5 Efficiency Engineer Interview Questions and Answers
Efficiency Engineers focus on optimizing processes, systems, and workflows to improve productivity and reduce waste. They analyze operations, identify inefficiencies, and implement solutions to enhance performance and cost-effectiveness. At junior levels, they assist in data collection and analysis, while senior engineers lead optimization projects, mentor teams, and drive strategic improvements across organizations. Need to practice for an interview? Try our AI interview practice for free then unlock unlimited access for just $9/month.
Unlimited interview practice for $9 / month
Improve your confidence with an AI mock interviewer.
No credit card required
1. Junior Efficiency Engineer Interview Questions and Answers
1.1. Can you describe a project where you improved a process or system's efficiency? What steps did you take?
Introduction
This question is crucial for a Junior Efficiency Engineer as it assesses your ability to identify inefficiencies and implement solutions, which is a core responsibility of the role.
How to answer
- Start by describing the process or system you worked on, including its original state
- Explain how you identified inefficiencies (data analysis, feedback, observations)
- Detail the specific actions you took to improve efficiency, emphasizing your role and contributions
- Quantify the results of your improvements, such as time saved or cost reductions
- Reflect on what you learned from the experience and how it can apply to future projects
What not to say
- Giving a vague answer without specific details about the process or improvements
- Not mentioning how you identified the inefficiency
- Failing to provide measurable outcomes from your actions
- Taking sole credit without acknowledging the contributions of team members
Example answer
“During my internship at BMW, I worked on a project to streamline the inventory management process. By analyzing data and gathering feedback from the warehouse staff, I identified bottlenecks in the tracking system. I implemented a new software solution that reduced inventory processing time by 30%. This experience taught me the importance of collaboration and data-driven decision-making in achieving efficiency.”
Skills tested
Question type
1.2. What tools or methodologies do you use to analyze and improve efficiency in engineering processes?
Introduction
Understanding the tools and methodologies you are familiar with helps gauge your technical competence and readiness to contribute to the team's efficiency goals.
How to answer
- List specific tools (e.g., Lean Six Sigma, Kaizen, process mapping software) that you have used
- Explain how you have applied these tools in past projects or academic work
- Discuss your understanding of the principles behind these methodologies and their relevance to efficiency engineering
- Provide examples of how these tools led to measurable improvements
- Mention any certifications or training related to these methodologies if applicable
What not to say
- Claiming to know tools or methodologies without being able to explain them
- Limiting your answer to only one tool without showing breadth of knowledge
- Failing to connect the tools to real-world applications
- Not demonstrating an understanding of efficiency principles
Example answer
“I have experience using Lean Six Sigma methodologies, particularly in my university capstone project, where we applied process mapping to identify waste in a manufacturing line. This approach helped us implement changes that reduced cycle time by 15%. Additionally, I am familiar with software tools like Minitab for data analysis, which I used to evaluate the effectiveness of our solutions.”
Skills tested
Question type
2. Efficiency Engineer Interview Questions and Answers
2.1. Can you describe a project where you significantly improved operational efficiency?
Introduction
This question assesses your ability to identify inefficiencies and implement solutions, which is crucial for the role of an Efficiency Engineer.
How to answer
- Start by outlining the initial state of operations and the specific inefficiencies observed
- Explain the methodology you used to analyze the processes involved
- Detail the changes you implemented and why you chose those methods
- Quantify the improvements achieved in terms of time, cost, or resource savings
- Discuss any challenges encountered during implementation and how you overcame them
What not to say
- Focusing solely on technical aspects without mentioning the impact on the team or organization
- Not providing concrete metrics to showcase your success
- Claiming success without acknowledging the contributions of others
- Minimizing the importance of stakeholder engagement in the process
Example answer
“At a manufacturing plant in Johannesburg, I noticed that our assembly line had a 20% downtime due to poorly coordinated shifts. I conducted a time-motion study and reorganized the shift schedules to align with peak production times. As a result, we reduced downtime by 30%, saving the company approximately R500,000 annually. This experience highlighted the importance of data-driven decisions and team collaboration.”
