with design, quality, supply chain, and production teams, requiring strong teamwork and communication skills to achieve common goals.
- Adaptability and flexibility: Manufacturing environments are dynamic; engineers must adapt quickly to changes in production demands, technology, and material availability.
- Continuous improvement mindset: A drive to constantly seek out inefficiencies, optimize processes, and implement new technologies is crucial for enhancing productivity and reducing costs.
- Project management: Manufacturing Engineers often lead or contribute to projects for new product introductions or process upgrades, requiring planning, execution, and stakeholder management skills.
- Technical communication: Explaining complex technical issues or process improvements clearly to non-technical staff, management, and operators is essential for effective implementation and training.
How to Become a Manufacturing Engineer
Entering the manufacturing engineering field offers diverse pathways, moving beyond traditional four-year engineering degrees. While a Bachelor's degree in engineering (Mechanical, Industrial, Chemical, or Manufacturing Engineering) remains a strong foundation, many successful manufacturing engineers transition from related technical roles or through specialized certifications and apprenticeships. The timeline for entry varies; a complete beginner might need 2-4 years for a degree, while someone with a technical associate's degree or a related trade background could transition within 1-2 years through targeted upskilling and practical experience.
Geographic location and company size significantly influence entry points. Large corporations and established manufacturing hubs often prefer candidates with formal degrees and some internship experience. In contrast, smaller companies or startups might prioritize hands-on problem-solving skills and a proven track record of process improvement, even from non-traditional backgrounds. Networking is crucial across all scenarios; connecting with professionals in the industry through LinkedIn, professional organizations like SME (Society of Manufacturing Engineers), or local industry events can open doors to unadvertised positions and mentorship opportunities.
A common misconception is that manufacturing engineering is solely about automation or robotics. This role encompasses optimizing entire production systems, from supply chain integration and quality control to lean manufacturing principles and continuous improvement. Successful entry often requires a blend of technical acumen, problem-solving capabilities, and strong communication skills to collaborate with diverse teams. Emphasize practical projects and hands-on experience over theoretical knowledge alone to stand out in the hiring process.
Step 1
Step 2
Step 3
Step 4
Step 5
Step 6
Step 7
Education & Training Needed to Become a Manufacturing Engineer
Becoming a Manufacturing Engineer requires a blend of theoretical knowledge and practical application. Formal university degrees, particularly a Bachelor's in Mechanical Engineering, Industrial Engineering, or Manufacturing Engineering, remain the most recognized pathway. These 4-year programs typically cost between $40,000 and $120,000+ for in-state tuition at public universities, and significantly more at private institutions. They provide a strong foundation in design, process optimization, materials science, and automation, which are critical for the role. Employers often prefer candidates with these degrees due to the depth of theoretical understanding they provide.
Alternative learning paths, such as specialized bootcamps or professional certifications, can supplement a degree or provide focused skills for those already in related fields. While a bootcamp alone is rarely sufficient for a direct entry-level Manufacturing Engineer role, programs focusing on Six Sigma, Lean Manufacturing, or specific CAD/CAM software can enhance a candidate's profile. These programs typically range from a few weeks to several months, costing $2,000 to $10,000. Self-study through online courses and industry journals can also contribute to continuous professional development, especially in areas like Industry 4.0 or advanced robotics. Practical experience, often gained through internships or co-op programs during a degree, is highly valued, sometimes more so than theoretical knowledge alone.
The market perception of credentials varies; a bachelor's degree is often a baseline requirement, while certifications demonstrate specialized expertise. Continuous learning is essential in this field due to rapid technological advancements in automation, additive manufacturing, and smart factories. Educational needs shift significantly with seniority; entry-level roles focus on core engineering principles, while senior positions require strategic thinking and expertise in supply chain optimization or global manufacturing strategies. Investing in a robust engineering degree provides a broad foundation, while targeted certifications offer cost-effective ways to specialize or stay current with emerging trends. Look for programs with ABET accreditation for engineering degrees, as this signifies adherence to quality standards and is often a prerequisite for professional licensure.
Manufacturing Engineer Salary & Outlook
Compensation for a Manufacturing Engineer varies significantly based on several critical factors. Geographic location plays a major role, with higher salaries typically found in regions with a strong manufacturing base and higher cost of living, such as California, Michigan, or Texas. Conversely, areas with lower living costs may offer more modest base salaries.
