7 Construction Millwright Interview Questions and Answers
Construction Millwrights are skilled tradespeople responsible for installing, maintaining, and repairing industrial machinery and mechanical equipment in construction settings. They work with precision tools to ensure machinery is aligned and functioning properly. Junior or apprentice millwrights focus on learning the trade and assisting with basic tasks, while senior millwrights and supervisors oversee projects, mentor teams, and ensure safety and efficiency on-site. Need to practice for an interview? Try our AI interview practice for free then unlock unlimited access for just $9/month.
Unlimited interview practice for $9 / month
Improve your confidence with an AI mock interviewer.
No credit card required
1. Apprentice Millwright Interview Questions and Answers
1.1. Can you describe a time when you had to troubleshoot a mechanical issue on machinery?
Introduction
This question assesses your problem-solving skills and hands-on experience with mechanical systems, which are crucial for an apprentice millwright.
How to answer
- Start by clearly outlining the machinery involved and the specific issue encountered
- Explain the steps you took to diagnose the problem, including any tools or techniques used
- Discuss how you collaborated with others, if applicable, to resolve the issue
- Quantify the impact of your solution (e.g., reduced downtime, improved efficiency)
- Highlight any lessons learned that will help you in future troubleshooting
What not to say
- Describing a situation where you didn’t take action or sought help immediately
- Failing to mention specific tools or techniques used during troubleshooting
- Not discussing any outcomes or impacts of your resolution
- Providing an overly complicated answer that lacks clarity
Example answer
“During my internship at a manufacturing plant, I encountered a conveyor belt that had stopped working. I first checked the power supply and found a blown fuse. After replacing it, the belt still didn't operate. I then inspected the motor and discovered that it had overheated due to lack of lubrication. After applying the appropriate lubricant and replacing the faulty motor, the conveyor functioned properly again. This experience taught me the importance of thorough inspections and regular maintenance.”
Skills tested
Question type
1.2. What safety procedures do you follow when working with heavy machinery?
Introduction
This question evaluates your understanding of safety protocols, which are critical in preventing accidents and ensuring a safe working environment.
How to answer
- Outline the specific safety procedures you are familiar with, such as using personal protective equipment (PPE)
- Discuss your awareness of risk assessment and hazard identification
- Explain how you ensure compliance with safety regulations and company policies
- Share an example of how you have promoted safety in your previous roles or during training
- Emphasize the importance of communication and teamwork in maintaining a safe workplace
What not to say
- Underestimating the importance of safety procedures
- Providing vague answers without specific examples of safety practices
- Neglecting to mention personal protective equipment (PPE)
- Saying that safety procedures are too time-consuming to follow
Example answer
“I prioritize safety by always wearing the required PPE, such as helmets, gloves, and eye protection when operating machinery. Before starting any task, I conduct a risk assessment to identify potential hazards. During my training at a local engineering firm, I initiated weekly safety briefings to ensure everyone was aware of best practices, which led to a notable reduction in near-misses on site. I firmly believe that safety is a collective responsibility, and clear communication is essential to achieving it.”
Skills tested
Question type
2. Junior Millwright Interview Questions and Answers
2.1. Can you describe a time when you identified a mechanical issue in a machine and how you resolved it?
Introduction
This question assesses your problem-solving skills and technical knowledge, which are critical for a Junior Millwright role, where maintenance and repair of machinery are key responsibilities.
How to answer
- Use the STAR method to structure your response: Situation, Task, Action, Result.
- Clearly describe the specific mechanical issue you encountered.
- Explain how you diagnosed the problem and the steps you took to resolve it.
- Highlight any tools or techniques you used during the repair process.
- Discuss the outcome of your actions and any lessons learned.
What not to say
- Avoid vague descriptions without specific details about the mechanical issue.
- Don't take sole credit; mention teamwork if applicable.
- Refrain from discussing unresolved issues or failures without highlighting what you learned.
- Avoid technical jargon that may not be understood by all interviewers.
Example answer
“At my previous internship with a manufacturing company, I noticed that a conveyor belt was not running smoothly. I inspected the components and found a misalignment in the rollers. I realigned them using a laser level tool, which improved the belt's operation. This action reduced downtime by 20% and taught me the importance of regular maintenance checks.”
