7 Tool Maker Interview Questions and Answers
Tool Makers are skilled professionals who design, create, and maintain tools, dies, and specialized equipment used in manufacturing processes. They work with precision instruments and machinery to ensure tools meet exact specifications. Junior roles focus on learning and assisting with basic tasks, while senior and lead roles involve overseeing projects, mentoring team members, and ensuring quality standards are met. Need to practice for an interview? Try our AI interview practice for free then unlock unlimited access for just $9/month.
Unlimited interview practice for $9 / month
Improve your confidence with an AI mock interviewer.
No credit card required
1. Apprentice Tool Maker Interview Questions and Answers
1.1. Can you describe a project where you had to use precision measurement tools in your work as a tool maker?
Introduction
This question assesses your technical skills and understanding of precision measurement, which are crucial for ensuring quality in tool making.
How to answer
- Clearly outline the project and its objectives.
- Specify the precision measurement tools you used, such as calipers, micrometers, or gauges.
- Explain how you ensured accuracy and quality in the measurements.
- Discuss any challenges faced and how you overcame them.
- Highlight the outcome of the project and any impact it had on the production process.
What not to say
- Vague references to measurements without specifics.
- Failing to explain the importance of precision in tool making.
- Neglecting to mention any challenges encountered.
- Only focusing on the tools without discussing the results.
Example answer
“During my internship at a local manufacturing company, I worked on creating a set of precision dies for metal stamping. I used calipers and micrometers to measure dimensions with a tolerance of ±0.01 mm. Initially, I faced challenges with the calibration of the tools, but I consulted with my supervisor and learned to adjust them correctly. This attention to detail ensured the final dies met the required specifications, leading to a 15% reduction in material waste during production.”
Skills tested
Question type
1.2. Describe a time when you had to work as part of a team to complete a tool-making project.
Introduction
This question evaluates your teamwork and collaboration skills, which are essential in a workshop environment where multiple roles often intersect.
How to answer
- Use the STAR method to structure your response.
- Describe your role in the team and the project's objective.
- Explain how you communicated and collaborated with team members.
- Detail any conflicts or challenges and how they were resolved.
- Highlight the success of the project and your contribution to it.
What not to say
- Claiming you worked alone without acknowledging team dynamics.
- Focusing solely on individual contributions without mentioning teamwork.
- Avoiding discussion of conflicts or challenges faced within the team.
- Not detailing the project's outcome.
Example answer
“In my vocational training, I was part of a team tasked with designing a new tooling system for a manufacturing line. My responsibility was to create the 3D models using CAD software. I regularly communicated with machinists to ensure my designs were feasible. We faced some disagreements about design specifications, but we held a meeting to discuss everyone's concerns and reached a consensus. The project was completed on time, and our tooling system improved production efficiency by 20%.”
Skills tested
Question type
2. Junior Tool Maker Interview Questions and Answers
2.1. Can you describe a project where you had to use precision tools to create a component?
Introduction
This question assesses your technical skills and hands-on experience with precision tools, which are crucial for a Junior Tool Maker role.
How to answer
- Start by providing context about the project and its objectives
- Detail the specific tools and equipment you used
- Explain the techniques you applied to ensure precision
- Discuss any challenges you faced and how you overcame them
- Highlight the final outcome and its significance to the project
What not to say
- Describing a project with no clear outcome or relevance
- Failing to mention specific tools or techniques used
- Neglecting to discuss challenges or how you solved them
- Giving vague answers without demonstrating your skills
Example answer
“In my previous internship at a manufacturing company, I worked on creating a mold for a plastic component. I used CNC machines and precision measuring tools to ensure exact specifications. Despite initial difficulties with the alignment, I collaborated with my supervisor to adjust the machine settings, which ultimately led to a perfectly fitting mold that improved our production efficiency by 20%.”
Skills tested
Question type
2.2. How do you ensure safety while working with heavy machinery and tools?
Introduction
Safety is paramount in tool making; this question evaluates your understanding of safety protocols and your commitment to maintaining a safe work environment.
