Complete Materials Coordinator Career Guide
Materials Coordinators are the unsung heroes of efficiency, ensuring that the right components are available at the right time to keep production lines moving and projects on schedule. You become the critical link managing inventory, logistics, and supplier relationships, directly impacting a company's operational flow and profitability. This role offers a dynamic challenge, blending supply chain management with hands-on coordination, and it is a vital step for those interested in logistics and operations careers.
Key Facts & Statistics
Median Salary
$48,770 USD
(U.S. national median, BLS May 2023)
Range: $30k - $70k+ USD
Growth Outlook
1%
slower than average (BLS 2022-2032)
Annual Openings
≈44,300
openings annually (growth plus replacements, BLS 2022-2032)
Top Industries
Typical Education
High school diploma or equivalent; some positions prefer an associate's degree in logistics or supply chain management, or relevant certifications.
What is a Materials Coordinator?
A Materials Coordinator is a specialized logistics professional responsible for the efficient flow of materials within an organization. This role ensures that the right materials are available at the right time and place to support production, construction, or operational needs. They act as the central point for managing the entire lifecycle of materials, from procurement to storage and distribution.
Unlike a general Warehouse Manager who focuses broadly on warehouse operations, or a Buyer who primarily handles purchasing, the Materials Coordinator's core function is the precise coordination and management of specific material inventories. They bridge the gap between purchasing, warehousing, and the end-users of materials, ensuring seamless supply chain continuity and minimizing delays or stockouts.
What does a Materials Coordinator do?
Key Responsibilities
- Monitor inventory levels and reconcile discrepancies to ensure accurate stock records.
- Coordinate the receipt, storage, and issuance of materials to support production or project schedules.
- Prepare and process purchase requisitions for new materials, ensuring compliance with procurement policies.
- Communicate with suppliers to track orders, resolve delivery issues, and manage returns.
- Organize and maintain the warehouse or storage area for optimal efficiency and safety.
- Conduct regular physical inventory counts and audits to verify system data.
- Generate reports on material usage, shortages, and delivery performance for management review.
Work Environment
A Materials Coordinator typically works in a dynamic environment that blends office settings with warehouse or production floor activities. They spend time at a desk managing data and communicating, but also move around physically to oversee material handling and storage.
The role involves frequent collaboration with procurement, production, logistics, and sales teams. The pace of work can be fast, especially when managing tight deadlines or unexpected material shortages. While most roles are on-site, some larger organizations might offer hybrid options. Work hours are generally standard business hours, but occasional overtime may be necessary to meet critical deadlines or manage inventory cycles.
Tools & Technologies
Materials Coordinators frequently use Enterprise Resource Planning (ERP) systems like SAP, Oracle, or Microsoft Dynamics 3. Materials Requirement Planning (MRP) modules within these systems are essential for forecasting and planning.
They also rely on inventory management software and warehouse management systems (WMS) to track stock, manage locations, and optimize space. Communication tools such as email, instant messaging, and video conferencing platforms like Microsoft Teams or Zoom facilitate interaction with suppliers and internal teams. Basic office productivity suites, including Microsoft Excel and Word, are crucial for data analysis, reporting, and document creation. Experience with barcode scanners and other data capture devices is also common.
Materials Coordinator Skills & Qualifications
A Materials Coordinator plays a crucial role in the supply chain, ensuring the efficient flow of materials from procurement to production or distribution. This position involves managing inventory, coordinating logistics, and maintaining accurate records of materials. The qualification landscape for this role emphasizes practical experience and a strong understanding of inventory management principles.
Requirements vary significantly by industry. For instance, a manufacturing company needs a Materials Coordinator with knowledge of production schedules and Bill of Materials (BOM), while a construction firm requires expertise in managing diverse building supplies across multiple job sites. Larger companies often prefer candidates with formal education or specialized certifications, whereas smaller businesses might prioritize extensive hands-on experience and proven organizational skills. Seniority levels also dictate the depth of knowledge required; entry-level positions focus on execution, while senior roles involve strategic planning and process improvement.
Formal education, such as a degree in supply chain management or logistics, provides a strong theoretical foundation. However, many successful Materials Coordinators enter the field through vocational training, relevant certifications, or by progressing from warehouse or logistics support roles. Certifications like APICS CSCP or CPIM significantly enhance a candidate's profile, demonstrating a commitment to professional development and a standardized understanding of supply chain best practices. The skill landscape is evolving with the increased adoption of enterprise resource planning (ERP) systems and automation, making proficiency in these technologies increasingly vital. Balancing broad logistical knowledge with deep understanding of specific material types is key for career progression in this field.