Skills tested
Question type
2.2. How do you ensure safety and compliance while performing maintenance tasks?
Introduction
This question evaluates your understanding of safety protocols and regulations, which are crucial in ensuring a safe working environment as a Junior Millwright.
How to answer
- Discuss your familiarity with safety regulations relevant to millwright work.
- Explain specific safety protocols you follow when working with machinery.
- Share examples of safety practices you implemented in previous roles or training.
- Mention the importance of using personal protective equipment (PPE).
- Discuss how you stay updated with safety training and compliance measures.
What not to say
- Avoid saying safety is not a priority for you.
- Don't provide generic responses without specific examples of safety practices.
- Refrain from neglecting the importance of PPE and safety gear.
- Avoid discussing accidents or unsafe practices without a clear learning outcome.
Example answer
“I prioritize safety by adhering to the safety protocols outlined in our training. For instance, during my internship, I ensured that all machinery was properly locked out before starting any maintenance work. I also conducted daily safety checks and used PPE consistently. This not only protected me but also contributed to a safer workplace overall.”
Skills tested
Question type
3. Millwright Interview Questions and Answers
3.1. Can you describe a complex mechanical issue you faced and how you resolved it?
Introduction
This question assesses your technical problem-solving abilities and your experience with mechanical systems, which are crucial for a Millwright's role.
How to answer
- Start with a clear description of the mechanical issue and its context in the workplace.
- Explain the steps you took to diagnose the problem.
- Detail the solution you implemented, including any tools or techniques used.
- Discuss the outcome and any improvements observed after your intervention.
- Reflect on what you learned from the experience and how it impacts your work today.
What not to say
- Vaguely describing the issue without specific details.
- Taking credit for a team effort without recognizing others' contributions.
- Failing to articulate the technical aspects of your solution.
- Not discussing the impact of your solution on operations.
Example answer
“At a manufacturing plant, I encountered a recurring issue with a conveyor system that was causing production delays. After thorough inspection, I identified worn-out bearings as the root cause. I replaced the bearings and realigned the conveyor, which solved the problem. This not only restored production efficiency but also reduced maintenance costs by 20%. I learned the importance of regular inspections to prevent such issues.”
Skills tested
Question type
3.2. How do you ensure safety while performing maintenance on heavy machinery?
Introduction
Safety is critical in a Millwright's role, and this question evaluates your understanding of safety protocols and practices.
How to answer
- Discuss your knowledge of safety regulations and standards relevant to the industry.
- Explain your personal safety procedures and how you prepare for maintenance tasks.
- Mention any training or certifications you have related to workplace safety.
- Provide examples of how you promote safety culture among your colleagues.
- Conclude with how you handle emergencies or unsafe situations.
What not to say
- Underestimating the importance of safety protocols.
- Failing to provide specific safety practices you follow.
- Ignoring the role of teamwork in promoting safety.
- Not mentioning any safety training or certifications.
Example answer
“I always start by reviewing the safety procedures related to the machinery I will be working on. Before any maintenance, I conduct a risk assessment and ensure all safety gear is in place. I have completed OSHA safety training and regularly conduct toolbox talks with my team to reinforce safety practices. In my last role, I implemented a new lockout/tagout procedure that significantly reduced accidents during maintenance tasks.”
Skills tested
Question type
4. Senior Millwright Interview Questions and Answers
4.1. Can you describe a challenging mechanical problem you encountered and how you resolved it?
Introduction
This question assesses your technical problem-solving skills and ability to work under pressure, which are critical for a Senior Millwright.
How to answer
- Start by clearly defining the mechanical problem and its implications on operations.
- Explain the steps you took to analyze the issue, including any diagnostic tools or methods used.
- Detail the solution you implemented, emphasizing your technical knowledge.
- Discuss the outcome, including any improvements in efficiency or reduction in downtime.
- Reflect on what you learned from the experience and how it enhanced your skills.
What not to say
- Avoid vague responses that lack specific details about the problem or solution.
- Don't take sole credit for team efforts; acknowledge contributions from colleagues.
- Steer clear of describing a problem you were unable to solve.
- Refrain from focusing only on the technical aspects without discussing their impact.
Example answer
“At a manufacturing plant, we experienced frequent breakdowns in a critical conveyor system. I conducted a thorough analysis using vibration analysis tools, which indicated misalignment in the drive motor. I realigned the motor and replaced worn components, which reduced downtime by 40%. This experience taught me the importance of thorough diagnostics and proactive maintenance.”
