5 Bag Machine Adjuster Interview Questions and Answers
Bag Machine Adjusters are responsible for setting up, maintaining, and troubleshooting bag-making machines to ensure efficient production. They monitor machine performance, make necessary adjustments, and perform routine maintenance to minimize downtime. Junior roles focus on learning machine operations and assisting with adjustments, while senior and lead roles involve overseeing machine performance, training team members, and ensuring production quality standards are met. Need to practice for an interview? Try our AI interview practice for free then unlock unlimited access for just $9/month.
Unlimited interview practice for $9 / month
Improve your confidence with an AI mock interviewer.
No credit card required
1. Junior Bag Machine Adjuster Interview Questions and Answers
1.1. Can you describe a situation where you had to troubleshoot a malfunctioning bag machine?
Introduction
This question is crucial for understanding your problem-solving skills and technical knowledge, which are essential for a Junior Bag Machine Adjuster role.
How to answer
- Use the STAR method to outline your response clearly
- Describe the specific issue you encountered with the machine
- Explain the steps you took to diagnose the problem
- Detail the solution you implemented and its effectiveness
- Emphasize any safety protocols you followed during troubleshooting
What not to say
- Focusing only on the problem without discussing the solution
- Failing to mention safety considerations
- Providing vague answers without specific details
- Claiming to have never encountered any issues
Example answer
“At my previous position at a local packaging company, I noticed our bag machine was consistently jamming. I examined the feed area and found an accumulation of debris obstructing the flow. After cleaning the area and adjusting the tension settings, the machine operated smoothly again. This experience reinforced my attention to detail and the importance of routine maintenance.”
Skills tested
Question type
1.2. What steps do you take to ensure quality control when operating a bag machine?
Introduction
This question assesses your understanding of quality assurance processes and your commitment to producing high-quality products.
How to answer
- Outline a systematic approach to quality checks during machine operation
- Mention specific quality metrics you monitor
- Discuss how you document your findings and any discrepancies
- Emphasize the importance of adhering to company standards
- Describe how you communicate quality issues to your supervisor
What not to say
- Neglecting to mention specific quality checks
- Claiming to rely solely on the machine's automatic systems
- Overlooking the importance of teamwork in quality control
- Failing to describe how you address quality issues
Example answer
“When operating the bag machine, I implement a quality control checklist that includes checking the bag dimensions, seal integrity, and print quality at regular intervals. I document any discrepancies and promptly report them to my supervisor. By ensuring adherence to these standards, I help maintain our reputation for high-quality products, as seen at my previous job at a local manufacturer.”
Skills tested
Question type
2. Bag Machine Adjuster Interview Questions and Answers
2.1. Can you describe your experience with adjusting bag-making machinery to optimize production?
Introduction
This question is crucial for assessing your technical expertise and hands-on experience with bag-making machinery, which is essential for a Bag Machine Adjuster.
How to answer
- Begin with a brief overview of your experience in operating and adjusting bag-making machines.
- Detail specific machinery you have worked with, such as automated bag-making machines or related equipment.
- Explain a situation where you identified a production issue and how you adjusted the machine to resolve it.
- Include any metrics or improvements achieved as a result of your adjustments.
- Mention any relevant training or certifications in machinery operation or maintenance.
What not to say
- Providing vague descriptions of your experience without specific examples.
- Claiming experience with equipment you are unfamiliar with.
- Neglecting to discuss the impact of your adjustments on production quality or efficiency.
- Failing to emphasize teamwork or collaboration with other operators or maintenance staff.
Example answer
“In my previous role at AEP Industries, I worked extensively with the Windmoeller & Hoelscher bag-making machines. I once noticed a decline in production speed due to misalignment. By carefully recalibrating the feed rollers and adjusting the tension settings, I improved the production rate by 20% while maintaining quality standards. This hands-on experience taught me the importance of attention to detail and proactive problem-solving in machine operation.”
Skills tested
Question type
2.2. Describe a time when you worked as part of a team to troubleshoot a malfunctioning bag machine.
Introduction
This question evaluates your teamwork and collaboration skills, which are vital when addressing machinery issues that require input from multiple team members.