How to answer
- Discuss your knowledge of safety regulations and best practices
- Describe specific safety gear and protocols you follow
- Share an example of how you handled a safety concern in the past
- Explain the importance of reporting hazards and maintaining a clean workspace
- Mention any safety training you have received
What not to say
- Ignoring safety protocols or dismissing their importance
- Failing to provide specific examples of safety practices
- Suggesting safety is the sole responsibility of supervisors
- Not mentioning personal responsibility for safety
Example answer
“I prioritize safety by always wearing the required personal protective equipment, such as gloves and goggles, when operating machinery. During my internship, I noticed a coworker not using proper safety gear, and I promptly reported it to our supervisor. Additionally, I participate in regular safety training sessions to stay updated on best practices. Keeping a clean work area is also vital to prevent accidents.”
Skills tested
Question type
3. Tool Maker Interview Questions and Answers
3.1. Can you describe a challenging tool-making project you worked on and how you overcame the obstacles?
Introduction
This question evaluates your problem-solving skills and technical expertise in tool making, which are critical for this role in precision engineering.
How to answer
- Use the STAR method to structure your answer: Situation, Task, Action, Result.
- Clearly outline the project details and the specific challenges faced.
- Discuss the methods or techniques you used to address the challenges.
- Highlight any collaboration with team members or other departments.
- Quantify the results if possible (e.g., improved efficiency, reduced costs).
What not to say
- Giving vague descriptions without specific details about the project.
- Focusing only on the obstacles without mentioning solutions or outcomes.
- Taking sole credit without acknowledging team efforts.
- Ignoring the importance of safety and quality standards.
Example answer
“At Renault, I worked on a project to develop a precision tool for a new engine component. We faced significant challenges with material choice that affected durability. By collaborating with the materials engineering team, we tested several alloys and ultimately found a lightweight solution that improved performance by 15%. This project taught me the importance of cross-departmental communication and innovative problem-solving.”
Skills tested
Question type
3.2. How do you ensure the accuracy and quality of the tools you produce?
Introduction
This question assesses your attention to detail and quality control processes, which are vital for maintaining high standards in tool making.
How to answer
- Discuss your approach to measuring and testing tools during production.
- Explain any quality control systems or standards you adhere to (e.g., ISO standards).
- Mention any tools or technology you use for precision measurement.
- Provide examples of how you handle discrepancies in quality.
- Emphasize the importance of continuous improvement in your work.
What not to say
- Suggesting that quality control is someone else's responsibility.
- Failing to mention specific measurements or standards.
- Downplaying the importance of accuracy in tool making.
- Neglecting to describe how you learn from past mistakes.
Example answer
“I adhere to ISO 9001 quality standards in my work. I utilize precision measuring tools like calipers and micrometers throughout the production process. If a tool doesn't meet specifications, I conduct a thorough analysis to identify the issue and implement corrective actions. At my previous job at Airbus, this rigorous approach helped reduce defect rates by 20% over six months, ensuring high-quality production.”
Skills tested
Question type
4. Senior Tool Maker Interview Questions and Answers
4.1. Can you describe a time when you had to troubleshoot a major issue with a tool you were responsible for?
Introduction
This question is crucial for evaluating your troubleshooting skills and technical expertise, which are vital in the role of a Senior Tool Maker.
How to answer
- Use the STAR method (Situation, Task, Action, Result) to structure your response.
- Clearly describe the issue with the tool and its impact on production.
- Detail the steps you took to identify and analyze the problem.
- Explain the solution you implemented and any adjustments made during the process.
- Quantify the results, such as reduced downtime or improved tool performance.
What not to say
- Avoid blaming others for the issue without taking responsibility.
- Don't focus solely on the technical aspects without discussing problem-solving skills.
- Refrain from providing vague answers without specific details.
- Do not neglect to mention the importance of communication with your team during troubleshooting.
Example answer
“In my role at Toyota, I encountered a significant issue with a milling tool that was causing defects in the parts produced. I initiated a root cause analysis, discovering that wear on the tool's edges was the culprit. I quickly coordinated with my team to replace the tool and implemented a more regular maintenance schedule. As a result, we reduced defect rates by 30% and improved overall production efficiency.”
