6 Materials Manager Interview Questions and Answers
Materials Managers oversee the procurement, storage, and distribution of materials within an organization to ensure efficient operations. They are responsible for inventory control, supplier relationships, and ensuring materials meet production needs. Junior roles may focus on assisting with inventory tracking and supplier coordination, while senior roles involve strategic planning, team leadership, and optimizing supply chain processes. Need to practice for an interview? Try our AI interview practice for free then unlock unlimited access for just $9/month.
Unlimited interview practice for $9 / month
Improve your confidence with an AI mock interviewer.
No credit card required
1. Assistant Materials Manager Interview Questions and Answers
1.1. Can you describe a time when you had to manage a supply chain disruption? What steps did you take to resolve the issue?
Introduction
This question evaluates your problem-solving skills and your ability to handle unexpected challenges in the supply chain, which is crucial for an Assistant Materials Manager.
How to answer
- Use the STAR method to structure your response: Situation, Task, Action, Result.
- Clearly define the nature of the supply chain disruption and its impact on operations.
- Detail the steps you took to analyze the problem and identify solutions.
- Explain how you communicated with relevant stakeholders throughout the process.
- Share the outcomes of your actions, including any metrics or improvements.
What not to say
- Avoid focusing solely on the problem without discussing your solution.
- Don't blame external suppliers or teams without acknowledging your role.
- Steering clear of vague responses that lack specific details.
- Neglecting to mention how you learned from the experience.
Example answer
“At my previous role with Balfour Beatty, we faced a sudden shortage of a critical raw material due to a supplier's factory closure. I quickly assessed our inventory, prioritized critical projects, and communicated with alternative suppliers. Through negotiation, I secured a temporary supply that kept our project on track without delays. This experience taught me the importance of proactive supplier relationship management and contingency planning.”
Skills tested
Question type
1.2. How do you ensure compliance with health and safety regulations in the materials management process?
Introduction
This question is important as it assesses your understanding of health and safety protocols, which are vital in materials management to ensure workplace safety.
How to answer
- Outline your knowledge of relevant health and safety regulations in the UK.
- Describe your experience in implementing safety protocols in materials handling.
- Explain how you conduct training and awareness programs for the team.
- Discuss monitoring processes to ensure ongoing compliance.
- Share specific instances where your actions improved safety outcomes.
What not to say
- Indicating that compliance is someone else's responsibility.
- Failing to mention specific regulations or safety standards.
- Providing generic responses that lack personal experience.
- Not addressing the importance of a safety culture.
Example answer
“At my last position with Jaguar Land Rover, I implemented a materials handling training program that emphasized compliance with the Health and Safety at Work Act. I regularly conducted safety audits and actively engaged the team in discussions about safety practices. As a result, we achieved a 30% reduction in safety incidents over one year, fostering a culture of safety awareness.”
Skills tested
Question type
2. Materials Manager Interview Questions and Answers
2.1. Can you describe a time when you optimized inventory management to reduce costs?
Introduction
This question evaluates your ability to manage materials efficiently, which is crucial for a Materials Manager to ensure cost-effectiveness and operational efficiency.
How to answer
- Use the STAR method to structure your response: Situation, Task, Action, Result.
- Clearly explain the initial inventory challenges you faced.
- Detail the specific strategies or tools you implemented to optimize inventory.
- Quantify the impact of your actions, such as cost savings or improved turnover rates.
- Discuss any challenges encountered and how you overcame them.
What not to say
- Providing vague answers without specific metrics or results.
- Blaming external factors without showcasing your proactive approach.
- Failing to mention collaboration with other departments.
- Ignoring the importance of continuous improvement in inventory management.
Example answer
“At XYZ Corp, we were facing excess inventory that tied up cash flow. I initiated a review of our inventory management practices and implemented Just-In-Time (JIT) principles. This reduced our holding costs by 30% and improved inventory turnover from 5 to 8 times per year. By collaborating with our suppliers for timely deliveries, we streamlined our operations and enhanced cash flow significantly.”
Skills tested
Question type
2.2. How do you ensure compliance with safety and environmental regulations in materials management?
Introduction
This question assesses your understanding of compliance and your ability to implement practices that adhere to regulatory standards, which is essential in materials management.
How to answer
- Discuss your knowledge of relevant regulations (e.g., OSHA, EPA).
- Explain how you stay updated on changes in regulations.
- Detail your experience in training teams on compliance standards.
- Describe specific initiatives you've implemented to ensure compliance.
- Highlight the importance of fostering a culture of safety within the organization.
What not to say
- Indicating a lack of knowledge about safety regulations.
- Suggesting compliance is solely the responsibility of the safety department.