Education Requirements
Technical Skills
- Inventory Management Software (e.g., SAP MM, Oracle SCM, Microsoft Dynamics 365, NetSuite)
- Warehouse Management Systems (WMS) operation and data entry
- Proficiency in Microsoft Excel (VLOOKUP, pivot tables, data analysis for inventory reporting)
- Understanding of Bill of Materials (BOM) and Material Requirements Planning (MRP)
- Knowledge of shipping, receiving, and warehousing procedures
- Familiarity with material handling equipment (forklifts, pallet jacks) and safety protocols
- Data entry and record-keeping accuracy for material transactions
- Basic understanding of supply chain principles and logistics operations
- Experience with cycle counting and physical inventory processes
- Vendor and supplier coordination for material delivery schedules
Soft Skills
- Organizational Skills: Essential for managing complex inventory, tracking multiple orders, and maintaining a tidy and efficient warehouse or storage area. This prevents errors and ensures timely material availability.
- Attention to Detail: Critical for accurate record-keeping, identifying discrepancies in shipments, and ensuring the correct materials are issued. Small errors can lead to significant operational delays or cost overruns.
- Problem-Solving: Required to address unexpected issues like material shortages, delivery delays, or damaged goods. This involves quickly finding solutions to minimize disruption to operations.
- Communication: Important for coordinating with suppliers, production teams, logistics partners, and internal departments. Clear and concise communication prevents misunderstandings and ensures smooth material flow.
- Adaptability: Necessary to adjust to changing production schedules, supply chain disruptions, or new material requirements. The ability to pivot quickly is vital in dynamic environments.
- Time Management: Crucial for prioritizing tasks, meeting deadlines for material delivery, and ensuring efficient loading/unloading processes. Poor time management can impact entire production or project timelines.
- Teamwork: Often works closely with warehouse staff, production teams, and purchasing departments. Effective collaboration ensures materials are handled and delivered efficiently across the organization.
How to Become a Materials Coordinator
Breaking into a Materials Coordinator role involves navigating various pathways, from entry-level warehouse positions to supply chain internships. The most direct route often begins with practical experience in inventory management or logistics, even if it is in a junior capacity. While a bachelor's degree in supply chain management or a related field can accelerate progress, many successful Materials Coordinators start with a high school diploma and relevant certifications, demonstrating that formal education is not always a strict prerequisite.
Timeline expectations vary; a complete beginner might spend 6-12 months gaining foundational experience and certifications, while someone transitioning from a related field could secure a role within 3-6 months. Geographic location significantly influences opportunities; major manufacturing or distribution hubs offer more entry points than smaller markets. Companies range from large corporations with structured training programs to smaller businesses where a Materials Coordinator might wear multiple hats, requiring a broader skill set.
A common misconception is that this role is purely physical labor; instead, it demands strong organizational, analytical, and communication skills to manage inventory systems, coordinate with vendors, and optimize material flow. Networking within the supply chain community, attending industry events, and connecting with professionals on platforms like LinkedIn are crucial for discovering unadvertised opportunities and gaining mentorship. Building a strong understanding of Enterprise Resource Planning (ERP) systems like SAP or Oracle, even through online courses, provides a significant advantage in the current hiring landscape.
Step 1
Step 2
Step 3
Step 4
Step 5
Step 6
Education & Training Needed to Become a Materials Coordinator
Becoming a Materials Coordinator primarily involves practical skills and organizational acumen rather than advanced degrees. While some roles may prefer a two-year associate's degree in supply chain management or logistics, many employers value vocational training, certifications, or direct experience more heavily. A typical associate's degree might cost $8,000-$25,000 and take two years, providing foundational knowledge in inventory control, purchasing, and distribution.
Alternative pathways, such as professional certifications or specialized online courses, often prove more cost-effective and time-efficient. These programs can range from $500 to $5,000 and take 6-18 months to complete, focusing on specific software proficiencies, inventory techniques, or safety protocols. Employers generally recognize these credentials as valid indicators of specialized skills. Self-study, combined with hands-on experience in a warehouse or manufacturing setting, can also lead to this role, though it requires significant self-discipline and networking.
Continuous learning is crucial for Materials Coordinators, especially with evolving supply chain technologies and automation. Understanding enterprise resource planning (ERP) systems like SAP or Oracle, along with inventory management software, is highly valued. While formal degrees offer a broad theoretical base, practical experience and targeted certifications often provide a quicker entry point and demonstrate direct applicability to the job's demands. The cost-benefit analysis often favors shorter, specialized training that directly addresses the operational needs of the role.
Materials Coordinator Salary & Outlook
Compensation for a Materials Coordinator varies significantly based on several factors, reflecting the role's critical function in supply chain efficiency. Geographic location plays a major role; areas with high manufacturing, logistics, or construction activity often offer higher salaries due to increased demand and a higher cost of living. Conversely, regions with lower economic activity or a lower cost of living may show more modest compensation.
