Complete Airset Caster Career Guide
Airset casters are the artisans behind complex metal components, transforming raw materials into precision parts vital for industries like aerospace and defense. This specialized role demands meticulous attention to detail and a deep understanding of foundry processes, ensuring the integrity of critical castings. It's a hands-on career for those who thrive on turning intricate designs into tangible, high-quality products.
Key Facts & Statistics
Median Salary
$45,610 USD
(U.S. Bureau of Labor Statistics, May 2023, for Foundry Mold and Coremakers)
Range: $35k - $60k+ USD, varying by experience, specialization, and location
Growth Outlook
1%
as fast as average (U.S. Bureau of Labor Statistics, 2022-2032)
Annual Openings
≈13,600
openings annually (for Foundry Workers, U.S. Bureau of Labor Statistics)
Top Industries
Typical Education
High school diploma or equivalent, with significant on-the-job training or apprenticeship
What is an Airset Caster?
An Airset Caster is a skilled professional responsible for producing metal castings using the airset molding process. This method involves using sand molds mixed with chemical binders that cure at room temperature (air-setting), creating highly stable and accurate molds. The caster's primary role is to oversee the entire casting process, from preparing the molds and melting the metal to pouring and initial post-casting handling.
This role differs significantly from a traditional 'Sand Caster' who might work with green sand (clay-bonded sand that requires compaction) or a 'Die Caster' who uses permanent metal molds. An Airset Caster specializes in a process that allows for greater precision and the production of complex geometries, often used for intricate industrial components where tight tolerances are critical. Their expertise ensures the structural integrity and dimensional accuracy of the final metal products, which are vital for industries like aerospace, automotive, and heavy machinery.
What does an Airset Caster do?
Key Responsibilities
- Prepare molds and cores by applying release agents, ensuring proper alignment, and verifying cavity integrity before pouring molten metal.
- Operate and monitor melting furnaces, controlling temperature and metal composition to achieve the precise alloy specifications required for casting.
- Pour molten metal into prepared molds, carefully controlling the flow rate and temperature to prevent defects and ensure complete mold filling.
- Monitor the cooling process of castings, adjusting environmental factors like airflow or temperature to optimize solidification and minimize stress.
- Remove solidified castings from molds, using appropriate tools and techniques to prevent damage to the finished product.
- Inspect finished castings for quality defects such as cracks, porosity, or surface imperfections, and document findings for process improvement.
- Maintain and clean casting equipment, including furnaces, ladles, and molds, to ensure operational efficiency and extend equipment lifespan.
Work Environment
Airset casters typically work in foundries or metal casting facilities, which are industrial environments characterized by high temperatures, noise from machinery, and the presence of molten metal and fumes. The work often involves standing for long periods, lifting heavy materials, and operating machinery. Collaboration with other foundry workers, such as mold makers and quality control technicians, is common to ensure efficient production. Schedules can vary, often involving shifts to accommodate continuous casting operations. The pace is generally steady but can become fast-paced during pouring sequences. Safety protocols are extremely strict due to the inherent hazards of working with extreme heat and heavy equipment.
Tools & Technologies
Airset casters primarily use specialized casting equipment, including induction furnaces or arc furnaces for melting metals. They work with various types of sand molds, often prepared with binders that harden upon exposure to air or chemical catalysts. Essential tools include ladles for transferring molten metal, pyrometers for temperature measurement, and personal protective equipment (PPE) such as heat-resistant clothing, gloves, and face shields. They also utilize grinding tools, chipping hammers, and various hand tools for post-casting cleanup and fettling. Depending on the facility, they might use overhead cranes or forklifts for material handling and basic computer systems for process monitoring or inventory tracking.
Airset Caster Skills & Qualifications
The role of an Airset Caster involves specialized skills focused on creating molds and cores using airset sand processes, primarily within foundries. This position demands a blend of hands-on technical proficiency and a deep understanding of metallurgical principles and casting defects. Qualification structures in this field heavily prioritize practical experience and demonstrated competence over formal academic degrees.
Requirements for an Airset Caster vary significantly by the size and specialization of the foundry. Larger operations with automated systems may seek individuals with experience in operating advanced machinery and monitoring process controls. Smaller, more traditional foundries often value manual dexterity and a keen eye for detail in mold assembly and finish. Industry sector also plays a role; aerospace or medical casting foundries demand extremely high precision and adherence to strict quality protocols, while general industrial casting might be more forgiving.
