Complete Precast Concrete Ironworker Career Guide
Precast Concrete Ironworkers are the skilled artisans who bring strength and precision to modern construction, specializing in the assembly and installation of pre-fabricated concrete components. This vital role ensures structural integrity in buildings, bridges, and infrastructure, offering a tangible impact on the built environment.
You'll combine traditional ironworking skills with specialized knowledge of precast systems, contributing to efficient and robust construction projects across diverse sectors.
Key Facts & Statistics
Median Salary
$60,920 USD
(U.S. national median for all Ironworkers)
Range: $40k - $90k+ USD (typical range for Ironworkers, varies by experience, location, and specialization), BLS
Growth Outlook
5%
as fast as average (for all Ironworkers), U.S. Bureau of Labor Statistics (BLS), 2022-2032
Annual Openings
≈30,700
openings annually (for all Ironworkers, including precast specialists), U.S. Bureau of Labor Statistics (BLS)
Top Industries
Typical Education
High school diploma or equivalent, followed by a formal apprenticeship (typically 3-4 years) or on-the-job training. Some may obtain certifications in welding or rigging.
What is a Precast Concrete Ironworker?
A Precast Concrete Ironworker specializes in the safe and precise erection of pre-manufactured concrete components on construction sites. Unlike traditional ironworkers who might focus solely on structural steel, this role centers specifically on handling and installing large, heavy precast concrete panels, beams, columns, and other elements that arrive ready-made from a fabrication plant. Their primary purpose is to assemble these components into the final structure, ensuring exact alignment and secure connections.
This role is distinct from a general Ironworker because of its specialized focus on concrete units, which requires different rigging techniques, connection methods, and an understanding of concrete's unique properties and handling requirements. They are also different from concrete finishers, who work with wet concrete on-site; Precast Concrete Ironworkers deal with cured, finished concrete sections. Their expertise ensures the structural integrity and aesthetic quality of buildings, parking garages, and bridges constructed with precast systems, contributing significantly to project speed and efficiency.
What does a Precast Concrete Ironworker do?
Key Responsibilities
- Read and interpret blueprints, schematics, and erection drawings to determine the precise placement and sequence of precast concrete panels and structural elements.
- Operate heavy machinery, including cranes, forklifts, and aerial lifts, to safely hoist, move, and position large precast concrete components.
- Connect precast sections using various methods such as welding, bolting, and reinforcing bar splicing, ensuring structural integrity and precise alignment.
- Install embeds, shims, and leveling plates to achieve accurate elevation and plumbness for each precast unit, maintaining strict tolerances.
- Perform quality checks on installed components, verifying dimensions, connections, and finishes to meet project specifications and safety standards.
- Work collaboratively with crane operators, concrete finishers, and project managers to coordinate lifting operations and installation schedules.
- Adhere strictly to all safety protocols, including fall protection, rigging safety, and personal protective equipment usage, to prevent accidents on site.
Work Environment
Precast Concrete Ironworkers primarily work outdoors on construction sites, which means exposure to various weather conditions, including heat, cold, rain, and wind. The work involves significant physical exertion, including heavy lifting, climbing, bending, and working at heights. The environment is often noisy and dusty, requiring strict adherence to personal protective equipment (PPE) like hard hats, safety glasses, gloves, and steel-toed boots. Teamwork and clear communication are crucial for safety and efficiency, as tasks often involve coordinating with crane operators and other trades. Work schedules can vary, sometimes including early mornings, evenings, or weekends to meet project deadlines.
Tools & Technologies
Precast Concrete Ironworkers utilize a range of specialized tools and heavy equipment. They regularly operate cranes (mobile, tower, crawler), forklifts, and various types of aerial work platforms like scissor lifts and boom lifts for positioning heavy components. Hand tools include wrenches, hammers, levels, tape measures, and cutting torches for metal work. Power tools such as grinders, drills, and welding equipment (SMAW, FCAW) are essential for making connections. They also work with rigging gear, including slings, shackles, and spreader bars, to safely lift and maneuver precast units. Blueprint reading software and communication devices like two-way radios are also critical for coordination on site.
Precast Concrete Ironworker Skills & Qualifications
The Precast Concrete Ironworker role demands a unique blend of structural knowledge and hands-on fabrication skills. Qualifications for this position are heavily weighted towards practical experience and certifications, rather than solely formal academic degrees. While a high school diploma or GED is foundational, success hinges on mastering specific trade skills.
Requirements for Precast Concrete Ironworkers vary significantly based on seniority and the specific type of precast products a company specializes in. Entry-level positions often focus on basic rigging, rebar tying, and form preparation. Senior roles require advanced welding, blueprint interpretation, and the ability to lead installation teams. Company size also plays a role; larger firms might have more specialized roles, while smaller shops expect versatility across many tasks.
