5 Maintenance Supervisor Interview Questions and Answers
Maintenance Supervisors oversee the upkeep and repair of facilities, equipment, and systems to ensure smooth operations. They coordinate maintenance teams, schedule repairs, and ensure compliance with safety standards. Entry-level roles focus on hands-on maintenance tasks, while supervisors and managers take on leadership, planning, and strategic responsibilities to optimize maintenance processes and team performance. Need to practice for an interview? Try our AI interview practice for free then unlock unlimited access for just $9/month.
Unlimited interview practice for $9 / month
Improve your confidence with an AI mock interviewer.
No credit card required
1. Maintenance Technician Interview Questions and Answers
1.1. Can you describe a time when you diagnosed and repaired a complex machinery issue?
Introduction
This question evaluates your technical troubleshooting abilities and hands-on experience, which are critical for a Maintenance Technician.
How to answer
- Use the STAR method to structure your response: Situation, Task, Action, Result.
- Clearly explain the issue you encountered and its impact on operations.
- Detail the steps you took to diagnose the problem, including any tools or techniques used.
- Describe the repair process, emphasizing your technical skills.
- Share the outcome and any improvements made to prevent future issues.
What not to say
- Focusing too much on the technical jargon without explaining in layman's terms.
- Not mentioning the impact of the issue on the workplace.
- Neglecting to discuss teamwork or collaboration if applicable.
- Providing an example without quantifiable results or improvements.
Example answer
“At a manufacturing plant, we experienced unexpected downtime due to a malfunction in a critical conveyor system. I quickly assessed the situation, using our diagnostic tools to identify a faulty sensor. After sourcing a replacement and recalibrating the system, we were back up and running within two hours. This not only minimized our downtime but also improved the sensor's performance, reducing future maintenance needs by 20%.”
Skills tested
Question type
1.2. How do you prioritize your tasks when multiple maintenance issues arise simultaneously?
Introduction
This question assesses your time management and prioritization skills, which are essential in a fast-paced maintenance environment.
How to answer
- Describe your approach to assessing urgency and impact of each issue.
- Discuss how you communicate with team members and supervisors to align on priorities.
- Explain any systems or tools you use to track and manage tasks.
- Share examples of how you've handled conflicting priorities in the past.
- Highlight the importance of safety and compliance in your prioritization.
What not to say
- Suggesting that you handle tasks without a clear prioritization strategy.
- Failing to mention collaboration with colleagues or supervisors.
- Overemphasizing personal workload without considering team dynamics.
- Neglecting the importance of safety or regulatory requirements.
Example answer
“When faced with multiple maintenance requests, I first assess each issue's urgency and impact on operations. For example, if a machine is down and affecting production, I prioritize that over routine checks. I use a digital task management tool to track requests and communicate with my team to ensure alignment on priorities. This structured approach helped us reduce response times to critical issues by 30% in my previous role.”
Skills tested
Question type
2. Senior Maintenance Technician Interview Questions and Answers
2.1. Can you describe a time when you diagnosed and resolved a complex mechanical issue?
Introduction
This question is critical for assessing your technical skills and problem-solving abilities in a maintenance role, especially since complex machinery often requires in-depth knowledge and expertise.
How to answer
- Use the STAR method to structure your response: Situation, Task, Action, Result.
- Clearly describe the mechanical issue, including the equipment involved and its significance to operations.
- Detail the diagnostic steps you took to identify the root cause of the problem.
- Explain the solution you implemented and any tools or techniques used.
- Quantify the impact of your resolution on operational efficiency or safety.
What not to say
- Avoid vague descriptions of the problem without specific details.
- Don't focus solely on the technical details without explaining your thought process.
- Refrain from taking sole credit; acknowledge any teamwork involved.
- Do not gloss over any challenges faced during diagnosis and resolution.
Example answer
“At Boeing, we faced a significant issue with one of our assembly line robots that consistently malfunctioned. I conducted a thorough diagnostic, analyzing error codes and conducting physical inspections, which revealed a misalignment in the mechanical arms. After recalibrating the system, I implemented a preventive maintenance schedule. This reduced downtime by 30% and improved overall production efficiency.”
Skills tested
Question type
2.2. How do you ensure safety standards are maintained during maintenance work?
Introduction
Understanding and upholding safety standards is paramount in maintenance roles to prevent accidents and ensure compliance with regulations. This question assesses your commitment to safety protocols.
How to answer
- Discuss your familiarity with OSHA regulations and company safety policies.
- Explain your process for assessing risks before starting maintenance tasks.
- Detail how you train or communicate safety procedures to your team.
- Provide examples of safety measures you've implemented in previous roles.
