Complete Bridge Ironworker Career Guide
Bridge ironworkers are the unsung heroes building and repairing the vital arteries of our transportation infrastructure, fabricating and erecting the steel skeletons of bridges that connect communities and facilitate commerce. This demanding yet rewarding career offers a direct path to seeing your hard work stand tall for generations, requiring precision, strength, and a keen eye for safety. It's a specialized trade within the broader ironworking field, focusing uniquely on the monumental structures that span rivers, valleys, and roadways.
Key Facts & Statistics
Median Salary
$60,420 USD
(U.S. national median for all ironworkers, May 2023, BLS)
Range: $41,000 - $94,000+ USD (for all ironworkers, based on experience and location, BLS)
Growth Outlook
6%
as fast as average (for all ironworkers, 2022-2032, BLS)
Annual Openings
≈11,600
openings annually (for all ironworkers, BLS)
Top Industries
Typical Education
High school diploma or equivalent, followed by a 3-4 year apprenticeship program. Some may enter directly from vocational schools.
What is a Bridge Ironworker?
A Bridge Ironworker is a highly skilled construction professional specializing in the assembly and erection of structural steel components for bridges. They are responsible for building the skeletal framework of bridges, from small pedestrian crossings to massive suspension bridges. This role involves interpreting complex blueprints, safely handling heavy materials, and meticulously connecting steel members to form a robust and durable structure.
Unlike general ironworkers who might work on buildings or other structures, bridge ironworkers possess specific expertise in the unique challenges of bridge construction, including working over water, at significant heights, and with specialized techniques for long-span structures. They ensure the foundational strength and integrity of bridges, which are critical infrastructure for transportation and commerce.
What does a Bridge Ironworker do?
Key Responsibilities
- Assemble and erect structural steel frameworks for bridges, following blueprints and specifications precisely.
- Operate heavy machinery such as cranes, forklifts, and aerial lifts to move and position large steel beams and other components.
- Weld, bolt, and rivet steel members to secure the bridge structure, ensuring all connections meet safety and engineering standards.
- Install temporary supports and scaffolding to aid in construction, then dismantle them safely upon completion of relevant sections.
- Cut and shape steel using torches, saws, and other specialized tools to fit specific bridge design requirements.
- Inspect completed work for quality, alignment, and adherence to structural integrity requirements, identifying and correcting any deficiencies.
- Collaborate with other construction trades, engineers, and project managers to ensure seamless project progression and problem resolution on site.
Work Environment
Bridge ironworkers primarily work outdoors on active construction sites, exposed to various weather conditions and heights. The environment is often noisy and requires constant vigilance due to the operation of heavy machinery and the movement of large steel components. This role demands significant physical exertion, including climbing, lifting, and working in confined spaces.
Collaboration is essential, as ironworkers work closely with other tradespeople, engineers, and project supervisors. Schedules typically follow standard construction hours, but may include early mornings, evenings, or weekends, especially when working on critical path items or under tight deadlines. Travel to different bridge construction sites is common, often requiring relocation for the duration of a project.
Tools & Technologies
Bridge ironworkers regularly use a wide array of specialized tools and heavy machinery. They operate cranes, forklifts, and aerial work platforms for lifting and positioning massive steel components. Hand tools include wrenches, spud bars, and hammers for bolting and aligning steel.
For cutting and shaping, ironworkers employ oxy-acetylene torches, plasma cutters, and various power saws. Welding equipment, including stick welders and wire feeders, is crucial for securing connections. They also use precision instruments like levels, transits, and plumb bobs to ensure accurate alignment. Personal protective equipment (PPE) such as hard hats, safety harnesses, and specialized gloves are always essential for safety on the job site.
Bridge Ironworker Skills & Qualifications
A Bridge Ironworker's qualifications are highly specialized, focusing on structural steel erection and reinforcement for bridges. Requirements vary significantly based on the project's complexity, the employer's size, and regional regulations. Large infrastructure projects often demand extensive experience and specific certifications, while smaller local projects might be more accessible to those with foundational training.
Practical experience and certifications often outweigh formal degrees in this trade. While some ironworkers enter through apprenticeships, others gain skills through vocational training or military service. Many states and provinces require specific licensing or journeyman certification, particularly for structural work. The industry is seeing an increased emphasis on safety certifications and specialized welding qualifications as bridge designs become more complex and materials evolve.
The skill landscape for Bridge Ironworkers is stable but evolving with new materials and construction techniques. Prioritizing hands-on experience with diverse bridge types and obtaining relevant certifications, such as those for welding or rigging, adds significant value. Understanding how to work with pre-fabricated components and advanced hoisting equipment is becoming increasingly important. Candidates should focus on developing both the fundamental skills of the trade and specialized knowledge specific to bridge construction.
