5 Electronic Assembler Interview Questions and Answers
Electronic Assemblers are responsible for assembling and testing electronic components, devices, and systems. They work with circuit boards, wiring, and other electronic parts to ensure proper functionality and quality. Junior roles focus on basic assembly tasks and learning processes, while senior and lead roles involve overseeing assembly operations, troubleshooting complex issues, and mentoring team members. Need to practice for an interview? Try our AI interview practice for free then unlock unlimited access for just $9/month.
Unlimited interview practice for $9 / month
Improve your confidence with an AI mock interviewer.
No credit card required
1. Junior Electronic Assembler Interview Questions and Answers
1.1. Can you describe a time when you had to troubleshoot a problem with an electronic assembly?
Introduction
This question is important for assessing your problem-solving skills and technical knowledge, which are crucial for a Junior Electronic Assembler.
How to answer
- Use the STAR method to structure your response: Situation, Task, Action, Result.
- Clearly explain the context of the assembly issue you encountered.
- Detail the steps you took to diagnose and troubleshoot the problem.
- Highlight any tools or techniques you used during the troubleshooting process.
- Discuss the outcome and what you learned from the experience.
What not to say
- Avoid vague descriptions without specific details of the problem.
- Don't focus solely on the negative outcome; emphasize what you learned.
- Refrain from blaming others; take ownership of your role in the situation.
- Do not neglect to mention any teamwork involved in resolving the issue.
Example answer
“While working on a PCB assembly at a local electronics company, I noticed that a batch of boards was not powering up. I systematically checked each component, using a multimeter to identify a faulty capacitor. After replacing it, the boards functioned correctly. This experience taught me the importance of methodical troubleshooting and reinforced my attention to detail.”
Skills tested
Question type
1.2. What safety procedures do you follow when working with electronic assemblies?
Introduction
This question evaluates your understanding of safety protocols, which is critical in electronic assembly to prevent accidents and ensure a safe working environment.
How to answer
- List specific safety procedures you follow, such as wearing PPE (Personal Protective Equipment).
- Explain the importance of grounding and anti-static measures.
- Discuss how you ensure a clean and organized workspace.
- Mention any training you have received related to safety in electronic assembly.
- Describe how you would handle an emergency situation.
What not to say
- Avoid generic statements about safety; provide specific examples.
- Don't underestimate the importance of safety procedures.
- Refrain from claiming to know everything; acknowledge that you are always learning.
- Do not ignore potential hazards in the workplace.
Example answer
“In my previous role, I adhered to strict safety protocols, including wearing gloves and safety glasses while handling components. I always ensured my workstation was organized to avoid hazards, and I regularly checked that my tools were in good condition. Additionally, I completed a safety training course that covered emergency procedures, so I feel prepared to respond effectively if needed.”
Skills tested
Question type
2. Electronic Assembler Interview Questions and Answers
2.1. Can you describe your experience with soldering and assembly techniques for electronic components?
Introduction
This question is crucial for assessing your technical skills and familiarity with the tools and processes used in electronic assembly, which are fundamental for this role.
How to answer
- Start by outlining your formal training or certifications in soldering and electronics assembly.
- Provide specific examples of projects or tasks where you applied these skills.
- Mention the types of components you have worked with, such as surface mount devices (SMD) or through-hole components.
- Discuss any quality control measures you implemented or followed during assembly.
- If applicable, share any experiences with troubleshooting or repairing assembled products.
What not to say
- Avoid giving vague answers without specific examples.
- Don't exaggerate your abilities; be honest about your experience level.
- Refrain from discussing unrelated skills that do not pertain to electronic assembly.
- Avoid technical jargon without explaining what it means, as it may confuse non-technical interviewers.
Example answer
“In my previous role at a local electronics manufacturer, I was responsible for assembling circuit boards using both manual soldering and reflow soldering techniques. I worked extensively with SMD components, ensuring that each assembly met the required quality standards. I implemented a thorough inspection process, which helped reduce defects by 15%. My experience has taught me the importance of precision and attention to detail in electronics assembly.”
