5 Materials Coordinator Interview Questions and Answers
Materials Coordinators are responsible for managing the flow of materials and supplies within an organization, ensuring that production or operational processes run smoothly. They track inventory, coordinate with suppliers, and ensure timely delivery of materials. Junior roles focus on assisting with inventory management and data entry, while senior roles involve overseeing procurement strategies, managing teams, and optimizing supply chain processes. Need to practice for an interview? Try our AI interview practice for free then unlock unlimited access for just $9/month.
Unlimited interview practice for $9 / month
Improve your confidence with an AI mock interviewer.
No credit card required
1. Junior Materials Coordinator Interview Questions and Answers
1.1. Can you describe a time when you had to manage inventory levels to meet production demands?
Introduction
This question assesses your ability to handle inventory management, a critical aspect of the materials coordinator role, ensuring that production runs smoothly without delays.
How to answer
- Use the STAR method to outline your experience: Situation, Task, Action, Result.
- Clearly define the production demand and inventory levels you were working with.
- Discuss the steps you took to monitor and adjust inventory levels.
- Highlight any tools or software you used for inventory management.
- Emphasize the results of your actions, such as improved efficiency or reduced costs.
What not to say
- Failing to provide specific examples or metrics.
- Blaming others for inventory shortages without taking responsibility.
- Neglecting to mention any proactive measures taken.
- Providing vague answers that lack detail.
Example answer
“At my previous internship with Tata Steel, we faced unexpected spikes in production demand. I monitored inventory levels daily and identified that certain materials were running low. I coordinated with suppliers to expedite orders, which ensured we maintained sufficient stock. As a result, we avoided production delays and improved our on-time delivery rate by 15%. This experience taught me the importance of proactive inventory management.”
Skills tested
Question type
1.2. How do you prioritize tasks when managing multiple supply orders?
Introduction
This question evaluates your organizational skills and ability to prioritize tasks effectively, which is essential in a role that involves handling multiple orders and deadlines.
How to answer
- Explain your approach to prioritization, such as using a task matrix or deadline-based sorting.
- Discuss how you evaluate the urgency and importance of each task.
- Provide an example of a time when you successfully managed competing priorities.
- Mention any tools or software you use to keep track of tasks.
- Highlight the outcome of your prioritization strategy, such as timely order fulfillment.
What not to say
- Saying you handle tasks as they come without a clear strategy.
- Neglecting to mention how you communicate with team members about priorities.
- Focusing solely on personal preferences rather than business needs.
- Providing examples that ended poorly without a lesson learned.
Example answer
“In my role at a local manufacturing company, I often managed multiple supply orders simultaneously. I prioritized tasks based on urgency and production schedules using a simple spreadsheet. For example, when a key supplier delayed a critical order, I shifted my focus to expedite alternate suppliers, ensuring we met our production timeline. This approach helped us avoid any downtime, reinforcing the importance of prioritization and adaptability.”
Skills tested
Question type
2. Materials Coordinator Interview Questions and Answers
2.1. Can you describe a time when you successfully managed inventory levels to meet production demands?
Introduction
This question assesses your ability to effectively manage inventory, which is crucial for a Materials Coordinator to ensure that production runs smoothly without delays.
How to answer
- Use the STAR method to structure your answer: Situation, Task, Action, Result
- Clearly describe the situation regarding inventory levels and production needs
- Explain the steps you took to analyze inventory and forecast requirements
- Detail any tools or systems you used to manage inventory effectively
- Quantify the results, such as improvements in production efficiency or cost savings
What not to say
- Providing vague examples without specific details or metrics
- Failing to discuss the impact of your actions on production or costs
- Blaming others for inventory issues rather than taking ownership
- Neglecting to mention collaboration with other departments
Example answer
“At a manufacturing company in Shanghai, I noticed our inventory levels were too low, risking production delays. I implemented a new inventory tracking system that allowed us to forecast needs based on production schedules. As a result, we reduced stockouts by 30% and improved overall production efficiency by 15%. This experience taught me the importance of proactive inventory management.”