Formal apprenticeships are a highly valued pathway into this trade, providing structured learning and on-the-job training. Industry-specific certifications, particularly in welding, rigging, and safety, significantly boost a candidate's marketability and demonstrate competency. The skill landscape is evolving with increasing adoption of automation in precast yards, requiring workers to adapt to new machinery and digital tools. A strong balance between traditional craftsmanship and an openness to new technologies is crucial for long-term success in this field.
Education Requirements
Technical Skills
- Blueprint Reading and Interpretation: Understanding structural and architectural drawings for rebar placement, formwork, and panel assembly.
- Rebar Fabrication and Tying: Cutting, bending, and securely tying steel reinforcing bars according to specifications.
- Welding (SMAW, FCAW): Proficiency in various welding processes for connecting steel components within precast elements and during installation.
- Rigging and Lifting Techniques: Safe operation and inspection of rigging equipment, including slings, chains, and hoists, for moving heavy precast units.
- Formwork Assembly and Dismantling: Constructing, setting, and stripping molds for concrete casting.
- Concrete Pouring and Finishing: Assisting with concrete placement, vibration, and basic finishing techniques.
- Hand and Power Tool Operation: Safe and effective use of grinders, saws, drills, rebar cutters, and other trade-specific tools.
- Quality Control and Inspection: Identifying defects in rebar, forms, or finished concrete and ensuring adherence to project standards.
- Basic Surveying and Layout: Using measuring tapes, levels, and laser tools for accurate placement and alignment of precast components.
Soft Skills
- Attention to Detail: Essential for ensuring precise rebar placement, accurate measurements, and correct assembly of precast elements, which directly impacts structural integrity and safety.
- Problem-Solving: Crucial for addressing unexpected challenges during fabrication or installation, such as fitting issues, material inconsistencies, or site-specific obstacles.
- Adherence to Safety Protocols: Paramount in a high-risk environment involving heavy machinery, elevated work, and hazardous materials; strict compliance prevents injuries and ensures project continuity.
- Team Collaboration: Vital for coordinating complex lifts, aligning large precast sections, and working efficiently with crane operators, welders, and other trades on site.
- Physical Stamina and Durability: Necessary for enduring long hours of manual labor, heavy lifting, and working in various weather conditions, maintaining productivity throughout the workday.
- Adaptability: Important for adjusting to changing project specifications, varying site conditions, and new equipment or techniques in the evolving precast industry.
How to Become a Precast Concrete Ironworker
Entering the precast concrete ironworker field offers several pathways, primarily through apprenticeships, vocational training, or direct entry as a labor hand. A formal apprenticeship provides the most structured and comprehensive training, typically lasting 3-4 years and covering both theoretical knowledge and practical on-the-job skills. Direct entry as a general labor hand or helper at a precast plant allows individuals to learn on the job, but progress might be slower and less formalized.
Timeline expectations vary significantly. A dedicated individual might secure an entry-level labor position within a few weeks to months, while an apprenticeship application process can take 6-12 months to complete before training begins. Geographic location plays a role; larger metropolitan areas with more construction projects often have more precast plants and union apprenticeship programs, potentially offering more opportunities than smaller, rural markets. Company size also matters; larger precast manufacturers may have structured training programs, while smaller shops might offer more hands-on, informal learning.
Misconceptions often include believing that extensive prior construction experience is mandatory, or that only unionized roles exist. Many entry-level positions welcome individuals with a strong work ethic and willingness to learn. While unions are a significant part of the industry, non-union opportunities are also available, especially in smaller companies. Building a strong network within local construction trades, attending industry events, and showing genuine interest can significantly enhance your chances of finding opportunities and mentorship.
Step 1
Step 2
Step 3
Step 4
Step 5
Step 6
Education & Training Needed to Become a Precast Concrete Ironworker
Becoming a Precast Concrete Ironworker primarily involves hands-on training and specific certifications, rather than traditional academic degrees. While a high school diploma or GED is generally a prerequisite, formal university programs are not typical for this trade. Apprenticeships are the most recognized and effective pathway, offering structured on-the-job learning combined with classroom instruction. These programs typically last 3-4 years, with apprentices earning wages while they learn. The cost for apprenticeships is often minimal, primarily involving union dues or small program fees, making them highly cost-effective compared to other educational routes.
Alternative pathways include vocational training schools, which offer shorter, more focused programs ranging from 6 months to 2 years. These can cost anywhere from $5,000 to $20,000, providing foundational skills but often requiring further on-the-job experience to achieve journeyman status. Self-study combined with entry-level labor positions can also lead to this role, though advancement may be slower without a structured program. Employers highly value practical experience and certifications in welding, rigging, and safety, which are often integrated into apprenticeship curricula. The industry strongly prefers individuals with documented training and a proven safety record.
