Complete Master Scheduler Career Guide
A Master Scheduler orchestrates the complex flow of production, ensuring that manufacturing operations run smoothly and efficiently to meet customer demand. This vital role balances raw material availability, production capacity, and sales forecasts, directly impacting a company's profitability and delivery performance. It's a challenging yet rewarding path for those who excel at strategic planning and problem-solving in dynamic environments.
Key Facts & Statistics
Median Salary
$55,270 USD
(U.S. national median for Production, Planning, and Expediting Clerks, May 2023, BLS)
Range: $35k - $90k+ USD, varying significantly by experience and industry
Growth Outlook
5%
as fast as average (for Production, Planning, and Expediting Clerks, 2022-2032, BLS)
Annual Openings
≈17,800
openings annually (for Production, Planning, and Expediting Clerks, BLS)
Top Industries
Typical Education
High school diploma or equivalent; however, associate's or bachelor's degrees in supply chain management or business are increasingly preferred for Master Scheduler roles, alongside professional certifications like APICS CPIM.
What is a Master Scheduler?
A Master Scheduler crafts and maintains the master production schedule, acting as the central orchestrator of a company's production plan. This professional translates sales forecasts and customer orders into a feasible manufacturing schedule, ensuring that products are made at the right time, in the right quantities, while considering available resources and capacity. They balance customer demand with production capabilities to optimize inventory levels and operational efficiency.
Unlike a Production Planner who focuses on detailed, short-term daily or weekly shop floor schedules, the Master Scheduler operates at a higher, more strategic level, typically planning for months or even a year out. They are distinct from Demand Planners, who focus on forecasting future customer needs, by taking those forecasts and converting them into actionable production plans. The Master Scheduler ensures that the overall business strategy aligns with operational execution, preventing both stockouts and excess inventory.
What does a Master Scheduler do?
Key Responsibilities
- Develop and maintain the master production schedule by balancing demand forecasts with production capacity and inventory levels.
- Collaborate with sales, marketing, and operations teams to integrate sales forecasts and customer orders into the production plan.
- Analyze production capacity and resource availability to identify potential bottlenecks and propose solutions to optimize flow.
- Monitor inventory levels of raw materials, work-in-progress, and finished goods to ensure optimal stock levels and prevent shortages or overstock.
- Adjust production schedules in response to unforeseen events such as material delays, equipment breakdowns, or sudden changes in demand.
- Generate reports on schedule adherence, production performance, and inventory metrics to inform management decisions.
- Participate in S&OP (Sales and Operations Planning) meetings to align production plans with overall business strategy and financial goals.
Work Environment
Master Schedulers typically work in an office setting, either on-site or remotely, within manufacturing, supply chain, or operations departments. The work environment is often dynamic and collaborative, requiring frequent interaction with cross-functional teams including sales, purchasing, production, and logistics. They often attend daily stand-up meetings and weekly planning sessions.
The pace can be fast, especially when responding to demand fluctuations or supply chain disruptions. While core hours are common, occasional extended hours may be necessary to meet deadlines or resolve urgent issues. Travel is generally minimal, though it may occur for inter-site collaboration or training.
Tools & Technologies
Master Schedulers heavily rely on Enterprise Resource Planning (ERP) systems like SAP, Oracle EBS, or Microsoft Dynamics 365 for managing production data, inventory, and demand. They also use Advanced Planning and Scheduling (APS) software such as Kinaxis RapidResponse or OMP Plus for complex optimization and scenario planning.
Spreadsheet software like Microsoft Excel or Google Sheets remains essential for detailed analysis, data manipulation, and ad-hoc reporting. Communication and collaboration tools, including Microsoft Teams, Slack, and email, facilitate interaction with various departments. Additionally, they often work with Business Intelligence (BI) tools like Tableau or Power BI to visualize performance metrics and identify trends.
Master Scheduler Skills & Qualifications
A Master Scheduler orchestrates the production plan, balancing customer demand with manufacturing capacity and material availability. This role is crucial for operational efficiency and on-time delivery, directly impacting profitability and customer satisfaction. The qualification landscape for a Master Scheduler varies significantly based on industry, company size, and the complexity of the supply chain.
For entry-level Master Scheduler positions, companies often seek candidates with a bachelor's degree and some internship experience in manufacturing or supply chain. More senior or strategic Master Scheduler roles, particularly in large, global organizations or highly regulated industries like aerospace or pharmaceuticals, typically require extensive practical experience, often 5-10 years, coupled with advanced certifications. While formal education provides foundational knowledge, practical experience navigating real-world supply chain disruptions and optimizing production flows is often more valued.
Certifications like APICS CSCP or CPIM are highly regarded and can often substitute for a portion of the experience requirement, especially for career changers. These credentials demonstrate a deep understanding of supply chain principles. The skill landscape for Master Schedulers is evolving rapidly with the adoption of advanced planning systems and AI-driven forecasting. Therefore, continuous learning in data analytics and digital tools is becoming increasingly important. Focusing on both robust planning methodologies and the ability to leverage technology provides a balanced and highly sought-after skill set.
