Complete Construction Ironworker Helper Career Guide
Construction Ironworker Helpers play a vital support role, directly assisting skilled ironworkers in erecting steel structures for buildings, bridges, and roads. They learn essential trade skills on the job, contributing to critical infrastructure projects while gaining hands-on experience in a physically demanding yet rewarding field. This entry-level position is a crucial stepping stone into a specialized construction career, offering a direct path to becoming a journey-level ironworker.
Key Facts & Statistics
Median Salary
$48,340 USD
(U.S. national median for Construction Laborers and Helpers, BLS, May 2023)
Range: $35k - $65k+ USD (Entry-level to experienced, varies by union and location)
Growth Outlook
5%
as fast as average (BLS, 2022-2032)
Annual Openings
≈34,700
openings annually (BLS, 2022-2032)
Top Industries
Typical Education
High school diploma or equivalent; most learn through on-the-job training or apprenticeships
What is a Construction Ironworker Helper?
A Construction Ironworker Helper is an entry-level position that provides direct, hands-on support to skilled ironworkers in erecting and dismantling structural steel frameworks, reinforcing concrete, and installing ornamental ironwork. This role is crucial for maintaining the efficiency and safety of a construction site, ensuring that materials are readily available and tasks are completed according to plan. They perform many of the manual and preparatory duties that allow journeymen ironworkers to focus on the more complex, skilled aspects of the job.
This helper role differs significantly from a general construction laborer because their duties are specifically focused on assisting ironworkers with metal-related tasks, such as handling rebar and structural steel. While a general laborer might do a wide range of tasks across a site, an Ironworker Helper's work directly prepares, moves, and supports the installation of iron and steel components, making them an integral part of the ironworking crew rather than just general support staff.
What does a Construction Ironworker Helper do?
Key Responsibilities
- Carry and position heavy steel beams, rebar, and other metal components as directed by journeymen ironworkers.
- Operate hand tools, such as wrenches, grinders, and hammers, to assist in the assembly and dismantling of structural frameworks.
- Clean and prepare work areas by removing debris, organizing materials, and ensuring a safe environment for ironworkers.
- Set up and dismantle rigging equipment, including ropes, cables, and hoists, under direct supervision.
- Assist with the cutting, bending, and shaping of rebar and other metal materials using specialized equipment.
- Perform general labor tasks like digging, shoveling, and moving materials to support the overall construction process.
- Maintain and clean tools and equipment regularly, reporting any damage or malfunction to supervisors.
Work Environment
Construction Ironworker Helpers work outdoors on various construction sites, regardless of weather conditions. The environment is physically demanding, involving heavy lifting, climbing, and working at heights. They typically work standard daytime hours, but project deadlines can require early starts, late finishes, or weekend work. The pace is often fast, driven by project schedules and the need to keep up with skilled ironworkers. Collaboration is constant, as they directly support a team of journeymen ironworkers and other construction trades. Travel to different job sites is common, depending on the employer's projects.
Tools & Technologies
Construction Ironworker Helpers primarily use a range of hand and power tools common in metalwork and general construction. These include wrenches, hammers, levels, tape measures, grinders, and cutting torches. They also work with rigging equipment such as slings, chains, cables, and come-alongs. Personal protective equipment (PPE) like hard hats, safety glasses, gloves, and steel-toed boots are essential daily wear. While not directly operating heavy machinery, they often assist in guiding cranes and forklifts. Communication tools like two-way radios are also used to coordinate tasks on noisy job sites.
Construction Ironworker Helper Skills & Qualifications
A Construction Ironworker Helper assists skilled ironworkers in erecting steel structures, reinforcing concrete, and installing metal components. This role is primarily an entry point into the ironworking trade, emphasizing hands-on learning and safety. Qualification priorities for this position revolve heavily around physical aptitude, a strong work ethic, and a commitment to safety protocols.
Requirements for an Ironworker Helper vary by seniority and company size. Entry-level helpers typically need minimal formal experience but must demonstrate a willingness to learn and adhere to strict safety guidelines. Larger construction firms may prefer candidates with some prior construction site exposure, even if not specifically in ironwork. Smaller companies often prioritize a strong, reliable individual who can quickly grasp tasks. Geographic location also influences demand; areas with significant infrastructure development or commercial building booms will have more opportunities.
Formal education holds less weight than practical experience and certifications for this role. While a high school diploma or GED is generally preferred, it is not always a strict requirement if a candidate possesses relevant physical capabilities and a strong desire to enter the trade. Apprenticeship programs, often union-sponsored, are the most valued pathway, providing structured training and on-the-job experience. These programs typically require helpers to accumulate thousands of hours of work and classroom instruction to advance to journeyman status. Certifications like OSHA 10 or OSHA 30 are highly beneficial and often mandatory for site access, demonstrating a foundational understanding of construction safety. The skill landscape in ironworking is stable in its core tasks but sees evolving safety standards and equipment. Helpers must prioritize foundational skills and safety to build a strong career path.
Education Requirements
Technical Skills
- Basic Hand Tool Proficiency: Using wrenches, hammers, tape measures, and other common construction tools effectively.
- Power Tool Operation: Safe and efficient use of grinders, drills, cutting torches, and other power tools under supervision.
- Material Handling and Rigging: Assisting in moving, lifting, and securing steel beams, rebar, and other heavy materials using ropes, chains, and hoists.
- Site Safety Procedures: Adhering to all safety protocols, wearing personal protective equipment (PPE), and understanding lockout/tagout procedures.
- Blueprint Reading (Basic): Ability to interpret simple diagrams and locate specific structural components on a blueprint.
