6 Maintenance Director Interview Questions and Answers
Maintenance Directors oversee the upkeep and repair of facilities, equipment, and systems to ensure smooth operations and compliance with safety standards. They manage maintenance teams, develop maintenance schedules, and coordinate with other departments to address operational needs. At junior levels, roles focus on hands-on maintenance and team supervision, while senior roles involve strategic planning, budgeting, and leadership responsibilities. Need to practice for an interview? Try our AI interview practice for free then unlock unlimited access for just $9/month.
Unlimited interview practice for $9 / month
Improve your confidence with an AI mock interviewer.
No credit card required
1. Maintenance Supervisor Interview Questions and Answers
1.1. Describe a time when you had to manage a critical equipment failure. What steps did you take to resolve the issue?
Introduction
This question assesses your problem-solving skills and ability to manage high-pressure situations, which are crucial for a maintenance supervisor.
How to answer
- Start with a brief overview of the equipment and the failure's impact on operations.
- Explain the immediate actions you took to mitigate further issues.
- Detail how you coordinated with your team and other departments.
- Discuss the long-term solutions implemented to prevent recurrence.
- Quantify the results, such as reduced downtime or cost savings.
What not to say
- Focusing only on the technical aspects without discussing team coordination.
- Neglecting to mention the importance of safety measures.
- Failing to provide specific results or improvements achieved.
- Blaming others for the equipment failure without taking responsibility.
Example answer
“At BHP, we faced a critical failure of a conveyor system that halted production. I immediately organized a team to assess the issue while implementing temporary measures to reroute operations. We worked overtime to repair the system, and I coordinated with suppliers for expedited parts. Within 48 hours, we had the system operational again, reducing potential downtime costs by 30%. Following the incident, I initiated regular maintenance training for the team, which has since decreased equipment failures by 25%.”
Skills tested
Question type
1.2. How do you prioritize maintenance tasks when faced with multiple urgent requests?
Introduction
This question evaluates your organizational and prioritization skills, which are essential for ensuring operational efficiency in maintenance management.
How to answer
- Describe your approach to assessing the urgency and impact of each request.
- Explain any frameworks or tools you use for prioritization, such as risk assessment or criticality analysis.
- Highlight the importance of communication with your team and stakeholders.
- Discuss how you ensure that urgent tasks do not compromise scheduled maintenance.
- Provide an example of a time when your prioritization led to a successful outcome.
What not to say
- Indicating that all tasks are treated equally without prioritization.
- Neglecting to mention stakeholder communication in the process.
- Failing to provide a structured approach to prioritization.
- Overemphasizing urgency without considering long-term maintenance needs.
Example answer
“When faced with multiple urgent requests at Rio Tinto, I first assess each situation's impact on safety and production. I use a risk matrix to categorize tasks based on urgency and potential consequences. For instance, when a critical boiler malfunctioned while other repairs were pending, I prioritized its resolution and temporarily rescheduled less urgent tasks. This approach ensured minimal production loss and maintained safety standards, ultimately enhancing our maintenance responsiveness.”
Skills tested
Question type
2. Maintenance Manager Interview Questions and Answers
2.1. Can you describe a time when you implemented a new maintenance strategy that significantly improved efficiency?
Introduction
This question is crucial for understanding your ability to innovate and enhance operational efficiency within maintenance management, which is vital for minimizing downtime and maximizing productivity.
How to answer
- Use the STAR method (Situation, Task, Action, Result) to structure your response
- Clearly describe the initial situation and the inefficiencies present
- Explain the strategy you implemented, including any tools or technologies used
- Detail the specific actions you took and how you engaged your team
- Quantify the results and improvements achieved, such as reduced downtime or cost savings
What not to say
- Focusing too much on the problems without discussing the solution
- Giving vague responses without concrete examples or metrics
- Not mentioning the role of teamwork or collaboration in your success
- Overlooking the importance of continuous improvement or follow-up
Example answer
“At my previous role with Bombardier, we faced frequent equipment failures that led to significant downtime. I introduced a predictive maintenance strategy using IoT sensors, allowing us to monitor equipment health in real-time. As a result, we reduced unplanned downtime by 30% within the first year, which also cut maintenance costs by 15%. This experience taught me the value of leveraging technology for operational efficiency.”
Skills tested
Question type
2.2. How do you ensure compliance with safety regulations and maintenance standards in your team?
Introduction
This question evaluates your knowledge of safety protocols and your ability to instill a culture of safety within your team, which is essential in maintenance management to prevent accidents and ensure regulatory compliance.