Experience, specialized skills, and industry sector also drive earning potential. Engineers with expertise in automation, lean manufacturing, or specific software tools often command premium compensation. Total compensation packages extend beyond base salary, frequently including performance bonuses, profit-sharing, and comprehensive benefits like health insurance, retirement plans, and professional development allowances. Some roles in high-growth sectors might also offer equity options.
Company size and industry impact salary scales; larger corporations or those in high-tech manufacturing often offer more competitive pay than smaller firms. Remote work opportunities are less common for Manufacturing Engineers due to the hands-on nature of the role, but some design or process optimization tasks might allow for hybrid arrangements, impacting geographic arbitrage. Understanding these factors provides a holistic view of a Manufacturing Engineer's earning potential and negotiation leverage.
Salary by Experience Level
Level | US Median | US Average |
---|---|---|
Junior Manufacturing Engineer | $70k USD | $75k USD |
Manufacturing Engineer | $90k USD | $95k USD |
Senior Manufacturing Engineer | $110k USD | $115k USD |
Lead Manufacturing Engineer | $130k USD | $135k USD |
Principal Manufacturing Engineer | $150k USD | $155k USD |
Manufacturing Engineering Manager | $170k USD | $175k USD |
Director of Manufacturing Engineering | $205k USD | $210k USD |
Market Commentary
The job market for Manufacturing Engineers shows steady demand, driven by ongoing efforts in process optimization, automation, and supply chain resilience across various industries. Industries like automotive, aerospace, medical devices, and consumer electronics consistently seek these professionals to enhance production efficiency and quality. The push towards Industry 4.0 and smart manufacturing technologies further fuels this demand, with a projected growth outlook of 5-8% over the next decade.
Emerging opportunities lie in advanced robotics, additive manufacturing (3D printing), and data analytics for predictive maintenance. Manufacturing Engineers who can integrate these technologies into existing production lines are highly valued. There is a general supply-demand balance, though specific regions with high manufacturing activity may experience a shortage of highly skilled engineers.
Future-proofing in this role involves continuous learning in new technologies and methodologies, such as AI-driven process control and sustainable manufacturing practices. While some routine tasks may face automation, the core problem-solving, design, and strategic oversight responsibilities of a Manufacturing Engineer remain critical and largely resistant to full automation. This profession exhibits relative economic resilience, as manufacturing is fundamental to most economies, though specific sector downturns can impact job availability.
Manufacturing Engineer Career Path
Career progression for a Manufacturing Engineer involves a blend of technical mastery, process optimization, and leadership development. Individuals typically advance through individual contributor (IC) roles, becoming experts in production systems and continuous improvement. Alternatively, a management track focuses on leading teams, setting departmental strategy, and overseeing broader operational efficiencies.
Advancement speed depends on several factors, including individual performance, the complexity of projects undertaken, and the specific industry. High-growth sectors or companies with rapid product development cycles often offer quicker progression. Specialization in areas like automation, lean manufacturing, or specific material processes can accelerate career growth, leading to more impactful roles.
Lateral moves are common, allowing engineers to gain experience across different product lines or manufacturing sites. This broadens their understanding of diverse production challenges. Networking with industry peers, engaging in professional organizations, and pursuing advanced certifications in areas like Six Sigma or Project Management are crucial for sustained career momentum. Some engineers may pivot into roles such as operations management, supply chain, or product development, leveraging their deep understanding of manufacturing processes.
Junior Manufacturing Engineer
0-2 yearsKey Focus Areas
Manufacturing Engineer
2-5 yearsKey Focus Areas
Senior Manufacturing Engineer
5-8 yearsKey Focus Areas
Lead Manufacturing Engineer
8-12 yearsKey Focus Areas
Principal Manufacturing Engineer
12+ yearsKey Focus Areas
Manufacturing Engineering Manager
10-15 years total experience, 2-4 years in a lead roleKey Focus Areas
Director of Manufacturing Engineering
15+ years total experience, 3-5 years in a management roleKey Focus Areas
Junior Manufacturing Engineer
0-2 yearsSupport senior engineers in process improvement and troubleshooting. Assist with data collection and analysis to identify production bottlenecks. Participate in small-scale projects, focusing on specific tasks within a larger manufacturing initiative. Work under direct supervision, primarily executing defined procedures.