Formal education, such as a degree, is rarely a prerequisite for entry-level Airset Caster positions. Vocational training, apprenticeships, or on-the-job training are the most common and accepted pathways. Certifications in foundry technology or specific casting processes, while not always mandatory, significantly enhance a candidate's profile and can lead to higher-paying or supervisory roles. The skill landscape evolves with new materials and automation, requiring casters to adapt to new equipment and quality control methods. Continuous learning in areas like lean manufacturing or advanced material science adds substantial value.
Education Requirements
Technical Skills
- Airset sand mixing and preparation (resin, hardener, sand ratios)
- Core making and assembly (shell cores, no-bake cores)
- Molding techniques (flask setup, parting lines, risers, gates, runners)
- Pattern recognition and cleaning (identifying pattern defects, proper release agent application)
- Basic metallurgy (understanding metal shrinkage, solidification, pouring temperatures)
- Use of hand tools (shovels, trowels, mallets, clamps) and pneumatic tools (sand rammers)
- Quality inspection (visual inspection of molds, basic measurement tools)
- Foundry safety protocols (PPE, lockout/tagout, molten metal handling)
- Defect identification and troubleshooting (gas porosity, sand inclusions, misruns)
- Preventative maintenance of molding equipment
Soft Skills
- Attention to Detail: Critical for ensuring mold integrity, accurate dimensions, and preventing defects, which directly impacts casting quality.
- Problem-Solving: Essential for diagnosing and rectifying issues with sand mix, mold assembly, or casting defects quickly to maintain production schedules.
- Safety Consciousness: Paramount in a foundry environment due to heavy machinery, molten metal, and hazardous materials; strict adherence to safety protocols protects oneself and coworkers.
- Physical Stamina: The role often involves manual labor, lifting, and working in demanding environments, requiring sustained physical effort.
- Teamwork: Collaboration with pattern makers, furnace operators, and quality control personnel ensures a smooth and efficient casting process.
- Adaptability: Adjusting to changes in production schedules, material specifications, or equipment breakdowns is vital for maintaining productivity.
- Time Management: Efficiently managing tasks like mold preparation, core setting, and pouring schedules to meet production deadlines.
- Initiative: Taking proactive steps to identify and resolve potential issues before they impact casting quality or production flow demonstrates commitment to the role and quality.
How to Become an Airset Caster
Entering the Airset Caster field typically involves a blend of practical training and hands-on experience, distinguishing it from roles requiring extensive academic degrees. Traditional entry often begins with apprenticeships or entry-level laborer positions within foundries, where individuals learn directly on the job. The timeline for becoming proficient can vary; a complete beginner might spend 6-12 months gaining foundational knowledge and basic skills before advancing, while someone with prior manufacturing experience might transition faster, perhaps in 3-6 months.
Multiple entry routes exist, including vocational programs focused on metallurgy or casting, which provide a structured learning environment and practical skills. However, many foundries still prioritize on-the-job training due to the unique processes involved. Geographic location significantly impacts opportunities; major industrial regions with strong manufacturing sectors, particularly those with a history of metalworking, will offer more entry points than areas without such infrastructure.
It is a misconception that this field is solely about manual labor; precision, attention to detail, and an understanding of material science are crucial. Networking within local industrial communities and attending trade-specific job fairs can open doors. The hiring landscape values reliability, a strong work ethic, and a willingness to learn specialized techniques. Overcoming barriers often involves demonstrating commitment and a capacity for detailed, repetitive work, making a strong case for practical aptitude over formal qualifications.
Step 1
Step 2
Step 3
Step 4
Step 5
Step 6
Education & Training Needed to Become an Airset Caster
Becoming an Airset Caster involves a distinct educational pathway, often differing from traditional university degrees. This specialized role, central to metal casting, typically requires hands-on training rather than academic credentials. While a formal four-year engineering degree (costing $40k-$100k+) offers theoretical foundations in metallurgy, it is not a direct prerequisite for this specific casting position. Most successful Airset Casters gain expertise through apprenticeships, vocational programs, or on-the-job training, which are more cost-effective and directly relevant.
