7 Manufacturing Millwright Interview Questions and Answers
Manufacturing Millwrights are skilled tradespeople responsible for installing, maintaining, and repairing industrial machinery and mechanical equipment in manufacturing settings. They ensure machines operate efficiently and safely, often troubleshooting and resolving mechanical issues. Junior or apprentice millwrights focus on learning and assisting with tasks, while senior and lead millwrights take on more complex responsibilities, including supervising teams and managing maintenance schedules. Need to practice for an interview? Try our AI interview practice for free then unlock unlimited access for just $9/month.
Unlimited interview practice for $9 / month
Improve your confidence with an AI mock interviewer.
No credit card required
1. Apprentice Millwright Interview Questions and Answers
1.1. Can you describe a time when you had to troubleshoot a mechanical issue on the job?
Introduction
This question is important for assessing your problem-solving skills and practical experience in handling mechanical issues, which are critical for a millwright.
How to answer
- Use the STAR method to structure your response: Situation, Task, Action, Result.
- Clearly describe the mechanical issue you faced and the context.
- Explain the steps you took to diagnose the problem.
- Detail the solution you implemented and why it was effective.
- Share the outcome and any lessons learned from the experience.
What not to say
- Vague descriptions of the problem without specific details.
- Not demonstrating your thought process in troubleshooting.
- Overlooking the importance of teamwork if applicable.
- Avoiding discussing any mistakes or how you learned from them.
Example answer
“During my apprenticeship at a local manufacturing plant, we faced a recurring issue with a conveyor belt that kept jamming. I first observed the system to identify any visible obstructions. After ruling out simple fixes, I opened the motor housing and found a worn-out bearing causing the malfunction. I replaced the bearing and realigned the belt, which resolved the issue and improved the conveyor's efficiency by 20%. This experience taught me the importance of thorough observation and not overlooking small details.”
Skills tested
Question type
1.2. How do you prioritize safety while working on machinery?
Introduction
Safety is paramount in millwright work. This question assesses your understanding of workplace safety protocols and your commitment to maintaining a safe working environment.
How to answer
- Discuss your knowledge of safety regulations and guidelines relevant to millwright work.
- Describe specific safety practices you follow when operating machinery.
- Share an example of how you identified and mitigated a safety risk.
- Explain how you ensure that others on your team adhere to safety protocols.
- Emphasize the importance of continuous learning and staying updated on safety procedures.
What not to say
- Neglecting to mention any safety protocols or practices.
- Focusing solely on efficiency without discussing safety.
- Underestimating the importance of safety training.
- Providing an example where safety was not prioritized.
Example answer
“In my apprenticeship, I always wore personal protective equipment like gloves and safety goggles when working with machinery. I also conducted a risk assessment before starting any task. For instance, when servicing a lathe, I ensured it was powered off and locked out to prevent accidental start-up. I regularly participated in safety training sessions to stay informed about best practices. This commitment to safety not only protects me but also my coworkers.”
Skills tested
Question type
2. Junior Millwright Interview Questions and Answers
2.1. Can you describe a time when you had to troubleshoot a mechanical issue on the job?
Introduction
This question is important as it assesses your problem-solving skills and ability to work under pressure, which are crucial for a Junior Millwright.
How to answer
- Begin by outlining the specific mechanical issue you encountered.
- Explain the steps you took to diagnose the problem.
- Detail any tools or techniques you used during the troubleshooting process.
- Discuss the outcome and how it impacted your team or project.
- Reflect on what you learned from the experience.
What not to say
- Giving vague descriptions of the issue without specifics.
- Failing to mention the steps taken to troubleshoot.
- Blaming others for the mechanical problem.
- Neglecting to discuss the outcome or lessons learned.
Example answer
“At my previous internship with a manufacturing plant, I encountered a recurring issue with a conveyor belt not operating properly. I systematically checked the alignment and tension of the belt and discovered that a bearing was worn out. After replacing it, the conveyor operated smoothly again, which improved our production efficiency by 15%. This experience taught me the importance of thorough troubleshooting and attention to detail.”
Skills tested
Question type
2.2. How do you prioritize safety while performing maintenance tasks?
Introduction
Safety is paramount in any millwright role, and this question evaluates your awareness and commitment to workplace safety standards.
