Complete Wire Welder Career Guide
Wire welders are the backbone of modern manufacturing and construction, precisely joining metal components using advanced wire-feed welding processes like MIG and TIG. This specialized skill creates durable structures and products, from automotive frames to industrial machinery, ensuring structural integrity and operational safety. If you enjoy hands-on work that demands precision and offers tangible results, a career as a wire welder provides stable demand and clear pathways for skill advancement.
Key Facts & Statistics
Median Salary
$48,220 USD
(BLS, May 2023)
Range: $35,000 - $70,000+ USD
Growth Outlook
2%
as fast as average (BLS 2022-2032)
Annual Openings
≈40,000
openings annually (BLS)
Top Industries
Typical Education
High school diploma or equivalent, plus vocational training or an apprenticeship; certifications (e.g., AWS) are highly valued
What is a Wire Welder?
A Wire Welder specializes in joining metal components using wire-fed welding processes, primarily MIG (Gas Metal Arc Welding) and Flux-Cored Arc Welding (FCAW). This role focuses on the continuous feeding of a consumable wire electrode into the weld pool, creating strong, durable bonds for various structures and products. Wire welders are essential in industries like manufacturing, construction, automotive, and shipbuilding, where efficient and precise metal fabrication is critical.
Unlike Stick Welders who use coated electrodes that require frequent replacement, Wire Welders benefit from continuous wire feed, which often leads to faster welding speeds and higher productivity. They differ from TIG Welders, who focus on intricate, high-precision welds requiring exceptional skill and often slower processes. The Wire Welder's expertise lies in mastering the balance of wire feed speed, voltage, and gas shielding to produce clean, consistent welds across different material thicknesses and joint configurations.
What does a Wire Welder do?
Key Responsibilities
- Set up and adjust wire welding machines, including power sources, wire feed speed, and gas flow rates, to achieve optimal weld quality.
- Perform various types of wire welding, such as MIG (GMAW) or Flux-Cored (FCAW), on different materials like steel, stainless steel, and aluminum.
- Inspect workpieces for defects like porosity, cracks, or insufficient penetration, making adjustments to technique or machine settings as needed.
- Clean and prepare metal surfaces by grinding, sanding, or chemical cleaning to ensure strong, contaminant-free welds.
- Read and interpret blueprints, welding symbols, and schematics to determine the precise specifications and dimensions for each welding project.
- Operate grinding equipment, saws, and other fabrication tools to cut, shape, and finish metal components before and after welding.
- Maintain welding equipment, perform routine checks, and troubleshoot minor issues to ensure consistent operation and extend machine lifespan.
Work Environment
Wire welders typically work in manufacturing plants, fabrication shops, construction sites, or shipyards. The environment often involves exposure to loud noises from machinery, sparks, fumes, and heat, necessitating strict adherence to safety protocols. Work typically involves standing for long periods, bending, and lifting heavy materials.
Collaboration with other fabricators, fitters, and engineers is common to ensure project specifications are met. The work pace can be fast-paced, especially when meeting production deadlines, but it also requires meticulous attention to detail and precision. Shift work may be necessary, and while most roles are on-site, some specialized welders might travel for specific projects or field repairs.
Tools & Technologies
Wire welders primarily use MIG (Gas Metal Arc Welding) and Flux-Cored Arc Welding (FCAW) machines, which are central to their daily tasks. They also operate grinding wheels, angle grinders, plasma cutters, and oxy-acetylene torches for material preparation and finishing. Essential personal protective equipment includes welding helmets, gloves, safety glasses, and flame-resistant clothing.
Measurement tools like calipers, micrometers, and tape measures are crucial for ensuring precise dimensions. They frequently use hand tools such as hammers, chisels, and clamps for fitting and securing workpieces. Knowledge of common metals like carbon steel, stainless steel, and aluminum is also vital for selecting appropriate welding parameters.
Wire Welder Skills & Qualifications
Becoming a successful Wire Welder requires a specific blend of practical skills, safety adherence, and foundational knowledge. Employers prioritize demonstrable welding proficiency and a strong safety record. While formal education is valuable, extensive hands-on experience often holds equal, if not greater, weight in the hiring process, especially for experienced roles.
Requirements for Wire Welders vary significantly based on the industry, company size, and project complexity. For instance, a welder in an aerospace manufacturing facility faces more stringent certification and precision requirements than one in a general fabrication shop. Geographic location also influences demand and specific code adherence. Entry-level positions may accept vocational training and basic certifications, while senior roles demand advanced certifications, specialized process knowledge, and a proven ability to work with various materials and joint configurations. Certifications from organizations like the American Welding Society (AWS) are crucial for validating competence and are often a prerequisite for many jobs.
The skill landscape for Wire Welders is evolving with advancements in automation and robotic welding. However, the demand for skilled manual wire welders remains high, particularly for custom fabrication, repair, and complex assemblies where robots lack the necessary dexterity. Continuous learning in new materials, advanced processes, and updated safety protocols ensures a welder remains competitive. Balancing depth in specific wire welding processes (e.g., MIG, Flux-Cored) with breadth in understanding different material properties enhances a welder's versatility and career progression.
Education Requirements
Technical Skills
- Gas Metal Arc Welding (GMAW/MIG) proficiency, including short-circuit, spray, and pulsed spray transfer modes.