Education Requirements
Technical Skills
- ERP systems (e.g., SAP PP/MM, Oracle SCM, Microsoft Dynamics 365) for production planning and control
- Advanced Planning and Scheduling (APS) software (e.g., Kinaxis RapidResponse, Blue Yonder, OMP Plus)
- Demand forecasting techniques and statistical modeling (e.g., time series analysis, regression)
- Material Requirements Planning (MRP) and Distribution Requirements Planning (DRP) principles
- Capacity planning and finite scheduling methodologies
- Inventory management principles (e.g., safety stock, reorder points, economic order quantity)
- Data analysis and visualization tools (e.g., Excel with advanced functions, Power BI, Tableau)
- Supply chain optimization and network design concepts
- Production process knowledge (e.g., discrete manufacturing, process manufacturing, lean principles)
- SQL for data extraction and reporting from planning systems
- Sales and Operations Planning (S&OP) process facilitation
- Proficiency in project management software (e.g., Microsoft Project, Asana)
Soft Skills
- Analytical Thinking: Master Schedulers must quickly interpret complex data sets, identify trends, and make informed decisions to optimize production schedules and mitigate risks.
- Problem-Solving: This role requires the ability to quickly identify scheduling conflicts, material shortages, or capacity constraints and develop effective, timely solutions to maintain production flow.
- Negotiation: Effective Master Schedulers negotiate with sales regarding demand, production regarding capacity, and procurement regarding material availability to balance competing priorities.
- Attention to Detail: Precision is critical in scheduling; small errors can lead to significant production delays or material waste, making meticulous attention to detail indispensable.
- Communication: Master Schedulers must clearly articulate complex scheduling plans, potential issues, and their impact to diverse stakeholders, including production, sales, and senior management.
- Adaptability: Production environments are dynamic. Master Schedulers must quickly adjust plans in response to unexpected changes in demand, supply, or capacity.
- Stakeholder Management: Managing expectations and priorities of various departments, such as sales, operations, and procurement, is vital for successful schedule implementation.
- Proactive Planning: A strong Master Scheduler anticipates future challenges, such as seasonal demand shifts or long lead times, and incorporates preventative measures into the schedule before issues arise
How to Become a Master Scheduler
Becoming a Master Scheduler involves navigating various entry points, from traditional supply chain degrees to transitioning from roles like production planning or inventory management. The timeline for entry varies significantly; a complete beginner might need 1-2 years to build foundational knowledge and gain relevant experience, while someone with adjacent experience could transition in 6-12 months. Geographic location also impacts opportunities, with more manufacturing and logistics hubs offering a higher volume of roles.
Entry strategies differ based on company size. Larger corporations often prefer candidates with formal education and prior experience in enterprise resource planning (ERP) systems, whereas smaller companies or startups may prioritize practical problem-solving skills and a willingness to learn on the job. A common misconception is that this role is purely administrative; in reality, it demands strong analytical abilities and strategic thinking to optimize production flows.
Building a robust network within the supply chain community is crucial. Attending industry events, joining professional organizations, and seeking mentorship can open doors to opportunities not advertised publicly. The hiring landscape values candidates who can demonstrate a clear understanding of production planning principles, data analysis, and the ability to work cross-functionally to balance demand and capacity effectively.
Develop a strong foundation in supply chain management principles and production planning. Consider pursuing certifications like APICS CPIM (Certified in Production and Inventory Management) or CSCP (Certified Supply Chain Professional), which provide a structured curriculum and industry-recognized credentials. This foundational knowledge is essential for understanding the complexities of master scheduling.
Gain practical experience in related operational roles such as production planning, inventory control, or material management. Seek opportunities within your current company or volunteer for projects that involve forecasting, scheduling, or capacity planning. Aim for at least 1-2 years of hands-on experience to build a realistic understanding of manufacturing processes.
Master essential software tools, particularly ERP systems like SAP, Oracle, or Microsoft Dynamics, and advanced planning and scheduling (APS) software. Familiarity with data analysis tools like Excel (advanced functions) or even basic SQL for data extraction is also highly beneficial. Hands-on practice with these tools will make you a more attractive candidate.
Build a portfolio of projects or case studies demonstrating your ability to analyze production data, develop master schedules, and improve operational efficiency. Include examples where you optimized resource allocation, reduced lead times, or improved on-time delivery. Document your problem-solving process and the measurable impact of your work.
Network with professionals in supply chain, operations, and manufacturing. Attend industry webinars, join LinkedIn groups focused on master scheduling, and connect with people working in roles you aspire to. Informational interviews can provide insights into daily responsibilities and common challenges, helping you tailor your approach.
Prepare a targeted resume and cover letter highlighting your quantitative skills, software proficiency, and any experience in planning or optimization. Practice answering behavioral and technical questions related to forecasting, capacity planning, and managing production constraints. Be ready to discuss specific scenarios and how you would approach them.
Step 1
Develop a strong foundation in supply chain management principles and production planning. Consider pursuing certifications like APICS CPIM (Certified in Production and Inventory Management) or CSCP (Certified Supply Chain Professional), which provide a structured curriculum and industry-recognized credentials. This foundational knowledge is essential for understanding the complexities of master scheduling.
Step 2
Gain practical experience in related operational roles such as production planning, inventory control, or material management. Seek opportunities within your current company or volunteer for projects that involve forecasting, scheduling, or capacity planning. Aim for at least 1-2 years of hands-on experience to build a realistic understanding of manufacturing processes.
Step 3
Master essential software tools, particularly ERP systems like SAP, Oracle, or Microsoft Dynamics, and advanced planning and scheduling (APS) software. Familiarity with data analysis tools like Excel (advanced functions) or even basic SQL for data extraction is also highly beneficial. Hands-on practice with these tools will make you a more attractive candidate.