Skills tested
Question type
2.2. How do you ensure compliance with safety and quality standards in materials procurement?
Introduction
This question evaluates your knowledge of safety and quality standards, which are vital in managing materials to prevent issues in production and ensure regulatory compliance.
How to answer
- Discuss specific standards relevant to your role, such as ISO or local regulations
- Explain your process for vetting suppliers and their compliance with these standards
- Describe how you monitor and enforce compliance throughout the procurement process
- Share examples of how you have addressed compliance issues in the past
- Emphasize the importance of training and communication with suppliers
What not to say
- Indicating that compliance is not a priority or responsibility
- Providing generic answers without specific examples or standards
- Failing to mention the importance of ongoing monitoring and training
- Overlooking the role of collaboration with quality assurance teams
Example answer
“In my previous role at a chemical manufacturing company, I ensured compliance with ISO 9001 by conducting thorough audits of our suppliers. I developed a checklist to evaluate their quality systems and arranged training sessions for them on our safety standards. This proactive approach led to a 20% reduction in quality-related issues, reinforcing the importance of compliance in our procurement processes.”
Skills tested
Question type
3. Senior Materials Coordinator Interview Questions and Answers
3.1. Can you describe a situation where you had to manage inventory discrepancies? What steps did you take to resolve the issue?
Introduction
This question assesses your problem-solving skills and your ability to maintain accurate inventory levels, which are critical for a Senior Materials Coordinator.
How to answer
- Use the STAR method (Situation, Task, Action, Result) to structure your response.
- Clearly outline the context of the inventory discrepancies you faced.
- Detail the steps you took to investigate the cause of the discrepancies.
- Explain how you collaborated with other departments (like procurement, warehouse, and finance) to resolve the issue.
- Quantify the outcome, such as improvements in accuracy or cost savings.
What not to say
- Blaming others without taking responsibility.
- Providing a vague response without specific actions or results.
- Failing to mention how you communicated the issue to your team.
- Overlooking the importance of preventive measures for future discrepancies.
Example answer
“At a manufacturing company, I discovered a significant inventory discrepancy during a routine audit. I quickly gathered data and identified that a miscommunication with the warehouse team had led to incorrect counts. I organized a cross-department meeting, where we traced the issue back to a new software implementation. Together, we established a more robust communication process and regular audits. As a result, we improved our inventory accuracy by 30% over the next quarter.”
Skills tested
Question type
3.2. How do you prioritize materials sourcing when faced with multiple urgent requests from different departments?
Introduction
This question evaluates your prioritization and decision-making skills, which are essential for coordinating materials effectively across various departments.
How to answer
- Explain your criteria for prioritization (e.g., criticality of the request, impact on production schedules).
- Describe how you gather information from different departments to understand their needs.
- Discuss your approach to communicating prioritization decisions to stakeholders.
- Mention any strategies you use to mitigate conflicts or delays.
- Provide an example of how your prioritization led to successful outcomes.
What not to say
- Claiming you can cater to all requests equally without a prioritization strategy.
- Not mentioning the importance of stakeholder communication.
- Avoiding specifics about how you handle conflicts.
- Focusing solely on one department's needs without considering the bigger picture.
Example answer
“When faced with multiple urgent requests, I prioritize based on the production schedule and the impact on overall operations. I hold brief meetings with department leads to gather insights and assess urgency. For instance, when our production line faced a halt due to material shortages, I prioritized sourcing those materials, communicating transparently with all stakeholders about the rationale behind my decisions. This approach not only minimized downtime but also strengthened inter-departmental relationships.”
Skills tested
Question type
4. Materials Supervisor Interview Questions and Answers
4.1. Can you describe a time when you successfully improved a materials management process?
Introduction
This question assesses your ability to identify inefficiencies and implement improvements, which is crucial for a Materials Supervisor responsible for optimizing supply chain operations.