Education Requirements
Technical Skills
- Structural steel erection and assembly techniques for bridges
- Rigging and signaling for heavy lifting operations, including complex bridge sections
- Arc welding (SMAW, FCAW) and oxy-fuel cutting specific to structural steel and bridge applications
- Blueprint reading and interpretation for bridge designs, including shop drawings and erection plans
- Use of hand and power tools common in ironworking (e.g., spud wrenches, impact guns, grinders)
- Fall protection systems and safe work practices at heights
- Bolt-up procedures, including torqueing and tensioning of structural bolts
- Operating aerial work platforms (AWPs) and other material handling equipment
- Basic metallurgy knowledge for structural steel and welding considerations
- Site layout and measurement techniques for accurate component placement
- Concrete reinforcing (rebar tying and placement) for bridge decks and piers
- Inspection and quality control of erected steel components and welds
Soft Skills
- Safety Consciousness: Critical for preventing accidents and ensuring compliance with strict site regulations, given the inherent hazards of working at heights and with heavy materials.
- Attention to Detail: Essential for precise measurements, alignment, and secure fastening of structural components to ensure the bridge's integrity and safety.
- Physical Stamina and Agility: Necessary for long hours of demanding physical labor, climbing, and maneuvering heavy materials in challenging environments.
- Problem-Solving: Important for addressing unexpected challenges on-site, such as fitting issues, equipment malfunctions, or adverse weather conditions.
- Teamwork and Collaboration: Crucial for coordinating complex lifts and installations with crane operators, welders, and other crew members to ensure efficiency and safety.
- Adaptability: Required to adjust to changing project specifications, weather conditions, and work schedules, often on short notice.
- Communication: Vital for clearly conveying instructions, reporting hazards, and coordinating effectively with supervisors and fellow workers to maintain a safe and productive work environment.
- Work Ethic and Reliability: Demonstrates commitment to completing tasks efficiently, showing up on time, and consistently performing duties to meet project deadlines and quality standards under pressure and often in harsh conditions, which is paramount in bridge construction.
How to Become a Bridge Ironworker
Becoming a Bridge Ironworker involves physically demanding work at heights, often in challenging conditions. Entry into this specialized trade primarily occurs through union apprenticeships, which provide structured training, on-the-job experience, and certifications. While non-union paths exist, they are less common and often require prior construction experience or direct connections.
The typical timeline for entry and full qualification can range from three to five years through an apprenticeship program. This includes thousands of hours of on-the-job training and hundreds of hours of classroom instruction. Geographic location significantly impacts opportunities; major infrastructure projects in urban centers or regions with aging bridges will have more demand than rural areas. Company size also matters; large construction firms or specialized bridge contractors will offer more consistent work than smaller, general contractors.
A common misconception is that extensive prior construction experience is always necessary. While helpful, many apprenticeship programs accept individuals with limited experience but a strong work ethic, physical fitness, and a willingness to learn. Success in this field relies heavily on discipline, adherence to safety protocols, and continuous skill development, rather than just raw strength. Building connections within local unions and attending pre-apprenticeship programs can provide a significant advantage.
Step 1
Step 2
Step 3
Step 4
Step 5
Step 6
Education & Training Needed to Become a Bridge Ironworker
Becoming a Bridge Ironworker primarily involves hands-on training rather than formal degrees. Apprenticeship programs are the most common and respected pathway, offering structured on-the-job training combined with classroom instruction. These programs typically last 3-4 years and are often union-sponsored, costing minimal fees beyond union dues, making them highly cost-effective compared to traditional academic routes. Apprenticeships provide both theoretical knowledge of structural principles and practical skills in welding, rigging, and safety, which are critical for bridge construction.
Alternative paths, such as vocational school certificates or self-study, exist but are less recognized by employers for entry-level positions. Vocational programs might offer foundational skills in welding or construction, ranging from 6 months to 2 years and costing $5,000-$20,000. However, these programs usually require additional on-the-job experience or an apprenticeship to gain full competency and employer trust. Employers strongly prefer candidates with formal apprenticeship completion due to the rigorous safety training and comprehensive skill development they provide, directly impacting job placement and career progression.
Continuous learning and certifications in specialized areas like advanced welding techniques, crane signaling, or specific safety protocols are essential throughout a Bridge Ironworker's career. These typically involve short courses lasting days to weeks, costing hundreds to a few thousand dollars. Practical experience remains paramount; theoretical knowledge gained in any program must be reinforced through extensive fieldwork. The industry values proven ability to work safely and efficiently at heights and with heavy materials, making on-site experience and recognized certifications more valuable than academic degrees for this specific role.