Skills tested
Question type
4.2. What techniques do you employ to ensure the precision and accuracy of the tools you create?
Introduction
This question assesses your technical knowledge and attention to detail, both of which are essential for a Senior Tool Maker.
How to answer
- Discuss specific measuring tools and technologies you use to ensure precision.
- Explain your process for verifying tool specifications against design requirements.
- Highlight any quality control measures or protocols you follow.
- Share examples of how you've improved precision in your previous work.
- Mention any relevant certifications or training that enhance your skills.
What not to say
- Avoid generic answers that don't specify tools or techniques.
- Don't downplay the importance of precision in tool making.
- Refrain from discussing only past experiences without current practices.
- Neglecting to mention collaboration with quality assurance teams.
Example answer
“I utilize a combination of precision measuring instruments such as calipers and micrometers, along with CNC technology to ensure accuracy in the tools I create. At Honda, I developed a checklist for every tool that included calibration steps and verification against design specs. This process led to a reduction in errors by 25% and enhanced our overall production quality.”
Skills tested
Question type
5. Lead Tool Maker Interview Questions and Answers
5.1. Can you describe a challenging project where you had to design and manufacture a tool from scratch?
Introduction
This question gauges your technical expertise in tool design and your problem-solving skills under challenging circumstances, which are vital for a Lead Tool Maker.
How to answer
- Outline the project requirements and constraints you faced
- Detail your design process and the tools/software used
- Explain the manufacturing techniques you implemented
- Discuss any adjustments made during the project and why
- Quantify the outcome and how it benefited the company
What not to say
- Vaguely describing the project without specific details
- Not mentioning any challenges faced or how you overcame them
- Neglecting to discuss the impact of the tool on operations
- Failing to mention collaboration with other team members
Example answer
“At my previous job with ST Engineering, I was tasked with designing a specialized tool for a new production line. I began with CAD software to prototype the design, ensuring it met all specifications. During the manufacturing phase, we encountered material limitations, which led me to adapt our approach and utilize a different alloy. The final tool improved our production efficiency by 30%, significantly reducing downtime.”
Skills tested
Question type
5.2. How do you ensure quality control in your tool-making process?
Introduction
This question assesses your understanding of quality assurance practices and your commitment to maintaining high standards in tool production.
How to answer
- Describe the quality control measures you implement at different stages of the tool-making process
- Talk about specific tools or technology used for quality assurance
- Explain how you train and involve your team in quality control
- Provide examples of how you've addressed quality issues in the past
- Mention any relevant certifications or standards you adhere to
What not to say
- Claiming quality control is someone else's responsibility
- Not providing any concrete examples
- Overlooking the importance of team involvement in quality assurance
- Suggesting that quality checks are just a formality
Example answer
“In my role at a major manufacturing firm, I implemented a multi-step quality control process that began at the design phase and continued through to final inspection. I utilize tools like CMM (Coordinate Measuring Machines) for precise measurements and involve the entire team in regular quality audits. When we faced a recurring defect in one of our tools, I led a root cause analysis and implemented corrective actions that reduced defects by 25%.”
Skills tested
Question type
6. Tooling Supervisor Interview Questions and Answers
6.1. Can you describe a time when you improved a tooling process to enhance efficiency?
Introduction
This question assesses your analytical skills and ability to implement process improvements, which are crucial in a supervisory role in tooling.
How to answer
- Start with a brief overview of the existing process and its limitations
- Explain the steps you took to analyze the process and identify areas for improvement
- Detail the specific changes you implemented and the rationale behind them
- Quantify the results achieved, such as time saved or cost reductions
- Discuss any challenges faced during implementation and how you overcame them
What not to say
- Providing vague examples without specific metrics or outcomes
- Focusing solely on the process without mentioning your role in the improvement
- Neglecting to address any resistance from team members or stakeholders
- Overlooking the importance of safety or compliance in tooling operations
Example answer
“At Bosch, I identified that our mold changeover times were significantly impacting production schedules. I conducted a thorough analysis and implemented a standardized procedure that included better tool organization and training for the team. As a result, we reduced changeover times by 30%, which significantly improved our overall production efficiency and reduced downtime.”