Years of experience, specific industry knowledge, and the complexity of materials managed directly influence earning potential. Specializations in areas like hazardous materials handling, just-in-time inventory systems, or global logistics can command premium compensation. Total compensation packages frequently extend beyond base salary to include performance bonuses tied to inventory accuracy or cost savings, comprehensive health benefits, and retirement contributions like 401(k) matching. Some companies also offer professional development allowances for certifications in supply chain management.
Industry-specific compensation trends are notable; for instance, the automotive or aerospace sectors may offer more robust packages than retail logistics due to the value and complexity of their materials. Remote work options are less common for this hands-on role, but hybrid models may emerge, potentially impacting local salary norms. When negotiating, highlight your proven ability to reduce waste, optimize inventory turns, or implement efficient materials flow systems. While these figures are USD-based, international markets will reflect local economic conditions and industry structures.
Salary by Experience Level
Level | US Median | US Average |
---|---|---|
Junior Materials Coordinator | $45k USD | $48k USD |
Materials Coordinator | $55k USD | $58k USD |
Senior Materials Coordinator | $68k USD | $70k USD |
Materials Supervisor | $78k USD | $82k USD |
Materials Manager | $100k USD | $105k USD |
Market Commentary
The job market for Materials Coordinators shows stable demand, driven by the ongoing need for efficient supply chain operations across various industries. The U.S. Bureau of Labor Statistics projects a steady outlook for logistics and supply chain roles, reflecting continuous growth in e-commerce, manufacturing, and distribution sectors. As companies focus on cost reduction and operational excellence, the precise management of materials remains a critical function.
Emerging opportunities for Materials Coordinators include roles integrating new technologies such as RFID tracking, automated inventory systems, and predictive analytics for demand forecasting. Professionals who can adapt to these digital tools and contribute to data-driven decision-making will find increased value. The supply and demand dynamics are relatively balanced; there is a consistent need for skilled individuals, but the pool of qualified candidates can be competitive in certain regions.
Future-proofing this role involves continuous learning in supply chain technology and process improvement methodologies. While automation handles routine tasks, the strategic oversight, problem-solving, and vendor relationship management aspects of the Materials Coordinator role remain essential and less susceptible to full automation. This profession tends to be relatively recession-resistant, as businesses always require efficient materials flow. Geographic hotspots include major manufacturing hubs and logistics centers, particularly around port cities and large distribution networks.
Materials Coordinator Career Path
Career progression for a Materials Coordinator typically follows a path focused on increasing responsibility in inventory management, logistics, and supply chain optimization. Professionals advance by mastering precise inventory control, understanding complex supply chain dynamics, and demonstrating strong organizational skills. This field offers both individual contributor (IC) tracks, deepening expertise in materials flow, and management tracks, leading teams and overseeing broader operations.
Advancement speed depends on performance, the complexity of materials handled, and company size. Larger corporations often have more structured progression paths and opportunities for specialization, while smaller companies might offer quicker jumps to broader responsibilities. Lateral movement within the field often involves transitioning to roles like logistics analyst or procurement specialist, broadening one's supply chain expertise.
Continuous learning in inventory software, logistics principles, and safety regulations is crucial. Building a robust network within the supply chain community and seeking mentorship from experienced professionals significantly aids career growth. Certifications in supply chain management (e.g., APICS CSCP or CPIM) also mark significant milestones, enhancing credibility and opening doors to higher-level roles.
Junior Materials Coordinator
0-2 yearsKey Focus Areas
Materials Coordinator
2-4 yearsKey Focus Areas
Senior Materials Coordinator
4-7 yearsKey Focus Areas
Materials Supervisor
7-10 years total experience, 2-3 years in supervisory rolesKey Focus Areas
Materials Manager
10+ years total experience, 3-5 years in management rolesKey Focus Areas
Junior Materials Coordinator
0-2 yearsAssists with receiving, storing, and issuing materials. Performs basic inventory counts and data entry into inventory management systems. Helps organize the warehouse and maintain cleanliness. Works under direct supervision, handling routine tasks with limited decision-making authority.
Key Focus Areas
Develop foundational knowledge of inventory software systems, common materials handling equipment, and basic safety protocols. Focus on accuracy in data entry, understanding stock rotation principles, and effective communication with team members. Seek guidance from senior colleagues to grasp operational nuances.
Materials Coordinator
2-4 yearsManages daily materials movements, including receiving, put-away, picking, and shipping. Conducts regular inventory audits and reconciles discrepancies. Coordinates with internal departments like production and procurement to ensure timely material availability. Operates with moderate autonomy on daily tasks.
