Complete Bridge Ironworker Helper Career Guide
A Bridge Ironworker Helper plays a vital role in constructing and maintaining the foundational infrastructure that connects our communities. You'll assist skilled ironworkers in assembling the massive steel skeletons of bridges, learning hands-on while contributing to structures that stand for decades. This path offers a unique blend of physical challenge, teamwork, and the satisfaction of building something tangible and essential.
Key Facts & Statistics
Median Salary
$60,700 USD
(for Structural Iron and Steel Workers, May 2023, BLS)
Range: $35k - $80k+ USD (entry-level helper to experienced ironworker, varies by location and union)
Growth Outlook
5%
as fast as average (for Structural Iron and Steel Workers, 2022-2032, BLS)
Annual Openings
≈2,300
openings annually (for Structural Iron and Steel Workers, including helpers, BLS)
Top Industries
Typical Education
High school diploma or equivalent, often followed by an apprenticeship or on-the-job training
What is a Bridge Ironworker Helper?
A Bridge Ironworker Helper provides essential support to skilled ironworkers during the construction and repair of bridges. This role is fundamental to ensuring the efficient and safe assembly of structural steel components. Helpers assist with material handling, tool management, and basic rigging, learning the trade under direct supervision. Their contributions allow experienced ironworkers to focus on the intricate and precise tasks of connecting and welding steel.
This helper role is distinct from a fully qualified Ironworker, who possesses certifications and extensive experience in complex structural erection, welding, and rigging. It also differs from a general construction laborer, as Bridge Ironworker Helpers focus specifically on steel structures and receive specialized training relevant to ironwork. They are crucial for maintaining workflow and safety on bridge projects, acting as the backbone of the ironworking crew.
What does a Bridge Ironworker Helper do?
Key Responsibilities
- Assist experienced ironworkers in positioning and connecting steel beams, girders, and columns for bridge construction using various hand tools and power equipment.
- Operate and maintain a variety of tools, including impact wrenches, torque wrenches, rebar cutters, and grinders, ensuring they are clean and in good working order.
- Move and secure materials, such as rebar, structural steel components, and rigging equipment, to designated work areas using dollies, hoists, and manual lifting techniques.
- Prepare work sites by setting up safety barricades, erecting temporary structures, and ensuring all necessary equipment and materials are readily available.
- Perform basic rigging tasks, including attaching slings and cables to steel components, under direct supervision, to facilitate safe lifting and placement.
- Clean and maintain the work area, removing debris, scrap materials, and potential hazards to ensure a safe and organized environment for all team members.
- Follow all safety protocols and procedures rigorously, including wearing appropriate personal protective equipment (PPE) and participating in daily safety briefings.
Work Environment
Bridge Ironworker Helpers work outdoors on active construction sites, exposed to various weather conditions, including extreme heat, cold, wind, and rain. The work involves significant physical exertion, including heavy lifting, climbing, bending, and working at heights on scaffolding, temporary platforms, or the bridge structure itself. The environment is often noisy due to machinery and construction activities. They work as part of a team, closely collaborating with experienced ironworkers, welders, and other tradespeople. Project schedules can be demanding, often requiring early mornings, long shifts, and sometimes weekend work to meet deadlines. Safety is paramount, with strict adherence to protocols and continuous vigilance required.
Tools & Technologies
Bridge Ironworker Helpers regularly use a range of hand tools such as spud wrenches, torque wrenches, and rebar benders. Power tools include impact wrenches, grinders, and cutting torches for preparing and fitting steel components. They also work with various rigging equipment, including slings, chains, and cables, to move heavy materials safely. Knowledge of basic measuring tools, such as tape measures and levels, is essential for accurate placement. While not directly operating heavy machinery, they often assist operators of cranes, forklifts, and aerial lifts, requiring familiarity with their operation and safety zones. Communication tools like two-way radios are critical for coordinating with team members on large bridge sites.
Bridge Ironworker Helper Skills & Qualifications
A Bridge Ironworker Helper assists skilled ironworkers in the construction, repair, and maintenance of bridges. This role is physically demanding and requires a strong understanding of safety protocols and basic construction techniques. Helpers learn on the job, gaining practical experience in rigging, welding, bolting, and operating various tools under direct supervision.
Requirements for a Bridge Ironworker Helper vary significantly by seniority and project complexity. Entry-level helpers primarily focus on material handling, site preparation, and basic tool operation. As experience grows, helpers take on more complex tasks, eventually progressing to journeyman ironworker roles. Formal education is less critical than practical experience and certifications in this field. Many enter through apprenticeships or union helper programs, which combine on-the-job training with classroom instruction.
Certifications like OSHA 10 or OSHA 30 are often mandatory before stepping onto a job site. Specialized certifications in rigging, signaling, or specific equipment operation add significant value. The skill landscape is evolving with increasing emphasis on safety compliance and the use of advanced equipment for efficiency. Prioritizing physical conditioning, safety training, and a willingness to learn practical skills are crucial for success in this role.