Skills tested
Question type
2.2. Describe a time when you faced a challenge during the assembly process and how you resolved it.
Introduction
This question evaluates your problem-solving skills and ability to work under pressure, both of which are essential in a fast-paced assembly environment.
How to answer
- Use the STAR method to clearly outline the situation, task, action, and result.
- Describe the specific challenge you encountered, such as a misalignment of components or equipment failure.
- Explain the steps you took to diagnose and fix the issue.
- Highlight any collaboration with team members or supervisors during the resolution process.
- Share the positive outcome and what you learned from the experience.
What not to say
- Avoid blaming others for the challenge without taking responsibility.
- Do not provide overly simplistic solutions that lack depth.
- Refrain from describing a situation where you did not take action or learn from the experience.
- Avoid vague answers that do not detail your specific contributions.
Example answer
“At my last job at a consumer electronics company, we encountered a critical issue where the assembly line was producing a high number of defective units due to incorrect soldering. I took the initiative to investigate the root cause and discovered that a specific soldering tool was malfunctioning. I coordinated with the maintenance team to repair the tool and retrained the assembly team on proper soldering techniques. As a result, we reduced defects by 30% and improved our production efficiency significantly. This experience reinforced the importance of proactive problem-solving in assembly.”
Skills tested
Question type
3. Senior Electronic Assembler Interview Questions and Answers
3.1. Can you describe a complex electronic assembly project you worked on and the challenges you faced?
Introduction
This question evaluates your technical expertise and problem-solving skills, both of which are critical for a Senior Electronic Assembler role.
How to answer
- Use the STAR method to structure your response (Situation, Task, Action, Result)
- Clearly outline the project and its specific requirements
- Detail the challenges encountered, including technical difficulties or time constraints
- Explain the steps you took to overcome these challenges
- Quantify the results or improvements made as a result of your actions
What not to say
- Providing vague descriptions without specifics about the project or challenges
- Focusing too much on problems without discussing solutions
- Neglecting to mention teamwork or collaboration if applicable
- Omitting any measurable outcomes from your actions
Example answer
“In my previous position at Siemens in Australia, I was tasked with assembling a complex communication device. We faced a tight deadline and issues with component sourcing. I coordinated with suppliers to expedite delivery and reorganized our assembly line to optimize workflow. Ultimately, we completed the project two weeks early, improving our team's efficiency by 20%.”
Skills tested
Question type
3.2. How do you ensure quality control in your assembly work?
Introduction
This question assesses your understanding of quality assurance processes, which are vital in electronic assembly to prevent defects.
How to answer
- Explain your methods for ensuring quality at each step of the assembly process
- Discuss any tools or technologies you use for testing and inspection
- Mention your experience with quality standards (like ISO 9001)
- Describe a specific instance where your attention to quality prevented a potential issue
- Highlight your commitment to continuous improvement in quality control
What not to say
- Implying that quality control is the responsibility of others
- Failing to mention specific techniques or tools used for quality assurance
- Giving a generic answer without concrete examples
- Neglecting to demonstrate an understanding of industry standards
Example answer
“I implement a thorough quality control process by conducting visual inspections and functional tests at each stage of assembly. At my last job with Schneider Electric, I identified a soldering issue during a routine inspection that could have led to product failure. By addressing it immediately, we saved the company significant costs on returns and repairs. I also advocate for regular team training on quality standards.”
Skills tested
Question type
4. Lead Electronic Assembler Interview Questions and Answers
4.1. Can you describe a time when you encountered a significant issue during the assembly process, and how you resolved it?
Introduction
This question is important as it evaluates your problem-solving skills, technical knowledge, and ability to maintain quality control during the assembly process.
How to answer
- Use the STAR method (Situation, Task, Action, Result) to structure your response.
- Clearly outline the specific issue you faced and its potential impact on production.
- Describe the steps you took to diagnose and fix the problem, highlighting your technical skills.
- Emphasize collaboration with team members or departments if applicable.