Skills tested
Question type
6.2. How do you ensure safety and compliance in tooling operations?
Introduction
This question evaluates your understanding of safety protocols and compliance regulations, which are critical for a tooling supervisor.
How to answer
- Discuss your familiarity with relevant safety standards and regulations in the industry
- Explain how you implement safety training and procedures for your team
- Describe your approach to conducting regular safety audits and inspections
- Share an example of how you addressed a safety issue in the past
- Highlight your commitment to fostering a safety-first culture among your team
What not to say
- Ignoring the importance of compliance or safety regulations
- Suggesting that safety measures slow down production without offering solutions
- Failing to mention specific safety training or protocols you've implemented
- Overlooking team involvement in safety initiatives
Example answer
“At Siemens, I implemented a comprehensive safety training program that included hands-on drills and regular safety meetings. We established a safety committee that met monthly to review incidents and ensure compliance with the latest regulations. After addressing a near-miss incident involving improper tool handling, we saw a 50% decrease in safety violations over the next year. This experience reinforced my belief that proactive engagement is key to maintaining a safe work environment.”
Skills tested
Question type
7. Tooling Manager Interview Questions and Answers
7.1. Can you describe a time when you implemented a new tooling process that significantly improved team productivity?
Introduction
This question assesses your ability to identify inefficiencies and implement effective tooling solutions, which is critical for a Tooling Manager role.
How to answer
- Use the STAR method to structure your response (Situation, Task, Action, Result)
- Clearly describe the initial situation and the challenges faced by the team
- Detail the specific tooling process you implemented and the rationale behind it
- Quantify the improvements in productivity or efficiency as a result of your actions
- Discuss any feedback you received from the team and how you continued to iterate on the process
What not to say
- Focusing on the technical details of the tool without discussing its impact
- Failing to provide concrete metrics or results
- Neglecting to mention team involvement or feedback
- Overstating the success without acknowledging any challenges faced during implementation
Example answer
“At a previous company, I noticed our deployment process was causing significant delays. I implemented a CI/CD pipeline that automated testing and deployment, which reduced our release time from two weeks to just three days. The team reported a 40% increase in productivity as they could focus more on development rather than manual processes. The positive feedback from the team motivated me to continually refine the process based on their input.”
Skills tested
Question type
7.2. How do you assess the effectiveness of the tools and technologies used by your team?
Introduction
This question evaluates your analytical skills and understanding of tool evaluation metrics, which are essential for maintaining an efficient tooling environment.
How to answer
- Discuss the criteria you use to evaluate tools (e.g., performance, usability, integration)
- Explain how you gather feedback from users to assess tool effectiveness
- Describe how you analyze the impact of tools on team productivity and project outcomes
- Mention any frameworks or metrics (like KPIs) you use to quantify effectiveness
- Highlight how you stay updated on the latest tools and technologies in the industry
What not to say
- Suggesting that effectiveness assessment is unnecessary or subjective
- Ignoring user feedback or team input in the evaluation process
- Failing to reference specific metrics or KPIs
- Overlooking the importance of continuous improvement in tooling
Example answer
“To assess the effectiveness of tools, I look at user satisfaction surveys, analyze key performance indicators such as task completion time, and gather direct feedback in team meetings. For instance, after implementing a new project management tool, I observed a reduction in project delivery times by 25%, confirmed through both metrics and team feedback. I also regularly review industry trends to ensure our tools remain competitive and effective.”
Skills tested
Question type
Similar Interview Questions and Sample Answers
Land your dream job with Himalayas Plus
Upgrade to unlock Himalayas' premium features and turbocharge your job search.