Continuous learning is vital in this field, particularly for staying current with new materials, techniques, and safety regulations. Specialized certifications in areas like OSHA safety, crane signaling, and specific welding techniques enhance an ironworker's marketability and earning potential. These certifications often require renewal and involve short courses, ranging from a few hundred to a few thousand dollars. The return on investment for formal apprenticeships is high, as they provide comprehensive skills, industry recognition, and direct pathways to well-paying jobs. In contrast, solely relying on self-study can limit career progression and employer trust.
Precast Concrete Ironworker Salary & Outlook
Compensation for a Precast Concrete Ironworker varies significantly based on several factors beyond just base salary. Geographic location plays a crucial role, with higher wages typically found in metropolitan areas and regions with strong construction activity, reflecting both higher costs of living and increased demand for skilled labor. For instance, salaries in the Northeast or Pacific Northwest generally exceed those in the Midwest or Southeast.
Experience level, specialized certifications, and specific skill sets in handling complex precast elements or advanced welding techniques directly impact earning potential. Total compensation packages often include more than just hourly wages; these can encompass overtime pay, project completion bonuses, health insurance, retirement plans (like 401k contributions), and sometimes even per diem allowances for travel to remote job sites. Union membership also frequently provides higher wages and more comprehensive benefits compared to non-union roles.
Industry-specific trends, such as infrastructure spending and commercial development, drive salary growth in this field. Precast concrete ironworkers with a proven track record of efficiency, safety, and leadership can command premium compensation. Remote work is generally not applicable to this hands-on role, meaning geographic arbitrage opportunities are limited. While the provided figures are in USD, international markets present different compensation structures based on local labor laws, economic conditions, and construction demand.
Salary by Experience Level
Level | US Median | US Average |
---|---|---|
Apprentice Precast Concrete Ironworker | $40k USD | $45k USD |
Journeyman Precast Concrete Ironworker | $60k USD | $65k USD |
Lead Precast Concrete Ironworker | $75k USD | $78k USD |
Foreman (Precast Concrete Ironwork) | $85k USD | $90k USD |
Supervisor (Precast Concrete Ironwork) | $100k USD | $105k USD |
Market Commentary
The job market for Precast Concrete Ironworkers shows a steady demand, driven by ongoing infrastructure projects, commercial construction, and the increasing adoption of prefabrication techniques in the building industry. The Bureau of Labor Statistics projects a growth rate for ironworkers, including those specializing in precast concrete, that is about as fast as the average for all occupations, with specific demand influenced by regional construction booms. This growth is underpinned by the efficiency and durability benefits of precast concrete, which continue to make it a favored material in various construction sectors.
Emerging opportunities in this field include specialization in advanced rigging, crane operations, and the installation of increasingly complex architectural precast elements. Technological changes, such as the use of Building Information Modeling (BIM) for precise prefabrication and robotic welding in manufacturing plants, are influencing skill requirements, emphasizing the need for ironworkers to adapt to digital tools and automated processes. Despite these advancements, the hands-on nature of installation ensures that human expertise remains critical, mitigating significant impact from full automation.
Supply and demand dynamics in this trade often favor skilled and certified ironworkers, as the demand for their specialized abilities frequently outpaces the number of qualified candidates. This imbalance can lead to competitive wages and stable employment opportunities. Geographically, major urban centers and areas with significant public works investments, like bridge repairs or new transit systems, serve as hotspots for employment. This profession is relatively recession-resistant due to the ongoing need for infrastructure maintenance and development, providing a stable career path for those with the necessary skills and dedication to continuous learning in evolving construction methods.
Precast Concrete Ironworker Career Path
Career progression for a Precast Concrete Ironworker typically follows a structured path, moving from foundational skills to advanced leadership and project management. This field values hands-on experience, precision, and adherence to safety protocols. Professionals advance by mastering complex fabrication and installation techniques, demonstrating reliability, and taking on greater responsibility.
Advancement often involves distinguishing between an individual contributor (IC) track, focused on technical mastery and specialized fabrication, and a management/leadership track, which emphasizes team oversight and project coordination. Factors influencing progression include consistent performance, the complexity of projects undertaken, and the ability to mentor others. Company size, from smaller, specialized shops to large-scale industrial manufacturers, also dictates the speed and specific opportunities for advancement.
Lateral movement within the precast industry might involve specializing in specific types of precast elements, such as architectural panels or structural components. Networking within the trade, seeking mentorship from experienced ironworkers, and maintaining a strong reputation for quality and safety are crucial. Certifications in welding, rigging, or specific equipment operation mark significant milestones, enhancing an ironworker's value and opening doors to higher roles. Some ironworkers may transition into roles like quality control, safety inspection, or even become estimators or project coordinators for precast concrete companies.