Skills tested
Question type
4.2. How do you approach preventive maintenance to ensure optimal machine performance?
Introduction
This question evaluates your understanding of preventive maintenance strategies and your ability to implement them effectively.
How to answer
- Outline your systematic approach to preventive maintenance planning.
- Discuss the tools and metrics you use to track equipment performance.
- Provide examples of successful preventive maintenance initiatives you led.
- Emphasize the importance of training and communication with your team.
- Mention how you adapt maintenance schedules based on equipment usage and condition.
What not to say
- Avoid suggesting that you solely rely on reactive maintenance.
- Don't provide a generic answer without specific examples.
- Refrain from overlooking the importance of documentation and tracking.
- Avoid discussing preventive maintenance as a one-time effort rather than an ongoing process.
Example answer
“I believe in a proactive approach to preventive maintenance. At a previous job, I implemented a maintenance schedule based on manufacturer's recommendations and usage logs. This included regular inspections and condition monitoring. As a result, we saw a 25% decrease in unexpected breakdowns and improved overall equipment efficiency. Training my team on these practices was crucial to our success.”
Skills tested
Question type
5. Lead Millwright Interview Questions and Answers
5.1. Can you describe a time when you had to troubleshoot a complex mechanical issue in a production setting?
Introduction
This question assesses your problem-solving abilities and hands-on technical skills, which are crucial for a Lead Millwright responsible for maintaining and optimizing machinery.
How to answer
- Begin by outlining the specific mechanical issue you faced and its impact on production.
- Explain the steps you took to diagnose the problem, including any tools or techniques used.
- Describe the solution you implemented and how it improved the situation.
- Quantify the results, such as reduced downtime or increased efficiency.
- Share any lessons learned from the experience that you apply in future troubleshooting.
What not to say
- Avoid vague descriptions without clear details on the issue or solution.
- Don't focus solely on the technical aspects without discussing the impact on production.
- Refrain from taking sole credit; acknowledge any teamwork involved.
- Don’t gloss over the challenges faced during troubleshooting.
Example answer
“At Singapore Technologies Engineering, I encountered a recurring issue with a conveyor system that was causing significant delays in production. I conducted a thorough inspection and discovered a misalignment in the bearings. By recalibrating the system and replacing faulty components, I reduced the downtime by 40%, which allowed us to meet production targets consistently. This experience reinforced my belief in the importance of detailed diagnostics and proactive maintenance.”
Skills tested
Question type
5.2. How do you ensure safety compliance while working on machinery in a team environment?
Introduction
Safety is paramount in industrial settings, and this question evaluates your commitment to safety standards and your ability to lead a team while maintaining those standards.
How to answer
- Discuss your knowledge of safety regulations and best practices relevant to millwright work.
- Explain how you communicate safety protocols to your team.
- Share a specific example of how you implemented safety measures in a previous role.
- Describe how you foster a culture of safety within your team.
- Mention any safety training or certifications you possess that enhance your leadership.
What not to say
- Avoid saying that safety is someone else's responsibility.
- Don’t provide generic answers without specific examples of safety practices.
- Refrain from neglecting the importance of ongoing safety training.
- Do not overlook the role of team engagement in maintaining safety.
Example answer
“In my previous role at Sembcorp Industries, I prioritized safety compliance by conducting regular safety briefings and ensuring all team members were trained in lockout/tagout procedures. During a project to overhaul a hydraulic press, I implemented a checklist for safety inspections that resulted in zero accidents. I believe that a proactive approach to safety not only protects our team but also boosts productivity and morale.”
Skills tested
Question type
6. Millwright Supervisor Interview Questions and Answers
6.1. Can you describe a time when you had to troubleshoot a mechanical failure on-site? What steps did you take to resolve the issue?
Introduction
This question is crucial for assessing your technical expertise and problem-solving abilities, which are vital for a Millwright Supervisor responsible for overseeing maintenance and repair operations.
How to answer
- Start by briefly describing the mechanical failure and its implications for operations.
- Outline the steps you took to diagnose the issue, including tools and techniques used.
- Discuss how you communicated with your team during the troubleshooting process.
- Explain the solution you implemented and any follow-up actions taken to prevent recurrence.