Education Requirements
Technical Skills
- Reading and interpreting blueprints and structural drawings (basic level)
- Safe operation of hand and power tools (e.g., wrenches, grinders, drills, cutting torches)
- Basic rigging and signaling for crane operations (hand signals, taglines)
- Material handling and identification of various steel components (beams, plates, bolts)
- Knowledge of fall protection systems and proper harness usage
- Basic welding and cutting techniques (e.g., oxy-fuel cutting, stick welding - often observed or assisted)
- Site preparation and cleanup procedures
- Understanding of construction site safety regulations and PPE requirements
- Bolt-up procedures and torque wrench operation
- Scaffolding erection and dismantling (basic assistance)
Soft Skills
- Safety Consciousness: Critical for recognizing hazards and adhering to strict safety protocols on bridge construction sites.
- Physical Stamina: Essential for performing strenuous tasks, lifting heavy materials, and working long hours in various weather conditions.
- Teamwork and Collaboration: Necessary for working effectively with ironworkers, crane operators, and other crew members to complete complex tasks safely.
- Attention to Detail: Important for accurately following instructions, identifying correct materials, and ensuring precise measurements in structural work.
- Problem-Solving Aptitude: Useful for quickly adapting to unexpected site conditions or equipment issues and finding practical solutions.
- Reliability and Dependability: Crucial for showing up on time, completing assigned tasks, and being a trustworthy part of the crew.
- Adaptability: Key for adjusting to changing work schedules, project requirements, and different types of bridge structures.
- Effective Communication: Important for clearly conveying information, asking questions, and reporting issues to supervisors and teammates, especially regarding safety and progress.
How to Become a Bridge Ironworker Helper
Entering the Bridge Ironworker Helper field offers a robust pathway into the skilled trades, primarily through apprenticeships and direct entry-level positions. While formal degrees are not typically required, a strong work ethic, physical stamina, and a commitment to safety are paramount. Geographic location significantly impacts opportunities; major infrastructure projects in urban centers or states with extensive bridge networks will have more openings than rural areas.
Many helpers start by gaining basic construction experience, often through general labor roles, which provides a foundational understanding of job site dynamics and safety protocols. The timeline to become a helper can be relatively quick, sometimes within a few months of active searching and networking, especially for those willing to relocate or work on large-scale projects. Progression to a full ironworker often involves a multi-year apprenticeship, which is a paid training program combining on-the-job experience with classroom instruction.
Misconceptions often include believing that only those with prior construction experience can enter; many companies and unions are open to training motivated individuals from scratch. Networking with current ironworkers, attending local union meetings, and directly contacting construction companies specializing in bridge work are crucial steps. The hiring landscape values reliability, eagerness to learn, and adherence to safety regulations above all else, making it an accessible field for dedicated individuals.
Research and understand the physical demands and safety requirements of ironworking. This includes knowing the risks involved with working at heights, with heavy materials, and in various weather conditions. Familiarize yourself with basic construction safety principles, such as OSHA 10-hour certification, which is often a prerequisite or highly recommended.
Gain foundational general labor or construction experience to demonstrate reliability and a basic understanding of job sites. Seek roles involving manual labor, material handling, or assisting skilled tradespeople. This experience proves your willingness to work hard and adapt to construction environments, even if it is not directly in ironworking.
Obtain essential certifications and licenses, such as a valid driver's license and, if required, a commercial driver's license (CDL) for transporting equipment. Many entry-level positions also benefit from certifications in first aid, CPR, or specific equipment operation like forklifts or aerial lifts, increasing your versatility.
Network with local ironworker unions, contractors specializing in bridge construction, and experienced ironworkers. Attend union meetings, industry job fairs, or career events where you can meet people in the field. Personal connections often lead to direct opportunities for helper positions or recommendations for apprenticeship programs.
Prepare a focused resume highlighting any physical labor experience, safety training, and certifications. Tailor your application materials to emphasize your strong work ethic, reliability, and eagerness to learn the trade. Clearly state your interest in a Bridge Ironworker Helper role and your commitment to a career in ironworking.
Actively apply for Bridge Ironworker Helper positions with construction companies, general contractors, and through local ironworker union halls. Be persistent in your applications and follow up on submissions. Be prepared for interviews that assess your physical capabilities, attitude towards safety, and commitment to the demanding nature of the job.
Step 1
Research and understand the physical demands and safety requirements of ironworking. This includes knowing the risks involved with working at heights, with heavy materials, and in various weather conditions. Familiarize yourself with basic construction safety principles, such as OSHA 10-hour certification, which is often a prerequisite or highly recommended.
Step 2
Gain foundational general labor or construction experience to demonstrate reliability and a basic understanding of job sites. Seek roles involving manual labor, material handling, or assisting skilled tradespeople. This experience proves your willingness to work hard and adapt to construction environments, even if it is not directly in ironworking.
Step 3
Obtain essential certifications and licenses, such as a valid driver's license and, if required, a commercial driver's license (CDL) for transporting equipment. Many entry-level positions also benefit from certifications in first aid, CPR, or specific equipment operation like forklifts or aerial lifts, increasing your versatility.
Step 4
Network with local ironworker unions, contractors specializing in bridge construction, and experienced ironworkers. Attend union meetings, industry job fairs, or career events where you can meet people in the field. Personal connections often lead to direct opportunities for helper positions or recommendations for apprenticeship programs.
Step 5
Prepare a focused resume highlighting any physical labor experience, safety training, and certifications. Tailor your application materials to emphasize your strong work ethic, reliability, and eagerness to learn the trade. Clearly state your interest in a Bridge Ironworker Helper role and your commitment to a career in ironworking.