Apprentice Precast Concrete Ironworker
0-3 yearsKey Focus Areas
Journeyman Precast Concrete Ironworker
3-7 years total experienceKey Focus Areas
Lead Precast Concrete Ironworker
7-12 years total experienceKey Focus Areas
Foreman (Precast Concrete Ironwork)
12-18 years total experienceKey Focus Areas
Supervisor (Precast Concrete Ironwork)
18+ years total experienceKey Focus Areas
Apprentice Precast Concrete Ironworker
0-3 yearsWorks under direct supervision, assisting Journeyman Ironworkers with basic tasks. Participates in the assembly of rebar cages, forms, and inserts for precast concrete elements. Primarily involved in learning and executing entry-level fabrication and assembly processes.
Key Focus Areas
Develop foundational skills in rebar cutting, bending, and tying. Learn to read blueprints and shop drawings accurately. Focus on understanding material properties, basic rigging, and adherence to all site-specific and general safety regulations. Build a strong work ethic and attention to detail.
Journeyman Precast Concrete Ironworker
3-7 years total experienceWorks independently on various precast concrete fabrication tasks, assembling complex rebar cages and setting up forms. Takes responsibility for the quality and accuracy of their work. Often guides and provides on-the-job training to Apprentices, contributing to team efficiency and project timelines.
Key Focus Areas
Master advanced rebar tying techniques, welding, and rigging. Develop proficiency in using specialized tools and equipment for precast fabrication. Enhance blueprint reading skills to interpret complex designs. Focus on problem-solving during assembly and maintaining high quality standards. Begin to mentor Apprentices.
Lead Precast Concrete Ironworker
7-12 years total experienceDirects small teams of Journeyman and Apprentice Ironworkers on specific fabrication or assembly sections. Assigns tasks, monitors progress, and ensures adherence to quality and safety standards. Acts as a key point of contact for technical questions and resolves immediate on-site issues, contributing to efficient project execution.
Key Focus Areas
Cultivate strong leadership and communication skills. Develop the ability to organize tasks, manage materials, and coordinate with other trades. Focus on advanced problem-solving, ensuring project specifications are met, and optimizing workflow. Begin to understand project scheduling and resource allocation.
Foreman (Precast Concrete Ironwork)
12-18 years total experienceOversees an entire section or multiple smaller projects within the precast concrete facility. Manages a larger team of ironworkers, ensuring project deadlines, budgets, and quality standards are met. Responsible for daily production reports, material requisitions, and safety compliance, directly impacting project profitability and client satisfaction.
Key Focus Areas
Strengthen project management and team leadership capabilities. Develop skills in conflict resolution, performance management, and effective communication with management and clients. Focus on strategic planning for project phases, risk assessment, and continuous improvement of fabrication processes. Pursue advanced safety certifications.
Supervisor (Precast Concrete Ironwork)
18+ years total experienceManages all ironwork operations within a precast concrete plant or across several projects. Responsible for overall departmental performance, including safety, quality, productivity, and cost control. Develops and implements operational policies, conducts performance reviews, and makes key hiring decisions, influencing the company's long-term success.
Key Focus Areas
Develop comprehensive operational management skills, including budgeting, scheduling, and resource optimization across multiple projects. Focus on strategic planning for the department, implementing new technologies or processes, and fostering a culture of safety and excellence. Build strong relationships with clients and suppliers.
Job Application Toolkit
Ace your application with our purpose-built resources:
Precast Concrete Ironworker Resume Examples
Proven layouts and keywords hiring managers scan for.
View examplesPrecast Concrete Ironworker Cover Letter Examples
Personalizable templates that showcase your impact.
View examplesTop Precast Concrete Ironworker Interview Questions
Practice with the questions asked most often.
View examplesPrecast Concrete Ironworker Job Description Template
Ready-to-use JD for recruiters and hiring teams.
View examplesGlobal Precast Concrete Ironworker Opportunities
Precast Concrete Ironworkers install and connect pre-manufactured concrete components globally. This specialized role is in high demand in countries with significant infrastructure development and modular construction growth. Regulatory differences in building codes and safety standards require adaptable professionals. Many consider international roles for higher wages and diverse project experience. No specific international certifications exist, but local licensing is often crucial.
Global Salaries
Salaries for Precast Concrete Ironworkers vary significantly by region and economic development. In North America, a skilled Ironworker earns between $60,000 and $90,000 USD annually in the United States, and $70,000 to $100,000 CAD in Canada ($50,000-$73,000 USD). These figures often include comprehensive benefits like health insurance, retirement plans, and paid vacation time, which substantially increase the overall compensation package.