Skills tested
Question type
2.2. How do you prioritize which processes to improve when faced with multiple opportunities?
Introduction
This question evaluates your decision-making skills and ability to balance multiple priorities, which is key for an Efficiency Engineer.
How to answer
- Describe a prioritization framework you use, such as the Eisenhower Matrix or cost-benefit analysis
- Explain how you gather input from stakeholders to assess the impact of each process
- Detail how you consider factors like ease of implementation, cost, and expected outcomes
- Provide an example of a time when you had to make a tough prioritization decision
- Discuss how you communicate your decisions with the team and stakeholders
What not to say
- Suggesting that all processes are equally important without a clear strategy
- Neglecting to mention stakeholder input in your decision-making process
- Failing to provide a systematic approach to prioritization
- Overemphasizing one aspect (e.g., cost) without considering other impacts
Example answer
“When prioritizing process improvements at a logistics company, I used a cost-benefit analysis to evaluate each opportunity. I engaged with team leads to understand the operational impact. One significant improvement was streamlining our inventory management process, which reduced holding costs by 15% while improving order accuracy. This structured approach helped align our improvements with broader business goals.”
Skills tested
Question type
3. Senior Efficiency Engineer Interview Questions and Answers
3.1. Can you describe a project where you identified and implemented a significant efficiency improvement in a process?
Introduction
This question assesses your analytical skills and ability to drive process improvements, which are crucial for a Senior Efficiency Engineer tasked with optimizing operations.
How to answer
- Use the STAR method (Situation, Task, Action, Result) to structure your response.
- Clearly define the initial situation and the inefficiencies you identified.
- Explain the analysis you conducted to understand the root causes of inefficiencies.
- Detail the specific actions you took to implement changes.
- Quantify the results and improvements achieved, such as cost savings or time reductions.
What not to say
- Focusing on minor improvements that lack significant impact.
- Failing to mention specific metrics or results.
- Not discussing the analysis process and how you reached your conclusions.
- Ignoring challenges faced during implementation.
Example answer
“At Bombardier, I led a project to streamline our supply chain processes. Initially, we faced delays due to redundant approval steps. I analyzed the workflow and proposed a new approval system that cut unnecessary steps by 40%. As a result, we reduced lead times by 25%, which significantly improved our on-time delivery rates.”
Skills tested
Question type
3.2. How do you approach balancing efficiency improvements with maintaining quality and safety in engineering projects?
Introduction
This question evaluates your ability to prioritize and balance multiple objectives, a key skill for a Senior Efficiency Engineer who must ensure that enhancements do not compromise quality or safety.
How to answer
- Discuss your framework for evaluating trade-offs between efficiency, quality, and safety.
- Provide examples of past experiences where you successfully balanced these priorities.
- Explain how you involve stakeholders in decision-making to ensure all aspects are considered.
- Highlight your understanding of industry standards and regulations that must be adhered to.
- Mention any tools or methodologies you use to analyze these trade-offs.
What not to say
- Suggesting that efficiency should always take precedence over other factors.
- Failing to provide specific examples or experiences.
- Overlooking the importance of stakeholder involvement.
- Neglecting to mention relevant industry standards or safety protocols.
Example answer
“In my role at SNC-Lavalin, I worked on optimizing a construction process. I conducted a thorough risk assessment and involved quality assurance teams to ensure changes wouldn’t compromise safety. We found a way to reduce material waste by 30% while maintaining compliance with all safety regulations. This balance allowed us to save costs without sacrificing quality.”
Skills tested
Question type
4. Lead Efficiency Engineer Interview Questions and Answers
4.1. Can you describe a project where you implemented significant improvements in operational efficiency?
Introduction
This question is vital for evaluating your ability to identify inefficiencies and implement effective solutions, which is crucial for a Lead Efficiency Engineer.