Key Focus Areas
Master advanced inventory control techniques, including cycle counting and discrepancy resolution. Develop problem-solving skills for materials flow issues and improve efficiency in receiving and dispatching. Begin to understand the impact of materials management on production schedules.
Senior Materials Coordinator
4-7 yearsOversees a specific section of the warehouse or a critical materials flow process. Identifies and resolves complex inventory issues, implements process improvements, and trains new team members. Collaborates with suppliers and carriers to resolve delivery issues. Provides input on inventory strategy and contributes to operational efficiency.
Key Focus Areas
Cultivate strong analytical skills to identify trends in inventory levels and optimize storage solutions. Develop leadership potential by mentoring junior staff and leading small process improvement initiatives. Gain deeper understanding of supply chain planning and logistics coordination.
Materials Supervisor
7-10 years total experience, 2-3 years in supervisory rolesDirectly supervises a team of Materials Coordinators, overseeing daily operations and ensuring adherence to procedures. Manages staffing, training, and performance reviews for their team. Implements and monitors inventory control procedures to meet operational goals. Reports on key performance indicators for their area of responsibility.
Key Focus Areas
Develop effective team leadership and motivation skills. Focus on performance management, scheduling, and resource allocation for a team of coordinators. Understand and implement lean inventory principles and continuous improvement methodologies. Strengthen cross-functional collaboration with other departments.
Materials Manager
10+ years total experience, 3-5 years in management rolesManages all aspects of materials handling, warehousing, and inventory control for a facility or a significant business unit. Develops and implements materials management strategies, budgets, and policies. Leads continuous improvement initiatives and ensures compliance with safety and regulatory standards. Plays a critical role in optimizing the supply chain and supporting business objectives.
Key Focus Areas
Acquire strategic planning abilities for overall materials flow and warehouse operations. Focus on budget management, vendor relationship management, and long-term capacity planning. Develop strong communication skills for presenting operational insights to senior leadership and driving strategic initiatives.
Job Application Toolkit
Ace your application with our purpose-built resources:
Materials Coordinator Resume Examples
Proven layouts and keywords hiring managers scan for.
View examplesMaterials Coordinator Cover Letter Examples
Personalizable templates that showcase your impact.
View examplesTop Materials Coordinator Interview Questions
Practice with the questions asked most often.
View examplesMaterials Coordinator Job Description Template
Ready-to-use JD for recruiters and hiring teams.
View examplesGlobal Materials Coordinator Opportunities
A Materials Coordinator manages the flow of materials, ensuring timely availability for production or projects worldwide. This role is crucial across diverse sectors like manufacturing, construction, logistics, and energy, with strong global demand.
International opportunities often arise in regions with high industrial activity or large-scale development projects. Regulatory and supply chain differences between countries significantly impact material handling and procurement. Professionals seek international roles for career advancement, exposure to new markets, and higher earning potential in specific regions.
While no single global certification exists, CSCMP's SCPro or APICS CPIM certifications enhance international mobility by demonstrating standardized knowledge.
Global Salaries
Salaries for Materials Coordinators vary significantly by region, industry, and experience. In North America, particularly the United States, a Materials Coordinator earns between $50,000 and $75,000 USD annually. Canada offers similar ranges, from $45,000 to $65,000 CAD ($33,000 to $48,000 USD).
Europe presents a broad spectrum. In Germany, salaries range from €40,000 to €60,000 ($43,000 to $65,000 USD), while in the UK, it is typically £28,000 to £45,000 ($35,000 to $57,000 USD). Eastern European countries generally offer lower compensation, such as €15,000 to €25,000 ($16,000 to $27,000 USD) in Poland.
In Asia-Pacific, salaries can differ greatly. Australia offers $60,000 to $85,000 AUD ($40,000 to $57,000 USD), reflecting a higher cost of living. Singapore typically pays S$40,000 to S$60,000 ($30,000 to $45,000 USD). Latin America, like Brazil, sees ranges from R$40,000 to R$70,000 ($8,000 to $14,000 USD), which offers strong purchasing power locally despite the lower USD equivalent.
Cost of living adjustments are crucial; a lower nominal salary in a country with lower expenses can offer a comparable or even better quality of life. For instance, a salary of $40,000 USD in a major US city might feel less substantial than €30,000 in a smaller European city. International roles often include benefits like housing allowances, relocation packages, or health insurance, which can significantly boost overall compensation. Tax implications also vary; some countries have higher income taxes but offer more comprehensive social benefits. Experience and specialized skills, like hazardous materials handling, often command higher pay globally.
Remote Work
International remote work for a Materials Coordinator is generally limited due to the inherent hands-on nature of the role. This position often requires physical presence for inventory management, receiving, dispatching, and direct interaction with on-site teams or suppliers.
