Complete Pre-Engineered Metal Building Ironworker Career Guide
Pre-Engineered Metal Building (PEMB) Ironworkers are the specialized artisans who bring steel structures to life, transforming raw materials into durable, cost-effective buildings. They meticulously assemble the framework for everything from warehouses to retail centers, ensuring precision and structural integrity. This hands-on career offers a clear path to mastering essential construction skills and contributing to tangible, lasting infrastructure.
Key Facts & Statistics
Median Salary
$60,980 USD
(U.S. national median for structural iron and steelworkers, May 2023, BLS)
Range: $38k - $100k+ USD (varies by experience, location, and union membership)
Growth Outlook
9%
as fast as average (for all structural iron and steelworkers, 2022-2032, BLS)
Annual Openings
≈17,000
openings annually (for all structural iron and steelworkers, BLS)
Top Industries
Typical Education
High school diploma or equivalent, often followed by an apprenticeship or on-the-job training
What is a Pre-Engineered Metal Building Ironworker?
A Pre-Engineered Metal Building (PEMB) Ironworker specializes in the assembly and erection of standardized steel structures manufactured off-site. Unlike general structural ironworkers who may work on diverse, custom-designed steel frameworks for skyscrapers or bridges, PEMB ironworkers focus specifically on the efficient and precise construction of pre-fabricated steel components for buildings like warehouses, commercial facilities, and industrial complexes.
This role is critical for delivering cost-effective and rapidly deployable building solutions. PEMB ironworkers interpret specific erection drawings, which differ from traditional architectural blueprints, to piece together the pre-manufactured steel frame, roof, and wall systems. Their expertise ensures the structural integrity and timely completion of these specialized metal buildings, making them a vital part of the light commercial and industrial construction sector.
What does a Pre-Engineered Metal Building Ironworker do?
Key Responsibilities
- Read and interpret blueprints, schematics, and erection drawings to understand the layout and specifications of pre-engineered metal buildings.
- Connect steel beams, columns, and other structural components using various methods, including bolting, welding, and riveting, ensuring precise alignment.
- Operate heavy equipment such as forklifts, cranes, and aerial lifts to move and position large steel members safely and efficiently.
- Install metal wall panels, roof panels, insulation, trim, and accessories, ensuring weather-tight seals and aesthetic finishes.
- Conduct safety inspections of equipment and the work area, identifying and mitigating potential hazards to maintain a secure construction site.
- Perform precise measurements and calculations to ensure structural integrity and adherence to design specifications.
- Collaborate with other tradespeople, supervisors, and project managers to coordinate work, resolve issues, and maintain project schedules and quality standards.
Work Environment
Pre-engineered metal building ironworkers primarily work outdoors on active construction sites, exposed to varying weather conditions. The work involves significant physical exertion, including climbing, lifting heavy materials, and working at heights. Team collaboration is crucial; they work closely with other ironworkers, crane operators, and various construction trades to ensure project progress. The pace is often fast-paced and deadline-driven, requiring adaptability and efficiency. Travel to different job sites is common, and work schedules can vary, sometimes including early mornings or extended hours to meet project timelines.
Tools & Technologies
Pre-engineered metal building ironworkers utilize a range of specialized tools and equipment daily. They regularly operate heavy machinery like forklifts, rough terrain telehandlers, and mobile cranes for material handling and positioning. For assembly, they use impact wrenches, torque wrenches, and various hand tools such as spud wrenches, tape measures, and levels. Cutting tools like plasma cutters and oxy-acetylene torches are essential for modifications. Safety equipment, including harnesses, lanyards, and hard hats, is paramount. They also work with welding machines (MIG, Stick) for specific connections and use laser levels and transits for precise alignment.
Pre-Engineered Metal Building Ironworker Skills & Qualifications
A Pre-Engineered Metal Building (PEMB) Ironworker specializes in the assembly and erection of structural steel components for pre-fabricated metal buildings. This role requires a unique blend of structural knowledge, precision, and adherence to safety protocols. Unlike general ironworkers who might work on diverse structures, PEMB ironworkers focus specifically on standardized, bolted systems, demanding a detailed understanding of manufacturer specifications and erection drawings.