How to answer
- Start by outlining the initial state of operations and the specific inefficiencies identified
- Explain the analysis methods used to assess the situation (e.g., data analysis, process mapping)
- Detail the steps you took to implement changes, including any tools or technologies used
- Quantify the results achieved, such as cost savings, time reductions, or increased output
- Discuss any challenges faced during implementation and how you overcame them
What not to say
- Focusing on efforts that did not yield measurable results
- Neglecting to mention team contributions or collaboration
- Providing vague descriptions without specific metrics
- Avoiding discussion of challenges and how they were addressed
Example answer
“At a manufacturing facility, I noticed that our assembly line had excessive downtime due to equipment failures. By analyzing the maintenance logs and employing a predictive maintenance strategy, we implemented a schedule that reduced downtime by 30% and increased overall output by 15%. This project highlighted the importance of data-driven decisions in operational efficiency.”
Skills tested
Question type
4.2. How do you prioritize which processes to improve when faced with multiple inefficiencies?
Introduction
This question assesses your strategic thinking and prioritization skills, which are essential for managing resources effectively in a Lead Efficiency Engineer role.
How to answer
- Describe a prioritization framework you would use (e.g., impact vs. effort matrix)
- Explain how you gather data to assess the potential impact of improvements
- Discuss stakeholder involvement in decision-making
- Detail how you consider short-term vs. long-term benefits
- Provide an example of a time when you had to make such decisions
What not to say
- Suggesting that all processes should be improved at once
- Ignoring data-driven decision-making
- Failing to communicate how you involve stakeholders
- Lacking a structured approach to prioritization
Example answer
“When prioritizing improvements, I use an impact vs. effort matrix to evaluate potential projects. For example, at a logistics company, I identified three processes with varying complexities. By focusing on a process that was low effort but high impact, we improved delivery times by 20% within a quarter while planning for more complex projects in the background. Stakeholder feedback was key in aligning on priorities.”
Skills tested
Question type
5. Efficiency Engineering Manager Interview Questions and Answers
5.1. Can you describe a project where you implemented a significant process improvement in engineering operations?
Introduction
This question is crucial for understanding your ability to drive efficiency and improve processes within engineering teams, which is a core responsibility of an Efficiency Engineering Manager.
How to answer
- Use the STAR method to clearly articulate the situation, task, action, and result
- Describe the initial state of the process and the challenges faced
- Detail the specific strategies and tools you used to implement improvements
- Quantify the results achieved, such as time saved, cost reduced, or quality enhanced
- Reflect on the lessons learned and how they can be applied to future projects
What not to say
- Focusing solely on technical aspects without mentioning the impact on team performance
- Neglecting to provide measurable outcomes from the improvement
- Claiming credit for team efforts without acknowledging contributions
- Avoiding discussions of any challenges faced during implementation
Example answer
“At Tesla, I led a project to streamline our product development process, which was causing delays. By adopting Agile methodologies and implementing a Kanban system, we reduced our time-to-market by 30%. This improvement not only enhanced team morale but also increased stakeholder satisfaction. I learned the importance of continuous feedback loops in sustaining process efficiency.”
Skills tested
Question type
5.2. How would you approach identifying inefficiencies within an engineering team?
Introduction
This question evaluates your analytical skills and approach to fostering a culture of continuous improvement within engineering teams.
How to answer
- Explain your methodology for assessing current processes and workflows
- Discuss the importance of data collection and analysis in identifying inefficiencies
- Describe how you would engage team members in the assessment process
- Outline how you would prioritize issues based on impact and feasibility
- Mention the tools or techniques you would use to track improvements over time
What not to say
- Claiming to have a one-size-fits-all solution without considering team dynamics
- Ignoring the role of team input in identifying inefficiencies
- Focusing only on quantitative data while neglecting qualitative insights
- Failing to mention follow-up measures to ensure sustained improvements
Example answer
“I would start with a comprehensive audit of current workflows, utilizing tools like value stream mapping to visualize processes. Engaging the team in workshops to gather insights about pain points is crucial. I would prioritize inefficiencies based on their impact on project delivery and employee satisfaction. Implementing a continuous feedback mechanism ensures we remain agile and responsive to emerging challenges.”
Skills tested
Question type
Similar Interview Questions and Sample Answers
Simple pricing, powerful features
Upgrade to Himalayas Plus and turbocharge your job search.