- Welding and Cutting (Basic Assistance): Assisting skilled welders, preparing materials, and understanding basic cutting techniques.
- Rebar Tying and Placement: Assisting in the bending, cutting, and placement of reinforcing steel bars for concrete structures.
- Scaffold Erection and Dismantling (Assistance): Helping in the safe assembly and disassembly of scaffolding and temporary work platforms.
- Fall Protection Systems: Understanding and correctly using harnesses, lanyards, and other fall protection equipment.
- Mathematical Measurement: Accurately reading tape measures, understanding basic geometry for angles, and performing simple calculations.
Soft Skills
- Safety Consciousness: Essential for identifying and mitigating hazards, protecting oneself and the team on a high-risk job site.
- Physical Stamina and Endurance: Crucial for prolonged periods of heavy lifting, climbing, and working in various weather conditions.
- Attention to Detail: Important for accurately measuring, positioning, and securing materials, preventing errors that could compromise structural integrity.
- Teamwork and Collaboration: Necessary for effectively assisting skilled ironworkers, coordinating tasks, and ensuring smooth workflow on complex projects.
- Willingness to Learn: Critical for absorbing instructions, mastering new techniques, and progressing within the trade.
- Problem-Solving Skills: Helps in adapting to unexpected site conditions or challenges and finding practical solutions quickly.
- Dependability and Punctuality: Essential for maintaining project schedules and ensuring the team can rely on timely assistance.
How to Become a Construction Ironworker Helper
Breaking into the Construction Ironworker Helper role involves a blend of practical skills and a strong work ethic. While formal degrees are not typically required, a foundational understanding of construction safety, tools, and basic rigging is highly beneficial. Many enter this field through apprenticeships, trade schools, or by starting in general labor positions to gain on-site experience.
The timeline for entry can vary; someone with prior construction exposure might secure a helper role in a few months, while a complete beginner might take 6-12 months to gain basic certifications and find an entry-level opportunity. Geographic location significantly impacts availability; major metropolitan areas with ongoing infrastructure projects offer more opportunities than smaller, rural markets. Larger construction companies and union halls often have structured helper programs, whereas smaller contractors might hire based on immediate need and demonstrated eagerness to learn.
Misconceptions often include believing that no prior experience is needed; while you start as a helper, employers prefer candidates who understand basic site safety and can quickly learn. Networking within the construction industry, even at local supply houses or job fairs, can open doors to opportunities that are not publicly advertised. Understanding that this is a physically demanding role requiring adherence to strict safety protocols is crucial for success.
Obtain essential safety certifications such as OSHA 10 or OSHA 30, which are often mandatory for any construction site entry. These certifications demonstrate a fundamental understanding of workplace hazards and safety procedures, making you a more attractive candidate.
Develop foundational construction skills by completing a pre-apprenticeship program or vocational training in basic carpentry, welding, or rigging. These programs provide hands-on experience with tools and materials, which are invaluable for an ironworker helper.
Build practical experience through entry-level general labor positions on construction sites. This exposes you to the daily routines, equipment, and teamwork dynamics of a construction environment, preparing you for the demands of an ironworker helper role.
Network with experienced ironworkers, foremen, and union representatives at local trade events, union halls, or through informational interviews. These connections can provide insights into the industry, lead to mentorship opportunities, and inform you about available helper positions.
Prepare a concise resume highlighting your safety certifications, any relevant training, and construction site experience, even if it is general labor. Focus on transferable skills like teamwork, attention to detail, and physical stamina, which are critical for an ironworker helper.
Actively apply for Construction Ironworker Helper positions with local construction companies, steel fabricators, and union apprenticeship programs. Tailor your cover letter to express your strong interest in ironworking and your commitment to learning and safety.
Step 1
Obtain essential safety certifications such as OSHA 10 or OSHA 30, which are often mandatory for any construction site entry. These certifications demonstrate a fundamental understanding of workplace hazards and safety procedures, making you a more attractive candidate.
Step 2
Develop foundational construction skills by completing a pre-apprenticeship program or vocational training in basic carpentry, welding, or rigging. These programs provide hands-on experience with tools and materials, which are invaluable for an ironworker helper.
Step 3
Build practical experience through entry-level general labor positions on construction sites. This exposes you to the daily routines, equipment, and teamwork dynamics of a construction environment, preparing you for the demands of an ironworker helper role.
Step 4
Network with experienced ironworkers, foremen, and union representatives at local trade events, union halls, or through informational interviews. These connections can provide insights into the industry, lead to mentorship opportunities, and inform you about available helper positions.
Step 5
Prepare a concise resume highlighting your safety certifications, any relevant training, and construction site experience, even if it is general labor. Focus on transferable skills like teamwork, attention to detail, and physical stamina, which are critical for an ironworker helper.
Step 6
Actively apply for Construction Ironworker Helper positions with local construction companies, steel fabricators, and union apprenticeship programs. Tailor your cover letter to express your strong interest in ironworking and your commitment to learning and safety.
Education & Training Needed to Become a Construction Ironworker Helper
A Construction Ironworker Helper assists skilled ironworkers in erecting steel structures. This role primarily emphasizes on-the-job training and practical experience over formal academic degrees. While a high school diploma or GED is often a prerequisite, specific college degrees are not typically required or beneficial for entry into this trade.