- Share measurable results or improvements post-resolution, if applicable.
What not to say
- Avoid focusing solely on the technical aspects without mentioning teamwork or communication.
- Don’t downplay the significance of the failure or its impact on operations.
- Avoid vague answers that lack specific details or metrics.
- Do not take full credit without acknowledging team contributions.
Example answer
“At Siemens, we faced a critical issue when a conveyor system broke down unexpectedly. I quickly assessed the situation using diagnostic tools to identify a faulty gearbox. I led my team in disassembling the system, which allowed us to replace the part within three hours, minimizing downtime. After the repair, we implemented regular checks that reduced gear failures by 30% over the next year. This experience reinforced the importance of efficient communication and teamwork in resolving mechanical issues.”
Skills tested
Question type
6.2. How do you ensure safety and compliance in your team's operations?
Introduction
Safety is paramount in manufacturing and maintenance environments. This question evaluates your approach to maintaining safety standards and compliance regulations.
How to answer
- Discuss your understanding of relevant safety regulations and standards applicable in Germany.
- Explain the training programs you implement for your team to promote safety awareness.
- Detail how you conduct regular safety audits and inspections.
- Share examples of how you respond to safety incidents and implement improvements.
- Highlight any safety metrics or improvements achieved under your supervision.
What not to say
- Avoid suggesting that safety is the sole responsibility of the safety officer.
- Don’t provide vague statements about safety without specific examples or procedures.
- Avoid downplaying the importance of compliance or suggesting shortcuts.
- Do not ignore the role of continuous improvement in safety practices.
Example answer
“In my role at Bosch, I prioritize safety by conducting monthly training sessions on compliance with the German Occupational Health and Safety Act. I implemented a buddy system for new team members to ensure they receive guidance on safety procedures. After a minor incident last year, I led a thorough investigation and revamped our safety protocols, resulting in a 50% reduction in workplace accidents over six months. My goal is to foster a culture of safety where everyone feels responsible for themselves and their colleagues.”
Skills tested
Question type
7. Millwright Foreman Interview Questions and Answers
7.1. Can you describe a situation where you had to troubleshoot a significant machinery failure on the job site?
Introduction
This question assesses your technical expertise and problem-solving skills, which are critical for a Millwright Foreman responsible for overseeing machinery maintenance and repairs.
How to answer
- Start with a clear description of the machinery involved and the nature of the failure.
- Explain the steps you took to diagnose the problem, including any tools or methods used.
- Detail the collaborative efforts with your team to rectify the issue.
- Share the outcome of your troubleshooting, including any improvements made to prevent future failures.
- Reflect on what you learned from the experience and how it has influenced your approach to maintenance.
What not to say
- Providing vague descriptions without technical details.
- Failing to mention collaboration with team members.
- Not discussing the outcome or impact of your actions.
- Neglecting to highlight preventive measures for the future.
Example answer
“At Toyota, we faced a critical failure in one of our assembly line robots that halted production. I quickly organized a team to analyze the fault codes and discovered a misalignment in the gears. By using precision tools, we recalibrated the machinery within a few hours, and I implemented a new routine check to monitor alignment regularly. This incident taught me the importance of proactive maintenance and teamwork in resolving urgent issues efficiently.”
Skills tested
Question type
7.2. How do you prioritize tasks when managing multiple projects or machinery repairs simultaneously?
Introduction
This question evaluates your organizational skills and ability to manage time effectively, which is essential for ensuring operational efficiency in a millwright role.
How to answer
- Explain your method for assessing the urgency and impact of each task.
- Discuss how you communicate priorities with your team and ensure alignment.
- Detail any tools or software you use to track progress and deadlines.
- Share an example of a time when prioritization led to successful outcomes.
- Mention how you adapt to changes in priorities based on unexpected developments.
What not to say
- Indicating you simply tackle tasks as they come without a clear strategy.
- Neglecting to mention team communication or collaboration.
- Focusing only on personal organization without considering team dynamics.
- Failing to provide a concrete example of effective prioritization.
Example answer
“In my role at Honda, I often managed multiple machinery repairs. I prioritize tasks by assessing their impact on production schedules and safety. I use project management software to assign tasks clearly and keep everyone informed. For instance, when a conveyor malfunctioned, I quickly prioritized that repair over routine maintenance and communicated the urgency to my team. This approach minimized downtime and ensured we met our production targets.”