- Flux-Cored Arc Welding (FCAW) proficiency, both gas-shielded and self-shielded processes.
- Ability to read and interpret blueprints, welding symbols, and schematics accurately.
- Proficiency in various welding positions (flat, horizontal, vertical, overhead) for both fillet and groove welds.
- Knowledge of various base metals (carbon steel, stainless steel, aluminum) and appropriate filler metals.
- Setup, adjustment, and maintenance of wire feed welding machines, including voltage, amperage, and wire speed settings.
- Safe operation of grinders, cutting torches, plasma cutters, and other fabrication tools.
- Understanding of weld defects (porosity, undercut, lack of fusion) and corrective actions.
- Proficiency in measuring tools (calipers, tape measures, squares) for accurate fit-up and inspection.
- Adherence to industry welding codes and standards (e.g., AWS D1.1, D1.3, D1.6).
- Basic metallurgy knowledge relevant to welding processes and material behavior.
- Ability to perform pre-weld preparation (cleaning, beveling) and post-weld finishing (grinding, chipping).
Soft Skills
- Attention to Detail: Critical for ensuring weld quality, detecting flaws, and adhering to precise specifications, which directly impacts structural integrity and safety.
- Problem-Solving: Essential for diagnosing issues with equipment, material, or weld quality and implementing effective solutions to maintain productivity and standards.
- Patience and Steadiness: Crucial for maintaining consistent torch angles, travel speeds, and arc length over extended periods to produce high-quality, uniform welds.
- Safety Consciousness: Paramount for adhering to strict safety protocols, using personal protective equipment (PPE), and identifying potential hazards to prevent accidents.
- Adaptability: Important for adjusting to different materials, joint configurations, welding positions, and project requirements, often under varying environmental conditions.
- Work Ethic and Reliability: Necessary for consistent output, meeting production deadlines, and minimizing downtime, which directly contributes to project success.
- Blueprint and Schematic Interpretation: Vital for accurately understanding welding symbols, dimensions, and material specifications before beginning work.
- Manual Dexterity and Hand-Eye Coordination: Fundamental for precise manipulation of the welding torch, maintaining a steady hand, and accurately guiding the wire feed along the joint line to produce clean, strong welds and avoid defects like undercut or excessive spatter. This skill is paramount for consistent bead placement and quality.
How to Become a Wire Welder
Breaking into wire welding, often referred to as MIG welding, offers multiple entry pathways, from formal education to on-the-job training. For a complete beginner, a structured vocational program typically provides the fastest route to foundational skills and certifications within six months to a year. Career changers with related mechanical aptitude might find apprenticeships or entry-level fabrication helper roles effective for hands-on learning.
Geographic location significantly influences opportunities; industrial hubs and manufacturing-heavy regions will have more openings than rural areas. Company size also matters; smaller shops might prioritize immediate skill sets, while larger corporations or unions often prefer certified welders or those from established apprenticeship programs. The timeline to securing a first role can range from three months for highly motivated individuals with prior mechanical experience entering a short program, to two years for those starting from scratch in a comprehensive apprenticeship.
A common misconception is that extensive academic degrees are necessary; practical skills, certifications, and a strong work ethic are far more critical. While formal education provides a solid base, continuous learning and adapting to new welding processes are essential for long-term career growth. Networking within local trade schools, supply houses, and fabrication shops can unveil hidden opportunities and mentorships, accelerating entry into this hands-on field.
Research and select a welding program or apprenticeship that specializes in MIG (GMAW) welding. Look for programs accredited by organizations like the American Welding Society (AWS) or local vocational schools, as they provide essential theoretical knowledge and practical hands-on experience, typically lasting from three months to one year.
Obtain industry-recognized welding certifications, particularly AWS D1.1 Structural Welding Code for Steel. These certifications validate your proficiency to potential employers and demonstrate your ability to meet industry standards, significantly increasing your employability for various fabrication and construction roles.
Develop a portfolio of welding samples that showcase your range and quality of work. Include examples of different joint types (fillet, groove), material thicknesses, and welding positions (flat, horizontal, vertical, overhead), as this visual evidence will be crucial during job interviews to demonstrate your practical skills.
Network with local welding professionals, instructors, and employers by attending career fairs, industry events, or visiting local fabrication shops. Informational interviews and connections can lead to mentorships, job leads, and insights into specific employer needs, opening doors to unadvertised positions.
Prepare a targeted resume highlighting your welding certifications, specific processes mastered (MIG/GMAW), and any project experience from your training or personal work. Practice common interview questions focusing on safety protocols, problem-solving, and your understanding of blueprints and welding symbols to impress potential employers.
Apply for entry-level wire welder, fabrication helper, or apprentice positions at manufacturing plants, construction sites, and repair shops. Tailor your application to each job description, emphasizing how your skills and certifications align with their requirements, and be prepared for a practical welding test as part of the interview process.
Step 1
Research and select a welding program or apprenticeship that specializes in MIG (GMAW) welding. Look for programs accredited by organizations like the American Welding Society (AWS) or local vocational schools, as they provide essential theoretical knowledge and practical hands-on experience, typically lasting from three months to one year.
Step 2
Obtain industry-recognized welding certifications, particularly AWS D1.1 Structural Welding Code for Steel. These certifications validate your proficiency to potential employers and demonstrate your ability to meet industry standards, significantly increasing your employability for various fabrication and construction roles.
