Complete Maintenance Supervisor Career Guide
Maintenance supervisors orchestrate the upkeep of vital equipment and facilities, ensuring operational continuity and safety across diverse industries. They blend technical expertise with leadership skills, optimizing performance and extending asset lifespans. This role offers a direct path to impact productivity and efficiency, making it a cornerstone of any successful operation.
Key Facts & Statistics
Median Salary
$70,080 USD
Range: $45k - $95k+ USD
Growth Outlook
4%
as fast as average
Annual Openings
≈34k
openings annually
Top Industries
Typical Education
High school diploma or equivalent, often with vocational training or an associate's degree; extensive on-the-job experience is crucial.
What is a Maintenance Supervisor?
A Maintenance Supervisor leads and manages a team of maintenance technicians, ensuring the smooth operation and upkeep of an organization's physical assets, machinery, and infrastructure. This role focuses on preventing equipment breakdowns, minimizing downtime, and optimizing the efficiency of maintenance operations. They bridge the gap between strategic maintenance planning and hands-on execution.
This position differs significantly from a Maintenance Technician, who performs the actual repairs and preventive tasks. While a technician executes the work, the supervisor plans, organizes, and oversees it, ensuring tasks align with production schedules and safety standards. They also differ from a Maintenance Manager, who typically handles broader strategic planning, budgeting, and long-term asset management across multiple sites or departments, whereas the supervisor focuses on daily operational oversight within a specific facility or team.
What does a Maintenance Supervisor do?
Key Responsibilities
- Coordinate daily maintenance activities, including corrective, preventive, and predictive tasks, to ensure operational continuity.
- Supervise a team of maintenance technicians, assigning tasks, providing guidance, and evaluating performance to uphold quality standards.
- Develop and implement maintenance schedules and procedures, optimizing resource allocation and minimizing downtime.
- Inspect completed work to ensure compliance with safety regulations, quality standards, and established procedures.
- Manage the inventory of spare parts and equipment, placing orders and tracking usage to prevent stockouts.
- Respond to urgent equipment breakdowns, troubleshooting issues and directing immediate repair efforts.
- Prepare detailed reports on maintenance activities, equipment performance, and budget utilization for management review.],
Work Environment
Maintenance Supervisors primarily work in industrial settings such as manufacturing plants, factories, hospitals, or large commercial facilities. Their environment often includes exposure to machinery, noise, and varying temperatures. They spend significant time on the shop floor, overseeing operations and interacting with technicians.
The role involves a mix of office work for planning and reporting, and hands-on supervision. It is a dynamic, often fast-paced environment where unexpected equipment failures can lead to urgent demands.
Collaboration with production managers, engineers, and safety officers is constant. While some roles might involve on-call duties or weekend shifts, most operate during standard business hours. Remote work is generally not applicable for this hands-on supervisory role.
Tools & Technologies
Maintenance Supervisors regularly use Computerized Maintenance Management Systems (CMMS) such as SAP PM, Maximo, or Fiix for scheduling, work order management, and tracking equipment history. They also utilize Enterprise Resource Planning (ERP) software for inventory control and procurement.
Common tools include diagnostic equipment like multimeters, thermal imagers, and vibration analysis tools, alongside standard hand and power tools. They work with various industrial machinery, including conveyors, pumps, motors, and HVAC systems.
Communication tools such as two-way radios and mobile devices are essential for coordinating teams. Proficiency with Microsoft Office Suite (Excel, Word, Outlook) is also necessary for reporting and administrative tasks.
Maintenance Supervisor Skills & Qualifications
A Maintenance Supervisor's qualifications are highly practical and rooted in hands-on experience, often more so than formal academic credentials. Employers prioritize a strong track record in equipment repair, preventive maintenance, and team leadership. The structure of requirements varies significantly by industry; for instance, a manufacturing plant demands different expertise than a commercial property or a fleet maintenance operation.
Seniority levels also dictate the depth of knowledge required. Entry-level supervisors might oversee a small team with routine tasks, while senior roles often manage complex systems, large budgets, and strategic maintenance planning. Company size influences the scope of responsibilities; smaller companies might expect supervisors to remain hands-on, whereas larger organizations emphasize administrative and managerial oversight. Geographic location can also impact requirements, particularly concerning local safety regulations or specific industry clusters.
Formal education, such as an Associate's degree or vocational training, provides a strong foundation but typically does not outweigh practical experience. Many successful Maintenance Supervisors began as technicians and advanced through on-the-job learning and certifications. Industry-specific certifications, like those in HVAC, electrical systems, or specific machinery operation, add significant value and demonstrate specialized competence. The skill landscape is evolving, with increasing demands for digital literacy, data analysis for predictive maintenance, and automation troubleshooting. Balancing broad mechanical, electrical, and hydraulic knowledge with specialized expertise in new technologies is crucial for career progression.