Bridge Ironworker Salary & Outlook
Compensation for a Bridge Ironworker varies significantly based on several factors, reflecting the demanding and specialized nature of the work. Geographic location plays a crucial role; areas with extensive infrastructure projects or higher costs of living, such as major metropolitan centers, typically offer higher wages. Conversely, regions with less construction activity or lower living expenses may have more modest pay rates.
Experience, specialized skills, and certifications directly impact earning potential. An Apprentice Bridge Ironworker earns less while gaining foundational knowledge, whereas a Journeyman or Lead Bridge Ironworker commands higher pay due to proven expertise in complex tasks like structural welding, rigging, and rebar installation. Performance and the ability to handle challenging conditions also influence pay.
Total compensation extends beyond base salary. Many Bridge Ironworkers receive comprehensive benefits packages, including health insurance, dental and vision coverage, and robust retirement plans, often through union affiliations. Overtime pay is common, particularly during critical project phases, significantly boosting annual income. Some projects may also offer per diem allowances for travel or remote site work.
Industry-specific trends, such as government infrastructure spending or the demand for modern bridge construction techniques, drive salary growth in this field. Highly skilled ironworkers with expertise in advanced materials or innovative construction methods possess strong negotiation leverage. While remote work is not applicable to this hands-on role, the demand for skilled labor creates opportunities across different states and occasionally internationally, though salary figures here are in USD.
Salary by Experience Level
Level | US Median | US Average |
---|---|---|
Apprentice Bridge Ironworker | $40k USD | $45k USD |
Journeyman Bridge Ironworker | $65k USD | $70k USD |
Lead Bridge Ironworker | $80k USD | $85k USD |
Foreman Bridge Ironworker | $90k USD | $95k USD |
Superintendent Bridge Ironworker | $105k USD | $115k USD |
Market Commentary
The job market for Bridge Ironworkers shows a stable outlook, primarily driven by ongoing infrastructure needs and government investment. The U.S. Bureau of Labor Statistics projects a modest growth for structural iron and steelworkers, which includes Bridge Ironworkers, indicating continued demand for skilled trades. The bipartisan Infrastructure Investment and Jobs Act (IIJA) provides significant funding for bridge repair and replacement, directly fueling job opportunities in this specific sector.
Current market trends highlight a consistent need for skilled ironworkers, often outpacing the supply of qualified candidates. This imbalance can lead to competitive wages and favorable working conditions for experienced professionals. Emerging opportunities include projects integrating advanced materials like high-performance concrete or specialized steel alloys, requiring ironworkers to adapt to new techniques and safety protocols.
Automation and AI have limited direct impact on the hands-on, physically demanding tasks of a Bridge Ironworker. While some prefabrication might occur off-site, the core work of erecting, connecting, and reinforcing bridge structures remains human-centric. This role is generally considered recession-resistant due to the critical nature of infrastructure maintenance and development.
Geographic hotspots for Bridge Ironworkers include states with aging infrastructure, such as those in the Northeast and Midwest, and rapidly growing regions needing new bridges, like parts of the South and West. Continuous learning in areas like advanced welding, rigging, and safety certifications is crucial for career advancement and securing high-demand projects.
Bridge Ironworker Career Path
Career progression for a Bridge Ironworker involves a clear, structured path focused on mastering specialized skills, ensuring safety, and developing leadership capabilities. The industry values hands-on experience, precision, and adherence to strict safety protocols. Advancement typically follows a traditional individual contributor (IC) track before branching into management roles.
Factors influencing advancement include consistent high performance, a strong safety record, and a willingness to take on more complex tasks. Specialization in areas like complex rigging, welding, or falsework can accelerate progression. Company size and project complexity significantly impact available opportunities; larger companies often handle more diverse and challenging bridge projects, offering broader exposure. Economic conditions and infrastructure spending directly affect job availability and project scale.
Lateral movement often involves transitioning between different types of structural ironwork or specializing further within bridge construction. Networking within union halls, participating in industry safety committees, and continuous learning through certifications in advanced rigging or welding techniques are crucial. Mentorship from experienced ironworkers plays a vital role in skill transfer and professional development, shaping a highly skilled and safety-conscious workforce.
Apprentice Bridge Ironworker
3-4 years (apprenticeship program)Key Focus Areas
Journeyman Bridge Ironworker
4-8 years total experienceKey Focus Areas
Lead Bridge Ironworker
8-12 years total experienceKey Focus Areas
Foreman Bridge Ironworker
12-18 years total experienceKey Focus Areas
Superintendent Bridge Ironworker
18+ years total experienceKey Focus Areas
Apprentice Bridge Ironworker
3-4 years (apprenticeship program)Works under direct supervision, learning the fundamentals of bridge construction and ironwork. Assists Journeyman Ironworkers with tasks like rigging, connecting steel, and installing structural components. Focuses on learning safe work practices and the correct use of tools and equipment. Responsibilities are highly structured with minimal decision-making authority.