Requirements for PEMB Ironworkers vary significantly based on experience and company size. Entry-level positions often accept vocational training or on-the-job apprenticeship, while senior roles demand extensive practical experience and often specialized certifications. Larger construction firms might prioritize formal apprenticeship completions, whereas smaller, specialized PEMB contractors may value proven field experience and a strong safety record above all else. Geographic region also influences requirements; some areas have stronger union presences or specific licensing mandates for structural steel work.
Practical experience is paramount in this field. While formal education provides a foundation, hands-on experience with PEMB systems, including understanding bolt-up procedures, bracing, and sheeting, is critical. Certifications, particularly in welding (if required for repairs or modifications) and rigging, add significant value and can accelerate career progression. The skill landscape is evolving with greater emphasis on digital blueprint reading and advanced safety equipment, though the core mechanical aptitude remains central. Prioritizing practical application and continuous safety training is essential for long-term success in this specialized ironworking discipline.
Education Requirements
Technical Skills
- Blueprint and Erection Drawing Interpretation: Ability to accurately read and understand detailed architectural, structural, and manufacturer-specific PEMB erection drawings.
- Structural Steel Erection Techniques: Proficiency in safely and efficiently erecting primary and secondary steel framing for PEMBs, including columns, beams, girts, and purlins.
- Bolting and Fastening: Expertise in proper torqueing, sequencing, and inspection of high-strength bolts and other fasteners specific to PEMB connections.
- Rigging and Signaling: Competence in selecting appropriate rigging gear, inspecting equipment, and effectively signaling crane operators for safe and precise lifts.
- Welding (SMAW, FCAW): Basic to advanced welding skills for minor structural modifications, repairs, or re-enforcements, often required for PEMB integration.
- Use of Hand and Power Tools: Proficient operation of impact wrenches, grinders, levels, tape measures, and other tools essential for steel erection.
- Fall Protection Systems: Comprehensive understanding and correct use of personal fall arrest systems, safety nets, and guardrail systems.
- Forklift and Aerial Lift Operation: Certification and practical experience operating telehandlers, forklifts, and various aerial work platforms (e.g., scissor lifts, boom lifts) for material handling and access.
- Layout and Measurement: Accurate use of measuring tools and techniques for establishing column lines, elevations, and verifying dimensions on site.
- Basic Metallurgy and Steel Properties: Foundational knowledge of different steel types, their properties, and how they behave under stress and weather conditions.
Soft Skills
- Attention to Detail: Critical for accurately interpreting erection drawings, ensuring proper alignment, and correct bolt-up sequences to prevent structural integrity issues.
- Problem-Solving: Necessary for addressing unexpected challenges on-site, such as misaligned components, site obstructions, or adverse weather conditions, to maintain project timelines.
- Teamwork and Collaboration: Essential for coordinating lifts, securing components, and working safely alongside crane operators, welders, and other crew members.
- Adaptability: Important for adjusting to changing site conditions, weather, and project scopes, ensuring efficient and safe work progression.
- Safety Consciousness: Paramount for adhering to strict safety protocols, recognizing hazards, and using personal protective equipment to prevent accidents in a high-risk environment.
- Physical Stamina and Endurance: Required for sustained physical labor, lifting, climbing, and working outdoors in various weather conditions for extended periods.
How to Become a Pre-Engineered Metal Building Ironworker
Entering the Pre-Engineered Metal Building (PEMB) Ironworker field offers several pathways, from direct entry as a laborer to formal apprenticeship programs. While a college degree is unnecessary, hands-on experience and a strong work ethic are crucial. The timeline to become proficient varies; a complete beginner might spend 6 months to a year as a helper before advancing, while a formal apprenticeship could take 3-4 years to achieve journeyman status.
Hiring for PEMB Ironworkers often prioritizes practical skills and reliability over formal certifications initially. Many companies, especially smaller and mid-sized contractors, prefer to train new hires on the job, starting them in entry-level helper roles. Larger union contractors typically require participation in structured apprenticeship programs. Geographic location heavily influences opportunities; demand is highest in areas with significant commercial and industrial construction, such as growing metropolitan centers or regions with new manufacturing facilities.
Understanding the distinction between a general ironworker and a PEMB-specific ironworker is important. While general ironworkers handle various structural steel, rebar, and ornamental iron, a PEMB ironworker specializes in erecting the unique components of pre-engineered metal buildings, including primary and secondary framing, wall panels, and roof systems. This specialization requires a specific skill set and knowledge of PEMB erection sequences and safety protocols. Networking within local construction communities and connecting with foremen or superintendents can open doors to opportunities not always advertised publicly.
