Complete Safety Coordinator Career Guide
Safety Coordinators are the vigilant guardians of the workplace, designing and implementing protocols that protect employees from hazards and ensure compliance with critical regulations. They blend meticulous attention to detail with practical problem-solving, making every day safer for countless individuals across diverse industries. This vital role offers a pathway to making a tangible impact on well-being and operational efficiency, requiring a blend of technical knowledge and strong communication skills.
Key Facts & Statistics
Median Salary
$78,070 USD
(U.S. Bureau of Labor Statistics, May 2023)
Range: $50k - $100k+ USD, varying significantly by industry and experience
Growth Outlook
6%
as fast as average (U.S. Bureau of Labor Statistics, 2022-2032)
Annual Openings
≈17,200
openings annually (U.S. Bureau of Labor Statistics)
Top Industries
Typical Education
Bachelor's degree in occupational safety and health, industrial hygiene, or a related field; some positions may accept an associate's degree with relevant experience or specialized certifications.
What is a Safety Coordinator?
A Safety Coordinator is a dedicated professional responsible for overseeing and implementing workplace safety programs to ensure a safe and healthy environment for all employees. This role focuses on preventing accidents, injuries, and health hazards by identifying risks, enforcing regulations, and promoting a strong safety culture within an organization. They act as the primary point of contact for safety-related matters, bridging the gap between management and employees regarding compliance and best practices.
Unlike a Safety Manager, who typically focuses on strategic planning, budget management, and high-level policy setting across an entire organization, a Safety Coordinator is more hands-on. They primarily focus on the day-to-day operational aspects of safety, including conducting inspections, delivering training, and investigating incidents at a specific site or within a particular department. This distinction ensures that while managers set the overarching safety vision, coordinators ensure its practical application and effectiveness on the ground.
What does a Safety Coordinator do?
Key Responsibilities
- Conduct regular safety inspections of worksites, equipment, and processes to identify potential hazards and non-compliance issues.
- Develop and deliver safety training programs for employees on topics such as emergency procedures, hazard communication, and proper use of personal protective equipment.
- Investigate workplace accidents and near-miss incidents, determining root causes and recommending corrective actions to prevent recurrence.
- Maintain accurate records of safety inspections, training sessions, incident reports, and safety-related documentation to ensure regulatory compliance.
- Collaborate with management and employees to implement new safety policies, procedures, and initiatives across various departments.
- Monitor adherence to safety regulations and company policies, providing guidance and support to foster a strong safety culture.
- Prepare and submit reports to regulatory agencies regarding safety performance and compliance, ensuring all legal requirements are met and documented properly for accountability and transparency purposes, which helps to maintain high safety standards.
Work Environment
A Safety Coordinator typically works in a hybrid environment, splitting time between an office setting and various worksites. Office time involves administrative tasks, report writing, training development, and meetings. Worksite visits can range from factories, construction sites, or laboratories, requiring adherence to strict safety protocols.
The role involves significant interaction and collaboration with employees at all levels, from frontline workers to senior management. The pace of work can be variable; routine tasks are consistent, but emergency responses or accident investigations can be fast-paced and require immediate attention. Travel to different company locations or project sites is common. While some remote administrative work is possible, the hands-on nature of site inspections and training often necessitates a physical presence.
Tools & Technologies
Safety Coordinators use a variety of tools and technologies to manage workplace safety. They frequently utilize safety management software such as Intelex, Cority, or SafetyCulture for incident reporting, inspection checklists, and compliance tracking. These platforms help them maintain digital records and streamline safety processes.
Personal protective equipment (PPE) like hard hats, safety glasses, and high-visibility vests are essential for site visits and inspections. They also use basic office productivity suites like Microsoft Office (Word, Excel, PowerPoint) for creating reports, presentations, and training materials. Communication tools such as email, instant messaging, and video conferencing software facilitate collaboration with various teams and stakeholders. Depending on the industry, they might also use specialized equipment for environmental monitoring or testing, such as gas detectors or noise meters.
Safety Coordinator Skills & Qualifications
The Safety Coordinator role requires a blend of regulatory knowledge, practical application, and strong communication skills. Qualifications vary significantly based on the industry, company size, and specific hazards present. For instance, a Safety Coordinator in manufacturing needs deep understanding of machine guarding and lockout/tagout, while one in construction focuses on fall protection and excavation safety.
Entry-level positions often accept candidates with an Associate's degree or relevant certifications coupled with some practical experience. More senior or specialized Safety Coordinator roles, especially in highly regulated industries like oil and gas or pharmaceuticals, typically require a Bachelor's degree in Occupational Safety and Health or a related engineering discipline. Practical experience often outweighs formal education in the hiring process, particularly for those demonstrating a strong track record of incident reduction and compliance.