Step 3
Develop a portfolio of welding samples that showcase your range and quality of work. Include examples of different joint types (fillet, groove), material thicknesses, and welding positions (flat, horizontal, vertical, overhead), as this visual evidence will be crucial during job interviews to demonstrate your practical skills.
Step 4
Network with local welding professionals, instructors, and employers by attending career fairs, industry events, or visiting local fabrication shops. Informational interviews and connections can lead to mentorships, job leads, and insights into specific employer needs, opening doors to unadvertised positions.
Step 5
Prepare a targeted resume highlighting your welding certifications, specific processes mastered (MIG/GMAW), and any project experience from your training or personal work. Practice common interview questions focusing on safety protocols, problem-solving, and your understanding of blueprints and welding symbols to impress potential employers.
Step 6
Apply for entry-level wire welder, fabrication helper, or apprentice positions at manufacturing plants, construction sites, and repair shops. Tailor your application to each job description, emphasizing how your skills and certifications align with their requirements, and be prepared for a practical welding test as part of the interview process.
Education & Training Needed to Become a Wire Welder
Becoming a proficient Wire Welder typically involves a blend of hands-on training and theoretical knowledge. Unlike roles requiring a four-year degree, the primary pathways are vocational programs, apprenticeships, and specialized certifications. Four-year degrees, which might cost $40,000-$100,000+, are generally not required or beneficial for this specific hands-on trade. In contrast, vocational programs or bootcamps range from $5,000-$15,000, with completion times from 6 weeks to 12 months. Apprenticeships, often lasting 3-5 years, provide paid on-the-job training and classroom instruction, with minimal upfront cost to the apprentice.
Employers highly value practical experience and certifications from recognized bodies like the American Welding Society (AWS). While self-study can build foundational knowledge, it rarely suffices for employment without supervised practical application and certification. The market perception favors candidates with demonstrable skills, often acquired through structured programs or extensive apprenticeship. Continuous learning in advanced techniques or new materials is important for career progression, especially as technology in manufacturing evolves.
Educational needs vary by the specific industry (e.g., automotive, construction, fabrication) and the type of wire welding (e.g., MIG, TIG, Flux-Cored Arc Welding). Companies often prioritize candidates with specific certifications relevant to their operations. The cost-benefit analysis heavily favors vocational training and apprenticeships, as they offer a direct path to employment with a strong return on investment compared to more academic routes. Quality programs often have strong industry connections and job placement services, ensuring graduates meet current industry standards and employer expectations.
Wire Welder Salary & Outlook
Compensation for a Wire Welder varies significantly based on several factors beyond just base pay. Geographic location plays a major role, with higher wages typically found in areas with high industrial demand or a higher cost of living, such as the Northeast or West Coast of the United States. Conversely, regions with lower living costs may offer comparatively lower salaries. International markets also present diverse compensation structures, though the figures provided here are in USD.
Years of experience are crucial for salary progression. An Apprentice Wire Welder earns less than a Senior Wire Welder due to skill mastery and autonomy. Specialization in advanced welding techniques, certifications (e.g., AWS CWI), and proficiency with specific materials or equipment can command premium compensation. Total compensation often extends beyond the hourly wage, including overtime pay, production bonuses, and sometimes profit-sharing. Benefits packages, such as health insurance, retirement plans like 401(k)s, and paid time off, significantly contribute to the overall value of a compensation package.
Industry-specific trends also influence earnings. Welders in high-demand sectors like aerospace, oil and gas, or specialized manufacturing generally earn more than those in general fabrication shops. Company size and union membership can also impact pay scales and benefits. Negotiating leverage comes from demonstrating a strong safety record, consistent quality, and the ability to handle complex or high-precision tasks. Remote work is generally not applicable to this hands-on role, but travel for specialized projects can offer per diem and premium pay.
Salary by Experience Level
Level | US Median | US Average |
---|---|---|
Apprentice Wire Welder | $36k USD | $38k USD |
Junior Wire Welder | $43k USD | $45k USD |
Wire Welder | $53k USD | $55k USD |
Senior Wire Welder | $65k USD | $68k USD |
Lead Wire Welder | $75k USD | $78k USD |
Welding Supervisor | $82k USD | $85k USD |
Welding Manager | $92k USD | $95k USD |
Market Commentary
The job market for Wire Welders shows consistent demand, driven by ongoing needs in manufacturing, construction, and infrastructure projects. The Bureau of Labor Statistics (BLS) projects a modest growth for welders, cutters, solderers, and brazers, with an outlook of about 2% from 2022 to 2032. This growth is slower than the average for all occupations, yet it reflects a steady need for skilled tradespeople to maintain and build essential structures and products. The aging workforce also contributes to a continuous need for new talent to replace retiring welders.
Emerging opportunities for Wire Welders often lie in specialized areas such as robotic welding operations, where human oversight and programming skills are critical, or in industries requiring high-precision work like defense and renewable energy infrastructure. The demand for qualified welders often outpaces the supply of newly trained professionals, creating a favorable environment for skilled individuals. This supply-demand imbalance can lead to competitive wages and signing bonuses, especially for those with advanced certifications or niche expertise.