Education Requirements
Technical Skills
- Preventive and Predictive Maintenance (PM/PdM) techniques and scheduling
- Mechanical systems repair and troubleshooting (e.g., hydraulics, pneumatics, rotating equipment)
- Electrical systems diagnosis and repair (e.g., motors, controls, wiring, schematics reading)
- Programmable Logic Controllers (PLC) troubleshooting and basic programming
- Computerized Maintenance Management Systems (CMMS) operation and data analysis
- Welding and fabrication techniques (e.g., MIG, TIG, stick)
- HVAC system maintenance and repair (depending on industry)
- Blueprint and schematic reading (mechanical, electrical, pneumatic)
- Safety regulations and compliance (e.g., OSHA, Lockout/Tagout, confined space)
- Root Cause Analysis (RCA) methodologies for equipment failures
- Inventory management for spare parts and consumables
- Basic IT network troubleshooting for connected equipment
Soft Skills
- Leadership and Team Motivation: Supervisors must inspire and guide their maintenance teams, fostering a productive and safety-conscious work environment.
- Problem-Solving and Troubleshooting: This role requires quickly diagnosing complex equipment failures and implementing effective, lasting solutions under pressure.
- Organizational and Planning Skills: Supervisors plan maintenance schedules, allocate resources, and manage inventory efficiently to minimize downtime.
- Decision-Making: Making timely and sound judgments regarding repairs, resource allocation, and safety protocols is critical for operational continuity.
- Communication and Interpersonal Skills: Effectively communicating with technicians, management, and other departments about maintenance issues, progress, and needs is essential.
- Safety Awareness and Enforcement: Ensuring strict adherence to safety procedures and regulations is paramount to prevent accidents and maintain a safe workplace.
- Adaptability and Flexibility: Maintenance environments are dynamic; supervisors must adjust plans quickly in response to unexpected breakdowns or changing priorities.
- Mentorship and Training: Developing junior technicians and sharing expertise to enhance team capabilities is a key responsibility.
How to Become a Maintenance Supervisor
Becoming a Maintenance Supervisor involves a blend of technical expertise, leadership skills, and practical experience. While some enter this field through formal education in engineering or industrial technology, many successful supervisors begin as skilled technicians in trades like HVAC, electrical, or mechanics. The timeline to become a supervisor varies; a complete beginner might need 3-5 years to gain foundational skills and experience, while a seasoned technician could transition into a supervisory role within 1-2 years.
Entry routes often depend on the industry and company size. Manufacturing plants, commercial facilities, and residential complexes all require maintenance supervision, but their specific needs differ. Larger corporations might prefer candidates with management certifications or degrees, while smaller businesses or agencies value hands-on experience and proven problem-solving abilities. Misconceptions exist, such as believing a supervisor only directs; in reality, they often troubleshoot complex issues and train junior staff.
Building a strong professional network and finding mentors within the maintenance or facilities management sector is crucial. These connections provide insights into industry best practices, hiring trends, and potential job openings. The hiring landscape values adaptability, strong communication skills, and a proactive approach to preventative maintenance. Overcoming barriers like a lack of formal leadership experience involves seeking out opportunities to lead projects or mentor colleagues in current roles.
Step 1
Step 2
Step 3
Step 4
Step 5
Step 6
Step 7
Education & Training Needed to Become a Maintenance Supervisor
A Maintenance Supervisor ensures operational efficiency and safety by overseeing maintenance activities. The educational pathway for this role often combines technical training with leadership development. While a four-year bachelor's degree in engineering or facilities management provides a strong theoretical foundation, many successful supervisors come from vocational backgrounds, supplemented by certifications and practical experience.
Formal degree programs, such as an Associate's or Bachelor's in Industrial Maintenance, Mechanical Engineering Technology, or Facilities Management, typically cost between $20,000 and $80,000+ and take two to four years to complete. These programs offer in-depth theoretical knowledge, but may lack hands-on experience in specific equipment. Vocational schools and technical colleges offer more focused programs, often leading to certifications or diplomas in areas like HVAC, electrical systems, or industrial machinery repair. These programs usually range from $5,000 to $20,000 and can be completed in 6 to 18 months. Employers often value the practical skills gained from these shorter, more intensive training options.
Online courses and self-study are also viable for acquiring specific technical skills or certifications, with costs ranging from free to a few thousand dollars, and completion times varying from a few weeks to several months. Industry-recognized certifications, such as those from the Society for Maintenance & Reliability Professionals (SMRP) or the Association for Facilities Engineering (AFE), are highly regarded. These demonstrate a commitment to professional standards and can enhance career progression. Continuous learning is crucial for Maintenance Supervisors to keep pace with new technologies and regulations. Many companies also provide in-house training or require participation in professional development workshops, focusing on leadership, safety, and advanced troubleshooting techniques.