Key Focus Areas
Develop foundational knowledge of manufacturing processes, equipment operation, and safety protocols. Focus on learning company-specific systems, CAD software, and data analysis tools. Build communication skills for effective team collaboration and documentation.
Manufacturing Engineer
2-5 yearsDesign and implement process improvements to enhance efficiency, quality, and cost-effectiveness. Conduct root cause analysis for production defects and implement corrective actions. Manage small to medium-sized projects independently, from concept to implementation. Collaborate with production teams, quality control, and R&D.
Key Focus Areas
Master process optimization techniques, including lean manufacturing and Six Sigma methodologies. Develop problem-solving skills for complex production issues. Enhance technical proficiency in specific manufacturing technologies. Improve project management capabilities and cross-functional communication.
Senior Manufacturing Engineer
5-8 yearsLead significant manufacturing engineering projects, often involving new product introductions or major equipment installations. Provide technical leadership and expertise to cross-functional teams. Drive continuous improvement initiatives across multiple production lines. Make independent technical decisions with significant impact on operational performance.
Key Focus Areas
Lead complex process development and optimization projects. Mentor junior engineers and provide technical guidance. Develop expertise in advanced manufacturing technologies, automation, and industrial IoT. Strengthen strategic thinking for long-term operational planning.
Lead Manufacturing Engineer
8-12 yearsAct as the primary technical expert and project lead for critical manufacturing initiatives. Oversee the technical aspects of complex projects, ensuring successful execution and adherence to budget and timeline. Mentor and guide a team of manufacturing engineers. Influence technical direction and best practices across the engineering department.
Key Focus Areas
Provide technical leadership and strategic direction for a specific manufacturing area or technology. Guide project teams and ensure alignment with business objectives. Develop strong leadership skills, including delegation, conflict resolution, and performance management. Cultivate a deep understanding of business financials and operational metrics.
Principal Manufacturing Engineer
12+ yearsDefine and champion advanced manufacturing strategies and technologies for the entire organization. Solve the most complex and ambiguous technical challenges. Provide expert consultation across departments and to executive leadership. Shape the future of manufacturing capabilities and competitiveness for the company.
Key Focus Areas
Drive innovation in manufacturing processes and technology. Develop long-term technical strategies and roadmaps. Influence organizational policy regarding manufacturing best practices. Become a recognized thought leader within the company and industry.
Manufacturing Engineering Manager
10-15 years total experience, 2-4 years in a lead roleManage a team of manufacturing engineers, overseeing their projects and professional development. Set departmental goals and priorities aligned with production targets and company strategy. Allocate resources and manage budgets for manufacturing engineering initiatives. Ensure the team delivers high-quality engineering solutions and drives continuous improvement.
Key Focus Areas
Develop strong people management skills, including hiring, performance reviews, and career development. Master budgeting, resource allocation, and operational planning. Enhance leadership presence and communication for effective team motivation and stakeholder engagement. Focus on strategic alignment of team goals with broader organizational objectives.
Director of Manufacturing Engineering
15+ years total experience, 3-5 years in a management roleOversee the entire manufacturing engineering function across multiple sites or product lines. Define the strategic direction for all manufacturing processes, technology, and continuous improvement initiatives. Lead major capital investment decisions for manufacturing infrastructure. Report directly to executive leadership, influencing overall company operational strategy.
Key Focus Areas
Formulate long-term manufacturing engineering strategies and technological roadmaps. Develop executive-level communication and presentation skills. Drive organizational change and innovation. Build strong relationships with cross-functional executive peers and external partners. Focus on global manufacturing trends and competitive advantage.
Job Application Toolkit
Ace your application with our purpose-built resources:
Manufacturing Engineer Resume Examples
Proven layouts and keywords hiring managers scan for.
View examplesManufacturing Engineer Cover Letter Examples
Personalizable templates that showcase your impact.
View examplesTop Manufacturing Engineer Interview Questions
Practice with the questions asked most often.
View examplesManufacturing Engineer Job Description Template
Ready-to-use JD for recruiters and hiring teams.
View examplesGlobal Manufacturing Engineer Opportunities
Manufacturing Engineers optimize production processes globally. This role translates across countries, focusing on efficiency, quality, and cost reduction in diverse industries like automotive, electronics, and aerospace.
