Complete Production Scheduler Career Guide
Production schedulers are the architects of efficiency in manufacturing, meticulously planning and optimizing the flow of goods to meet demand while minimizing waste. You'll orchestrate resources, materials, and labor, ensuring products move seamlessly from raw materials to finished goods. This critical role directly impacts a company's profitability and delivery reliability, offering a dynamic career path in a wide array of industries.
Key Facts & Statistics
Median Salary
$64,740 USD
(U.S. Bureau of Labor Statistics, May 2023)
Range: $40k - $95k+ USD, varying by experience, industry, and location
Growth Outlook
1%
as fast as average (U.S. Bureau of Labor Statistics, 2022-2032)
Annual Openings
≈17,200
openings annually (U.S. Bureau of Labor Statistics, 2022-2032)
Top Industries
Typical Education
High school diploma or equivalent, though an associate's or bachelor's degree in supply chain management or business is increasingly preferred; relevant certifications like APICS CSCP or CPIM can enhance prospects.
What is a Production Scheduler?
A Production Scheduler is a critical professional responsible for optimizing the flow of goods through a manufacturing process. This role involves planning, coordinating, and overseeing the entire production timeline, from raw material arrival to finished product dispatch. They ensure that production targets are met efficiently, resources are utilized effectively, and customer delivery dates are honored.
This role differs significantly from a Production Manager, who focuses more on supervising staff and day-to-day operational execution. While a Production Manager ensures the work gets done, a Production Scheduler designs the detailed plan for how and when it gets done. They are the architects of the production timeline, balancing demand, capacity, and material availability to create a feasible and efficient schedule that drives the manufacturing process forward.
What does a Production Scheduler do?
Key Responsibilities
- Develop and maintain detailed production schedules for manufacturing operations, ensuring timely delivery of goods.
- Monitor production progress daily, identifying potential bottlenecks or delays and implementing corrective actions promptly.
- Coordinate with procurement to ensure the availability of raw materials and components needed for scheduled production runs.
- Communicate schedule changes and production updates to relevant departments, including sales, operations, and logistics.
- Analyze production data to identify opportunities for efficiency improvements and optimize resource allocation.
- Adjust production plans in response to unforeseen events such as equipment breakdowns, material shortages, or rush orders.
- Collaborate with quality control to integrate inspection and testing phases into the production timeline effectively.
Work Environment
Production Schedulers typically work in an office setting within a manufacturing facility, often close to the production floor. This proximity allows for quick communication and observation of operations. The work environment is generally fast-paced and dynamic, requiring constant adaptation to changing priorities and unexpected challenges. They collaborate extensively with factory managers, procurement specialists, logistics teams, and sales personnel. While most work occurs during standard business hours, occasional extended hours or on-call availability may be necessary to resolve urgent production issues. Remote work is less common due to the need for close interaction with physical production processes.
Tools & Technologies
Production Schedulers regularly use Enterprise Resource Planning (ERP) systems like SAP, Oracle, or Microsoft Dynamics 365 to manage production orders, inventory, and resource allocation. They also employ Manufacturing Execution Systems (MES) to track real-time production data and visualize plant floor activities. Spreadsheet software such as Microsoft Excel or Google Sheets remains crucial for detailed analysis, custom reporting, and what-if scenarios. Furthermore, they utilize planning and scheduling software (e.g., Asprova, Preactor) for advanced optimization. Communication tools like Microsoft Teams or Slack facilitate collaboration, while business intelligence dashboards provide insights into operational performance.
Production Scheduler Skills & Qualifications
A Production Scheduler plays a critical role in manufacturing and supply chain operations, ensuring products are manufactured efficiently and delivered on time. This position requires a blend of analytical rigor, meticulous planning, and practical understanding of production processes. Requirements for a Production Scheduler vary significantly based on the industry, company size, and the complexity of the manufacturing environment.
For entry-level positions, companies often prioritize candidates with a foundational understanding of supply chain principles and strong data analysis skills. As individuals advance to senior or lead scheduler roles, the emphasis shifts towards strategic planning, optimization, and the ability to manage complex, multi-site production schedules. Certifications in supply chain management or production planning, such as APICS CPIM (Certified in Production and Inventory Management), add substantial value and are often preferred or even required for mid-to-senior level roles, validating specialized knowledge beyond a traditional degree.
Formal education provides a strong theoretical base, but practical experience within a manufacturing or logistics setting is equally, if not more, crucial. Many successful Production Schedulers enter the field through operational roles, gaining firsthand knowledge of production constraints and opportunities. The skill landscape for Production Schedulers is evolving with the increasing adoption of advanced planning systems (APS) and AI-driven optimization tools. Schedulers must continuously adapt to new technologies and integrate data analytics into their daily decision-making, balancing traditional scheduling methods with modern predictive capabilities.
