6 Millwright Interview Questions and Answers
Millwrights are skilled tradespeople responsible for installing, maintaining, and repairing industrial machinery and mechanical equipment. They work in various industries, including manufacturing, construction, and energy. At junior levels, millwrights focus on learning the trade and assisting with basic tasks, while senior and lead millwrights take on more complex projects, oversee teams, and ensure machinery operates efficiently and safely. Need to practice for an interview? Try our AI interview practice for free then unlock unlimited access for just $9/month.
Unlimited interview practice for $9 / month
Improve your confidence with an AI mock interviewer.
No credit card required
1. Apprentice Millwright Interview Questions and Answers
1.1. Can you describe a situation where you had to troubleshoot a mechanical issue? What steps did you take?
Introduction
This question is crucial for evaluating your problem-solving skills and hands-on experience, which are essential for an Apprentice Millwright.
How to answer
- Begin by outlining the specific mechanical issue you encountered
- Explain the diagnostic steps you took to identify the problem
- Detail the tools and techniques you used to troubleshoot the issue
- Discuss how you implemented the solution and any challenges faced
- Highlight the outcome and what you learned from the experience
What not to say
- Avoid being vague about the mechanical issue or your role in resolving it
- Don’t focus solely on the tools without explaining their application
- Refrain from taking full credit; mention teamwork if applicable
- Avoid discussing unrelated experiences that don't showcase relevant skills
Example answer
“In my previous role during my training at a manufacturing facility, I faced a problem with a conveyor belt that had stopped functionally due to a misaligned motor. I first inspected the motor and belt alignment, then used a level to check the installation. I re-aligned the motor and adjusted the tension on the belt. After testing the conveyor, it operated smoothly, and I learned the importance of regular maintenance checks to prevent such issues.”
Skills tested
Question type
1.2. How do you prioritize safety in your work as an apprentice millwright?
Introduction
This question assesses your understanding of safety protocols and your commitment to maintaining a safe work environment, which is vital in this role.
How to answer
- Explain the safety protocols and practices you follow
- Share a specific example of when you prioritized safety on the job
- Discuss how you ensure compliance with safety regulations
- Mention any training you have received related to safety
- Describe how you communicate safety concerns to your team
What not to say
- Avoid downplaying the importance of safety in the workplace
- Don’t provide examples where safety protocols were ignored
- Refrain from suggesting that safety is someone else's responsibility
- Avoid being vague about the safety measures you follow
Example answer
“Safety is my top priority as an apprentice millwright. During my training at a local factory, I encountered a situation where a colleague was not wearing the required protective gear while operating machinery. I immediately reminded him of the safety protocol and reported the situation to our supervisor. I also ensure I follow all safety guidelines, such as conducting risk assessments before starting work and using appropriate PPE at all times.”
Skills tested
Question type
1.3. Describe a time when you had to learn a new skill quickly to complete a task. How did you approach it?
Introduction
This question evaluates your adaptability and willingness to learn, which are essential traits for an Apprentice Millwright.
How to answer
- Choose a relevant example where you had to learn a skill on the job
- Explain the context of the task and why the new skill was necessary
- Describe the steps you took to learn the skill, including research or seeking help
- Discuss how you applied the new skill to complete the task successfully
- Reflect on the impact this had on your overall development
What not to say
- Avoid choosing an example that lacks relevance to mechanical work
- Don’t imply that learning was easy or did not require effort
- Refrain from discussing failure without showing what you learned
- Avoid blaming others for not helping you learn the skill
Example answer
“During my apprenticeship at a machining workshop, I was tasked with operating a CNC machine for the first time. Recognizing the urgency, I quickly turned to online resources and asked a seasoned machinist for a brief tutorial. I practiced on a demo machine before working on an actual project. By the end of the day, I successfully completed the task, which taught me the value of proactive learning and seeking guidance when needed.”
Skills tested
Question type
2. Millwright Interview Questions and Answers
2.1. Can you describe a complex mechanical issue you encountered and how you resolved it?
Introduction
This question is essential for assessing your problem-solving skills and technical expertise as a Millwright, which are crucial for maintaining machinery effectively.