- Mention any certifications or training you have related to workplace safety.
What not to say
- Indicating that safety is not a priority in your work.
- Failing to provide specific examples of safety practices.
- Avoiding mention of any previous incidents without analysis.
- Not acknowledging the importance of teamwork in maintaining safety.
Example answer
“At Honeywell, I prioritize safety by strictly adhering to OSHA guidelines and conducting risk assessments before any maintenance work. I lead safety briefings and ensure all team members understand the necessary protocols. For instance, I implemented a lockout/tagout procedure that significantly reduced incidents during equipment servicing, leading to zero safety violations in the past year.”
Skills tested
Question type
2.3. Describe a situation where you had to work under pressure to meet a tight deadline for maintenance tasks.
Introduction
This question evaluates your ability to perform under pressure, a common scenario in maintenance roles where equipment downtime can have significant operational impacts.
How to answer
- Briefly outline the situation that created the pressure, such as a breakdown during peak production.
- Explain the specific tasks you had to complete and the deadline involved.
- Discuss your approach to managing time and resources effectively.
- Highlight any teamwork or collaboration that helped meet the deadline.
- Conclude with the result and any feedback received from management.
What not to say
- Avoid portraying the situation as unmanageable or chaotic.
- Don't neglect to mention your role in the team or the strategies used.
- Refrain from saying you work best under pressure without examples.
- Avoid discussing failures without mentioning lessons learned.
Example answer
“While working at Ford, we experienced an unexpected failure in a critical assembly machine just days before a major production deadline. I quickly coordinated with my team to assess the issue and developed a plan to replace a key component. We worked overtime, ensuring clear communication and task division. Ultimately, we completed the repairs ahead of schedule, allowing production to proceed without delay, which impressed upper management.”
Skills tested
Question type
3. Maintenance Supervisor Interview Questions and Answers
3.1. Can you describe a time when you had to handle a critical equipment failure? How did you manage the situation?
Introduction
This question is crucial for assessing your problem-solving skills and ability to handle high-pressure situations, which are essential for a Maintenance Supervisor.
How to answer
- Use the STAR method to outline the situation clearly
- Describe the nature of the equipment failure and its impact on operations
- Explain the immediate steps you took to address the failure
- Detail how you communicated with your team and other stakeholders during the crisis
- Share the outcomes and any preventive measures you implemented to avoid future occurrences
What not to say
- Focusing solely on the technical aspects without addressing your team management
- Avoiding mention of any mistakes made or lessons learned
- Blaming others for the failure without taking responsibility
- Not providing specific metrics or results that demonstrate your impact
Example answer
“At a manufacturing plant in Lyon, we experienced a critical failure of a main conveyor system that halted production. I quickly assessed the situation and organized an emergency response team. We identified the issue as a faulty motor and managed to replace it within two hours, minimizing downtime to only three hours. I then initiated a review of our maintenance schedule to ensure more regular checks on critical components. This experience taught me the importance of swift action and thorough communication.”
Skills tested
Question type
3.2. How do you prioritize maintenance tasks when faced with limited resources?
Introduction
This question evaluates your ability to manage resources effectively and prioritize tasks in a maintenance environment, which is vital for a Maintenance Supervisor.
How to answer
- Describe your approach to assessing the urgency and importance of maintenance tasks
- Explain any frameworks or tools you use to prioritize tasks
- Detail how you communicate prioritization decisions to your team
- Discuss how you balance immediate needs with long-term maintenance goals
- Mention any past experiences where you successfully managed limited resources
What not to say
- Indicating that all tasks are equally important without justification
- Failing to mention any systematic approach to prioritization
- Ignoring the importance of team input in decision-making
- Suggesting that limited resources are an excuse for poor maintenance
Example answer
“When faced with limited resources, I prioritize tasks by assessing their impact on safety and production. I use a simple matrix to rank tasks based on urgency and importance. For instance, when our cooling system malfunctioned, I prioritized it over routine maintenance tasks because it directly affected production quality. I communicated this to my team, ensuring everyone understood the focus. This approach not only keeps operations running smoothly but also fosters a culture of transparency.”
Skills tested
Question type
4. Maintenance Manager Interview Questions and Answers
4.1. Can you describe a time when you improved the efficiency of a maintenance process?
Introduction
This question assesses your ability to identify areas for improvement and implement effective maintenance strategies, which is crucial for a Maintenance Manager.
How to answer
- Use the STAR method to structure your response: Situation, Task, Action, Result.
- Clearly describe the initial maintenance process and its inefficiencies.
- Detail the specific changes you implemented to improve efficiency.
- Quantify the results, such as reduced downtime or cost savings.
- Reflect on what you learned from the experience and how it can apply to future processes.