Apprenticeships or specialized vocational programs, ranging from 6 to 24 months and costing $0 to $10,000, provide the practical skills essential for airset molding. These programs focus on mold making, sand mixing, pouring techniques, and safety protocols. Employer acceptance of these practical credentials is high, as they demonstrate immediate job readiness. Self-study, while possible for theoretical knowledge, cannot replace the hands-on experience required to master the nuances of airset casting.
Continuous learning in this field involves staying updated on new materials, equipment, and safety standards through manufacturer training or industry workshops. The educational needs for an Airset Caster are highly specific to the casting process itself, prioritizing practical experience over extensive theoretical knowledge. Cost-benefit considerations heavily favor vocational training or apprenticeships, as they offer a direct path to employment with minimal educational debt. Quality programs often hold industry recognition through associations like the American Foundry Society, ensuring adherence to professional standards.
Airset Caster Salary & Outlook
Compensation for an Airset Caster varies significantly based on several factors, reflecting the specialized skills and physical demands of the role. Geographic location plays a crucial role; areas with a higher concentration of foundries or industrial manufacturing often offer more competitive wages due to demand and cost of living. For instance, states in the Midwest or industrial belts may show different pay scales compared to regions with less heavy industry.
Experience and specific skill sets dramatically influence earning potential. An Airset Caster proficient in handling complex molds, operating advanced machinery, or working with diverse metal alloys can command higher pay. Total compensation packages frequently extend beyond base salary, including overtime pay, production bonuses, and comprehensive benefits such as health insurance, retirement contributions, and paid time off. Some companies may also offer allowances for specialized training or certifications.
Industry-specific trends, particularly within the manufacturing and automotive sectors, drive salary growth for Airset Casters. Companies investing in modern airset molding technologies or expanding production lines often offer better compensation to attract and retain skilled talent. Negotiation leverage for a Caster comes from demonstrating a proven track record of efficiency, quality, and safety compliance. While most Airset Caster roles require on-site presence, remote work does not apply to this hands-on position. Salary figures provided are primarily in USD, with international markets showing variations based on local industrial wages and economic conditions.
Salary by Experience Level
Level | US Median | US Average |
---|---|---|
Junior Airset Caster | $42k USD | $45k USD |
Airset Caster | $55k USD | $58k USD |
Senior Airset Caster | $68k USD | $70k USD |
Lead Airset Caster | $80k USD | $82k USD |
Casting Supervisor | $92k USD | $95k USD |
Market Commentary
The job market for Airset Casters shows steady demand, largely driven by the continuous need for cast metal components across various industries, including automotive, aerospace, and heavy machinery. While traditional manufacturing has seen shifts, the specialized nature of airset casting, which allows for intricate and high-quality parts, maintains its relevance. The growth outlook is stable, projected at around 2-4% over the next decade, aligning with the overall manufacturing sector's modest expansion.
Emerging opportunities for Airset Casters stem from advancements in automation and material science. Foundries are increasingly integrating robotic pourers and automated sand handling systems, requiring Casters to adapt to overseeing these technologies rather than purely manual operations. This shift necessitates a blend of traditional casting expertise with an understanding of digital controls and process optimization. The demand for skilled Casters often outpaces the supply of qualified candidates, particularly those with experience in modern airset techniques, creating a favorable market for experienced professionals.
Future-proofing in this role involves continuous learning in new casting technologies, quality control methods, and safety protocols. While automation assists, the human element of skilled oversight and problem-solving remains critical for complex casting processes. This profession is relatively recession-resistant as it serves foundational industries, though demand can fluctuate with economic cycles in sectors like automotive. Geographic hotspots for Airset Casters remain concentrated in industrial regions with strong manufacturing bases, particularly in the Midwest and Southeast United States.
Airset Caster Career Path
Career progression for an Airset Caster typically follows a structured path, emphasizing hands-on skill development, efficiency, and eventually leadership within a foundry environment. Advancement hinges on mastering the intricacies of the airset molding process, from pattern preparation to mold assembly and pouring.
Progression offers both individual contributor (IC) tracks, where casters deepen their technical expertise and potentially specialize in complex casting techniques, and management/leadership tracks, which involve overseeing teams, optimizing production, and managing safety protocols. Factors like consistent performance, adherence to safety standards, and a willingness to train new team members significantly influence advancement speed. Company size and the specific type of foundry (e.g., aerospace, automotive, general industrial) also dictate the pace and specific opportunities for growth.