Global demand remains strong, particularly in emerging economies and industrialized nations investing in advanced manufacturing. Professionals consider international opportunities for specialized projects, career advancement, and exposure to new technologies. Some international certifications, like Six Sigma or Lean Manufacturing, enhance global mobility.
Global Salaries
Salaries for Manufacturing Engineers vary significantly by region and experience. In North America, entry-level engineers earn $60,000-$80,000 USD, while experienced professionals can reach $90,000-$120,000 USD annually. For instance, a Manufacturing Engineer in Michigan might earn $75,000 USD, while one in California could earn $95,000 USD, reflecting higher cost of living.
European salaries range widely. In Germany, a Manufacturing Engineer earns €50,000-€75,000 (approx. $55,000-$82,000 USD), often with strong social benefits. The UK offers £35,000-£55,000 (approx. $44,000-$69,000 USD). Asian markets like Japan and South Korea offer competitive packages, with salaries from ¥4,500,000-¥7,500,000 (approx. $30,000-$50,000 USD) in Japan, adjusted for lower cost of living. In Singapore, salaries range from S$50,000-S$80,000 (approx. $37,000-$59,000 USD), but purchasing power is generally higher.
Latin American countries typically offer lower nominal salaries but often provide good purchasing power. For example, in Mexico, a Manufacturing Engineer might earn MXN 300,000-MXN 600,000 (approx. $18,000-$36,000 USD). Salary structures also differ; some countries offer higher base pay, while others emphasize bonuses, vacation time, or comprehensive healthcare packages. Tax implications vary significantly, impacting take-home pay. Experience and specialized skills like automation or robotics generally command higher compensation internationally.
Remote Work
Full-time international remote work for Manufacturing Engineers is limited due to the hands-on nature of the role. Most tasks involve direct interaction with production lines, machinery, and physical products. However, some aspects, like process design, data analysis, supply chain optimization, or simulation, can be performed remotely.
Companies might hire Manufacturing Engineers for remote roles focused on global project management, software development for manufacturing systems, or technical support. Legal and tax implications of working across borders require careful consideration, often involving complex compliance. Time zone differences can pose collaboration challenges for international teams.
Digital nomad opportunities are rare for this specific role, as most require site presence. Some companies offer hybrid models where engineers visit facilities periodically. Salary expectations for remote roles might be adjusted based on the employee's location and the company's global compensation policies. Platforms like LinkedIn and specialized engineering job boards list remote-friendly roles when available. Reliable internet and a dedicated workspace are essential for any remote arrangement.
Visa & Immigration
Manufacturing Engineers often qualify for skilled worker visas in countries with strong industrial sectors. Popular destinations include Germany (EU Blue Card), Canada (Express Entry), Australia (Skilled Nominated Visa), and the USA (H-1B visa, though lottery-based). Requirements often include a relevant engineering degree, professional experience, and a job offer from a local employer.
Education credential recognition is crucial; applicants may need to have their degrees assessed by a national authority. Professional licensing is generally not required for engineers in most countries for employment, but specific certifications might be beneficial. Typical visa timelines range from a few months to over a year. Application processes involve submitting documentation, demonstrating financial stability, and sometimes attending interviews.
Pathways to permanent residency exist in many countries, often after several years of skilled employment. Language requirements, such as German for Germany or English for Canada/Australia, are common. Some countries may have specific fast-track programs for highly skilled professionals in demand. Family visas for spouses and dependents are usually available alongside the primary applicant's visa.
2025 Market Reality for Manufacturing Engineers
Understanding current market conditions is paramount for Manufacturing Engineers to forge successful careers. The profession has undergone significant transformation from 2023 to 2025, driven by post-pandemic supply chain recalibrations and the accelerating integration of AI into production systems.
Broader economic factors, such as inflation and consumer demand shifts, directly influence manufacturing output and, consequently, engineering hiring. Market realities vary considerably by experience level, with senior engineers in higher demand than entry-level candidates. Geographic location and the size of the manufacturing operation also play a crucial role, influencing available opportunities and compensation structures. This analysis provides an honest assessment of current hiring dynamics.
