Complete Metal Fabricator Career Guide
Metal fabricators are the skilled artisans who transform raw metal into precision components and structures, building everything from intricate machinery parts to large architectural elements. They combine technical expertise with hands-on craftsmanship, playing a vital role in manufacturing and construction industries. This career offers a tangible sense of accomplishment, shaping the physical world around us while providing stable employment opportunities.
Key Facts & Statistics
Median Salary
Range: $35k - $70k+ USD
Growth Outlook
Annual Openings
Top Industries
Typical Education
High school diploma or equivalent; many learn through vocational training programs, apprenticeships, or on-the-job training
What is a Metal Fabricator?
A Metal Fabricator is a skilled tradesperson who specializes in creating metal structures and products by cutting, bending, shaping, and assembling raw metal materials. They take raw stock, such as steel plates, beams, or pipes, and transform them into finished components or complete assemblies according to engineering blueprints. This role requires a deep understanding of metal properties, fabrication techniques, and precision measurement.
Unlike a general welder who primarily focuses on joining metals, a metal fabricator handles the entire process from interpreting designs to the final assembly and finishing. They are distinct from machinists who remove material to create precise parts, or ironworkers who primarily install large-scale structural steel. Metal fabricators are crucial in industries ranging from construction and manufacturing to automotive and aerospace, building everything from custom parts to large industrial frameworks.
What does a Metal Fabricator do?
Key Responsibilities
- Interpret blueprints and engineering drawings to understand project specifications, dimensions, and material requirements for fabrication.
- Cut, bend, and shape metal components using specialized machinery like shears, press brakes, plasma cutters, and saws.
- Weld metal parts together using various welding techniques such as MIG, TIG, or stick welding, ensuring strong and precise joints.
- Grind and polish fabricated metal surfaces to remove sharp edges, burrs, and excess weld material, achieving a smooth finish.
- Assemble fabricated components into final products or sub-assemblies, often involving bolting, riveting, or further welding.
- Inspect finished products for quality, accuracy, and adherence to design specifications, making adjustments as needed.
- Perform routine maintenance on fabrication equipment to ensure optimal performance and workplace safety.
Work Environment
Metal fabricators typically work in workshops, factories, or construction sites, often in environments that can be noisy and dusty. The work involves significant physical activity, including standing for long periods, lifting heavy materials, and operating machinery. Collaboration with other fabricators, welders, and supervisors is common, often within a team-oriented setting focused on project deadlines. Schedules are usually full-time, often with early starts, and overtime may be required to meet production demands. Safety is paramount, with strict protocols and personal protective equipment always in use due to the inherent risks of working with heavy machinery and hot metals.
Tools & Technologies
Metal fabricators regularly use a diverse array of tools and machinery. Cutting tools include plasma cutters, oxy-acetylene torches, band saws, shears, and angle grinders. For bending and shaping, they operate press brakes, plate rolls, and hand tools like hammers and clamps. Welding equipment such as MIG, TIG, and stick welders are essential, along with appropriate personal protective equipment like welding helmets and gloves. Measurement tools like calipers, micrometers, and tape measures are critical for precision. They also utilize various power tools, hand tools, and material handling equipment like forklifts or overhead cranes, especially when working with large or heavy metal sheets and beams.
Metal Fabricator Skills & Qualifications
A Metal Fabricator's qualifications are highly practical and skill-based, with a strong emphasis on hands-on experience and proven competency. While formal education provides foundational knowledge, direct experience manipulating and shaping metal is paramount. Requirements vary significantly by the complexity of the projects, the materials used, and the industry sector.
For entry-level positions, employers often seek candidates with vocational training or a completed apprenticeship, demonstrating basic safety knowledge and tool proficiency. More senior or specialized roles, such as those involving custom architectural fabrication or aerospace components, demand extensive experience, advanced certification, and often a deep understanding of metallurgy and advanced welding techniques. Small job shops might prioritize versatility across various processes, while large manufacturing plants often seek specialists in a single area like robotic welding or precision laser cutting.
Certifications from organizations like the American Welding Society (AWS) significantly enhance a fabricator's marketability, often being 'must-haves' for specific types of welding or high-stakes projects. These certifications demonstrate a standardized level of skill and adherence to industry codes. While a bachelor's degree is rarely required, an associate's degree in welding technology or manufacturing can accelerate career progression into supervisory or lead fabricator roles. The field is evolving with automation and advanced materials, requiring fabricators to adapt to CNC machinery, laser technology, and new joining methods, shifting some focus from purely manual techniques to programming and machine operation.