Education Requirements
Technical Skills
- ERP/MRP Systems (e.g., SAP PP, Oracle SCM, Microsoft Dynamics 365) for production planning and control
- Advanced Planning and Scheduling (APS) software (e.g., Siemens Opcenter APS, Asprova, Kinaxis RapidResponse)
- Data analysis and reporting tools (e.g., Microsoft Excel, Google Sheets) for forecasting and performance tracking
- Database querying and reporting (basic SQL or equivalent) for extracting and manipulating production data
- Inventory management principles and techniques (e.g., JIT, safety stock, reorder points)
- Forecasting methodologies (e.g., demand forecasting, sales and operations planning - S&OP)
- Capacity planning and finite scheduling techniques to optimize resource utilization
- Lean manufacturing and Six Sigma principles for process improvement and waste reduction
- Understanding of Bill of Materials (BOM) and routing structures
- Logistics and transportation planning basics for coordinating material flow and finished goods delivery
Soft Skills
- Problem-solving and Analytical Thinking: Production Schedulers must identify and resolve scheduling conflicts, bottlenecks, and unforeseen disruptions by analyzing data and developing effective solutions.
- Attention to Detail and Accuracy: Precise data entry, meticulous planning, and careful monitoring are essential to prevent errors that could lead to production delays or inefficiencies.
- Time Management and Prioritization: Schedulers juggle multiple demands and deadlines, requiring strong organizational skills to prioritize tasks and manage time effectively.
- Communication and Collaboration: Effective communication with production, sales, procurement, and logistics teams is vital for coordinating schedules, managing expectations, and resolving issues.
- Adaptability and Flexibility: Production environments are dynamic; schedulers must adjust plans quickly in response to changes in demand, material availability, or equipment breakdowns.
- Proactive Planning and Foresight: A Production Scheduler anticipates potential issues before they arise, developing contingency plans to maintain smooth operations.
- Stress Management and Resilience: The role involves managing tight deadlines and unexpected challenges, requiring the ability to remain calm and effective under pressure.
- Negotiation and Influence: Schedulers often need to negotiate with various departments to secure resources or adjust timelines, requiring persuasive communication skills to achieve optimal outcomes for production goals and customer delivery dates.
How to Become a Production Scheduler
Breaking into Production Scheduling involves a blend of analytical skills, process understanding, and practical experience. Traditional paths often include a degree in supply chain management, operations, or industrial engineering. However, many successful schedulers transition from roles like production associate, inventory control specialist, or logistics coordinator, leveraging their hands-on factory or warehouse experience.
The timeline for entry varies significantly; a complete beginner might need 12-18 months to gain foundational knowledge and relevant certifications, while someone in a related manufacturing role could transition in 3-6 months. Entry strategies differ by industry, with discrete manufacturing often prioritizing technical system knowledge, and process manufacturing valuing deep understanding of material flow. Smaller companies may seek generalists, while larger corporations prefer specialists with experience in specific ERP systems.
Misconceptions include believing a scheduler only creates a plan; the role also involves constant problem-solving, adapting to disruptions, and communicating across departments. Networking within manufacturing and supply chain communities is crucial for uncovering opportunities and gaining insights. The hiring landscape values adaptability and proficiency with planning software, reflecting a shift towards more data-driven and agile production environments. Barriers can include a lack of specific system experience or industry knowledge, which targeted training and project work can help overcome.
Step 1
Step 2
Step 3
Step 4
Step 5
Step 6
Education & Training Needed to Become a Production Scheduler
A Production Scheduler's role involves optimizing manufacturing processes, managing inventory flow, and ensuring timely product delivery. This requires a blend of analytical skills, knowledge of supply chain principles, and familiarity with production planning software. Formal degrees in Supply Chain Management, Industrial Engineering, or Operations Management provide a strong theoretical foundation, typically costing $40,000-$120,000+ for a four-year bachelor's degree. These programs often take four years to complete and are highly regarded by larger corporations and those seeking leadership roles.
Alternatively, many successful Production Schedulers enter the field through professional certifications or specialized online courses, which focus on practical application and industry-specific tools. These alternative paths can range from $1,000 to $10,000 and typically take 3 to 12 months to complete. Employers increasingly value certifications from recognized industry bodies like APICS (now ASCM) as they demonstrate direct competency in production and inventory management. Self-study, while cost-effective, requires significant discipline and often benefits from structured course materials or mentorship.