Future-proofing for Wire Welders involves continuous learning and adaptation to new technologies, including automated welding systems and advanced materials. While automation handles repetitive tasks, complex, custom, and repair welding will always require human skill. Geographic hotspots for employment typically include industrial hubs, shipbuilding centers, and regions with significant infrastructure development projects. The profession's essential nature makes it relatively recession-resistant, as foundational industries always require maintenance and new construction.
Wire Welder Career Path
Career progression for a Wire Welder typically unfolds through a combination of hands-on experience, advanced skill acquisition, and a demonstrated commitment to quality and safety. Initial advancement focuses on mastering various welding techniques and understanding material properties. As welders gain proficiency, they take on more complex projects and assume greater responsibility.
Individual contributor (IC) tracks for welders often lead to highly specialized roles, such as certified inspectors or master fabricators, where deep technical expertise is paramount. Management and leadership tracks, conversely, involve overseeing teams, managing production schedules, and ensuring compliance with industry standards. Performance, continuous learning, and the ability to train others significantly influence advancement speed.
Company size affects career paths; larger corporations might offer more structured advancement and specialized roles, while smaller shops might provide broader exposure to different tasks. Networking within the industry, pursuing advanced certifications, and developing a reputation for precision and reliability are crucial for navigating career transitions and unlocking new opportunities within the welding field.
Apprentice Wire Welder
0-2 yearsAssist experienced welders with preparatory tasks, material handling, and basic fabrication. Perform simple, repetitive welds under direct supervision. Clean work areas and maintain tools. Decision-making is minimal, primarily following explicit directions.
Key Focus Areas
Learn fundamental welding safety protocols and proper equipment setup. Develop basic proficiency in MIG/MAG welding techniques, focusing on consistent bead formation and penetration. Understand blueprint reading and basic measurement skills. Focus on observation and following instructions precisely.
Junior Wire Welder
2-4 yearsExecute a range of standard wire welding tasks independently, such as fabricating components or performing repairs. Work on projects with moderate complexity, requiring some interpretation of blueprints. Ensure welds meet specified quality standards with periodic checks.
Key Focus Areas
Improve welding speed and accuracy on various joint types and material thicknesses. Develop problem-solving skills for minor welding issues. Begin understanding distortion control and basic metallurgy. Focus on consistent quality and efficiency.
Wire Welder
4-7 yearsPerform complex and critical wire welding operations, often on structural components or pressure vessels. Interpret intricate blueprints and specifications independently, making minor adjustments as needed. Take responsibility for the quality and integrity of finished welds, often working with minimal supervision.
Key Focus Areas
Master advanced wire welding techniques, including pulsed MIG and flux-cored arc welding. Develop expertise in welding various materials like aluminum or stainless steel. Understand quality control procedures and perform self-inspection. Focus on maximizing efficiency and minimizing waste.
Senior Wire Welder
7-10 yearsTackle the most challenging and specialized wire welding jobs, often involving custom fabrication or repair of critical equipment. Provide technical guidance and support to other welders on complex projects. Act as a subject matter expert for specific welding applications or materials. Ensure adherence to stringent quality and safety standards.
Key Focus Areas
Develop advanced troubleshooting skills for complex welding challenges. Begin mentoring junior welders and providing technical guidance. Understand advanced material science and non-destructive testing (NDT) methods. Focus on continuous improvement and sharing expertise.
Lead Wire Welder
10-14 yearsOversee a small team of welders, assigning tasks, monitoring progress, and ensuring project deadlines are met. Provide hands-on training and technical instruction to junior and experienced welders. Troubleshoot complex welding issues and implement corrective actions. Maintain production quality and safety standards for the team.
Key Focus Areas
Cultivate strong leadership and communication skills. Develop project planning and coordination abilities. Understand production scheduling and resource allocation. Focus on team efficiency, quality assurance, and problem resolution at a team level.
Welding Supervisor
14-18 yearsManage a larger group of welders, overseeing daily operations, scheduling, and workflow optimization. Ensure compliance with all safety regulations and quality control procedures. Conduct performance reviews and provide ongoing coaching. Collaborate with other departments to meet production targets and resolve operational issues.
Key Focus Areas
Enhance leadership and team management skills, including conflict resolution and performance evaluation. Develop a deeper understanding of production metrics, cost control, and lean manufacturing principles. Focus on optimizing workflow and fostering a productive work environment.
Welding Manager
18+ yearsDirect the overall operations of the welding department, including strategic planning, budgeting, and resource allocation. Implement new technologies and processes to improve efficiency and quality. Recruit, train, and develop welding staff. Responsible for departmental performance metrics, safety compliance, and overall contribution to company goals.
Key Focus Areas
Develop strategic planning and budget management capabilities. Enhance cross-functional collaboration and communication skills. Focus on long-term departmental goals, technology adoption, and talent development. Understand industry trends and competitive landscapes.
Apprentice Wire Welder
0-2 yearsAssist experienced welders with preparatory tasks, material handling, and basic fabrication. Perform simple, repetitive welds under direct supervision. Clean work areas and maintain tools. Decision-making is minimal, primarily following explicit directions.
Key Focus Areas
Learn fundamental welding safety protocols and proper equipment setup. Develop basic proficiency in MIG/MAG welding techniques, focusing on consistent bead formation and penetration. Understand blueprint reading and basic measurement skills. Focus on observation and following instructions precisely.