Key Focus Areas
Mastering fundamental ironworking techniques, including blueprint reading, basic welding, and proper use of tools. Adhering strictly to all safety regulations and learning to identify potential hazards. Developing physical endurance and precision in tasks such as material handling and bolt-up procedures. Building a strong work ethic and understanding site logistics.
Journeyman Bridge Ironworker
4-8 years total experiencePerforms complex ironworking tasks independently, including structural steel erection, welding, and cable installation for bridges. Interprets blueprints, solves on-site technical issues, and ensures work meets precise specifications. May guide apprentices and ensure their work adheres to safety standards. Operates with significant autonomy on assigned tasks.
Key Focus Areas
Refining advanced welding and rigging skills, including complex lifts and structural assembly. Developing problem-solving abilities for on-site challenges and adapting to varying project conditions. Mentoring apprentices and ensuring their understanding of tasks and safety. Participating in pre-task planning and contributing to safety briefings.
Lead Bridge Ironworker
8-12 years total experienceLeads small teams of ironworkers on specific sections of a bridge project, ensuring work is completed safely, on schedule, and to quality standards. Organizes daily tasks, assigns duties to team members, and provides technical guidance. Identifies potential issues and implements solutions, collaborating with the Foreman. Holds responsibility for the efficiency and safety of their immediate workgroup.
Key Focus Areas
Developing leadership skills, including effective communication, task delegation, and conflict resolution. Enhancing expertise in specialized areas like post-tensioning, segmental bridge construction, or complex rigging. Participating in advanced safety training and incident prevention. Contributing to project planning and scheduling.
Foreman Bridge Ironworker
12-18 years total experienceManages a crew of Bridge Ironworkers, overseeing daily operations for a significant portion of a bridge project. Ensures all work complies with blueprints, specifications, and safety regulations. Coordinates with other trades, manages material flow, and tracks progress. Makes critical on-site decisions regarding personnel, equipment, and task execution to maintain project timelines and budget.
Key Focus Areas
Mastering project management fundamentals, including resource allocation, budget awareness, and schedule adherence. Developing strong communication skills for interaction with different trades and project management. Focusing on proactive problem-solving, risk assessment, and detailed safety planning. Cultivating mentorship and team development abilities.
Superintendent Bridge Ironworker
18+ years total experienceHolds overall responsibility for the successful execution of an entire bridge construction project or multiple smaller projects. Manages Foremen, oversees budget, schedule, and quality control across all ironwork aspects. Acts as the primary point of contact for clients and senior management regarding project progress and challenges. Ensures compliance with all regulatory and company standards, driving overall project success and profitability.
Key Focus Areas
Developing executive leadership skills, including strategic planning, financial oversight, and large-scale team management. Cultivating strong client relations and contractual understanding. Focusing on long-term project viability, risk mitigation, and continuous improvement processes. Building a network of industry contacts and staying current with construction innovations.
Job Application Toolkit
Ace your application with our purpose-built resources:
Bridge Ironworker Cover Letter Examples
Personalizable templates that showcase your impact.
View examplesBridge Ironworker Job Description Template
Ready-to-use JD for recruiters and hiring teams.
View examplesGlobal Bridge Ironworker Opportunities
Bridge ironworkers find global demand due to infrastructure development worldwide. This profession involves constructing and repairing bridges, requiring specialized skills that translate across international projects. Cultural differences in safety standards and construction practices exist, but core techniques remain similar. Many ironworkers consider international work for higher pay or participation in large-scale projects. Some international certifications, like those from the American Welding Society (AWS), can aid global mobility.
Global Salaries
Salaries for bridge ironworkers vary significantly by region and project complexity. In North America, particularly the United States and Canada, annual salaries range from $60,000 to $100,000 USD, often with substantial overtime. These figures reflect high demand and strong unionization. European countries like Germany or the UK offer €45,000 to €70,000 (approximately $48,000-$75,000 USD), though cost of living can be higher.
Asia-Pacific markets, such as Australia and New Zealand, provide competitive wages, typically AUD 80,000 to AUD 120,000 (around $53,000-$80,000 USD), driven by ongoing infrastructure booms. Latin American countries might offer $25,000 to $45,000 USD annually, but with a significantly lower cost of living, purchasing power can be comparable for basic needs. Middle Eastern nations, like UAE or Saudi Arabia, often offer tax-free salaries ranging from $40,000 to $70,000 USD, often including housing allowances, making them attractive.