Continuous learning is crucial in this field, especially as new technologies like AI and advanced analytics integrate into production planning. Practical experience, often gained through internships or entry-level roles, complements theoretical knowledge significantly. While a degree provides a broad understanding, certifications and hands-on experience often carry more weight for immediate job placement. Different specializations within production scheduling, such as lean manufacturing or demand planning, may require specific additional training. The cost-benefit of a degree versus certification depends on career aspirations and desired employer types.
Production Scheduler Salary & Outlook
Compensation for a Production Scheduler varies significantly based on several key factors. Geographic location plays a crucial role; major industrial hubs or areas with high manufacturing activity often offer higher salaries due to increased demand and cost of living. Conversely, regions with lower living expenses may see more modest compensation figures. These figures are generally presented in USD, but international markets will have their own distinct salary scales.
Experience, specialized skills, and industry knowledge dramatically influence earning potential. A Production Scheduler with expertise in advanced planning systems (APS) or specific ERP modules like SAP PP will command higher salaries. The total compensation package extends beyond base salary to include performance bonuses, profit sharing, and comprehensive benefits such as health insurance, retirement contributions, and paid time off. Some roles in larger corporations might also offer stock options or professional development allowances.
Industry-specific trends also affect pay; sectors like automotive, aerospace, or pharmaceuticals, which have complex supply chains and high-value products, typically offer more competitive compensation. Company size can also impact earnings, with larger enterprises often providing more structured pay scales and benefit programs. Strong negotiation skills, particularly when highlighting direct contributions to efficiency and cost savings, can significantly increase a Production Scheduler's starting salary and subsequent raises. Remote work opportunities are emerging, which can influence geographic arbitrage, allowing individuals in high-cost areas to work for companies in lower-cost regions, or vice versa, impacting salary expectations.
Salary by Experience Level
Level | US Median | US Average |
---|---|---|
Junior Production Scheduler | $58k USD | $62k USD |
Production Scheduler | $70k USD | $75k USD |
Senior Production Scheduler | $85k USD | $90k USD |
Lead Production Scheduler | $100k USD | $105k USD |
Production Planning Manager | $120k USD | $125k USD |
Market Commentary
The job market for Production Schedulers remains stable with a steady demand, particularly within manufacturing, logistics, and supply chain sectors. The Bureau of Labor Statistics projects a modest growth outlook for roles related to production and operations, driven by the ongoing need for efficient resource allocation and timely delivery of goods. Companies continually seek professionals who can optimize production lines, reduce waste, and improve lead times, making this role essential for operational efficiency.
Emerging opportunities for Production Schedulers are increasingly tied to technological advancements. The adoption of AI, machine learning, and advanced analytics in supply chain management is transforming the role. Schedulers who can leverage these tools for predictive analytics, real-time adjustments, and scenario planning will be highly sought after. This shift emphasizes a need for strong analytical skills alongside traditional scheduling expertise.
The supply and demand dynamics for skilled Production Schedulers are relatively balanced, though there is a growing demand for individuals with strong digital proficiencies. Automation may handle routine tasks, but the strategic decision-making and problem-solving aspects of scheduling remain firmly human-centric. This makes the profession resilient and not easily replaced by full automation. Geographic hotspots for these roles include major manufacturing states and logistics hubs. Continuous learning in areas like lean manufacturing, Six Sigma, and specialized planning software is crucial for long-term career viability and growth in this evolving field.
Production Scheduler Career Path
Career progression for a Production Scheduler involves a clear path from operational execution to strategic planning and leadership. Professionals typically begin by mastering daily scheduling tasks before advancing to optimize complex production flows and manage broader planning initiatives. This field offers distinct individual contributor (IC) and management tracks.
Advancement speed depends on several factors, including a professional's performance, the complexity of the manufacturing environment, and the company's size and industry. Larger organizations with diverse product lines often provide more opportunities for specialization and vertical movement. Lateral opportunities might include roles in supply chain planning, inventory management, or logistics.
Continuous learning in supply chain methodologies, advanced planning software, and lean manufacturing principles is crucial for progression. Networking within professional organizations and pursuing certifications like APICS CPIM or CSCP can significantly accelerate career growth and open doors to leadership roles. Experience across different company types, from high-volume manufacturers to custom production facilities, also broadens a scheduler's expertise and marketability.
Junior Production Scheduler
0-2 yearsKey Focus Areas
Production Scheduler
2-4 yearsKey Focus Areas
Senior Production Scheduler
4-7 yearsKey Focus Areas
Lead Production Scheduler
7-10 yearsKey Focus Areas
Production Planning Manager
10+ years total experienceKey Focus Areas
Junior Production Scheduler
0-2 yearsExecute daily production schedules under direct supervision, primarily focusing on data entry, order release, and tracking progress. Monitor production against the schedule and report discrepancies. Coordinate with production floor personnel to address immediate issues and ensure material availability. This role handles routine scheduling tasks for specific production lines or work centers.