Apprenticeship programs offer the most recognized and structured pathway into this career. These programs, usually sponsored by local unions or contractor associations, combine paid on-the-job training with classroom instruction. They typically last 3-4 years, costing minimal tuition fees, often just for books and materials, while apprentices earn an increasing percentage of a journey-level worker's wage. Non-union entry often involves starting as a general labor helper and gaining experience, which can be less structured but offers immediate entry. Community colleges may offer pre-apprenticeship programs or welding certifications that provide a foundational edge, usually ranging from 6 months to 1 year and costing between $2,000 and $10,000.
Employers highly value practical skills, safety knowledge, and a strong work ethic for Ironworker Helpers. Industry certifications in areas like welding (e.g., AWS certifications) or rigging can significantly enhance a helper's employability and demonstrate a commitment to the trade. Continuous learning in safety protocols, new tools, and techniques through workshops or online courses is crucial for advancement. The most effective educational investment for this role is hands-on training combined with formal apprenticeship, leading directly to higher-paying skilled ironworker positions.
Construction Ironworker Helper Salary & Outlook
Compensation for a Construction Ironworker Helper varies significantly based on several factors. Geographic location plays a crucial role; areas with higher costs of living or strong union presence typically offer better wages. Major metropolitan areas with ongoing large-scale construction projects often provide higher earning potential compared to rural regions.
Years of experience and the acquisition of specific skills, such as welding certifications or rigging expertise, directly impact salary progression. While a helper role is entry-level, demonstrating aptitude and a strong work ethic can accelerate advancement to a full ironworker position, unlocking higher pay scales.
Total compensation packages often extend beyond base salary. Many ironworker positions, especially those under union contracts, include comprehensive benefits like health insurance, pension plans, and paid time off. Overtime pay is also a significant component, as construction projects frequently require extended hours to meet deadlines. Some larger projects might offer per diem allowances for travel or subsistence.
Industry-specific trends, such as infrastructure spending or commercial development booms, can drive up demand and, consequently, wages. Performance and safety records are key to maintaining employment and gaining leverage for salary negotiations, particularly when transitioning to more skilled roles. Remote work is not applicable in this hands-on field, but project mobility can offer opportunities in different high-paying regions within the U.S. International markets have their own distinct compensation structures, making direct comparisons to U.S. figures challenging.
Salary by Experience Level
Level | US Median | US Average |
---|---|---|
Construction Ironworker Helper | $38k USD | $42k USD |
Junior Ironworker | $52k USD | $55k USD |
Ironworker | $65k USD | $68k USD |
Senior Ironworker | $76k USD | $80k USD |
Ironworker Foreman | $90k USD | $95k USD |
Ironworker Supervisor | $105k USD | $110k USD |
Market Commentary
The job market for Construction Ironworker Helpers and the broader ironworking profession shows a steady demand, primarily driven by infrastructure spending and commercial construction. The Bureau of Labor Statistics projects employment of structural iron and steel workers to grow 5 percent from 2022 to 2032, which is about as fast as the average for all occupations. This growth translates into approximately 2,900 openings each year, many of which will be filled by helpers advancing into skilled roles.
Current trends indicate increased investment in bridges, highways, and public buildings, alongside ongoing development of industrial and commercial structures. These projects consistently require skilled ironworkers and their indispensable helpers. The supply of qualified candidates can sometimes lag behind demand, especially for specialized welding or rigging skills, creating opportunities for those with the right training and certifications.
Emerging opportunities for ironworkers include roles in renewable energy infrastructure, such as wind turbine construction, and the modernization of existing structures. Automation and AI have a limited direct impact on the hands-on, physically demanding nature of ironworking, though digital tools for project planning and safety are becoming more prevalent. This profession is relatively resilient to economic downturns, particularly when supported by government infrastructure initiatives.
Geographic hotspots for ironworker employment include major urban centers and states with significant industrial or energy sector development. Continuous learning, especially in advanced welding techniques or new materials, is crucial for career longevity and maximizing earning potential in this evolving field.
Construction Ironworker Helper Career Path
Career progression for a Construction Ironworker Helper involves a clear path from entry-level support to skilled tradesperson, then to leadership roles. Advancement often depends on acquiring specific skills, demonstrating reliability, and obtaining certifications. The journey typically shifts from an individual contributor (IC) track, focused on hands-on craft, to a management/leadership track, which emphasizes team oversight and project coordination.
Advancement speed is influenced by consistent performance, dedication to safety, and the ability to master complex ironworking techniques. Specialization in areas like structural, ornamental, or reinforcing ironwork can also accelerate progression. Company size, project scale, and regional demand for skilled ironworkers also play significant roles in career opportunities. Larger construction firms and major infrastructure projects often offer more structured advancement paths.
Lateral movement might include transitioning between different types of ironwork (e.g., from structural to ornamental) or moving into related trades like welding or rigging. Networking within local unions and with experienced ironworkers is crucial for mentorship and job opportunities. Continuous learning, often through apprenticeship programs and on-the-job training, is fundamental. Achieving journeyman status and specialized certifications are key milestones marking significant professional growth.
Construction Ironworker Helper
0-1 yearThis entry-level role provides direct support to experienced ironworkers. Responsibilities involve assisting with material movement, organizing tools, and maintaining a clean work environment. Decisions are limited to immediate tasks under direct supervision. Impact is primarily on site organization and efficiency, ensuring materials are readily available for skilled tradespersons.
Key Focus Areas
Priorities include understanding basic construction site safety protocols, identifying tools and materials, and learning to follow directions precisely. Developing a strong work ethic, punctuality, and the ability to work effectively as part of a team are essential. Learning to assist with material handling and site preparation tasks efficiently is also vital.