Education Requirements
Technical Skills
- Blueprint Reading and Interpretation (including GD&T)
- Measuring Tools Proficiency (calipers, micrometers, squares, protractors)
- Metal Cutting Techniques (sawing, shearing, plasma cutting, oxy-fuel cutting, laser cutting)
- Welding Processes (SMAW, GMAW/MIG, GTAW/TIG, FCAW) across various metals (steel, aluminum, stainless steel)
- Metal Forming and Bending (press brakes, roll formers, bending machines, manual forming)
- Grinding and Finishing Techniques (angle grinders, orbital sanders, deburring tools)
- Layout and Marking (scribing, punching, templating)
- Drilling and Tapping (drill presses, hand drills)
- Shop Math and Geometry (calculating angles, lengths, material yield)
- Basic Machine Operation and Maintenance (CNC plasma tables, press brakes, shears)
- Material Handling and Rigging (forklifts, overhead cranes, slings)
- Quality Control and Inspection (visual inspection, dimensional checks)
Soft Skills
- Attention to Detail: Essential for ensuring precise measurements, accurate cuts, and flawless welds, which directly impacts the quality and integrity of fabricated parts.
- Problem-Solving: Crucial for identifying and resolving issues that arise during fabrication, such as material inconsistencies, design challenges, or equipment malfunctions.
- Spatial Reasoning: Important for visualizing 2D blueprints as 3D objects and understanding how different metal components will fit together.
- Safety Consciousness: Paramount in a workshop environment to prevent accidents, injuries, and damage to equipment, requiring strict adherence to safety protocols.
- Adaptability: Necessary to work with various metals, different fabrication techniques, and evolving project requirements or design changes.
- Team Collaboration: Often required to work effectively with other fabricators, welders, engineers, and project managers to meet production deadlines and quality standards.
- Time Management: Important for organizing tasks, prioritizing work, and completing fabrication projects efficiently to meet production schedules.
How to Become a Metal Fabricator
Entering the metal fabrication field offers multiple pathways, from traditional apprenticeships to vocational training and direct entry-level positions. The most effective route often depends on your prior experience, available time, and local industry demands. Apprenticeships provide comprehensive, hands-on training alongside experienced professionals, typically lasting 3-5 years, and are highly valued for their practical skill development. Vocational schools offer structured programs that can accelerate foundational knowledge, usually taking 6 months to 2 years, preparing individuals for entry-level roles more quickly.
Geographic location significantly influences opportunities; industrial hubs and manufacturing regions will have more openings and specialized shops. Smaller companies might prioritize hands-on experience and a willingness to learn on the job, while larger corporations may prefer candidates with formal certifications. Misconceptions often include believing extensive prior experience is always necessary; many shops are willing to train motivated individuals with a strong mechanical aptitude and a commitment to safety. Networking within the local manufacturing community and connecting with experienced fabricators can also open doors to unadvertised opportunities.
The hiring landscape values practical skills, a strong work ethic, and adaptability to new technologies like CNC machinery. While a degree is not typically required, certifications in welding, blueprint reading, or specific machinery operation can significantly enhance your resume. Overcoming barriers often involves demonstrating a genuine passion for the craft, a commitment to safety protocols, and a proactive approach to learning, whether through formal education or self-directed projects.
Step 1
Step 2
Step 3
Step 4
Step 5
Step 6
Step 7
Education & Training Needed to Become a Metal Fabricator
Becoming a skilled Metal Fabricator involves a blend of theoretical knowledge and extensive practical application. While formal four-year degrees are uncommon and generally unnecessary for this specific trade, vocational schools, community college programs, and apprenticeships form the backbone of a Metal Fabricator's education. These pathways typically focus on welding, blueprint reading, material science, and safety protocols relevant to shaping and joining metal components.
Vocational programs and community college associate degrees often take 1-2 years to complete, costing between $5,000 and $20,000. Apprenticeships, which combine on-the-job training with classroom instruction, can last 3-5 years and often pay trainees while they learn, making them a cost-effective and highly practical route. Online courses or self-study might supplement learning in areas like CAD software or advanced welding techniques, but they cannot replace hands-on shop experience, which is crucial for employer acceptance.
Employers highly value certifications in specific welding processes (e.g., AWS certifications) and demonstrable experience. Continuous learning in new fabrication techniques, automation, and material advancements is essential for career progression. The educational needs for a Metal Fabricator vary depending on specialization, such as structural fabrication, custom artistic work, or manufacturing, with specialized roles often requiring more advanced training or certifications in specific niche areas.
Metal Fabricator Salary & Outlook
Compensation for a Metal Fabricator varies significantly based on several key factors. Geographic location plays a crucial role; areas with a high concentration of manufacturing, such as the Midwest or parts of the Southern US, often offer competitive wages due to demand. Conversely, regions with a higher cost of living may have slightly elevated salaries to offset expenses, though local industry presence remains the primary driver.
Experience dramatically impacts earning potential. An entry-level fabricator will earn less than a seasoned professional with a decade of specialized expertise in complex welding or advanced machinery operation. Specializations like TIG welding, custom sheet metal work, or CNC programming capabilities command higher pay. Total compensation extends beyond base salary, often including overtime pay, production bonuses, and comprehensive benefits packages. These benefits typically encompass health insurance, retirement plans like 401(k)s, and sometimes allowances for professional certifications or safety training.