Maintenance Supervisor Salary & Outlook
Compensation for a Maintenance Supervisor varies significantly based on several factors. Geographic location plays a crucial role, with higher salaries typically found in major metropolitan areas or regions with high costs of living, as well as in industrial hubs where demand for skilled supervisors is intense. Conversely, rural areas often present lower salary figures.
Years of experience and specialized skills also directly impact earning potential. A supervisor with extensive experience in complex machinery, facility management, or specific industry certifications can command a higher salary. Total compensation packages frequently extend beyond base salary, including performance bonuses, overtime pay, and comprehensive benefits such as health insurance, retirement contributions like 401(k) matching, and paid time off. Some roles may offer professional development allowances for certifications or training.
Industry-specific trends also influence compensation. For instance, supervisors in manufacturing or large-scale industrial operations often earn more than those in commercial real estate or hospitality, due to the complexity and criticality of the equipment managed. Company size also matters; larger organizations with more extensive facilities and budgets generally offer higher pay. Remote work is less common for this role, given its hands-on nature, but some supervisory aspects might be managed remotely for multi-site operations.
Salary negotiation leverage increases with proven leadership skills, a strong track record of efficiency improvements, and the ability to manage complex maintenance projects. While figures primarily reflect the USD context, international markets will show different salary scales influenced by local economic conditions, labor laws, and industry prevalence.
Salary by Experience Level
Level | US Median | US Average |
---|---|---|
Maintenance Technician | $50k USD | $55k USD |
Senior Maintenance Technician | $65k USD | $68k USD |
Maintenance Supervisor | $75k USD | $78k USD |
Maintenance Manager | $90k USD | $95k USD |
Director of Maintenance | $118k USD | $125k USD |
Market Commentary
The job market for Maintenance Supervisors remains stable with steady demand. The Bureau of Labor Statistics projects employment of maintenance and repair workers, including supervisors, to grow by 5% from 2022 to 2032, which is about as fast as the average for all occupations. This growth is driven by the ongoing need to maintain and upgrade existing infrastructure, machinery, and facilities across various industries.
Emerging opportunities for Maintenance Supervisors include roles in smart building technology, predictive maintenance, and automation. As more facilities adopt IoT devices and advanced analytics, supervisors with skills in data interpretation, system diagnostics, and managing automated processes will be highly sought after. This technological shift requires continuous learning and adaptation to new maintenance strategies.
The supply and demand dynamics generally favor experienced candidates, especially those with strong leadership and technical problem-solving abilities. While the overall pool of maintenance workers is large, there is a consistent demand for skilled supervisors who can lead teams, manage budgets, and ensure operational efficiency. Geographic hotspots for this role include manufacturing centers, logistics hubs, and regions with significant commercial or industrial development.
Future-proofing this career involves embracing digital tools, understanding sustainable maintenance practices, and developing expertise in specialized equipment. While automation may change some tasks, the critical human element of supervision, problem-solving, and team leadership remains essential. This profession is relatively recession-resistant, as maintenance is always necessary to prevent costly breakdowns and ensure safety, regardless of economic cycles.
Maintenance Supervisor Career Path
Career progression for a Maintenance Supervisor typically involves a blend of technical mastery, leadership development, and operational management. Individuals often begin as technicians, building hands-on expertise before transitioning into supervisory and managerial roles. This path often divides into an individual contributor (IC) track, focusing on deep technical specialization, or a management track, emphasizing team leadership and strategic oversight. Both paths require continuous learning and adaptation to new technologies.
Advancement speed depends on several factors: an individual's performance, the complexity of the systems maintained, and the size and type of the organization. Larger corporations with complex machinery may offer more structured advancement opportunities than smaller operations. Specializing in critical systems, such as robotics or HVAC, can accelerate progression. Lateral movements might involve transitioning to roles in facilities management, operations, or even engineering within the same industry.
Networking within professional organizations, pursuing relevant certifications (e.g., CMRP, lean manufacturing), and seeking mentorship are crucial for career growth. These actions enhance visibility and provide access to advanced knowledge. Career pivots often lead to roles in quality assurance, project management, or technical training, leveraging the deep understanding of operational systems gained in maintenance.
Maintenance Technician
0-3 yearsKey Focus Areas
Senior Maintenance Technician
3-7 yearsKey Focus Areas
Maintenance Supervisor
6-10 years total experienceKey Focus Areas
Maintenance Manager
10-15 years total experienceKey Focus Areas
Director of Maintenance
15+ years total experienceKey Focus Areas
Maintenance Technician
0-3 yearsPerform routine maintenance tasks, troubleshoot minor equipment issues, and execute repairs under direct supervision. Follow established procedures for preventative and corrective maintenance. Operate standard tools and diagnostic equipment. Document completed work orders and report anomalies to senior technicians or supervisors.