- Quantify the results or improvements that came from your solution.
What not to say
- Focusing solely on the technical aspects without mentioning the resolution process.
- Blaming others for the issue instead of taking responsibility.
- Neglecting to discuss what you learned from the experience.
- Providing a vague answer without specific details or outcomes.
Example answer
“During my time at Embraer, we encountered a major issue where solder joints were failing quality inspection. I led a team to investigate the root cause, which we identified as a calibration error in our soldering equipment. I coordinated with the quality assurance team to recalibrate the machines and retrain staff on proper techniques. As a result, we reduced defects by 30% within a month, which significantly improved our production efficiency.”
Skills tested
Question type
4.2. How do you ensure that you are adhering to safety protocols while assembling electronic components?
Introduction
This question assesses your commitment to safety standards and your ability to implement best practices in a manufacturing environment, which is crucial in the electronics industry.
How to answer
- Discuss your understanding of safety protocols relevant to electronic assembly.
- Explain how you stay updated with safety regulations and training.
- Provide examples of how you promote safety within your team.
- Highlight any past experiences where you identified potential safety risks and acted on them.
- Mention any certifications or training you have completed related to workplace safety.
What not to say
- Suggesting that safety protocols are not a priority.
- Failing to provide specific examples of safety practices.
- Ignoring the importance of team training on safety protocols.
- Mentioning incidents without discussing preventative measures.
Example answer
“At Flex, I prioritize safety by strictly adhering to OSHA regulations and participating in regular safety training. I conduct daily safety checks before starting work and encourage my team to report any hazards. For instance, when I noticed a colleague not using proper PPE while working with soldering tools, I addressed it immediately and organized a refresher training. This proactive approach has fostered a culture of safety within our team.”
Skills tested
Question type
5. Electronic Assembly Supervisor Interview Questions and Answers
5.1. Can you describe a time when you improved a production process in your assembly line?
Introduction
This question is crucial for understanding your ability to identify inefficiencies and implement effective changes to enhance productivity and quality in electronic assembly.
How to answer
- Use the STAR method to structure your response: Situation, Task, Action, Result.
- Clearly outline the specific production process that needed improvement.
- Discuss the steps you took to analyze the process and identify areas for improvement.
- Explain the changes you implemented and how you involved your team in the process.
- Quantify the results, such as increased efficiency or reduced error rates.
What not to say
- Focusing on minor adjustments that had little impact.
- Not mentioning teamwork or collaboration with other departments.
- Avoiding specifics about how you measured success.
- Blaming others for inefficiencies without taking responsibility.
Example answer
“At my previous job with Siemens, I noticed that our soldering process was causing a 15% defect rate. I led a team to analyze the workflow, and we implemented a new training protocol for operators and introduced a quality check after each stage. As a result, we reduced defects to 5% within three months, significantly improving overall production quality.”
Skills tested
Question type
5.2. How do you ensure that safety protocols are followed in your assembly line?
Introduction
This question assesses your commitment to workplace safety, a critical aspect of supervising an electronic assembly team.
How to answer
- Explain your approach to training employees on safety protocols.
- Discuss how you monitor compliance and address violations.
- Share examples of how you foster a safety-first culture within your team.
- Highlight any safety metrics you track and improvements made over time.
- Describe how you involve team members in safety discussions and updates.
What not to say
- Suggesting safety is not a priority in production.
- Failing to provide concrete examples of safety measures.
- Ignoring the importance of employee engagement in safety.
- Mentioning that safety protocols are only enforced after incidents.
Example answer
“In my role at Foxconn, I prioritized safety by implementing a comprehensive training program for all new hires and regular refresher courses for existing staff. I also established a monthly safety meeting where team members could voice concerns and suggest improvements. This proactive approach led to a 30% reduction in workplace accidents over the year.”
Skills tested
Question type
Similar Interview Questions and Sample Answers
Simple pricing, powerful features
Upgrade to Himalayas Plus and turbocharge your job search.