Key Focus Areas
Develop foundational knowledge of production processes, material flow, and ERP/MRP systems. Focus on accuracy, attention to detail, and timely data entry. Understand the impact of scheduling decisions on production efficiency and delivery dates. Begin to learn about capacity constraints and basic inventory principles.
Production Scheduler
2-4 yearsDevelop and maintain production schedules for multiple product lines or complex manufacturing processes. Analyze capacity, material availability, and demand forecasts to create optimized plans. Proactively identify and resolve scheduling conflicts, communicating potential delays or issues to relevant stakeholders. This role operates with increasing autonomy.
Key Focus Areas
Master advanced scheduling techniques, including constraint-based planning and optimization. Enhance problem-solving skills to anticipate and mitigate production bottlenecks. Develop strong communication and collaboration skills to work effectively with cross-functional teams. Explore continuous improvement methodologies like Lean or Six Sigma.
Senior Production Scheduler
4-7 yearsLead the development of master production schedules and long-range capacity plans. Optimize complex production flows across multiple departments or facilities. Analyze performance metrics, identify trends, and implement process improvements to enhance scheduling efficiency and responsiveness. This role often serves as a subject matter expert.
Key Focus Areas
Develop expertise in demand forecasting, inventory management, and supply chain integration. Focus on strategic planning, long-range capacity planning, and master scheduling. Mentor junior schedulers and contribute to process improvement initiatives. Cultivate strong analytical skills to drive data-driven decisions.
Lead Production Scheduler
7-10 yearsOversee the entire production scheduling function for a significant division or plant. Coordinate the activities of a team of schedulers, providing guidance and technical expertise. Drive continuous improvement in scheduling processes, tools, and methodologies. This role ensures scheduling strategies align with operational targets and customer demand.
Key Focus Areas
Cultivate strong leadership and team coordination skills. Develop project management capabilities for implementing new scheduling systems or processes. Focus on strategic alignment of production planning with overall business goals. Enhance negotiation and stakeholder management skills.
Production Planning Manager
10+ years total experienceManage the entire production planning department, including strategic planning, team leadership, and budget management. Establish departmental goals and KPIs, ensuring alignment with organizational objectives. Drive the adoption of best practices in production planning and supply chain optimization. This role holds ultimate responsibility for planning efficiency and effectiveness.
Key Focus Areas
Develop comprehensive supply chain management expertise, including S&OP (Sales and Operations Planning) and integrated business planning. Focus on strategic leadership, talent development, and cross-functional collaboration at an executive level. Acquire strong financial acumen and change management skills.
Job Application Toolkit
Ace your application with our purpose-built resources:
Production Scheduler Resume Examples
Proven layouts and keywords hiring managers scan for.
View examplesProduction Scheduler Cover Letter Examples
Personalizable templates that showcase your impact.
View examplesTop Production Scheduler Interview Questions
Practice with the questions asked most often.
View examplesProduction Scheduler Job Description Template
Ready-to-use JD for recruiters and hiring teams.
View examplesGlobal Production Scheduler Opportunities
Production schedulers ensure efficient manufacturing workflows globally. This role involves optimizing resource allocation and delivery timelines across diverse international supply chains. Global demand remains strong in 2025, driven by complex manufacturing and logistics needs. Cultural nuances in labor practices and regulatory differences in production standards significantly impact scheduling strategies. Professionals seek international roles for exposure to advanced manufacturing techniques and varied industry challenges. APICS CSCP or CPIM certifications enhance global mobility.
Global Salaries
Production scheduler salaries vary significantly by region and experience. In North America, specifically the U.S., entry-level schedulers earn $50,000-$65,000 USD, while experienced professionals can reach $80,000-$110,000 USD annually. Canada offers similar ranges, though often slightly lower. Europe sees diverse compensation; Germany and the UK offer €45,000-€70,000 (approximately $48,000-$75,000 USD), reflecting higher living costs in major cities. Eastern European countries typically present lower figures, around €25,000-€40,000.
Asia-Pacific markets like Singapore and Australia provide competitive salaries, ranging from S$60,000-S$90,000 (approx. $45,000-$67,000 USD) and A$70,000-A$100,000 (approx. $47,000-$67,000 USD) respectively. India's salaries are lower in absolute terms, but purchasing power is higher, with typical earnings between ₹500,000-₹1,000,000 (approx. $6,000-$12,000 USD). Latin America offers lower salary scales; Brazil might pay R$80,000-R$150,000 (approx. $16,000-$30,000 USD).