Junior Wire Welder
2-4 yearsExecute a range of standard wire welding tasks independently, such as fabricating components or performing repairs. Work on projects with moderate complexity, requiring some interpretation of blueprints. Ensure welds meet specified quality standards with periodic checks.
Key Focus Areas
Improve welding speed and accuracy on various joint types and material thicknesses. Develop problem-solving skills for minor welding issues. Begin understanding distortion control and basic metallurgy. Focus on consistent quality and efficiency.
Wire Welder
4-7 yearsPerform complex and critical wire welding operations, often on structural components or pressure vessels. Interpret intricate blueprints and specifications independently, making minor adjustments as needed. Take responsibility for the quality and integrity of finished welds, often working with minimal supervision.
Key Focus Areas
Master advanced wire welding techniques, including pulsed MIG and flux-cored arc welding. Develop expertise in welding various materials like aluminum or stainless steel. Understand quality control procedures and perform self-inspection. Focus on maximizing efficiency and minimizing waste.
Senior Wire Welder
7-10 yearsTackle the most challenging and specialized wire welding jobs, often involving custom fabrication or repair of critical equipment. Provide technical guidance and support to other welders on complex projects. Act as a subject matter expert for specific welding applications or materials. Ensure adherence to stringent quality and safety standards.
Key Focus Areas
Develop advanced troubleshooting skills for complex welding challenges. Begin mentoring junior welders and providing technical guidance. Understand advanced material science and non-destructive testing (NDT) methods. Focus on continuous improvement and sharing expertise.
Lead Wire Welder
10-14 yearsOversee a small team of welders, assigning tasks, monitoring progress, and ensuring project deadlines are met. Provide hands-on training and technical instruction to junior and experienced welders. Troubleshoot complex welding issues and implement corrective actions. Maintain production quality and safety standards for the team.
Key Focus Areas
Cultivate strong leadership and communication skills. Develop project planning and coordination abilities. Understand production scheduling and resource allocation. Focus on team efficiency, quality assurance, and problem resolution at a team level.
Welding Supervisor
14-18 yearsManage a larger group of welders, overseeing daily operations, scheduling, and workflow optimization. Ensure compliance with all safety regulations and quality control procedures. Conduct performance reviews and provide ongoing coaching. Collaborate with other departments to meet production targets and resolve operational issues.
Key Focus Areas
Enhance leadership and team management skills, including conflict resolution and performance evaluation. Develop a deeper understanding of production metrics, cost control, and lean manufacturing principles. Focus on optimizing workflow and fostering a productive work environment.
Welding Manager
18+ yearsDirect the overall operations of the welding department, including strategic planning, budgeting, and resource allocation. Implement new technologies and processes to improve efficiency and quality. Recruit, train, and develop welding staff. Responsible for departmental performance metrics, safety compliance, and overall contribution to company goals.
Key Focus Areas
Develop strategic planning and budget management capabilities. Enhance cross-functional collaboration and communication skills. Focus on long-term departmental goals, technology adoption, and talent development. Understand industry trends and competitive landscapes.
Job Application Toolkit
Ace your application with our purpose-built resources:
Global Wire Welder Opportunities
Wire welders find consistent demand globally, as manufacturing, construction, and infrastructure projects require their specialized skills. This profession translates directly across borders, with standardized welding codes like AWS and ISO facilitating international recognition. Global demand remains strong for skilled welders in 2025, driven by industrial growth and infrastructure development. Understanding different safety regulations and material specifications in various countries is crucial for international work. Professionals often seek international opportunities for higher wages or specialized project experience.
Global Salaries
Wire welder salaries vary significantly by region, reflecting local economies and demand. In North America, specifically the United States, annual salaries range from $45,000 to $70,000 USD, with higher pay in unionized or specialized sectors. Canadian welders earn between $50,000 and $80,000 CAD (approximately $37,000 - $59,000 USD), often with comprehensive benefits.
European salaries differ widely. In Germany, wire welders can expect €35,000 to €55,000 ($38,000 - $60,000 USD) annually, benefiting from strong social welfare programs. The UK offers £28,000 to £45,000 ($35,000 - $56,000 USD). Scandinavian countries like Norway provide higher wages, often reaching NOK 400,000 to NOK 600,000 ($37,000 - $55,000 USD), though with a higher cost of living.
In Asia-Pacific, Australia offers attractive salaries of AUD 60,000 to AUD 90,000 ($40,000 - $60,000 USD), especially for welders in mining or shipbuilding. Countries like Singapore might offer S$30,000 to S$50,000 ($22,000 - $37,000 USD), but with a lower cost of living. Middle Eastern countries, particularly in the oil and gas sector, offer competitive tax-free salaries, often ranging from $40,000 to $75,000 USD, plus accommodation allowances. Experience, specific welding certifications (e.g., ASME, EN), and the industry sector significantly influence compensation globally.
Remote Work
Wire welding is inherently a hands-on profession, making traditional remote work impossible. Welders must be physically present at manufacturing sites, construction zones, or fabrication shops. The nature of the work requires specialized heavy equipment and direct interaction with materials.
