7 Industrial Engineer Interview Questions and Answers
Industrial Engineers focus on optimizing complex systems, processes, and organizations to improve efficiency, productivity, and quality. They analyze workflows, design systems, and implement solutions to reduce waste and enhance performance. Entry-level roles involve data collection and process analysis, while senior positions oversee large-scale projects, mentor teams, and drive strategic improvements across operations. Need to practice for an interview? Try our AI interview practice for free then unlock unlimited access for just $9/month.
Unlimited interview practice for $9 / month
Improve your confidence with an AI mock interviewer.
No credit card required
1. Junior Industrial Engineer Interview Questions and Answers
1.1. Can you describe a project where you improved a process in a manufacturing setting?
Introduction
This question is crucial for assessing your practical experience and understanding of process improvement, which is a key aspect of industrial engineering.
How to answer
- Use the STAR method (Situation, Task, Action, Result) to structure your response
- Clearly describe the initial situation and the specific process you aimed to improve
- Detail the steps you took to analyze and implement changes
- Discuss the tools or methodologies used, such as Lean or Six Sigma
- Quantify the results achieved, such as time savings or cost reductions
What not to say
- Providing vague examples without specific metrics
- Focusing on a project where you had no active role
- Neglecting to explain the analysis process
- Overlooking the importance of teamwork in the improvement
Example answer
“At a local automotive parts factory, I identified inefficiencies in the assembly line that caused delays. By applying Lean principles, I mapped the workflow, pinpointed bottlenecks, and reorganized the workspace layout. This led to a 20% reduction in cycle time and improved overall efficiency. The project reinforced my belief in continuous improvement and teamwork.”
Skills tested
Question type
1.2. How do you approach problem-solving when faced with a technical challenge?
Introduction
This question evaluates your critical thinking and problem-solving skills, essential for addressing technical issues in industrial engineering.
How to answer
- Describe your structured approach to problem-solving, such as defining the problem, analyzing data, and developing solutions
- Share an example of a technical challenge you faced and how you resolved it
- Highlight any tools or software you used in your analysis
- Explain how you validated your solution's effectiveness
- Discuss how you involve others in the problem-solving process
What not to say
- Claiming you solve problems solely based on intuition
- Providing examples that lack depth or clarity
- Neglecting to mention the importance of data in decision-making
- Failing to acknowledge the role of collaboration
Example answer
“When faced with a recurring defect in a production line, I first gathered data on the defect rates and analyzed the process using statistical tools. I identified that a specific machine was misaligned, causing the issue. After recalibrating the machine, defects dropped by 30%. This experience taught me the value of data-driven decision-making and teamwork.”
Skills tested
Question type
2. Industrial Engineer Interview Questions and Answers
2.1. Can you describe a project where you improved a manufacturing process? What methods did you use?
Introduction
This question assesses your problem-solving skills and ability to apply industrial engineering principles to enhance efficiency in manufacturing processes.
How to answer
- Start with a brief overview of the manufacturing process you worked on.
- Explain the specific issues or inefficiencies you identified.
- Describe the methods or tools you used to analyze and improve the process (e.g., Lean, Six Sigma, process mapping).
- Quantify the improvements you achieved, such as cost savings or production time reductions.
- Discuss any challenges faced during the project and how you overcame them.
What not to say
- Vague descriptions without specific methods or tools.
- Focusing on the problem without discussing the solution.
- Failing to mention measurable outcomes or results.
- Taking sole credit without acknowledging team contributions.
Example answer
“At Boeing, I identified bottlenecks in the assembly line causing delays. I applied Lean principles to streamline workflows, implementing a Just-In-Time (JIT) inventory system. This reduced lead time by 30% and saved the company approximately $200,000 annually. The key was involving the team in the process redesign to ensure buy-in and practical implementation.”
Skills tested
Question type
2.2. Describe a time when you had to work with a cross-functional team to achieve a project goal. How did you ensure effective collaboration?
Introduction
This question evaluates your teamwork and communication skills, which are crucial for industrial engineers who often collaborate with multiple departments.
How to answer
- Use the STAR method to structure your response.
- Clearly outline the project and the roles of different team members.
- Explain how you facilitated communication between team members.