Industry-specific trends also shape compensation. The aerospace, defense, and heavy machinery sectors often offer higher wages compared to general construction or light manufacturing due to the precision and critical nature of the work. Company size can also influence pay, with larger enterprises generally providing more structured pay scales and benefit programs. While remote work is not typical for hands-on fabrication roles, some design or supervisory positions might offer hybrid flexibility. International markets present different pay scales; the figures provided here reflect the US dollar context.
Salary by Experience Level
Level | US Median | US Average |
---|---|---|
Apprentice Metal Fabricator | $36k USD | $38k USD |
Junior Metal Fabricator | $42k USD | $45k USD |
Metal Fabricator | $52k USD | $55k USD |
Senior Metal Fabricator | $65k USD | $68k USD |
Lead Metal Fabricator | $75k USD | $78k USD |
Metal Fabrication Supervisor | $82k USD | $85k USD |
Metal Fabrication Manager | $95k USD | $98k USD |
Market Commentary
The job market for Metal Fabricators shows steady demand, driven by ongoing activity in manufacturing, construction, and infrastructure development. The Bureau of Labor Statistics projects a modest growth outlook for welders, cutters, solderers, and brazers, a category that includes metal fabricators. This growth is influenced by the need to maintain and upgrade existing infrastructure, as well as new construction projects and continued domestic manufacturing.
Emerging opportunities for fabricators include specialized roles in advanced manufacturing, where skills in automated fabrication systems, robotic welding, and additive manufacturing are increasingly valuable. The adoption of new technologies like laser cutting, plasma cutting, and CNC machining requires fabricators to adapt and acquire new proficiencies. There is a persistent demand for skilled fabricators, particularly those with certifications in various welding techniques or experience with complex blueprints and precision work. This creates a supply-demand imbalance in some regions, favoring skilled candidates.
The profession is relatively resilient to economic downturns due to its foundational role in various industries, though demand can fluctuate with major construction or manufacturing cycles. Future-proofing this career involves continuous learning, especially in digital fabrication technologies and materials science. Geographic hotspots for employment include industrial hubs in Texas, Ohio, Michigan, and California. While automation handles repetitive tasks, the need for skilled human oversight, custom fabrication, and intricate assembly ensures a continued role for experienced metal fabricators.
Metal Fabricator Career Path
Career progression for a Metal Fabricator involves a clear path from foundational learning to advanced specialization and leadership. Individuals typically begin by mastering core fabrication techniques before moving into more complex project work and eventually supervisory or management roles.
Advancement speed depends on several factors, including an individual's skill acquisition rate, dedication to precision, and commitment to safety. Specialization in areas like welding, sheet metal work, or structural fabrication can accelerate progression. Company size and industry also play a role; smaller shops might offer quicker advancement to supervisory roles, while larger manufacturers might provide more opportunities for highly specialized technical expertise or management of larger teams.
The field offers both individual contributor (IC) tracks, where fabricators become highly skilled specialists, and management tracks, which focus on overseeing teams and production. Lateral moves between different types of fabrication (e.g., from architectural metalwork to aerospace components) are common, expanding a fabricator's skill set. Continuous learning, obtaining relevant certifications (e.g., welding certifications), and building a reputation for quality and reliability are crucial for upward mobility. Networking within the industry, especially through trade associations or professional development courses, can also open doors to new opportunities.
Apprentice Metal Fabricator
0-2 yearsKey Focus Areas
Junior Metal Fabricator
2-4 yearsKey Focus Areas
Metal Fabricator
4-7 yearsKey Focus Areas
Senior Metal Fabricator
7-10 yearsKey Focus Areas
Lead Metal Fabricator
10-14 yearsKey Focus Areas
Metal Fabrication Supervisor
14-18 yearsKey Focus Areas
Metal Fabrication Manager
18+ yearsKey Focus Areas
Apprentice Metal Fabricator
0-2 yearsWorks under direct supervision, assisting experienced fabricators with material preparation, basic cutting, and grinding tasks. Learns to operate common fabrication equipment safely and effectively. Follows instructions meticulously, focusing on acquiring foundational skills and understanding shop procedures. Responsibilities are limited to simple, repetitive tasks.
Key Focus Areas
Develop a strong understanding of shop safety protocols, tool identification, and basic material handling. Focus on mastering fundamental cutting, grinding, and simple welding techniques. Learn to read and interpret basic blueprints and fabrication drawings. Cultivate meticulous attention to detail and precision in all tasks.