How to answer
- Use the STAR method to structure your response.
- Describe the malfunction and how it impacted production.
- Explain your role in the team and how you communicated with others.
- Detail the troubleshooting steps taken and any adjustments made.
- Share the outcome and what you learned from the experience.
What not to say
- Taking sole credit for the team's success.
- Focusing only on technical details without mentioning collaboration.
- Blaming others for the malfunction without discussing your contributions.
- Failing to articulate lessons learned or improvements for future situations.
Example answer
“At my last job with Novolex, our bag-making machine experienced an unexpected shutdown during a critical production run. I collaborated with two other operators and our maintenance technician. We quickly assessed the control panel and identified a blown fuse. I communicated the issue to my team, and we coordinated to replace the fuse while keeping production running on a secondary machine. This teamwork not only minimized downtime but also reinforced the importance of clear communication in crisis situations.”
Skills tested
Question type
3. Senior Bag Machine Adjuster Interview Questions and Answers
3.1. Can you describe a time when you identified a mechanical issue with a bag machine and how you resolved it?
Introduction
This question is vital for assessing your technical troubleshooting skills and your ability to work under pressure in a manufacturing environment.
How to answer
- Use the STAR method to structure your response: Situation, Task, Action, Result.
- Clearly describe the mechanical issue you encountered and its impact on production.
- Explain the steps you took to diagnose the problem.
- Detail the solution you implemented and any adjustments made to prevent future issues.
- Quantify the results, such as reduced downtime or increased efficiency.
What not to say
- Failing to explain the specific mechanical issue or its impact.
- Not showcasing your problem-solving process.
- Taking sole credit without acknowledging team contributions.
- Being vague about the results or outcomes of your actions.
Example answer
“At a packaging facility in Toronto, I noticed our bag machine frequently jammed, causing a 20% drop in output. I conducted a thorough inspection and identified a misaligned conveyor belt as the culprit. After realigning it and adjusting the tension settings, I monitored the machine for a week, which led to a 50% reduction in jams and restored our production efficiency. This experience reinforced my commitment to proactive maintenance.”
Skills tested
Question type
3.2. How do you ensure that the machines you adjust are consistently operating at optimal performance?
Introduction
Understanding your approach to maintenance and performance optimization is crucial for ensuring quality output in a manufacturing setting.
How to answer
- Discuss your routine maintenance practices and their importance.
- Mention any specific performance metrics you monitor.
- Explain how you train or guide team members in machine operation.
- Describe any tools or technology you utilize for monitoring performance.
- Share examples of how your practices have led to improved output or efficiency.
What not to say
- Implying that maintenance is solely the responsibility of another team.
- Not referencing any specific metrics or tools.
- Overlooking the importance of training and collaboration with colleagues.
- Failing to mention any proactive measures taken.
Example answer
“To ensure optimal performance of the bag machines, I implement a strict maintenance schedule that includes daily checks and monthly overhauls. I monitor metrics such as output rate and error frequency, making adjustments as needed. Additionally, I hold weekly training sessions for the team to ensure everyone is aware of best practices. For instance, this proactive approach helped us increase machine efficiency by 30% over the last quarter.”
Skills tested
Question type
4. Lead Bag Machine Adjuster Interview Questions and Answers
4.1. Can you describe a time when you had to troubleshoot a significant issue with a bag machine during production?
Introduction
This question is critical as it assesses your technical troubleshooting skills and your ability to maintain production efficiency, which is central to the role of a Lead Bag Machine Adjuster.
How to answer
- Start by outlining the specific issue you encountered with the bag machine and its impact on production.
- Explain the steps you took to troubleshoot the problem, including any diagnostic tools or methods used.
- Discuss how you collaborated with your team or other departments to resolve the issue.
- Highlight the outcome, focusing on how your actions minimized downtime and maintained production quality.
- Mention any lessons learned that improved your future troubleshooting processes.
What not to say
- Describing a situation without clearly defining the problem or its impact.
- Focusing solely on technical details without mentioning teamwork or collaboration.