- Detail any tools or techniques you used to enhance collaboration (e.g., project management software, regular meetings).
- Share the outcome of the project and any lessons learned about teamwork.
What not to say
- Focusing only on your contributions without mentioning team dynamics.
- Describing a lack of communication as the norm.
- Vague references to teamwork without specific examples.
- Neglecting to mention how you handled conflicts or challenges.
Example answer
“While working at General Motors, I was part of a cross-functional team tasked with reducing waste in the supply chain. I set up weekly meetings and used Trello for project tracking, ensuring everyone was aligned. This collaborative approach led to a 15% reduction in material waste and improved relationships between departments. I learned that clear communication is key to successful project outcomes.”
Skills tested
Question type
3. Senior Industrial Engineer Interview Questions and Answers
3.1. Can you describe a project where you improved a manufacturing process? What steps did you take?
Introduction
This question assesses your experience with process improvement and your ability to apply engineering principles in a manufacturing context, which is crucial for a Senior Industrial Engineer.
How to answer
- Use the STAR method to structure your response: Situation, Task, Action, Result.
- Describe the specific manufacturing process you targeted for improvement.
- Explain the data collection and analysis methods you employed to identify inefficiencies.
- Detail the changes you implemented and why you chose those specific strategies.
- Quantify the results achieved, such as cost savings, efficiency gains, or reduction in waste.
What not to say
- Focusing too much on theoretical knowledge without practical examples.
- Failing to mention collaboration with other team members or departments.
- Neglecting to discuss how you measured the success of the improvements.
- Providing vague answers without specific metrics or outcomes.
Example answer
“At Toyota, I led a project to streamline our assembly line process for a new vehicle. By analyzing production data, I identified bottlenecks that caused delays. I implemented a new scheduling system that improved workflow and reduced idle time by 20%. As a result, we increased production capacity and decreased operational costs by 15%. This experience taught me the importance of data-driven decision-making in process improvement.”
Skills tested
Question type
3.2. How do you ensure safety and compliance in an industrial engineering project?
Introduction
This question gauges your understanding of safety standards and your ability to integrate compliance into engineering practices, vital for maintaining workplace safety.
How to answer
- Discuss your knowledge of industry regulations and safety standards relevant to the manufacturing sector.
- Explain your methods for conducting risk assessments and audits.
- Describe how you incorporate safety measures into your engineering designs and processes.
- Share examples of how you have trained staff on safety practices.
- Mention any certifications or training you have related to safety compliance.
What not to say
- Ignoring the importance of safety measures and only focusing on efficiency.
- Providing generic responses without specific safety protocols or standards.
- Failing to demonstrate a proactive approach to safety and compliance.
- Neglecting to mention collaboration with safety officers or regulatory bodies.
Example answer
“In my role at Hitachi, I conducted thorough risk assessments before initiating any project. I ensured compliance with ISO 45001 standards by integrating safety protocols into our project plans. I also organized regular training sessions for staff on safety practices, which resulted in a 30% decrease in workplace incidents. This proactive approach not only ensured compliance but also fostered a culture of safety in the workplace.”
Skills tested
Question type
4. Lead Industrial Engineer Interview Questions and Answers
4.1. Can you describe a complex process improvement project you led and the results that were achieved?
Introduction
This question assesses your ability to lead process improvement initiatives, a critical skill for a Lead Industrial Engineer, as it directly impacts efficiency and cost reduction.
How to answer
- Use the STAR method to structure your response: Situation, Task, Action, Result.
- Clearly define the process that needed improvement and its significance to the organization.
- Discuss the specific steps you took to analyze the process and identify bottlenecks.
- Detail the solutions you implemented and how you engaged your team throughout the process.
- Quantify the results in terms of efficiency gains, cost savings, or other relevant metrics.
What not to say
- Focusing solely on the technical aspects without discussing leadership or team involvement.
- Neglecting to mention the impact of your actions on the organization.
- Providing vague results without specific metrics or outcomes.
- Overlooking challenges faced and how you overcame them.
Example answer
“At Tata Steel, I led a project to streamline the steel production process. We identified delays caused by equipment maintenance and restructured the scheduling system. By implementing predictive maintenance and optimizing workflows, we reduced production downtime by 30%, resulting in a cost savings of approximately $500,000 annually. This project not only improved efficiency but also boosted team morale as everyone saw the tangible results of our efforts.”
