Complete Quality Systems Manager Career Guide
Quality Systems Managers are the architects of operational excellence, ensuring organizations consistently deliver products and services that meet rigorous standards. They design, implement, and maintain the frameworks that prevent defects and drive continuous improvement, directly impacting customer satisfaction and regulatory compliance.
This critical role demands a blend of technical expertise and leadership, making it ideal for professionals who thrive on optimizing processes and fostering a culture of quality across an enterprise.
Key Facts & Statistics
Median Salary
$115,600 USD
(U.S. Bureau of Labor Statistics, May 2023)
Range: $70k - $160k+ USD, varying significantly by industry, company size, and geographic location.
Growth Outlook
5%
as fast as average (U.S. Bureau of Labor Statistics, 2022-2032)
Annual Openings
≈17,000
openings annually (U.S. Bureau of Labor Statistics, 2022-2032)
Top Industries
Typical Education
Bachelor's degree in Engineering, Business Administration, or a related field. Many positions prefer or require a Master's degree, and certifications like ASQ Certified Quality Manager (CQM/OE) are highly valued.
What is a Quality Systems Manager?
A Quality Systems Manager is a specialized professional responsible for the design, implementation, maintenance, and continuous improvement of an organization's Quality Management System (QMS). This role ensures that a company’s processes, products, and services consistently meet or exceed established quality standards, regulatory requirements, and customer expectations. They act as the primary custodian of quality frameworks, such as ISO 9001, AS9100, or ISO 13485, ensuring certification readiness and ongoing compliance.
This role differs significantly from a Quality Control (QC) Inspector, who focuses on inspecting products at specific points, or a Quality Assurance (QA) Engineer, who designs tests and processes to prevent defects. The Quality Systems Manager operates at a strategic level, focusing on the overarching system that governs all quality activities, rather than individual product testing or process verification. They ensure the entire organization adheres to a structured approach to quality, driving systemic improvements and fostering a culture of quality from top to bottom.
What does a Quality Systems Manager do?
Key Responsibilities
- Develop and implement quality management system (QMS) processes and procedures in compliance with industry standards such as ISO 9001, AS9100, or ISO 13485.
- Lead internal and external audits, including preparing audit plans, conducting audits, and managing corrective actions to ensure ongoing compliance and identify areas for improvement.
- Manage the document control system, ensuring all quality-related documents, records, and forms are current, accessible, and properly archived.
- Facilitate root cause analysis and corrective/preventive action (CAPA) processes for non-conformances, customer complaints, and audit findings.
- Provide training and guidance to employees on quality system requirements, quality tools, and best practices to foster a culture of quality throughout the organization.
- Monitor key performance indicators (KPIs) related to quality, analyze trends, and report on the effectiveness of the QMS to senior management.
- Collaborate with cross-functional teams, including engineering, production, and supply chain, to integrate quality requirements into product development and operational processes.],
Work Environment
Quality Systems Managers typically work in an office setting, often within manufacturing plants, pharmaceutical companies, or aerospace facilities. Their work involves a mix of independent analysis, team collaboration, and occasional presence on the production floor for audits or process observations. The role often requires frequent interaction with all levels of the organization, from production staff to senior leadership, as well as external auditors and regulatory bodies. The pace of work can be steady but often includes periods of intense activity, especially during audits or when addressing critical non-conformances. While primarily office-based, some roles may involve occasional travel to supplier sites or other company locations. Remote work flexibility varies greatly by industry and company, but many aspects of the role can be managed digitally.
Tools & Technologies
Quality Systems Managers rely on a suite of software for effective QMS management. They frequently use Electronic Quality Management Systems (EQMS) platforms such as MasterControl, Sparta Systems TrackWise, or Veeva QualityOne for document control, CAPA management, audit management, and training tracking. Statistical analysis software like Minitab or JMP helps them analyze quality data and identify trends. Collaboration tools such as Microsoft Teams, Slack, or Zoom are essential for coordinating with various departments and remote teams. They also utilize enterprise resource planning (ERP) systems like SAP or Oracle to access production data and integrate quality processes. Proficiency in standard office suites like Microsoft Office (Excel, Word, PowerPoint) is fundamental for reporting and documentation.
Quality Systems Manager Skills & Qualifications
A Quality Systems Manager develops, implements, and maintains an organization's quality management system (QMS). This role ensures adherence to industry standards, regulatory requirements, and internal policies. Success hinges on a blend of technical expertise in quality methodologies and strong leadership capabilities.
Requirements for a Quality Systems Manager vary significantly based on the industry. For instance, pharmaceutical or medical device industries demand strict adherence to FDA regulations (e.g., cGMP, ISO 13485), while manufacturing might focus on ISO 9001 and Lean Six Sigma. Company size also plays a role; larger enterprises often require specialized knowledge in enterprise-level QMS software, whereas smaller companies might need someone with broad, hands-on experience across all QMS facets. Seniority also dictates the depth of expertise required. Entry-level quality professionals might focus on documentation and auditing, while senior managers lead strategic QMS improvements and regulatory compliance.