How to answer
- Discuss your understanding of relevant safety regulations and standards
- Explain how you educate and train your team on these regulations
- Describe your approach to conducting regular safety audits and inspections
- Highlight any safety improvements you implemented and their impact
- Emphasize the importance of safety culture and open communication
What not to say
- Neglecting to mention specific regulations or standards
- Not providing examples of training or education efforts
- Failing to discuss the importance of team engagement in safety
- Overlooking the consequences of non-compliance
Example answer
“In my role at CN Rail, I prioritized safety compliance by implementing a comprehensive training program for my team on OSHA regulations. We conducted monthly safety audits and established an open-door policy for reporting hazards. Over the last year, we achieved a 20% reduction in workplace incidents, demonstrating that a strong safety culture not only protects employees but also enhances operational efficiency.”
Skills tested
Question type
3. Senior Maintenance Manager Interview Questions and Answers
3.1. Can you describe a time when you implemented a proactive maintenance strategy that significantly reduced downtime?
Introduction
This question assesses your ability to think strategically and implement processes that enhance operational efficiency, a critical aspect of a Senior Maintenance Manager's role.
How to answer
- Use the STAR method to structure your answer, focusing on Situation, Task, Action, and Result.
- Clearly outline the context of your previous maintenance strategy and the challenges faced.
- Detail the proactive measures you took, such as predictive maintenance technologies or training programs.
- Quantify the results, highlighting reduced downtime and cost savings.
- Discuss any lessons learned and how you would apply them to future strategies.
What not to say
- Focusing solely on reactive maintenance without discussing improvements.
- Omitting specific metrics or results from your actions.
- Blaming external factors without taking ownership of the solutions implemented.
- Underestimating the importance of team involvement in the maintenance strategy.
Example answer
“At Renault, I led a project to implement a predictive maintenance system using IoT sensors on our production line. This shift from reactive to proactive maintenance reduced our downtime by 30% within six months and saved the company approximately €200,000 annually. The experience taught me the value of leveraging technology and engaging the team in the transition process.”
Skills tested
Question type
3.2. How do you prioritize maintenance tasks when resources are limited?
Introduction
This question evaluates your decision-making and prioritization skills, essential for managing maintenance operations efficiently.
How to answer
- Describe your approach to assessing the criticality of each maintenance task.
- Explain how you involve your team and use data to inform your prioritization.
- Detail any frameworks or methods you use, such as risk assessment or the criticality matrix.
- Discuss how you communicate priorities to your team and stakeholders.
- Provide an example of a time you successfully managed limited resources.
What not to say
- Claiming to prioritize tasks without any systematic approach.
- Failing to mention how you consider safety and compliance in prioritization.
- Neglecting to involve your team in the decision-making process.
- Overlooking the impact of prioritization on overall operations.
Example answer
“In my role at Airbus, we faced a situation where critical equipment was failing, but we had limited resources. I used a risk assessment approach to prioritize tasks based on safety, operational impact, and cost. By involving my team in discussions, we focused our efforts on high-impact areas, which resulted in a 40% reduction in emergency repairs over three months, demonstrating effective resource management.”
Skills tested
Question type
4. Maintenance Director Interview Questions and Answers
4.1. Can you describe a time when you implemented a preventive maintenance program that significantly reduced equipment downtime?
Introduction
This question evaluates your ability to develop and implement maintenance strategies that enhance operational efficiency, which is crucial for a Maintenance Director.
How to answer
- Start by outlining the initial state of equipment and the challenges faced with downtime
- Explain the steps you took to design and implement the preventive maintenance program
- Discuss the metrics used to measure success and the results achieved
- Highlight any team involvement and training provided to ensure the program's sustainability
- Conclude with lessons learned and how this experience shaped your maintenance philosophy
What not to say
- Focusing on reactive maintenance efforts without discussing preventive strategies
- Not providing specific metrics or results to demonstrate impact
- Neglecting to mention team collaboration or buy-in
- Overlooking the importance of continuous improvement and follow-up
Example answer
“At Tata Steel, I identified that recurring equipment failures were affecting production efficiency. I implemented a preventive maintenance program that included regular inspections and staff training on equipment care. Within six months, we reduced downtime by 30% and improved overall equipment effectiveness by 25%. This experience reinforced the importance of proactive maintenance planning and team engagement.”
Skills tested
Question type
4.2. How would you prioritize maintenance requests when resources are limited?
Introduction
This question assesses your decision-making skills and ability to manage resources effectively under pressure, key competencies for a Maintenance Director.