Junior Metal Fabricator
2-4 yearsPerforms routine fabrication tasks with increasing independence, including cutting, forming, and welding components according to specifications. Works on individual parts or sub-assemblies under general supervision. Contributes to project completion by ensuring accuracy and quality of fabricated pieces. Starts to take responsibility for specific segments of larger projects.
Key Focus Areas
Refine welding techniques across various materials and joint types. Improve proficiency in operating a wider range of fabrication machinery, including brakes, shears, and presses. Enhance blueprint reading skills to understand more complex assemblies. Begin to troubleshoot minor equipment issues and optimize workflow for efficiency.
Metal Fabricator
4-7 yearsIndependently fabricates complex metal components and assemblies from start to finish, interpreting detailed blueprints and specifications. Makes decisions on optimal fabrication methods and material utilization. Collaborates with engineers or designers to resolve technical issues. Ensures high-quality output and adherence to project timelines.
Key Focus Areas
Master advanced welding processes (e.g., TIG, MIG, Stick) and specialized fabrication techniques. Develop problem-solving skills for complex design challenges and material properties. Improve efficiency and reduce waste in fabrication processes. Consider pursuing specialized certifications relevant to specific materials or industry standards.
Senior Metal Fabricator
7-10 yearsServes as a subject matter expert in specific fabrication techniques or materials, tackling the most challenging and critical projects. Provides technical guidance and mentorship to less experienced fabricators. Takes ownership of project quality and adherence to strict specifications. May lead small, specialized fabrication efforts.
Key Focus Areas
Develop expertise in advanced fabrication processes, including specialty welding, exotic material handling, or complex forming. Mentor junior fabricators, providing technical guidance and sharing best practices. Contribute to process improvement initiatives. Begin to take on leadership responsibilities for specific project phases or complex builds.
Lead Metal Fabricator
10-14 yearsDirects and coordinates the daily activities of a small team of fabricators on specific projects or production lines. Assigns tasks, monitors progress, and ensures adherence to quality standards and deadlines. Provides on-the-job training and guidance. Acts as the primary point of contact for technical issues within the team.
Key Focus Areas
Cultivate strong leadership and team coordination skills. Develop a deeper understanding of project management principles, including scheduling and resource allocation. Enhance communication skills to effectively convey instructions and provide feedback. Focus on optimizing team productivity and maintaining high safety standards.
Metal Fabrication Supervisor
14-18 yearsOversees the entire fabrication process for a section of the shop or a specific product line, managing a team of fabricators and leads. Ensures production targets are met efficiently and safely. Conducts performance reviews, manages attendance, and resolves personnel issues. Implements and enforces safety regulations and quality control procedures.
Key Focus Areas
Develop comprehensive understanding of production planning, scheduling, and inventory management. Enhance problem-solving skills for operational challenges, including equipment maintenance and workflow bottlenecks. Improve leadership capabilities in conflict resolution and performance management. Focus on continuous improvement methodologies.
Metal Fabrication Manager
18+ yearsManages the overall operations of the metal fabrication department, including budgeting, strategic planning, and resource allocation. Develops and implements production policies and procedures to optimize efficiency and profitability. Leads and mentors supervisory staff. Responsible for departmental performance, safety compliance, and continuous improvement initiatives.
Key Focus Areas
Acquire strong business acumen, including budgeting, cost control, and strategic planning. Develop advanced leadership skills in team building, talent development, and organizational change. Master project management methodologies for large-scale initiatives. Focus on industry trends and technological advancements to drive innovation.
Job Application Toolkit
Ace your application with our purpose-built resources:
Metal Fabricator Cover Letter Examples
Personalizable templates that showcase your impact.
View examplesMetal Fabricator Job Description Template
Ready-to-use JD for recruiters and hiring teams.
View examplesGlobal Metal Fabricator Opportunities
Metal Fabricators find consistent demand globally, as manufacturing and infrastructure development remain core to economies. This profession translates well across borders, focusing on similar skills like welding, cutting, and shaping metal. Global demand for skilled fabricators is stable, particularly in industrialized nations and emerging markets as of 2025. Professionals often seek international roles for higher wages or specialized projects. International certifications like AWS (American Welding Society) or ISO 9606 (International Organization for Standardization) enhance global mobility.
Global Salaries
Salaries for Metal Fabricators vary significantly by region, reflecting local economic conditions and cost of living. In North America, a fabricator in the United States earns between $45,000 and $65,000 USD annually, while in Canada, the range is typically $50,000 to $75,000 CAD ($36,000-$55,000 USD). European salaries show diversity; a fabricator in Germany might earn €35,000-€55,000 ($38,000-$60,000 USD), whereas in the UK, it's £28,000-£40,000 ($35,000-$50,000 USD).
In Asia-Pacific, Australia offers competitive salaries of AUD $60,000-$80,000 ($40,000-$54,000 USD), while Japan's range is ¥3,500,000-¥5,500,000 ($23,000-$37,000 USD), with higher purchasing power in local terms. Latin American countries like Brazil typically offer R$35,000-R$60,000 ($7,000-$12,000 USD), but with a much lower cost of living.