Current Challenges
Manufacturing Engineers face increased competition, especially for entry-level roles, as companies seek experienced talent to navigate complex supply chains and production automation. Economic uncertainty leads some firms to delay capital investments, impacting project-based hiring. The rapid adoption of AI and advanced robotics creates a skill gap, demanding new proficiencies in automation programming and data analytics.
Job searches in this field can extend from three to six months, particularly for roles requiring specialized industry experience or security clearances. Companies prioritize candidates who demonstrate adaptability and a proactive approach to learning new manufacturing technologies.
Growth Opportunities
Despite market challenges, significant opportunities exist for Manufacturing Engineers in specialized areas. Strong demand persists in sectors focused on automation and robotics integration, particularly for engineers skilled in designing and implementing automated production lines. Roles involving advanced materials, such as composites and biomaterials, also offer growth prospects.
Emerging specializations include AI-driven process optimization and digital twin development. Engineers who can leverage data analytics to enhance efficiency or create virtual factory models are highly sought after. Companies are increasingly seeking professionals who understand cybersecurity in operational technology (OT) environments, protecting smart factories from threats.
Strategic positioning involves acquiring certifications in industrial automation, robotics programming (e.g., FANUC, ABB), or data science for manufacturing. Experience with lean manufacturing and Six Sigma remains valuable but is now complemented by a need for digital fluency. Underserved markets often include regions with growing defense manufacturing or those investing heavily in sustainable energy production. Focusing on these areas or upskilling in AI-adjacent competencies can provide a clear competitive advantage.
Current Market Trends
Hiring for Manufacturing Engineers in 2025 shows a bifurcated demand. Established industries like automotive and aerospace maintain steady, albeit sometimes cautious, hiring. Emerging sectors, such as advanced battery production and personalized medicine, are rapidly expanding their engineering teams. This growth is driven by reshoring initiatives and the push for greater supply chain resilience.
Generative AI and machine learning are fundamentally reshaping the role. Engineers are now expected to design production processes optimized by AI, predict equipment failures with predictive analytics, and manage automated quality control systems. This shifts the focus from purely mechanical process improvement to integrated digital and physical system optimization. Many companies are seeking engineers who can bridge the gap between IT and operations, particularly in implementing Industry 4.0 solutions.
Salary growth remains stable for experienced professionals, with a premium on those possessing expertise in automation, robotics, and data-driven process optimization. Entry-level salaries face some pressure due to increased competition and a larger pool of graduates with foundational engineering degrees. The market is less saturated for engineers with hands-on experience in additive manufacturing or complex robotics. Remote work is less common for Manufacturing Engineers, given the hands-on nature of the role. However, roles involving process simulation, data analysis, and digital twin development can offer more flexibility. Hiring typically peaks in the first and third quarters as companies budget for new projects and production ramp-ups.
Emerging Specializations
The manufacturing engineering landscape is undergoing a profound transformation, driven by rapid advancements in automation, data analytics, and sustainable practices. These technological shifts are not merely optimizing existing processes; they are fundamentally reshaping the roles and responsibilities of manufacturing engineers, creating entirely new specialization opportunities. Early positioning in these emerging areas is crucial for professionals aiming to secure leadership roles and maximize their career trajectory in 2025 and beyond.
Specializing in cutting-edge fields often leads to premium compensation and accelerated career growth. While established specializations offer stability, emerging niches provide a competitive edge, allowing engineers to become indispensable experts in nascent but rapidly expanding domains. The timeline for these emerging areas to become mainstream, generating significant job opportunities, is typically within the next three to five years, making proactive skill development essential now.
Pursuing emerging specializations involves a strategic balance between risk and reward. While some areas might evolve differently than predicted, the foundational knowledge and problem-solving skills gained are universally valuable. The strategic choice to invest in these future-oriented capabilities positions manufacturing engineers at the forefront of industrial innovation, ensuring long-term relevance and impactful contributions to the industry's evolution.
Autonomous Manufacturing Systems Engineer
This specialization focuses on the design, implementation, and optimization of fully autonomous manufacturing systems, incorporating advanced robotics, AI-driven decision-making, and machine learning for predictive maintenance. Manufacturing engineers in this area develop intelligent factories where machines communicate seamlessly, adapt to production changes, and self-diagnose issues, minimizing human intervention. It addresses the growing industry demand for lights-out manufacturing and highly efficient, resilient production lines.