How to answer
- Use the STAR method to structure your answer (Situation, Task, Action, Result)
- Clearly outline the existing process and its limitations
- Explain the steps you took to analyze and improve the process
- Highlight the tools or methodologies you used for this improvement
- Quantify the results and impacts of your actions on efficiency and cost savings
What not to say
- Vaguely describing a process without concrete improvements
- Focusing solely on the problems without discussing solutions
- Taking credit for team efforts without acknowledging contributions
- Failing to provide measurable outcomes or results
Example answer
“At a manufacturing plant, I noticed our inventory turnover was low due to excess stock levels. I implemented a just-in-time inventory system, analyzed demand patterns, and collaborated with suppliers for timely deliveries. As a result, we reduced inventory holding costs by 20% and improved turnover rates by 30%, which significantly enhanced our cash flow.”
Skills tested
Question type
4.2. How do you handle conflicts with suppliers regarding material quality or delivery issues?
Introduction
This question evaluates your conflict resolution skills and ability to maintain supplier relationships under challenging circumstances, essential for a Materials Supervisor.
How to answer
- Describe your approach to conflict resolution, emphasizing communication and collaboration
- Give a specific example where you faced a quality or delivery issue
- Explain how you engaged with the supplier to address the problem
- Detail the outcomes of your actions and any long-term improvements made
- Highlight the importance of maintaining professional relationships
What not to say
- Avoiding direct communication with suppliers
- Focusing on blame rather than solutions
- Describing a situation where you escalated without trying to resolve it first
- Neglecting to mention follow-up actions to prevent recurrence
Example answer
“When a key supplier delivered subpar material that affected our production schedule, I promptly scheduled a meeting to discuss the issue. I presented the data on the quality discrepancies and worked collaboratively to find a solution. We agreed on stricter quality checks and established a contingency plan for future deliveries. This approach not only resolved the immediate issue but also strengthened our partnership, leading to improved quality and reliability.”
Skills tested
Question type
5. Materials Manager Interview Questions and Answers
5.1. Can you describe a time when you successfully reduced material costs while maintaining quality?
Introduction
This question is crucial for assessing your ability to balance cost management with quality assurance, a key responsibility for a Materials Manager.
How to answer
- Use the STAR method to structure your answer: Situation, Task, Action, Result.
- Clearly articulate the specific materials involved and the context of the cost reduction effort.
- Describe the strategies you implemented to negotiate better prices or find alternatives.
- Emphasize how you ensured that quality standards were not compromised.
- Quantify the results in terms of cost savings and any impact on product quality.
What not to say
- Focusing solely on cost-cutting without discussing quality implications.
- Vague answers without concrete metrics or outcomes.
- Blaming suppliers rather than discussing your active role in the process.
- Neglecting to mention teamwork or collaboration with other departments.
Example answer
“At Ford, I led an initiative to reduce the costs of raw materials by 15%. I negotiated better terms with our suppliers and explored alternative materials that met our quality standards. This not only saved the company $200,000 annually but also maintained the integrity of our assembly line processes, ensuring no disruptions in production.”
Skills tested
Question type
5.2. How do you ensure compliance with industry standards and regulations in your materials management processes?
Introduction
This question evaluates your understanding of regulatory compliance and your ability to implement processes that adhere to industry standards, which is vital in materials management.
How to answer
- Discuss the specific regulations relevant to your industry (e.g., ISO standards, environmental regulations).
- Explain how you keep updated on changes in regulations and standards.
- Detail your methods for training staff on compliance and best practices.
- Share examples of audits or assessments you've conducted to ensure adherence.
- Describe how you mitigate risks associated with non-compliance.
What not to say
- Implying that compliance is not a priority in materials management.
- Providing generic answers without specific regulations or standards.
- Failing to mention processes for ongoing training and updates.
- Neglecting to discuss the consequences of non-compliance.
Example answer
“At General Motors, I implemented a compliance framework that ensured our materials met ISO 9001 standards. I conducted regular training sessions for my team and organized bi-annual audits to assess our adherence. By staying informed on regulatory changes and proactively adjusting our processes, we maintained a 100% compliance rate during my tenure.”
Skills tested
Question type
Similar Interview Questions and Sample Answers
Simple pricing, powerful features
Upgrade to Himalayas Plus and turbocharge your job search.