Step 6
Actively apply for Bridge Ironworker Helper positions with construction companies, general contractors, and through local ironworker union halls. Be persistent in your applications and follow up on submissions. Be prepared for interviews that assess your physical capabilities, attitude towards safety, and commitment to the demanding nature of the job.
Education & Training Needed to Become a Bridge Ironworker Helper
Becoming a Bridge Ironworker Helper primarily involves hands-on training rather than formal degree programs. Most individuals enter this field through apprenticeships or direct entry-level positions within construction companies or unions. These pathways provide the essential practical skills and safety knowledge required for working on bridge construction and repair.
Formal degrees are not typically required for this role, unlike many other construction specializations. Instead, the focus is on vocational training, certifications, and on-the-job learning. Apprenticeships, often lasting 3-4 years, are the most comprehensive route, combining classroom instruction with extensive paid work experience. These programs can cost anywhere from minimal fees (e.g., $500-$2,000 for materials and union dues) to being fully sponsored by the union or employer. Self-study or short-term courses, while less common for full entry, might cover specific safety certifications like OSHA 10 or 30, which are typically under $200 and can be completed in a few days.
Employers highly value practical experience and safety certifications. Apprenticeships are often seen as the gold standard, ensuring a well-rounded skill set and adherence to industry standards. Continuous learning in safety protocols, new construction techniques, and equipment operation remains crucial throughout a career. The educational needs for a Bridge Ironworker Helper are distinct from a certified Ironworker, focusing more on foundational support, material handling, and basic rigging, rather than advanced welding or structural assembly. The cost-benefit analysis strongly favors apprenticeships due to their paid training component and high job placement rates upon completion.
Bridge Ironworker Helper Salary & Outlook
Compensation for a Bridge Ironworker Helper varies significantly based on several factors, extending beyond just the base hourly wage. Geographic location plays a crucial role, with higher wages typically found in metropolitan areas or regions with extensive infrastructure projects. These areas often have a higher cost of living and increased demand for skilled trades.
Years of experience and the acquisition of specialized skills, such as welding certifications or advanced rigging, dramatically increase earning potential. Total compensation packages frequently include benefits like health insurance, retirement plans (often union-backed pensions), and sometimes per diem for travel to remote job sites. Performance bonuses are less common in this field, but consistent work and reliability can lead to more opportunities and quicker advancement.
Industry-specific trends, such as federal infrastructure spending or large-scale private developments, directly influence salary growth. Union membership often provides standardized wage scales and benefits, which can differ from non-union compensation. Remote work is not applicable for this hands-on role. While salary figures are presented in USD, international markets have their own distinct compensation structures and demand patterns for bridge construction.
Salary by Experience Level
Level | US Median | US Average |
---|---|---|
Bridge Ironworker Helper | $36k USD | $38k USD |
Apprentice Bridge Ironworker | $45k USD | $47k USD |
Bridge Ironworker | $62k USD | $65k USD |
Senior Bridge Ironworker | $75k USD | $78k USD |
Lead Bridge Ironworker | $85k USD | $88k USD |
Foreman (Bridge Ironwork) | $92k USD | $95k USD |
Superintendent (Bridge Ironwork) | $105k USD | $110k USD |
Market Commentary
The job market for Bridge Ironworker Helpers shows a steady demand, primarily driven by ongoing infrastructure repair and new construction projects across the United States. Projections indicate a stable outlook for ironworkers, including those focused on bridges, as the nation addresses aging infrastructure. Government funding initiatives, such as the Infrastructure Investment and Jobs Act, provide a significant boost to this sector, ensuring a consistent pipeline of work for the foreseeable future.
Demand for skilled labor in bridge construction often outstrips supply, especially for experienced ironworkers. This imbalance can lead to competitive wages and benefits packages for qualified individuals. Emerging opportunities include projects involving advanced materials and construction techniques, requiring continuous learning and adaptation to new methods. Automation and AI have minimal impact on the hands-on nature of this role, making it relatively resistant to technological displacement.
This profession is somewhat cyclical, tied to economic health and government spending, but essential infrastructure needs provide a baseline of recession resistance. Geographic hotspots for bridge ironwork include regions with major river crossings, coastal areas, and states with high population growth. Future-proofing in this career involves mastering diverse rigging techniques, welding certifications, and adherence to stringent safety protocols, ensuring adaptability across various project types.
Bridge Ironworker Helper Career Path
Career progression for a Bridge Ironworker Helper involves a structured path from entry-level support to seasoned leadership. Advancement hinges on acquiring specialized skills in structural steel erection, safety compliance, and heavy equipment operation. The field distinctly separates individual contributor (IC) tracks, focusing on hands-on construction, from management tracks, which involve overseeing projects and teams.
Advancement speed depends on several factors: consistent performance, mastery of complex techniques, and dedication to safety protocols. Obtaining specific certifications, particularly in welding or rigging, significantly accelerates progression. Company size also plays a role; larger firms may offer more structured apprenticeship programs and diverse project types, while smaller companies might provide faster exposure to varied tasks.
Networking within the construction industry, seeking mentorship from experienced ironworkers, and maintaining an impeccable safety record are crucial for career growth. Lateral moves often involve specializing in areas like welding, rigging, or prefabrication. This field emphasizes continuous learning, adapting to new technologies, and a deep understanding of structural integrity to ensure long-term success.