Salary structures also differ. European countries often include more robust benefits, like extended vacation and comprehensive healthcare, within the base salary. North America might see more overtime opportunities. Tax implications also impact take-home pay; for instance, Scandinavian countries have higher taxes but provide extensive social services. Experience and specialized skills, such as TIG welding or CNC machine operation, consistently command higher international compensation.
Remote Work
Metal Fabricators perform hands-on work, making traditional remote work largely impossible. The role requires physical presence with machinery, materials, and safety protocols in a workshop or industrial setting. Therefore, digital nomad opportunities or fully remote positions do not exist for this specific role.
However, some related functions, like design or project management for fabrication shops, may offer hybrid or remote options for engineers or managers, not the fabricator themselves. International collaboration for fabricators occurs on-site, often through large-scale construction or manufacturing projects that temporarily relocate teams. Companies typically do not have policies for international remote work for this role due to its inherent physical nature.
Visa & Immigration
Skilled Metal Fabricators often qualify for skilled worker visas in countries with labor shortages. Popular destinations include Canada (Express Entry), Australia (Skilled Nominated Visa 190, Skilled Regional Visa 491), Germany (Skilled Immigration Act), and the UK (Skilled Worker visa). These visas usually require a job offer, relevant experience, and sometimes a skills assessment.
Education credential recognition is crucial; trade qualifications must meet destination country standards. Professional licensing is generally not required for fabricators, but specific welding certifications (e.g., ASME, EN standards) are often mandatory for employment. The typical visa timeline can range from 3 to 12 months, depending on the country and visa type.
Some countries offer pathways to permanent residency after several years of skilled work. Language requirements, such as English for Canada or Australia, or German for Germany, may apply. Family visas are often available for spouses and dependents accompanying the primary applicant. Intra-company transfers are less common for fabricators unless part of a specialized project team.
2025 Market Reality for Metal Fabricators
Understanding the current market reality for metal fabricators is vital for successful career navigation. This field has seen significant evolution from 2023 to 2025, driven by technological advancements and shifting economic landscapes. The post-pandemic environment accelerated automation in manufacturing, directly influencing the skills employers seek. Broader economic factors like inflation and supply chain stability also dictate project volumes and, consequently, hiring needs.
Market realities vary considerably based on experience level, with highly skilled, certified fabricators commanding better opportunities than entry-level workers. Geographic region matters immensely, as demand concentrates in industrial centers. Company size also plays a role, with larger manufacturers often investing more in automation. This analysis provides an honest assessment, preparing job seekers for the practical realities of the current metal fabrication market.
Current Challenges
Metal fabricators face increased competition, especially for entry-level roles, as some tasks become more automated. Economic uncertainty can slow down large-scale construction or manufacturing projects, directly impacting demand. Furthermore, a skill gap exists as employers seek fabricators proficient with advanced machinery and digital blueprints, which many traditional training programs do not fully cover. Job searches can extend for several weeks, particularly for specialized positions.
Growth Opportunities
Despite challenges, strong opportunities exist for metal fabricators with specific skill sets. Roles focused on custom fabrication, specialized welding (e.g., TIG, orbital), and advanced materials (e.g., composites, exotic alloys) are in high demand. Fabricators proficient in operating and programming CNC plasma cutters, laser cutters, and robotic welding cells find excellent prospects. These emerging roles require a blend of traditional craftsmanship and modern technological literacy.
Professionals can gain an advantage by pursuing certifications in advanced manufacturing technologies or specific software platforms. Underserved markets often include smaller, specialized shops needing versatile fabricators, or regions with a burgeoning renewable energy sector requiring custom metal components. Expertise in quality control, inspection, or even light maintenance of fabrication machinery also provides a competitive edge. Strategic career moves involve targeting industries like aerospace, defense, or medical device manufacturing, which often require precision fabrication and offer more stable employment. Investing in continuous learning, especially in automation and digital design tools, positions fabricators for long-term success in an evolving market.
Current Market Trends
Demand for skilled metal fabricators remains stable but highly specialized as of 2025. Industrial and commercial construction sectors show consistent need, alongside custom fabrication shops. However, the market increasingly favors fabricators who can operate advanced CNC machinery and interpret complex digital designs, moving beyond traditional manual techniques. The integration of robotics and automation in larger facilities means fewer fabricators are needed for repetitive tasks, shifting the focus to maintenance, programming, and quality control roles.