Key Focus Areas
Develop foundational mechanical, electrical, and hydraulic repair skills. Learn to interpret blueprints, schematics, and technical manuals. Understand safety protocols and preventative maintenance schedules. Focus on problem-solving basic equipment malfunctions and documenting work accurately.
Senior Maintenance Technician
3-7 yearsLead complex repairs and diagnostics, often working independently on critical equipment. Provide technical guidance and on-the-job training to less experienced technicians. Assist in planning preventative maintenance programs and participate in equipment installation and commissioning. Serve as a subject matter expert for specific machinery.
Key Focus Areas
Master complex troubleshooting techniques for advanced equipment. Develop diagnostic skills for identifying root causes of failures. Train and mentor junior technicians. Learn to optimize maintenance schedules and contribute to process improvement initiatives. Begin understanding equipment lifecycle management.
Maintenance Supervisor
6-10 years total experienceOversee a team of maintenance technicians, assigning tasks, managing schedules, and ensuring work quality. Responsible for the daily operation and reliability of a section of plant equipment or facility systems. Conduct performance reviews, manage disciplinary actions, and ensure adherence to safety standards. Report on team productivity and equipment status to management.
Key Focus Areas
Develop strong leadership and team management skills, including scheduling, performance management, and conflict resolution. Learn to manage budgets, inventory, and procurement processes. Understand regulatory compliance and safety management systems. Focus on optimizing team efficiency and equipment uptime.
Maintenance Manager
10-15 years total experienceManage the entire maintenance department, including multiple supervisory teams, budgets, and strategic planning. Oversee all preventative, predictive, and corrective maintenance activities across a facility or production line. Responsible for departmental KPIs, cost control, and ensuring regulatory compliance. Develop and implement maintenance policies and procedures.
Key Focus Areas
Develop strategic planning abilities for long-term maintenance programs. Understand asset management principles and capital expenditure planning. Enhance leadership skills for managing multiple teams or shifts. Focus on implementing continuous improvement methodologies like Lean or Six Sigma.
Director of Maintenance
15+ years total experienceProvide executive leadership for all maintenance and reliability functions across multiple sites or a large division. Develop and execute long-term maintenance strategies aligned with corporate objectives. Manage multi-million dollar budgets, capital projects, and vendor relationships at a strategic level. Influence organizational culture towards proactive maintenance and operational excellence.
Key Focus Areas
Develop executive-level leadership, strategic vision, and cross-functional collaboration skills. Understand industry trends, technological advancements, and their impact on maintenance strategies. Focus on optimizing overall operational efficiency and driving significant cost reductions through maintenance excellence.
Job Application Toolkit
Ace your application with our purpose-built resources:
Maintenance Supervisor Resume Examples
Proven layouts and keywords hiring managers scan for.
View examplesMaintenance Supervisor Cover Letter Examples
Personalizable templates that showcase your impact.
View examplesTop Maintenance Supervisor Interview Questions
Practice with the questions asked most often.
View examplesMaintenance Supervisor Job Description Template
Ready-to-use JD for recruiters and hiring teams.
View examplesGlobal Maintenance Supervisor Opportunities
A Maintenance Supervisor's role translates consistently across countries, focusing on overseeing facility or equipment upkeep. Global demand remains high, particularly in manufacturing, logistics, and infrastructure, as industries worldwide prioritize operational efficiency and asset longevity. Regulatory and safety standards vary significantly by region, impacting daily operations and training requirements. Professionals seek international opportunities for career advancement, higher earning potential, or exposure to diverse industrial practices. International certifications like CMRP (Certified Maintenance & Reliability Professional) or specific industry-recognized qualifications enhance global mobility.
Global Salaries
Maintenance Supervisor salaries vary significantly by region, reflecting local economies and industry demands. In North America, specifically the United States, annual salaries typically range from $60,000 to $90,000 USD, with higher figures in metropolitan areas or specialized industries. Canadian salaries are comparable, often between $55,000 and $85,000 CAD (approx. $40,000-$62,000 USD).
Europe shows a wide range. In Western Europe, such as Germany or the UK, salaries might be €45,000 to €70,000 (approx. $48,000-$75,000 USD). Eastern European countries like Poland or the Czech Republic offer lower nominal salaries, perhaps €25,000 to €40,000 (approx. $27,000-$43,000 USD), but purchasing power can be higher due to lower living costs.
Asia-Pacific markets also differ. Australia and New Zealand offer $70,000 to $100,000 AUD (approx. $46,000-$66,000 USD). In Southeast Asia, like Singapore, salaries could be SGD 50,000 to SGD 80,000 (approx. $37,000-$59,000 USD), while in India, they might range from INR 700,000 to INR 1,200,000 (approx. $8,400-$14,400 USD), reflecting vast differences in economic scale and cost of living.