International salary structures differ in benefits. North American roles often include robust health benefits and pension plans. European positions may have more vacation time and universal healthcare access. Tax implications vary; some countries have higher income taxes but offer more social services. Experience and specific certifications directly influence compensation across all markets, with specialized welding or rigging skills commanding higher rates.
Remote Work
Bridge ironwork is inherently a hands-on, on-site profession. Therefore, direct international remote work opportunities for bridge ironworkers are non-existent. The role requires physical presence at construction sites for tasks like erecting steel beams, welding, and rigging.
However, related roles such as project management, structural design, or engineering, which involve planning and oversight, might offer remote components. These are distinct from the ironworker's core duties. Digital nomad opportunities do not apply to this trade. Employers in this field globally require physical presence and adherence to local safety regulations. Compensation is tied directly to on-site hours and project completion.
Visa & Immigration
Bridge ironworkers typically seek skilled worker visas in countries with infrastructure projects. Popular destinations include Canada, Australia, Germany, and the United States. Canada's Express Entry system and Australia's Skilled Migration program often list trades, including ironwork, on their occupation lists, requiring skills assessments and English proficiency tests.
In the US, H-2B visas are common for temporary non-agricultural workers, including construction trades, but require employer sponsorship. European countries may offer similar skilled worker permits, often requiring recognition of vocational qualifications. Processing times vary from a few months to over a year. Education credential recognition for vocational trades is crucial, and some countries require specific local certifications or apprenticeships. Language requirements vary by country, with English often sufficient in Anglophone nations or for major international projects. Pathways to permanent residency can exist after several years of continuous skilled employment.
2025 Market Reality for Bridge Ironworkers
Understanding current market conditions is crucial for Bridge Ironworkers to navigate career paths effectively. The landscape for this specialized trade has evolved significantly since 2023, influenced by national infrastructure initiatives and post-pandemic recovery efforts. Broader economic factors, such as inflation and material costs, directly impact project funding and timelines.
Market realities vary by experience level; seasoned professionals with specialized certifications find consistent demand, while entry-level workers often rely on apprenticeships. Geographic location and the scale of local infrastructure projects also dictate job availability, emphasizing the need for strategic planning in this essential but demanding field.
Current Challenges
Bridge Ironworkers face significant challenges from fluctuating project pipelines and economic downturns, which directly impact job availability. Competition for specialized roles remains high, particularly for experienced workers on large-scale infrastructure projects. Furthermore, the demanding physical nature of the work and stringent safety regulations create a high barrier to entry and require continuous adherence to rigorous standards.
Seasonal slowdowns, especially in regions with harsh winters, also reduce work hours. Project delays or cancellations due to funding issues or material costs can abruptly halt employment, requiring workers to seek new assignments frequently.
Growth Opportunities
Despite challenges, significant opportunities exist for Bridge Ironworkers, particularly in specialized areas like complex truss assembly, suspension bridge cable work, and retrofitting existing structures. The federal infrastructure bill continues to fund numerous large-scale bridge projects, ensuring a steady pipeline of work for the foreseeable future. Additionally, the increasing focus on repairing and upgrading America's aging infrastructure creates consistent demand for skilled professionals.
Ironworkers who pursue advanced certifications in welding, rigging, or specific structural systems gain a competitive edge. There is an emerging need for workers proficient in using advanced surveying tools and robotic welding equipment, creating new specializations. Underserved markets, especially in regions with expanding urban centers or critical transportation bottlenecks, often offer better opportunities and potentially higher compensation.
Strategic career moves might involve relocating for major projects or joining unions with strong national presences to access diverse job sites. The long-term nature of bridge construction and maintenance projects offers stability compared to some other construction sectors. Investing in continuous training and adapting to new construction methods ensures long-term employability in this vital trade.
Current Market Trends
The market for Bridge Ironworkers in 2025 shows a mixed but generally stable outlook, driven by ongoing infrastructure investments and the need for maintenance on aging structures. Demand remains strong for skilled workers capable of complex steel erection, cable installation, and structural reinforcement on bridges. However, project timelines often dictate hiring surges, leading to periods of intense work followed by lulls.
Technological advancements, including advanced welding techniques and specialized lifting equipment, are changing skill requirements. Ironworkers must adapt to these tools, which enhance efficiency and safety on large bridge projects. Economic conditions, while generally supportive of infrastructure spending, can cause delays in new project starts, impacting consistent work availability.