Certifications like OSHA 30-Hour, CSP (Certified Safety Professional), or ASP (Associate Safety Professional) significantly enhance a candidate's profile, often becoming 'must-haves' for advancement. The field is evolving with increasing emphasis on data analytics for proactive risk assessment and a shift towards human factors in safety, making skills in these areas increasingly valuable. Understanding how to balance compliance with operational efficiency is also crucial, distinguishing effective Safety Coordinators from those who only focus on rules.
Education Requirements
Technical Skills
- OSHA Regulations (General Industry and/or Construction): Deep understanding of 29 CFR 1910 and/or 1926 standards, including specific sections relevant to the industry.
- Hazard Identification and Risk Assessment: Ability to systematically identify, evaluate, and prioritize workplace hazards and assess associated risks.
- Incident Investigation and Root Cause Analysis: Proficiency in methodologies like TapRooT, 5 Whys, or Fishbone diagrams to determine underlying causes of incidents.
- Safety Management Systems (e.g., ISO 45001): Knowledge of developing, implementing, and maintaining structured safety management systems.
- Emergency Preparedness and Response Planning: Skill in creating and executing plans for emergencies, including fire, chemical spills, and natural disasters.
- Safety Auditing and Inspection: Conducting systematic evaluations of workplace conditions and practices against established safety standards.
- Data Analysis and Reporting: Using software (e.g., Excel, specific EHS software) to track incident rates, identify trends, and generate actionable safety reports.
- Personal Protective Equipment (PPE) Selection and Management: Expertise in selecting appropriate PPE, ensuring proper fit, maintenance, and training on its use.
- Lockout/Tagout (LOTO) Procedures: Developing and implementing energy control procedures for hazardous machinery.
- Confined Space Entry Procedures: Understanding and managing the risks associated with working in confined spaces.
- Industrial Hygiene Principles: Basic knowledge of recognizing, evaluating, and controlling environmental factors that may affect health.
Soft Skills
- Communication: Effectively conveys complex safety regulations and procedures to diverse audiences, from frontline workers to senior management, ensuring understanding and compliance.
- Attention to Detail: Crucial for identifying subtle hazards, meticulously documenting incidents, and accurately interpreting safety data and regulations.
- Problem-Solving: Analyzes incidents and near-misses to determine root causes and develops effective, sustainable corrective actions to prevent recurrence.
- Influence and Persuasion: Encourages safe behaviors and compliance without direct authority, fostering a proactive safety culture through collaboration and education.
- Adaptability: Adjusts safety protocols and training methods in response to changing regulations, new technologies, or evolving workplace hazards.
- Ethical Judgment: Upholds safety standards and acts with integrity, even when facing pressure to compromise on safety for production or cost reasons.
- Training and Facilitation: Develops and delivers engaging safety training programs, ensuring effective knowledge transfer and skill development among employees.
- Conflict Resolution: Mediates disagreements regarding safety practices or compliance, finding constructive solutions that satisfy safety requirements and operational needs.
How to Become a Safety Coordinator
Breaking into the Safety Coordinator role involves several pathways, not just a single educational route. You can pursue traditional academic degrees in occupational safety and health, but many successful Safety Coordinators transition from related fields like construction, manufacturing, or healthcare, bringing practical experience. The timeline for entry varies significantly; a complete beginner might need 1-2 years to gain foundational knowledge and relevant certifications, while someone with existing industry experience could transition in 3-6 months with focused effort on safety-specific training.
Entry strategies also depend on the industry and company size. Larger corporations often prefer candidates with formal degrees or extensive certification, while smaller businesses or startups might prioritize practical experience and a demonstrated understanding of compliance. Geographic location plays a role as well; industrial hubs will have more opportunities than purely service-oriented regions. Overcoming barriers often involves highlighting transferable skills from previous roles, especially in areas like risk assessment, training, and documentation, and actively seeking mentorship to navigate industry specifics.
The hiring landscape for Safety Coordinators is evolving, with an increasing emphasis on proactive safety culture, data analysis, and regulatory compliance. Effective networking and building industry connections are crucial, as many roles are filled through referrals or within professional communities. Focus on building a portfolio of safety-related projects or initiatives, even from volunteer work or previous job duties, to showcase your practical application of safety principles.
Step 1
Step 2
Step 3
Step 4
Step 5
Step 6
Education & Training Needed to Become a Safety Coordinator
Becoming a Safety Coordinator requires a blend of formal education and practical certifications, with pathways varying significantly based on industry and employer. While a four-year bachelor's degree in occupational health and safety, environmental health, or a related engineering field provides a strong theoretical foundation, many roles are accessible through associate degrees or specialized certification programs. Bachelor's degrees typically cost $40,000-$100,000+ and take four years, offering comprehensive knowledge in safety regulations, risk management, and industrial hygiene. Associate degrees, costing $15,000-$30,000 over two years, focus more on practical application and specific safety protocols.