How to answer
- Clearly outline the specific mechanical issue you faced
- Explain the steps you took to diagnose the problem
- Describe the solution you implemented and why you chose that approach
- Discuss the outcome and any measurable improvements
- Reflect on what you learned from the experience
What not to say
- Providing vague descriptions without specific details
- Failing to explain your thought process during diagnosis
- Not mentioning collaboration with colleagues if applicable
- Neglecting to mention follow-up measures or maintenance after resolving the issue
Example answer
“At a manufacturing plant, I encountered a recurring issue with a hydraulic press that would intermittently fail. I began by analyzing the hydraulic fluid levels and filters, discovering a clog that was causing pressure loss. After replacing the filters and cleaning the system, the press operated smoothly. This experience taught me the importance of thorough maintenance checks and preventive measures, which reduced downtime by 30%.”
Skills tested
Question type
2.2. How do you prioritize safety while performing maintenance on heavy machinery?
Introduction
Safety is paramount in the role of a Millwright. This question evaluates your commitment to safety protocols and your ability to implement them effectively.
How to answer
- Discuss the safety protocols you follow regularly
- Explain how you ensure a safe working environment before starting maintenance
- Share an example of a safety issue you encountered and how you addressed it
- Mention any relevant certifications or training in safety practices
- Outline how you promote a safety culture among your colleagues
What not to say
- Implying that safety protocols are optional or can be bypassed
- Failing to provide specific examples or experiences
- Not mentioning collaboration with safety officers or teams
- Overlooking the importance of personal protective equipment (PPE)
Example answer
“I prioritize safety by always conducting a thorough risk assessment before starting any maintenance work. For instance, while working on a conveyor system, I noticed a loose cover that could pose a risk. I immediately secured it and informed my supervisor. I also hold a Level 2 Safety Management certification, which has helped me implement best practices on-site. Encouraging my team to report potential hazards has fostered a strong safety culture.”
Skills tested
Question type
2.3. Describe a time you worked under pressure to complete a project on time. How did you manage?
Introduction
This question helps assess your time management and stress-handling abilities, which are critical for a Millwright, especially during breakdowns or urgent repairs.
How to answer
- Use the STAR method to structure your response
- Describe the project and the specific pressure you faced
- Explain the steps you took to ensure timely completion
- Highlight any teamwork or leadership aspects involved
- Discuss the outcome and what you learned from the experience
What not to say
- Focusing solely on the stress without detailing the solution
- Neglecting to mention how you prioritized tasks
- Ignoring the role of teamwork or collaboration
- Failing to discuss the lessons learned from the experience
Example answer
“While working on a critical pump installation, we faced an unexpected delay due to shipping issues. With the deadline approaching, I organized a meeting with the team to prioritize tasks, delegating responsibilities based on each member's strengths. We worked overtime, and I ensured clear communication throughout the process. Ultimately, we completed the project on time, and the experience taught me the importance of teamwork and adaptability under pressure.”
Skills tested
Question type
3. Senior Millwright Interview Questions and Answers
3.1. Can you describe a time when you diagnosed and repaired a complex mechanical issue on machinery?
Introduction
This question evaluates your technical expertise and problem-solving skills, crucial for a Senior Millwright who often tackles complex machinery challenges.
How to answer
- Use the STAR method to clearly outline the situation, task, action, and result
- Describe the specific machinery involved and the nature of the mechanical issue
- Detail the diagnostic steps you took to identify the root cause
- Explain the repair process and any tools or techniques used
- Quantify the impact of your repair work on machine performance and downtime
What not to say
- Giving vague descriptions without technical details
- Claiming success without discussing the challenges faced
- Failing to mention teamwork if applicable
- Not explaining the importance of safety procedures during repairs
Example answer
“At a manufacturing facility in Barcelona, I encountered a recurring issue with a CNC machine where it would intermittently stop. I conducted a thorough diagnosis, discovering a faulty sensor. After replacing it and recalibrating the machine, I improved its efficiency by 30% and reduced downtime significantly. This process reinforced my belief in meticulous diagnostics and proactive maintenance.”