Skills tested
Question type
Similar Interview Questions and Sample Answers
Simple pricing, powerful features
Upgrade to Himalayas Plus and turbocharge your job search.
Himalayas
Himalayas Plus
Himalayas Max
Find your dream job
Sign up now and join over 100,000 remote workers who receive personalized job alerts, curated job matches, and more for free!
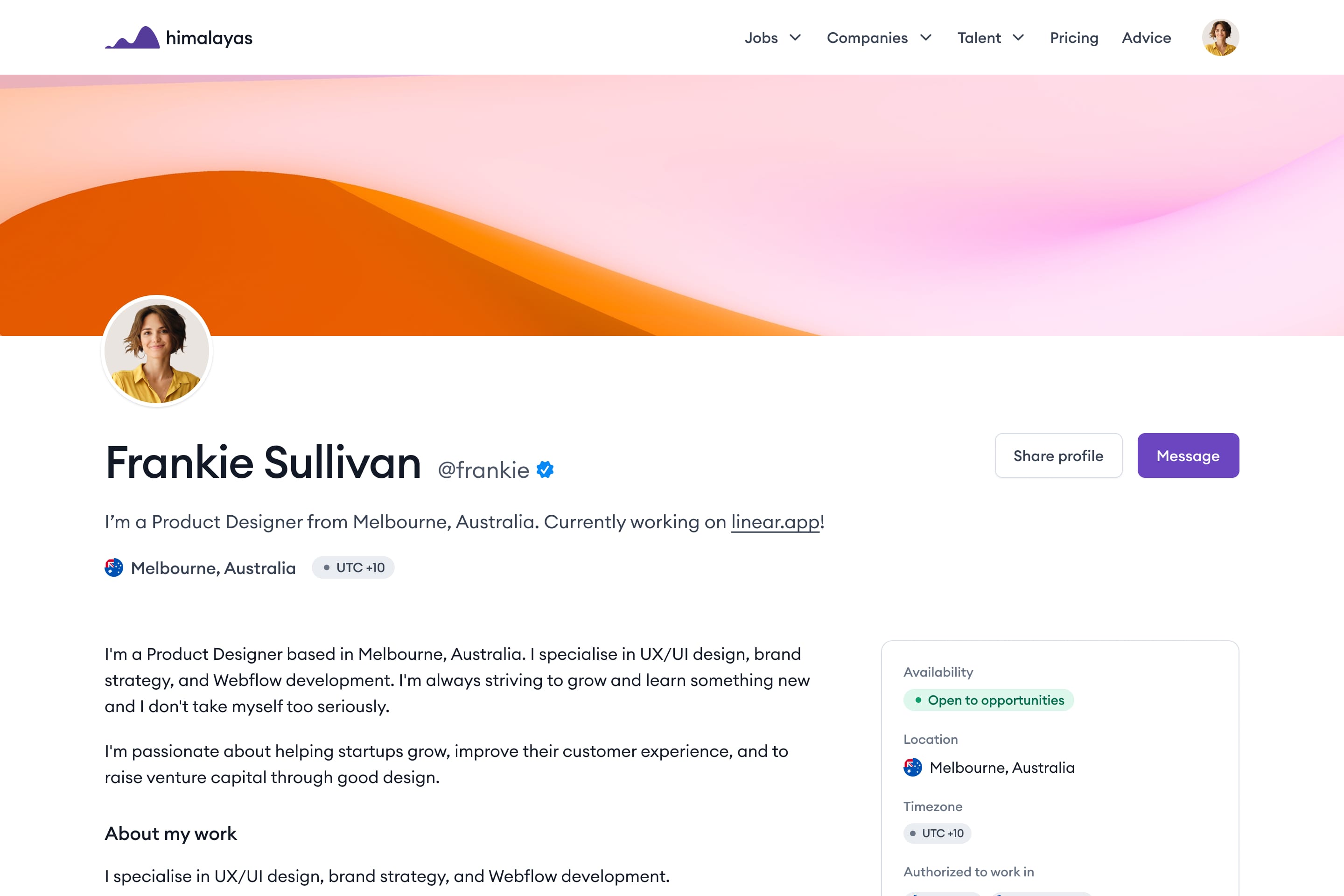