Europe offers diverse salary landscapes. In Western European countries like Germany or the Netherlands, annual salaries typically range from €40,000 to €60,000 ($43,000-$65,000 USD). These countries often have strong social security systems, meaning higher take-home pay might be offset by higher taxes. Eastern European nations like Poland or Romania may offer €18,000 to €30,000 ($19,500-$32,500 USD), but with a much lower cost of living, purchasing power can be comparable.
In the Asia-Pacific region, Australia provides high compensation, with Ironworkers earning AUD 70,000 to AUD 100,000 ($46,000-$66,000 USD) due to high demand and unionization. Meanwhile, in developing Asian markets like India or Vietnam, salaries might be significantly lower, ranging from $8,000 to $15,000 USD annually, reflecting different economic scales and labor costs. Experience and specialized skills, such as advanced rigging or welding certifications, always command higher pay globally, regardless of the country.
Remote Work
Precast Concrete Ironwork is inherently a hands-on, on-site profession. Therefore, direct remote work opportunities are virtually non-existent for the core installation and connection tasks. The job demands physical presence at construction sites to handle and position heavy precast elements.
However, some related functions can be remote. Project coordination, scheduling, and material procurement for precast projects might be handled remotely by management or administrative staff. Digital nomad opportunities do not apply to the Precast Concrete Ironworker role itself. Companies hiring for this field typically require employees to reside near or be willing to relocate to project sites. Salary expectations for site-based work reflect the physical demands and location requirements. International remote work policies are not applicable to the on-site nature of this specific trade.
Visa & Immigration
Precast Concrete Ironworkers seeking international employment primarily use skilled worker visas. Countries like Canada (through Express Entry with specific NOC codes), Australia (via skilled migration programs), and various European Union nations (with Blue Card or national skilled worker visas) have pathways. Requirements typically include recognized trade qualifications, several years of experience, and often a job offer from a local employer. Credential recognition for trade skills is vital; some countries require skill assessments or equivalency tests.
Typical visa timelines range from a few months to over a year, depending on the country and application backlog. Language proficiency, usually English or the local language, is often a requirement for integration and safety on site. Germany's skilled worker visa or the UK's Skilled Worker visa are common routes. Pathways to permanent residency exist after several years of continuous employment and tax contributions. Family visas for dependents are usually available once the primary applicant secures their work visa. Some countries offer fast-track processing for occupations in high demand, which can sometimes include specialized trades like Precast Concrete Ironwork.
2025 Market Reality for Precast Concrete Ironworkers
Understanding current market conditions is paramount for precast concrete ironworkers navigating their careers. This specialized trade has seen shifts in recent years, influenced by post-pandemic supply chain adjustments and a broader push towards efficiency in construction. Economic factors, including interest rates and government infrastructure spending, directly impact project volume for precast components.
Market realities for precast concrete ironworkers vary significantly by experience level, with senior, certified professionals in higher demand. Geographic regions with active commercial and public works construction also present more opportunities. Smaller fabrication shops might offer different experiences than large-scale manufacturing plants. This analysis provides an honest assessment of current hiring realities.
Current Challenges
Precast concrete ironworkers face challenges from increased competition, especially for entry-level positions, as more individuals seek trades careers. Economic slowdowns can directly impact construction project timelines, reducing immediate demand for these specialized roles. Skill gaps persist, particularly in adapting to new prefabrication technologies or advanced rigging techniques, which employers now prioritize.
The job search timeline for precast concrete ironworkers can extend, especially in regions with fewer large-scale precast facilities or during periods of reduced commercial construction starts. Industry consolidation also limits the number of potential employers in some areas.
Growth Opportunities
Specific areas within the precast concrete ironworker field experiencing strong demand include infrastructure projects like bridges, tunnels, and large-scale public transit systems, which heavily rely on precast elements. Data centers and large industrial facilities also offer consistent work for specialized precast installation teams.
Emerging opportunities exist in sustainable construction, where precast concrete offers advantages in energy efficiency and waste reduction. Ironworkers proficient in installing insulated precast panels or those with experience in modular construction techniques will find growing niches. Professionals can position themselves advantageously by acquiring advanced certifications in specific welding techniques for precast connections, digital blueprint reading, or specialized rigging for complex lifts.
Underserved markets often align with regions undergoing significant urban redevelopment or those receiving substantial federal infrastructure funding. Skills in precision assembly, a strong understanding of structural integrity, and the ability to work with various precast connection types provide competitive advantages. Market corrections might create opportunities for those willing to relocate or specialize in less common precast applications, such as architectural precast or specialized retaining wall systems.
Current Market Trends
The precast concrete ironworker market in 2025 sees steady, though not explosive, demand. Infrastructure projects and modular construction trends maintain a baseline need for skilled ironworkers specializing in precast elements. However, the industry prioritizes efficiency and precision, leading to a demand for workers proficient with modern lifting equipment, digital blueprints, and safety protocols.