Lateral movement might involve transitioning to related foundry roles like pattern making, quality control, or metallurgy, leveraging a deep understanding of casting processes. Continuous learning in materials science, automation, and advanced casting technologies is crucial. Networking within the foundry industry and pursuing relevant certifications, particularly in safety and quality, can solidify one's reputation and open doors to supervisory or specialized roles.
Junior Airset Caster
0-2 yearsKey Focus Areas
Airset Caster
2-5 yearsKey Focus Areas
Senior Airset Caster
5-8 yearsKey Focus Areas
Lead Airset Caster
8-12 yearsKey Focus Areas
Casting Supervisor
12+ yearsKey Focus Areas
Junior Airset Caster
0-2 yearsPerforms basic airset casting tasks under direct supervision. Responsibilities include preparing patterns, mixing sand, operating sand mixers, and assisting with mold assembly. Follows established procedures and safety guidelines to produce simple castings. Impact is primarily on individual task completion and learning correct techniques.
Key Focus Areas
Develop foundational skills in pattern handling, sand mixing, and basic mold assembly. Learn to identify common molding defects and understand their causes. Focus on strict adherence to safety protocols and tool maintenance. Building a strong work ethic and attention to detail are critical at this stage.
Airset Caster
2-5 yearsIndependently performs airset casting operations for a variety of part complexities. Sets up molds, operates machinery, and conducts quality checks on finished castings. Works with minimal supervision, making routine decisions about process adjustments. Contributes to daily production targets and quality standards.
Key Focus Areas
Master advanced molding techniques, including complex core setting and gating systems. Improve efficiency and reduce scrap rates. Develop problem-solving skills for common casting challenges. Begin to understand the impact of process variables on casting quality. Cross-training on different casting machines or materials is beneficial.
Senior Airset Caster
5-8 yearsHandles complex and critical airset casting projects, often involving tight tolerances or specialized materials. Troubleshoots intricate molding issues and implements solutions. Provides technical expertise to the team and may lead small, specialized production runs. Exercises significant autonomy in operational decision-making.
Key Focus Areas
Specialize in challenging casting geometries or exotic alloys. Mentor junior casters and provide technical guidance. Optimize casting parameters for improved yield and quality. Develop a deeper understanding of metallurgical properties and their relation to casting performance. Pursue certifications in quality control or specific casting processes.
Lead Airset Caster
8-12 yearsOversees a specific section of the airset casting floor, coordinating tasks and ensuring production schedules are met. Provides direct guidance and mentorship to a team of casters. Identifies and resolves operational bottlenecks, ensuring quality and safety standards are consistently upheld. Reports on team performance and material usage.
Key Focus Areas
Develop strong leadership and communication skills. Focus on workflow optimization, scheduling, and resource allocation for casting operations. Learn to analyze production data to identify areas for improvement. Participate in training program development and implement best practices. Understand lean manufacturing principles.
Casting Supervisor
12+ yearsManages the entire airset casting department, including personnel, equipment, and production processes. Responsible for meeting overall production targets, quality metrics, and safety compliance. Makes strategic decisions regarding staffing, equipment upgrades, and process improvements. Collaborates with engineering and sales to ensure efficient project execution and customer satisfaction.
Key Focus Areas
Cultivate comprehensive management skills, including budgeting, performance evaluation, and strategic planning for the casting department. Master advanced problem-solving and root cause analysis techniques. Focus on continuous improvement initiatives and technological adoption. Develop strong interpersonal skills for managing a diverse workforce and collaborating with other departments.
Job Application Toolkit
Ace your application with our purpose-built resources:
Global Airset Caster Opportunities
Airset casters shape and pour molten metal into molds, specializing in non-ferrous alloys for diverse industrial parts. This role demands precision and adherence to strict material specifications across global manufacturing hubs. International demand remains steady in countries with strong aerospace, automotive, and heavy machinery sectors. Cultural differences affect workplace safety standards and production methodologies. International certifications in metallurgy or casting technology can significantly enhance global mobility.