What not to say
- Focusing only on the problems without discussing solutions.
- Providing vague examples without measurable impact.
- Neglecting to mention the involvement of team members or collaboration.
- Ignoring the importance of safety and compliance during the process.
Example answer
“At a manufacturing plant, I noticed that our preventive maintenance schedule was leading to excessive downtime. I implemented a new computerized maintenance management system (CMMS) that allowed us to prioritize tasks based on equipment criticality. This change reduced our downtime by 30% over six months and saved the company around €50,000 annually. The experience taught me the importance of data-driven decision making in maintenance operations.”
Skills tested
Question type
4.2. How do you prioritize maintenance tasks in a high-demand environment?
Introduction
This question evaluates your ability to manage multiple priorities and allocate resources effectively, a key skill for a Maintenance Manager.
How to answer
- Explain your prioritization strategy, such as using a risk-based approach.
- Discuss how you assess the urgency and impact of maintenance tasks.
- Provide examples of how you communicate priorities to your team.
- Mention the tools or systems you use to track and manage tasks.
- Highlight your ability to adapt to changing demands or emergencies.
What not to say
- Indicating that all tasks are equally important.
- Failing to mention any frameworks or methods for prioritization.
- Overlooking the importance of team communication in prioritizing tasks.
- Suggesting a lack of organization in managing maintenance requests.
Example answer
“In my previous role at a logistics company, I prioritized maintenance tasks using a risk assessment matrix. I categorized tasks based on their potential impact on operations and safety. For instance, if a conveyor system was malfunctioning, I would quickly assess its effect on shipping timelines and allocate resources accordingly. This method ensured that critical systems were maintained promptly while keeping the workflow smooth and efficient.”
Skills tested
Question type
4.3. What strategies do you employ to ensure compliance with safety regulations in maintenance operations?
Introduction
This question gauges your commitment to safety and regulatory compliance, which are vital aspects of a Maintenance Manager's role.
How to answer
- Discuss your understanding of relevant safety regulations and standards.
- Explain how you implement safety training for your team.
- Share examples of how you conduct safety audits or inspections.
- Detail your approach to reporting and addressing safety incidents.
- Highlight the importance of fostering a safety culture within the team.
What not to say
- Downplaying the importance of safety compliance.
- Suggesting that safety training is unnecessary or infrequent.
- Failing to mention any specific safety protocols or standards.
- Ignoring the role of team engagement in promoting safety.
Example answer
“In my role at a chemical processing plant, I ensured compliance with OSHA regulations by implementing a rigorous safety training program for all maintenance staff. We held monthly safety drills and audits to reinforce safe practices. Additionally, I established a reporting system for near-misses, which encouraged open communication about safety concerns. As a result, we achieved a 40% reduction in safety incidents within a year, showcasing our commitment to a safe working environment.”
Skills tested
Question type
5. Director of Maintenance Interview Questions and Answers
5.1. Can you describe a time when you implemented a maintenance program that significantly improved operational efficiency?
Introduction
This question assesses your strategic thinking and ability to enhance operational efficiency through effective maintenance management, which is crucial for a Director of Maintenance.
How to answer
- Use the STAR method to structure your response (Situation, Task, Action, Result)
- Clearly outline the existing maintenance issues and their impact on operations
- Discuss the specific maintenance program you developed or improved
- Detail how you measured the program's success and its impact on efficiency
- Share any challenges faced during implementation and how you overcame them
What not to say
- Focusing only on technical aspects without discussing strategic goals
- Neglecting to mention measurable outcomes or metrics
- Blaming others for previous inefficiencies without showcasing your role in the solution
- Providing vague examples that lack clarity or depth
Example answer
“At XYZ Manufacturing, our equipment downtime was causing significant production delays. I implemented a predictive maintenance program using data analytics to identify potential failures before they occurred. Within six months, we reduced downtime by 30% and improved overall equipment effectiveness (OEE) by 15%. This experience taught me the importance of leveraging technology in maintenance processes.”
Skills tested
Question type
5.2. How do you prioritize maintenance tasks when faced with limited resources?
Introduction
This question evaluates your decision-making skills and ability to manage resources effectively, which is vital for a Director of Maintenance role.