Circular Economy Manufacturing Engineer
This area involves integrating circular economy principles into manufacturing processes, focusing on waste reduction, resource efficiency, and product lifecycle management. Manufacturing engineers in this specialization design processes for material recovery, remanufacturing, and recycling, ensuring sustainable production from raw material sourcing to end-of-life. It addresses increasing regulatory pressures and corporate commitments to environmental responsibility, creating demand for engineers who can implement eco-friendly production strategies.
Manufacturing Data Scientist
This specialization applies advanced data analytics and machine learning techniques to optimize manufacturing operations, including predictive quality, process control, and supply chain efficiency. Manufacturing engineers in this role analyze vast datasets from production lines to identify patterns, forecast potential failures, and recommend real-time adjustments. The increasing complexity of modern manufacturing and the availability of sensor data drive the need for engineers who can extract actionable insights to enhance productivity and reduce costs.
Additive Manufacturing Process Engineer
This specialization focuses on the design and implementation of additive manufacturing processes, particularly for industrial-scale production of complex parts and customized products. Manufacturing engineers in this field optimize designs for 3D printing, select appropriate materials, and develop quality control protocols for additive manufacturing workflows. The ability to produce highly customized components on demand, reduce material waste, and accelerate prototyping drives the demand for expertise in this area.
Digital Twin & Simulation Engineer
This specialization centers on creating and managing digital twins of physical manufacturing systems, enabling real-time monitoring, simulation, and predictive analysis. Manufacturing engineers in this role build virtual replicas of factories, production lines, and individual machines to test changes, predict performance issues, and optimize operations without disrupting physical production. The pursuit of greater efficiency, reduced downtime, and enhanced decision-making in complex manufacturing environments fuels the demand for this expertise.
Pros & Cons of Being a Manufacturing Engineer
Making an informed career decision requires a clear understanding of both the potential advantages and genuine challenges of a chosen field. The experience of a manufacturing engineer can vary significantly based on the company's industry, its specific culture, the engineer's specialization within manufacturing, and their individual personality and preferences. What one person views as a pro, another might see as a con. Furthermore, the nature of these pros and cons can shift at different stages of a career, from early entry-level positions to senior leadership roles. This assessment aims to provide a realistic overview, helping aspiring manufacturing engineers set appropriate expectations for this dynamic and essential profession.
Pros
- Manufacturing engineers enjoy strong job security and consistent demand across various industries, as every organization involved in physical product creation relies on their expertise to optimize production processes.
- This role offers significant intellectual stimulation through continuous problem-solving, involving complex challenges related to efficiency, quality, and cost reduction within a dynamic production environment.
- Manufacturing engineers have tangible impact, directly seeing the results of their work in improved production lines, higher quality products, and reduced operational costs, which provides a strong sense of accomplishment.
- There are diverse career paths available within manufacturing engineering, allowing professionals to specialize in areas like automation, lean manufacturing, quality control, or supply chain, offering flexibility for career progression.
- The role provides opportunities for cross-functional collaboration, working closely with design, production, maintenance, and quality teams, which fosters a broad understanding of business operations and enhances teamwork skills.
- Salaries for experienced manufacturing engineers are competitive, reflecting the critical role they play in a company's profitability and efficiency, with potential for significant earnings as expertise grows.
- Manufacturing engineers often lead or contribute to projects involving cutting-edge technologies, such as robotics, advanced automation, and data analytics, keeping their work innovative and forward-thinking.
Cons
- Manufacturing engineers often face high-pressure environments, especially when production lines experience unexpected shutdowns or quality issues, requiring immediate troubleshooting to minimize costly delays.
- The role frequently demands a high degree of problem-solving under tight deadlines, as engineers must quickly identify root causes of inefficiencies or defects and implement effective solutions to maintain production targets.
- Manufacturing engineers may experience limited opportunities for remote work, as their presence is often required on the factory floor to monitor processes, inspect equipment, and collaborate directly with production teams.
- Continuous learning is essential in this field, as manufacturing technologies and industry standards evolve rapidly, requiring engineers to regularly update their skills and knowledge to remain effective.
- Exposure to industrial environments means manufacturing engineers may encounter noise, machinery, and various materials, necessitating strict adherence to safety protocols and potentially posing physical demands.