How to answer
- Discuss your knowledge of safety protocols and regulations.
- Explain how you assess risks before starting a task.
- Detail the personal protective equipment (PPE) you use.
- Share an example of how you ensured safety in a previous role.
- Highlight your willingness to speak up about safety concerns.
What not to say
- Minimizing the importance of safety protocols.
- Failing to mention specific safety measures or equipment.
- Suggesting shortcuts that compromise safety.
- Not providing an example of a safety-conscious approach.
Example answer
“In my training, I learned the importance of adhering to OSHA regulations. Before performing any maintenance, I conduct a risk assessment and ensure I have the necessary PPE, including gloves and safety goggles. During a previous project, I noticed a colleague bypassing a safety guard on a machine. I immediately reported it, and we addressed the issue together, reinforcing our team's commitment to safety. I believe that prioritizing safety not only protects us but also ensures efficient operations.”
Skills tested
Question type
3. Millwright Interview Questions and Answers
3.1. Describe a time when you diagnosed a mechanical failure in a complex piece of machinery.
Introduction
This question assesses your technical expertise and problem-solving skills, crucial for a Millwright role where diagnosing and fixing machinery issues is a daily task.
How to answer
- Start with a brief overview of the machinery and its function
- Describe the symptoms that indicated a mechanical failure
- Explain the diagnostic process you followed, including tools and methods used
- Detail the steps you took to resolve the issue and prevent future occurrences
- Quantify the impact of your work on production or safety
What not to say
- Focusing only on the technical aspects without explaining your thought process
- Failing to mention specific tools or techniques used
- Not discussing the outcome or impact of your diagnosis
- Overlooking the importance of teamwork or communication in the resolution process
Example answer
“At a mining facility, I noticed unusual vibrations in our conveyor system. I conducted a thorough inspection using vibration analysis tools and discovered a misaligned drive shaft. After realigning it and replacing some worn bearings, the vibrations decreased significantly, improving the conveyor's efficiency by 20% and preventing further mechanical failures.”
Skills tested
Question type
3.2. How do you ensure safety while performing maintenance on heavy machinery?
Introduction
This question is essential as safety is paramount in any industrial setting, especially for Millwrights who work closely with heavy equipment.
How to answer
- Discuss your knowledge of safety protocols and standards
- Explain how you assess risks before starting any maintenance task
- Describe the personal protective equipment (PPE) you use
- Highlight your approach to communicating safety procedures with team members
- Provide an example of a time when your safety measures prevented an incident
What not to say
- Minimizing the importance of safety protocols
- Sharing vague practices without specific examples
- Neglecting the importance of team communication regarding safety
- Overlooking the use of PPE or safety equipment
Example answer
“I prioritize safety by conducting a risk assessment before any maintenance task. I always wear appropriate PPE and ensure that all equipment is properly locked out and tagged. Once, while servicing a hydraulic press, my team and I identified a potential hazard and altered our approach, which ultimately prevented a possible injury and kept our work environment safe.”
Skills tested
Question type
4. Senior Millwright Interview Questions and Answers
4.1. Can you describe a complex mechanical problem you encountered and how you resolved it?
Introduction
This question assesses your technical problem-solving skills and your ability to work under pressure, which are crucial for a Senior Millwright.
How to answer
- Start with a clear description of the mechanical issue and its impact on operations.
- Explain the steps you took to diagnose the problem, including any tools or methods used.
- Detail the solution you implemented and any alternative options you considered.
- Quantify the results of your solution, such as reduced downtime or cost savings.
- Reflect on what you learned from the experience and how it improved your skills.
What not to say
- Providing vague descriptions of the problem without specific details.
- Focusing solely on technical aspects without mentioning the impact on operations or teamwork.
- Ignoring the challenges faced during the resolution process.
- Failing to mention safety considerations in your approach.
Example answer
“At a mining facility, we encountered a recurring failure in a conveyor system that was halting production for hours. I performed a thorough inspection and identified misalignment issues. I adjusted the bearings and realigned the system, which not only resolved the immediate issue but also improved efficiency by 20%. This experience taught me the importance of preventive maintenance and regular checks.”