Step 1
Step 2
Step 3
Step 4
Step 5
Step 6
Education & Training Needed to Become a Pre-Engineered Metal Building Ironworker
Becoming a Pre-Engineered Metal Building (PEMB) Ironworker involves a blend of practical skills and theoretical knowledge, with educational pathways varying significantly. Traditional 4-year university degrees are not typically required for this hands-on trade. Instead, most successful PEMB ironworkers enter the field through apprenticeships, vocational training programs, or direct entry with on-the-job training.
Apprenticeships, often union-sponsored, provide the most comprehensive training, combining paid work experience with classroom instruction. These programs usually last 3-4 years, costing apprentices minimal or no tuition, and often lead to higher wages and better benefits. Vocational schools and community colleges offer shorter, focused certificate or associate degree programs in welding, construction, or structural ironworking, usually taking 6 months to 2 years. These programs can range from $5,000 to $20,000, providing foundational skills but often requiring further on-the-job learning. Self-study and direct entry involve learning through experience, but without formal credentials, career progression may be slower.
Employers highly value practical experience and certifications in welding (e.g., AWS certifications) and safety (e.g., OSHA 10/30). While formal degrees are less common, a strong understanding of blueprints, structural mechanics, and safety protocols is crucial. Continuing education through specialized workshops on new building techniques or advanced welding processes is vital for career advancement. The industry recognizes hands-on competence and safety adherence above all else, making apprenticeships and industry certifications the most cost-effective and career-accelerating educational investments.
Pre-Engineered Metal Building Ironworker Salary & Outlook
Compensation for a Pre-Engineered Metal Building (PEMB) Ironworker varies significantly based on several factors. Geographic location plays a crucial role, with higher wages typically found in major metropolitan areas or regions with robust construction activity, reflecting local cost of living and specific project demand. Conversely, rural areas may offer lower compensation.
Experience and specialized skills also drive earning potential. Ironworkers with extensive experience in erecting complex PEMB structures, or those certified in specific welding techniques or rigging, command higher salaries. Total compensation packages often extend beyond base hourly wages to include overtime pay, per diem allowances for travel, and comprehensive benefits. These benefits typically encompass health insurance, retirement plans like 401(k)s, and sometimes union-negotiated pension contributions.
Industry-specific compensation trends are influenced by the overall health of the construction sector and the demand for commercial and industrial buildings. Economic cycles and infrastructure spending directly impact project availability and, consequently, salary growth. Ironworkers with a strong safety record and proven efficiency in project completion gain significant leverage in salary negotiations. Remote work, as traditionally understood, does not apply to this hands-on role; however, traveling to various job sites is common, and per diem rates often compensate for living expenses away from home, effectively increasing take-home pay. While the provided figures are USD-centric, international markets will have their own distinct compensation structures influenced by local labor laws, economic conditions, and construction standards.
Salary by Experience Level
Level | US Median | US Average |
---|---|---|
Apprentice Ironworker | $38k USD | $40k USD |
Journeyman Ironworker | $58k USD | $60k USD |
Senior Ironworker | $72k USD | $75k USD |
Lead Ironworker | $82k USD | $85k USD |
Foreman Ironworker | $92k USD | $95k USD |
Superintendent (Ironwork) | $110k USD | $115k USD |
Market Commentary
The job market for Pre-Engineered Metal Building Ironworkers shows steady demand, largely tied to the commercial and industrial construction sectors. Growth is projected at approximately 9% over the next decade, which is on par with the average for all occupations, driven by ongoing needs for new warehouses, manufacturing facilities, and retail spaces. This growth is particularly strong in developing areas and regions experiencing economic expansion.
Emerging opportunities for PEMB Ironworkers include specialized roles in complex architectural designs and integration with smart building technologies. The increasing sophistication of PEMB systems requires ironworkers with enhanced skills in precise assembly and adherence to stringent safety protocols. While automation and AI are transforming many industries, the hands-on nature of ironwork, particularly in the erection phase, makes it less susceptible to full automation in the near future. However, technological advancements in tools and planning software will require continuous skill development.