Global Salaries
Salaries for airset casters vary significantly by region, reflecting local industrial demand and cost of living. In North America, particularly the US and Canada, annual salaries range from $45,000 to $70,000 USD. Experienced casters in industrial states like Ohio or Michigan might earn at the higher end. European salaries, converted to USD, typically fall between $35,000 and $60,000. Countries like Germany and the UK offer competitive wages, often accompanied by strong social benefits like extended vacation and comprehensive healthcare, which effectively boost overall compensation.
In Asia-Pacific, salaries in countries like South Korea or Japan range from $28,000 to $48,000 USD. China's manufacturing sector offers $20,000 to $35,000 USD, but with a lower cost of living. Latin American countries, such as Mexico or Brazil, see salaries from $15,000 to $25,000 USD, though purchasing power in these regions can be higher for local goods and services. Tax implications also differ; for example, European countries often have higher income taxes but offer more public services, impacting take-home pay differently than in North America.
Experience and specialized skills, such as expertise in specific alloy types or advanced casting techniques, command higher compensation globally. Some international companies might have standardized pay scales for similar roles across their global operations, but local market conditions usually dictate the final offer. Understanding these variations helps airset casters evaluate potential international opportunities more accurately.
Remote Work
Direct remote work opportunities for airset casters are virtually nonexistent. This role requires hands-on interaction with heavy machinery, molten metals, and physical molds in a foundry environment. The nature of the work, involving precise pouring, temperature control, and safety protocols, necessitates on-site presence. Digital nomad opportunities do not apply to this profession.
However, some related roles, like casting process engineers or quality control specialists who analyze data remotely, might have limited hybrid options. These roles are distinct from the airset caster's core responsibilities. Employers in the manufacturing sector rarely support international remote work for operational roles like airset casting due to equipment, safety, and production line dependencies. Geographic arbitrage is not relevant for this hands-on, location-dependent profession.
Visa & Immigration
Airset casters typically qualify for skilled worker visas in countries with strong manufacturing sectors. Popular destinations include Germany, Canada, Australia, and the United States. Each country has specific requirements; for instance, Germany's skilled immigration law requires a recognized vocational qualification and a job offer. Canada's Express Entry system considers skilled trades, where experience as an airset caster can be valuable. Australia's skilled occupation list often includes roles in manufacturing and metallurgy.
Credential recognition for vocational training is crucial. Applicants might need to undergo skills assessments by professional bodies in the destination country. Visa timelines vary, ranging from a few months to over a year, depending on the country and application volume. English language proficiency tests, like IELTS or CELPIP, are often mandatory for English-speaking countries. Some European countries may require basic proficiency in their national language.
Pathways to permanent residency often exist after several years of continuous skilled employment. Family visas are generally available for spouses and dependents. No specific fast-track programs for airset casters are widely advertised, but strong demand in certain regions can expedite processing. Understanding these country-specific nuances is vital for a successful international career move.
2025 Market Reality for Airset Casters
Understanding the current market reality for an Airset Caster is crucial for career planning. The industrial landscape is shifting, and staying informed helps professionals adapt.
Over the past few years, particularly from 2023 to 2025, the casting industry has seen significant changes driven by post-pandemic supply chain adjustments and a push towards automation. Broader economic factors, such as manufacturing output and material costs, directly influence job availability. Market realities also vary by a caster's experience level, the region's industrial concentration, and the specific foundry's size and investment in technology.
Current Challenges
Airset casters face increasing pressure from automation in foundries. Many facilities are investing in robotic pouring and mold handling, reducing the need for manual labor.
Economic downturns directly impact manufacturing, leading to reduced production quotas and potential layoffs in the casting sector. Maintaining consistent output quality is also a constant challenge in a demanding market.
Growth Opportunities
Despite automation, opportunities exist for Airset casters who specialize in niche or complex alloy casting. Industries requiring high-precision components, such as aerospace or medical devices, still rely on skilled manual casting and intricate airset processes.
Professionals who cross-train in robotics operation, quality control automation, or advanced metallurgical testing gain a significant advantage. Becoming proficient in maintaining or programming automated pouring lines can transition a caster into a supervisory or technical support role, which are in higher demand.
Underserved markets might include smaller, specialized foundries that cannot afford full automation but require consistent, high-quality output. These operations often seek experienced casters willing to take on broader responsibilities. Strategic career moves involve pursuing certifications in advanced materials or automation systems, positioning oneself as a valuable asset in a modern foundry environment.