Formal education, practical experience, and relevant certifications all contribute significantly. A bachelor's degree is generally a prerequisite, but extensive practical experience can sometimes compensate. Certifications like ASQ Certified Quality Manager (CQM/OE) or Lean Six Sigma Black Belt demonstrate specialized knowledge and often accelerate career progression. The skill landscape is evolving, with increasing emphasis on data analytics for quality improvement and digital transformation of QMS processes. Understanding how to integrate quality systems with broader business processes, rather than treating them in isolation, is becoming crucial.
Education Requirements
Technical Skills
- Quality Management System (QMS) frameworks (e.g., ISO 9001, ISO 13485, AS9100)
- Regulatory compliance (e.g., FDA 21 CFR Part 820, cGMP, MDR, IVDR)
- Root Cause Analysis (RCA) methodologies (e.g., 5 Whys, Fishbone diagrams, FMEA)
- Statistical Process Control (SPC) and data analysis tools (e.g., Minitab, JMP)
- Lean Six Sigma principles and tools (e.g., Value Stream Mapping, Kaizen, DMAIC)
- Internal and external auditing principles and execution (e.g., ISO 19011)
- Document control and record management systems (e.g., electronic QMS software)
- Corrective and Preventive Actions (CAPA) management
- Supplier quality management and qualification processes
- Risk management principles and application within a QMS (e.g., ISO 14971)
- Calibration and metrology principles
- Proficiency in Microsoft Office Suite (Excel, Word, PowerPoint, Visio) for reporting and documentation
Soft Skills
- Leadership and Team Development: Essential for guiding quality teams, fostering a culture of quality, and mentoring junior quality professionals.
- Problem Solving and Analytical Thinking: Crucial for identifying root causes of quality issues, developing effective corrective actions, and driving continuous improvement.
- Communication and Presentation Skills: Important for articulating complex quality data, presenting QMS performance to management, and training employees on quality procedures.
- Stakeholder Management: Necessary for collaborating with cross-functional teams, external auditors, and regulatory bodies to ensure QMS alignment and compliance.
- Attention to Detail: Paramount for ensuring accuracy in documentation, audit findings, and compliance with intricate regulatory requirements.
- Adaptability and Change Management: Vital for navigating evolving regulations, implementing new quality standards, and integrating technological advancements into the QMS.
- Negotiation and Influence: Key for gaining buy-in for quality initiatives, resolving disagreements during audits, and advocating for necessary QMS resources.
- Ethical Conduct and Integrity: Fundamental for maintaining credibility, ensuring unbiased quality assessments, and upholding regulatory compliance standards without compromise.
How to Become a Quality Systems Manager
Becoming a Quality Systems Manager involves a blend of technical expertise and managerial acumen, with several pathways to entry. Individuals often transition from quality assurance, regulatory affairs, or engineering roles, bringing existing industry knowledge. A complete beginner might spend 2-3 years building foundational skills and experience, while someone with related experience could achieve this within 1-2 years.
Entry strategies vary significantly by industry and company size. Pharmaceutical and medical device companies, for example, typically require extensive regulatory knowledge (e.g., FDA, ISO 13485), while manufacturing might focus more on ISO 9001 and process optimization. Smaller companies might prefer a hands-on manager who can also perform audits, whereas larger corporations may seek specialists in specific quality system components.
Networking is crucial; attending industry conferences and joining professional organizations like ASQ provides valuable insights and connections. Many enter through internal promotions or by demonstrating strong analytical and problem-solving skills in previous roles. Building a portfolio of process improvement projects or audit experiences significantly enhances a candidate's profile.
Step 1
Step 2
Step 3
Step 4
Step 5
Step 6
Step 7
Education & Training Needed to Become a Quality Systems Manager
A Quality Systems Manager needs a blend of theoretical knowledge and practical application, focusing on implementing and maintaining robust quality management systems. Formal degree programs, typically in engineering, business administration, or quality management, provide a strong foundational understanding of organizational processes and statistical methods. A Bachelor's degree usually takes four years and costs $40,000-$100,000+, while a Master's can add two more years and $20,000-$60,000. These degrees offer comprehensive theoretical depth and are highly valued by larger, more traditional organizations.
Alternatively, specialized certifications and professional development courses offer focused, quicker pathways. These programs, often lasting weeks to months, cost $1,000-$10,000 and concentrate on specific quality methodologies like ISO 9001, Six Sigma, or Lean. Employers widely accept these credentials, especially for candidates with existing industry experience. Self-study, combined with practical experience, can also be effective but requires significant discipline; it might take 6-18 months and cost minimal amounts for books or online resources. The market values practical experience highly, often preferring candidates who can demonstrate hands-on application of quality principles over those with only theoretical knowledge.
Continuous learning is critical for Quality Systems Managers due to evolving industry standards and technologies. Professional organizations often provide ongoing training to keep skills current. Educational needs vary by industry; for instance, a Quality Systems Manager in pharmaceuticals requires different specialized knowledge than one in manufacturing. Cost-benefit considerations suggest that while degrees provide broad career mobility, certifications offer a more direct return on investment for specific skill gaps. Industry-specific accreditations, such as those from ASQ, are often benchmarks for program quality and professional competence.