Supply and demand dynamics vary regionally; some areas face shortages of skilled ironworkers, leading to competitive wages and increased opportunities, especially for those with certifications. This profession is somewhat cyclical, influenced by economic downturns that can slow construction, but the fundamental need for infrastructure and commercial buildings provides a degree of recession resistance. Geographic hotspots include major logistical hubs and areas with growing industrial parks. Future-proofing this career involves continuous training in new erection techniques, safety standards, and specialized welding or rigging certifications.
Pre-Engineered Metal Building Ironworker Career Path
Career progression for a Pre-Engineered Metal Building (PEMB) Ironworker involves a structured path from foundational skill acquisition to advanced leadership. New entrants typically begin as apprentices, learning safety protocols and basic erection techniques. Advancement often hinges on mastering specialized skills, such as reading complex blueprints, operating heavy machinery, and leading rigging operations, while consistently demonstrating a strong commitment to safety and quality.
Individual contributor (IC) tracks focus on honing technical expertise and becoming highly efficient in complex installations. Management tracks, conversely, emphasize leadership, project coordination, and crew supervision. Performance, continuous skill development, and industry certifications significantly accelerate progression. Company size, from smaller local contractors to large national firms, also shapes career paths; larger companies may offer more defined leadership roles and specialized training opportunities.
Lateral moves might involve specializing in specific types of PEMB structures, becoming a safety officer, or transitioning into welding or rigging roles within the broader construction industry. Networking with other trades, mentors, and foremen proves invaluable for understanding advancement opportunities and securing leadership roles. Field-specific certifications in rigging, welding, or crane signaling mark key milestones. Some ironworkers transition into roles like project management, construction supervision, or even sales for PEMB manufacturers, leveraging their deep field experience.
Apprentice Ironworker
0-4 yearsKey Focus Areas
Journeyman Ironworker
4-8 yearsKey Focus Areas
Senior Ironworker
8-12 yearsKey Focus Areas
Lead Ironworker
10-15 yearsKey Focus Areas
Foreman Ironworker
15-20 yearsKey Focus Areas
Superintendent (Ironwork)
20+ yearsKey Focus Areas
Apprentice Ironworker
0-4 yearsWorks under direct supervision, assisting Journeyman and Senior Ironworkers with basic tasks. Handles material staging, prepares connections, and performs simple bolt-up and paneling. Responsibility is limited to following instructions and maintaining a safe work environment.
Key Focus Areas
Develop foundational knowledge of PEMB components, safety procedures, and tool usage. Learn basic rigging, bolt-up, and panel installation techniques under direct supervision. Focus on physical conditioning and understanding site-specific safety plans. Cultivate a strong work ethic and attention to detail.
Journeyman Ironworker
4-8 yearsIndependently performs complex erection tasks, including main frame assembly, secondary framing, and roof/wall panel installation. Makes routine decisions regarding sequence of work and material handling. Works with minimal supervision, often guiding apprentices on specific tasks.
Key Focus Areas
Master advanced rigging, structural assembly, and sheeting techniques. Independently interpret blueprints and erection drawings. Develop proficiency in operating various lifts and equipment safely. Begin mentoring apprentices and troubleshooting minor field issues.
Senior Ironworker
8-12 yearsLeads small sections of a project or specialized tasks, such as complex eave conditions or large-scale sheeting operations. Provides technical guidance to Journeyman and Apprentice Ironworkers. Identifies and resolves on-site issues, ensuring adherence to plans and safety standards.
Key Focus Areas
Refine problem-solving skills for complex structural challenges and field modifications. Enhance leadership capabilities by guiding small teams. Specialize in advanced rigging, heavy lifting, or specific PEMB systems. Focus on optimizing erection efficiency and quality control.
Lead Ironworker
10-15 yearsDirects a small crew of 2-4 ironworkers on a specific section of a PEMB project. Responsible for task assignment, quality of work, and ensuring safety protocols are followed by the crew. Reports progress and issues directly to the Foreman, making on-the-fly adjustments to maintain flow.
Key Focus Areas
Develop strong communication and organizational skills for coordinating small crews. Learn to delegate tasks effectively and monitor progress. Focus on project scheduling, resource allocation for specific tasks, and maintaining high productivity levels. Start understanding project budgets and timelines.
Foreman Ironworker
15-20 yearsManages and supervises multiple crews or a significant portion of a large PEMB project. Oversees daily operations, ensures adherence to project timelines and budgets, and enforces all safety regulations. Acts as the primary point of contact for the site, coordinating with other trades and project management.