Current Market Trends
Demand for skilled Airset casters remains steady but is not experiencing significant growth as of 2025. Many foundries are modernizing their operations, leading to a focus on efficiency and automation. This means fewer new positions but a consistent need for experienced professionals who can manage complex casting processes.
The integration of advanced monitoring systems and robotics is a key trend. Casters now need to understand how to operate and oversee automated pouring lines, not just perform manual tasks. Employers seek candidates with a blend of traditional casting expertise and an aptitude for technology, including basic troubleshooting of automated equipment.
Salary trends for Airset casters show stability, with slight increases for those demonstrating proficiency with new technologies. Entry-level positions are becoming less common as companies favor experienced casters or invest in automation. Geographic variations are significant; regions with strong manufacturing bases, particularly automotive or heavy machinery, show more consistent demand. Remote work is not applicable to this hands-on role.
Emerging Specializations
The landscape of manufacturing, particularly in casting, is undergoing significant transformation. Advanced technologies like automation, robotics, and new material science are creating unprecedented opportunities for specialization. Professionals who proactively position themselves in these emerging areas gain a distinct advantage, often commanding premium compensation and accelerated career growth well into 2025 and beyond.
Early positioning in these nascent fields allows Airset Casters to become subject matter experts as demand escalates. While established specializations offer stability, emerging areas promise innovation and leadership roles. The most promising emerging areas typically transition from niche to mainstream within five to ten years, generating a substantial volume of job opportunities.
Pursuing cutting-edge specializations involves a balance of risk and reward. It requires continuous learning and adaptability, but the potential for significant career impact and higher earning potential is substantial. Understanding these strategic implications helps professionals make informed choices about their future career trajectory.
Automated Casting Systems Operator
Digital Process Optimization Specialist
Eco-Friendly Casting Technologist
Hybrid Manufacturing Integration Specialist
In-Line Quality Assurance Technician
Pros & Cons of Being an Airset Caster
Understanding both the advantages and challenges of a career path is crucial for making an informed decision. Career experiences vary significantly based on company culture, industry sector, specific specialization, and individual preferences. What one person views as a benefit, another might see as a drawback, underscoring the importance of personal values and lifestyle alignment. Moreover, the pros and cons can evolve at different stages of a career, from entry-level to senior positions. This assessment provides an honest, balanced perspective on the realities of working as an Airset Caster, helping prospective job seekers set appropriate expectations for this demanding but essential role.
Pros
- Airset casters typically find stable employment due to the consistent demand for metal components across various industries like automotive, aerospace, and manufacturing.
- The role offers opportunities for hands-on work and direct involvement in the manufacturing process, which can be satisfying for individuals who prefer tangible results.
- Entry into this field often requires vocational training or on-the-job learning rather than a four-year degree, making it accessible to a wider range of individuals seeking skilled trades.
- Workers in foundry environments, including Airset Casters, often earn competitive hourly wages, especially with experience and specialized skills in the casting process.
- There is a strong sense of camaraderie and teamwork among foundry workers, as many tasks require close coordination and mutual support to ensure safety and efficiency.
- Developing expertise in airset casting provides valuable skills in metallurgy, mold making, and material handling, which are transferable to other areas within the manufacturing sector.
- The process of transforming raw materials into finished metal products can be intellectually engaging, requiring precision and an understanding of chemical and physical properties.
Cons
- The work environment is often hot, dusty, and noisy due to the nature of metal casting operations, which can be physically demanding and uncomfortable over long shifts.
- Airset casters face exposure to fumes, molten metal, and heavy machinery, requiring strict adherence to safety protocols and the constant use of personal protective equipment.
- The job involves repetitive tasks and heavy lifting, which can lead to physical strain, fatigue, and an increased risk of musculoskeletal injuries over time.
- Work schedules often include irregular hours, night shifts, weekends, and overtime, as casting operations typically run continuously to meet production demands.
- Career progression can be limited within this specific role; advancement often requires transitioning into supervisory positions, quality control, or other specialized areas within the foundry.
- The manual nature of the work means less intellectual stimulation compared to roles requiring complex problem-solving or strategic thinking, which some individuals may find unfulfilling.