Recent industry changes include a greater emphasis on off-site construction and prefabrication, which directly benefits precast ironworkers. This shift means more work occurs in controlled factory environments before on-site assembly. Economic conditions, while stable, mean that larger, riskier projects face more scrutiny, impacting the pipeline for some major precast installations. Smaller to medium-sized projects, particularly in residential and light commercial sectors utilizing precast, provide consistent work.
Technology trends, such as advanced lifting automation and augmented reality for precise placement, are slowly integrating into larger precast operations. This requires precast ironworkers to be adaptable and willing to learn new digital tools. Employer requirements increasingly include certifications in specific rigging, welding, and safety standards, beyond general ironworking skills. Companies seek individuals who can integrate seamlessly into a highly coordinated prefabrication and installation workflow.
Salary trends for experienced precast concrete ironworkers remain competitive, especially for those with specialized certifications in complex rigging or welding specific to precast connections. Entry-level saturation is less pronounced than in general construction trades, given the specialized nature of the work, but competition for apprenticeships exists. Geographic variations are significant; areas with robust infrastructure development, manufacturing hubs, or rapidly expanding urban centers show stronger market activity. Remote work is not applicable to this hands-on role.
Emerging Specializations
The construction industry, particularly the precast concrete sector, is undergoing significant transformation driven by technological advancements and a renewed focus on efficiency and sustainability. These shifts are creating new specialization opportunities for Precast Concrete Ironworkers, moving beyond traditional rebar tying and erection. Understanding these evolving niches allows professionals to strategically position themselves for the future.
Early positioning in these emerging areas can lead to substantial career advancement and often commands premium compensation starting in 2025 and beyond. As these specializations mature, demand for skilled workers in these precise fields will intensify. While established specializations remain vital, focusing on cutting-edge areas offers a clear pathway to leadership roles and innovative project involvement.
Emerging areas typically take 3-5 years to transition from novel concepts to mainstream practices with significant job opportunities. Investing in these skills now involves a calculated risk, as not all innovations achieve widespread adoption. However, the potential rewards of being an early adopter in a field like robotic rebar assembly or advanced structural scanning significantly outweigh the risks for ambitious professionals.
Automated Rebar Assembly System Operator
Precast Concrete Ironworkers specializing in Automated Rebar Assembly Systems operate and maintain robotic equipment used for tying and positioning rebar cages. This specialization addresses the industry's need for increased speed, precision, and safety in rebar fabrication, reducing manual labor and human error. As automation becomes more prevalent in prefabrication yards, expertise in these systems is crucial.
Digital Precast Element Layout Specialist
This specialization involves setting up and operating digital surveying equipment, such as total stations and laser scanners, to ensure precise placement and alignment of precast concrete elements. Digital layout specialists interpret complex 3D models and blueprints, translating them into accurate on-site measurements for crane operators and rigging teams. Their role minimizes costly errors and rework, enhancing project efficiency.
Integrated MEP Precast Module Installer
Precast Concrete Ironworkers with this specialization focus on the safe and efficient installation of modular precast units that integrate mechanical, electrical, and plumbing (MEP) systems. This requires a deep understanding of multi-trade coordination, precise rigging for complex assemblies, and quality control checks for embedded systems. This area is growing as projects increasingly adopt off-site modular construction.
Energy-Efficient Precast Panel Erector
This emerging area focuses on the installation and connection of precast concrete elements designed for enhanced thermal performance and energy efficiency. Ironworkers in this field often work with insulated sandwich panels, thermal breaks, and specialized connection details that minimize heat transfer. Demand for these skills grows as sustainable construction practices become standard.
Pros & Cons of Being a Precast Concrete Ironworker
Making a career choice is a significant decision that benefits greatly from a thorough understanding of both the positive aspects and the inherent challenges. A career as a Precast Concrete Ironworker, like many specialized trades, offers unique rewards alongside specific difficulties. Individual experiences can vary significantly based on the employer, the specific projects undertaken, company culture, and even the worker's personal aptitude and preferences. What one person views as a benefit, such as consistent physical activity, another might see as a demanding challenge. Moreover, the nature of pros and cons can evolve throughout a career; for example, a demanding learning curve early on might lead to greater autonomy and satisfaction later. This assessment aims to provide a realistic and balanced perspective to help individuals set appropriate expectations and determine if this demanding yet rewarding path aligns with their personal and professional goals.
Pros
- Precast concrete ironworkers typically earn competitive wages, often with opportunities for overtime pay, reflecting the specialized skills and physical demands of the role.
- There is a consistent demand for skilled precast concrete ironworkers in the construction industry, providing good job security and steady employment opportunities across various projects.
- The work is hands-on and tangible, allowing ironworkers to see the direct results of their labor in the form of completed structures, which can be highly satisfying.