Salary structures also differ. European packages often include generous vacation time and robust public healthcare benefits. North American compensation might emphasize base salary and performance bonuses, with healthcare often employer-subsidized. Tax implications vary widely; countries like Germany have higher income taxes but offer comprehensive social security. Experience and specialized certifications, such as SAP or Oracle scheduling module expertise, enhance international compensation prospects.
Remote Work
International remote work for production schedulers is less common than for purely digital roles, given the need for direct interaction with factory floors or physical inventory. However, some companies with geographically dispersed manufacturing operations hire schedulers for remote oversight of specific product lines or regional hubs. This trend is growing with advanced digital twins and IoT integration in manufacturing.
Legal and tax implications for international remote work require careful consideration; schedulers must understand their tax residency and employer's compliance requirements in different jurisdictions. Time zone differences can pose challenges for real-time collaboration with production teams. Digital nomad visas are less applicable for this role due to its operational dependencies. Companies like Siemens or Schneider Electric might offer internal global remote roles. Salary expectations for remote positions often align with the employer's country of origin, not the employee's location. Reliable internet and a dedicated workspace are essential.
Visa & Immigration
Production schedulers often qualify for skilled worker visas in many countries. Popular destinations include Germany, Canada, Australia, and the UK, due to their strong manufacturing sectors. These countries typically require a job offer, relevant experience, and sometimes a bachelor’s degree in supply chain, engineering, or business. Credential recognition for degrees obtained abroad is often required, usually through an equivalency assessment body.
The visa application process typically involves submitting an online application, providing documentation like employment contracts, educational certificates, and proof of funds. Timelines vary from a few weeks to several months. Some countries, like Canada and Australia, offer points-based immigration systems where experience in high-demand roles like production scheduling can earn significant points. Language proficiency, especially in English or the local language, is often a requirement for integration and professional success. Pathways to permanent residency exist after several years of skilled employment. Family members can typically apply for dependent visas.
2025 Market Reality for Production Schedulers
Understanding the current market realities for production schedulers is vital for career progression and job search success. The landscape for this role has evolved significantly since 2023, influenced by post-pandemic supply chain disruptions and the rapid integration of AI into manufacturing operations.
Broader economic factors, such as inflation and consumer demand fluctuations, directly impact production volumes and, consequently, the need for schedulers. Market realities for production schedulers vary considerably by experience level, with senior roles requiring more strategic oversight, and by geographic region, depending on the concentration of manufacturing facilities. This analysis provides an honest assessment of what to expect.
Current Challenges
Production schedulers face heightened competition, especially for remote roles. Automation tools now handle routine scheduling tasks, increasing employer expectations for analytical and strategic contributions from human schedulers. Economic slowdowns can also reduce production volumes, directly impacting the demand for these roles.
Growth Opportunities
Despite challenges, strong opportunities exist for production schedulers with specialized skills. Roles focused on integrating AI-driven forecasting and optimization within ERP systems are in high demand. Companies seek schedulers who can transition from reactive planning to proactive, data-driven strategy.
Emerging specializations include supply chain optimization through AI, real-time demand sensing, and sustainable production scheduling. Schedulers who can demonstrate proficiency with advanced planning software like SAP APO, Kinaxis, or OMP, combined with analytical skills, hold a significant competitive advantage. Certifications in supply chain management or production and inventory management (e.g., APICS CPIM) are also highly valued.
Underserved markets often align with niche manufacturing sectors experiencing growth, such as medical devices, renewable energy components, or advanced robotics. These sectors often require highly precise and complex scheduling, creating more specialized and stable opportunities. Strategic career moves might involve targeting companies investing heavily in automation and digital transformation within their production facilities.
Current Market Trends
Demand for production schedulers remains steady but is shifting. Companies are increasingly seeking schedulers who can optimize complex supply chains and integrate with advanced planning systems, moving beyond simple task allocation. The focus is now on efficiency gains and cost reduction.
Generative AI and advanced analytics are transforming the role. Employers expect schedulers to leverage AI-driven forecasting and optimization tools, not just react to immediate needs. This requires a strong understanding of data interpretation and system integration, pushing the role towards a more analytical and strategic function.
Economic conditions have led some companies to consolidate operations, impacting the overall number of available positions. However, sectors experiencing growth, such as specialized manufacturing or high-tech production, continue to hire. Salary trends are stable, but significant increases often require expertise in new technologies like AI-powered scheduling software or advanced ERP systems.
Geographically, opportunities are strongest in regions with robust manufacturing bases. Remote work for production schedulers is less common than in other fields due to the need for direct interaction with production floors and physical inventory. Some cyclical hiring patterns exist, often linked to new product launches or seasonal demand spikes.