Economic conditions, particularly interest rates affecting construction and manufacturing investments, influence job availability. While widespread layoffs have not hit this sector broadly, project-based hiring introduces some volatility. Generative AI, while not directly fabricating, assists in design optimization and material waste reduction, impacting the efficiency expected from human fabricators. Employers now prioritize adaptability and a willingness to learn new software and machine interfaces. Salary trends show a premium for those with certifications in specialized welding, advanced CAD/CAM software, or robotic welding operations, while general fabrication roles see modest increases. Market saturation appears more pronounced at the entry level without specialized skills. Geographically, demand is strongest in industrial hubs and areas with ongoing infrastructure development, such as the Midwest and parts of the South. Remote work is not applicable to this hands-on profession, maintaining localized market dynamics. Demand often peaks with construction seasons and large project cycles.
Emerging Specializations
The metal fabrication industry stands on the cusp of significant transformation, driven by advancements in automation, materials science, and digital manufacturing. These evolving technologies are creating entirely new specialization opportunities for skilled metal fabricators. Understanding these future-oriented career paths allows professionals to strategically position themselves for next-generation roles.
Early positioning in these emerging areas can provide a substantial advantage for career advancement from 2025 onwards. Such specialized skills often command premium compensation and open doors to leadership roles in innovative manufacturing environments. While established fabrication techniques remain crucial, investing in cutting-edge skills ensures long-term career resilience and growth.
Many emerging areas, particularly those involving advanced robotics or additive manufacturing, are currently in a high-growth phase. They are expected to transition from niche specializations to mainstream job opportunities within the next five to ten years, creating a significant demand for uniquely skilled individuals. Pursuing these specializations involves a balance of risk and reward; while the initial investment in training may be higher, the potential for career acceleration and competitive earnings is considerable.
Robotic Fabrication & Automation Specialist
This specialization focuses on the programming, operation, and maintenance of robotic welding and fabrication systems. As automation becomes more prevalent in manufacturing, fabricators who can integrate and optimize robotic workflows are in high demand. This role goes beyond simple machine operation, requiring an understanding of robotic kinematics, sensor integration, and system troubleshooting to ensure precision and efficiency in high-volume production.
Metal Additive Manufacturing Technician
Additive manufacturing, particularly with metals (e.g., DMLS, SLM), is revolutionizing how complex metal components are produced. A specialist in this area manages the entire 3D printing process, from preparing digital models and selecting appropriate metal powders to operating sophisticated printers and post-processing the printed parts. This involves a deep understanding of material properties and print parameters to achieve desired mechanical characteristics and surface finishes.
Sustainable Fabrication & Recycling Specialist
With increasing emphasis on sustainable practices, fabricators specializing in eco-friendly processes focus on minimizing waste, optimizing material usage, and implementing energy-efficient fabrication methods. This includes expertise in recycling metal scrap, designing for disassembly, and utilizing low-emission welding or cutting technologies. They also understand the lifecycle assessment of fabricated products, contributing to a circular economy in metal manufacturing.
Digital Quality Control & Metrology Technician
This role centers on using advanced metrology tools and digital inspection techniques to ensure the highest quality and precision in fabricated components. Specialists employ technologies like laser scanners, CMMs (Coordinate Measuring Machines), and digital imaging to perform non-contact measurements and identify defects. They interpret complex data to provide feedback for process optimization, crucial for industries like aerospace and medical devices.
Fiber Laser System Operator & Programmer
Fiber laser technology is transforming cutting, welding, and marking processes in metal fabrication due to its speed, precision, and energy efficiency. A fiber laser specialist operates and optimizes these advanced machines, understanding beam characteristics, material interactions, and safety protocols. This role requires the ability to troubleshoot complex laser systems and adapt parameters for various metal types and thicknesses, pushing the boundaries of what is possible in metal shaping.
Pros & Cons of Being a Metal Fabricator
Making informed career choices requires understanding both the rewarding aspects and the significant challenges of a profession. The experience of a Metal Fabricator can vary widely depending on the specific company, the industry sector, and the specialization within fabrication, such as structural, artistic, or precision work. Factors like company culture, project complexity, and individual personality can also influence how a fabricator perceives their daily work. Furthermore, the pros and cons may shift at different career stages; for example, physical demands might be more pronounced in early career, while leadership challenges emerge at senior levels. Some aspects, like the hands-on nature of the work, might be a pro for one person and a con for another. This assessment provides an honest, balanced perspective to help set realistic expectations for anyone considering a career in metal fabrication.
Pros
- Metal fabricators create tangible products from raw materials, offering a strong sense of accomplishment and visible results for their efforts in constructing everything from intricate parts to large structures.
- Skilled metal fabricators are consistently in demand across various industries, including construction, manufacturing, aerospace, and automotive, providing good job security and diverse employment opportunities.
- The work is hands-on and dynamic, involving a variety of tasks such as cutting, shaping, welding, and assembling, which keeps the job engaging and prevents monotony for those who enjoy working with their hands.
- There is a clear path for skill development and specialization, allowing fabricators to advance their expertise in areas like advanced welding techniques, blueprint reading, or operating CNC machinery, leading to higher earning potential.