However, some peripheral roles related to welding, such as welding inspection, quality control, or instructional positions, might offer limited remote components. These roles often involve reviewing documentation, conducting virtual audits, or delivering online training. Purely digital nomad opportunities are not applicable for active wire welders. Companies hiring welders internationally expect on-site presence. Any remote aspect would involve administrative or supervisory tasks, not the actual welding process.
Visa & Immigration
Skilled wire welders often qualify for skilled worker visas in countries with labor shortages. Popular destinations include Canada, Australia, Germany, and the UK. Canada's Express Entry system and Australia's Skilled Migration program frequently list welders on their occupation lists. Applicants typically need to demonstrate relevant work experience, often 2-5 years, and hold recognized certifications.
Education credential recognition is crucial; applicants may need to have their qualifications assessed by a professional body in the destination country. For instance, in Canada, bodies like the Red Seal program might assess welding credentials. Language proficiency tests (e.g., IELTS for English-speaking countries, Goethe-Institut for Germany) are standard requirements. Visa processing times vary, from a few months to over a year, depending on the country and specific visa stream. Some countries offer pathways to permanent residency for skilled trades, including welders, after several years of employment. Family visas for dependents are usually available once the primary applicant secures a work visa.
2025 Market Reality for Wire Welders
Understanding the current job market for wire welders is essential for career success. This field has seen significant evolution from 2023 to 2025, influenced by post-pandemic economic shifts and the increasing integration of automation.
Broader economic factors, such as construction spending and manufacturing output, directly impact demand for welding services. Market realities for wire welders vary considerably by experience level—from entry-level apprentices to highly specialized journeymen—and by geographic region, with industrial centers often offering more opportunities. This analysis provides an honest assessment of current hiring realities.
Current Challenges
Wire welders face increased competition, particularly for entry-level positions, as automation and robotic welding systems handle more repetitive tasks. Economic slowdowns impact manufacturing and construction, leading to fewer new projects. This creates a market where employers seek highly skilled, multi-certified welders, leaving those with basic skills struggling to find consistent work.
Growth Opportunities
Despite market shifts, strong opportunities exist for wire welders specializing in niche areas. Infrastructure projects, particularly bridge repair, pipeline maintenance, and power plant upgrades, show consistent demand for certified welders proficient in FCAW and advanced MIG processes. Custom fabrication shops and high-precision manufacturing, where robotic welding is less adaptable, also seek skilled human welders.
Welders who expand their skill set to include robotic welding operation or maintenance, non-destructive testing (NDT), or multi-process welding (TIG, Stick, MIG) gain a significant competitive edge. Companies value adaptability and the ability to work with new materials like exotic alloys. Underserved markets, such as rural industrial zones or areas with aging infrastructure, often present better opportunities due to less competition.
Strategic career moves include pursuing certifications in specific codes (e.g., D1.1 for structural steel, D1.6 for stainless steel) or specializing in industries like shipbuilding or energy. Investing in advanced training now can position welders for higher-paying, more stable roles as the industry continues to evolve towards higher precision and automation integration.
Current Market Trends
The market for wire welders in 2025 shows steady demand in specialized sectors but faces shifts due to automation. While general fabrication roles see some consolidation, industries like infrastructure repair, pipeline construction, and custom metalwork continue to hire. Employers increasingly seek welders proficient with advanced wire processes like pulsed MIG and flux-cored arc welding (FCAW) for high-integrity joints.
Economic conditions, particularly in manufacturing and heavy industry, directly influence hiring. A slight downturn in new commercial construction impacts demand for structural welders, though maintenance and repair work remain consistent. The rise of AI in manufacturing is more about optimizing production lines and predictive maintenance, rather than directly displacing skilled welders; however, it drives demand for welders who can work alongside or maintain automated systems.
Hiring criteria now emphasize certifications (AWS, ASME), safety compliance, and the ability to interpret complex blueprints. Companies also value problem-solving skills and adaptability to new materials or techniques. Salary trends for highly skilled wire welders remain stable or show modest growth, especially for those with specialized certifications in niche areas like aerospace or pressure vessels. Entry-level wages are more stagnant due to a larger pool of basic-skilled candidates.
Geographically, demand is stronger in industrial hubs and areas with ongoing infrastructure projects. Remote work is not applicable for this hands-on role. Seasonal patterns, particularly in construction, mean higher demand in warmer months, while shop-based fabrication offers more consistent year-round employment.
Emerging Specializations
Technological advancements and evolving industry demands consistently create new specialization opportunities for skilled trades. For Wire Welders, understanding these shifts is crucial for career longevity and advancement. Early positioning in emerging areas, particularly those integrating automation, advanced materials, and data, can significantly enhance a professional's value in the market from 2025 onwards.
Specializing in these cutting-edge niches often leads to premium compensation and accelerated career growth. While established welding specializations remain vital, exploring future-oriented paths opens doors to roles with higher complexity and greater strategic importance. These emerging areas typically take 3-7 years to transition from novel applications to mainstream job opportunities, creating a window for proactive professionals to gain expertise.
Pursuing emerging specializations involves a balance of risk and reward. It requires investing in new training and adapting to unfamiliar technologies. However, the reward includes becoming an indispensable expert in high-demand fields, setting oneself apart from the general workforce and securing a more robust career trajectory.