Bridge Ironworker Helper
0-1 yearAssist experienced ironworkers by moving materials, preparing tools, and maintaining a clean work area. Learn fundamental safety procedures and site protocols. Work under direct supervision, with minimal decision-making authority, primarily focusing on task execution and support.
Key Focus Areas
Develop foundational safety knowledge, including hazard recognition and proper use of personal protective equipment. Master basic tool handling, material identification, and site organization. Focus on active listening and following instructions precisely to support experienced ironworkers effectively.
Apprentice Bridge Ironworker
1-4 yearsParticipate in the erection of structural steel components, performing tasks such as bolting, welding, and connecting beams. Work under the guidance of journeymen, gaining practical experience and contributing to project segments. Begin to understand the sequence of operations and material flow.
Key Focus Areas
Acquire practical skills in bolt-up, welding, and rigging techniques through hands-on training. Understand blueprints and structural drawings, learning to interpret specifications for steel erection. Develop a strong commitment to safety regulations and quality workmanship.
Bridge Ironworker
4-8 yearsIndependently perform a wide range of tasks in structural steel erection, including connecting, bolting, welding, and rigging. Interpret complex blueprints and execute work according to specifications. Contribute significantly to project milestones, often guiding apprentices and ensuring quality standards.
Key Focus Areas
Master advanced rigging, welding, and erection techniques, becoming proficient in complex structural assemblies. Develop problem-solving skills for on-site challenges and unforeseen structural issues. Cultivate strong teamwork and communication skills to coordinate effectively with the crew.
Senior Bridge Ironworker
8-12 yearsLead specific segments of structural erection projects, ensuring adherence to design specifications and safety standards. Provide technical guidance and on-the-job training to less experienced team members. Take ownership of critical tasks and contribute to planning daily operations.
Key Focus Areas
Refine expertise in specialized ironwork techniques, such as heavy lift planning or complex structural alterations. Mentor junior ironworkers, providing guidance and technical instruction. Begin developing leadership qualities and an understanding of project timelines and resource allocation.
Lead Bridge Ironworker
12-16 yearsDirect a small crew of ironworkers, assigning tasks, monitoring progress, and ensuring work aligns with project plans. Oversee specific work zones or structural components, ensuring safety compliance and quality control. Report progress and issues to the Foreman, making immediate operational decisions.
Key Focus Areas
Develop strong leadership skills, including delegation, conflict resolution, and performance management. Enhance planning and organizational capabilities to manage daily tasks and project sequences. Improve communication skills for effective interaction with foremen, engineers, and crew members.
Foreman (Bridge Ironwork)
16-20 yearsManage and supervise multiple crews or a significant portion of a bridge construction project. Responsible for daily operations, safety enforcement, quality assurance, and adherence to project schedules. Act as the primary liaison between the Superintendent and the on-site ironworker teams.
Key Focus Areas
Master project management principles, including scheduling, budgeting, and resource allocation. Develop advanced problem-solving and decision-making skills under pressure. Cultivate strong interpersonal and negotiation skills for managing crew, subcontractors, and site management.
Superintendent (Bridge Ironwork)
20+ yearsOversee the entire bridge ironwork aspect of large-scale construction projects, including planning, budgeting, staffing, and execution. Ensure project completion on time, within budget, and to the highest quality and safety standards. Manage all personnel and resources, making critical strategic decisions.
Key Focus Areas
Acquire executive-level leadership, strategic planning, and financial management skills. Develop a comprehensive understanding of contracts, regulatory compliance, and risk management. Cultivate strong stakeholder management and communication abilities for high-level interactions.
Bridge Ironworker Helper
0-1 yearAssist experienced ironworkers by moving materials, preparing tools, and maintaining a clean work area. Learn fundamental safety procedures and site protocols. Work under direct supervision, with minimal decision-making authority, primarily focusing on task execution and support.
Key Focus Areas
Develop foundational safety knowledge, including hazard recognition and proper use of personal protective equipment. Master basic tool handling, material identification, and site organization. Focus on active listening and following instructions precisely to support experienced ironworkers effectively.
Apprentice Bridge Ironworker
1-4 yearsParticipate in the erection of structural steel components, performing tasks such as bolting, welding, and connecting beams. Work under the guidance of journeymen, gaining practical experience and contributing to project segments. Begin to understand the sequence of operations and material flow.
Key Focus Areas
Acquire practical skills in bolt-up, welding, and rigging techniques through hands-on training. Understand blueprints and structural drawings, learning to interpret specifications for steel erection. Develop a strong commitment to safety regulations and quality workmanship.
Bridge Ironworker
4-8 yearsIndependently perform a wide range of tasks in structural steel erection, including connecting, bolting, welding, and rigging. Interpret complex blueprints and execute work according to specifications. Contribute significantly to project milestones, often guiding apprentices and ensuring quality standards.
Key Focus Areas
Master advanced rigging, welding, and erection techniques, becoming proficient in complex structural assemblies. Develop problem-solving skills for on-site challenges and unforeseen structural issues. Cultivate strong teamwork and communication skills to coordinate effectively with the crew.