Some aspects, like documentation, planning, and supplier communication, can be done remotely. However, a fully remote international role is uncommon. Hybrid models are more feasible, combining on-site duties with remote administrative tasks. Digital nomad opportunities are rare for this specific job because of the need for direct material interaction. Companies in logistics or supply chain management might offer roles with some remote flexibility for planning or analytical tasks, but not full-time remote international work.
When considering remote work, time zone differences can complicate international team collaboration and urgent material issues. Tax implications for cross-border remote work are complex and depend on individual residency and company setup. Employers typically prefer local hiring for roles requiring physical presence.
Visa & Immigration
Materials Coordinators seeking international opportunities often rely on skilled worker visas. Popular destinations include Canada (Express Entry), Australia (Skilled Nominated or Employer Sponsored), Germany (EU Blue Card), and the UK (Skilled Worker visa). Each country has specific points-based systems or employer sponsorship requirements.
Most countries require a job offer for a work visa. Educational credential recognition is important; many nations assess foreign degrees or diplomas for equivalency. While specific professional licensing is not typically required for this role, industry certifications like those from APICS can strengthen applications. The visa application process usually involves submitting educational and employment history, a valid passport, and sometimes language proficiency tests like IELTS or TOEFL, particularly for English-speaking countries.
Visa processing times vary from a few weeks to several months, depending on the country and visa type. Pathways to permanent residency often exist after several years of continuous skilled employment. Some countries offer dependent visas, allowing spouses and children to accompany the primary applicant. Employers sponsoring visas typically handle much of the paperwork, but individual responsibility for documentation is crucial.
2025 Market Reality for Materials Coordinators
Understanding current market conditions is paramount for Materials Coordinators. The supply chain landscape fundamentally changed from 2023 to 2025, moving from crisis management to optimization. This shift impacts job availability and required skills.
Broader economic factors, such as inflation and interest rates, directly influence manufacturing output and construction projects, which in turn affect the demand for material coordination. Market realities for this role vary significantly by industry, company size, and geographic location, with larger enterprises and specific sectors often having more structured roles. This analysis provides an honest assessment of these dynamics, helping job seekers align their expectations with the real world.
Current Challenges
Materials Coordinators face increased competition, especially as supply chain disruptions ease and companies seek leaner operations. Entry-level roles often see saturation, making differentiation through specific software skills or certifications crucial. Economic uncertainty can lead to reduced inventory levels, potentially slowing hiring for these roles.
The push for automation also means some companies look to reduce manual coordination, shifting demand towards roles with more analytical or system management responsibilities. Job search timelines can extend, requiring persistence.
Growth Opportunities
Despite challenges, strong opportunities exist for Materials Coordinators who embrace technological integration and efficiency. Roles focused on optimizing inventory through advanced analytics, or those with a strong understanding of supply chain software implementation, are in high demand. Companies seek individuals who can not just track, but also forecast and proactively manage material flow to prevent bottlenecks.
Niche industries, such as renewable energy manufacturing, specialized electronics, or medical device production, often present stable and growing opportunities due to their complex material requirements. Professionals who gain certifications in lean manufacturing, Six Sigma, or specific ERP modules (e.g., SAP MM) possess a significant competitive advantage. Experience with automation in warehousing or logistics also elevates a candidate’s profile.
Strategic career moves might involve targeting companies investing heavily in supply chain digitization, where a Materials Coordinator can evolve into a supply chain analyst or system administrator. While core roles remain, the most promising pathways involve skill diversification into data interpretation and system management, enhancing adaptability in a rapidly evolving market.
Current Market Trends
Hiring for Materials Coordinators shows steady demand, but with a clear shift towards efficiency and technological proficiency as of 2025. Companies prioritize candidates who can optimize inventory flow, reduce waste, and leverage digital tools. The post-pandemic surge in supply chain focus has normalized, leading to more measured hiring patterns rather than rapid expansion.
Economic conditions influence material flow, impacting job availability. When manufacturing or construction slows, so does the need for immediate material handling oversight. Conversely, growth in e-commerce and specialized manufacturing maintains a baseline demand.
Technology, particularly advanced ERP systems, inventory management software, and even AI-driven forecasting tools, fundamentally changes the role. Employers now seek coordinators who understand data analytics, can troubleshoot system discrepancies, and adapt to automated warehousing solutions. Basic manual tracking skills are no longer sufficient; proficiency with tools like SAP, Oracle, or specialized WMS platforms is often a prerequisite.
Salary trends for Materials Coordinators remain stable but competitive, with upward mobility tied to specialized skills in areas like lean inventory practices or specific industry knowledge (e.g., aerospace, pharmaceuticals). Market saturation is notable at the entry level, requiring new candidates to highlight relevant internships or project experience. Geographically, demand remains strongest in industrial hubs, logistics corridors, and areas with active manufacturing or construction sectors, though remote opportunities are rare for this hands-on role.