- Many fabricators learn valuable, transferable skills that are highly sought after, enabling them to transition into roles like welding inspection, project management, or even starting their own fabrication businesses.
- Entry into the field often does not require a four-year degree, with many successful fabricators learning through vocational training, apprenticeships, or on-the-job experience, making it accessible to a broader range of individuals.
- The problem-solving aspect of fitting pieces together, troubleshooting designs, and achieving precise specifications provides intellectual stimulation and a continuous learning environment.
Cons
- The work environment often includes exposure to loud noises from machinery, sparks, fumes, and intense heat, which necessitates strict adherence to safety protocols and can be physically demanding.
- Metal fabrication is a physically demanding job that involves heavy lifting, prolonged standing, bending, and repetitive motions, increasing the risk of musculoskeletal injuries and general fatigue over time.
- The job often requires working irregular hours, including evenings, weekends, or overtime, especially when meeting tight production deadlines or handling urgent client orders.
- The learning curve is continuous, as fabricators must stay updated with new welding techniques, machinery, and material properties, requiring ongoing training and skill refinement.
- The precision required for quality work means mistakes can be costly in terms of time and materials, leading to pressure and the need for meticulous attention to detail.
- While initial entry may not require extensive formal education, career advancement to supervisory or specialized roles often depends on acquiring advanced certifications or specialized training.
- The demand for metal fabricators can fluctuate with economic conditions and the health of industries like construction or manufacturing, potentially affecting job security in some regions.
Frequently Asked Questions
Metal Fabricators face distinct questions about the hands-on nature of the work, safety, and the path to gaining specialized skills. This section addresses common concerns about entry requirements, physical demands, and career growth within this precise trade.
What are the common entry requirements and educational paths to become a Metal Fabricator?
Most Metal Fabricators start with vocational training, an apprenticeship, or a combination of both. Vocational schools offer programs lasting from a few months to two years, covering welding, blueprint reading, and various fabrication techniques. Apprenticeships provide on-the-job training, often lasting 3-5 years, where you learn directly from experienced professionals while earning a wage.
Can I become a Metal Fabricator without a college degree?
Yes, many Metal Fabricators successfully enter the field without a traditional four-year degree. Employers prioritize practical skills, certifications (especially in welding), and demonstrated experience. A strong portfolio of projects or successful completion of a vocational program often carries more weight than a bachelor's degree in this trade.
How long does it typically take to become a proficient Metal Fabricator?
The time to become job-ready varies. With a focused vocational program, you could be ready for an entry-level position in 6-12 months. An apprenticeship typically takes 3-5 years to complete, providing a more comprehensive skill set and higher earning potential upon completion. Your dedication to practice and learning significantly impacts this timeline.
What are the typical salary expectations for a Metal Fabricator?
Starting salaries for entry-level Metal Fabricators vary by location and experience, but generally range from $35,000 to $45,000 annually. Experienced fabricators with specialized skills, such as advanced welding or CNC operation, can earn significantly more, often exceeding $60,000 to $75,000 per year. Overtime opportunities also increase earning potential.
What is the typical work-life balance and physical demand like for a Metal Fabricator?
The work-life balance for a Metal Fabricator often involves standard daytime hours, but project deadlines or specialized jobs might require overtime, including evenings or weekends. The work is physically demanding, requiring strength, stamina, and attention to detail, which can impact personal energy levels outside of work. Safety is paramount, and adherence to protocols is critical.
Is the Metal Fabricator role secure given advancements in automation and technology?
The job market for skilled Metal Fabricators remains stable due to ongoing demand in manufacturing, construction, and custom fabrication. While some tasks may become automated, the need for skilled individuals who can interpret blueprints, problem-solve, and perform complex welds or assemblies persists. Specializing in niche areas like aerospace or artistic fabrication can enhance job security.
What are the opportunities for career growth and advancement as a Metal Fabricator?
Career growth for Metal Fabricators often involves specializing in advanced welding techniques, becoming a certified welding inspector, or moving into supervisory or management roles. Some fabricators transition into design, project management, or even start their own custom fabrication businesses. Continuous learning and certifications open doors to higher-paying and more complex opportunities.
Are there remote work opportunities available for Metal Fabricators?
The majority of Metal Fabricator roles require on-site presence due to the need for specialized equipment, heavy machinery, and collaborative work environments. While some administrative or design aspects might be done remotely, the core fabrication work is hands-on and location-dependent. Therefore, remote work options are very limited for this specific trade.
Related Careers
Explore similar roles that might align with your interests and skills:
Fabricator
A growing field with similar skill requirements and career progression opportunities.
Explore career guideMetal Worker
A growing field with similar skill requirements and career progression opportunities.
Explore career guideWelder Fabricator
A growing field with similar skill requirements and career progression opportunities.
Explore career guideSheet Metal Fabricator
A growing field with similar skill requirements and career progression opportunities.