Skills tested
Question type
3.2. How do you prioritize safety while performing maintenance on heavy machinery?
Introduction
This question assesses your commitment to safety standards, which is paramount in the role of a Senior Millwright.
How to answer
- Discuss your understanding of safety regulations and best practices
- Share specific protocols you follow before, during, and after maintenance
- Explain how you ensure that team members adhere to safety measures
- Provide examples of how your safety practices prevented accidents or injuries
- Mention any relevant certifications or training in safety management
What not to say
- Minimizing the importance of safety procedures
- Failing to provide specific examples of safety practices
- Suggesting safety is solely someone else's responsibility
- Not mentioning the impact of safety on operational efficiency
Example answer
“In my previous role at a steel mill, safety was my top priority. Before starting any maintenance work, I conducted risk assessments and ensured that all team members were equipped with the necessary PPE. I implemented a lockout/tagout procedure which prevented accidents during machine servicing. As a result, we maintained a zero-accident record for over a year, demonstrating my commitment to a safe working environment.”
Skills tested
Question type
4. Lead Millwright Interview Questions and Answers
4.1. Can you describe a complex mechanical problem you encountered and how you resolved it?
Introduction
This question assesses your technical problem-solving skills and ability to handle complex machinery, which are crucial for a Lead Millwright.
How to answer
- Use the STAR method to structure your response: Situation, Task, Action, Result.
- Clearly define the mechanical problem and its implications on operations.
- Explain the steps you took to diagnose the problem and identify potential solutions.
- Detail the specific actions you implemented to resolve the issue.
- Quantify the results in terms of efficiency, cost savings, or downtime reduction.
What not to say
- Failing to provide a specific example or using a vague scenario.
- Not mentioning the impact of the problem on the operations.
- Overlooking any teamwork or collaboration aspects involved in the solution.
- Being overly technical without explaining the thought process clearly.
Example answer
“At a manufacturing plant, we faced frequent breakdowns in a critical conveyor system. I led a root cause analysis that revealed misalignment in the drive motors. I organized a team to realign the motors and implement regular maintenance checks. As a result, we reduced downtime by 30% over the next quarter, significantly improving production efficiency.”
Skills tested
Question type
4.2. How do you ensure safety and compliance in your work as a Lead Millwright?
Introduction
Safety is paramount in industrial settings. This question evaluates your commitment to safety practices and compliance regulations.
How to answer
- Discuss your knowledge of relevant health and safety regulations (e.g., OSHA in the U.S., CSA in Canada).
- Explain how you implement safety protocols within your team.
- Share specific training or certifications you have completed.
- Describe how you encourage a culture of safety among team members.
- Provide an example of a safety improvement initiative you led.
What not to say
- Neglecting to mention any specific safety standards or regulations.
- Minimizing the importance of safety in the workplace.
- Providing a generic response without personal involvement in safety initiatives.
- Not mentioning any proactive safety measures or training efforts.
Example answer
“I prioritize safety by conducting regular training sessions on CSA safety standards and ensuring our team is up-to-date on compliance. Last year, I initiated a safety audit that identified hazards in our work area. By addressing these issues, we reduced reportable incidents by 40%, fostering a stronger safety culture among all team members.”
Skills tested
Question type
5. Millwright Supervisor Interview Questions and Answers
5.1. Can you describe a time when you had to troubleshoot a mechanical failure in a plant?
Introduction
This question assesses your problem-solving abilities and technical knowledge, which are crucial for a Millwright Supervisor responsible for equipment maintenance and repair.
How to answer
- Use the STAR method to structure your answer: Situation, Task, Action, Result.
- Describe the specific mechanical failure and its impact on operations.
- Explain the steps you took to diagnose the issue and the rationale behind your approach.
- Detail the repair process and any collaboration with other team members.
- Quantify the results, such as downtime reduced or production restored.
What not to say
- Focusing too much on the technical details without explaining the impact.
- Not mentioning teamwork or collaboration when relevant.