Salary trends for experienced Bridge Ironworkers continue to reflect the high-risk, high-skill nature of the job, often including robust union benefits. Entry-level positions face more competition, requiring individuals to demonstrate commitment through apprenticeships. Geographic variations are significant; states with major port cities, navigable rivers, or extensive highway systems show higher demand for bridge construction and repair.
Remote work is not applicable to this field, emphasizing the importance of mobility and willingness to travel for projects. Hiring often follows cyclical patterns, with increased activity during warmer months when outdoor construction is feasible. Union membership remains a critical pathway, providing access to training, projects, and standardized wages.
Emerging Specializations
The field of bridge ironworking is undergoing a significant transformation, driven by advancements in materials science, automation, and infrastructure demands. These technological shifts are creating new specialization opportunities that were once unimaginable. Understanding these emerging niches is crucial for professionals seeking to position themselves strategically for career advancement in 2025 and beyond.
Early positioning in these developing areas often commands premium compensation and accelerated career growth. As new techniques and technologies become standard, skilled ironworkers with specialized knowledge will be in high demand. While established specializations remain vital, focusing on emerging areas offers a pathway to becoming a leader in the next generation of bridge construction.
Many emerging areas take time to move from niche applications to mainstream adoption, typically between three to seven years. This timeline allows for skill development and strategic entry before the market becomes saturated. Pursuing cutting-edge specializations involves a balance of risk and reward; while the initial investment in training may be higher, the potential for long-term career stability and higher earning potential is substantial.
Smart Bridge Systems Integration Ironworker
This specialization involves the installation and integration of smart sensors and monitoring systems directly into bridge structures during construction or repair. These systems collect real-time data on structural integrity, stress, temperature, and environmental conditions, enabling predictive maintenance and enhancing safety. Ironworkers with this expertise ensure the precise placement and secure connection of these advanced components, which are vital for modern infrastructure management and longevity.
Advanced Materials & Modular Assembly Specialist
As bridge designs incorporate more complex geometries and sustainable materials, the demand for ironworkers skilled in advanced material handling and assembly is growing. This includes working with high-strength composites, specialized alloys, and modular pre-fabricated units that require precise alignment and joining methods. This specialization focuses on the safe and efficient erection of these innovative components, optimizing structural performance and reducing construction time.
Robotics & Automation Integration Ironworker
This area focuses on the implementation of robotic and automated systems for tasks such as welding, bolting, and material placement on bridge construction sites. Ironworkers in this role operate, program, and maintain these sophisticated machines, ensuring their safe and efficient deployment alongside human teams. They are critical in overseeing the execution of complex or repetitive tasks, enhancing safety and precision while reducing manual labor.
Sustainable Bridge Construction Ironworker
With increasing emphasis on environmental protection and sustainable construction, this specialization involves working with eco-friendly bridge designs and materials. This includes projects focused on minimizing environmental impact, such as installing structures designed for wildlife crossings or integrating renewable energy solutions into bridge infrastructure. Ironworkers in this area understand the unique requirements and challenges of green construction practices.
Digital Construction & AR/VR Application Ironworker
This specialization involves the use of augmented reality (AR) and virtual reality (VR) tools for pre-visualization, real-time guidance, and quality control during bridge construction. Ironworkers use AR overlays to precisely position components, verify measurements, and identify potential clashes before or during installation. This technology enhances accuracy, reduces errors, and improves overall project efficiency on complex bridge projects.
Pros & Cons of Being a Bridge Ironworker
Understanding the advantages and challenges of any career is crucial before making a commitment. For a Bridge Ironworker, experiences can vary significantly based on the specific project, company culture, geographic location, and individual temperament. What one person views as a benefit, like extensive travel, another might see as a major drawback. Furthermore, the nature of the work and its demands can shift at different career stages, from an apprentice learning the ropes to a seasoned foreman overseeing complex operations. This assessment provides an honest, balanced look at the realistic benefits and genuine difficulties of this specialized trade, helping aspiring ironworkers set appropriate expectations.
Pros
- Bridge ironworkers command high wages, reflecting the specialized skills and inherent risks of the job, providing a strong earning potential, especially for experienced and certified professionals.
- There is high demand for skilled bridge ironworkers across the country due to aging infrastructure and new construction projects, ensuring consistent job security and opportunities.
- The work offers a profound sense of accomplishment and pride, as ironworkers contribute directly to visible, long-lasting structures that serve communities for decades.
- The job provides a dynamic and varied work environment; no two bridge projects are exactly alike, offering continuous intellectual and physical challenges.
- Bridge ironworking offers strong camaraderie among crew members, as teamwork and mutual reliance are essential for safety and project success, fostering a tight-knit community.
- Opportunities for advancement exist, allowing experienced ironworkers to move into supervisory roles like foreman or superintendent, or even into project management positions.