Latin American countries typically have lower nominal salaries. Brazil might offer BRL 60,000 to BRL 100,000 (approx. $12,000-$20,000 USD). Salary structures also differ; some countries offer extensive social benefits and longer vacation times, while others emphasize higher base pay. Tax implications and take-home pay vary significantly based on national tax laws. International experience and specialized education generally enhance compensation prospects globally.
Remote Work
The Maintenance Supervisor role has limited direct international remote work potential. This position fundamentally requires on-site presence to oversee physical assets, teams, and operations. Some administrative tasks, like scheduling, reporting, or budget planning, can be done remotely. However, the core responsibilities demand physical presence in a facility or on a project site.
Digital nomad opportunities are generally not applicable for this role due to its hands-on nature. Companies rarely hire Maintenance Supervisors for fully international remote positions. Any remote aspect usually involves a hybrid model where the supervisor is on-site for most of the week. Therefore, international remote work for a Maintenance Supervisor typically means relocating for an on-site position rather than working from a different country.
Visa & Immigration
Maintenance Supervisors seeking international work often qualify for skilled worker visas. Popular destinations like Canada, Australia, and Germany have specific immigration pathways for skilled trades and management roles. Requirements typically include relevant work experience, a recognized diploma or certification, and a job offer from a local employer. Education credential recognition is crucial; applicants often need their qualifications assessed by designated authorities in the destination country.
Visa timelines vary, from a few months to over a year, depending on the country and visa type. For example, Canada's Express Entry system can process applications relatively quickly for eligible candidates. Language proficiency, usually English or the local language, is often a requirement, demonstrated through standardized tests like IELTS or Goethe-Zertifikat. Some countries offer profession-specific advantages for in-demand trades. Pathways to permanent residency often exist after several years of continuous employment. Practical considerations include securing family visas if dependents are relocating, understanding local labor laws, and potentially obtaining professional licensing where applicable, such as for electrical or mechanical supervision roles.
2025 Market Reality for Maintenance Supervisors
Understanding current market conditions is vital for maintenance supervisors to advance their careers. The industry has evolved significantly since 2023, influenced by post-pandemic operational shifts and the rapid integration of AI into industrial processes. Broader economic factors, such as inflation and supply chain stability, directly impact maintenance budgets and hiring priorities. Market realities for this role vary considerably by experience level, from entry-level team leads to seasoned facility managers, and also by geographic region or the size of the employing organization. This analysis sets realistic expectations for navigating today's maintenance supervision job market.
Current Challenges
Maintenance supervisor candidates face significant competition for senior roles, particularly in stable industries. Economic uncertainty causes some companies to defer equipment upgrades, reducing demand for new supervisory staff. A skill gap exists for those lacking advanced predictive maintenance technologies or data analysis experience. Remote work normalization means more applicants from wider geographic areas, intensifying competition. Companies increasingly seek supervisors with AI-driven diagnostic tool proficiency, a skill many long-term professionals may lack.
Growth Opportunities
Strong demand exists for maintenance supervisors specializing in advanced automation and predictive analytics. Emerging roles like 'Smart Factory Maintenance Lead' or 'IoT Facilities Supervisor' offer significant growth. Professionals can gain an advantage by acquiring certifications in data analysis, condition monitoring technologies, or specific industrial automation platforms. Underserved markets include critical infrastructure sectors, such as utilities and transportation, which consistently need skilled oversight. Geographic regions with new manufacturing investments or expanding logistics hubs also present robust opportunities.
Proficiency with AI-driven diagnostic tools, such as machine learning for anomaly detection or digital twin simulations, provides a strong competitive edge. Supervisors who can demonstrate cost savings through optimized maintenance schedules or improved asset uptime are highly valued. Market corrections, particularly those affecting capital expenditures, can lead companies to prioritize maximizing existing asset lifespan, thus increasing the importance of efficient maintenance supervision. Sectors like renewable energy, data centers, and advanced manufacturing continue to expand, offering stable and growing opportunities for skilled maintenance leaders. Investing in specialized training now can position supervisors for long-term career resilience and upward mobility.
Current Market Trends
Hiring for maintenance supervisors shows steady demand, driven by aging infrastructure and the need for operational efficiency. Industries like manufacturing, logistics, and facilities management consistently seek experienced leaders. Recent years saw a shift towards digital transformation, with companies prioritizing supervisors who can integrate IoT sensors and data analytics into maintenance routines. Economic conditions, while fluctuating, generally support essential maintenance functions, mitigating widespread layoffs in this specific role. However, budget tightening can slow expansion hires.