Skills tested
Question type
4.2. How do you approach balancing quality control with production efficiency in manufacturing?
Introduction
This question evaluates your strategic thinking and ability to optimize both quality and efficiency, which is crucial for a Lead Industrial Engineer in manufacturing settings.
How to answer
- Discuss the importance of both quality control and efficiency in manufacturing.
- Explain your approach to integrating quality checks without slowing down production.
- Share specific methods or tools you have used to monitor and improve quality while maintaining efficiency.
- Provide examples of how you have successfully implemented this balance in past roles.
- Highlight the role of team training and communication in achieving this balance.
What not to say
- Implying that quality is secondary to efficiency.
- Providing examples where quality was compromised for the sake of speed.
- Failing to mention the importance of continuous improvement.
- Neglecting to discuss team involvement and collaboration.
Example answer
“In my role at Mahindra, I implemented a quality management system that integrated real-time monitoring into our production line. By using Six Sigma methodologies, we reduced defects by 20% while increasing throughput by 15%. This was achieved through regular team training and fostering a culture of quality awareness. I believe that when quality is embedded in the production process, efficiency naturally follows.”
Skills tested
Question type
5. Principal Industrial Engineer Interview Questions and Answers
5.1. Can you describe a time when you implemented a process improvement that resulted in significant cost savings?
Introduction
This question is crucial for a Principal Industrial Engineer as it assesses your ability to identify inefficiencies and implement effective solutions that have a measurable impact on the organization.
How to answer
- Use the STAR method (Situation, Task, Action, Result) to structure your response.
- Clearly outline the initial situation and the specific challenges faced.
- Detail the process improvement strategy you implemented, highlighting your role in the initiative.
- Quantify the cost savings achieved as a result of your actions.
- Reflect on the broader impact of the improvement on the organization and any lessons learned.
What not to say
- Failing to provide concrete numbers or metrics related to the cost savings.
- Taking sole credit for team-based efforts without acknowledging collaboration.
- Describing a process improvement that did not yield any measurable results.
- Being vague about your specific actions or involvement in the project.
Example answer
“At Siemens, I identified that our assembly line had a bottleneck causing delays and increased labor costs. After analyzing the workflow, I proposed a reconfiguration of the layout and introduced lean principles, which reduced assembly time by 30%. This change saved the company approximately €200,000 annually. The experience taught me the importance of continuous process evaluation.”
Skills tested
Question type
5.2. How do you approach cross-functional collaboration in engineering projects?
Introduction
This question evaluates your teamwork and communication skills, which are essential for a Principal Industrial Engineer who often needs to liaise with various departments.
How to answer
- Explain your strategy for fostering collaboration across different teams.
- Provide examples of successful cross-functional projects you've led.
- Discuss how you handle conflicts or differences in priorities among teams.
- Highlight your communication methods to ensure alignment and understanding.
- Mention any tools or techniques you use to facilitate collaboration.
What not to say
- Implying that collaboration is not important or necessary.
- Failing to provide specific examples of collaboration.
- Being negative about past experiences with teamwork.
- Suggesting that you work independently without engaging others.
Example answer
“In my role at Bosch, I led a project that required collaboration between the engineering, quality, and supply chain teams. I organized regular cross-departmental meetings to ensure everyone was aligned on goals and timelines. When conflicts arose, I facilitated discussions to find common ground. This collaborative approach not only helped us meet our deadlines but also improved our product quality significantly.”
Skills tested
Question type
6. Industrial Engineering Manager Interview Questions and Answers
6.1. Can you describe a time when you optimized a manufacturing process? What steps did you take to achieve this?
Introduction
This question is crucial for assessing your practical experience in process optimization, which is a core responsibility for an Industrial Engineering Manager.
How to answer
- Use the STAR method to structure your answer: Situation, Task, Action, Result.
- Clearly describe the initial state of the manufacturing process and the specific inefficiencies identified.
- Detail the analysis methods you used (e.g., Six Sigma, Lean methodologies) to identify areas for improvement.