Quality Systems Manager Salary & Outlook
Compensation for a Quality Systems Manager varies significantly based on several factors. Geographic location plays a crucial role, with higher salaries typically found in areas with a high concentration of life sciences, manufacturing, or technology companies, such as California, Massachusetts, or New Jersey, reflecting the higher cost of living and specialized industry demand. In contrast, regions with lower costs of living may offer comparatively lower salaries.
Experience, specialized knowledge in regulatory frameworks like ISO 9001, FDA regulations, or specific industry standards, and the complexity of the quality systems managed directly impact earning potential. For instance, managing global quality systems across multiple sites commands a premium. Total compensation packages often extend beyond base salary to include performance-based bonuses, stock options or equity in publicly traded companies, and comprehensive benefits. These benefits typically encompass health insurance, retirement plans like 401(k) with employer contributions, and allowances for professional development and certifications, which are vital for career advancement.
Industry-specific trends also influence salary growth. Highly regulated industries, such as pharmaceuticals, medical devices, and aerospace, generally offer higher compensation due to the critical nature and complexity of quality compliance. Company size and revenue also correlate with salary levels; larger, more established organizations often provide more lucrative compensation and benefits packages. Remote work, while offering flexibility, can sometimes lead to location-adjusted salaries, where compensation aligns with the cost of living in the employee's location rather than the company's headquarters. For international roles, salaries are benchmarked against local market rates, though USD figures offer a common reference point for global compensation discussions, emphasizing the importance of understanding local economic conditions.
Salary by Experience Level
Level | US Median | US Average |
---|---|---|
Associate Quality Systems Manager | $75k USD | $80k USD |
Quality Systems Manager | $100k USD | $105k USD |
Senior Quality Systems Manager | $130k USD | $135k USD |
Quality Systems Lead | $150k USD | $155k USD |
Director of Quality Systems | $185k USD | $190k USD |
VP of Quality Systems | $240k USD | $250k USD |
Market Commentary
The job market for Quality Systems Managers remains robust, driven by increasing regulatory scrutiny and the growing complexity of global supply chains across various industries. Industries such as pharmaceuticals, medical devices, biotechnology, and advanced manufacturing continue to experience high demand for skilled professionals who can ensure compliance and drive continuous improvement in quality processes. This demand is projected to grow by approximately 6-8% over the next five years, aligning with the overall growth in quality assurance and compliance roles. The push for digital transformation means that managers with expertise in electronic quality management systems (eQMS) and data analytics for quality metrics are particularly sought after.
Emerging opportunities include specialization in areas like cybersecurity within quality systems, ensuring data integrity in regulated environments, and managing quality for novel technologies such as AI-driven medical devices or advanced biologics. There is a strong supply of candidates with foundational quality experience, but a noticeable demand-supply imbalance exists for those with advanced certifications, specific regulatory expertise (e.g., EU MDR, IVDR), or experience in integrating quality systems with broader enterprise resource planning (ERP) platforms. Organizations are increasingly looking for Quality Systems Managers who can not only maintain compliance but also contribute strategically to operational efficiency and risk mitigation.
To future-proof this role, continuous learning in evolving regulations, automation technologies, and data science is essential. While automation and AI will streamline routine quality tasks, the strategic oversight, interpretation of complex regulations, and human judgment required to design, implement, and audit quality systems will remain critical. This profession is relatively recession-resistant due to the non-negotiable nature of regulatory compliance and product quality in regulated industries. Geographic hotspots for these roles include major biopharma hubs like Boston, San Francisco, and San Diego, as well as manufacturing centers in the Midwest and Southeast. Remote work is increasingly common, allowing companies to tap into a broader talent pool, though some roles still require on-site presence for audits or facility-specific quality oversight.
Quality Systems Manager Career Path
Career progression for a Quality Systems Manager involves a blend of technical expertise, regulatory knowledge, and leadership development. Professionals typically advance by demonstrating increasing proficiency in designing, implementing, and maintaining robust quality management systems (QMS) compliant with industry standards like ISO, FDA, or specific sector regulations.
Advancement can occur through individual contributor (IC) tracks, focusing on specialized QMS areas or complex system architecture, or through management tracks, which involve leading teams and overseeing broader quality initiatives. Factors like company size, industry (e.g., pharmaceutical, medical device, aerospace), and economic conditions significantly influence advancement speed and specific opportunities. Larger corporations often have more structured progression paths, while startups may offer quicker advancement but with broader responsibilities.
Continuous learning, pursuing relevant certifications (e.g., ASQ certifications, Lead Auditor), and active networking within quality assurance communities are vital. Lateral movements might involve transitioning between different industries or specializing in areas like supplier quality, validation, or compliance. Key milestones include successful QMS audits, leading major system implementations, and achieving significant improvements in quality metrics. Career pivots could lead to roles in regulatory affairs, operational excellence, or general management, leveraging the strong foundational understanding of processes and compliance.