Skills tested
Question type
4.2. How do you ensure safety compliance while performing maintenance tasks?
Introduction
This question is vital to evaluate your safety awareness and adherence to regulations, which are paramount in the millwright profession.
How to answer
- Discuss your understanding of safety regulations and protocols relevant to your work.
- Explain how you integrate safety checks into your daily tasks and maintenance schedules.
- Provide examples of safety training you've undergone or led.
- Describe a specific instance where you identified a safety risk and how you addressed it.
- Highlight the importance of safety culture within the team and how you contribute to it.
What not to say
- Indicating that safety is not a priority in your work.
- Providing a generic answer without specific safety protocols or examples.
- Failing to acknowledge the role of teamwork in maintaining safety standards.
- Neglecting to mention continuous training and adaptation to new safety regulations.
Example answer
“I prioritize safety compliance by always following the OSHA guidelines and conducting pre-task safety assessments. For instance, while working on a high-pressure pump, I noticed worn safety guards that could pose a risk. I halted work, reported it, and ensured the guards were replaced before proceeding. I also regularly conduct safety workshops for the team to reinforce our culture of safety first.”
Skills tested
Question type
5. Lead Millwright Interview Questions and Answers
5.1. Can you describe a complex mechanical issue you've encountered and how you resolved it?
Introduction
This question is crucial for assessing your problem-solving and technical expertise as a Lead Millwright, given the complexities of machinery maintenance and repair.
How to answer
- Begin by outlining the specific mechanical issue and the context in which it occurred.
- Detail the steps you took to diagnose the problem, including any tools or techniques used.
- Explain the solution you implemented and any collaboration with other team members.
- Quantify the outcome, such as improved efficiency or reduced downtime.
- Reflect on what you learned from the experience and how it has influenced your approach to similar issues.
What not to say
- Avoid being vague about the mechanical issue or your role in resolving it.
- Don't focus solely on the technical aspects without discussing the problem-solving process.
- Refrain from taking full credit without acknowledging team efforts.
- Avoid discussing failures without highlighting what you learned.
Example answer
“At a manufacturing plant, we faced repeated failures in a conveyor system that caused significant downtime. I led a thorough analysis using vibration analysis and thermography to identify misalignment in the bearings. After realigning and replacing the worn components, we reduced downtime by 30%. This experience taught me the importance of preventative maintenance and teamwork in troubleshooting.”
Skills tested
Question type
5.2. How do you ensure safety protocols are followed while working on heavy machinery?
Introduction
This question is essential for evaluating your commitment to safety standards in a role that involves significant mechanical work and team leadership.
How to answer
- Discuss your understanding of safety regulations relevant to the millwright trade.
- Explain how you communicate safety protocols to your team.
- Describe any safety training or certifications you have completed.
- Share specific examples of how you have addressed safety violations or near misses.
- Mention any improvements you have implemented to enhance safety practices.
What not to say
- Avoid indicating that safety is not a priority in your work.
- Don't provide vague assurances without specific examples.
- Refrain from blaming others for safety issues instead of focusing on proactive measures.
- Avoid discussing safety only in the context of past incidents without mentioning preventative measures.
Example answer
“Safety is my top priority as a Lead Millwright. I regularly conduct safety briefings before maintenance tasks and ensure all team members are trained in lockout/tagout procedures. When I noticed a colleague not wearing proper PPE while working on a machine, I addressed it immediately and organized a refresher training session. My proactive approach led to a 15% reduction in safety incidents in our department last year.”
Skills tested
Question type
6. Millwright Supervisor Interview Questions and Answers
6.1. Can you describe a time when you had to resolve a conflict between team members on a project?
Introduction
This question is important as it assesses your conflict resolution skills and your ability to maintain a harmonious work environment, which is crucial for a Millwright Supervisor managing a diverse team.
How to answer
- Use the STAR method to structure your response: Situation, Task, Action, Result.
- Clearly outline the conflict, avoiding personal details but focusing on the issue.
- Describe the steps you took to mediate the situation, including communication styles used.
- Discuss the outcome and how it positively impacted team dynamics or project progress.
- Reflect on what you learned from the experience and how it improved your leadership.
What not to say
- Blaming one party without acknowledging your role in the resolution.
- Providing vague or overly simplistic responses without clear actions.