- Neglecting to mention proactive measures or training.
- Failing to acknowledge the importance of a safety culture.
Example answer
“In my role at ABC Manufacturing, I ensured compliance by conducting quarterly audits to assess adherence to OSHA regulations. I organized training sessions for staff on safe handling and storage of materials. Additionally, I implemented a reporting system for safety incidents. This initiative not only improved our compliance rate but also fostered a culture of safety, resulting in a 40% reduction in workplace accidents over two years.”
Skills tested
Question type
3. Senior Materials Manager Interview Questions and Answers
3.1. Can you describe a time when you optimized the supply chain process to reduce costs?
Introduction
This question is crucial for a Senior Materials Manager as it assesses your ability to identify inefficiencies and implement solutions that directly impact the bottom line.
How to answer
- Use the STAR method (Situation, Task, Action, Result) to structure your response.
- Clearly outline the situation and the specific challenges you faced with the supply chain.
- Detail the specific actions you took to optimize processes, including any innovative strategies or technologies you implemented.
- Quantify the results achieved, such as cost savings or efficiency improvements.
- Highlight any collaboration with cross-functional teams during this process.
What not to say
- Avoid vague descriptions without concrete examples or metrics.
- Neglecting to mention the impact of your actions on the overall supply chain.
- Taking sole credit for team efforts without acknowledging others' contributions.
- Focusing solely on problems without discussing the solutions you implemented.
Example answer
“At BMW, I identified inefficiencies in our supplier selection process that were leading to higher costs. By implementing a new supplier evaluation framework that included performance metrics and cost analysis, we reduced supplier costs by 15% within six months. This optimization not only cut costs but also improved supplier reliability, enhancing our overall supply chain performance.”
Skills tested
Question type
3.2. How do you ensure compliance with industry regulations and standards in materials management?
Introduction
This question evaluates your knowledge of compliance requirements and your ability to implement best practices in materials management, which is essential in the manufacturing sector.
How to answer
- Discuss your understanding of relevant regulations and standards (e.g., ISO, REACH, RoHS).
- Explain your process for staying updated on regulatory changes and how you communicate these to your team.
- Detail specific examples of compliance initiatives you have led or contributed to.
- Highlight any tools or systems you utilize to monitor compliance.
- Discuss how you ensure that suppliers also adhere to these regulations.
What not to say
- Claiming compliance is solely the responsibility of the legal department.
- Providing generic answers without specific examples.
- Indicating a lack of awareness regarding current regulations.
- Failing to mention the importance of training your team on compliance practices.
Example answer
“In my role at Siemens, I led a compliance initiative that involved conducting a comprehensive audit of our materials sourcing practices. I ensured our suppliers met REACH and RoHS standards by implementing a supplier compliance checklist and regular audits. I also organized training sessions for my team to raise awareness about compliance requirements. This proactive approach resulted in zero compliance issues during external audits over the past two years.”
Skills tested
Question type
4. Materials Management Lead Interview Questions and Answers
4.1. Can you describe a time when you successfully reduced material costs in a project without compromising quality?
Introduction
This question is crucial for a Materials Management Lead as it assesses your ability to balance cost efficiency with quality control, which is essential in supply chain management.
How to answer
- Use the STAR method (Situation, Task, Action, Result) to structure your answer
- Clearly describe the situation and the specific challenge you faced regarding material costs
- Explain the actions you took to analyze costs and identify savings opportunities
- Discuss how you engaged with suppliers and stakeholders to implement changes
- Quantify the results in terms of cost savings and any improvements in quality or performance
What not to say
- Focusing solely on cost-cutting without discussing quality considerations
- Failing to mention collaboration with team members or suppliers
- Neglecting to provide specific metrics or results from your actions
- Being vague about the strategies used to achieve cost reductions
Example answer
“At BMW, I led a project to reduce materials costs for a new vehicle line. By analyzing our supplier contracts and negotiating bulk purchase agreements, we achieved a 15% reduction in material costs while maintaining quality standards. This involved collaborating closely with our engineering team to ensure the materials met all specifications. The project not only saved us €1 million but also improved our production timeline.”
Skills tested
Question type
4.2. How do you prioritize and manage multiple suppliers to ensure timely delivery of materials?
Introduction
This question evaluates your organizational and prioritization skills, which are critical for managing supplier relationships in materials management.