Associate Quality Systems Manager
0-2 yearsKey Focus Areas
Quality Systems Manager
2-5 yearsKey Focus Areas
Senior Quality Systems Manager
5-8 yearsKey Focus Areas
Quality Systems Lead
8-12 yearsKey Focus Areas
Director of Quality Systems
12-18 yearsKey Focus Areas
VP of Quality Systems
18+ yearsKey Focus Areas
Associate Quality Systems Manager
0-2 yearsSupport the implementation and maintenance of the quality management system. Assist with documentation control, record management, and basic quality system audits. Gather data for quality metrics and contribute to process improvement initiatives under direct supervision. Participate in internal and external audits by preparing documentation.
Key Focus Areas
Develop foundational knowledge of QMS principles, relevant regulations (e.g., ISO 9001, 13485, FDA 21 CFR Part 820), and internal company procedures. Focus on accurate documentation practices, data integrity, and learning to support internal and external audits. Understand the company's products and processes.
Quality Systems Manager
2-5 yearsManage specific elements of the quality management system, such as CAPA, change control, or document control. Lead internal audits and support external regulatory inspections by providing expert guidance and documentation. Identify non-conformances and propose solutions, contributing to QMS effectiveness and compliance.
Key Focus Areas
Deepen understanding of specific regulatory requirements pertinent to the industry. Enhance skills in root cause analysis, corrective and preventive actions (CAPA), and change control. Develop communication skills for interacting with cross-functional teams and external auditors. Pursue relevant certifications like ASQ Certified Quality Auditor (CQA).
Senior Quality Systems Manager
5-8 yearsLead major QMS projects, including system upgrades or new module implementations. Oversee multiple QMS elements and ensure their integration and compliance. Provide expert guidance during regulatory inspections and customer audits. Mentor junior quality systems personnel and drive continuous improvement within the QMS.
Key Focus Areas
Cultivate strong analytical and problem-solving skills for complex QMS challenges. Develop project management capabilities to lead QMS improvement initiatives. Strengthen leadership skills to mentor junior team members and influence stakeholders. Consider advanced certifications like ASQ Certified Quality Manager (CQM/OE).
Quality Systems Lead
8-12 yearsAct as a subject matter expert across all QMS areas, providing strategic direction and technical leadership. Drive the overall effectiveness and compliance of the QMS, ensuring alignment with organizational goals. Lead QMS training programs and represent the quality function in cross-functional strategic initiatives. May supervise a small team.
Key Focus Areas
Focus on strategic QMS planning and alignment with business objectives. Develop advanced risk management and mitigation strategies within the quality system. Enhance cross-functional leadership and stakeholder management abilities. Begin to engage in industry best practices and contribute to quality standards development.
Director of Quality Systems
12-18 yearsResponsible for the strategic direction, development, and oversight of the entire quality management system across the organization. Ensure global regulatory compliance and lead all interactions with regulatory agencies during inspections. Build and lead a team of quality systems professionals, setting departmental goals and budgets. Influence overall organizational quality culture.
Key Focus Areas
Develop executive leadership skills, including strategic planning, financial acumen, and organizational development. Focus on building high-performing teams and fostering a strong quality culture. Engage with industry groups and regulatory bodies to anticipate future trends and requirements. Master negotiation and conflict resolution.
VP of Quality Systems
18+ yearsProvide executive leadership for all quality systems initiatives, integrating them with overall business strategy. Responsible for the global quality management system, ensuring its robustness, efficiency, and scalability. Drive continuous improvement and innovation in quality processes to achieve world-class quality performance and regulatory excellence. Serve as a key member of the executive leadership team, influencing company-wide decisions.
Key Focus Areas
Focus on enterprise-level quality strategy, innovation, and competitive advantage through quality systems. Develop expertise in global regulatory landscapes and emerging technologies impacting quality. Cultivate strong executive presence, board-level communication, and cross-organizational influence. Drive a culture of continuous improvement and excellence.
Job Application Toolkit
Ace your application with our purpose-built resources:
Quality Systems Manager Resume Examples
Proven layouts and keywords hiring managers scan for.
View examplesQuality Systems Manager Cover Letter Examples
Personalizable templates that showcase your impact.
View examplesTop Quality Systems Manager Interview Questions
Practice with the questions asked most often.
View examplesQuality Systems Manager Job Description Template
Ready-to-use JD for recruiters and hiring teams.
View examplesGlobal Quality Systems Manager Opportunities
A Quality Systems Manager's role translates consistently across global industries, focusing on ISO standards and regulatory compliance. Global demand remains strong, particularly in manufacturing, pharmaceuticals, and technology, as companies prioritize robust quality frameworks. Regulatory nuances vary by region, but core principles of process improvement and audit readiness are universal. Professionals seek international roles for specialized industry exposure, higher earning potential, or diverse cultural experiences. Certifications like ASQ CMQ/OE or ISO Lead Auditor enhance global mobility significantly.
Global Salaries
Salaries for Quality Systems Managers vary widely by region, reflecting local economies and industry demands. In North America, particularly the USA, annual salaries range from $90,000 to $130,000 USD, with higher figures in biotech or aerospace hubs. Canadian salaries typically fall between $80,000 and $115,000 CAD. These figures often include comprehensive benefits packages like health insurance, retirement plans, and paid time off.
European salaries show significant diversity. In Germany, a Quality Systems Manager earns €65,000 to €95,000 EUR (approx. $70,000-$103,000 USD), while in the UK, the range is £50,000 to £75,000 GBP (approx. $63,000-$95,000 USD). Scandinavian countries offer similar or slightly higher compensation but with higher costs of living. European compensation frequently includes strong social security contributions and generous vacation allowances.