Senior Bridge Ironworker
8-12 yearsLead specific segments of structural erection projects, ensuring adherence to design specifications and safety standards. Provide technical guidance and on-the-job training to less experienced team members. Take ownership of critical tasks and contribute to planning daily operations.
Key Focus Areas
Refine expertise in specialized ironwork techniques, such as heavy lift planning or complex structural alterations. Mentor junior ironworkers, providing guidance and technical instruction. Begin developing leadership qualities and an understanding of project timelines and resource allocation.
Lead Bridge Ironworker
12-16 yearsDirect a small crew of ironworkers, assigning tasks, monitoring progress, and ensuring work aligns with project plans. Oversee specific work zones or structural components, ensuring safety compliance and quality control. Report progress and issues to the Foreman, making immediate operational decisions.
Key Focus Areas
Develop strong leadership skills, including delegation, conflict resolution, and performance management. Enhance planning and organizational capabilities to manage daily tasks and project sequences. Improve communication skills for effective interaction with foremen, engineers, and crew members.
Foreman (Bridge Ironwork)
16-20 yearsManage and supervise multiple crews or a significant portion of a bridge construction project. Responsible for daily operations, safety enforcement, quality assurance, and adherence to project schedules. Act as the primary liaison between the Superintendent and the on-site ironworker teams.
Key Focus Areas
Master project management principles, including scheduling, budgeting, and resource allocation. Develop advanced problem-solving and decision-making skills under pressure. Cultivate strong interpersonal and negotiation skills for managing crew, subcontractors, and site management.
Superintendent (Bridge Ironwork)
20+ yearsOversee the entire bridge ironwork aspect of large-scale construction projects, including planning, budgeting, staffing, and execution. Ensure project completion on time, within budget, and to the highest quality and safety standards. Manage all personnel and resources, making critical strategic decisions.
Key Focus Areas
Acquire executive-level leadership, strategic planning, and financial management skills. Develop a comprehensive understanding of contracts, regulatory compliance, and risk management. Cultivate strong stakeholder management and communication abilities for high-level interactions.
Job Application Toolkit
Ace your application with our purpose-built resources:
Bridge Ironworker Helper Resume Examples
Proven layouts and keywords hiring managers scan for.
View examplesBridge Ironworker Helper Cover Letter Examples
Personalizable templates that showcase your impact.
View examplesTop Bridge Ironworker Helper Interview Questions
Practice with the questions asked most often.
View examplesBridge Ironworker Helper Job Description Template
Ready-to-use JD for recruiters and hiring teams.
View examplesGlobal Bridge Ironworker Helper Opportunities
Bridge Ironworker Helpers support the construction and repair of bridges globally. This role involves assisting skilled ironworkers with tasks like rigging, welding, and structural assembly. Demand for infrastructure development worldwide drives a consistent need for these skilled trades. Cultural differences often impact safety protocols and training standards, while regulatory environments dictate project specifications.
Professionals consider international opportunities for higher wages or specialized projects. While formal international certifications are less common, strong practical experience and safety training are highly valued. This helps bridge ironworker helpers adapt to diverse global construction practices.
Global Salaries
Salaries for Bridge Ironworker Helpers vary significantly by region, reflecting economic conditions and union strength. In North America, particularly the United States and Canada, annual salaries range from $40,000 to $70,000 USD, or approximately CAD 55,000 to CAD 95,000. These figures often include robust benefits packages like health insurance, retirement plans, and paid vacation due to strong union representation.
Europe sees varied compensation. In Western European countries like Germany or the UK, helpers might earn €30,000 to €50,000 (approximately $32,000 to $54,000 USD). Southern and Eastern European nations offer lower ranges, often €18,000 to €30,000. Purchasing power often aligns, meaning lower nominal salaries might still provide a comfortable local living standard.
In Asia-Pacific, such as Australia, salaries can be competitive, ranging AUD 50,000 to AUD 80,000 (around $33,000 to $53,000 USD). However, countries like India or Southeast Asian nations typically offer much lower wages, often $5,000 to $15,000 USD annually, but with a significantly lower cost of living. Latin American countries generally fall into similar lower ranges, typically $8,000 to $20,000 USD.
Take-home pay is affected by local tax rates, which differ substantially. For example, Scandinavian countries have higher taxes but often provide extensive social benefits. Experience and specialized skills, like welding certifications, enhance earning potential globally. International pay scales are not standardized, but large international construction firms may offer expatriate packages that include housing allowances or relocation bonuses.
Remote Work
International remote work for Bridge Ironworker Helpers is not feasible. This role is inherently hands-on and requires physical presence at construction sites. The work involves direct assistance with heavy machinery, structural components, and on-site fabrication. Bridge construction demands continuous, collaborative physical labor.
Digital nomad opportunities do not apply to this profession. The nature of the work precludes any form of remote engagement. Employers in this field do not hire internationally for remote positions; they require on-site personnel. There are no platforms or companies known for offering international remote work in this trade.
Salary expectations are tied directly to on-site labor and local market rates. Geographic arbitrage is not relevant as the work cannot be performed from a lower-cost location. Equipment, internet, and workspace setup are all dictated by the physical demands of the bridge construction site.