Alternative learning paths, such as professional certifications and intensive training courses, offer faster entry into the field. Certifications like the Occupational Safety and Health Administration (OSHA) 30-Hour General Industry or Construction Safety, while not degrees, are often prerequisites for entry-level Safety Coordinator positions. Specialized certifications from organizations like the Board of Certified Safety Professionals (BCSP) or the National Safety Council (NSC) can significantly enhance career prospects and salary potential. These programs range from a few hundred dollars for basic OSHA training to several thousand for comprehensive certification exam preparation, typically requiring weeks to months of study.
Employers generally value a combination of theoretical knowledge and practical experience. While a degree demonstrates foundational understanding, certifications validate specific competencies and adherence to industry standards. Continuous learning is crucial; safety regulations and best practices evolve constantly, necessitating ongoing professional development through workshops, seminars, and advanced certifications. The investment in education and certification directly correlates with career advancement and the ability to handle more complex safety challenges in diverse industrial settings.
Safety Coordinator Salary & Outlook
Compensation for a Safety Coordinator varies significantly based on several factors, reflecting the role's critical importance in ensuring workplace compliance and employee well-being. Geographic location plays a substantial role; areas with higher costs of living or strong industrial bases often offer increased salaries due to higher demand for safety professionals. For example, salaries in California or Texas typically exceed those in less industrialized states.
Experience levels, specialized certifications (like CSP or OHST), and the specific industry sector also drive salary differences. A Safety Coordinator in a high-risk manufacturing environment, for instance, may command a higher salary than one in an office-based setting due to the complexity and inherent dangers involved. Total compensation extends beyond base salary to include performance bonuses, health and wellness benefits, and robust retirement plans. Larger organizations or those in heavily regulated industries often provide more comprehensive benefits packages and opportunities for professional development.
Negotiation leverage for a Safety Coordinator often stems from demonstrated success in reducing incidents, ensuring regulatory compliance, and implementing effective safety programs. Remote work options, while less common for hands-on safety roles, can impact geographic arbitrage for hybrid positions, though most Safety Coordinators require on-site presence. International markets present different salary structures and regulatory environments, meaning the USD figures primarily reflect the United States market.
Salary by Experience Level
Level | US Median | US Average |
---|---|---|
Junior Safety Coordinator | $52k USD | $55k USD |
Safety Coordinator | $68k USD | $70k USD |
Senior Safety Coordinator | $82k USD | $85k USD |
Safety Manager | $100k USD | $105k USD |
Director of Safety | $135k USD | $140k USD |
VP of Safety | $185k USD | $195k USD |
Market Commentary
The job market for Safety Coordinators shows steady demand, driven by an ongoing emphasis on workplace safety, regulatory compliance, and risk management across various industries. The Bureau of Labor Statistics projects growth for occupational health and safety specialists, including Safety Coordinators, at about 5% from 2022 to 2032, which is about as fast as the average for all occupations. This growth is fueled by increasing regulatory scrutiny, a heightened awareness of workplace hazards, and the need for organizations to minimize liability and improve employee welfare.
Emerging opportunities for Safety Coordinators include roles focused on ergonomic assessments, mental health and wellness programs, and the integration of technology like IoT sensors and AI for predictive safety analytics. Industries such as construction, manufacturing, healthcare, and energy continue to be significant employers, requiring skilled professionals to manage complex safety protocols. The supply of qualified candidates remains relatively balanced with demand, but those with advanced certifications and specialized industry experience often have a competitive edge.
Future-proofing this career involves continuous learning in areas like industrial hygiene, environmental regulations, and data analysis for safety performance. While automation may handle some data collection, the core functions of risk assessment, human interaction, and program implementation remain critical, making the role relatively recession-resistant due to its essential nature in preventing costly incidents and maintaining compliance. Geographic hotspots for Safety Coordinators align with industrial and manufacturing hubs, though remote work for strategic planning or auditing roles may see an increase.
Safety Coordinator Career Path
Career progression for a Safety Coordinator typically involves increasing responsibility for safety program development, implementation, and oversight. Professionals can advance along an individual contributor (IC) track, becoming highly specialized experts, or transition into a management/leadership track, overseeing teams and broader organizational safety initiatives.
Advancement speed depends on several factors, including individual performance, the complexity of the industry (e.g., manufacturing vs. tech), company size, and the regulatory environment. Specialization in areas like hazardous materials, ergonomics, or specific industry regulations can accelerate progression. Lateral moves might involve shifting between different industries or focusing on a specific type of safety, such as construction safety or occupational health.