Key Focus Areas
Master project management principles, including scheduling, budgeting, and safety management. Develop strong leadership and conflict resolution skills. Understand client relations and subcontractor coordination. Focus on strategic planning for complex PEMB erections and continuous process improvement.
Superintendent (Ironwork)
20+ yearsOversees all ironwork operations across multiple PEMB projects or a very large, complex single project. Responsible for overall project success, resource allocation, and ensuring compliance with all company policies and industry standards. Manages Foremen, liaises with senior management, and drives operational efficiency and profitability.
Key Focus Areas
Cultivate executive leadership skills, including strategic planning, risk management, and large-scale project oversight. Develop expertise in contract negotiation, client satisfaction, and business development. Focus on mentoring Foremen and fostering a strong safety culture across multiple projects. Understand broader company objectives.
Job Application Toolkit
Ace your application with our purpose-built resources:
Pre-Engineered Metal Building Ironworker Resume Examples
Proven layouts and keywords hiring managers scan for.
View examplesPre-Engineered Metal Building Ironworker Cover Letter Examples
Personalizable templates that showcase your impact.
View examplesTop Pre-Engineered Metal Building Ironworker Interview Questions
Practice with the questions asked most often.
View examplesPre-Engineered Metal Building Ironworker Job Description Template
Ready-to-use JD for recruiters and hiring teams.
View examplesGlobal Pre-Engineered Metal Building Ironworker Opportunities
Pre-Engineered Metal Building (PEMB) Ironworkers erect structural steel frameworks for buildings globally. Demand for these specialized skills remains consistent across industrial and commercial construction sectors worldwide. International projects often require skilled teams, creating opportunities in developing and developed economies. Cultural differences impact safety protocols and project management, while standardized building codes facilitate some cross-border work. Professionals seek international roles for higher wages or diverse project experience. No specific international certifications exist; local licensing or proven experience matters most.
Global Salaries
Salaries for PEMB Ironworkers vary significantly by region, reflecting local economies and demand. In North America, particularly the United States, an experienced PEMB Ironworker earns between $60,000 and $90,000 USD annually. Canadian salaries are comparable, often ranging from $55,000 to $85,000 CAD (approx. $40,000-$62,000 USD). These figures typically include benefits such as health insurance, retirement plans, and paid time off, which are often robust due to unionization.
European salaries show a wider range. In Western Europe (e.g., Germany, Netherlands), an Ironworker might earn €40,000-€60,000 (approx. $43,000-$65,000 USD). Eastern European countries offer lower nominal wages, perhaps €18,000-€30,000 (approx. $19,000-$32,000 USD), but purchasing power parity can make these salaries more competitive locally. Benefits packages in Europe often include comprehensive public healthcare and generous vacation time, which impacts overall compensation.
Asia-Pacific markets, like Australia, offer high wages, with Ironworkers earning AUD 80,000-120,000 (approx. $53,000-$80,000 USD), though the cost of living is also high. The Middle East, particularly the UAE and Saudi Arabia, presents tax-free income opportunities for skilled trades, with salaries ranging from $35,000-$65,000 USD, often including housing allowances. Latin American wages are generally lower, perhaps $15,000-$30,000 USD, but cost of living is also considerably less. Tax implications vary greatly; for instance, Scandinavian countries have higher income taxes but offer extensive social benefits. Experience and specialized skills, like rigging or welding certifications, enhance earning potential globally.
Remote Work
Pre-Engineered Metal Building Ironworkers perform hands-on, physically demanding work at construction sites. This role requires direct physical presence for steel erection, bolting, and welding. Therefore, international remote work opportunities are non-existent for the core responsibilities of a PEMB Ironworker.
However, some related, supervisory, or planning roles within the PEMB industry might offer limited remote or hybrid options. For example, a project manager or structural engineer specializing in PEMB could potentially work remotely for design or coordination tasks. An Ironworker, by definition, works on-site. Digital nomad opportunities do not apply to this trade. Companies hire Ironworkers for specific on-site projects, not for remote contributions. Equipment for an Ironworker is specialized and site-dependent, making remote setup impossible.
Visa & Immigration
For Pre-Engineered Metal Building Ironworkers, common immigration pathways involve skilled worker visas. Countries like Canada, Australia, and the UK often have specific visa categories for tradespeople if there is a demonstrated labor shortage. For instance, Canada's Express Entry system or Australia's Skilled Migration Program include trades on their occupation lists. Requirements typically include proof of trade qualifications, often assessed by an accredited body, and several years of professional experience.