Step 4
Build a portfolio of projects or case studies demonstrating your ability to analyze production data, develop master schedules, and improve operational efficiency. Include examples where you optimized resource allocation, reduced lead times, or improved on-time delivery. Document your problem-solving process and the measurable impact of your work.
Step 5
Network with professionals in supply chain, operations, and manufacturing. Attend industry webinars, join LinkedIn groups focused on master scheduling, and connect with people working in roles you aspire to. Informational interviews can provide insights into daily responsibilities and common challenges, helping you tailor your approach.
Step 6
Prepare a targeted resume and cover letter highlighting your quantitative skills, software proficiency, and any experience in planning or optimization. Practice answering behavioral and technical questions related to forecasting, capacity planning, and managing production constraints. Be ready to discuss specific scenarios and how you would approach them.
Education & Training Needed to Become a Master Scheduler
Becoming a Master Scheduler involves navigating a diverse educational landscape, blending formal academic programs with practical, industry-specific training. While a bachelor's degree in supply chain management, business administration, industrial engineering, or operations management provides a strong theoretical foundation, it is not always a strict prerequisite. These 4-year degrees typically cost between $40,000 and $100,000+ for in-state tuition at public universities, extending to $150,000-$250,000+ for private institutions, and generally require four years to complete.
Alternative pathways, such as professional certifications and specialized online courses, offer more focused and time-efficient learning. Certifications from organizations like APICS (now ASCM) are highly valued in the industry and often preferred by employers for Master Scheduler roles. These certification programs, like the CSCP or CPIM, can range from $1,500 to $5,000, including course materials and exam fees, and typically take 6-18 months of dedicated study. Bootcamps specifically for supply chain analytics or planning are less common but emerging, potentially costing $10,000-$20,000 for 12-24 weeks of intensive training.
Employers often prioritize a blend of theoretical knowledge and practical experience. While degrees provide a broad understanding, certifications demonstrate a commitment to specific industry best practices and can significantly enhance job prospects. Continuous learning remains crucial; new technologies and methodologies in supply chain planning necessitate ongoing professional development. The most effective educational investment combines foundational academic learning with targeted professional certifications and hands-on experience, adapting to the specific demands of the industry and the size of the organization.
Master Scheduler Salary & Outlook
Compensation for a Master Scheduler varies significantly based on several critical factors. Geographic location plays a substantial role; areas with higher costs of living or a strong presence of manufacturing and logistics industries, such as the Northeast or California, typically offer higher salaries. Conversely, regions with lower living expenses may show more modest figures.
Years of experience and specialized skills in advanced planning systems (APS), enterprise resource planning (ERP) software like SAP or Oracle, and demand forecasting methodologies directly impact earning potential. A Master Scheduler's ability to optimize complex supply chains and production schedules adds considerable value, commanding higher compensation.
Total compensation packages often extend beyond base salary to include performance-based bonuses, especially in companies with tight production targets or efficiency incentives. Benefits, such as health insurance, retirement contributions, and professional development allowances for certifications like APICS CSCP or CPIM, are standard. Remote work opportunities can influence salary ranges, sometimes allowing for geographic arbitrage where individuals earn higher-market salaries while residing in lower cost-of-living areas. International market variations exist, with USD figures primarily reflecting the U.S. labor market.
Salary by Experience Level
Level | US Median | US Average |
---|---|---|
Junior Scheduler | $60k USD | $65k USD |
Scheduler | $75k USD | $78k USD |
Senior Scheduler | $90k USD | $95k USD |
Master Scheduler | $110k USD | $115k USD |
Scheduling Manager | $130k USD | $135k USD |
Director of Scheduling | $155k USD | $165k USD |
Market Commentary
The job market for Master Schedulers remains stable with a projected growth outlook, driven by increasing complexity in global supply chains and the ongoing push for operational efficiency across manufacturing, logistics, and retail sectors. The Bureau of Labor Statistics projects a steady demand for logisticians and related roles, which includes Master Schedulers, indicating continued relevance.
Emerging opportunities for Master Schedulers include specializations in advanced analytics, predictive modeling for demand forecasting, and integrating AI-driven scheduling tools. The role is evolving to require more data analysis skills and less manual input, as automation streamlines routine tasks. Companies seek professionals who can leverage technology to create more resilient and agile supply chain operations.
Supply and demand dynamics for Master Schedulers are generally balanced, though a shortage of candidates with strong analytical skills combined with deep industry experience exists. This creates a competitive advantage for those who can demonstrate proficiency in modern planning software and data interpretation. The profession is relatively recession-resistant, as efficient resource allocation and production planning remain crucial for companies during economic downturns.
Geographic hotspots for Master Schedulers include major manufacturing hubs and distribution centers, particularly in the Midwest, Southeast, and along key port cities. Future-proofing this career involves continuous learning in supply chain technology, embracing digital transformation, and focusing on strategic planning rather than just execution.
Master Scheduler Career Path
Career progression for a Master Scheduler involves a clear path from operational execution to strategic planning and leadership. Professionals typically start by mastering the fundamentals of scheduling, then advance to managing complex projects and eventually leading entire scheduling functions. Movement often distinguishes between individual contributor (IC) tracks, which focus on deep technical expertise and complex problem-solving, and management tracks, which emphasize team leadership and strategic oversight.