Emerging Specializations
The role of a Materials Coordinator is evolving significantly due to rapid advancements in supply chain technology and global logistics. Emerging specialization opportunities are arising from innovations in automation, data analytics, and sustainability, reshaping how materials are managed and moved. Understanding these shifts and positioning oneself early in these new areas is crucial for career advancement from 2025 onwards.
Specializing in these cutting-edge fields often leads to premium compensation and accelerated career growth. These roles demand unique skill sets that are currently in high demand but short supply. While established specializations remain vital, a strategic balance involves exploring these nascent areas to future-proof one's career.
Many emerging areas, initially niche, are on a trajectory to become mainstream within the next three to five years, generating a substantial number of job opportunities. Early adopters gain a competitive advantage and become subject matter experts as these fields mature. Pursuing cutting-edge specializations involves a calculated risk, yet the potential for high reward in terms of influence and career trajectory is considerable.
Automated Logistics Systems Coordinator
This specialization focuses on integrating advanced automation and robotics into material handling and storage processes. Materials Coordinators in this area manage automated guided vehicles (AGVs), robotic picking systems, and automated storage and retrieval systems (AS/RS). They optimize the flow of materials through highly automated warehouses and distribution centers, ensuring seamless operation and minimal human intervention.
Sustainable Materials Lifecycle Coordinator
This area involves managing the lifecycle of materials with a focus on environmental impact, circular economy principles, and sustainable sourcing. Materials Coordinators specialize in tracking material origins, ensuring compliance with eco-certifications, and optimizing reverse logistics for recycling and reuse. They identify opportunities to reduce waste, minimize carbon footprint, and support a company's broader sustainability goals throughout the supply chain.
Predictive Inventory Analyst
This specialization focuses on leveraging data analytics to predict material demand, optimize inventory levels, and identify supply chain bottlenecks. Materials Coordinators in this role utilize predictive modeling, machine learning algorithms, and business intelligence tools to make data-driven decisions. They transform raw inventory and logistics data into actionable insights, improving efficiency and reducing costs.
Supply Chain Cybersecurity Coordinator
This specialization addresses the secure management of materials and supply chain data against cyber threats and disruptions. Materials Coordinators focus on implementing robust cybersecurity protocols for inventory management systems, tracking devices, and logistics networks. They safeguard sensitive material information, prevent unauthorized access, and ensure the integrity and resilience of the supply chain against digital attacks.
Regulated Materials Compliance Coordinator
This emerging area involves coordinating materials in highly specialized and regulated environments, such as those for pharmaceuticals, aerospace, or advanced electronics. Materials Coordinators ensure strict adherence to industry-specific quality control, traceability, and compliance standards. They manage complex documentation, temperature-sensitive storage, and serialized inventory, guaranteeing materials meet stringent regulatory requirements.
Pros & Cons of Being a Materials Coordinator
Making informed career decisions requires a thorough understanding of both the benefits and challenges associated with a particular field. The experience of a Materials Coordinator can vary significantly based on the employing company's culture, the industry sector (e.g., manufacturing, retail, healthcare), and the specific specialization within logistics. Pros and cons may also shift at different career stages; for instance, entry-level roles might focus on learning foundational tasks, while senior roles involve more strategic planning. What one individual perceives as an advantage, such as a structured work environment, another might view as a disadvantage, like a lack of spontaneity. This assessment provides an honest, balanced perspective to help you set appropriate expectations for a career as a Materials Coordinator.
Pros
- Materials Coordinators are consistently in demand across various industries, including manufacturing, retail, and healthcare, ensuring strong job security and numerous employment opportunities.
- The role provides a clear, hands-on understanding of supply chain operations, inventory management, and logistics, offering valuable foundational experience for broader career growth in the field.
- Many positions offer stable, predictable work schedules, particularly in industries with consistent production cycles, which can contribute to a good work-life balance.
- There is a direct correlation between meticulous work and operational efficiency; successful inventory management directly contributes to cost savings and smooth production, providing a sense of accomplishment.
- The role requires interaction with various internal departments (production, sales, finance) and external suppliers, allowing for diverse professional networking and collaborative problem-solving.
- Entry-level Materials Coordinator positions often require only a high school diploma and some relevant experience, making it an accessible career path for individuals without extensive formal education.
- The job involves practical problem-solving, such as optimizing storage space, troubleshooting delivery issues, or finding alternative suppliers, which keeps the work engaging and intellectually stimulating.
Cons
- The role often involves repetitive tasks such as counting inventory, updating spreadsheets, and organizing storage areas, which can lead to monotony over time.