Explore career guideSteel Fabricator
A growing field with similar skill requirements and career progression opportunities.
Explore career guideAssess your Metal Fabricator readiness
Understanding where you stand today is the first step toward your career goals. Our Career Coach helps identify skill gaps and create personalized plans.
Skills Gap Analysis
Get a detailed assessment of your current skills versus Metal Fabricator requirements. Our AI Career Coach identifies specific areas for improvement with personalized recommendations.
See your skills gapCareer Readiness Assessment
Evaluate your overall readiness for Metal Fabricator roles with our AI Career Coach. Receive personalized recommendations for education, projects, and experience to boost your competitiveness.
Assess your readinessSimple pricing, powerful features
Upgrade to Himalayas Plus and turbocharge your job search.
Himalayas
Himalayas Plus
Himalayas Max
Find your dream job
Sign up now and join over 100,000 remote workers who receive personalized job alerts, curated job matches, and more for free!
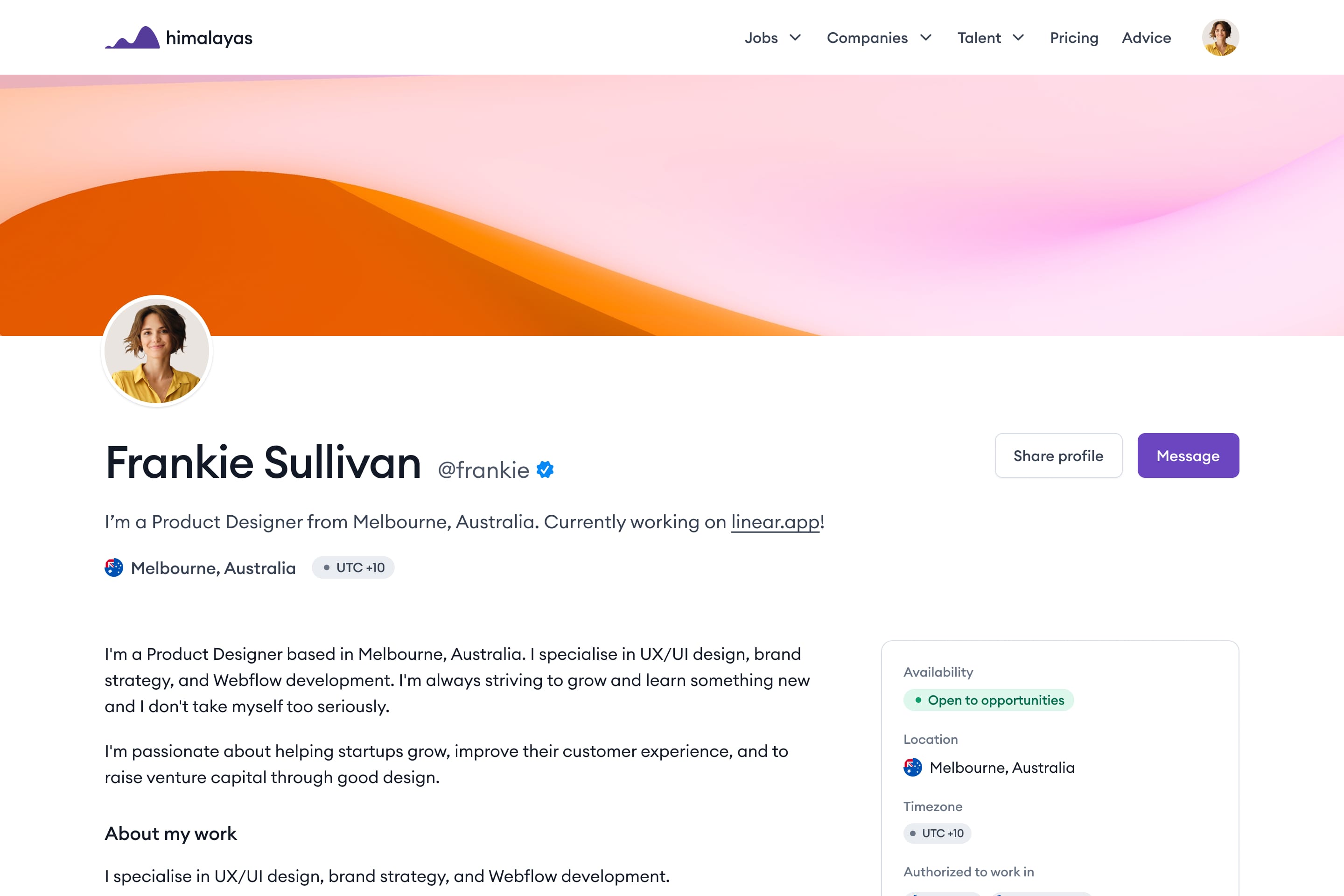