Visa & Immigration
Bridge Ironworker Helpers seeking international work typically require skilled worker visas. Popular destinations like Canada, Australia, and parts of Europe offer pathways for skilled trades. Requirements often include proof of relevant experience, a job offer from an employer, and sometimes a skills assessment or trade certification from the destination country.
For example, Canada's Express Entry system or specific Provincial Nominee Programs target tradespeople, requiring a job offer and language proficiency. Australia's skilled migration visas also list specific trade occupations. Education credential recognition is less formal than for professional roles, but practical experience and demonstrated competence are critical. Some countries may require specific safety training certifications valid in their jurisdiction.
Visa timelines vary, from a few months to over a year, depending on the country and visa type. Employers often assist with the process, especially for large infrastructure projects. Pathways to permanent residency exist in many developed nations after several years of continuous employment. Language requirements depend on the country; English proficiency is often needed for Anglophone nations, while basic conversational skills in the local language can be beneficial elsewhere.
Practical considerations include securing an employer-sponsored visa, understanding local labor laws, and potentially bringing dependents on family visas. Some countries may have fast-track programs for in-demand construction trades.
2025 Market Reality for Bridge Ironworker Helpers
Understanding current market conditions for a bridge ironworker helper is crucial for navigating this hands-on career. The infrastructure sector, including bridge construction and repair, has seen significant shifts since 2023 due to increased federal funding and a focus on upgrading aging systems.
Broader economic factors directly influence project timelines and funding availability for public works. While AI integration impacts many sectors, its effect on this specific role is less about displacement and more about improving safety and efficiency on job sites. Market realities also vary by geographic region, with more opportunities in states with large infrastructure initiatives. This analysis provides an honest look at the current landscape for helpers.
Current Challenges
Bridge ironworker helpers face significant competition for entry-level roles as project availability fluctuates. Economic uncertainty can delay or halt infrastructure projects, directly impacting job security and creating periods of reduced work. The physical demands and hazardous nature of the work also present ongoing challenges, requiring constant vigilance and strict adherence to safety protocols.
Growth Opportunities
Despite challenges, strong opportunities exist for bridge ironworker helpers, particularly in states with high infrastructure spending and a critical need for bridge repair. Emerging opportunities lie in specialized bridge types, such as those requiring advanced composite materials or complex cable-stayed designs, where helpers can gain valuable niche experience.
Helpers can position themselves advantageously by pursuing certifications in areas like welding, rigging, or specific equipment operation, which are highly valued on bridge crews. Underserved markets in less populated regions or areas with recent natural disasters often present quicker entry points for new helpers. Developing a reputation for reliability, a strong work ethic, and a commitment to safety provides a significant competitive edge.
While economic slowdowns might delay some projects, the long-term need for bridge maintenance and construction remains constant due to the critical nature of these structures. This creates a stable career path for those willing to learn and grow within the trade. Strategic career moves include joining union apprenticeship programs, which offer structured training and clear pathways to journeyman status.
Current Market Trends
Hiring for bridge ironworker helpers in 2025 shows steady demand, driven by ongoing infrastructure investments and the need to repair aging bridges across various regions. Government funding initiatives, such as the Infrastructure Investment and Jobs Act, continue to fuel new projects and maintenance work. This creates a consistent need for skilled support staff on bridge construction and repair crews.
The industry increasingly adopts advanced safety protocols and specialized lifting technologies, which requires helpers to quickly adapt and learn new equipment operation. While AI does not directly impact the physical tasks of a helper, project planning and material logistics increasingly use AI-driven tools, streamlining site operations and potentially changing workflow coordination. Employers prioritize candidates with a strong commitment to safety, basic tool proficiency, and a willingness to learn on the job.
Salary trends for helpers remain stable, often tied to union agreements or prevailing wage rates in specific areas. Remote work is not applicable to this hands-on role. Market strength varies geographically, with higher demand in states undergoing significant infrastructure upgrades or with a large number of aging bridges. Seasonal hiring patterns are common, with more outdoor work available during warmer months, though some indoor or covered projects continue year-round.
Emerging Specializations
Technological advancements and evolving infrastructure demands are consistently creating new specialization opportunities within the skilled trades, particularly for those supporting complex construction like bridge building. Early positioning in these emerging areas is crucial for career advancement in 2025 and beyond. Professionals who adapt to new methods and materials often command premium compensation and experience accelerated career growth.
While established specializations remain vital, pursuing emerging areas offers a strategic advantage. These new niches often become mainstream within five to ten years, generating significant job opportunities as projects adopt innovative solutions. Specializing in cutting-edge areas involves a balance of risk and reward; it requires proactive learning but offers substantial long-term benefits for those prepared to lead change.
Understanding these future-oriented paths allows individuals to strategically invest in new skills and training. This foresight can transform a traditional role into a highly specialized and indispensable position within the evolving construction landscape. The ability to integrate new technologies and techniques directly impacts project efficiency and safety.
Smart Bridge Technology Assistant
Advanced Composites Assembly Helper
Robotics & Automation Support
Sustainable Construction Assistant
AR/VR Field Operations Helper
Pros & Cons of Being a Bridge Ironworker Helper
Making informed career decisions requires understanding both the positive and challenging aspects of a profession. While a career as a Bridge Ironworker Helper offers unique advantages, it also comes with specific demands and potential drawbacks. Individual experiences can vary greatly depending on the specific company, the scale and location of bridge projects, and personal resilience. What one person views as a challenging aspect, another might see as an exciting part of the job. For example, working outdoors might be a pro for some and a con for others. Additionally, the nature of pros and cons can shift as you gain experience and move into more senior roles. This assessment provides an honest, balanced view to help you set realistic expectations for this demanding but vital trade.