- Avoiding the mention of lessons learned or improvement in future conflicts.
- Failing to show empathy or understanding of team members' perspectives.
Example answer
“In my previous role at Fiat, two of my millwrights had a disagreement over the installation process of a new assembly line. I facilitated a meeting where each could express their concerns. By encouraging open dialogue, we identified a compromise that incorporated both viewpoints. As a result, not only did we complete the installation ahead of schedule, but the team also felt more cohesive and collaborative. This experience taught me the value of active listening and fostering a supportive environment.”
Skills tested
Question type
6.2. How do you ensure the safety and compliance of your team while working on machinery?
Introduction
This question evaluates your understanding of safety protocols and compliance measures, which are critical in the millwright field to prevent accidents and ensure regulatory adherence.
How to answer
- Discuss your knowledge of relevant safety standards and regulations.
- Explain your approach to conducting regular safety training and drills.
- Detail how you assess risks before starting any project and implement safety measures.
- Describe how you encourage a culture of safety among your team members.
- Provide examples of past initiatives you have taken to enhance safety compliance.
What not to say
- Claiming safety is solely the responsibility of the safety officer.
- Ignoring the importance of ongoing training and awareness.
- Focusing only on past incidents without discussing preventive measures.
- Underestimating the role of team involvement in maintaining safety.
Example answer
“At my previous job with CNH Industrial, I implemented a weekly safety briefing to discuss potential hazards associated with our machinery. I also initiated a buddy system where team members would check each other’s equipment before use. This proactive approach led to a 30% reduction in near-miss incidents over six months. Safety isn't just a checkbox for me; it’s an integral part of our daily routine that I take pride in fostering.”
Skills tested
Question type
7. Millwright Manager Interview Questions and Answers
7.1. Can you describe a time when you had to manage a significant machinery failure and how you handled the situation?
Introduction
This question evaluates your technical knowledge and crisis management skills, which are crucial for a Millwright Manager in ensuring the operational efficiency of machinery.
How to answer
- Start with a brief overview of the machinery involved and the nature of the failure
- Explain how you assessed the situation and prioritized actions
- Discuss the steps you took to resolve the issue, including team coordination and resource allocation
- Describe the outcome and any improvements you implemented to prevent future issues
- Mention how you communicated with relevant stakeholders during the crisis
What not to say
- Blaming others for the machinery failure without taking responsibility
- Providing vague details about the situation without clear actions taken
- Neglecting to mention the importance of team collaboration
- Failing to highlight any lessons learned from the incident
Example answer
“At a manufacturing plant in Ontario, we experienced a sudden breakdown of a critical conveyor system. I immediately gathered my team to assess the cause and prioritized restoring functionality. We discovered a misalignment that had caused excessive wear. I coordinated a rapid response, reallocating resources and working overtime to repair the system. The conveyor was back in operation within 24 hours, and I implemented a more rigorous maintenance schedule to prevent future failures. This experience reinforced the importance of proactive maintenance and clear communication.”
Skills tested
Question type
7.2. How do you ensure that your team remains compliant with safety regulations while performing maintenance and repairs?
Introduction
Compliance with safety regulations is critical in millwright operations. This question assesses your understanding of safety protocols and your ability to enforce them among your team.
How to answer
- Discuss your familiarity with safety regulations relevant to millwright work in Canada
- Explain how you communicate these regulations to your team during training and daily operations
- Describe the safety measures you implement to ensure compliance, such as regular audits and checklists
- Share examples of how you have successfully improved safety standards in past roles
- Highlight the importance of fostering a safety-first culture within your team
What not to say
- Suggesting that safety regulations are not a priority
- Failing to provide concrete examples of safety practices
- Overlooking ongoing training and education on safety protocols
- Neglecting to mention the consequences of non-compliance
Example answer
“In my previous role at a manufacturing facility, I ensured our team was well-versed in the latest safety regulations by conducting monthly training sessions and safety drills. I implemented a compliance checklist for all maintenance tasks and conducted regular audits to ensure adherence. After noticing some lapses in safety practices, I created an anonymous feedback system for team members to report concerns, which significantly improved our safety culture. This proactive approach not only kept us compliant but also reduced accidents on the floor by 30%.”