Himalayas
Himalayas Plus
Himalayas Max
Find your dream job
Sign up now and join over 100,000 remote workers who receive personalized job alerts, curated job matches, and more for free!
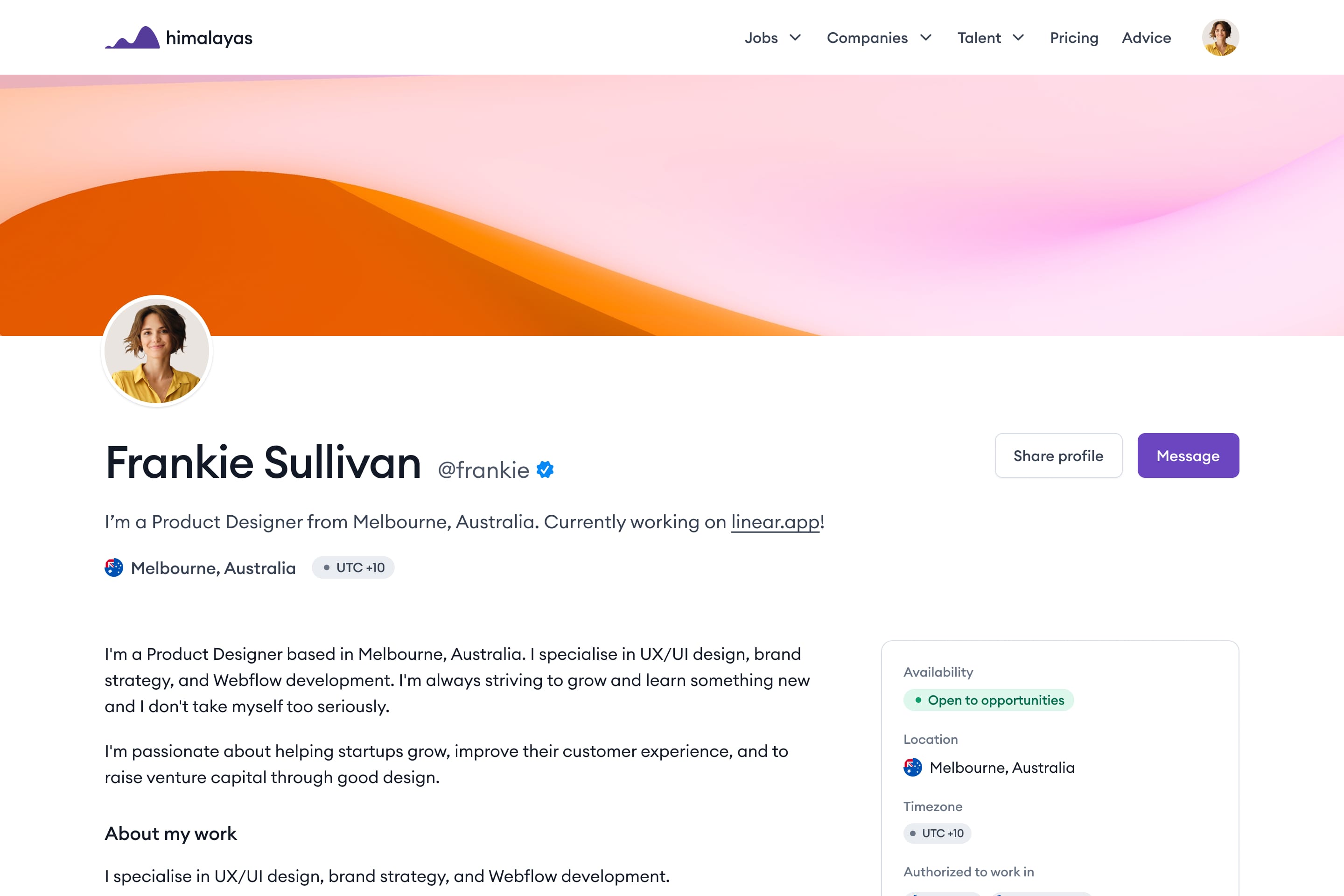