How to answer
- Describe your criteria for prioritizing maintenance requests (e.g., safety, impact on production, cost)
- Explain how you communicate priorities to your team and stakeholders
- Discuss any tools or systems you use for tracking and managing requests
- Include an example of a challenging situation and how you handled it
- Highlight your approach to continuous evaluation and reassessment of priorities
What not to say
- Indicating that all requests are equally important without a clear prioritization framework
- Failing to mention communication with stakeholders about prioritization
- Overlooking the importance of safety in maintenance decisions
- Not providing a real-life example to support your approach
Example answer
“In my role at Larsen & Toubro, I prioritized maintenance requests based on their impact on safety and production. For instance, a request for a critical conveyor repair took precedence over non-essential tasks. I communicated these priorities across the team using a maintenance management software that tracked requests. This approach not only streamlined our workflow but also ensured that safety issues were addressed promptly.”
Skills tested
Question type
5. Senior Maintenance Director Interview Questions and Answers
5.1. Can you describe a situation where you had to implement a maintenance strategy that significantly improved operational efficiency?
Introduction
This question is crucial for assessing your strategic thinking and ability to enhance operational efficiency, key responsibilities of a Senior Maintenance Director.
How to answer
- Use the STAR method (Situation, Task, Action, Result) to organize your response
- Clearly outline the initial operational challenges you faced
- Detail the specific maintenance strategy you implemented
- Quantify the improvements in efficiency or cost savings resulting from your actions
- Discuss any challenges you encountered during implementation and how you overcame them
What not to say
- Focusing only on the technical aspects without discussing the strategic impact
- Avoiding specifics or metrics that demonstrate success
- Blaming others for any challenges faced during implementation
- Neglecting to describe how you engaged your team in the process
Example answer
“At a manufacturing plant in Milan, we faced high downtime due to equipment failures. I developed a predictive maintenance program using IoT sensors to monitor equipment health. This strategy reduced unplanned downtime by 30% and saved the company €150,000 in maintenance costs over a year. The key was training the team on the new system and ensuring their buy-in for the changes.”
Skills tested
Question type
5.2. How do you ensure compliance with safety and environmental regulations in maintenance operations?
Introduction
This question evaluates your knowledge of industry regulations and your ability to implement compliance measures effectively, which is vital for maintaining safety standards.
How to answer
- Discuss your familiarity with relevant safety and environmental regulations in Italy
- Explain your approach to training and educating your team on compliance
- Detail the processes you put in place to monitor and enforce compliance
- Share an example of a successful compliance initiative you led
- Mention how you stay updated with any regulatory changes
What not to say
- Implying that compliance is not a priority in maintenance operations
- Providing vague statements without concrete examples
- Ignoring the role of teamwork and communication in ensuring compliance
- Failing to mention any specific regulatory frameworks
Example answer
“In my previous role at Fiat, I established a comprehensive training program for the maintenance team on safety regulations, focusing on the ISO 45001 standards. We implemented weekly safety audits, and as a result, our compliance rates improved to 98% over six months. Staying informed about changes through industry workshops also played a crucial role in maintaining our standards.”
Skills tested
Question type
6. VP of Maintenance Interview Questions and Answers
6.1. Can you describe a time when you implemented a preventive maintenance program that significantly reduced downtime?
Introduction
This question is crucial as it evaluates your ability to proactively manage maintenance processes and your impact on operational efficiency, which is essential in a VP role.
How to answer
- Start with a brief overview of the maintenance issues you faced before implementation
- Detail the steps you took to develop and implement the preventive maintenance program
- Explain how you involved your team and other stakeholders in the process
- Quantify the results, such as reductions in downtime and cost savings
- Discuss any challenges you encountered and how you overcame them
What not to say
- Failing to provide specific metrics or data to showcase the impact
- Describing a reactive approach instead of preventive
- Neglecting to mention team involvement or collaboration
- Overlooking the importance of continuous improvement in maintenance
Example answer
“At Huawei, I led the implementation of a preventive maintenance program for our manufacturing equipment. We identified critical machines that frequently broke down and developed a schedule based on usage and wear patterns. This initiative reduced equipment downtime by 30% and saved the company approximately $500,000 in production costs annually. The success was due to strong cross-departmental collaboration and continuous monitoring and adjustments to the program.”
Skills tested
Question type
6.2. How do you ensure safety standards are met within your maintenance team?
Introduction
This question assesses your commitment to safety, which is a top priority in maintenance operations, ensuring compliance and protecting employees.