Advancement speed depends on several factors, including individual performance, the complexity of projects handled, and the size and industry of the employing company. Larger organizations or those with highly complex supply chains often present more opportunities for specialization and vertical movement. Lateral moves may involve transitioning between different production environments, such as discrete manufacturing to process industries, or moving into related fields like supply chain planning or logistics.
Continuous learning in supply chain methodologies, enterprise resource planning (ERP) systems, and data analytics is crucial. Networking within industry associations, seeking mentorship, and building a reputation for accurate and efficient scheduling significantly aid progression. Certifications in supply chain management or production and inventory control also mark important milestones. Professionals might pivot into roles like production planning management, supply chain analysis, or operations consulting as alternative pathways.
Junior Scheduler
0-2 yearsAssists senior schedulers with data input and basic schedule adjustments. Monitors production progress against simple schedules and identifies minor deviations. Primarily responsible for administrative tasks related to scheduling, working under close supervision. Has limited decision-making authority, focusing on executing defined tasks.
Key Focus Areas
Develop foundational understanding of production processes, material flow, and scheduling software. Focus on accuracy in data entry and adherence to established procedures. Learn to identify and report basic scheduling conflicts and production bottlenecks. Build strong communication skills to interact with production teams.
Scheduler
2-4 yearsDevelops and maintains detailed production schedules for specific product lines or work centers. Identifies and resolves scheduling conflicts, material shortages, and capacity bottlenecks. Collaborates with production, procurement, and logistics teams to ensure schedule adherence. Makes independent decisions on minor schedule adjustments to meet production targets.
Key Focus Areas
Master the scheduling software and advanced planning techniques. Develop problem-solving skills for resolving conflicts and optimizing production flows. Learn to analyze capacity constraints and material availability. Enhance collaboration with cross-functional teams, including procurement and logistics.
Senior Scheduler
4-7 yearsCreates and manages complex master production schedules for multiple product lines or facilities. Leads efforts to optimize production sequences, minimize changeovers, and maximize resource utilization. Analyzes scheduling performance metrics and identifies areas for process improvement. Provides guidance and training to junior schedulers.
Key Focus Areas
Develop expertise in demand forecasting integration and inventory management principles. Focus on strategic capacity planning and long-range scheduling. Cultivate strong analytical skills for performance metrics and continuous improvement. Mentor junior team members and contribute to process enhancements.
Master Scheduler
7-10 yearsOversees the entire master scheduling process for a large organization or business unit. Develops and implements strategic scheduling policies and procedures. Integrates demand forecasts, sales plans, and inventory targets into a cohesive master production schedule. Has significant decision-making authority impacting production efficiency and customer delivery.
Key Focus Areas
Focus on strategic alignment of scheduling with business objectives and financial goals. Develop advanced skills in supply chain optimization, risk management, and scenario planning. Drive continuous improvement initiatives for scheduling processes. Build strong leadership and influencing skills to gain stakeholder buy-in.
Scheduling Manager
10-15 yearsLeads and manages a team of schedulers, overseeing their performance and development. Establishes departmental goals and objectives aligned with organizational strategy. Responsible for resource allocation within the scheduling department and managing departmental budget. Drives continuous improvement in scheduling processes and systems.
Key Focus Areas
Develop team leadership, performance management, and talent development skills. Focus on strategic planning, resource allocation, and cross-departmental collaboration. Drive technological adoption and process standardization. Enhance communication and negotiation skills for managing complex stakeholder relationships.
Director of Scheduling
15+ yearsProvides strategic direction and leadership for all scheduling and production planning functions across the organization. Develops long-term supply chain strategies and ensures alignment with overall business objectives. Responsible for technology roadmaps, system implementations, and major process redesigns within planning. Influences executive-level decisions related to production capacity, inventory, and customer service levels.
Key Focus Areas
Focus on executive leadership, strategic vision, and organizational transformation. Develop skills in large-scale change management, global supply chain strategy, and enterprise-level system implementation. Build strong relationships with executive leadership and external partners. Drive innovation in planning and scheduling methodologies.
Junior Scheduler
0-2 yearsAssists senior schedulers with data input and basic schedule adjustments. Monitors production progress against simple schedules and identifies minor deviations. Primarily responsible for administrative tasks related to scheduling, working under close supervision. Has limited decision-making authority, focusing on executing defined tasks.
Key Focus Areas
Develop foundational understanding of production processes, material flow, and scheduling software. Focus on accuracy in data entry and adherence to established procedures. Learn to identify and report basic scheduling conflicts and production bottlenecks. Build strong communication skills to interact with production teams.
Scheduler
2-4 yearsDevelops and maintains detailed production schedules for specific product lines or work centers. Identifies and resolves scheduling conflicts, material shortages, and capacity bottlenecks. Collaborates with production, procurement, and logistics teams to ensure schedule adherence. Makes independent decisions on minor schedule adjustments to meet production targets.
Key Focus Areas
Master the scheduling software and advanced planning techniques. Develop problem-solving skills for resolving conflicts and optimizing production flows. Learn to analyze capacity constraints and material availability. Enhance collaboration with cross-functional teams, including procurement and logistics.
Senior Scheduler
4-7 yearsCreates and manages complex master production schedules for multiple product lines or facilities. Leads efforts to optimize production sequences, minimize changeovers, and maximize resource utilization. Analyzes scheduling performance metrics and identifies areas for process improvement. Provides guidance and training to junior schedulers.