Himalayas
Himalayas Plus
Himalayas Max
Find your dream job
Sign up now and join over 100,000 remote workers who receive personalized job alerts, curated job matches, and more for free!
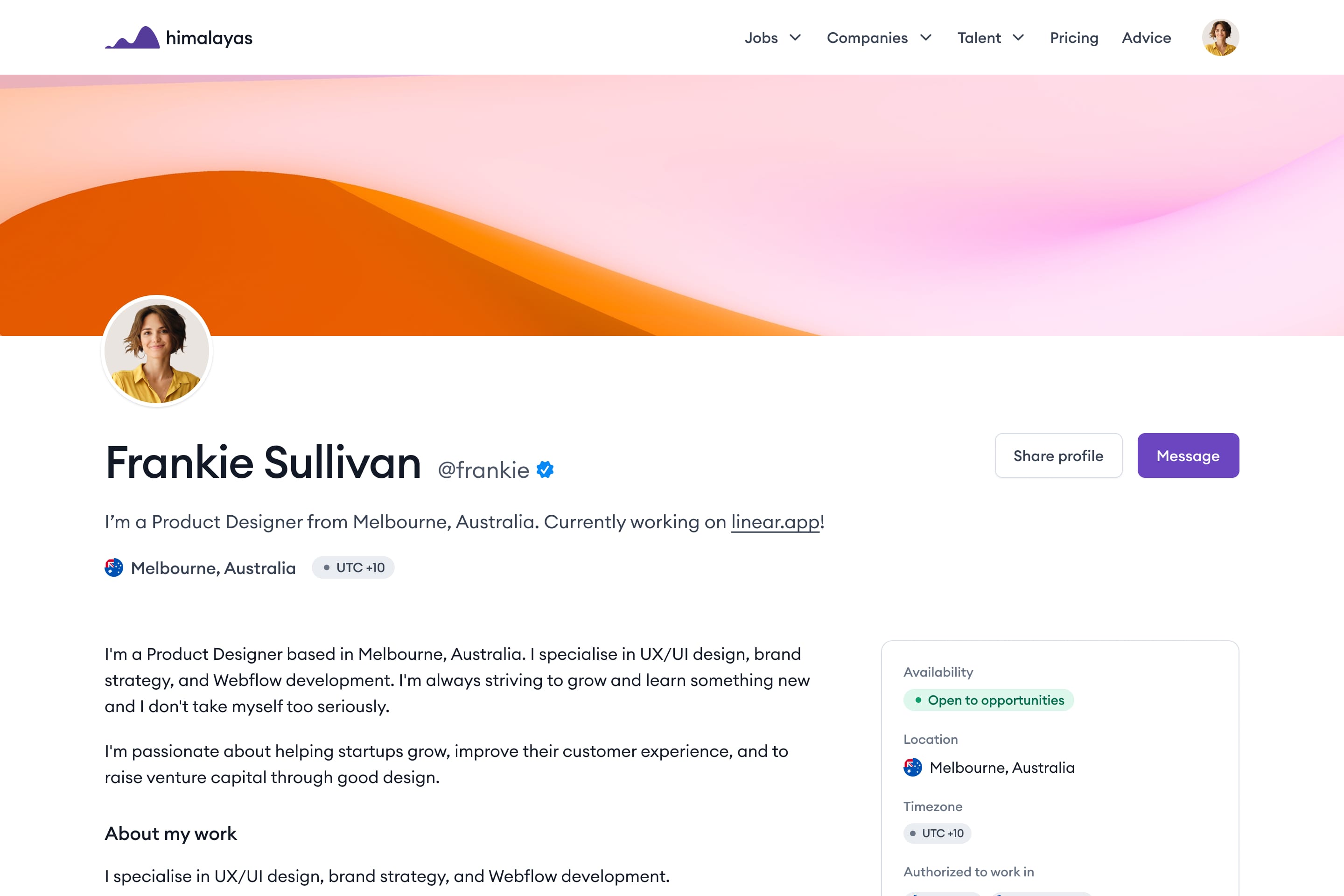