How to answer
- Discuss your criteria for prioritization, such as safety, impact on production, and regulatory compliance
- Explain any tools or systems you use to assess and prioritize tasks
- Share a specific example of how you managed competing priorities in the past
- Detail how you communicate priorities to your team and ensure alignment
- Mention how you adapt to changing circumstances in prioritization
What not to say
- Suggesting that all tasks are equally important without a clear rationale
- Failing to mention collaboration with other departments or stakeholders
- Neglecting to discuss the importance of safety and compliance
- Providing a one-size-fits-all approach to task prioritization
Example answer
“In my previous role at ABC Corp, we faced a sudden equipment failure that impacted production. I prioritized maintenance tasks based on safety concerns first, followed by tasks that would restore production capacity quickly. I used a risk assessment matrix to communicate priorities to my team and worked closely with production managers to ensure we were aligned. This approach minimized downtime and maintained safety standards.”
Skills tested
Question type
Similar Interview Questions and Sample Answers
Simple pricing, powerful features
Upgrade to Himalayas Plus and turbocharge your job search.
Himalayas
Himalayas Plus
Himalayas Max
Find your dream job
Sign up now and join over 100,000 remote workers who receive personalized job alerts, curated job matches, and more for free!
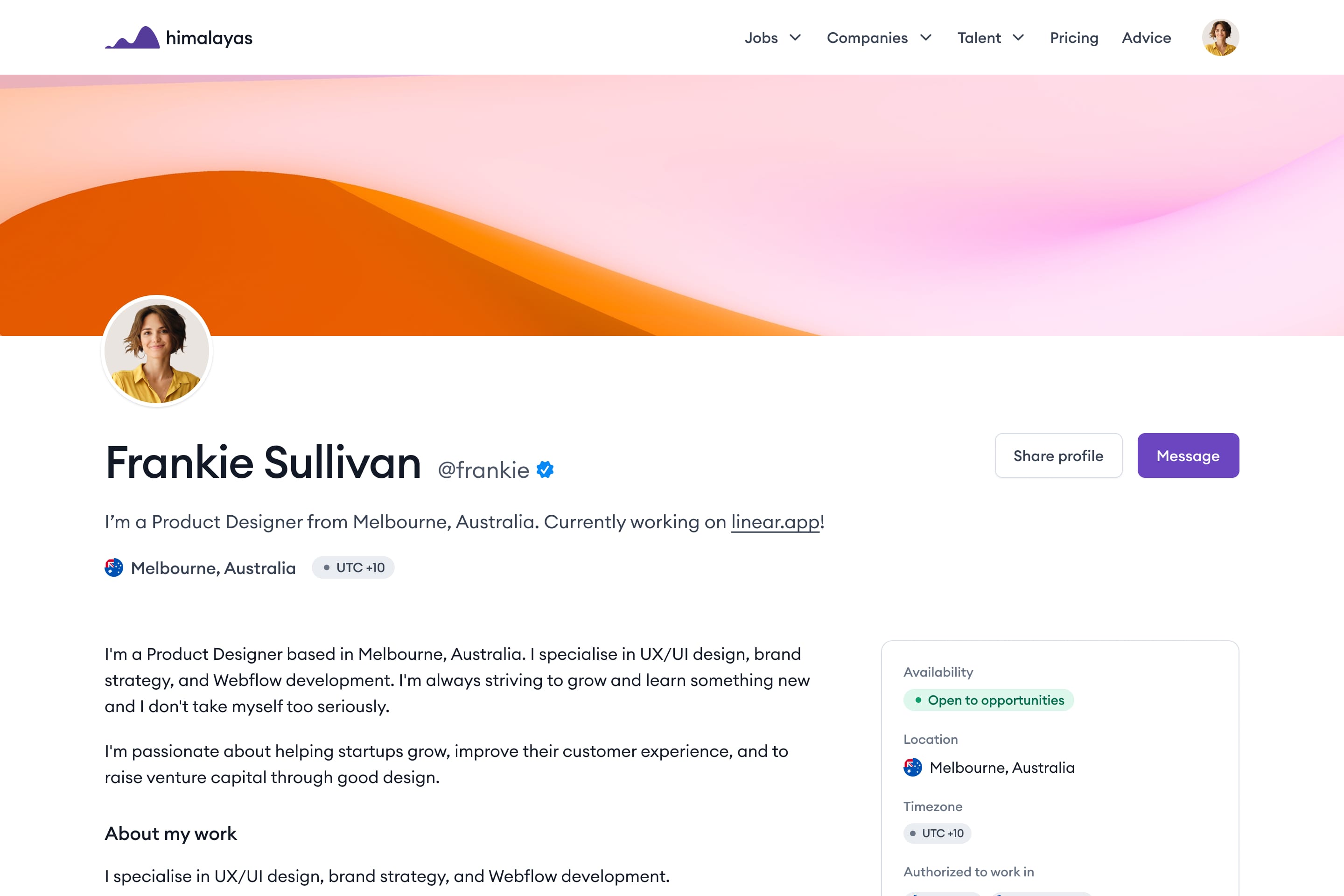