Key Focus Areas
Develop expertise in demand forecasting integration and inventory management principles. Focus on strategic capacity planning and long-range scheduling. Cultivate strong analytical skills for performance metrics and continuous improvement. Mentor junior team members and contribute to process enhancements.
Master Scheduler
7-10 yearsOversees the entire master scheduling process for a large organization or business unit. Develops and implements strategic scheduling policies and procedures. Integrates demand forecasts, sales plans, and inventory targets into a cohesive master production schedule. Has significant decision-making authority impacting production efficiency and customer delivery.
Key Focus Areas
Focus on strategic alignment of scheduling with business objectives and financial goals. Develop advanced skills in supply chain optimization, risk management, and scenario planning. Drive continuous improvement initiatives for scheduling processes. Build strong leadership and influencing skills to gain stakeholder buy-in.
Scheduling Manager
10-15 yearsLeads and manages a team of schedulers, overseeing their performance and development. Establishes departmental goals and objectives aligned with organizational strategy. Responsible for resource allocation within the scheduling department and managing departmental budget. Drives continuous improvement in scheduling processes and systems.
Key Focus Areas
Develop team leadership, performance management, and talent development skills. Focus on strategic planning, resource allocation, and cross-departmental collaboration. Drive technological adoption and process standardization. Enhance communication and negotiation skills for managing complex stakeholder relationships.
Director of Scheduling
15+ yearsProvides strategic direction and leadership for all scheduling and production planning functions across the organization. Develops long-term supply chain strategies and ensures alignment with overall business objectives. Responsible for technology roadmaps, system implementations, and major process redesigns within planning. Influences executive-level decisions related to production capacity, inventory, and customer service levels.
Key Focus Areas
Focus on executive leadership, strategic vision, and organizational transformation. Develop skills in large-scale change management, global supply chain strategy, and enterprise-level system implementation. Build strong relationships with executive leadership and external partners. Drive innovation in planning and scheduling methodologies.
Job Application Toolkit
Ace your application with our purpose-built resources:
Master Scheduler Cover Letter Examples
Personalizable templates that showcase your impact.
View examplesMaster Scheduler Job Description Template
Ready-to-use JD for recruiters and hiring teams.
View examplesGlobal Master Scheduler Opportunities
Master Schedulers manage production plans and resource allocation across global supply chains. This role requires understanding diverse market demands and regulatory frameworks. International job markets show consistent demand for skilled schedulers, especially in manufacturing and logistics hubs. Professionals often pursue international opportunities to gain exposure to varied operational models and advanced planning technologies. Certifications like APICS CSCP or CPIM enhance global mobility and recognition.
Global Salaries
Master Scheduler salaries vary significantly by region and industry. In North America, particularly the USA, salaries range from $75,000 to $120,000 USD annually, reflecting high demand in advanced manufacturing sectors. Canada offers $60,000 to $95,000 CAD, equivalent to $45,000 to $70,000 USD, with a lower cost of living.
European markets present diverse compensation. In Germany, Master Schedulers earn €55,000 to €85,000 ($60,000 to $92,000 USD). The UK typically offers £45,000 to £70,000 ($57,000 to $89,000 USD). These figures often include comprehensive benefits like robust healthcare and generous vacation time, which impact overall compensation value.
Asia-Pacific regions, such as Singapore, offer S$60,000 to S$90,000 ($44,000 to $66,000 USD), with a higher cost of living. Australia's salaries are A$80,000 to A$110,000 ($53,000 to $73,000 USD), balancing a higher cost of living. Latin American countries like Mexico provide salaries from MXN 300,000 to MXN 600,000 ($17,000 to $35,000 USD), where purchasing power can be strong despite lower nominal figures.
Tax implications and take-home pay differ greatly. Countries with higher social welfare benefits, like Germany, often have higher income taxes. Experience and specialized industry knowledge significantly influence compensation globally, with aerospace or automotive industries often paying more. Some multinational corporations use standardized global pay scales for senior roles, ensuring some parity across regions.
Remote Work
International remote work for Master Schedulers is growing, especially for roles focused on strategic planning rather than shop-floor execution. Companies increasingly adopt hybrid models, allowing schedulers to manage global supply chains from various locations. Legal and tax implications require careful consideration; professionals need to understand their tax residency and potential permanent establishment risks for employers.
Time zone differences present a key challenge for international collaboration, requiring flexible working hours. Digital nomad visas in countries like Portugal or Spain offer pathways for Master Schedulers to work remotely. Many large manufacturing and logistics firms are open to international remote hiring, particularly for experienced professionals. Remote work can impact salary expectations, with some companies adjusting pay based on the employee's location and cost of living. Essential equipment includes reliable internet and robust scheduling software access.
Visa & Immigration
Master Schedulers often qualify for skilled worker visas in major economies. Popular destinations include Canada (Express Entry), Australia (Skilled Nominated Visa), Germany (EU Blue Card), and the UK (Skilled Worker Visa). Each country requires specific points for age, education, language proficiency, and work experience. Credential recognition for university degrees is generally straightforward, though specific professional licensing is not typically required for this role.