- Budget constraints and cost reduction pressures are common challenges, as engineers must find ways to optimize processes and improve efficiency while working within strict financial limitations.
- The role can involve irregular hours, particularly during equipment installations, system upgrades, or when critical production issues arise that require immediate attention outside of standard shifts to restore operations quickly and efficiently.
Frequently Asked Questions
Manufacturing Engineers face unique challenges in optimizing production and integrating new technologies. This section addresses common questions about entering this field, from essential skills and educational paths to career growth and daily work-life balance.
What educational qualifications do I need to become a Manufacturing Engineer?
Most entry-level Manufacturing Engineer positions require a bachelor's degree in engineering, typically in mechanical, industrial, or manufacturing engineering. While a master's degree can be beneficial for specialization or leadership roles, it is not usually a prerequisite for starting your career. Relevant internships or co-op experiences during your studies significantly boost your employability.
What are the most important skills for a successful Manufacturing Engineer?
The core skills include strong analytical and problem-solving abilities, process optimization, CAD software proficiency, and knowledge of lean manufacturing and Six Sigma principles. Communication and collaboration skills are also crucial, as you will work closely with production teams, designers, and suppliers. Experience with automation, robotics, and data analysis is increasingly valuable.
What are the typical salary expectations for a Manufacturing Engineer, both entry-level and experienced?
Entry-level Manufacturing Engineers can expect a competitive starting salary, which varies based on location, industry, and company size. With 3-5 years of experience, salaries typically increase significantly as you take on more complex projects and responsibilities. Specializing in areas like automation or supply chain optimization can further enhance earning potential.
What is the typical work-life balance like for a Manufacturing Engineer?
Manufacturing Engineers often work in fast-paced production environments, which can sometimes involve irregular hours or on-call duties, especially during new product launches or critical equipment breakdowns. However, many roles offer standard business hours. Work-life balance depends heavily on the specific company culture and the demands of particular projects, but it is generally manageable.
Is the job market for Manufacturing Engineers stable, and what are the long-term prospects?
The demand for Manufacturing Engineers remains strong across various industries, including automotive, aerospace, medical devices, and consumer goods. Companies continuously seek to improve efficiency, reduce costs, and adopt new technologies, ensuring a steady need for skilled engineers. The growth of automation and smart factories further solidifies job security in this field.
What are the typical career advancement opportunities for a Manufacturing Engineer?
Career progression for a Manufacturing Engineer can lead to senior engineering roles, project management, or leadership positions such as Manufacturing Manager or Director of Operations. Many also transition into roles focused on continuous improvement, supply chain management, or even product design. Pursuing certifications in Six Sigma or Lean methodologies can accelerate advancement.
Can I become a Manufacturing Engineer without a traditional engineering degree?
Transitioning into this field without a traditional engineering degree is challenging but possible. You would need to demonstrate strong technical aptitude, perhaps through certifications in specific manufacturing processes or software, and build a portfolio of relevant projects. Networking and gaining practical experience through internships or entry-level technician roles are crucial for non-traditional candidates.
How much remote work or travel is typically involved in a Manufacturing Engineer role?
Manufacturing Engineers are primarily based on-site in factories or production facilities to directly observe and optimize processes. While some administrative or design tasks can be done remotely, the hands-on nature of the role means significant remote work is uncommon. Travel might be required for supplier visits, equipment installations, or multi-site responsibilities.
Related Careers
Explore similar roles that might align with your interests and skills:
Fabrication Engineer
A growing field with similar skill requirements and career progression opportunities.
Explore career guideIndustrial Engineer
A growing field with similar skill requirements and career progression opportunities.
Explore career guideManufacturing Manager
A growing field with similar skill requirements and career progression opportunities.
Explore career guideManufacturing Process Engineer
A growing field with similar skill requirements and career progression opportunities.
Explore career guideProduction Engineer
A growing field with similar skill requirements and career progression opportunities.
Explore career guideAssess your Manufacturing Engineer readiness
Understanding where you stand today is the first step toward your career goals. Our Career Coach helps identify skill gaps and create personalized plans.
Skills Gap Analysis
Get a detailed assessment of your current skills versus Manufacturing Engineer requirements. Our AI Career Coach identifies specific areas for improvement with personalized recommendations.