Career paths vary significantly between startups, which might offer broader exposure but less formal structure, and large corporations, which often have more defined progression paths. Networking within professional organizations like the American Society of Safety Professionals (ASSP), pursuing certifications (e.g., CSP, ASP), and continuous learning about evolving safety standards and technologies are crucial for sustained growth and opening alternative pathways in risk management or environmental health.
Junior Safety Coordinator
0-2 yearsKey Focus Areas
Safety Coordinator
2-4 yearsKey Focus Areas
Senior Safety Coordinator
4-7 yearsKey Focus Areas
Safety Manager
7-10 yearsKey Focus Areas
Director of Safety
10-15 yearsKey Focus Areas
VP of Safety
15+ yearsKey Focus Areas
Junior Safety Coordinator
0-2 yearsSupport safety operations by assisting with inspections, maintaining safety records, and preparing basic safety reports. This role involves learning established procedures and working under direct supervision. Impact is primarily at the departmental or project level, ensuring compliance with immediate tasks.
Key Focus Areas
Develop foundational knowledge of OSHA regulations, company safety policies, and basic risk assessment techniques. Learn to conduct safety inspections, document findings, and support incident investigations. Build communication skills for delivering safety briefings and interacting with frontline employees.
Safety Coordinator
2-4 yearsManage routine safety inspections, conduct incident investigations, and ensure compliance with safety regulations for specific areas or projects. This role involves more independent decision-making regarding daily safety operations. Impact extends to improving safety performance within assigned operational units.
Key Focus Areas
Strengthen skills in incident investigation, root cause analysis, and corrective action implementation. Master safety data analysis to identify trends and areas for improvement. Begin to contribute to the development of specific safety training modules and emergency response plans.
Senior Safety Coordinator
4-7 yearsLead complex safety audits, develop and implement specialized safety programs, and oversee incident management processes. Provide technical guidance to management and employees on safety best practices. Influence safety culture and compliance across larger departments or multiple sites with significant autonomy.
Key Focus Areas
Advance expertise in risk management, auditing, and compliance across multiple regulatory frameworks. Develop project management skills for leading safety initiatives. Begin to mentor junior staff and participate in cross-functional safety committees. Focus on proactive safety measures and culture building.
Safety Manager
7-10 yearsOversee a team of safety professionals, developing departmental goals and ensuring effective safety program execution across the organization. Make strategic decisions regarding safety policy, resource deployment, and compliance initiatives. Impact directly affects overall organizational safety performance and regulatory standing.
Key Focus Areas
Cultivate strong leadership, team management, and strategic planning skills. Develop proficiency in budgeting, resource allocation, and performance management for safety teams. Focus on influencing organizational leadership and integrating safety into business objectives. Pursue advanced certifications like CSP.
Director of Safety
10-15 yearsDirect the overall safety strategy and programs for a large business unit or multiple regions. This role involves significant influence on executive leadership and cross-functional teams. Responsible for developing and maintaining a robust safety culture and ensuring regulatory compliance at a senior level.
Key Focus Areas
Focus on enterprise-level safety strategy, risk mitigation, and regulatory affairs. Develop executive presence, stakeholder engagement, and change management capabilities. Understand global safety standards and their application. Drive continuous improvement through innovation and technology adoption.
VP of Safety
15+ yearsSet the vision and strategic direction for all aspects of corporate safety and environmental health. This executive role involves high-level decision-making impacting the entire organization's risk profile, reputation, and operational continuity. Accountable for achieving world-class safety performance and compliance.
Key Focus Areas
Master corporate governance, strategic foresight, and organizational resilience planning. Develop expertise in crisis management and business continuity from a safety perspective. Build a network with industry leaders and regulatory bodies to shape future safety practices.
Job Application Toolkit
Ace your application with our purpose-built resources:
Safety Coordinator Resume Examples
Proven layouts and keywords hiring managers scan for.
View examplesSafety Coordinator Cover Letter Examples
Personalizable templates that showcase your impact.
View examplesTop Safety Coordinator Interview Questions
Practice with the questions asked most often.
View examplesSafety Coordinator Job Description Template
Ready-to-use JD for recruiters and hiring teams.
View examplesGlobal Safety Coordinator Opportunities
Safety Coordinators ensure workplace safety standards globally, with high demand across manufacturing, construction, and logistics sectors. This role involves adapting to diverse international safety regulations and cultural norms, from ISO 45001 to regional compliance. Professionals often seek international roles for diverse industry exposure and career advancement. Certifications like NEBOSH or OSHA are widely recognized, enhancing global mobility.