Application processes usually involve submitting extensive documentation, including educational transcripts and employment letters. Timelines vary from a few months to over a year. Many skilled worker visas offer pathways to permanent residency after several years of continuous employment. English language proficiency tests (IELTS, TOEFL) are often mandatory for English-speaking countries. Some countries, like Germany, may require basic German language skills for integration. Family visas for dependents are usually available alongside the primary applicant's visa.
2025 Market Reality for Master Schedulers
Understanding the current market reality for Master Schedulers is critical for career success. This field has seen significant evolution from 2023 to 2025, driven by post-pandemic supply chain recalibrations and the rapid integration of AI and automation.
Broader economic factors, including inflation and interest rates, directly impact manufacturing output and thus the need for production planning expertise. Market realities for Master Schedulers vary considerably by experience level—senior roles are more stable—and by company size and geographic region, with larger enterprises and specific industrial zones offering more opportunities. This analysis provides an honest assessment to help professionals navigate these complex dynamics.
Current Challenges
Master Schedulers face increased competition from a smaller pool of available roles, especially as some companies consolidate planning functions or adopt advanced ERP systems that automate basic scheduling tasks. Economic uncertainty also prompts companies to delay or reduce new hires in operational roles, extending job search timelines. Furthermore, a skill gap exists; many candidates lack the specific proficiency in AI-driven predictive analytics tools now desired by employers, creating a barrier to entry for traditional schedulers.
Growth Opportunities
Despite challenges, strong demand persists for Master Schedulers who can navigate complex, global supply chains and integrate advanced technologies. Emerging opportunities lie in roles focused on predictive scheduling, real-time optimization, and supply chain resilience using AI-driven platforms. Professionals who specialize in these areas find themselves highly sought after.
Master Schedulers can position themselves advantageously by acquiring certifications in supply chain analytics, predictive modeling, and specific ERP systems with advanced planning modules. Demonstrating proficiency in AI tools like machine learning for demand forecasting or generative AI for scenario planning provides a significant competitive edge. Underserved markets exist in specialized manufacturing sectors experiencing growth, such as renewable energy components or advanced medical devices, where precise scheduling is paramount. Furthermore, strategic career moves into companies undergoing digital transformation or expanding their global logistics operations offer substantial growth potential. Investing in skills that bridge traditional scheduling with data science and AI offers the best return on investment.
Current Market Trends
The demand for Master Schedulers in 2025 shows a nuanced pattern. While core manufacturing and supply chain sectors maintain a steady need, the overall volume of new openings has moderated compared to the post-pandemic surge. Companies prioritize efficiency and cost reduction, leading to a focus on experienced schedulers who can optimize complex production flows and integrate new technologies.
Generative AI and advanced automation are significantly reshaping the role. Employers now seek schedulers capable of leveraging AI-powered forecasting tools, predictive analytics, and digital twins to enhance accuracy and responsiveness. This shift means traditional, manual scheduling skills are less valued; proficiency in data analysis, system integration, and scenario planning with AI support becomes paramount. Salary trends reflect this demand for advanced skills, with experienced professionals commanding competitive compensation, while entry-level roles face greater saturation and slower growth.
Geographic variations persist. Strong demand remains in manufacturing hubs and regions with robust logistics infrastructure. Remote work normalization has intensified competition for virtual roles, as candidates from broader geographic areas now apply. Cyclical trends tied to industrial production and consumer demand also influence hiring, often seeing increased activity during growth phases and slowdowns during economic contractions.
Emerging Specializations
Technological advancements and evolving global supply chains are rapidly reshaping the landscape for Master Schedulers. New specialization opportunities are emerging from the intersection of advanced analytics, artificial intelligence, and increased demands for supply chain resilience. Understanding these future-oriented career paths is crucial for professionals aiming to position themselves for significant career advancement in 2025 and beyond.
Early positioning in these emerging areas often commands premium compensation and accelerated career growth. These specializations address complex, high-value problems that traditional scheduling methods cannot resolve. While established specializations remain vital, focusing on cutting-edge areas allows professionals to become indispensable as industries increasingly adopt advanced technologies.
Many emerging areas, particularly those driven by AI and advanced analytics, are poised to become mainstream within the next three to five years, creating a significant number of job opportunities. Specializing in these cutting-edge fields involves a balance of risk and reward. While initial roles may be fewer, the long-term potential for impact and leadership is substantial for those who acquire the necessary skills.
Strategic choices in specialization allow Master Schedulers to lead the transformation of operational planning. This forward-thinking approach ensures relevance and opens doors to roles with greater strategic influence within organizations.
AI-Driven Predictive Scheduling
Supply Chain Resilience Master Scheduling
Sustainable Operations Master Scheduling
Digital Twin Scheduling Optimization
Advanced Scheduling Data Analytics
Pros & Cons of Being a Master Scheduler
Making an informed career choice requires a clear understanding of both the benefits and the challenges associated with a profession. The experience of a Master Scheduler can vary significantly based on the company's industry, its operational scale, the specific technologies used, and the overall company culture. Factors such as a company's financial health and its approach to supply chain management also play a crucial role. Furthermore, the advantages and challenges may evolve at different stages of a Master Scheduler's career, from an entry-level position to a senior strategic role. What one individual perceives as a pro, another might consider a con, depending on personal preferences, work style, and lifestyle priorities. This assessment aims to provide a realistic and balanced perspective on the Master Scheduler role, helping you set appropriate expectations.