Generative AI and automation are reshaping the supervisor's role, moving from reactive repairs to proactive, predictive maintenance. Employers now demand supervisors capable of interpreting AI-driven diagnostics and optimizing maintenance schedules using advanced software. This elevates the technical requirements beyond traditional mechanical or electrical skills. Salary trends for maintenance supervisors remain stable, with slight increases for those possessing specialized digital or automation expertise. Market saturation is minimal at the experienced level, but entry-level supervisory roles can see more applicants. Geographic variations exist; industrial hubs in the Midwest and Southeast show stronger demand, while coastal urban centers focus on facilities management. Seasonal patterns are less pronounced, but capital expenditure cycles can influence hiring in specific sectors.
Emerging Specializations
The landscape of maintenance operations is undergoing significant transformation, driven by advancements in technology and evolving industry demands. Understanding these shifts is crucial for Maintenance Supervisors aiming to future-proof their careers and capitalize on new opportunities.
Early positioning in emerging specialization areas allows professionals to become subject matter experts in fields that will define the next generation of maintenance. This strategic foresight often leads to premium compensation, accelerated career progression, and increased influence within an organization. While established specializations offer stability, emerging areas provide a distinct competitive advantage.
Many of these cutting-edge specializations, particularly those integrating AI, IoT, and sustainability principles, are transitioning from niche concepts to mainstream requirements. This timeline suggests that significant job opportunities will materialize and expand rapidly from 2025 onwards. Pursuing these areas involves a calculated risk, as specific technologies or methodologies may evolve quickly. However, the reward for developing expertise in these nascent fields typically outweighs the initial uncertainty, offering a chance to shape the future of maintenance rather than simply react to it.
Predictive Maintenance & IoT Integration Supervisor
This specialization focuses on overseeing the integration and utilization of IoT sensors and data analytics platforms to predict equipment failures before they occur. It involves managing the collection of real-time operational data, interpreting predictive models, and scheduling proactive maintenance interventions. This role significantly reduces downtime and optimizes asset performance across various industrial sectors.
Industrial Automation & Robotics Maintenance Lead
This area involves supervising the deployment, programming, and maintenance of robotic systems and automated guided vehicles (AGVs) within industrial environments. It requires ensuring the seamless operation of automated equipment, troubleshooting complex robotic faults, and optimizing robotic workflows for efficiency and safety. This specialization is vital as automation becomes central to manufacturing and logistics.
Sustainable Operations & Green Building Maintenance
This specialization centers on managing maintenance activities with a strong emphasis on energy efficiency, waste reduction, and sustainable operational practices. It includes overseeing the repair and optimization of energy-efficient equipment, implementing waste management protocols, and ensuring compliance with environmental regulations. This role supports an organization's sustainability goals while reducing operational costs.
Cyber-Physical System (CPS) Security Maintenance Supervisor
This role involves supervising the maintenance of critical industrial cybersecurity infrastructure, ensuring the integrity and security of operational technology (OT) systems. It requires managing the implementation of security patches for industrial control systems, responding to cyber threats affecting machinery, and ensuring network segmentation for maintenance access. This specialization is crucial as industrial systems face increasing cyber risks.
Pros & Cons of Being a Maintenance Supervisor
Making informed career decisions requires a clear understanding of both the benefits and challenges associated with a specific role. A career as a Maintenance Supervisor offers distinct advantages, but it also comes with genuine difficulties that prospective candidates should consider.
It is important to remember that individual experiences can vary significantly based on factors such as company culture, industry sector, the specific types of equipment managed, and the size of the team. What one person views as a pro, another might see as a con, depending on their personal values, lifestyle preferences, and career stage. This assessment aims to provide a realistic outlook to help set appropriate expectations for this demanding yet rewarding profession.
Pros
- Maintenance Supervisors are critical to operational continuity, ensuring machinery and facilities function smoothly, which provides a strong sense of purpose and direct impact on business success. This direct contribution is often highly valued by management.
- The role offers consistent demand across various industries, including manufacturing, healthcare, hospitality, and public utilities, providing strong job security and diverse employment opportunities. Economic downturns often highlight the need for efficient maintenance.
- Supervisors gain extensive technical knowledge across a wide range of equipment and systems, enhancing their problem-solving abilities and making them highly versatile professionals. This continuous learning keeps the job intellectually stimulating.
- The position often comes with a competitive salary and benefits package, reflecting the specialized skills and critical responsibilities involved in minimizing downtime and ensuring asset longevity. Overtime and on-call pay can further boost earnings.
- Maintenance Supervisors lead and mentor a team of technicians, developing their leadership, communication, and team-building skills. This aspect of the role can be very rewarding as they guide others to grow professionally.
- The role involves diverse tasks daily, from troubleshooting complex equipment failures and implementing preventive maintenance programs to managing budgets and coordinating with other departments. This variety prevents monotony.