- Failing to provide a resolution or outcome resulting from your troubleshooting efforts.
- Avoiding discussion of any mistakes made during the process.
Example answer
“At my previous job with a packaging company, we experienced a sudden malfunction in the bag machine that halted production. I quickly identified that the sensor was misaligned. After adjusting it and recalibrating the machine, I collaborated with the maintenance team to ensure all components were functioning correctly. As a result, we were able to resume production within an hour, ultimately reducing potential losses significantly. This experience reinforced the importance of quick thinking and teamwork in troubleshooting.”
Skills tested
Question type
4.2. How do you ensure that bag machines are properly set up and calibrated before production runs?
Introduction
This question evaluates your understanding of machine setup and maintenance, which is vital for ensuring quality and efficiency in production.
How to answer
- Describe your standard operating procedures for machine setup and calibration.
- Explain the importance of each step in the setup process and how it impacts production quality.
- Discuss any specific tools or software you use for calibration.
- Share an example of how you identified and corrected a setup error in the past.
- Mention any training or knowledge you provide to your team about machine setup.
What not to say
- Suggesting that setup is a minor part of the production process.
- Failing to outline a clear procedure or approach to machine calibration.
- Neglecting to mention the importance of quality control in setup.
- Not acknowledging the role of team training in ensuring proper setup.
Example answer
“Before each production run at XYZ Packaging, I follow a checklist that includes verifying the machine's alignment, checking the calibration settings, and inspecting the quality of input materials. I use specialized software to ensure precise settings. Last month, I discovered a calibration error that could have affected product quality. By correcting it before production started, we maintained our quality standards. I also routinely conduct training sessions for my team to ensure everyone is up to speed on best practices.”
Skills tested
Question type
5. Bag Machine Maintenance Specialist Interview Questions and Answers
5.1. Can you describe a time when you diagnosed and resolved a critical failure in a bag-making machine?
Introduction
This question assesses your technical troubleshooting skills and ability to maintain machine functionality, which are vital for a Bag Machine Maintenance Specialist.
How to answer
- Use the STAR method to structure your response (Situation, Task, Action, Result)
- Clearly outline the specific failure you encountered and its impact on production
- Describe the diagnostic steps you took to identify the root cause
- Explain the solution you implemented to fix the issue
- Share the results and how you ensured the machine was back to optimal performance
What not to say
- Focusing solely on theoretical knowledge without practical experience
- Neglecting to mention the importance of safety protocols
- Failing to quantify the impact of the failure or your solution
- Blaming others for the failure instead of taking responsibility
Example answer
“In my previous role at a packaging plant, I encountered a sudden stoppage in one of our bag-making machines. I quickly assessed the situation and discovered that a critical sensor had failed. After replacing the sensor and recalibrating the system, I conducted tests to ensure everything was functioning correctly. This not only minimized downtime but also improved the machine's efficiency by 15%.”
Skills tested
Question type
5.2. How do you prioritize maintenance tasks when managing multiple machines in a facility?
Introduction
This question evaluates your organizational skills and ability to manage time effectively in a maintenance environment.
How to answer
- Discuss your approach to assessing machine conditions and prioritizing based on urgency
- Explain any frameworks or tools you use for maintenance scheduling
- Highlight how you communicate with production teams to align priorities
- Mention the importance of preventive maintenance and how it fits into your strategy
- Describe how you handle unexpected breakdowns while maintaining scheduled tasks
What not to say
- Suggesting that all machines should receive equal attention regardless of their condition
- Ignoring the role of communication with other departments
- Failing to mention the importance of preventive measures
- Not providing examples of managing competing priorities
Example answer
“At my previous job at a textile manufacturing facility, I prioritized maintenance tasks by assessing the machines' operational status and any reported issues. I used a computerized maintenance management system (CMMS) to track and schedule tasks, balancing urgent repairs with preventive maintenance. This structured approach helped reduce our machine downtime by 20% over six months, allowing for smoother operations.”
Skills tested
Question type
Similar Interview Questions and Sample Answers
Simple pricing, powerful features
Upgrade to Himalayas Plus and turbocharge your job search.