Global Salaries
Global salaries for a Safety Coordinator vary significantly by region and industry. In North America, particularly the USA and Canada, salaries range from $60,000 to $90,000 USD annually. This reflects a strong demand for compliance in heavily regulated sectors. European countries like Germany and the UK offer €45,000 to €70,000 (approximately $48,000 to $75,000 USD), with higher compensation in Scandinavia due to robust social welfare systems and higher living costs.
Asia-Pacific markets, such as Australia and Singapore, see ranges of AUD 70,000 to AUD 100,000 (approximately $46,000 to $66,000 USD) and SGD 50,000 to SGD 75,000 (approximately $37,000 to $55,000 USD) respectively. These figures often include comprehensive benefits packages typical of the region. Latin American countries, like Brazil and Mexico, typically offer lower nominal salaries, ranging from $25,000 to $45,000 USD, but purchasing power parity can make these competitive locally.
Salary structures also differ, with North American packages often emphasizing base salary and bonuses, while European and Australian packages may include more extensive healthcare, pension contributions, and generous vacation time. Tax implications vary widely; for example, Nordic countries have higher income taxes but offer universal services. International experience and specialized certifications significantly boost earning potential, particularly in multinational corporations that value standardized safety practices across their global operations.
Remote Work
International remote work for Safety Coordinators is limited due to the inherent on-site nature of the role. Most responsibilities involve direct workplace inspections, risk assessments, and incident response. However, some administrative tasks like policy development, training material creation, and data analysis can be done remotely. This often applies to roles within larger corporate safety departments supporting multiple sites.
Digital nomad opportunities are rare for this specific role, as physical presence is usually required for effective oversight. Companies are unlikely to hire an international remote Safety Coordinator for a single location. Time zone differences can complicate remote collaboration on global safety initiatives. Equipment needs are minimal beyond a reliable internet connection and standard office setup. Compensation for remote tasks typically aligns with the hiring company's primary location. Hybrid models, combining occasional on-site visits with remote administrative work, are more common than fully remote positions.
Visa & Immigration
Skilled worker visas are the most common pathway for Safety Coordinators seeking international roles. Countries like Canada, Australia, the UK, and Germany often list safety professionals on their skilled occupation lists. Requirements typically include relevant tertiary education, professional certifications like NEBOSH or OSHA, and several years of experience in the field. Language proficiency, often demonstrated via IELTS or TOEFL, is also a common requirement, especially for English-speaking countries.
The application process usually involves employer sponsorship, a job offer, and a review of educational credentials. Processing times vary from a few months to over a year, depending on the country and visa type. For example, Canada's Express Entry system offers a streamlined process for eligible candidates. Some countries, particularly in the EU, may require local professional licensing or recognition of foreign qualifications. Pathways to permanent residency often exist after several years of continuous employment. Family visas are usually available for spouses and dependents, allowing them to accompany the primary visa holder.
2025 Market Reality for Safety Coordinators
Understanding current market realities is crucial for Safety Coordinators aiming for career success. The field has evolved significantly from 2023 to 2025, impacted by post-pandemic shifts in workplace safety protocols and the burgeoning influence of AI in risk management.
Broader economic factors, such as supply chain stability and industrial output, directly influence the demand for safety professionals. Market realities also vary by experience level, with senior roles often requiring specialized industry knowledge, while entry-level positions face higher competition. Regional regulatory differences and company size further shape opportunities, demanding a tailored approach to job searching and career planning.
Current Challenges
Safety Coordinator roles face heightened competition due to increased applicant pools and the perceived stability of the field. Economic uncertainty prompts organizations to scrutinize every new hire, sometimes consolidating safety responsibilities among existing staff.
Entry-level saturation remains an issue, as many graduates seek initial roles in safety. Furthermore, companies increasingly demand coordinators with specialized certifications or experience in specific, high-risk industries, creating a skill gap for generalists.
Growth Opportunities
Despite market challenges, specific areas within safety coordination are experiencing strong demand. Roles focusing on data-driven safety management, leveraging predictive analytics and AI tools, are emerging as key opportunities. Professionals who can analyze complex safety data to prevent incidents, rather than just react, hold a competitive edge.
Specializations in niche, high-compliance sectors like renewable energy, advanced manufacturing, and biotechnology offer significant growth. These industries often have unique safety challenges and strict regulatory oversight, creating a continuous need for skilled coordinators. Underserved markets, particularly in rapidly developing industrial zones, also present better opportunities.
Developing expertise in specific safety software platforms and obtaining certifications in areas like OSHA 30, CSP, or ASP provide competitive advantages. Furthermore, a proactive approach to understanding and implementing new safety technologies, including IoT sensors and wearable tech for hazard detection, positions coordinators as forward-thinking assets. Strategic career moves might involve targeting companies investing heavily in safety innovation or those expanding into new, regulated markets.