Junior Ironworker
1-3 yearsA Junior Ironworker begins to perform more hands-on tasks under closer supervision. This includes assisting with the erection of steel structures, tying rebar, and performing basic cuts and welds. Decision-making involves choosing appropriate tools for specific tasks and ensuring work adheres to initial instructions. Impact is on completing assigned structural components accurately.
Key Focus Areas
Focus areas shift to mastering fundamental ironworking techniques such as tying rebar, basic welding, and operating hand tools safely. Developing proficiency in reading blueprints and understanding structural diagrams becomes important. Building a foundational understanding of different types of steel and their applications is also critical for this stage.
Ironworker
3-6 yearsAn Ironworker independently performs complex tasks such as erecting structural steel, installing precast concrete, and performing advanced welding. This role requires interpreting detailed blueprints and making independent decisions regarding installation methods and safety procedures. Impact directly affects the structural integrity and timely completion of major project components.
Key Focus Areas
Key development areas include advanced welding techniques, precise steel fitting, and complex rigging operations. Understanding load bearing capacities and structural integrity is crucial. Developing problem-solving skills for on-site challenges and enhancing communication with team members and other trades are also significant. Pursuing journeyman certification is a primary focus.
Senior Ironworker
6-10 yearsA Senior Ironworker takes on highly complex and critical structural tasks, often serving as a technical expert on the team. Responsibilities include ensuring the accuracy and quality of work, troubleshooting on-site issues, and providing guidance to less experienced ironworkers. Decisions involve critical technical solutions and adherence to stringent safety and quality standards. Impact is on the overall success and structural soundness of challenging project phases.
Key Focus Areas
Focus areas include specializing in complex structural assemblies, advanced rigging, and potentially ornamental or reinforcing ironwork. Developing mentoring skills to guide junior team members and contributing to project planning are important. Enhancing knowledge of building codes, safety regulations, and quality control standards is also critical for this advanced role.
Ironworker Foreman
10-15 yearsAn Ironworker Foreman supervises a team of ironworkers, overseeing daily operations, ensuring adherence to safety protocols, and managing task distribution. This role involves interpreting project plans, coordinating with other trades, and reporting progress to site management. Decision-making includes on-the-spot adjustments to work plans and addressing immediate team challenges. Impact is on the team's productivity, safety compliance, and meeting project deadlines for specific sections of work.
Key Focus Areas
Key development areas include leadership, team coordination, and effective communication with project managers and other foremen. Understanding project schedules, resource allocation, and budget constraints becomes vital. Developing conflict resolution skills and the ability to motivate a team under pressure are also crucial for this supervisory role.
Ironworker Supervisor
15+ yearsAn Ironworker Supervisor manages multiple ironworker crews across different project areas or entire projects. This role involves high-level planning, resource management, and ensuring compliance with all regulatory and company standards. Decision-making impacts overall project timelines, budget, and safety performance for all ironworking activities. This role requires significant leadership and strategic thinking.
Key Focus Areas
Focus areas shift to strategic planning, risk management, and overall project oversight. Developing strong communication skills for interacting with clients, engineers, and senior management is essential. Mastering advanced safety management systems and continuous improvement processes for ironworking operations is also critical. Mentoring foremen and contributing to company-wide training initiatives become important.
Construction Ironworker Helper
0-1 yearThis entry-level role provides direct support to experienced ironworkers. Responsibilities involve assisting with material movement, organizing tools, and maintaining a clean work environment. Decisions are limited to immediate tasks under direct supervision. Impact is primarily on site organization and efficiency, ensuring materials are readily available for skilled tradespersons.
Key Focus Areas
Priorities include understanding basic construction site safety protocols, identifying tools and materials, and learning to follow directions precisely. Developing a strong work ethic, punctuality, and the ability to work effectively as part of a team are essential. Learning to assist with material handling and site preparation tasks efficiently is also vital.
Junior Ironworker
1-3 yearsA Junior Ironworker begins to perform more hands-on tasks under closer supervision. This includes assisting with the erection of steel structures, tying rebar, and performing basic cuts and welds. Decision-making involves choosing appropriate tools for specific tasks and ensuring work adheres to initial instructions. Impact is on completing assigned structural components accurately.
Key Focus Areas
Focus areas shift to mastering fundamental ironworking techniques such as tying rebar, basic welding, and operating hand tools safely. Developing proficiency in reading blueprints and understanding structural diagrams becomes important. Building a foundational understanding of different types of steel and their applications is also critical for this stage.
Ironworker
3-6 yearsAn Ironworker independently performs complex tasks such as erecting structural steel, installing precast concrete, and performing advanced welding. This role requires interpreting detailed blueprints and making independent decisions regarding installation methods and safety procedures. Impact directly affects the structural integrity and timely completion of major project components.
Key Focus Areas
Key development areas include advanced welding techniques, precise steel fitting, and complex rigging operations. Understanding load bearing capacities and structural integrity is crucial. Developing problem-solving skills for on-site challenges and enhancing communication with team members and other trades are also significant. Pursuing journeyman certification is a primary focus.
Senior Ironworker
6-10 yearsA Senior Ironworker takes on highly complex and critical structural tasks, often serving as a technical expert on the team. Responsibilities include ensuring the accuracy and quality of work, troubleshooting on-site issues, and providing guidance to less experienced ironworkers. Decisions involve critical technical solutions and adherence to stringent safety and quality standards. Impact is on the overall success and structural soundness of challenging project phases.