In Asia-Pacific, salaries are generally lower but offer strong purchasing power in certain markets. Singapore pays S$80,000 to S$120,000 SGD (approx. $59,000-$89,000 USD), while Australia offers A$90,000 to A$130,000 AUD (approx. $60,000-$87,000 USD). India's range is significantly lower, typically ₹1,000,000 to ₹2,500,000 INR (approx. $12,000-$30,000 USD), but with a very low cost of living. Tax implications and take-home pay differ substantially; some countries have higher income taxes but offer universal healthcare or other public services. Experience and specific industry certifications can notably increase international compensation.
Remote Work
International remote work for Quality Systems Managers is evolving, though less prevalent than in purely digital roles. Companies increasingly hire for global remote positions, especially for maintaining documentation, auditing processes, or implementing new systems that do not require physical presence. Legal and tax complexities arise when working remotely across borders; individuals must understand their tax residency and employer's compliance obligations.
Time zone differences present a significant challenge for international team collaboration, requiring flexible work schedules. Digital nomad visas, offered by countries like Portugal or Spain, can facilitate long-term remote work for Quality Systems Managers. Employers often provide equipment and ensure secure network access for international remote staff. Remote work can impact salary expectations, with some companies adjusting pay based on the employee's location, leading to geographic arbitrage opportunities.
Visa & Immigration
Quality Systems Managers typically pursue skilled worker visas for international roles. Popular destinations include Canada, Australia, Germany, and the UK, which have points-based or employer-sponsored systems. Requirements often include a relevant bachelor's degree, several years of experience, and a job offer from a local employer. Credential recognition for engineering or science degrees is usually straightforward, but specific industry certifications may be mandatory.
Visa application timelines vary from a few months to over a year, depending on the country and visa type. Many skilled worker visas offer pathways to permanent residency after a specified period of employment. Language proficiency tests, such as IELTS for English-speaking countries or Goethe-Zertifikat for Germany, are frequently required. Some countries prioritize roles in critical sectors, which may include specific quality management positions in healthcare or advanced manufacturing. Family members, like spouses and dependent children, can typically join the primary visa holder.
2025 Market Reality for Quality Systems Managers
Understanding current market realities is crucial for Quality Systems Managers. The landscape has evolved significantly since 2023, shaped by post-pandemic operational shifts and the rapid integration of AI.
Broader economic factors, such as inflation and supply chain disruptions, directly influence how companies invest in quality infrastructure. Market conditions for this role vary by experience level, with senior professionals facing different dynamics than those at entry or mid-level. Geographic location and company size also play a substantial role in job availability and required skill sets. This analysis provides an honest assessment of these complex dynamics.
Current Challenges
Quality Systems Managers face heightened competition, especially for senior roles, due to a market correction. Economic uncertainty causes companies to delay hiring, particularly for roles perceived as overhead rather than direct revenue generators.
A critical skill gap exists in integrating traditional quality management with AI-driven process optimization. Job seekers without this hybrid expertise find fewer opportunities.
Growth Opportunities
Strong demand persists for Quality Systems Managers capable of leading digital transformation within quality departments. Roles focused on AI integration, data-driven quality improvement, and predictive analytics are emerging as key opportunities. Professionals who can bridge the gap between traditional quality management and cutting-edge technology find themselves in high demand.
Underserved markets include small to medium-sized enterprises (SMEs) struggling to adapt to evolving regulatory landscapes and incorporate new technologies. These companies often seek consultants or fractional managers to establish robust quality systems. Experience with specific industry regulations, such as FDA, ISO 13485, or AS9100, combined with a strong understanding of AI's application in quality, provides a significant competitive advantage.
Strategic career moves involve acquiring certifications in AI ethics, data governance, or advanced process automation. Sectors like biotech, advanced manufacturing, and sustainable energy production are expanding and require sophisticated quality systems, offering stable opportunities. Timing investments in new skills now prepares professionals for future growth cycles, positioning them as essential leaders in an increasingly automated quality landscape.
Current Market Trends
Demand for Quality Systems Managers remains stable but is not experiencing rapid growth as of 2025. Companies prioritize optimizing existing quality frameworks rather than expanding teams. This focus reflects a broader economic caution after 2023's market adjustments.
Recent industry shifts emphasize digital transformation within quality assurance. Generative AI and advanced analytics are reshaping how quality systems are designed, monitored, and improved. Employers now seek managers who can integrate AI tools into ISO, Six Sigma, and other established methodologies. This shift means the role moves beyond compliance to include strategic technological adoption.
Hiring criteria increasingly favor candidates with expertise in data analytics, process automation, and change management. Traditional experience in auditing and documentation is no longer sufficient. Salary trends show a slight upward pressure for those with advanced digital skills, while salaries for managers without these capabilities remain flat or see minor increases. Market saturation is evident at the mid-career level for those lacking modern tech proficiencies.