Robotic Welding Technician
Advanced Material Welding Specialist
Additive Manufacturing (WAAM) Welder
Smart Welding Process Analyst
Sustainable Welding Practitioner
Pros & Cons of Being a Wire Welder
Understanding both the benefits and challenges of a career as a Wire Welder is crucial for making an informed decision. Career experiences can vary significantly based on the industry sector, the specific company culture, and the type of projects involved. What one welder finds advantageous, another might perceive as a challenge, reflecting individual preferences and work styles. Moreover, the demands and rewards of the role may shift as one progresses from an entry-level position to a more experienced or specialized capacity. This assessment aims to provide an honest, balanced overview to help prospective wire welders set realistic expectations for this hands-on profession.
Pros
Consistent demand across various industries, including manufacturing, construction, and automotive, provides strong job security and diverse employment opportunities for skilled wire welders.
Relatively quick entry into the workforce is possible, as many wire welding positions require vocational training or certifications rather than a lengthy degree, allowing for faster career commencement.
Tangible results of your work are immediately visible, offering a strong sense of accomplishment and pride in creating durable, functional structures or components.
Competitive earning potential, especially for experienced and certified wire welders, can lead to a stable and comfortable income, often with opportunities for overtime pay on urgent projects.
Skill development is continuous, as mastering various wire welding techniques and working with different materials enhances expertise and opens doors to more complex and higher-paying specialized roles.
Opportunities for travel may arise in roles that involve on-site construction, infrastructure projects, or specialized repair work, appealing to those who enjoy varied work locations.
A sense of craftsmanship and precision is cultivated, as wire welding demands a high degree of accuracy and attention to detail to ensure the integrity and quality of welds, fostering a valuable practical skill.
Cons
Exposure to hazardous conditions, including fumes, sparks, and intense light, requires strict adherence to safety protocols and can lead to long-term health issues if proper precautions are not consistently followed.
Physically demanding work involves prolonged standing, bending, and lifting heavy materials, which can lead to musculoskeletal strain and fatigue over time, especially in production environments.
Repetitive tasks are common in many wire welding roles, particularly in manufacturing or assembly lines, which can become monotonous and lead to mental fatigue or a lack of varied intellectual stimulation.
Limited career progression beyond mastering welding techniques exists in some settings, as advancement often requires transitioning into supervisory roles, quality control, or specialized certifications rather than just more welding.
Inconsistent work availability can occur in project-based or contract roles, leading to periods of unemployment or reduced income if new projects are not secured promptly.
Working in confined spaces or awkward positions is frequently required, which can be uncomfortable and increase the risk of injury due to restricted movement and poor ergonomics.
Continuous skill maintenance and adaptation to new materials or equipment are necessary, as welding technology evolves and different projects demand specific techniques, requiring ongoing training and practice.
Frequently Asked Questions
What are the essential qualifications to become a Wire Welder?
You generally need a high school diploma or GED. Most wire welders gain skills through vocational training programs, community college courses, or apprenticeships. These programs teach specific wire welding processes like MIG (GMAW) and flux-cored (FCAW), blueprint reading, and essential safety protocols. Certifications, such as those from the American Welding Society (AWS), significantly boost your employability.
How long does it take to become a job-ready Wire Welder from scratch?
Becoming a proficient wire welder can take 6 months to 2 years, depending on your learning path. Vocational school programs often last 6-12 months for entry-level skills. Apprenticeships typically take 2-4 years, providing comprehensive on-the-job training and classroom instruction. The key is consistent practice to develop the hand-eye coordination and precision required for quality welds.
What are the typical salary expectations for a Wire Welder?
Entry-level wire welders can expect to earn around $18-$22 per hour, while experienced and certified professionals can command $25-$35 per hour or more, especially with specialized skills. Overtime opportunities are common and can significantly increase annual income. Salary varies by industry, location, and the complexity of the welding work performed.
What are the physical demands and typical working conditions for a Wire Welder?
Wire welding often involves physically demanding work, including standing for long periods, lifting, and working in various positions. Safety is paramount, requiring strict adherence to protocols and proper use of personal protective equipment (PPE) like helmets, gloves, and flame-resistant clothing. The work environment can be noisy and dusty, but modern ventilation and equipment help mitigate these issues.
Is the Wire Welder profession secure, or is it at risk from automation?
The job market for skilled wire welders remains stable, driven by demand in manufacturing, construction, automotive, and infrastructure projects. Automation handles some repetitive tasks, but complex and specialized welding still requires human expertise. Your job security often depends on your skill level, versatility in different welding processes, and willingness to adapt to new technologies.
What are the career advancement opportunities for a Wire Welder?
Career growth for wire welders can lead to specialized roles like robotic welding technicians, welding inspectors, or supervisors. You can also advance by becoming a certified welding educator or starting your own mobile welding business. Gaining certifications in advanced welding processes, such as TIG or pipe welding, expands your opportunities and earning potential significantly.
Can Wire Welders work remotely, or is it always an on-site job?
Many wire welding jobs require on-site presence, especially in fabrication shops, construction sites, or manufacturing plants. However, some roles, particularly those involving advanced robotic welding programming or quality control, might offer hybrid or more flexible arrangements. Remote work is generally not common for hands-on production wire welding.
What ongoing learning and soft skills are important for a Wire Welder?
Wire welding requires continuous learning because new materials, techniques, and equipment regularly emerge. You need to stay updated on safety regulations and best practices. Developing strong problem-solving skills is crucial for troubleshooting issues like weld defects or equipment malfunctions. Attention to detail ensures high-quality, durable welds that meet specifications.