- Materials Coordinators frequently work in warehouse or manufacturing environments, which can be noisy, dusty, and require standing or walking for extended periods, potentially leading to physical fatigue.
- Dealing with unexpected supply chain disruptions, damaged goods, or incorrect shipments can create high-stress situations requiring quick problem-solving under pressure.
- Career progression can be limited within this specific role, often requiring further education or a shift into broader logistics, purchasing, or supply chain management to advance significantly.
- The job may require working irregular hours, including early mornings, late evenings, or occasional weekends, especially in operations that run 24/7 or during peak production periods.
- Errors in inventory management, such as miscounts or misplacements, can lead to significant financial losses for the company, creating pressure to maintain high accuracy.
- Interaction with various departments and external vendors means constantly managing different personalities and expectations, which can sometimes be challenging or conflict-ridden.
Frequently Asked Questions
Materials Coordinators face distinct challenges in managing inventory, logistics, and supplier relationships to prevent costly delays. This section addresses the most pressing questions about entering this role, from necessary organizational skills to career progression in supply chain management.
What are the essential qualifications or educational backgrounds needed to become a Materials Coordinator?
You typically need a high school diploma or GED, along with strong organizational and basic computer skills. Many employers prefer candidates with an associate's degree in supply chain, logistics, or business administration, or relevant certifications like APICS's CPIM (Certified in Production and Inventory Management) or CSCP (Certified Supply Chain Professional). Prior experience in warehousing, inventory, or shipping roles is highly beneficial.
How long does it typically take to become job-ready as a Materials Coordinator if I'm starting fresh?
Transitioning into a Materials Coordinator role can take 3-12 months. If you have prior experience in a related field like warehousing or logistics, you might find a role quickly. If you are new to the field, obtaining an associate's degree or a relevant certification can take 6 months to 2 years. Building practical experience through entry-level roles like inventory clerk or warehouse associate can significantly shorten your job search time.
What are the typical salary expectations for a Materials Coordinator, especially at entry-level?
Entry-level Materials Coordinators can expect to earn between $35,000 and $50,000 annually, depending on location, industry, and company size. With experience and specialized skills, salaries can rise to $60,000-$75,000 or more. Obtaining certifications and demonstrating strong performance in inventory optimization and cost savings can lead to higher earning potential.
What is the typical work-life balance like for a Materials Coordinator, considering potential overtime or irregular hours?
The work-life balance for a Materials Coordinator can vary. Standard office hours are common, but tight deadlines, inventory counts, or unexpected supply chain issues may occasionally require extended hours. Some roles might involve shift work, especially in manufacturing or distribution centers that operate 24/7. Overall, it is generally a stable role with predictable hours once you master the daily routines.
Is the Materials Coordinator role a secure career, and what is the job market demand like?
The job outlook for Materials Coordinators is stable. As businesses increasingly focus on efficient supply chains, the demand for skilled professionals who can manage inventory and logistics remains consistent. Automation may change some tasks, but the need for human oversight, problem-solving, and supplier relationship management ensures continued relevance for this role. Economic fluctuations can impact specific industries, but overall demand remains strong.
What are the common career advancement paths for a Materials Coordinator?
You can advance from a Materials Coordinator to roles like Senior Materials Coordinator, Inventory Manager, Logistics Manager, or Supply Chain Analyst. Further progression might lead to Supply Chain Manager or Operations Manager positions. Gaining experience with Enterprise Resource Planning (ERP) systems, pursuing advanced certifications, and demonstrating leadership skills are key to upward mobility in this field.
What are the biggest day-to-day challenges or pain points a Materials Coordinator faces?
A common challenge is balancing inventory levels to avoid both stockouts and overstocking, which directly impacts costs and production. You also need to manage complex supplier relationships, handle unexpected delays, and ensure data accuracy within inventory management systems. Effective communication and problem-solving skills are crucial for navigating these daily pressures.
Can a Materials Coordinator realistically work remotely, or is it primarily an on-site position?
Remote work options for Materials Coordinators are limited because the role often requires physical presence in warehouses, production facilities, or distribution centers to manage inventory and oversee shipments. Some administrative or planning aspects might be done remotely, but the core function usually demands on-site work. Hybrid models are rare, but not impossible, depending on the company and specific responsibilities.
Related Careers
Explore similar roles that might align with your interests and skills:
Material Controller
A growing field with similar skill requirements and career progression opportunities.
Explore career guideMaterials Manager
A growing field with similar skill requirements and career progression opportunities.
Explore career guideMaterials Planner
A growing field with similar skill requirements and career progression opportunities.
Explore career guideSupply Coordinator
A growing field with similar skill requirements and career progression opportunities.
Explore career guideMaterial Expediter
A growing field with similar skill requirements and career progression opportunities.