Current Market Trends
The market for Safety Coordinators in 2025 shows steady, rather than explosive, demand. Organizations prioritize maintaining compliance and reducing liability, driving consistent hiring for these roles, particularly in sectors like manufacturing, construction, and logistics. However, the pace of new job creation has moderated compared to the post-pandemic surge.
AI integration affects the role by automating data analysis for incident reporting and predictive risk assessment. This shifts the coordinator's focus from manual data entry to interpreting AI-generated insights and implementing proactive strategies. Employers increasingly seek candidates who can leverage safety software and data analytics tools, moving beyond traditional inspection-centric duties.
Economic conditions, while generally stable, lead some companies to optimize safety teams, sometimes expecting coordinators to manage broader environmental or quality assurance tasks. Remote work normalization has had less impact on this inherently on-site role, though some administrative aspects can be handled remotely. Salary growth for experienced coordinators remains modest, reflecting a mature market rather than rapid expansion.
Geographic variations are significant; industrial hubs and regions with stringent regulatory environments exhibit stronger demand. Conversely, areas with declining industrial bases see fewer opportunities. Seasonal hiring patterns are minimal, with a consistent need throughout the year, though large project-based industries might see slight fluctuations.
Emerging Specializations
The role of a Safety Coordinator is evolving rapidly, driven by advancements in technology, increasing regulatory complexity, and a heightened global focus on employee well-being. These shifts are creating new specialization opportunities that move beyond traditional compliance. Professionals who anticipate these changes and position themselves early in emerging areas will find significant career advantages in 2025 and beyond.
Specializing in cutting-edge fields often leads to premium compensation and accelerated career growth. These emerging niches demand unique skill sets that are currently in high demand and short supply. While established safety specializations remain important, pursuing emerging areas offers a strategic path for professionals seeking to differentiate themselves and lead future initiatives.
Emerging specializations typically take several years to become mainstream and generate a large volume of job opportunities. Early adopters face the risk of investing in areas that may not fully materialize, but the potential rewards – including thought leadership and first-mover advantage – are substantial. Strategic professionals balance foundational knowledge with a forward-looking perspective, ensuring they remain adaptable as the safety landscape continues to transform.
Predictive Safety Analytics Coordinator
Emerging Technology Safety Coordinator
Psychological Safety & Well-being Coordinator
Remote Work Safety Coordinator
Sustainable Operations Safety Coordinator
Pros & Cons of Being a Safety Coordinator
Understanding both the advantages and challenges of a career is crucial for making informed decisions. While a role like Safety Coordinator offers significant rewards, it also comes with unique demands and pressures. Career experiences vary greatly depending on the company culture, industry sector, specific responsibilities, and individual personality. What one person views as a benefit, another might see as a drawback. Furthermore, the nature of pros and cons can shift at different career stages, from entry-level responsibilities to senior leadership roles. This assessment provides a realistic, balanced view to help set appropriate expectations.
Pros
- Safety Coordinators play a vital role in protecting lives and preventing injuries, offering a strong sense of purpose and direct contribution to employee well-being.
- There is consistent demand for Safety Coordinators across various industries, including manufacturing, construction, healthcare, and logistics, providing strong job security.
- The role offers diverse responsibilities, from conducting inspections and developing training programs to investigating incidents and ensuring regulatory compliance, which prevents monotony.
- Safety Coordinators often interact with all levels of an organization, from front-line workers to senior executives, fostering strong communication and interpersonal skills.
- The field offers clear opportunities for professional growth through certifications (e.g., CSP, ASP) and specialization, leading to advanced roles like Safety Manager or Director.
- Safety Coordinators contribute directly to a company's operational efficiency and financial stability by reducing accident-related costs, insurance premiums, and potential fines.
- Developing and implementing effective safety programs allows for creative problem-solving and the application of technical knowledge to real-world workplace challenges.
Cons
- Navigating resistance to safety protocols from employees or management is a common challenge, as some may view safety measures as hindrances to productivity or unnecessary bureaucracy.
- Safety Coordinators often bear significant liability and responsibility for workplace incidents, facing scrutiny and potential legal repercussions if safety protocols fail or are not adequately enforced.
- The role can involve exposure to hazardous environments or materials during inspections and incident investigations, which requires strict adherence to personal protective equipment and safety procedures.
- Dealing with workplace accidents and injuries can be emotionally taxing, requiring empathy and resilience while managing sensitive situations and distressed individuals.
- Safety Coordinators must continuously update their knowledge on evolving regulations, standards, and best practices, which demands ongoing professional development and training outside of regular work hours.