- Entry into the field often involves apprenticeships that provide paid on-the-job training, allowing individuals to earn a living while learning the necessary skills without incurring significant educational debt.
Cons
- Bridge ironworkers face significant physical demands, including heavy lifting, climbing, and working in awkward positions for extended periods, which can lead to chronic fatigue and musculoskeletal issues over time.
- The work environment often involves extreme weather conditions, such as high winds, intense heat, or freezing temperatures, making the job physically taxing and potentially dangerous.
- Bridge ironworking carries a high risk of serious injury or fatality due to falls from heights, equipment malfunctions, and the inherent dangers of working with heavy steel at elevated levels.
- Job availability can be seasonal or project-dependent, leading to periods of unemployment or the need to travel to different regions for work, impacting income stability.
- The work schedule is often unpredictable, with long hours, early starts, and weekend work common, especially when projects face tight deadlines or require continuous pours.
- Requires continuous vigilance and strict adherence to safety protocols; even minor lapses in attention can have catastrophic consequences, leading to high-stress workdays.
- The job often involves extensive travel and time away from home, as bridge projects can be located in remote areas or require workers to follow construction opportunities across states or even countries for several months.
Frequently Asked Questions
Bridge Ironworkers face unique challenges around safety, physical demands, and specialized skills. This section addresses the most common questions about entering this demanding yet rewarding trade, from apprenticeship pathways and earning potential to the realities of working at heights and in varied weather conditions.
What are the typical entry requirements and training pathways to become a Bridge Ironworker?
Most Bridge Ironworkers enter the trade through a formal apprenticeship program, typically lasting 3-4 years. These programs combine paid on-the-job training with classroom instruction in welding, rigging, blueprint reading, and safety. Some individuals may start as helpers and gain experience before pursuing an apprenticeship. A high school diploma or GED is usually required, along with passing a physical and drug test.
What are the salary expectations and earning potential for a Bridge Ironworker?
Bridge Ironworkers generally earn a good living, especially with experience and specialized skills. Starting apprentice wages are lower but increase significantly with each year of training. Experienced journeymen can earn high hourly rates, often with excellent benefits packages including health insurance and pension plans, making it a financially stable career. Overtime pay is common due to project demands.
What is the daily work environment like, and what are the physical demands of this job?
Bridge Ironwork is physically demanding, requiring strength, stamina, and agility. You will work at heights, in confined spaces, and in various weather conditions, including extreme heat, cold, and wind. The work involves heavy lifting, climbing, and operating power tools. This role also requires strong problem-solving skills and strict adherence to safety protocols to mitigate inherent risks.
How significant are the safety risks, and what measures are in place to protect workers?
Safety is paramount in bridge ironwork due to the inherent risks of working at heights and with heavy materials. Comprehensive safety training is a continuous part of the job, covering fall protection, rigging safety, and equipment operation. Adherence to safety protocols, wearing personal protective equipment, and participating in regular safety briefings are mandatory. While accidents can occur, strict safety measures minimize risks.
What is the job outlook and long-term career stability for a Bridge Ironworker?
Job security for Bridge Ironworkers is generally strong, driven by ongoing infrastructure projects and the need for maintenance on existing bridges. Demand can fluctuate with economic cycles and government funding for infrastructure. However, the specialized skills of bridge ironworkers make them highly sought after. Geographic mobility can further enhance job opportunities, as projects are located nationwide.
What is the typical work-life balance like, considering project demands and travel?
Working hours can vary significantly based on project deadlines and weather conditions. Overtime is common, and you may work long shifts, including nights and weekends, to meet construction schedules. Travel is often required, as bridge projects are located across different regions, meaning time away from home. This demanding schedule can impact personal life, requiring flexibility and understanding.
What are the opportunities for career growth and advancement within bridge ironwork?
Career advancement for Bridge Ironworkers can include becoming a foreman, superintendent, or safety manager, leveraging your field experience into leadership roles. Many also transition into inspection, project management, or even start their own contracting businesses. Continuous learning, gaining certifications in specialized welding or rigging techniques, and demonstrating leadership skills open doors to these opportunities.
Related Careers
Explore similar roles that might align with your interests and skills:
Ironworker
A growing field with similar skill requirements and career progression opportunities.
Explore career guideBridge Ironworker Helper
A growing field with similar skill requirements and career progression opportunities.
Explore career guideConstruction Ironworker
A growing field with similar skill requirements and career progression opportunities.
Explore career guideRebar Worker
A growing field with similar skill requirements and career progression opportunities.
Explore career guideStructural Steel Erector
A growing field with similar skill requirements and career progression opportunities.