Key Focus Areas
Focus areas include specializing in complex structural assemblies, advanced rigging, and potentially ornamental or reinforcing ironwork. Developing mentoring skills to guide junior team members and contributing to project planning are important. Enhancing knowledge of building codes, safety regulations, and quality control standards is also critical for this advanced role.
Ironworker Foreman
10-15 yearsAn Ironworker Foreman supervises a team of ironworkers, overseeing daily operations, ensuring adherence to safety protocols, and managing task distribution. This role involves interpreting project plans, coordinating with other trades, and reporting progress to site management. Decision-making includes on-the-spot adjustments to work plans and addressing immediate team challenges. Impact is on the team's productivity, safety compliance, and meeting project deadlines for specific sections of work.
Key Focus Areas
Key development areas include leadership, team coordination, and effective communication with project managers and other foremen. Understanding project schedules, resource allocation, and budget constraints becomes vital. Developing conflict resolution skills and the ability to motivate a team under pressure are also crucial for this supervisory role.
Ironworker Supervisor
15+ yearsAn Ironworker Supervisor manages multiple ironworker crews across different project areas or entire projects. This role involves high-level planning, resource management, and ensuring compliance with all regulatory and company standards. Decision-making impacts overall project timelines, budget, and safety performance for all ironworking activities. This role requires significant leadership and strategic thinking.
Key Focus Areas
Focus areas shift to strategic planning, risk management, and overall project oversight. Developing strong communication skills for interacting with clients, engineers, and senior management is essential. Mastering advanced safety management systems and continuous improvement processes for ironworking operations is also critical. Mentoring foremen and contributing to company-wide training initiatives become important.
Job Application Toolkit
Ace your application with our purpose-built resources:
Construction Ironworker Helper Resume Examples
Proven layouts and keywords hiring managers scan for.
View examplesConstruction Ironworker Helper Cover Letter Examples
Personalizable templates that showcase your impact.
View examplesTop Construction Ironworker Helper Interview Questions
Practice with the questions asked most often.
View examplesConstruction Ironworker Helper Job Description Template
Ready-to-use JD for recruiters and hiring teams.
View examplesGlobal Construction Ironworker Helper Opportunities
Construction Ironworker Helpers support skilled ironworkers globally. They assist in erecting steel structures, reinforcing concrete, and installing metal components. Demand for this role remains steady in developing and developed nations due to ongoing infrastructure and building projects. Cultural differences impact safety standards and work practices, while regulatory variations affect training and certification.
Professionals consider international opportunities for higher wages, diverse project experience, or better working conditions. No universal international certifications exist, but vocational training and on-the-job experience are highly valued worldwide.
Global Salaries
Salaries for Construction Ironworker Helpers vary significantly by region and economic development. In North America, specifically the United States, annual salaries range from $35,000 to $55,000 USD, often including benefits like health insurance and pension plans. Canadian helpers earn similar amounts, approximately $40,000 to $60,000 CAD, equivalent to $29,000-$44,000 USD, with strong union representation.
European salaries show wide variation. In Germany, helpers might earn €28,000-€40,000 annually ($30,000-$43,000 USD), while in Eastern Europe, such as Poland, wages are lower, around 35,000-50,000 PLN ($8,500-$12,000 USD). These figures reflect differing costs of living; purchasing power for a helper in Poland might be comparable to a helper in Germany, despite the lower nominal wage. In the UK, expect £25,000-£35,000 ($31,000-$44,000 USD).
Asia-Pacific markets like Australia offer competitive wages, often AUD 50,000-70,000 ($33,000-$46,000 USD), reflecting high living costs. In contrast, Southeast Asian countries, such as Thailand, might pay 150,000-250,000 THB ($4,000-$7,000 USD) annually. Latin American countries, like Brazil, offer around 30,000-50,000 BRL ($6,000-$10,000 USD). Experience and specific project demands heavily influence compensation globally. Tax implications and social security contributions also significantly affect take-home pay, varying by country.
Remote Work
International remote work opportunities are virtually nonexistent for Construction Ironworker Helpers. This role requires hands-on physical presence at construction sites. The nature of the work involves direct assistance to skilled ironworkers, handling materials, and operating equipment, which cannot be performed off-site.
Digital nomad lifestyles are not applicable to this profession. The job demands on-site collaboration and adherence to strict safety protocols. Therefore, the concept of working remotely across international borders, or leveraging geographic arbitrage for this specific role, does not apply. All work takes place on physical construction sites.
Visa & Immigration
Construction Ironworker Helpers generally rely on skilled worker visas or specific labor shortage programs for international moves. Popular destination countries include Canada, Australia, and parts of Europe (e.g., Germany, Scandinavian countries) which often have demand for skilled trades. Requirements typically involve proving relevant experience, often through employer sponsorship.
Educational credential recognition is less formal for this role; practical experience and vocational training are usually key. Some countries may require trade assessments or certifications unique to their building codes. Visa timelines vary, from a few months to over a year, depending on the country and visa type. Employers usually initiate the application process.
Pathways to permanent residency are possible in countries like Canada and Australia through points-based immigration systems that value skilled trades. Language requirements, such as English for Canada or Australia, or German for Germany, are often necessary for integration and employment. Family visas for dependents are usually part of skilled worker programs, allowing families to relocate together.
2025 Market Reality for Construction Ironworker Helpers
Understanding current market conditions for a Construction Ironworker Helper is crucial for setting realistic career expectations. The construction industry, including specialized trades, navigates shifts influenced by economic cycles and evolving project demands.
Over the past few years (2023-2025), post-pandemic supply chain adjustments and fluctuating material costs have shaped the landscape. While not directly impacted by AI displacement, the industry embraces new techniques and safety standards, requiring helpers to adapt. Market realities can vary significantly based on local construction activity, union presence, and project scale, influencing both job availability and compensation for individuals at different experience levels.