- Budget constraints often limit the implementation of desired safety improvements or the acquisition of necessary equipment, forcing Safety Coordinators to find creative, cost-effective solutions.
- Measuring the direct return on investment (ROI) for safety initiatives can be difficult, making it challenging to justify expenses or demonstrate the tangible value of prevention efforts to upper management.
Frequently Asked Questions
Safety Coordinators face distinct challenges balancing regulatory compliance with practical workplace safety implementation. This section addresses key questions about entering this role, from required certifications and educational paths to daily responsibilities and career growth within the safety field.
What educational background and certifications do I need to become a Safety Coordinator?
Most entry-level Safety Coordinator roles require a high school diploma or GED, but many employers prefer an associate's or bachelor's degree in occupational safety, environmental health, or a related field. Relevant certifications like OSHA 10 or OSHA 30 are often mandatory, with more advanced certifications such as the Certified Safety Professional (CSP) or Associate Safety Professional (ASP) being highly valued for career progression. Practical experience through internships or entry-level safety support roles also significantly boosts your candidacy.
How long does it take to become job-ready as a Safety Coordinator, starting from scratch?
The time to become job-ready as a Safety Coordinator varies. If you pursue an associate's degree, it typically takes two years. A bachelor's degree path usually takes four years. For those with relevant experience or a non-safety degree, obtaining OSHA 30 and other basic certifications might take a few weeks to a few months. Gaining practical experience through internships or volunteer work in safety can also accelerate your readiness, often allowing you to secure an entry-level position within 6-12 months after completing initial training.
What are the typical salary expectations for an entry-level Safety Coordinator?
Starting salaries for Safety Coordinators typically range from $45,000 to $60,000 annually, depending on location, industry, and specific responsibilities. With a few years of experience and additional certifications, salaries can increase to $60,000-$80,000 or more. Factors like working in high-risk industries (e.g., construction, manufacturing) or for larger corporations can lead to higher compensation. Continuous professional development and specialization in areas like industrial hygiene or environmental safety can also boost your earning potential.
What is the typical work-life balance for a Safety Coordinator, and are there frequent emergencies?
The work-life balance for Safety Coordinators is generally good, often involving standard business hours. However, emergency situations or accident investigations can sometimes require extended hours or on-call availability. Industries with higher inherent risks, such as manufacturing or construction, might involve more frequent site visits or occasional weekend work for inspections or training. Many roles offer a predictable schedule, allowing for a healthy balance between professional and personal life.
Is the job market for Safety Coordinators stable, and what is the long-term job security like?
The job market for Safety Coordinators remains stable and is expected to grow. Businesses across all sectors prioritize safety to protect employees, comply with regulations, and avoid costly incidents. This consistent demand ensures good job security. Economic downturns might slow hiring in some areas, but the fundamental need for safety professionals persists. Specialization in niche areas or obtaining advanced certifications can further enhance your long-term career prospects and security.
What are the typical career advancement opportunities for a Safety Coordinator?
Safety Coordinators have several avenues for career advancement. You can progress to roles like Safety Manager, Environmental Health and Safety (EHS) Manager, or even Director of Safety. Specializing in areas such as industrial hygiene, ergonomics, or fire safety can also open up new opportunities. Pursuing advanced certifications like the CSP, obtaining a master's degree in occupational safety, or gaining experience in different industries are common ways to accelerate your career growth and take on more senior leadership responsibilities.
Can Safety Coordinators work remotely, or is it primarily an on-site role?
While some administrative tasks can be done remotely, the Safety Coordinator role often requires a strong physical presence on-site. This is essential for conducting inspections, identifying hazards, leading safety training, and responding to incidents. Hybrid models are becoming more common, allowing for some remote work for planning or reporting. However, a fully remote Safety Coordinator position is rare due to the hands-on nature of ensuring workplace safety and compliance.
What are the biggest challenges or frustrations that Safety Coordinators commonly face?
The biggest challenges for Safety Coordinators include gaining employee buy-in for safety protocols, managing complex regulatory compliance, and balancing safety initiatives with operational demands. You must effectively communicate safety importance to diverse groups, from frontline workers to senior management. Additionally, staying updated on ever-changing safety regulations and effectively investigating incidents while maintaining a positive workplace culture can be demanding aspects of the role.
Related Careers
Explore similar roles that might align with your interests and skills:
Health And Safety Coordinator
A growing field with similar skill requirements and career progression opportunities.
Explore career guideSafety Manager
A growing field with similar skill requirements and career progression opportunities.
Explore career guideSafety Officer
A growing field with similar skill requirements and career progression opportunities.
Explore career guideSafety Specialist
A growing field with similar skill requirements and career progression opportunities.
Explore career guideSafety Supervisor
A growing field with similar skill requirements and career progression opportunities.