Explore career guideAssess your Bridge Ironworker readiness
Understanding where you stand today is the first step toward your career goals. Our Career Coach helps identify skill gaps and create personalized plans.
Skills Gap Analysis
Get a detailed assessment of your current skills versus Bridge Ironworker requirements. Our AI Career Coach identifies specific areas for improvement with personalized recommendations.
See your skills gapCareer Readiness Assessment
Evaluate your overall readiness for Bridge Ironworker roles with our AI Career Coach. Receive personalized recommendations for education, projects, and experience to boost your competitiveness.
Assess your readinessSimple pricing, powerful features
Upgrade to Himalayas Plus and turbocharge your job search.
Himalayas
Himalayas Plus
Himalayas Max
Find your dream job
Sign up now and join over 100,000 remote workers who receive personalized job alerts, curated job matches, and more for free!
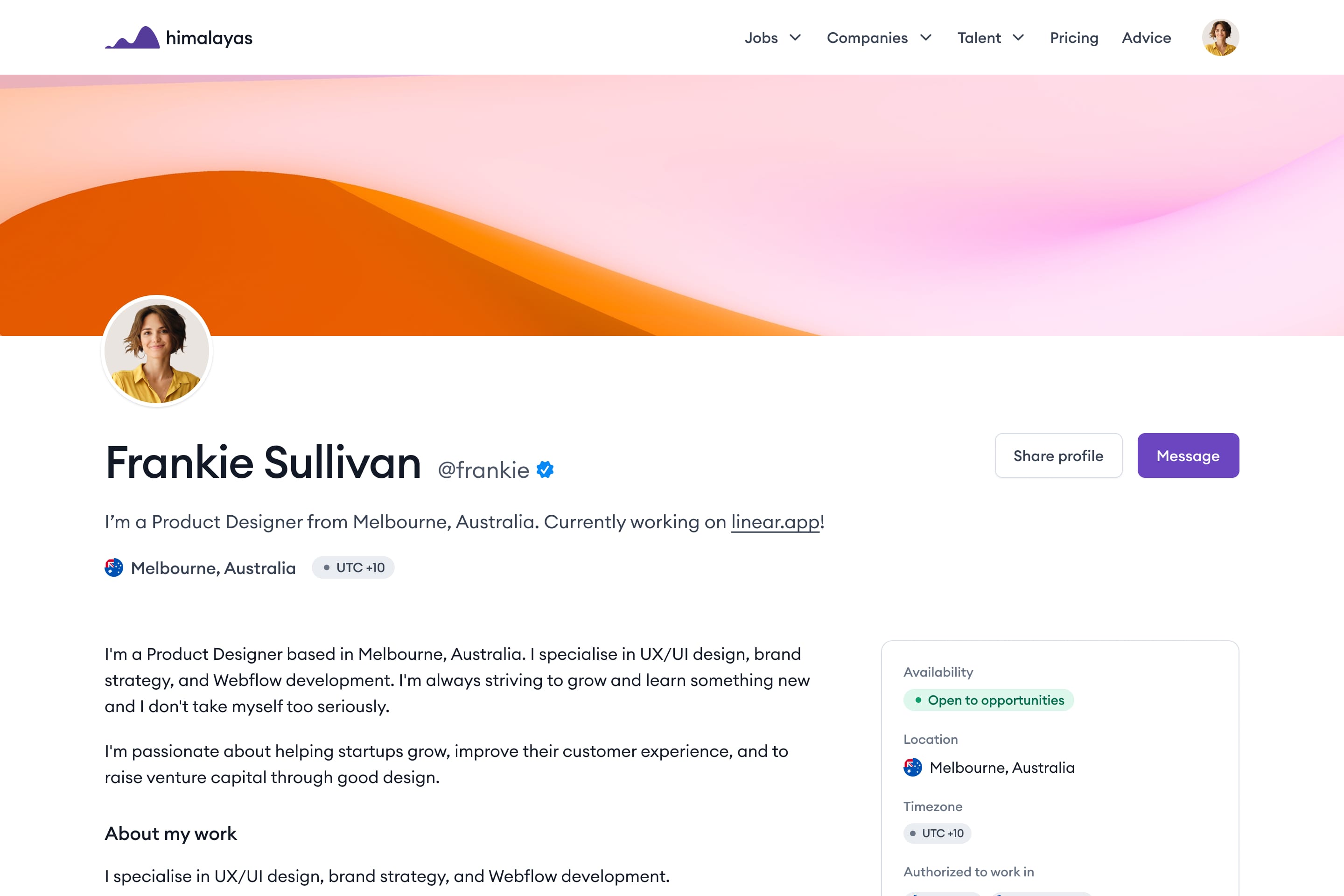