Geographically, demand is strongest in highly regulated sectors like pharmaceuticals, aerospace, and medical devices, particularly in established manufacturing hubs. Remote work options are less common for this role compared to others, as on-site presence for system implementation and auditing is often required. There are no significant seasonal hiring patterns for this position; hiring aligns with project cycles or regulatory mandates.
Emerging Specializations
Technological advancements and evolving industry standards consistently create new specialization opportunities for Quality Systems Managers. Understanding these shifts and positioning oneself early in emerging areas is crucial for career advancement from 2025 onwards. Such foresight allows professionals to become early experts in high-demand niches, often commanding premium compensation and accelerated career growth.
While established quality specializations remain vital, focusing on cutting-edge areas offers a distinct competitive advantage. These emerging fields, driven by innovations in data analytics, AI, and sustainability, represent the next wave of significant job opportunities. They typically transition from niche interests to mainstream demand within three to five years, creating a strategic window for early adoption.
Pursuing emerging specializations involves a balance of risk and reward. Early movers face the challenge of defining nascent roles and developing new methodologies. However, the reward lies in shaping industry best practices and securing leadership positions as these areas mature. Strategic career planning dictates exploring these future-oriented paths to ensure long-term relevance and impactful contributions within quality management.
AI-Driven Predictive Quality Manager
This specialization focuses on integrating AI and machine learning tools into quality management systems. It involves designing, implementing, and validating AI-driven solutions for predictive quality, automated defect detection, and process optimization. The goal is to leverage AI to identify potential quality issues before they arise and to enhance decision-making accuracy within complex manufacturing or service environments.
Sustainability & Circular Economy Quality Systems Lead
This area emphasizes embedding sustainability and environmental compliance directly into quality processes. It involves developing and managing quality systems that ensure products and operations meet rigorous environmental standards, minimize waste, and adhere to circular economy principles. This specialization is critical for companies aiming to reduce their ecological footprint and meet increasing regulatory and consumer demands for green products.
Adaptive Quality for On-Demand Manufacturing
This specialization addresses the unique quality challenges posed by highly personalized and on-demand production, such as 3D printing and customized manufacturing. It involves developing flexible quality frameworks that can adapt to variable product specifications and small batch sizes while maintaining high standards. This role ensures that quality control processes are scalable and effective in dynamic, agile production environments.
Data Integrity & Governance Quality Manager
This emerging field focuses on ensuring the quality and integrity of data used within quality management systems, especially in highly regulated industries. It involves establishing robust data governance frameworks, validating data sources, and implementing data quality controls to support accurate analytics and regulatory compliance. This specialization is crucial for reliable decision-making and audit readiness in data-intensive environments.
Digital Ecosystem Quality Assurance Manager
This specialization involves managing the quality aspects of interconnected digital ecosystems, particularly in smart factories or IoT-enabled products. It focuses on ensuring the reliability, security, and performance of data flows and integrated systems that impact product or service quality. This role extends traditional quality control to encompass the entire digital value chain, from sensor data to cloud analytics.
Pros & Cons of Being a Quality Systems Manager
Making an informed career decision requires a clear understanding of both the benefits and challenges associated with a specific role. Career experiences can vary significantly based on company culture, the specific industry sector, the specialization area within quality systems, and individual preferences. For instance, a Quality Systems Manager in pharmaceuticals will face different daily realities than one in automotive manufacturing. Furthermore, the pros and cons may shift at different career stages; early in a career, learning demands might be a challenge, while at a senior level, strategic influence becomes a major pro. Some aspects, such as the emphasis on meticulous detail, might be a pro for an organized individual but a con for someone who prefers less structure. This assessment aims to provide an honest, balanced perspective to help set realistic expectations for a Quality Systems Manager role.
Pros
- Quality Systems Managers play a critical role in ensuring product safety and regulatory compliance, directly contributing to consumer trust and company reputation. This position offers excellent job stability and consistent demand across various highly regulated industries, including pharmaceuticals, medical devices, aerospace, and food production. The role provides opportunities for significant intellectual challenge, involving complex problem-solving to design, implement, and improve robust quality management systems. Quality Systems Managers often have a broad impact across an organization, collaborating with multiple departments from R&D to production and sales, which fosters a holistic business understanding. There are clear pathways for career advancement into senior management, director-level quality roles, or even consulting, given the specialized expertise gained. The work involves developing highly transferable skills in auditing, risk management, process improvement, and regulatory interpretation, which are valuable in many different professional contexts. This position typically offers competitive salaries and benefits, reflecting the specialized knowledge and critical responsibility involved in maintaining high-quality standards and avoiding costly non-compliance issues.
- Quality Systems Managers play a critical role in ensuring product safety and regulatory compliance, directly contributing to consumer trust and company reputation.
- This position offers excellent job stability and consistent demand across various highly regulated industries, including pharmaceuticals, medical devices, aerospace, and food production.
- The role provides opportunities for significant intellectual challenge, involving complex problem-solving to design, implement, and improve robust quality management systems.
- Quality Systems Managers often have a broad impact across an organization, collaborating with multiple departments from R&D to production and sales, which fosters a holistic business understanding.
- There are clear pathways for career advancement into senior management, director-level quality roles, or even consulting, given the specialized expertise gained.