- This career offers clear pathways for skill development and advancement, from entry-level positions to becoming a foreman, supervisor, or even moving into project management roles.
- Precast concrete ironworkers often work as part of a close-knit team, fostering strong camaraderie and a supportive work environment where individuals rely on each other's skills and cooperation.
- The job involves solving practical problems daily, requiring critical thinking and adaptability to overcome challenges on the construction site, which can be intellectually stimulating.
- Many employers provide on-the-job training and apprenticeship programs, allowing individuals to enter the field with minimal prior experience and gain valuable skills while earning a living.
Cons
- Precast concrete ironworkers often work outdoors in varying weather conditions, from extreme heat to cold, rain, or snow, which can be physically demanding and uncomfortable.
- The work involves heavy lifting, repetitive motions, and working at heights, leading to a high risk of injuries such as strains, sprains, falls, and cuts if safety protocols are not strictly followed.
- Project-based work can lead to periods of unemployment or inconsistent hours between jobs, requiring workers to be adaptable and manage their finances carefully.
- The physical demands of the job can take a toll on the body over time, potentially leading to chronic pain or long-term health issues for some individuals.
- Work schedules can be irregular, with early starts, long shifts, and occasional weekend work required to meet project deadlines, impacting personal time and work-life balance.
- Travel to different job sites is frequently required, sometimes involving long commutes or temporary relocation for the duration of a project, which can be disruptive.
- The work environment often includes loud noises from machinery, dust from concrete, and exposure to various chemicals, necessitating proper personal protective equipment and ventilation to mitigate health risks and ensure safety on the jobsite.
Frequently Asked Questions
What is the typical path to become a Precast Concrete Ironworker?
Becoming a Precast Concrete Ironworker typically involves completing an apprenticeship, which lasts 3-4 years. These programs combine paid on-the-job training with classroom instruction, covering blueprint reading, rebar tying, welding, rigging, and safety protocols. Some start as laborers and gain experience before entering an apprenticeship.
How physically demanding is this job, and what are the typical working conditions?
The physical demands are significant, requiring strength, stamina, and good hand-eye coordination. You will lift and move heavy rebar, bend and cut steel, and work in various weather conditions within a precast plant environment. The job involves standing for long periods, bending, kneeling, and working at heights or in confined spaces within forms.
What are the key safety considerations and training involved in this role?
Safety is paramount in precast concrete plants, with strict protocols in place. Ironworkers receive extensive training in fall protection, crane signaling, rigging safety, and proper use of power tools. Adhering to these rules and wearing personal protective equipment (PPE) like hard hats, safety glasses, steel-toed boots, and gloves is mandatory to mitigate risks.
What are the salary expectations and potential benefits for a Precast Concrete Ironworker?
Entry-level Precast Concrete Ironworkers can expect to earn competitive wages, often starting above minimum wage during apprenticeships, with regular increases as skills develop. Fully qualified journeymen can earn excellent hourly rates, typically higher than general construction laborers, plus benefits like health insurance, retirement plans, and pension contributions through union agreements.
What is the job security like for Precast Concrete Ironworkers?
Job security in precast concrete ironworking is generally stable, driven by consistent demand for infrastructure, commercial, and residential construction projects. Precast plants often operate year-round, offering more consistent work than outdoor-dependent construction roles. Skilled ironworkers are always in demand, especially those with specialized knowledge of precast applications.
What are the career advancement opportunities for a Precast Concrete Ironworker?
Career growth paths include becoming a foreman, supervisor, or moving into quality control, safety management, or project management within a precast plant. Experienced ironworkers can also specialize in complex rebar designs, welding, or rigging. Continuous learning and taking on leadership roles can lead to significant advancement.
What is the typical work schedule and work-life balance in this role?
While some precast plants operate in shifts, work-life balance generally depends on project deadlines and plant workload. Overtime is common during busy periods, but the work is often more predictable than on-site construction, as it is factory-based. Many union contracts provide clear guidelines for hours and overtime pay, contributing to better work-life predictability.
How is technology impacting the Precast Concrete Ironworker role?
The precast industry is increasingly adopting automation and advanced fabrication techniques. This means future Precast Concrete Ironworkers will need to be adaptable, potentially working with robotic rebar welders or digital layout tools. Staying updated on new technologies and materials will be crucial for long-term career success in this evolving field.
Related Careers
Explore similar roles that might align with your interests and skills:
Concrete Worker
A growing field with similar skill requirements and career progression opportunities.
Explore career guideIronworker
A growing field with similar skill requirements and career progression opportunities.
Explore career guideConstruction Ironworker
A growing field with similar skill requirements and career progression opportunities.
Explore career guidePre-Engineered Metal Building Ironworker
A growing field with similar skill requirements and career progression opportunities.