Himalayas
Himalayas Plus
Himalayas Max
Find your dream job
Sign up now and join over 100,000 remote workers who receive personalized job alerts, curated job matches, and more for free!
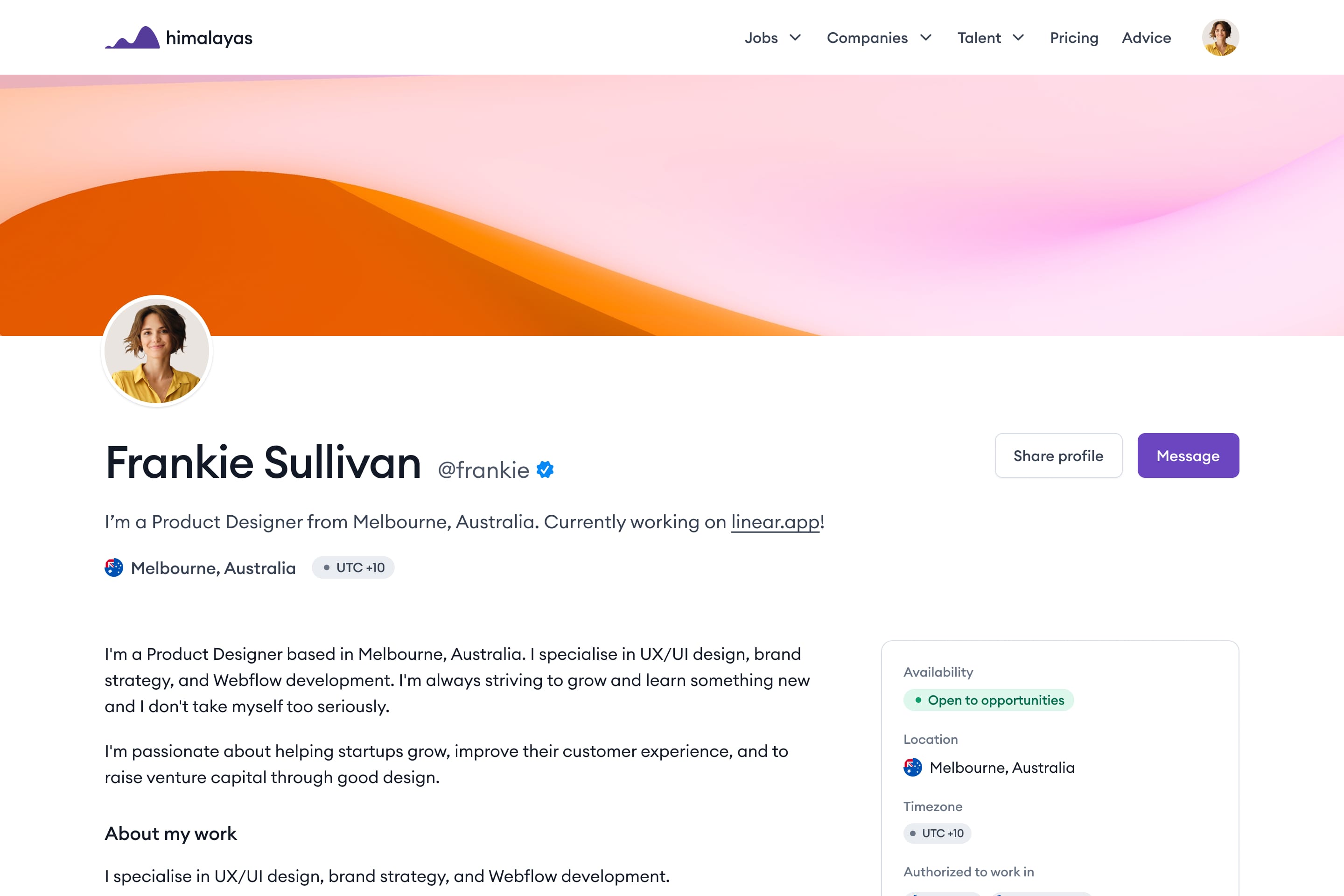