- Explain the steps you took to implement changes, including team involvement and any tools or technologies used.
- Quantify the results, such as reduced cycle time or increased throughput, to illustrate the impact of your actions.
What not to say
- Focusing on problems without discussing your solutions.
- Neglecting to mention collaboration with team members or other departments.
- Using vague metrics or failing to quantify the outcomes.
- Not addressing any challenges faced during the optimization process.
Example answer
“At a manufacturing plant in Mexico, I identified that our assembly line was experiencing significant delays, impacting our delivery times. I led a team to conduct a root-cause analysis using Lean principles, which revealed bottlenecks in the workflow. We restructured the line layout, implemented standardized work procedures, and provided training to our operators. As a result, we improved our production efficiency by 30% and reduced lead times by two days, greatly enhancing customer satisfaction.”
Skills tested
Question type
6.2. How do you handle conflicts or disagreements within your engineering team?
Introduction
This question evaluates your leadership and conflict resolution skills, which are essential for managing a diverse team in a technical environment.
How to answer
- Describe your approach to understanding both sides of a conflict.
- Detail how you facilitate open communication to resolve issues.
- Explain any frameworks or techniques you use to mediate disagreements.
- Share an example of a conflict you resolved and the positive outcome that resulted.
- Highlight the importance of maintaining team cohesion and morale.
What not to say
- Claiming to avoid conflicts or not addressing them directly.
- Suggesting that conflicts are solely the responsibility of those involved.
- Failing to provide a specific example or resolution strategy.
- Overemphasizing authority rather than collaboration in resolving the conflict.
Example answer
“In my previous role, I encountered a disagreement between two engineers regarding the best approach to a project. I facilitated a meeting where both could voice their opinions and concerns. By encouraging a collaborative discussion, we explored the merits of each approach and ultimately devised a hybrid solution that incorporated elements from both sides. This not only resolved the conflict but also fostered a sense of teamwork and respect among the engineers, leading to a successful project outcome.”
Skills tested
Question type
7. Director of Industrial Engineering Interview Questions and Answers
7.1. Can you describe a project where you optimized a manufacturing process? What approach did you take?
Introduction
This question is crucial for evaluating your ability to analyze and improve manufacturing processes, a key responsibility for a Director of Industrial Engineering.
How to answer
- Start with a brief overview of the project and its objectives.
- Explain the initial challenges or inefficiencies you identified.
- Describe the methodologies you utilized, such as Lean, Six Sigma, or Kaizen.
- Detail your role in leading the team and implementing changes.
- Share measurable outcomes, such as cost savings, efficiency improvements, or quality enhancements.
What not to say
- Providing vague descriptions without specific methodologies.
- Focusing solely on the technical aspects without mentioning team collaboration.
- Neglecting to mention the impact on stakeholders or the business.
- Failing to quantify results or improvements.
Example answer
“At Bosch, I led a project to optimize our assembly line for electric motors. We identified bottlenecks using value stream mapping and implemented Lean principles to streamline workflows. By reorganizing station layouts and reducing cycle times, we achieved a 30% increase in productivity and a 20% reduction in waste, significantly impacting our bottom line.”
Skills tested
Question type
7.2. How do you ensure continuous improvement within your engineering teams?
Introduction
This question assesses your commitment to fostering a culture of continuous improvement, which is vital for enhancing productivity and innovation in industrial engineering.
How to answer
- Discuss your strategies for encouraging feedback and knowledge sharing.
- Explain how you implement regular training and development opportunities.
- Describe how you integrate performance metrics and KPIs into team processes.
- Share examples of successful initiatives you've led to promote continuous improvement.
- Highlight the importance of celebrating successes and learning from failures.
What not to say
- Indicating that continuous improvement is not a priority for your team.
- Failing to provide specific examples of initiatives or programs.
- Neglecting to mention employee engagement or motivation.
- Avoiding discussions about metrics or performance indicators.
Example answer
“At Siemens, I established a quarterly review process to assess project outcomes and identify areas for improvement. I encouraged team members to suggest innovations, leading to a 'best ideas' forum. One initiative reduced our defect rate by 15% through better training and revised protocols. Celebrating these successes built momentum for ongoing improvement.”