Emerging Specializations
The landscape of production scheduling is undergoing a significant transformation, driven by advancements in artificial intelligence, real-time data analytics, and the increasing complexity of global supply chains. These technological shifts are not merely optimizing existing processes; they are creating entirely new specialization opportunities for production schedulers. Early positioning in these emerging areas is crucial for career advancement, offering paths to leadership roles and often commanding premium compensation in 2025 and beyond.
While established scheduling methodologies remain important, the future belongs to those who can integrate cutting-edge tools and strategic foresight into their practice. Emerging specializations provide a distinct competitive advantage, moving professionals beyond routine task execution to strategic optimization and problem-solving. This shift allows schedulers to become indispensable assets within their organizations, driving efficiency and responsiveness.
Many emerging areas, particularly those involving AI and advanced analytics, are on a trajectory to become mainstream within the next three to five years, creating a substantial volume of job opportunities. Pursuing these cutting-edge paths involves a balance of risk and reward. While they require a commitment to continuous learning and adapting to new technologies, the potential for significant career growth and impact far outweighs the initial investment.
AI-Driven Dynamic Production Scheduler
This specialization focuses on integrating AI and machine learning algorithms directly into the scheduling process to predict demand fluctuations, optimize resource allocation, and dynamically adjust production plans in real time. AI-driven scheduling moves beyond static models, allowing for proactive problem-solving and significantly enhancing operational agility. It is crucial for complex manufacturing environments seeking to minimize waste and maximize throughput.
Smart Factory Optimization Scheduler
This area involves optimizing production schedules within highly automated smart factories, where IoT sensors, robotics, and interconnected systems generate vast amounts of real-time data. Specialists in this field ensure seamless communication between automated processes and the scheduling system, leveraging data streams to prevent bottlenecks and ensure continuous, efficient production flows. They are critical for realizing the full potential of Industry 4.0 initiatives.
Sustainable Production Scheduler
This specialization addresses the growing need for sustainable and circular economy practices within manufacturing. Production schedulers in this role optimize schedules to minimize waste, reduce energy consumption, and integrate recycled or renewable materials. They consider the entire product lifecycle, from raw material sourcing to end-of-life processing, ensuring that production plans meet environmental regulations and corporate sustainability goals.
Supply Chain Resilience Scheduler
Focusing on the resilience of production schedules against disruptions, this specialization involves developing robust contingency plans for supply chain failures, equipment breakdowns, or unforeseen events. Professionals in this area utilize predictive analytics and scenario planning tools to identify potential vulnerabilities and build adaptable schedules that can quickly pivot without significant loss of productivity. This role is increasingly vital in volatile global markets.
Custom & Complex Manufacturing Scheduler
This niche focuses on the intricate scheduling required for highly customized or low-volume, high-complexity production environments, such as aerospace, medical devices, or specialized machinery. Schedulers in this area manage unique material requirements, highly variable lead times, and complex assembly sequences, often leveraging advanced project management and simulation tools to ensure on-time delivery of bespoke products.
Pros & Cons of Being a Production Scheduler
Making informed career decisions requires understanding both the benefits and challenges of a role. The experience of a Production Scheduler can vary significantly based on the company's industry, its specific operational culture, and the scale of its production processes. What one person considers a benefit, such as a structured environment, another might see as a challenge. Furthermore, the demands and opportunities of this role may evolve at different career stages, from entry-level to senior positions. This assessment aims to provide a realistic overview, helping individuals set appropriate expectations and determine if this career path aligns with their personal values and professional aspirations.
Pros
- Production schedulers play a critical role in a company's operational efficiency, directly impacting productivity and profitability, which provides a strong sense of purpose and contribution.
- The role offers excellent opportunities to develop strong analytical and problem-solving skills, as schedulers must optimize complex processes and adapt to unforeseen variables.
- This position provides a comprehensive understanding of the entire production lifecycle, from raw materials to finished goods, offering valuable insights into supply chain dynamics.
- Production schedulers gain exposure to various departments, including manufacturing, logistics, and sales, fostering cross-functional collaboration and networking opportunities.
- The demand for skilled production schedulers remains consistent across diverse manufacturing industries, offering good job security and a wide range of employment opportunities.
- There is a clear path for professional growth into broader supply chain management, operations management, or even leadership roles within a manufacturing organization.
- Many companies are adopting advanced planning software and automation tools, allowing schedulers to work with cutting-edge technology and continuously enhance their technical skills.
Cons
- Production schedulers often face high pressure to meet tight deadlines and production targets, which can lead to stress and long hours, especially during peak demand or unexpected disruptions.