Explore career guideAssess your Materials Coordinator readiness
Understanding where you stand today is the first step toward your career goals. Our Career Coach helps identify skill gaps and create personalized plans.
Skills Gap Analysis
Get a detailed assessment of your current skills versus Materials Coordinator requirements. Our AI Career Coach identifies specific areas for improvement with personalized recommendations.
See your skills gapCareer Readiness Assessment
Evaluate your overall readiness for Materials Coordinator roles with our AI Career Coach. Receive personalized recommendations for education, projects, and experience to boost your competitiveness.
Assess your readinessSimple pricing, powerful features
Upgrade to Himalayas Plus and turbocharge your job search.
Himalayas
Himalayas Plus
Himalayas Max
Find your dream job
Sign up now and join over 100,000 remote workers who receive personalized job alerts, curated job matches, and more for free!
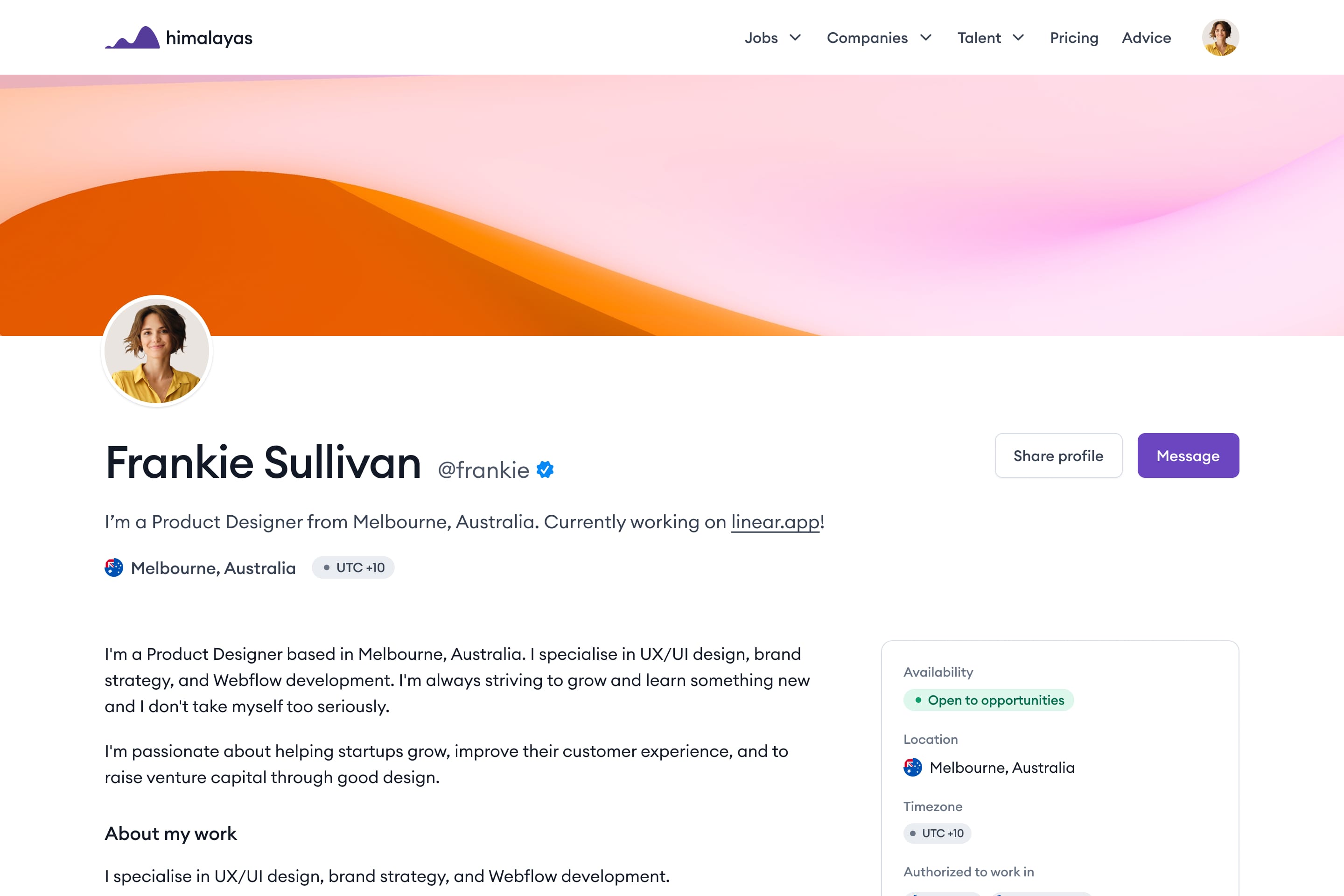