Explore career guideRebar Worker
A growing field with similar skill requirements and career progression opportunities.
Explore career guideAssess your Precast Concrete Ironworker readiness
Understanding where you stand today is the first step toward your career goals. Our Career Coach helps identify skill gaps and create personalized plans.
Skills Gap Analysis
Get a detailed assessment of your current skills versus Precast Concrete Ironworker requirements. Our AI Career Coach identifies specific areas for improvement with personalized recommendations.
See your skills gapCareer Readiness Assessment
Evaluate your overall readiness for Precast Concrete Ironworker roles with our AI Career Coach. Receive personalized recommendations for education, projects, and experience to boost your competitiveness.
Assess your readinessSimple pricing, powerful features
Upgrade to Himalayas Plus and turbocharge your job search.
Himalayas
Himalayas Plus
Himalayas Max
Find your dream job
Sign up now and join over 100,000 remote workers who receive personalized job alerts, curated job matches, and more for free!
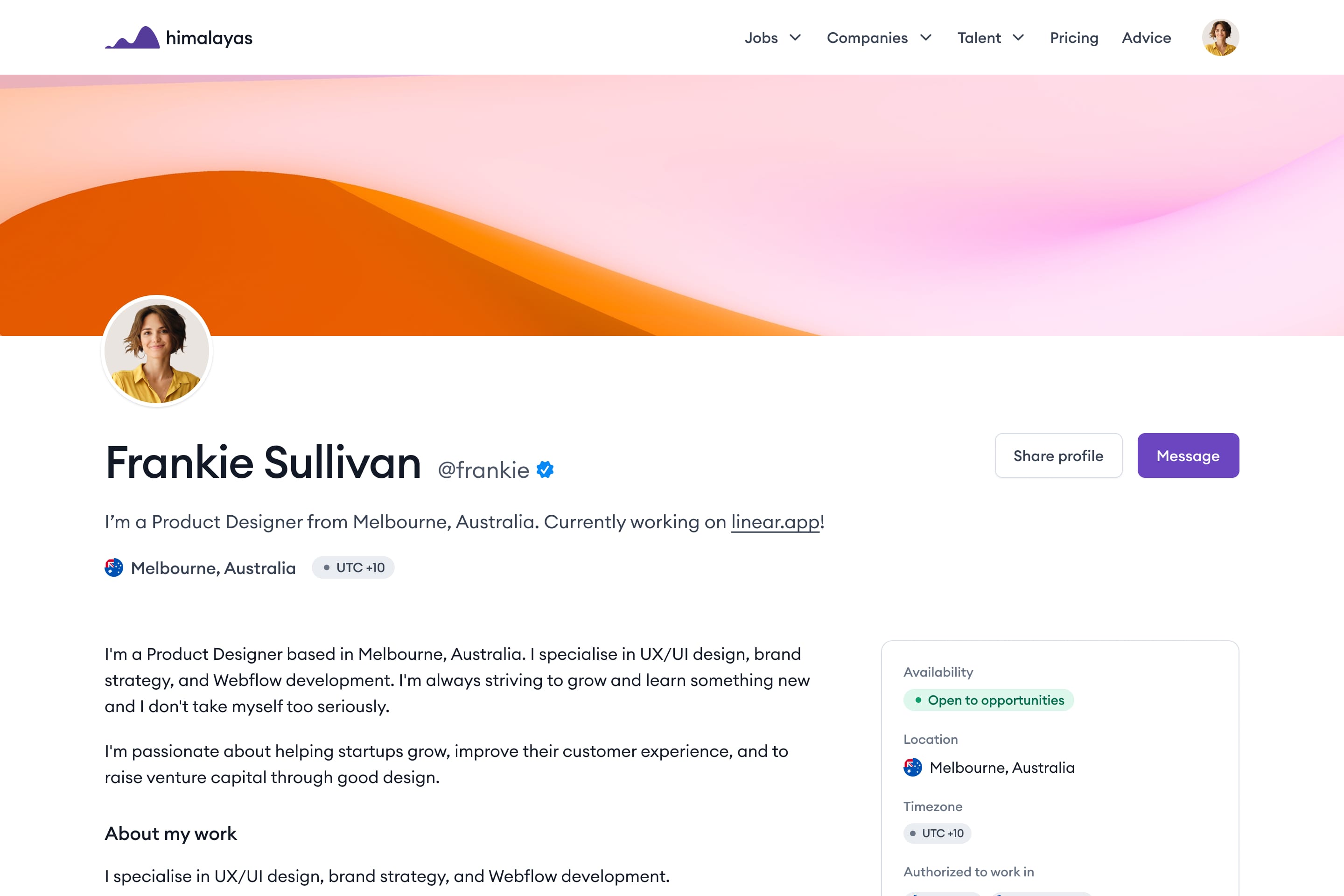