- The role requires meticulous attention to detail and accuracy; even small errors in scheduling can lead to significant production delays, material waste, and increased costs.
- Production environments can be dynamic and unpredictable, with frequent changes in orders, material availability, or equipment breakdowns, requiring constant adjustments and quick problem-solving.
- Communication and coordination with multiple departments, including sales, procurement, and operations, can be challenging, requiring strong interpersonal skills to manage conflicting priorities.
- Career progression can sometimes be limited within the direct scheduling function itself, often requiring a move into broader supply chain management or operations roles for significant advancement.
- The work can become repetitive, involving similar tasks like data entry, report generation, and routine schedule adjustments, which might not appeal to those seeking constant novelty.
- Production schedulers are frequently on call or expected to respond to urgent issues outside regular business hours, particularly in 24/7 manufacturing operations, impacting work-life balance at times.
Frequently Asked Questions
Production Schedulers face unique challenges balancing demand, capacity, and material availability to optimize manufacturing flow. This section addresses the most common questions about entering this critical role, from required skills and daily responsibilities to career progression and work-life balance within a production environment.
What exactly does a Production Scheduler do on a day-to-day basis?
A Production Scheduler typically plans and coordinates production schedules to meet customer demand and optimize resource utilization. This involves analyzing sales forecasts, inventory levels, and production capacities to create efficient schedules. You will often work with cross-functional teams, including sales, operations, and supply chain, to ensure smooth production flow and on-time delivery.
What are the essential qualifications or education needed to become a Production Scheduler?
Many entry-level Production Scheduler roles require a bachelor's degree in supply chain management, business, logistics, or a related field. However, practical experience in a manufacturing environment or a strong understanding of production processes can sometimes substitute for a formal degree. Certifications like APICS CPIM (Certified in Production and Inventory Management) are highly valued and can significantly boost your qualifications.
How long does it typically take to become job-ready as a Production Scheduler if I'm starting fresh?
The timeline to become job-ready as a Production Scheduler varies based on your background. If you have a relevant degree and some foundational knowledge, you might find an entry-level position within 3-6 months of focused job searching. For those transitioning without direct experience, gaining a certification like CPIM and networking can take 6-12 months before securing a suitable role.
What are the typical salary expectations for an entry-level and experienced Production Scheduler?
Starting salaries for Production Schedulers generally range from $45,000 to $60,000 annually, depending on location, industry, and company size. With 3-5 years of experience, this can increase to $60,000-$80,000. Senior or lead roles, especially in complex manufacturing environments, can command salaries upwards of $90,000, particularly with advanced certifications and a proven track record.
What is the typical work-life balance like for a Production Scheduler, and are there common periods of high stress?
Work-life balance for a Production Scheduler can vary. In some manufacturing environments, especially those with continuous operations, you might encounter occasional demands for off-hour support or urgent schedule adjustments. However, many roles offer standard business hours. It's crucial to clarify the specific demands of the role during interviews, as some companies prioritize flexibility more than others.
Is the job market for Production Schedulers growing, or is it at risk from automation?
The job market for Production Schedulers remains stable due to the ongoing need for efficient manufacturing and supply chain operations across various industries. As businesses continue to optimize their production processes, skilled schedulers are in consistent demand. Automation tools are emerging, but the need for human oversight, problem-solving, and strategic planning in scheduling ensures job security.
What are the typical career progression paths for a Production Scheduler?
Career growth for a Production Scheduler can lead to various roles within supply chain and operations. You might advance to Senior Production Scheduler, Master Scheduler, or even Production Planning Manager. Further specialization can lead to roles in demand planning, inventory management, or supply chain analysis. Some also transition into consulting or enterprise resource planning (ERP) system implementation roles.
Can Production Schedulers work remotely, or is it primarily an in-office role?
Remote work opportunities for Production Schedulers are becoming more common, especially for roles focused on planning and data analysis rather than direct shop floor interaction. However, many companies still prefer schedulers to be on-site or adopt a hybrid model to facilitate closer collaboration with manufacturing teams. The feasibility of remote work often depends on the complexity of the production process and company culture.
Related Careers
Explore similar roles that might align with your interests and skills:
Manufacturing Planner
A growing field with similar skill requirements and career progression opportunities.
Explore career guideMaster Scheduler
A growing field with similar skill requirements and career progression opportunities.
Explore career guideProduction Planner
A growing field with similar skill requirements and career progression opportunities.
Explore career guideProject Scheduler
A growing field with similar skill requirements and career progression opportunities.
Explore career guideScheduler
A growing field with similar skill requirements and career progression opportunities.