Pros
- This career offers a clear path to becoming a skilled ironworker, with on-the-job training and apprenticeship programs that can lead to a highly respected and well-compensated trade.
- Bridge ironworker helpers gain valuable, hands-on experience in structural construction, welding, and rigging, skills that are highly transferable within the construction and infrastructure industries.
- There is a strong sense of accomplishment and pride in contributing to large-scale infrastructure projects like bridges, which are vital to communities and visible for decades.
- The demand for skilled tradespeople in infrastructure development and repair remains consistent, providing good job security for those with the necessary skills and certifications.
- Many bridge projects are unionized, offering competitive wages, comprehensive health benefits, and robust retirement plans for members, which can be a significant advantage over non-unionized construction roles.
- The work is primarily outdoors, offering a dynamic environment and avoiding the monotony of an office setting, which appeals to individuals who prefer physical activity and fresh air.
- You work as part of a close-knit team, fostering strong camaraderie and mutual support, which can make challenging tasks more manageable and enjoyable.
Cons
- This role involves significant physical strain and repetitive heavy lifting, leading to a high risk of musculoskeletal injuries over time.
- Working at heights on bridges can be inherently dangerous, with risks of falls, falling objects, and severe weather exposure. Safety protocols are strict, but accidents can still occur.
- The work is often seasonal or project-based, leading to periods of unemployment between bridge construction or repair jobs, which impacts income stability.
- Entry-level pay for a helper may be lower than for a certified ironworker, requiring a prolonged apprenticeship or training period to achieve higher earning potential.
- Bridge ironworker helpers often work in noisy environments with heavy machinery, requiring constant use of personal protective equipment and potentially leading to hearing damage over long careers.
- The job often requires travel to different bridge sites, which can mean extended periods away from home, impacting personal and family life.
- Work schedules can be unpredictable, with long hours, early starts, or weekend work often required to meet project deadlines or take advantage of favorable weather conditions, leading to work-life balance challenges for some individuals.
Frequently Asked Questions
Bridge Ironworker Helpers face distinct challenges, from mastering safety protocols to working at heights and in varying weather conditions. This section addresses crucial questions about entering this demanding field, covering entry requirements, physical demands, and the clear path to becoming a skilled ironworker.
What are the basic entry requirements to become a Bridge Ironworker Helper?
You typically need a high school diploma or GED. Most helpers learn on the job through apprenticeships or by working directly under experienced ironworkers. While no specific college degree is required, vocational training in welding or construction can be beneficial. Crucially, you must be at least 18 years old and often pass a drug test and physical examination.
How long does it take to gain enough experience to advance beyond a helper role?
Most helpers start by joining a union apprenticeship program, which typically lasts 3-4 years. During this time, you combine on-the-job training with classroom instruction. If you're not in an apprenticeship, gaining enough experience to advance to a journey-level ironworker can take 2-5 years, depending on your dedication, the projects available, and your ability to learn specialized skills like welding or rigging.
What does a typical day look like for a Bridge Ironworker Helper?
Bridge Ironworker Helpers assist with lifting, positioning, and securing heavy steel beams and girders. This involves a lot of manual labor, working at heights, and operating various hand and power tools. You'll prepare materials, clean work sites, and help with rigging and hoisting operations. The work is physically demanding and requires constant attention to safety protocols.
What are the biggest safety concerns and working conditions I should expect?
The work is inherently dangerous due to heights, heavy loads, and power tools. Safety training is paramount, and strict protocols are always in place to mitigate risks. You will work outdoors in all weather conditions, which can be physically taxing. The job also involves irregular hours, including early mornings, evenings, and weekends, especially when meeting project deadlines.
What are the typical salary expectations for a Bridge Ironworker Helper, and how does it progress?
Starting wages for helpers vary by region and union affiliation but generally range from $18 to $25 per hour, plus benefits in many unionized environments. As you gain experience and move into an apprenticeship or journey-level role, your earning potential significantly increases, often reaching $30-$50+ per hour, along with comprehensive benefits like health insurance, pension plans, and retirement savings.
Is there good job security and demand for Bridge Ironworker Helpers?
Demand for skilled ironworkers, including those who start as helpers, remains steady, especially with ongoing infrastructure projects. Job security is generally good, though it can fluctuate with economic cycles and the availability of large construction projects. Union membership often provides greater job stability and access to a wider range of projects.
What are the career growth opportunities for a Bridge Ironworker Helper?
Advancement typically involves completing an apprenticeship to become a journey-level ironworker, specializing in areas like structural steel, ornamental iron, or rigging. With further experience, you can move into leadership roles such as foreman, superintendent, or even project management. Many also pursue certifications in welding or crane operation to broaden their skills and increase earning potential.
Can Bridge Ironworker Helpers work remotely or with flexible hours?
Bridge Ironworker Helper positions are almost exclusively on-site due to the nature of the work. You will travel to various construction sites, which can be local, regional, or even national depending on the employer and project. The job does not offer remote work flexibility; your presence at the physical job site is always required.