The United States offers H-2B visas for temporary non-agricultural workers, which some construction companies utilize for specific projects. European countries, such as Germany, have skilled worker visas requiring recognized qualifications and a job offer. Credential recognition for trade skills varies; some countries require formal assessments or apprenticeships to be equivalent to their local standards. Language requirements, like English or German proficiency, are often mandatory for integration and safety.
Visa timelines range from a few months to over a year, depending on the country and visa type. Employers often sponsor these visas, particularly for large-scale international projects. Pathways to permanent residency exist in countries like Canada and Australia after a period of skilled work. Family visas are usually available for spouses and dependents of primary visa holders, allowing them to accompany the Ironworker. This profession does not typically have fast-track immigration programs.
2025 Market Reality for Pre-Engineered Metal Building Ironworkers
Understanding the current market realities for Pre-Engineered Metal Building (PEMB) Ironworkers is critical for career success. This specialized trade has seen shifts in recent years due to evolving construction demands and technological advancements. Post-pandemic, the demand for efficient, rapid construction methods has grown, favoring PEMB.
Broader economic factors, such as interest rates and industrial expansion, directly influence project pipelines for PEMB structures. Market realities for ironworkers vary significantly by experience level, with senior roles commanding more stability and higher pay. Geographic region and the size of contracting firms also play a substantial role in job availability. This analysis provides an honest assessment of current conditions, helping you navigate this specific trade with realistic expectations.
Current Challenges
Pre-engineered metal building (PEMB) ironworkers face fluctuating project pipelines, tied directly to economic cycles and commercial construction demand. Competition for stable, long-term employment can be high during downturns, especially for those lacking diverse welding or rigging certifications. The specialized nature of PEMB work means fewer immediate transferrable skills to other ironworking sectors without additional training.
Newer AI-driven design software in PEMB can optimize material use and fabrication, indirectly raising productivity expectations on site. This pushes ironworkers to achieve faster, more precise installations. Job seekers should also prepare for variable work availability and the need to travel for projects, as local demand can be inconsistent.
Growth Opportunities
Despite market challenges, strong demand persists for Pre-Engineered Metal Building (PEMB) Ironworkers in specific growth areas. Logistics and e-commerce continue to drive the construction of large warehouses and distribution centers, a core market for PEMB. Data centers and light industrial facilities also present consistent opportunities.
Professionals can gain a competitive advantage by pursuing advanced certifications in specialized welding techniques (e.g., structural, flux-cored arc welding) and advanced rigging, which are increasingly sought after. Underserved markets in rapidly developing suburban and exurban areas, particularly around new transportation corridors, often have higher demand. Demonstrating proficiency with digital blueprint reading and understanding of building information modeling (BIM) software can also set candidates apart.
The current market correction, while affecting some construction sectors, has highlighted the cost-effectiveness and speed of PEMB, making it an attractive option for developers. This creates a stable niche for skilled ironworkers. Focusing on companies specializing in large-scale commercial or industrial projects can offer more consistent work. Investing in ongoing safety training and maintaining a clean work record also enhances employability.
Current Market Trends
The market for Pre-Engineered Metal Building (PEMB) Ironworkers shows steady demand in 2025, driven by continued growth in commercial, industrial, and agricultural sectors. Warehouses, distribution centers, and light manufacturing facilities frequently utilize PEMB structures. Hiring patterns reflect a need for skilled individuals capable of precise structural assembly, often under tight deadlines.
Economic conditions, while showing some inflationary pressures, have not significantly curtailed new construction starts requiring PEMB. Interest rates affect financing for larger projects, but the cost-effectiveness and speed of PEMB construction maintain its appeal. Layoffs remain minimal within this specialized niche, reflecting a consistent need for hands-on assembly.
Technology trends impact the field through advanced fabrication techniques and more complex designs, requiring ironworkers to interpret detailed blueprints and utilize modern fastening systems. While direct AI integration on the job site for ironworkers is limited, AI-optimized design software helps streamline material delivery and assembly sequences. Employers now prioritize certifications in advanced welding, rigging, and safety, alongside practical experience.