- The work involves developing highly transferable skills in auditing, risk management, process improvement, and regulatory interpretation, which are valuable in many different professional contexts.
Cons
- Quality Systems Managers often face significant pressure to ensure compliance with stringent industry regulations and internal policies, where any lapse can result in serious consequences like product recalls or regulatory fines. This role frequently involves navigating complex bureaucratic processes and extensive documentation, which can be time-consuming and mentally taxing as precision is paramount. Balancing the demands of maintaining quality standards with business objectives, such as cost efficiency and production timelines, can create internal conflict and require constant negotiation. Dealing with resistance to change from employees or departments accustomed to older processes is common, requiring strong change management and communication skills to implement new quality systems effectively. The work can become repetitive, focusing on audits, documentation review, and corrective actions, which may not appeal to those seeking highly dynamic or creative roles. Staying updated with evolving quality standards, regulations, and technologies requires continuous professional development and learning, adding to the workload outside of core responsibilities. While critical, the role's impact is often indirect, meaning Quality Systems Managers may not see the immediate, tangible results of their efforts, which can be less fulfilling for some individuals.
- Quality Systems Managers often face significant pressure to ensure compliance with stringent industry regulations and internal policies, where any lapse can result in serious consequences like product recalls or regulatory fines.
- This role frequently involves navigating complex bureaucratic processes and extensive documentation, which can be time-consuming and mentally taxing as precision is paramount.
- Balancing the demands of maintaining quality standards with business objectives, such as cost efficiency and production timelines, can create internal conflict and require constant negotiation.
- Dealing with resistance to change from employees or departments accustomed to older processes is common, requiring strong change management and communication skills to implement new quality systems effectively.
- The work can become repetitive, focusing on audits, documentation review, and corrective actions, which may not appeal to those seeking highly dynamic or creative roles.
- Staying updated with evolving quality standards, regulations, and technologies requires continuous professional development and learning, adding to the workload outside of core responsibilities.
Frequently Asked Questions
Quality Systems Managers navigate unique challenges in ensuring organizational standards and compliance. This section addresses common questions about entering this critical role, from required certifications and educational paths to managing complex regulatory frameworks and fostering a culture of quality across an enterprise.
What educational background and certifications are essential to become a Quality Systems Manager?
A bachelor's degree in a scientific, engineering, or business-related field is typically required, with a focus on quality management or a related discipline. Many successful Quality Systems Managers also hold certifications like ASQ Certified Quality Manager (CQM/OE) or ISO 9001 Lead Auditor, which demonstrate specialized knowledge and commitment to the field. Practical experience in quality assurance or a regulated industry is also crucial.
How long does it typically take to transition into a Quality Systems Manager role from an entry-level position?
Transitioning into this role usually takes 3-7 years, depending on your starting point. If you have a relevant degree, you might start as a Quality Engineer or Auditor, gaining experience with quality tools, regulations, and system implementation. Advancing to a management role requires demonstrating leadership capabilities, project management skills, and a deep understanding of various quality standards.
What are the typical salary expectations for a Quality Systems Manager, and what factors influence them?
Salaries for Quality Systems Managers vary significantly by industry, company size, and location. Entry-level managers might earn $70,000-$90,000 annually, while experienced professionals in highly regulated sectors like pharmaceuticals or aerospace can command $100,000-$150,000 or more. Performance bonuses and benefits packages often add to the total compensation.
What is the typical work-life balance like for a Quality Systems Manager, given the responsibilities?
The work-life balance can fluctuate. During audits, system implementations, or issue resolution, the role might demand longer hours. However, outside of critical periods, the work often involves strategic planning, process improvement, and team leadership, which can offer more predictable hours. The ability to manage multiple projects and prioritize effectively helps maintain balance.
Is the demand for Quality Systems Managers growing, and what does job security look like in this field?
The demand for Quality Systems Managers remains strong across diverse industries, including manufacturing, healthcare, technology, and food production. Companies increasingly recognize the importance of robust quality systems for compliance, efficiency, and reputation. Professionals with expertise in specific regulatory frameworks, like FDA or ISO, are particularly sought after, indicating good job security.
What are the typical career growth opportunities and advancement paths for a Quality Systems Manager?
Career growth paths include advancing to Senior Quality Systems Manager, Director of Quality, or even Vice President of Quality Assurance. Some professionals specialize in consulting, helping multiple organizations establish and improve their quality systems. Opportunities also exist to move into broader operational management roles, leveraging their process optimization and compliance expertise.
What are the biggest challenges or frustrations that Quality Systems Managers commonly face?
A significant challenge is keeping up with evolving regulations and standards across different industries and geographies. Quality Systems Managers must also effectively influence various departments to adopt and adhere to quality processes, which requires strong communication and change management skills. Balancing compliance with operational efficiency can also be a complex task.
Can Quality Systems Managers work remotely, or is on-site presence typically required for this role?
Remote work feasibility for Quality Systems Managers varies by company and industry. While some tasks, like document control, training, and virtual audits, can be performed remotely, on-site presence is often required for physical inspections, direct team leadership, and collaboration with production or operations teams. Hybrid models are becoming more common, offering flexibility.