Current Challenges
Competition for entry-level helper positions remains stiff, especially in urban areas. Limited formal training programs often create a skill gap, as many employers prefer helpers with some prior site experience. Economic fluctuations directly impact project starts, leading to periods of reduced hiring.
Job security can be cyclical, tied to project completion and new contract awards. Physical demands and safety risks are constant challenges, requiring strict adherence to protocols.
Growth Opportunities
Opportunities for Construction Ironworker Helpers are robust in infrastructure development, including bridges, roads, and large commercial buildings. Industrial construction, such as energy plants and manufacturing facilities, also presents consistent demand for helpers.
Emerging opportunities exist for helpers willing to learn advanced rigging techniques or assist with prefabrication processes that incorporate new technologies. Individuals who proactively obtain basic safety certifications, like OSHA 10, or demonstrate proficiency with hand and power tools, gain a competitive edge.
Underserved markets often align with regions experiencing significant urban renewal or industrial expansion where local labor pools are tight. For instance, areas with new factory construction or large-scale public transportation projects frequently have more openings. Developing strong communication skills and a reputation for reliability can lead to rapid advancement to apprentice roles.
Despite broader economic uncertainties, sectors like essential infrastructure and critical industrial maintenance maintain consistent demand. Strategic career moves involve seeking out projects with long durations or companies known for investing in their workforce's training. Investing in basic welding or blueprint reading courses can greatly enhance long-term career prospects.
Current Market Trends
Hiring for Construction Ironworker Helpers shows steady, localized demand as of 2025, driven by infrastructure projects and commercial construction. While not directly impacted by AI in the same way as office jobs, automation in some fabrication processes means helpers need a foundational understanding of modern equipment and material handling.
Economic conditions, particularly interest rates and material costs, influence the pace of new construction, affecting job availability. Some regions, especially those with significant public works initiatives or booming industrial sectors, report stronger demand than others. Remote work is not applicable here; all work is on-site.
Employer requirements increasingly favor candidates who demonstrate strong safety awareness, a basic mechanical aptitude, and a willingness to learn on the job. While formal certifications are less common for helpers, a valid driver's license and reliable transportation are often critical. Salary trends for helpers are stable, with incremental increases tied to union agreements or project-specific prevailing wages. Market saturation is low for truly dedicated and reliable helpers who show up ready to work, but high for those without basic safety training or a strong work ethic.
Seasonal hiring patterns are pronounced; activity often slows during harsh winter months in colder climates, picking up significantly from spring through fall. This cyclical nature requires helpers to plan for potential downtime or seek temporary work during off-seasons. The post-pandemic construction boom has largely stabilized, leading to a more predictable but less frenzied hiring pace than in 2021-2022.
Emerging Specializations
The construction industry is undergoing a significant transformation, driven by advancements in robotics, material science, and digital fabrication. These shifts are creating new specialization opportunities, even for roles historically considered foundational, such as a Construction Ironworker Helper. Understanding these evolving niches allows professionals to strategically position themselves for future career growth and higher earning potential.
Early positioning in emerging areas is crucial for career advancement in 2025 and beyond. While established specializations offer stability, emerging fields often command premium compensation due to specialized skill sets and lower market saturation. Professionals who acquire these cutting-edge skills can become invaluable assets, leading to accelerated career progression.
Emerging areas typically take 3-7 years to transition from nascent concepts to mainstream opportunities with significant job volumes. This timeline provides a window for proactive professionals to invest in new training and certifications. Pursuing these cutting-edge specializations involves a balance of risk and reward; while initial demand might be lower, the long-term potential for leadership and innovation within the field is substantial.
The strategic choice to specialize in an emerging area can differentiate a Construction Ironworker Helper, moving them beyond traditional support roles into more technical and specialized functions. This proactive approach ensures relevance and competitiveness in a rapidly changing construction landscape.
Modular Construction Assembly Assistant
This specialization focuses on assisting with the assembly and installation of modular structural components fabricated off-site. As construction shifts towards greater prefabrication and modular building, ironworker helpers will need to understand the precise handling, alignment, and connection of these larger, often heavier, pre-assembled sections. This approach significantly reduces on-site labor and accelerates project timelines.
Automated Structural Assembly Technician
This role involves supporting the operation and maintenance of robotic welding and automated assembly systems used in structural steel erection. As automation becomes more prevalent on construction sites, ironworker helpers will assist in setting up, monitoring, and troubleshooting robotic equipment, ensuring proper material feeding and quality control. This includes tasks like preparing steel for robotic welding and ensuring automated systems function correctly.
Advanced Materials Installation Support
This specialization focuses on working with advanced, lightweight composite materials like carbon fiber and reinforced plastics, which are increasingly used in modern structures for their strength-to-weight ratio. Ironworker helpers will assist in the unique handling, cutting, and fastening methods required for these materials, which differ significantly from traditional steel. This includes precise installation to maintain structural integrity.
Digital Alignment & Spatial Positioning Assistant
This area involves the use of augmented reality (AR) and virtual reality (VR) tools to assist in the precise positioning, alignment, and inspection of structural steel components. Ironworker helpers will utilize AR overlays for real-time guidance during assembly, ensuring components are placed exactly as per digital models. This technology enhances accuracy and reduces errors on complex projects, improving safety and efficiency.