Related Careers
Explore similar roles that might align with your interests and skills:
Mig Welder
A growing field with similar skill requirements and career progression opportunities.
Explore career guideTig Welder
A growing field with similar skill requirements and career progression opportunities.
Explore career guideWelder
A growing field with similar skill requirements and career progression opportunities.
Explore career guideMachine Welder
A growing field with similar skill requirements and career progression opportunities.
Explore career guideWelding Machine Operator
A growing field with similar skill requirements and career progression opportunities.
Explore career guideAssess your Wire Welder readiness
Understanding where you stand today is the first step toward your career goals. Our Career Coach helps identify skill gaps and create personalized plans.
Skills Gap Analysis
Get a detailed assessment of your current skills versus Wire Welder requirements. Our AI Career Coach identifies specific areas for improvement with personalized recommendations.
See your skills gapCareer Readiness Assessment
Evaluate your overall readiness for Wire Welder roles with our AI Career Coach. Receive personalized recommendations for education, projects, and experience to boost your competitiveness.
Assess your readinessSimple pricing, powerful features
Upgrade to Himalayas Plus and turbocharge your job search.
Himalayas
Himalayas Plus
Himalayas Max
Find your dream job
Sign up now and join over 100,000 remote workers who receive personalized job alerts, curated job matches, and more for free!
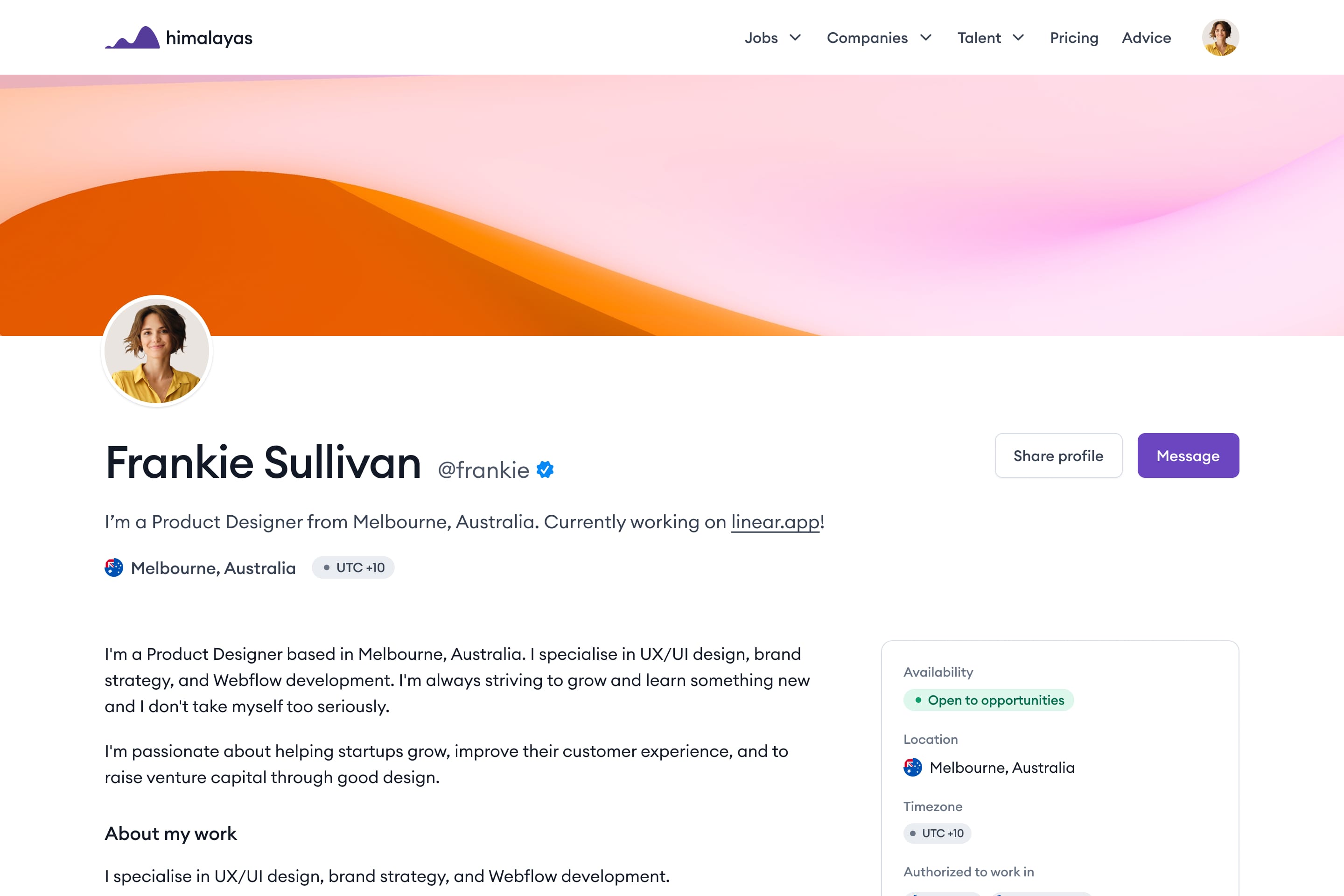