How to answer
- Discuss your approach to developing and implementing safety protocols
- Explain how you train and communicate safety practices to your team
- Share examples of safety audits or assessments you've conducted
- Highlight any improvements in safety records or incidents due to your initiatives
- Mention how you foster a culture of safety within the team
What not to say
- Suggesting that safety is someone else's responsibility
- Failing to provide specific examples of safety practices or training
- Overlooking the importance of ongoing safety education
- Neglecting to mention compliance with local regulations and standards
Example answer
“At China National Petroleum Corporation, I developed a comprehensive safety program that included regular training sessions, safety audits, and the implementation of a reporting system for near-misses. As a result, we achieved a 40% reduction in workplace incidents over two years. I believe fostering a culture of safety starts with open communication and accountability among all team members.”
Skills tested
Question type
Similar Interview Questions and Sample Answers
Simple pricing, powerful features
Upgrade to Himalayas Plus and turbocharge your job search.
Himalayas
Himalayas Plus
Himalayas Max
Find your dream job
Sign up now and join over 100,000 remote workers who receive personalized job alerts, curated job matches, and more for free!
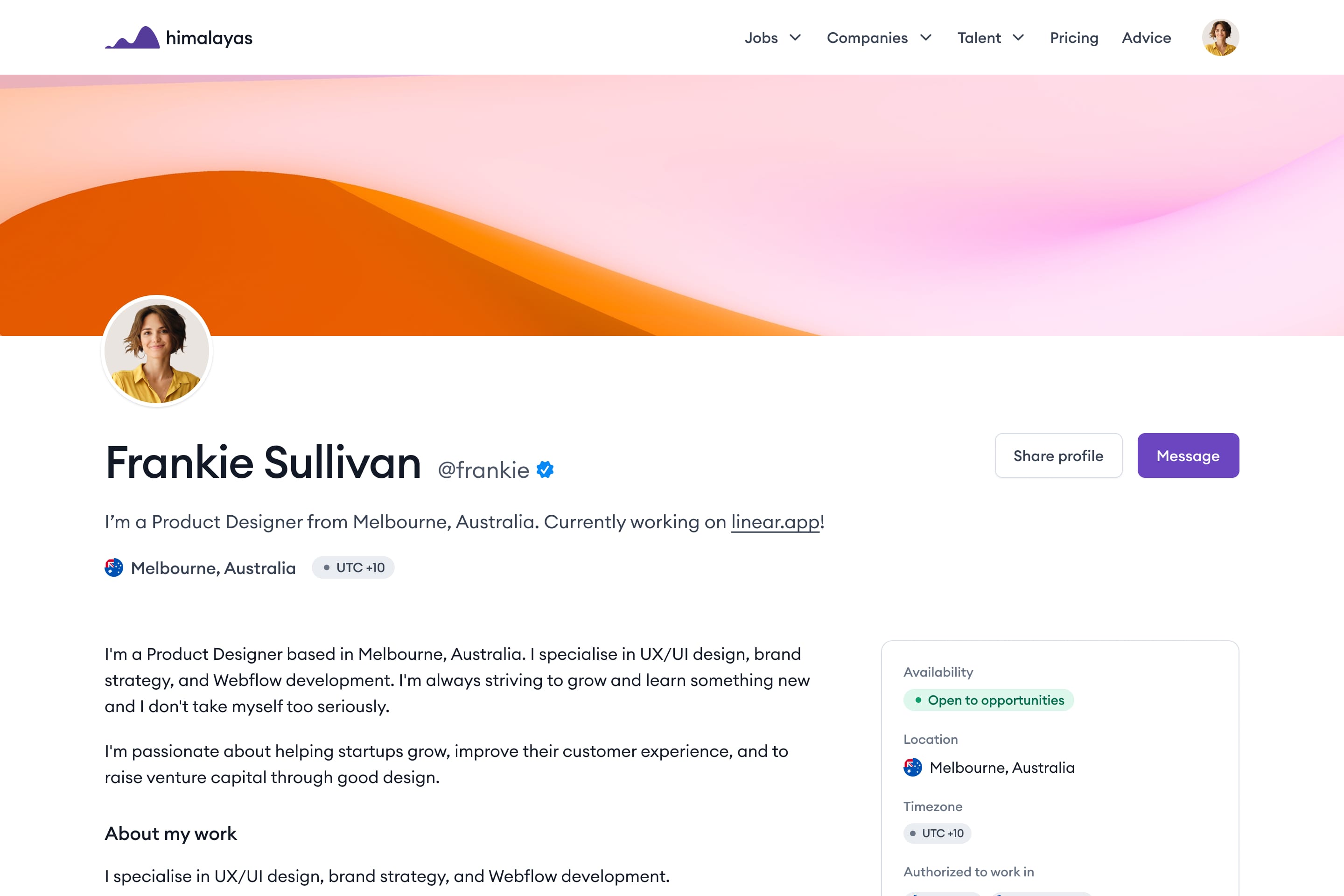