- Successful performance in this role can open doors to more senior management positions, such as Maintenance Manager, Operations Manager, or even Plant Manager, offering clear pathways for career advancement within an organization or industry.
Cons
- Maintenance Supervisors often face unpredictable work schedules, including on-call duties, nights, and weekends, to address unexpected equipment breakdowns or urgent repairs. This can significantly impact personal time and work-life balance.
- The role carries significant responsibility for equipment uptime, safety, and team performance, leading to high-pressure situations when critical machinery fails or production targets are at risk. Managing these high-stakes scenarios can be mentally taxing.
- Supervisors must constantly balance competing demands from production, safety, and budget constraints, often requiring difficult decisions about resource allocation and repair priorities. This balancing act can be a source of daily frustration.
- Dealing with diverse personalities, skill levels, and potential resistance to new procedures among a maintenance team requires strong interpersonal and conflict resolution skills. Managing team dynamics and performance can be challenging.
- The work environment often involves exposure to noise, dust, chemicals, and varying temperatures in industrial or facility settings. This can present physical discomforts and potential health hazards over time.
- Career progression can sometimes be limited within a single organization, as senior maintenance management roles are fewer. Advancing often requires moving to larger companies or different industries.
- Maintenance Supervisors must stay updated on new technologies, safety regulations, and equipment advancements. This demands continuous learning and adaptation to ensure effective team leadership and operational efficiency.
Frequently Asked Questions
Maintenance Supervisors balance technical expertise with leadership, often facing distinct challenges around team management, budget oversight, and unexpected equipment failures. This section addresses crucial questions about transitioning into this role, from required certifications to managing diverse teams and navigating on-call responsibilities.
What are the typical qualifications and experience needed to become a Maintenance Supervisor?
Most Maintenance Supervisor roles require several years of hands-on experience in a maintenance or trade field, typically 5-10 years, along with a high school diploma or GED. Some employers prefer an associate's degree in a related technical field or maintenance management. Certifications like CMRP (Certified Maintenance and Reliability Professional) or CRL (Certified Reliability Leader) can significantly boost your qualifications and demonstrate advanced understanding.
What is the typical work schedule and does it involve on-call duties or irregular hours?
While some roles follow standard business hours, many Maintenance Supervisor positions require flexibility, including on-call availability for emergencies, especially in 24/7 operations. You can expect to work occasional evenings or weekends, particularly during peak production times, equipment breakdowns, or planned maintenance shutdowns. The work-life balance largely depends on the industry and the size of the facility.
What are the core responsibilities of a Maintenance Supervisor on a day-to-day basis?
Maintenance Supervisors oversee a team of technicians, schedule and prioritize work orders, manage preventive maintenance programs, and ensure safety compliance. You will also be responsible for troubleshooting complex issues, managing parts inventory, and contributing to budget planning for maintenance operations. Effective communication and problem-solving are crucial.
What is the typical salary range and benefits package for a Maintenance Supervisor?
The salary for a Maintenance Supervisor varies widely based on industry, location, and experience. Entry-level supervisors might start around $60,000-$70,000 annually, while experienced supervisors in high-demand industries like manufacturing or utilities can earn $80,000-$100,000+. Benefits packages often include health insurance, retirement plans, and paid time off, reflecting the critical nature of the role.
What are the potential career advancement opportunities for a Maintenance Supervisor?
The career path for a Maintenance Supervisor often leads to roles like Maintenance Manager, Operations Manager, or even Plant Manager. You can also specialize in areas like reliability engineering, facilities management, or project management. Continuous learning, leadership training, and pursuing advanced certifications are key to upward mobility.
How secure is the job market for Maintenance Supervisors, and is the field growing?
The field of maintenance is generally stable and in high demand, as all industries rely on functioning equipment and facilities. The job security for Maintenance Supervisors is strong, particularly for those with diverse technical skills and strong leadership abilities. Automation is changing some tasks, but the need for skilled oversight and problem-solving remains essential.
What are the biggest challenges or stressors unique to being a Maintenance Supervisor?
The most significant challenges include managing unexpected breakdowns, balancing preventive maintenance with reactive repairs, and effectively motivating and training a diverse team. You also need to navigate budget constraints, ensure compliance with safety regulations, and adapt to new technologies. It requires strong organizational skills and the ability to perform under pressure.
Related Careers
Explore similar roles that might align with your interests and skills:
Building Maintenance Supervisor
A growing field with similar skill requirements and career progression opportunities.
Explore career guideMaintenance Director
A growing field with similar skill requirements and career progression opportunities.
Explore career guideMaintenance Manager
A growing field with similar skill requirements and career progression opportunities.
Explore career guideMaintenance Superintendent
A growing field with similar skill requirements and career progression opportunities.