Renewable Energy Structure Integrator
This specialization involves assisting in the installation of structures that integrate renewable energy systems, such as solar panel mounting on steel frameworks or wind turbine tower assembly. Ironworker helpers will work with specialized tools and safety protocols unique to energy infrastructure. They will ensure the structural integrity supports the energy components, often at height, and connect these systems to the main framework.
Pros & Cons of Being a Construction Ironworker Helper
Making a career choice is a significant decision. Understanding both the advantages and challenges of a specific field is crucial for setting realistic expectations and ensuring a good fit. Career experiences can vary widely based on company culture, specific industry sector, the specialization within the role, and individual personality. Some aspects might be seen as benefits by one person and drawbacks by another, depending on personal values and lifestyle preferences. Furthermore, the pros and cons can shift at different stages of a career, from an entry-level position to a senior role. This assessment provides an honest, balanced view of the Construction Ironworker Helper role to help you make an informed decision.
Pros
- You gain practical, hands-on experience in the construction industry, learning directly from skilled ironworkers about structural steel erection, welding, and rigging techniques.
- This role offers a clear path to becoming a journey-level ironworker, allowing you to develop specialized skills and potentially enter an apprenticeship program for higher pay and responsibilities.
- The work is tangible and offers a strong sense of accomplishment; you can see the direct result of your efforts as large structures take shape from the ground up.
- There is consistent demand for skilled tradespeople in construction, providing good job security and opportunities for employment across various regions and project types.
- Many companies offer on-the-job training and opportunities to earn certifications in areas like welding, rigging, and safety, enhancing your skills and marketability.
- The work often involves being outdoors and engaging in physical activity, which can be appealing for those who prefer an active job over an office setting.
- Working in a team environment is common, fostering camaraderie and strong working relationships with fellow crew members as you collaborate on complex tasks.
Cons
- The work is physically demanding, requiring heavy lifting, bending, and working in various weather conditions, which can lead to fatigue and long-term joint or back issues.
- Safety is a constant concern due to working at heights, with heavy materials, and around machinery; despite training, the risk of serious injury remains higher than in many other professions.
- Job stability can fluctuate with construction project cycles, meaning periods of intense work may be followed by layoffs or reduced hours if new projects are not secured.
- Entry-level pay for a helper can be modest, especially when compared to the skilled ironworkers they assist, though it typically increases with experience and certifications.
- The work environment is often noisy and dirty, involving exposure to dust, metal shavings, and chemical fumes, which requires consistent use of personal protective equipment.
- Work schedules can be unpredictable, with early starts and potential for overtime or weekend work to meet project deadlines, impacting personal time and commitments.
- There is a steep learning curve for mastering the tools, techniques, and safety protocols involved in handling and connecting structural steel, requiring continuous attention and practical application of knowledge on the job site for several years to become proficient and advance in the trade.
Frequently Asked Questions
Construction Ironworker Helpers face unique challenges learning the trade while ensuring safety on demanding job sites. This section addresses the most common questions about starting in this role, from required physical fitness and safety training to career progression and expected daily tasks.
What are the basic qualifications to become a Construction Ironworker Helper?
Most Construction Ironworker Helper positions do not require formal education beyond a high school diploma or GED. Employers prioritize physical fitness, a strong work ethic, and a willingness to learn on the job. Some may prefer candidates with basic construction experience or certifications in safety, but these are often learned during initial training.
How does a Construction Ironworker Helper progress into a full Ironworker role?
The path typically starts with an entry-level helper position. You gain experience by assisting skilled ironworkers, learning techniques, and understanding safety protocols. Many helpers then pursue apprenticeships, which can take 3-4 years, to become a journeyman ironworker. This combines on-the-job training with classroom instruction, leading to higher pay and more responsibility.
What is the typical starting salary for a Construction Ironworker Helper, and what are the growth prospects?
Starting wages for a Construction Ironworker Helper vary by location and union status but typically range from $18 to $25 per hour. As you gain experience and move into an apprenticeship, your pay significantly increases, often including benefits like health insurance and retirement plans. Journeyman ironworkers can earn $35-$50+ per hour, depending on the region and specialization.
What are the daily physical demands and tasks of a Construction Ironworker Helper?
Construction Ironworker Helper work is physically demanding, involving lifting heavy materials, working at heights, and standing for long periods. You must have good stamina, strength, and balance. A typical day involves assisting with rigging, welding, bolting, and moving structural steel or rebar, always under the supervision of a skilled ironworker. Safety is paramount, with strict adherence to protocols.
What is the work-life balance like for a Construction Ironworker Helper, considering the physical demands and potential travel?
The work-life balance can be challenging due to demanding schedules, especially during peak construction seasons. Overtime is common, and projects may require travel or working in various weather conditions. However, the industry often provides good pay for the hours worked, and many find satisfaction in the tangible results of their labor.
Is there good job security and demand for Construction Ironworker Helpers?
Job security for Construction Ironworker Helpers is generally stable, driven by ongoing infrastructure development and commercial construction projects. While economic downturns can cause temporary slowdowns, the demand for skilled ironworkers remains consistent long-term. As you gain experience and certifications, your employability significantly increases, making you a valuable asset.
Are there specific certifications or training programs that would help me get hired as a Construction Ironworker Helper?
While not strictly required, obtaining certifications in areas like OSHA 10 or OSHA 30, rigging, welding, or first aid can significantly boost your resume. These demonstrate a commitment to safety and a foundational understanding of key industry practices. Many employers or apprenticeship programs will provide or require these certifications as part of your training.
How important is safety, and what kind of safety training can I expect as an Ironworker Helper?