- Technological advancements, such as automated casting processes, could potentially impact job demand in the long term, requiring workers to adapt or retrain for new roles in the industry.
Frequently Asked Questions
Airset Casters operate complex machinery and handle molten metal, facing distinct challenges related to safety, precision, and physical demands. This section addresses crucial questions about entering this specialized trade, from training requirements to the work environment and career stability.
What are the typical entry requirements and qualifications to become an Airset Caster?
Becoming an Airset Caster typically starts with on-the-job training or an apprenticeship. While a specific degree is not usually required, a high school diploma or GED is standard. Some employers prefer candidates with vocational training in metallurgy, foundry operations, or industrial mechanics, which can provide a strong foundational understanding of the processes involved.
How long does it take to become a skilled Airset Caster, from starting as a trainee to being fully proficient?
The timeline to become a proficient Airset Caster can range from 1 to 3 years. Initial training focuses on safety protocols, equipment operation, and basic casting techniques. Mastery of the role, including understanding various alloys, troubleshooting, and achieving consistent quality, develops over several years of hands-on experience and continuous learning within the foundry environment.
What are the realistic salary expectations for an entry-level and experienced Airset Caster?
Starting salaries for Airset Caster trainees can range from $35,000 to $45,000 annually, depending on location and company. Experienced Airset Casters with specialized skills and a proven track record can earn between $50,000 and $70,000 or more per year. Overtime opportunities are often available, which can significantly boost overall earnings.
What is the typical work-life balance and daily work environment like for an Airset Caster?
The work-life balance for an Airset Caster can vary, as foundry operations often run 24/7. This means shifts can include nights, weekends, and holidays. The work is physically demanding, involving heavy lifting, standing for long periods, and working in hot environments. Despite the challenging conditions, many find stability and a sense of camaraderie within their teams.
Is the Airset Caster role stable, and what are the long-term job security prospects in this field?
Job security for Airset Casters is generally stable, particularly in industries that rely on cast metal components, such as automotive, aerospace, and heavy machinery manufacturing. While automation can impact some roles, the specialized skill set required to operate and troubleshoot complex airset casting equipment ensures ongoing demand for skilled professionals. The aging workforce in many foundries also creates opportunities for new entrants.
What are the common career growth paths and advancement opportunities for an Airset Caster?
Career growth for an Airset Caster often involves moving into supervisory roles, becoming a lead caster, or specializing in quality control or maintenance of casting equipment. Some experienced casters transition into roles like foundry technicians, metallurgists (with further education), or even into sales of casting equipment and materials. Continuous learning about new materials and processes is key for advancement.
What are the biggest challenges or common misconceptions about working as an Airset Caster?
The primary challenges include working in a demanding physical environment with high temperatures and noise levels. Safety is paramount, requiring strict adherence to protocols to prevent injuries from molten metal or heavy machinery. Maintaining precision and quality control under pressure is also a constant challenge, as even small errors can lead to costly defects in castings.
Does the Airset Caster role offer any remote work options or significant geographical flexibility?
Remote work is not feasible for an Airset Caster, as the role requires hands-on operation of heavy machinery and direct involvement in the casting process within a manufacturing facility. Therefore, geographical flexibility is limited to the location of foundries and manufacturing plants. Relocation might be necessary to pursue specific opportunities or higher-paying positions in areas with a high concentration of casting operations.
Related Careers
Explore similar roles that might align with your interests and skills:
Airset Molder
A growing field with similar skill requirements and career progression opportunities.
Explore career guideFoundry Molder
A growing field with similar skill requirements and career progression opportunities.
Explore career guideIngot Caster
A growing field with similar skill requirements and career progression opportunities.
Explore career guideNo Bake Molder
A growing field with similar skill requirements and career progression opportunities.
Explore career guideWhite Metal Caster
A growing field with similar skill requirements and career progression opportunities.
Explore career guideAssess your Airset Caster readiness
Understanding where you stand today is the first step toward your career goals. Our Career Coach helps identify skill gaps and create personalized plans.
Skills Gap Analysis
Get a detailed assessment of your current skills versus Airset Caster requirements. Our AI Career Coach identifies specific areas for improvement with personalized recommendations.