Himalayas
Himalayas Plus
Himalayas Max
Find your dream job
Sign up now and join over 100,000 remote workers who receive personalized job alerts, curated job matches, and more for free!
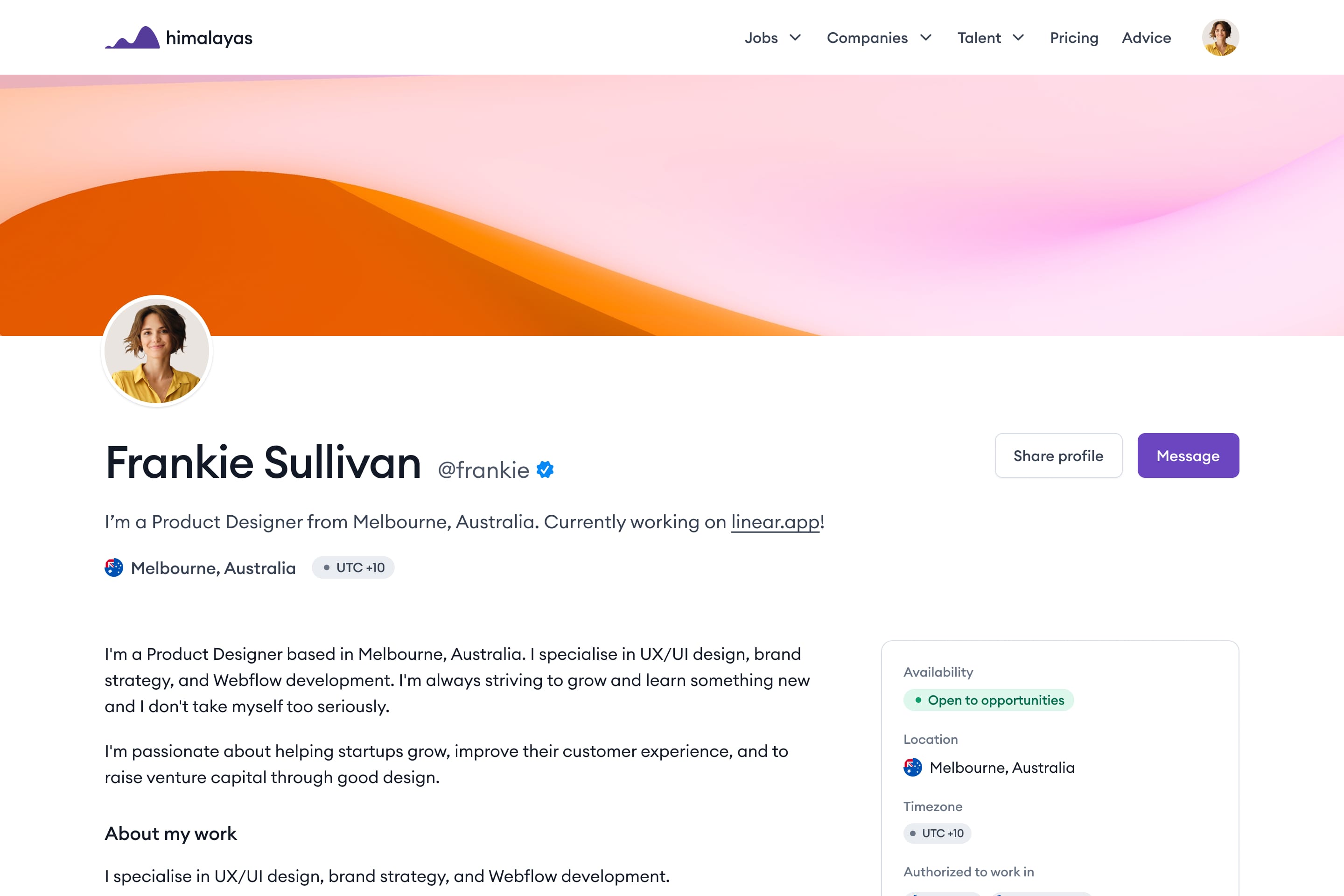