Explore career guideMaintenance Technician
A growing field with similar skill requirements and career progression opportunities.
Explore career guideAssess your Maintenance Supervisor readiness
Understanding where you stand today is the first step toward your career goals. Our Career Coach helps identify skill gaps and create personalized plans.
Skills Gap Analysis
Get a detailed assessment of your current skills versus Maintenance Supervisor requirements. Our AI Career Coach identifies specific areas for improvement with personalized recommendations.
See your skills gapCareer Readiness Assessment
Evaluate your overall readiness for Maintenance Supervisor roles with our AI Career Coach. Receive personalized recommendations for education, projects, and experience to boost your competitiveness.
Assess your readinessSimple pricing, powerful features
Upgrade to Himalayas Plus and turbocharge your job search.
Himalayas
Himalayas Plus
Himalayas Max
Find your dream job
Sign up now and join over 100,000 remote workers who receive personalized job alerts, curated job matches, and more for free!
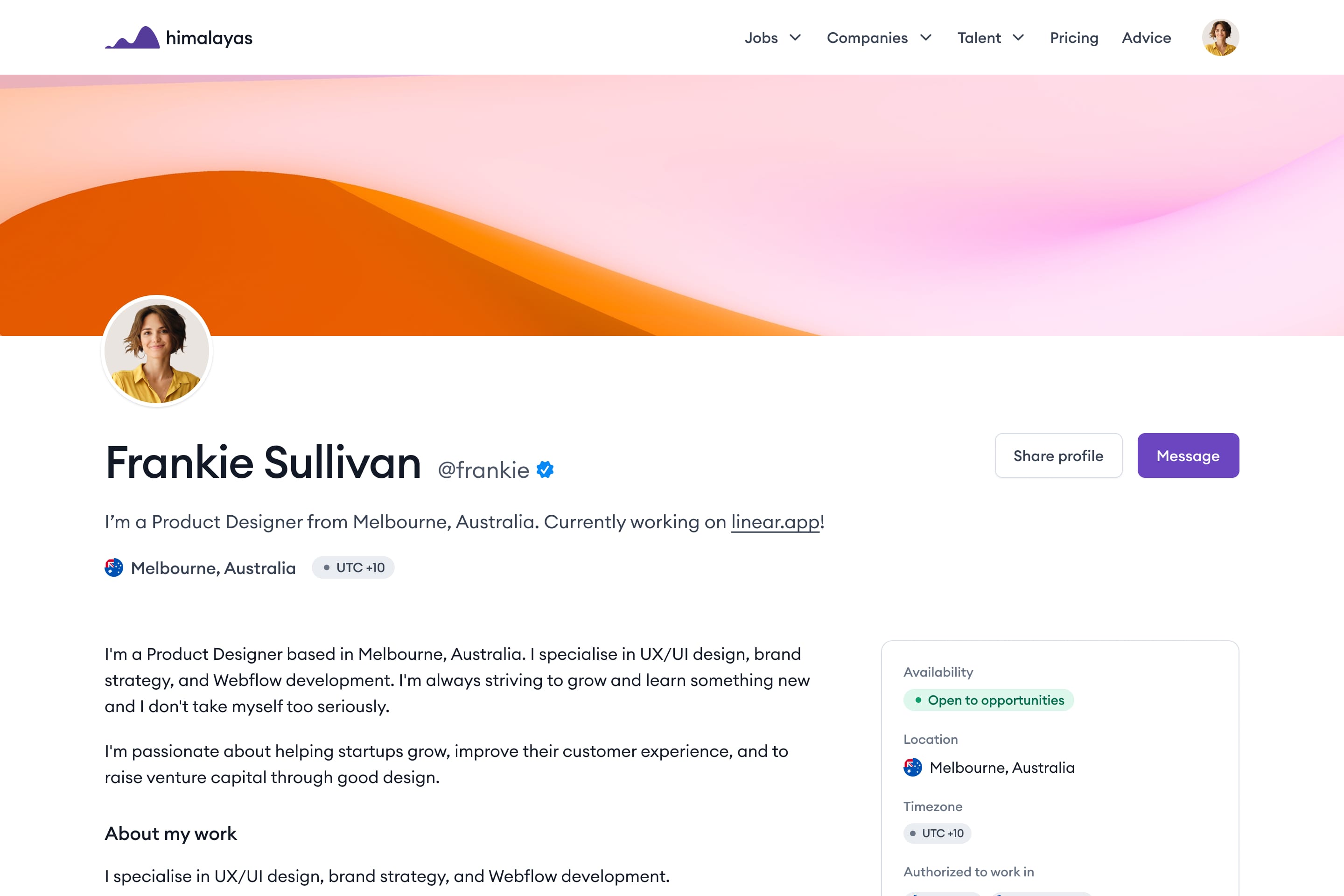