How to answer
- Describe your approach to supplier evaluation and selection criteria
- Explain how you assess supplier performance and manage relationships
- Discuss strategies you use to mitigate risks in the supply chain
- Outline how you communicate with suppliers to maintain transparency and expectations
- Provide an example of how you managed a situation with a delayed supplier
What not to say
- Claiming to have a 'one-size-fits-all' approach to supplier management
- Ignoring the importance of building relationships with suppliers
- Failing to mention proactive risk management strategies
- Not addressing how you handle conflicts or issues with suppliers
Example answer
“At Siemens, I used a supplier scorecard system to prioritize and evaluate suppliers based on delivery performance, quality, and cost. I held regular review meetings with key suppliers to maintain open lines of communication. When one supplier faced delays, I quickly assessed alternatives and communicated transparently with our production team, which minimized disruption. This proactive management helped us maintain a 98% on-time delivery rate.”
Skills tested
Question type
5. Director of Materials Management Interview Questions and Answers
5.1. Can you describe a time when you successfully optimized a supply chain process to reduce costs?
Introduction
This question evaluates your ability to identify inefficiencies and implement cost-saving measures, which are crucial for a Director of Materials Management.
How to answer
- Use the STAR method to structure your response: Situation, Task, Action, Result.
- Describe the specific supply chain process you optimized and the initial challenges you faced.
- Detail the steps you took to analyze and improve the process, including any tools or methodologies used.
- Quantify the cost savings or efficiencies gained from your actions.
- Share any lessons learned that could help in future optimization efforts.
What not to say
- Focusing solely on the problem without discussing your solution.
- Providing vague answers without specific metrics or results.
- Claiming success without acknowledging team contributions.
- Failing to show understanding of the supply chain's broader impact on the business.
Example answer
“At General Motors, we faced rising logistics costs due to inefficient routing. I led a team that utilized data analytics to redesign our distribution routes, reducing transportation costs by 25% annually. This experience taught me the importance of data-driven decision-making and cross-department collaboration.”
Skills tested
Question type
5.2. How do you ensure compliance with industry regulations and standards in materials management?
Introduction
This question assesses your knowledge of regulatory compliance and your ability to uphold industry standards, which is critical for maintaining quality and safety in materials management.
How to answer
- Discuss your understanding of relevant regulations and standards in the materials management field.
- Describe the processes you have implemented to ensure compliance, such as audits or training programs.
- Share examples of how you have dealt with compliance issues in the past.
- Explain how you keep your team informed and updated on regulatory changes.
- Highlight the importance of compliance in protecting the company and its reputation.
What not to say
- Suggesting compliance is solely the responsibility of the legal team.
- Underestimating the importance of staying updated on regulations.
- Providing vague responses without concrete examples of compliance efforts.
- Failing to mention proactive strategies for compliance.
Example answer
“At Boeing, I established a comprehensive compliance framework that included regular training sessions and audits to ensure adherence to FAA regulations. When we faced a potential compliance issue, I coordinated with our legal team to address it promptly, resulting in zero violations. This proactive approach not only safeguarded our operations but also fostered a culture of accountability within the team.”
Skills tested
Question type
6. VP of Materials Management Interview Questions and Answers
6.1. Can you describe a time when you successfully reduced material costs while maintaining quality?
Introduction
This question is crucial for understanding your ability to balance cost management with quality assurance, a key responsibility for a VP of Materials Management.
How to answer
- Use the STAR method to structure your response: Situation, Task, Action, Result.
- Start by describing the initial challenge regarding material costs and quality standards.
- Explain the strategies you implemented to negotiate with suppliers or optimize processes.
- Highlight any tools or methodologies you used to analyze and track costs.
- Share the measurable results, such as percentage reductions in costs or improvements in quality metrics.
What not to say
- Focusing solely on cost-cutting without discussing quality implications.
- Neglecting to mention teamwork or collaboration with other departments.
- Providing vague examples without quantifiable outcomes.
- Indicating a lack of awareness about market trends affecting material costs.
Example answer
“At Grupo Bimbo, we faced rising material costs that threatened our profit margins. I led a cross-functional team to negotiate bulk purchasing agreements with key suppliers, which reduced costs by 15%. Simultaneously, we implemented a quality control protocol that ensured our product standards remained high. As a result, we not only saved costs but also improved customer satisfaction scores by 20%.”
Skills tested
Question type
6.2. How do you stay updated with the latest trends in materials management and supply chain logistics?
Introduction
This question evaluates your commitment to continuous learning and industry awareness, which are essential for strategic leadership in materials management.
How to answer
- Mention specific resources you use, such as industry publications, webinars, or professional associations.
- Describe any conferences or workshops you attend to network with peers and learn about innovations.
- Share how you implement new knowledge into your organization’s practices.
- Discuss any mentorship or collaboration with other leaders in the field.
- Explain how staying informed helps you anticipate market changes and adapt strategies.
What not to say
- Claiming you rely solely on past experiences without seeking new information.