- Failing to describe the outcome or improvements achieved.
- Avoiding discussion of challenges faced during troubleshooting.
Example answer
“At a manufacturing plant in São Paulo, we faced an unexpected shutdown due to a failed gearbox in a critical conveyor system. I quickly assessed the situation, coordinating with my team to isolate the issue. We diagnosed the problem as a lubrication failure, and I led the repair process, ensuring we replaced the damaged parts efficiently. This action restored operations within 4 hours, minimizing downtime and losses significantly. It reinforced my belief in proactive maintenance practices.”
Skills tested
Question type
5.2. How do you ensure safety compliance among your team during maintenance tasks?
Introduction
Safety is paramount in industrial environments, and this question evaluates your commitment to safety protocols and your ability to enforce them.
How to answer
- Discuss your understanding of relevant safety regulations and standards.
- Describe your strategies for training team members on safety practices.
- Explain how you conduct safety audits and inspections.
- Share examples of how you've responded to safety violations in the past.
- Highlight the importance of fostering a safety-first culture.
What not to say
- Implying that safety training is optional.
- Failing to provide concrete examples of safety measures implemented.
- Neglecting to mention the importance of regular safety meetings.
- Overlooking the role of personal responsibility in safety compliance.
Example answer
“In my previous role at a manufacturing facility, I implemented a rigorous training program for new hires focused on safety protocols. I conduct weekly safety briefings and regularly review compliance with OSHA standards. When a team member disregarded safety gear usage, I addressed it immediately by reinforcing the importance of personal safety and held a team meeting to discuss potential risks. This proactive approach resulted in a 30% reduction in safety incidents over the year.”
Skills tested
Question type
6. Maintenance Manager (Millwright Specialization) Interview Questions and Answers
6.1. Can you describe a complex mechanical failure you encountered and how you resolved it?
Introduction
This question assesses your problem-solving skills and technical expertise, which are crucial for a Maintenance Manager specializing in millwright tasks.
How to answer
- Use the STAR method (Situation, Task, Action, Result) to structure your response
- Clearly describe the mechanical failure and its impact on operations
- Detail your diagnostic process and tools you used to identify the root cause
- Explain the steps you took to resolve the issue and the collaboration with your team
- Quantify the results and improvements gained from your solution
What not to say
- Providing vague descriptions without specifics on the failure
- Neglecting to explain your role in the resolution process
- Focusing solely on technical jargon without clarity
- Failing to mention any lessons learned or preventative measures taken
Example answer
“At a manufacturing plant, we faced a critical failure in our hydraulic press that halted production. I led an investigation using vibration analysis tools, discovering a misalignment in the drive coupling. After recalibrating the equipment and replacing worn bearings, we reduced downtime by 30% and implemented a new maintenance schedule that improved reliability. This experience highlighted the importance of proactive diagnostics.”
Skills tested
Question type
6.2. How do you ensure your maintenance team remains compliant with safety regulations?
Introduction
This question evaluates your knowledge of safety standards and your ability to instill a safety culture within your team, which is critical in maintenance roles.
How to answer
- Discuss your understanding of relevant safety regulations in Canada, such as OHSA
- Explain how you conduct regular training sessions and safety drills
- Detail how you encourage open communication about safety concerns
- Describe your methods for monitoring compliance and addressing violations
- Share any successful initiatives you've implemented to improve safety culture
What not to say
- Implying that safety is someone else's responsibility
- Providing generic answers without specific examples
- Neglecting to mention ongoing training or monitoring practices
- Failing to acknowledge the importance of employee feedback
Example answer
“In my previous role at a large manufacturing facility, I ensured compliance with OHSA regulations by conducting monthly safety audits and organizing quarterly training sessions for the team. I introduced a 'safety champion' program where team members could voice concerns and suggest improvements, leading to a 25% reduction in safety incidents over a year. This proactive approach fostered a culture of safety and accountability.”
Skills tested
Question type
Similar Interview Questions and Sample Answers
Simple pricing, powerful features
Upgrade to Himalayas Plus and turbocharge your job search.