See your skills gapCareer Readiness Assessment
Evaluate your overall readiness for Airset Caster roles with our AI Career Coach. Receive personalized recommendations for education, projects, and experience to boost your competitiveness.
Assess your readinessSimple pricing, powerful features
Upgrade to Himalayas Plus and turbocharge your job search.
Himalayas
Himalayas Plus
Himalayas Max
Find your dream job
Sign up now and join over 100,000 remote workers who receive personalized job alerts, curated job matches, and more for free!
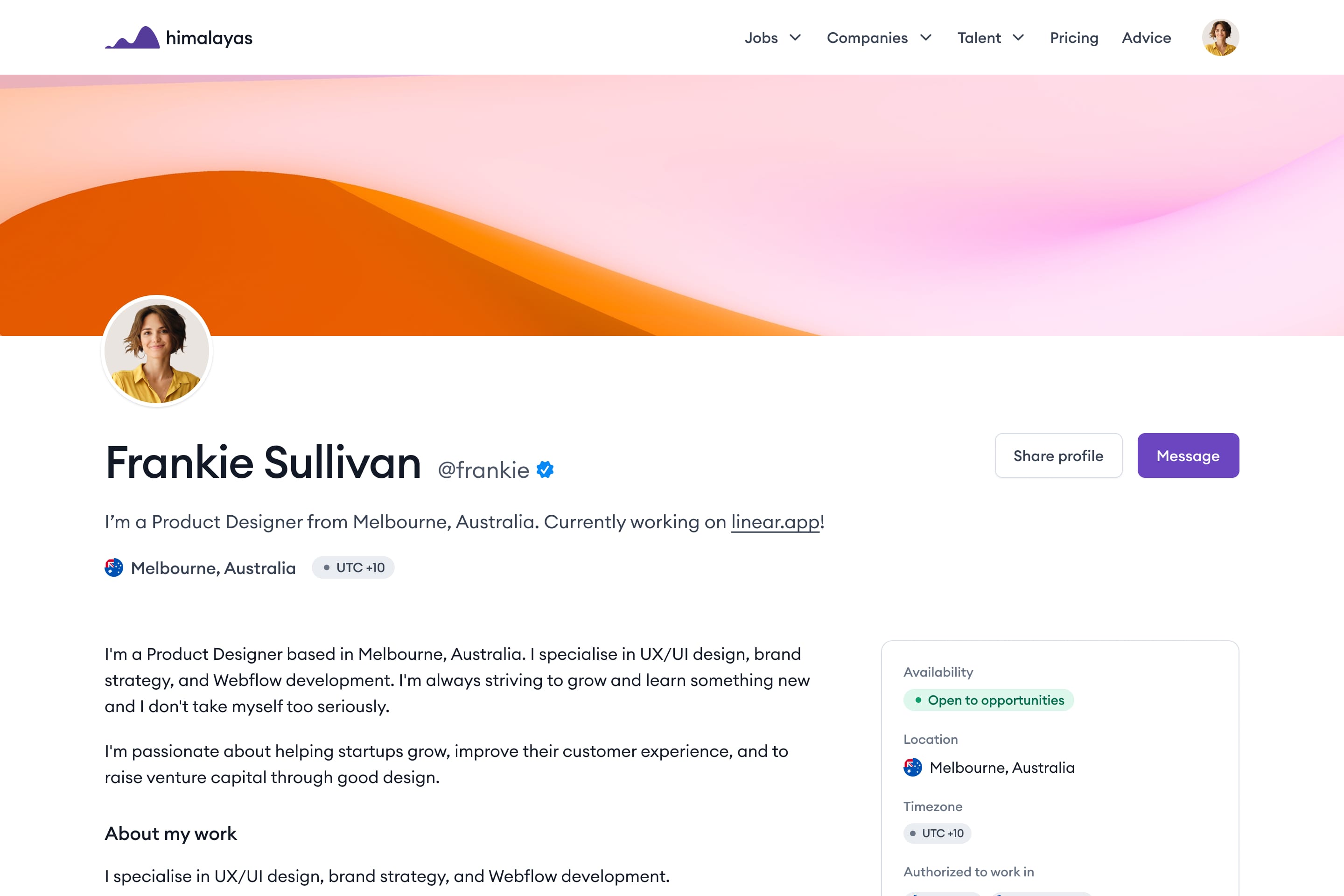