- Failing to mention any specific resources or networks.
- Indicating a lack of engagement with the broader industry community.
- Providing outdated examples or irrelevant information.
Example answer
“I am an active member of the Mexican Association of Materials Management and regularly attend their seminars. I also subscribe to Supply Chain Management Review and participate in online forums. Recently, I attended a workshop on sustainable materials, which inspired our shift towards eco-friendly sourcing. This ongoing education ensures our strategies are innovative and aligned with industry best practices.”
Skills tested
Question type
Similar Interview Questions and Sample Answers
Simple pricing, powerful features
Upgrade to Himalayas Plus and turbocharge your job search.
Himalayas
Himalayas Plus
Himalayas Max
Find your dream job
Sign up now and join over 100,000 remote workers who receive personalized job alerts, curated job matches, and more for free!
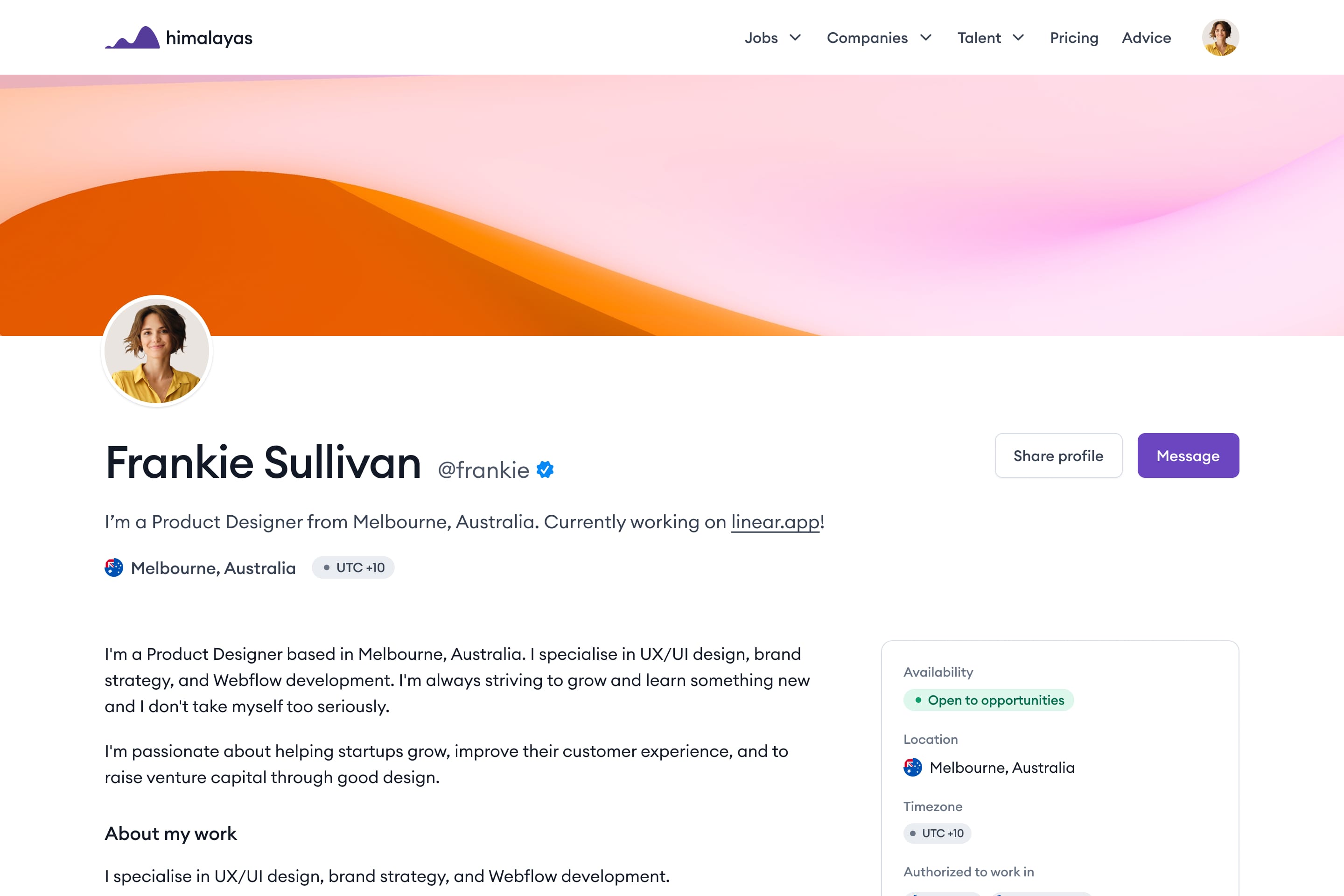