Himalayas
Himalayas Plus
Himalayas Max
Find your dream job
Sign up now and join over 100,000 remote workers who receive personalized job alerts, curated job matches, and more for free!
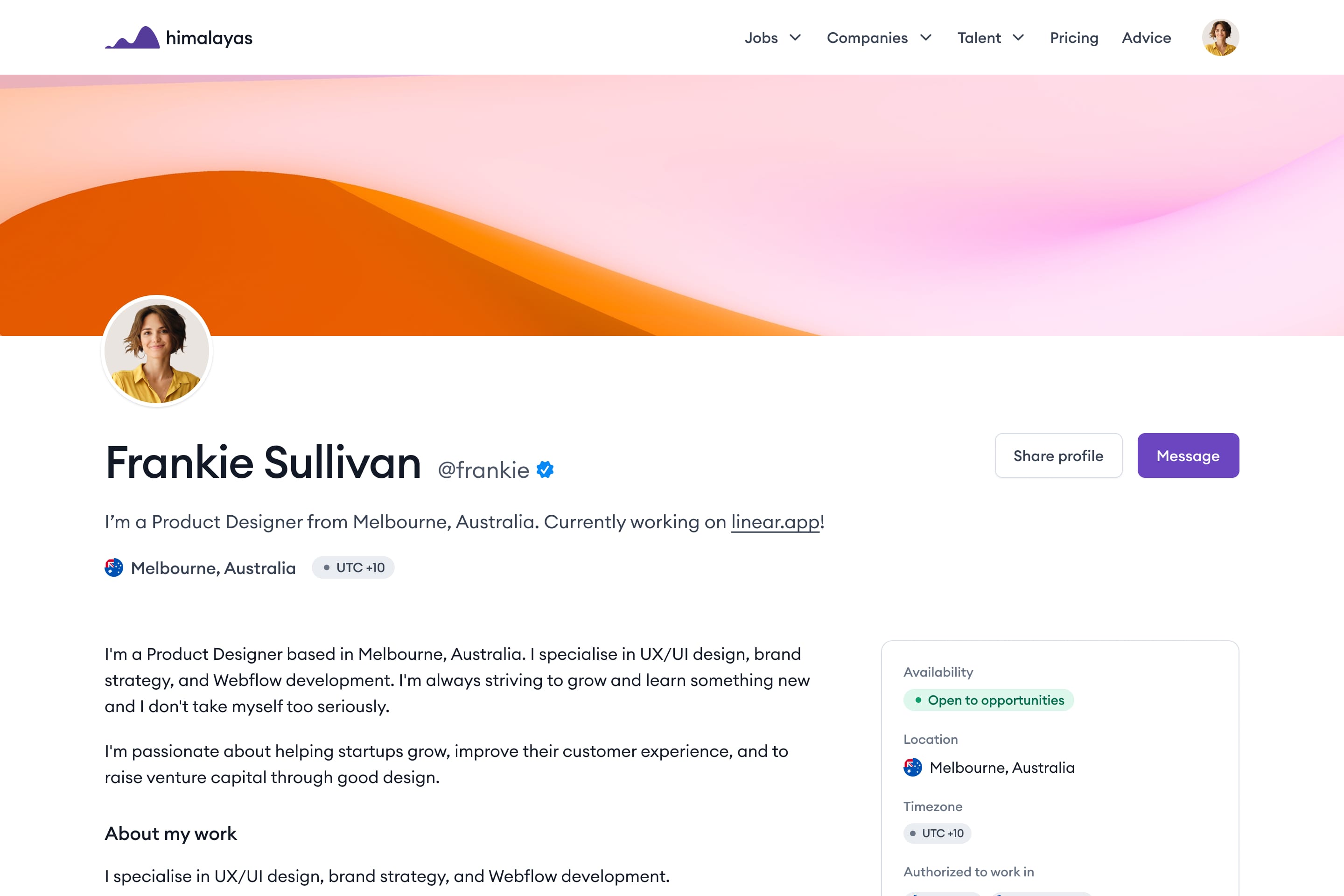