See your skills gapCareer Readiness Assessment
Evaluate your overall readiness for Manufacturing Engineer roles with our AI Career Coach. Receive personalized recommendations for education, projects, and experience to boost your competitiveness.
Assess your readinessSimple pricing, powerful features
Upgrade to Himalayas Plus and turbocharge your job search.
Himalayas
Himalayas Plus
Himalayas Max
Find your dream job
Sign up now and join over 100,000 remote workers who receive personalized job alerts, curated job matches, and more for free!
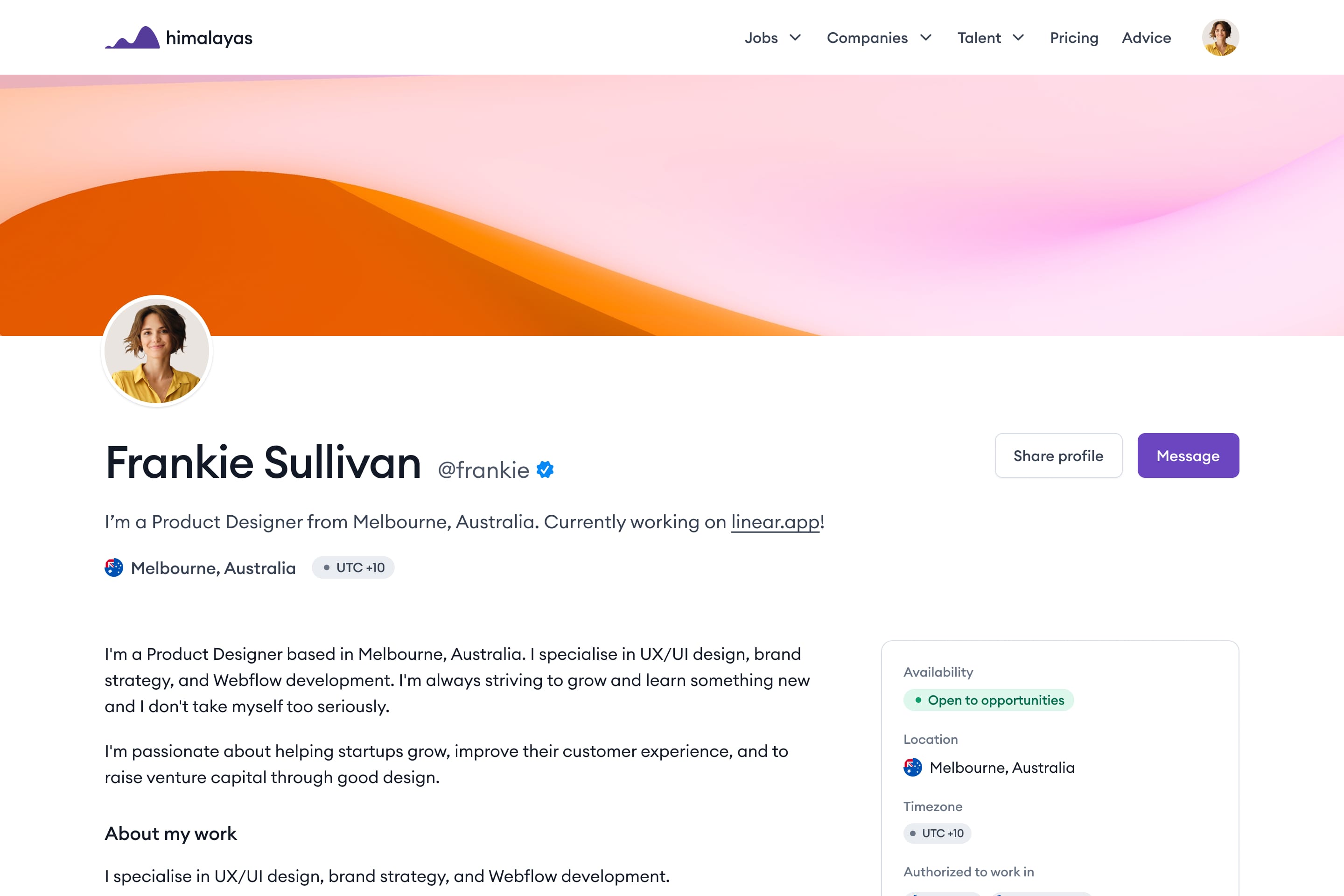