Related Careers
Explore similar roles that might align with your interests and skills:
Ironworker
A growing field with similar skill requirements and career progression opportunities.
Explore career guideBridge Ironworker
A growing field with similar skill requirements and career progression opportunities.
Explore career guideBridge Painter Helper
A growing field with similar skill requirements and career progression opportunities.
Explore career guideConstruction Ironworker Helper
A growing field with similar skill requirements and career progression opportunities.
Explore career guideOrnamental Ironworker Helper
A growing field with similar skill requirements and career progression opportunities.
Explore career guideAssess your Bridge Ironworker Helper readiness
Understanding where you stand today is the first step toward your career goals. Our Career Coach helps identify skill gaps and create personalized plans.
Skills Gap Analysis
Get a detailed assessment of your current skills versus Bridge Ironworker Helper requirements. Our AI Career Coach identifies specific areas for improvement with personalized recommendations.
See your skills gapCareer Readiness Assessment
Evaluate your overall readiness for Bridge Ironworker Helper roles with our AI Career Coach. Receive personalized recommendations for education, projects, and experience to boost your competitiveness.
Assess your readinessSimple pricing, powerful features
Upgrade to Himalayas Plus and turbocharge your job search.
Himalayas
Himalayas Plus
Himalayas Max
Find your dream job
Sign up now and join over 100,000 remote workers who receive personalized job alerts, curated job matches, and more for free!
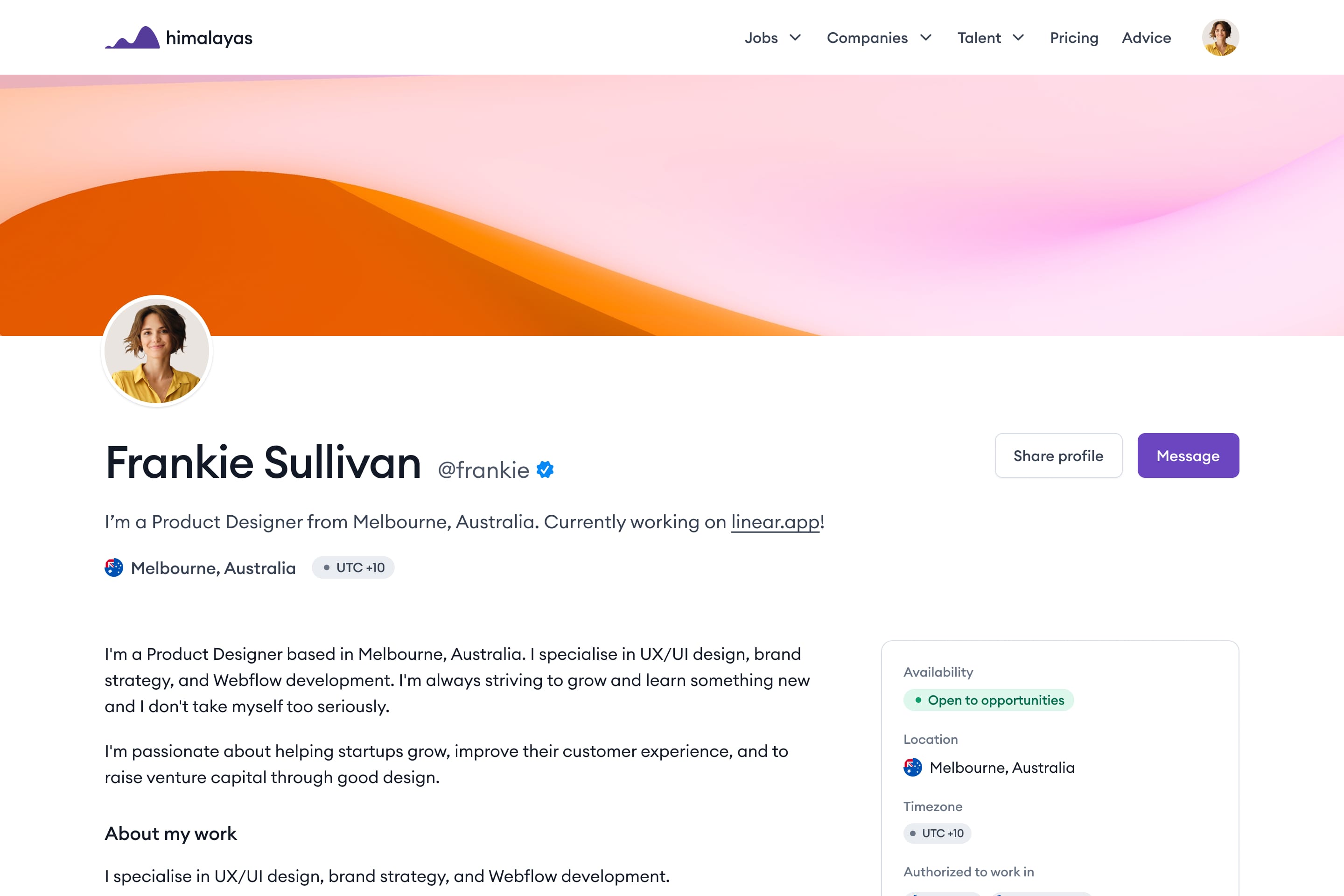