Skills tested
Question type
Similar Interview Questions and Sample Answers
Simple pricing, powerful features
Upgrade to Himalayas Plus and turbocharge your job search.
Himalayas
Himalayas Plus
Himalayas Max
Find your dream job
Sign up now and join over 100,000 remote workers who receive personalized job alerts, curated job matches, and more for free!
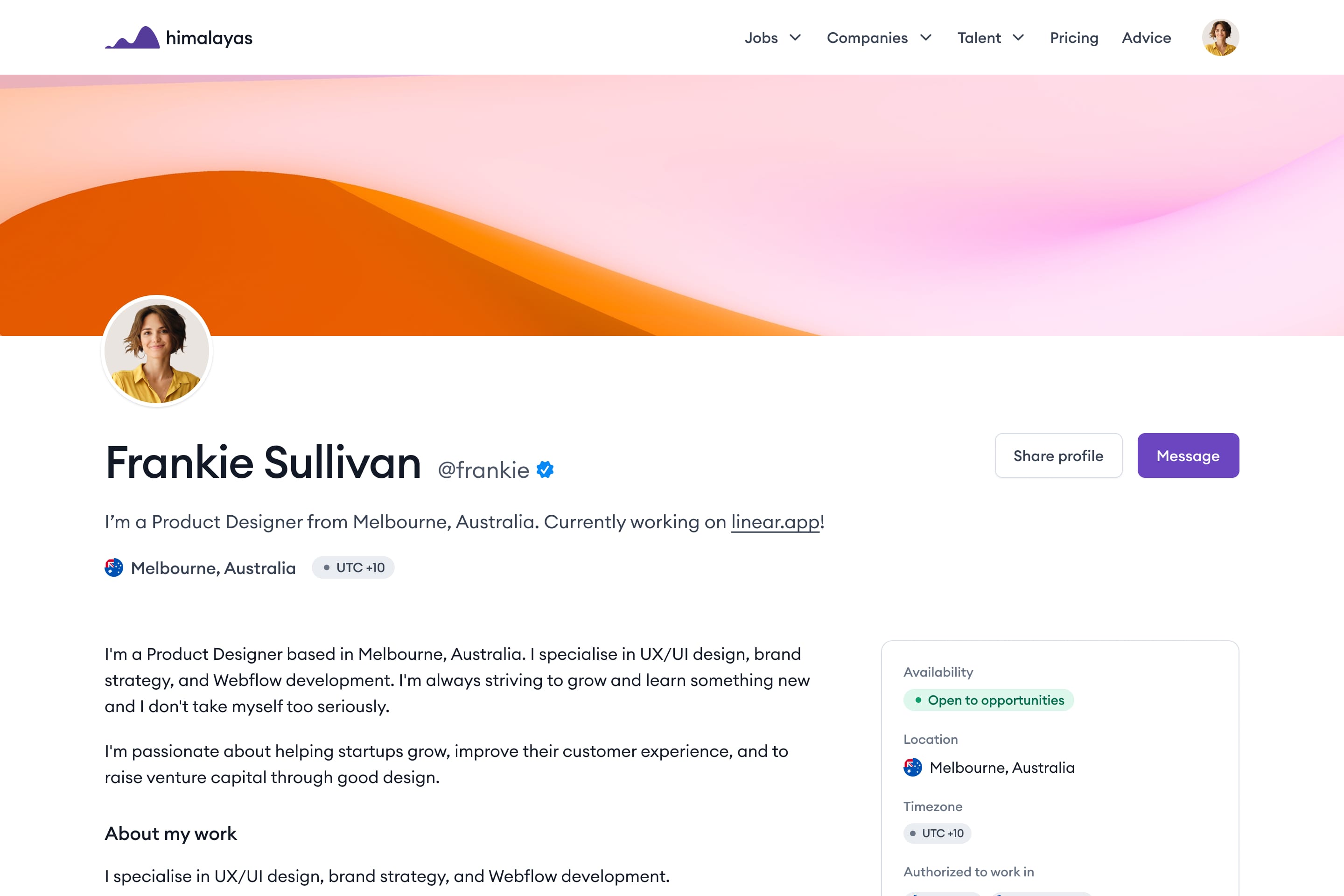