Pros
- Master Schedulers hold a critical, central role in an organization, directly impacting operational efficiency and profitability by optimizing production and resource allocation.
- The position offers significant intellectual stimulation, as it involves complex problem-solving, strategic planning, and continuous optimization of intricate supply chain processes.
- Master Schedulers develop highly transferable skills in data analysis, forecasting, resource management, and cross-functional communication, which are valuable across various industries and roles.
- There is a clear sense of accomplishment when successfully balancing demand and supply, leading to on-time deliveries and efficient resource utilization, which provides tangible results.
- The role often involves collaboration with diverse departments, including sales, production, procurement, and logistics, offering broad exposure to different business functions and fostering strong professional networks.
- As industries increasingly rely on efficient supply chains, the demand for skilled Master Schedulers remains robust, offering good job security and consistent career opportunities.
- Many organizations utilize advanced planning systems and data analytics tools in scheduling, providing opportunities to work with cutting-edge technology and enhance technical proficiency.
Cons
- Master Schedulers often face high-pressure environments, especially when managing tight production deadlines or unexpected supply chain disruptions, which can lead to increased stress and longer work hours during critical periods.
- The role demands meticulous attention to detail and continuous data analysis, which can become repetitive and mentally draining over time, particularly when dealing with large volumes of information and constant adjustments.
- Master Schedulers frequently mediate between various departments, such as production, sales, and procurement, which can involve navigating conflicting priorities and managing interpersonal conflicts.
- Career progression can sometimes be limited within the Master Scheduler role itself, often requiring a transition into broader supply chain management or operations leadership to advance significantly.
- The job requires constant adaptation to changing market demands, material availability, and production capabilities, meaning planned schedules often need frequent, sudden revisions, leading to a dynamic but sometimes chaotic work environment.
- Reliance on accurate data from other departments means a Master Scheduler's effectiveness can be hampered by poor data quality or delays from other teams, leading to frustration and rework.
- Staying current with advanced planning software and methodologies requires continuous learning and professional development, which can be time-consuming and challenging to integrate into a busy work schedule.
Frequently Asked Questions
Master Schedulers face unique challenges in balancing production demands with material availability and resource capacity. This section addresses common questions about entering this critical role, from required analytical skills to managing supply chain disruptions and career progression in manufacturing and logistics.
What educational background or certifications do I need to become a Master Scheduler?
A bachelor's degree in supply chain management, logistics, business administration, or industrial engineering is often preferred. However, many successful Master Schedulers also have strong experience in production planning, inventory management, or materials control. Certifications like APICS CSCP or CPIM are highly valued and can significantly enhance your resume, especially if your degree is not directly related.
How long does it take to become a Master Scheduler if I'm starting from a different field?
Transitioning into a Master Scheduler role typically takes 2-5 years of foundational experience in related areas like production planning, inventory control, or demand forecasting. If you are starting from scratch, a degree and relevant certifications could take 2-4 years, followed by entry-level positions to gain practical experience before moving into a dedicated Master Scheduler role. Building strong analytical and problem-solving skills is crucial during this period.
What is the typical salary range for a Master Scheduler?
Salaries for Master Schedulers vary based on experience, industry, and location. Entry-level positions might start around $55,000 to $70,000 annually. Experienced Master Schedulers, especially those in complex manufacturing or global supply chains, can earn $80,000 to $120,000 or more. Companies with higher production volumes or more volatile demand often offer competitive compensation due to the role's critical impact.
What is the typical work-life balance for a Master Scheduler, and does it involve a lot of overtime?
The work-life balance for a Master Scheduler can vary. During normal operations, it often involves standard business hours. However, unexpected production issues, supply chain disruptions, or urgent demand changes can require extended hours to adjust schedules and mitigate impact. The role demands responsiveness and a proactive approach to problem-solving, which can sometimes extend beyond typical workdays, especially in fast-paced industries.
Is the Master Scheduler role secure, or is it at risk from automation?
Job security for Master Schedulers is generally strong due to the critical nature of the role in manufacturing and logistics. Companies constantly need efficient production planning to minimize costs and meet customer demand. The demand for skilled schedulers is stable, particularly for those who can adapt to new technologies like advanced planning systems and manage complex global supply chains. Automation may change some tasks, but the strategic decision-making aspect of the role remains vital.
What are the common career advancement paths for a Master Scheduler?
Career growth for Master Schedulers often leads to roles such as Senior Master Scheduler, Planning Manager, Supply Chain Manager, or Director of Operations. With experience and strong performance, you can specialize in areas like demand planning, inventory optimization, or supply chain analytics. Continuous learning in areas like ERP systems, lean manufacturing, and data analysis will open doors to higher-level management and strategic positions within the supply chain.
What are the biggest challenges or frustrations of being a Master Scheduler?
The biggest challenge is balancing competing priorities, such as customer delivery dates, production efficiency, and material availability, often with limited resources. You must quickly adapt to unforeseen disruptions like supplier delays or equipment breakdowns while maintaining a feasible and optimal production plan. Effective communication with various departments, from sales to production, is also a constant challenge, as everyone has different objectives.
Can a Master Scheduler work remotely, or is it primarily an in-office role?
While some companies offer remote or hybrid options for Master Schedulers, many roles require on-site presence. This is because the position often involves close collaboration with production teams, warehouse staff, and other departments directly involved in the physical flow of goods. Being present allows for quicker problem-solving, better understanding of shop floor realities, and direct engagement with the operational teams you support. Remote options are more common in roles focused solely on demand forecasting or global supply chain planning, but less so for day-to-day production scheduling.