Related Careers
Explore similar roles that might align with your interests and skills:
QA Manager
A growing field with similar skill requirements and career progression opportunities.
Explore career guideQuality Assurance Director
A growing field with similar skill requirements and career progression opportunities.
Explore career guideQuality Assurance Manager
A growing field with similar skill requirements and career progression opportunities.
Explore career guideQuality Control Manager
A growing field with similar skill requirements and career progression opportunities.
Explore career guideQuality Manager
A growing field with similar skill requirements and career progression opportunities.
Explore career guideAssess your Quality Systems Manager readiness
Understanding where you stand today is the first step toward your career goals. Our Career Coach helps identify skill gaps and create personalized plans.
Skills Gap Analysis
Get a detailed assessment of your current skills versus Quality Systems Manager requirements. Our AI Career Coach identifies specific areas for improvement with personalized recommendations.
See your skills gapCareer Readiness Assessment
Evaluate your overall readiness for Quality Systems Manager roles with our AI Career Coach. Receive personalized recommendations for education, projects, and experience to boost your competitiveness.
Assess your readinessSimple pricing, powerful features
Upgrade to Himalayas Plus and turbocharge your job search.
Himalayas
Himalayas Plus
Himalayas Max
Find your dream job
Sign up now and join over 100,000 remote workers who receive personalized job alerts, curated job matches, and more for free!
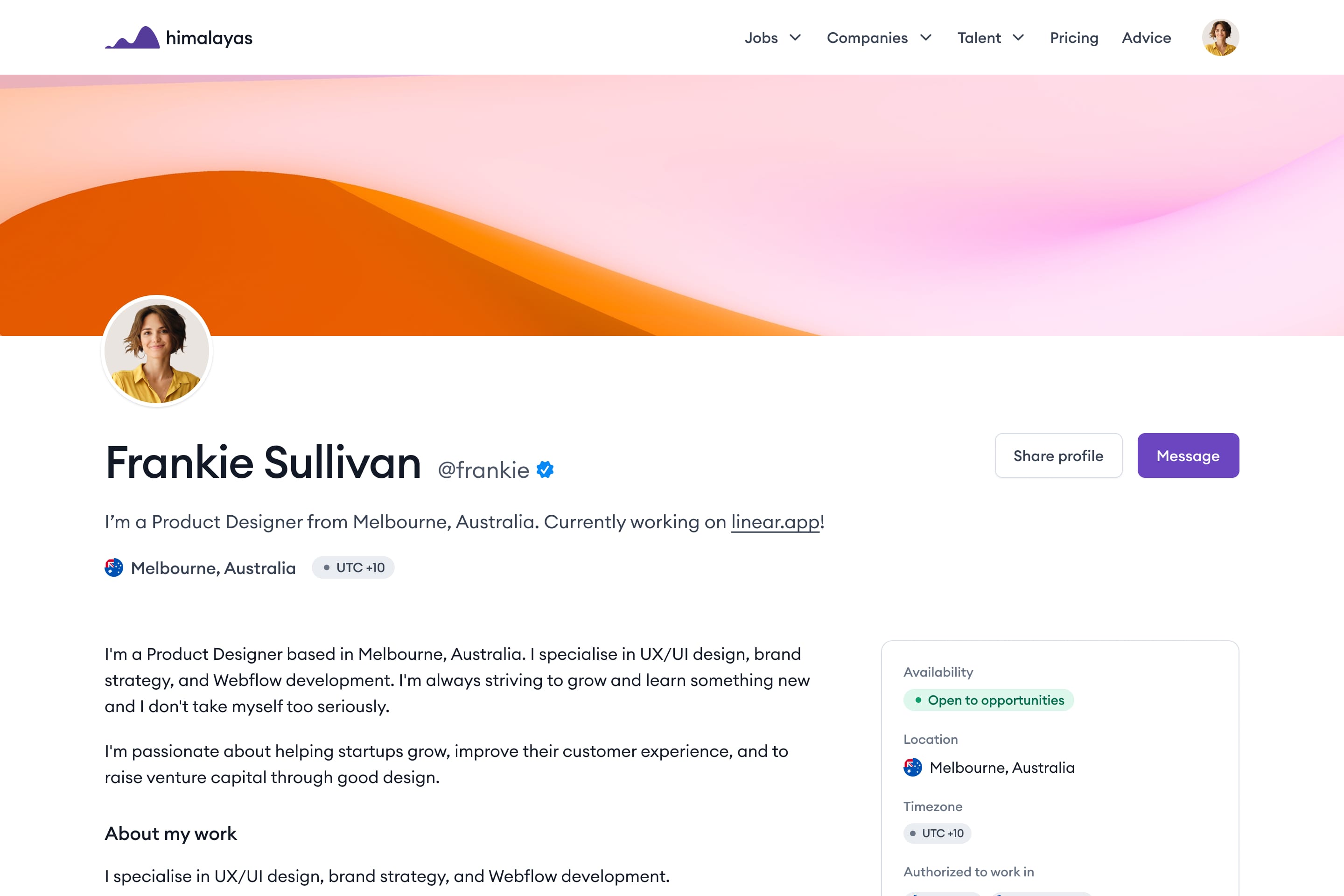