Safety is the absolute top priority. Ironworker Helpers receive extensive training on fall protection, proper lifting techniques, equipment operation, and hazard recognition. You will always wear personal protective equipment (PPE) like hard hats, safety glasses, gloves, and steel-toed boots. Adhering to strict safety protocols and constant vigilance are essential to prevent accidents on site.
Related Careers
Explore similar roles that might align with your interests and skills:
Ironworker
A growing field with similar skill requirements and career progression opportunities.
Explore career guideBridge Ironworker Helper
A growing field with similar skill requirements and career progression opportunities.
Explore career guideConstruction Ironworker
A growing field with similar skill requirements and career progression opportunities.
Explore career guideOrnamental Ironworker Helper
A growing field with similar skill requirements and career progression opportunities.
Explore career guidePost Tensioning Ironworker Helper
A growing field with similar skill requirements and career progression opportunities.
Explore career guideAssess your Construction Ironworker Helper readiness
Understanding where you stand today is the first step toward your career goals. Our Career Coach helps identify skill gaps and create personalized plans.
Skills Gap Analysis
Get a detailed assessment of your current skills versus Construction Ironworker Helper requirements. Our AI Career Coach identifies specific areas for improvement with personalized recommendations.
See your skills gapCareer Readiness Assessment
Evaluate your overall readiness for Construction Ironworker Helper roles with our AI Career Coach. Receive personalized recommendations for education, projects, and experience to boost your competitiveness.
Assess your readinessSimple pricing, powerful features
Upgrade to Himalayas Plus and turbocharge your job search.
Himalayas
Himalayas Plus
Himalayas Max
Find your dream job
Sign up now and join over 100,000 remote workers who receive personalized job alerts, curated job matches, and more for free!
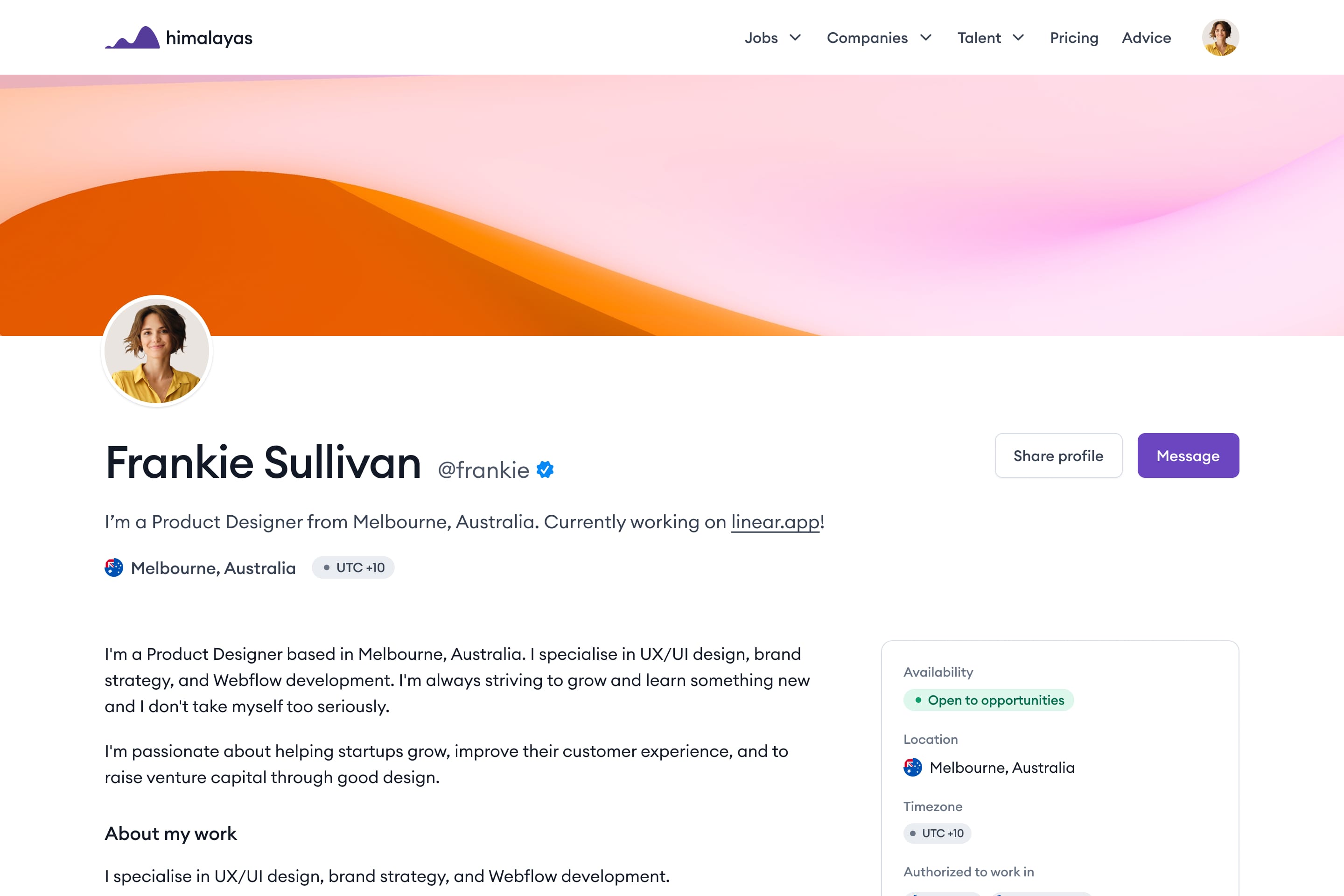