Related Careers
Explore similar roles that might align with your interests and skills:
Production Scheduler
A growing field with similar skill requirements and career progression opportunities.
Explore career guideScheduler
A growing field with similar skill requirements and career progression opportunities.
Explore career guideScheduling Coordinator
A growing field with similar skill requirements and career progression opportunities.
Explore career guideScheduling Manager
A growing field with similar skill requirements and career progression opportunities.
Explore career guidePersonnel Scheduler
A growing field with similar skill requirements and career progression opportunities.
Explore career guideAssess your Master Scheduler readiness
Understanding where you stand today is the first step toward your career goals. Our Career Coach helps identify skill gaps and create personalized plans.
Skills Gap Analysis
Get a detailed assessment of your current skills versus Master Scheduler requirements. Our AI Career Coach identifies specific areas for improvement with personalized recommendations.
See your skills gapCareer Readiness Assessment
Evaluate your overall readiness for Master Scheduler roles with our AI Career Coach. Receive personalized recommendations for education, projects, and experience to boost your competitiveness.
Assess your readinessSimple pricing, powerful features
Upgrade to Himalayas Plus and turbocharge your job search.
Himalayas
Himalayas Plus
Himalayas Max
Find your dream job
Sign up now and join over 100,000 remote workers who receive personalized job alerts, curated job matches, and more for free!
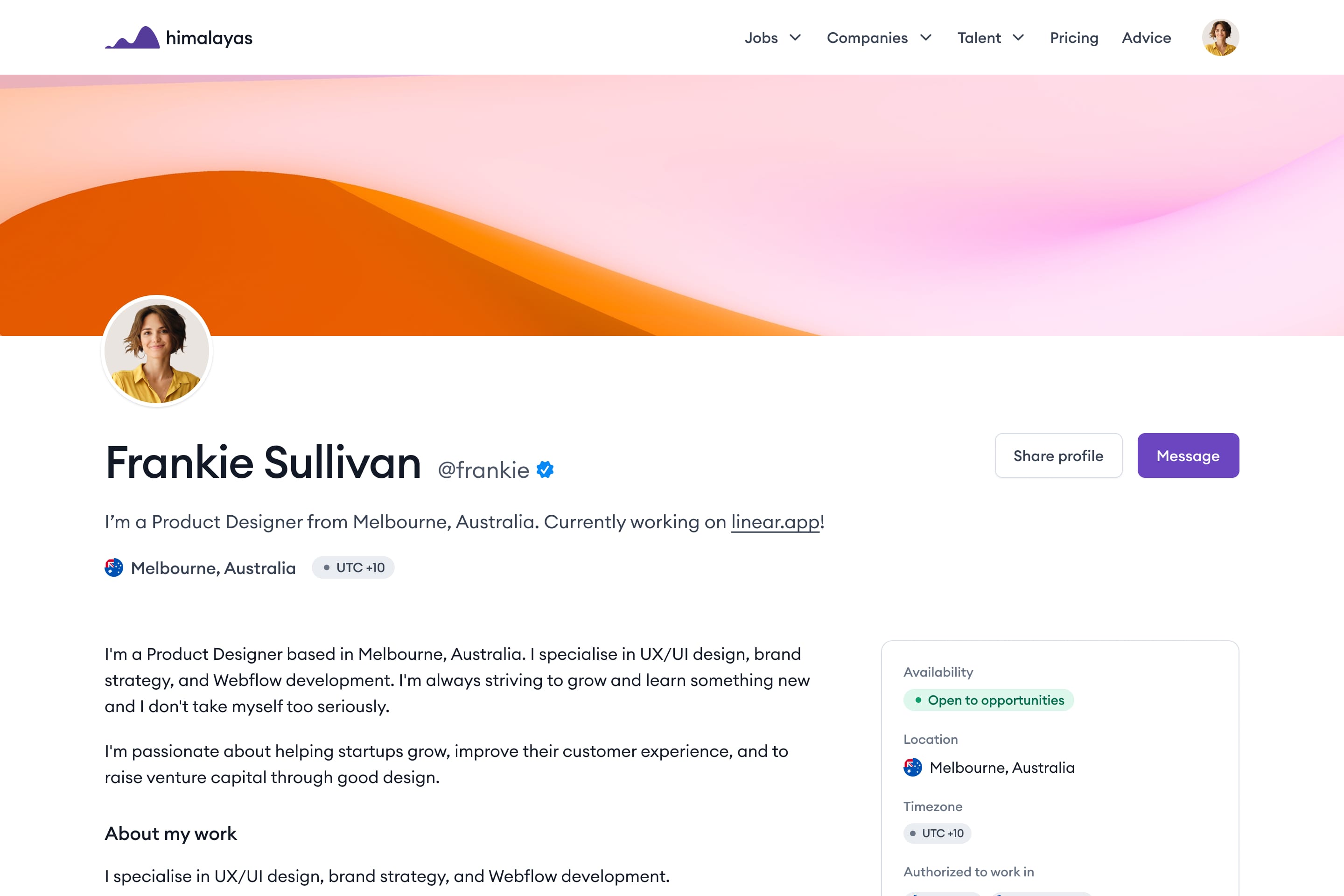