Skills tested
Question type
Similar Interview Questions and Sample Answers
Simple pricing, powerful features
Upgrade to Himalayas Plus and turbocharge your job search.
Himalayas
Himalayas Plus
Himalayas Max
Find your dream job
Sign up now and join over 100,000 remote workers who receive personalized job alerts, curated job matches, and more for free!
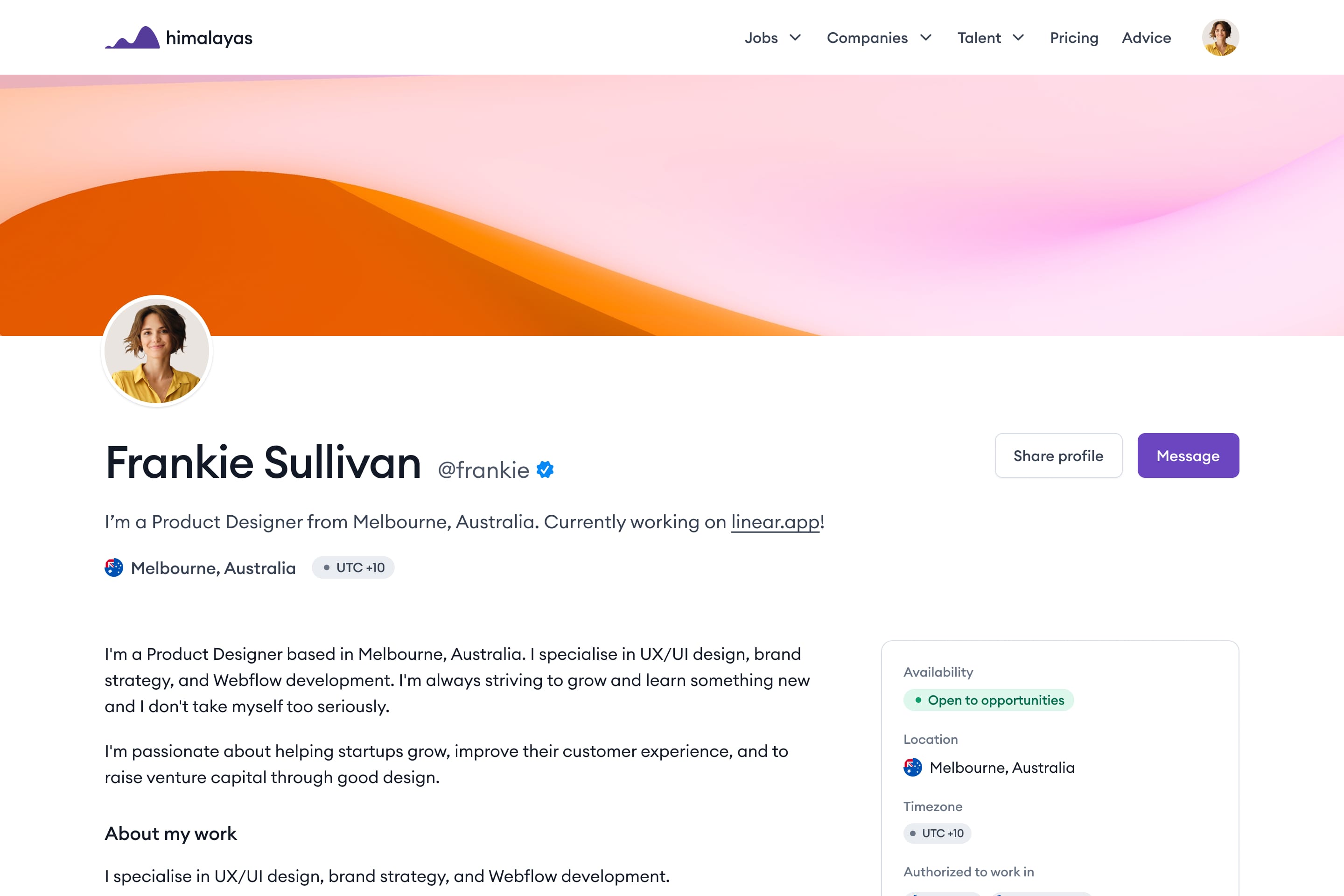