Himalayas
Himalayas Plus
Trusted by hundreds of job seekers • Easy to cancel • No penalties or fees
Get started for freeNo credit card required
Find your dream job
Sign up now and join over 85,000 remote workers who receive personalized job alerts, curated job matches, and more for free!
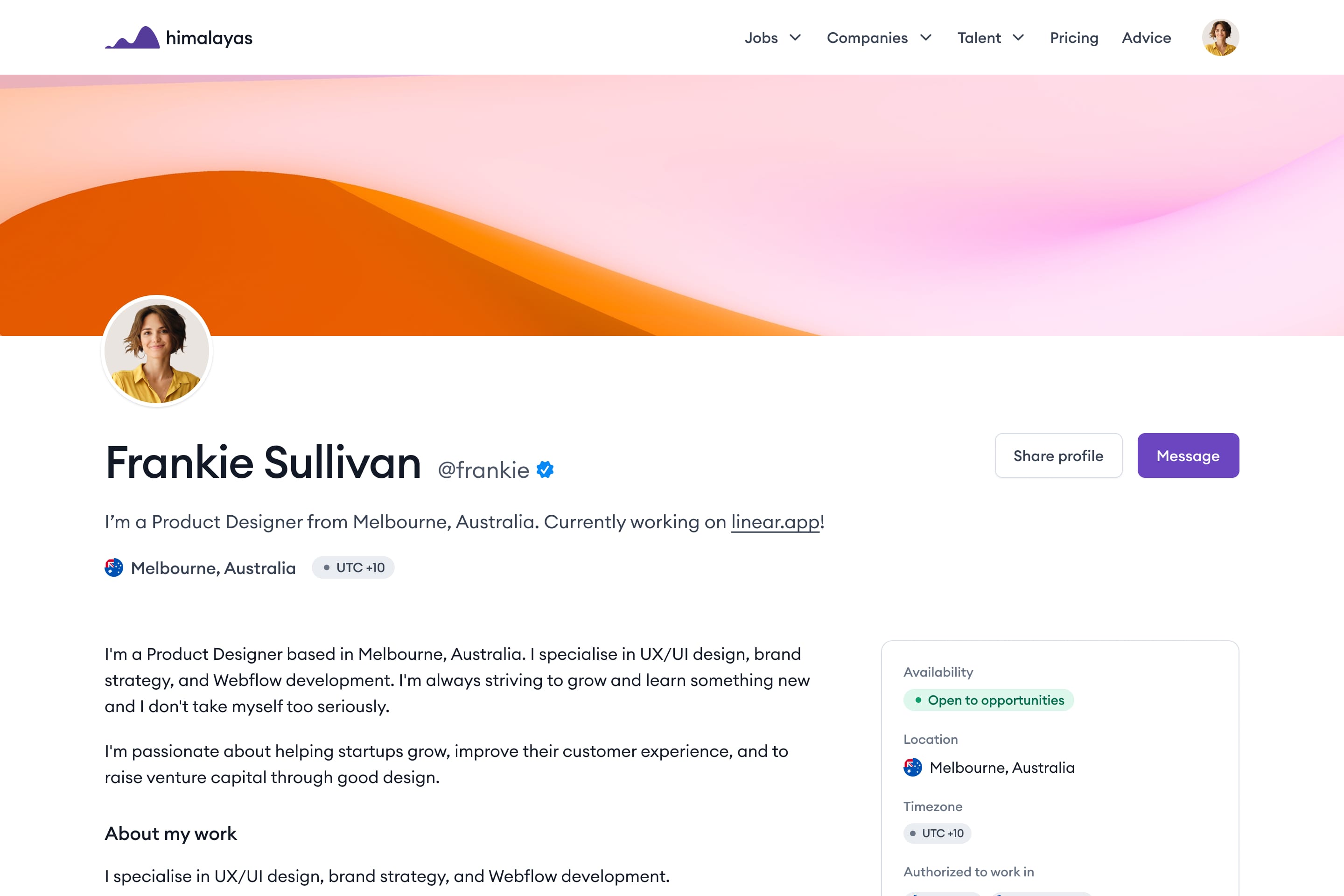