Explore career guideAssess your Safety Coordinator readiness
Understanding where you stand today is the first step toward your career goals. Our Career Coach helps identify skill gaps and create personalized plans.
Skills Gap Analysis
Get a detailed assessment of your current skills versus Safety Coordinator requirements. Our AI Career Coach identifies specific areas for improvement with personalized recommendations.
See your skills gapCareer Readiness Assessment
Evaluate your overall readiness for Safety Coordinator roles with our AI Career Coach. Receive personalized recommendations for education, projects, and experience to boost your competitiveness.
Assess your readinessSimple pricing, powerful features
Upgrade to Himalayas Plus and turbocharge your job search.
Himalayas
Himalayas Plus
Himalayas Max
Find your dream job
Sign up now and join over 100,000 remote workers who receive personalized job alerts, curated job matches, and more for free!
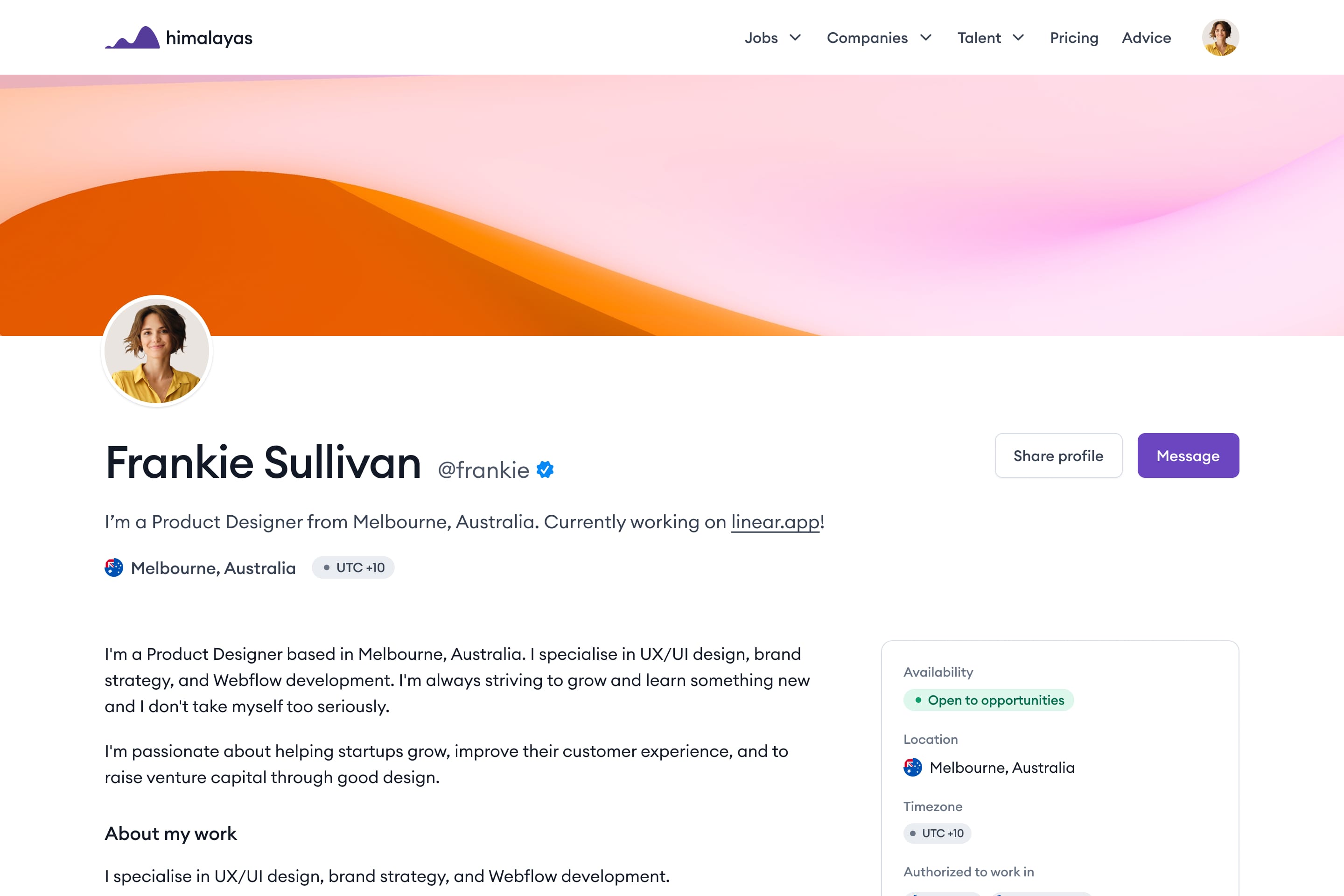