Explore career guideAssess your Production Scheduler readiness
Understanding where you stand today is the first step toward your career goals. Our Career Coach helps identify skill gaps and create personalized plans.
Skills Gap Analysis
Get a detailed assessment of your current skills versus Production Scheduler requirements. Our AI Career Coach identifies specific areas for improvement with personalized recommendations.
See your skills gapCareer Readiness Assessment
Evaluate your overall readiness for Production Scheduler roles with our AI Career Coach. Receive personalized recommendations for education, projects, and experience to boost your competitiveness.
Assess your readinessSimple pricing, powerful features
Upgrade to Himalayas Plus and turbocharge your job search.
Himalayas
Himalayas Plus
Himalayas Max
Find your dream job
Sign up now and join over 100,000 remote workers who receive personalized job alerts, curated job matches, and more for free!
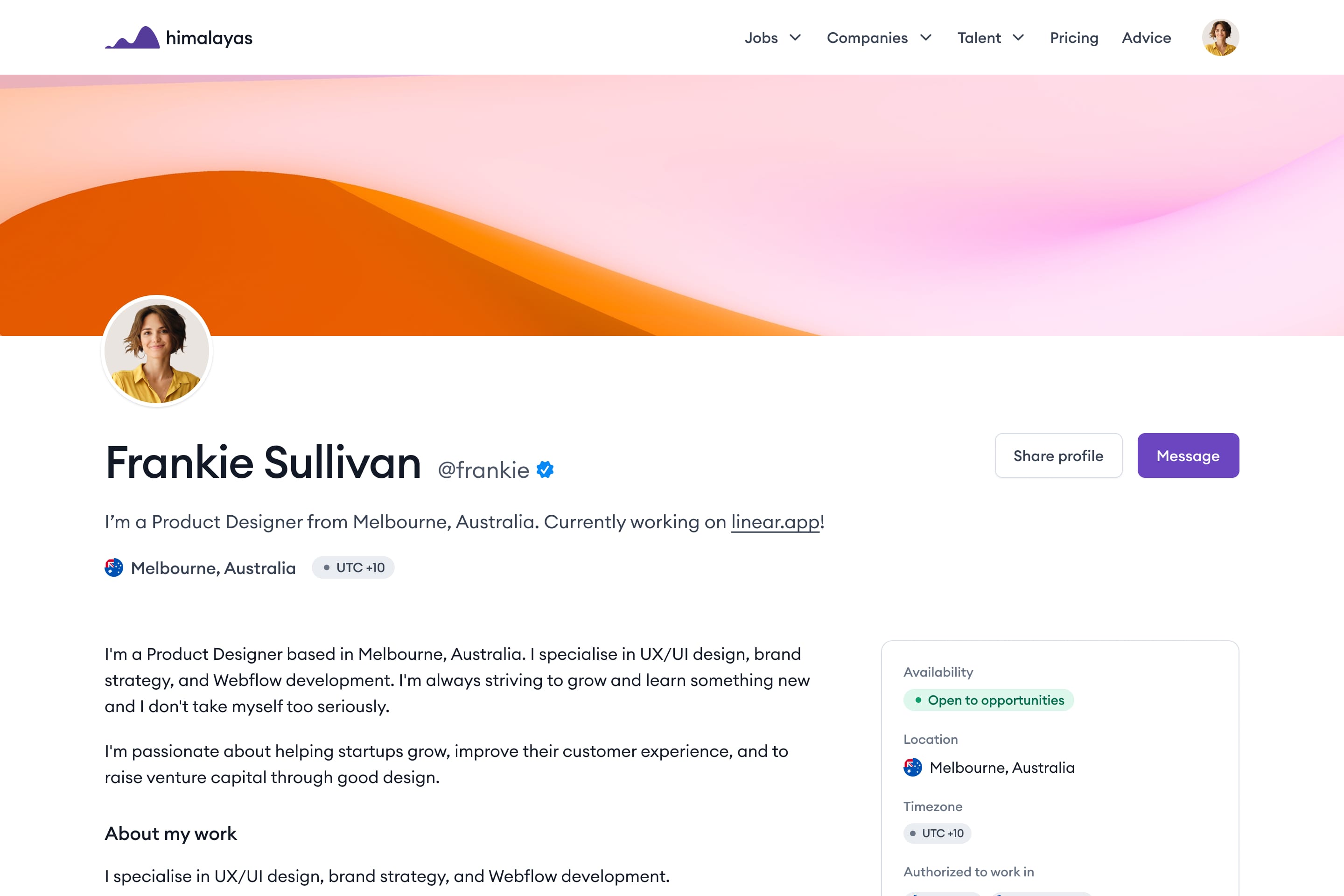