Salary trends for experienced PEMB ironworkers remain stable, with a slight upward trajectory for highly skilled individuals. Market saturation is low for certified, experienced professionals, though entry-level positions might see more applicants. Geographic variations exist; robust commercial development in the Sun Belt states and major logistical hubs shows stronger demand. Remote work is not applicable to this hands-on role. Seasonal hiring often aligns with better weather for outdoor construction, typically peaking from spring through fall.
Emerging Specializations
The construction industry, particularly in pre-engineered metal building (PEMB) erection, experiences continuous evolution driven by technological advancements and shifting project demands. Understanding these trends helps ironworkers identify and pursue new specialization opportunities. Early positioning in these emerging areas provides a significant advantage for career advancement in 2025 and beyond.
Specializing in cutting-edge techniques or technologies often leads to premium compensation and enhanced career growth. These emerging roles require unique skill sets that are currently in high demand but not yet widely available. While established specializations remain vital, a strategic balance involves exploring future-oriented paths that align with industry innovation.
Many emerging areas, initially niche, become mainstream within three to five years, creating a substantial volume of job opportunities. Investing in these skills now positions professionals at the forefront of the industry. This approach carries some initial risk due to the novelty of the fields, but the potential rewards in terms of career longevity, leadership opportunities, and earning potential are substantial for those willing to adapt and learn.
Automated PEMB Erection Specialist
As construction sites increasingly adopt advanced robotic systems for repetitive or hazardous tasks, a specialized ironworker will oversee and manage these automated processes. This includes programming robotic welders, guiding automated material handling equipment, and ensuring seamless integration of robotic assistance into the PEMB erection sequence. This role moves the ironworker from purely manual labor to a supervisory and technical oversight position.
Sustainable PEMB Installation Technician
The demand for sustainable construction practices is growing, influencing PEMB design and material use. This specialization focuses on the installation of metal buildings designed for high energy efficiency, integration of renewable energy components (like solar panel mounting systems on metal roofs), and the use of eco-friendly fastening or sealing methods. It requires understanding of green building standards and specialized installation techniques for sustainable materials.
Digital Construction & BIM Ironworker
Building Information Modeling (BIM) is transforming construction planning and execution. A BIM-integrated ironworker uses 3D models and digital tools on-site to visualize complex assemblies, identify potential clashes before physical erection, and verify structural accuracy in real-time. This specialization enhances precision, reduces rework, and improves overall project efficiency by linking digital design directly to field operations.
Advanced Smart Rigging & Modular Assembly Specialist
With increasing complexity and tighter schedules, advanced rigging and lifting techniques are becoming critical. This specialization involves expertise in using smart lifting equipment with integrated sensors, drone-assisted load positioning, and developing complex lift plans for oversized or uniquely shaped PEMB components. It focuses on maximizing safety and efficiency for challenging erection scenarios, often involving modular construction elements.
Pros & Cons of Being a Pre-Engineered Metal Building Ironworker
Understanding both the advantages and challenges of any career is crucial before making a commitment. A career as a Pre-Engineered Metal Building Ironworker offers unique experiences, but these can vary significantly based on the company, specific projects, and individual skills. The pros and cons may also shift as an individual progresses from an apprentice to a seasoned journeyman. What one person views as a benefit, such as outdoor work, another might see as a challenge. This assessment provides an honest, balanced view to help set realistic expectations for anyone considering this demanding yet rewarding trade.
Pros
- Pre-engineered metal building ironworkers typically earn competitive wages, especially with experience and specialized skills, reflecting the demand and physical nature of the work.
- There is a strong sense of accomplishment from seeing a large structure quickly rise from the ground; ironworkers contribute directly to visible, tangible projects.
- The demand for skilled ironworkers remains consistent as commercial, industrial, and agricultural sectors continue to build and expand, offering good job security.
- This role involves dynamic, hands-on work with heavy machinery and structural components, providing an active alternative to desk-bound jobs.
- Many roles offer opportunities for travel to different project sites, which can appeal to individuals who enjoy variety in their work location and experiencing new places.
- The trade offers clear pathways for skill development and career advancement, from apprentice to journeyman, foreman, or even supervisor, with corresponding increases in pay and responsibility.
- Working as part of a crew fosters strong camaraderie and teamwork, as success on a project relies heavily on effective collaboration and mutual support among team members.
Cons
- Pre-engineered metal building ironworkers often work at significant heights, which carries inherent risks of falls and requires constant vigilance and adherence to strict safety protocols.
- The work is physically demanding, involving heavy lifting, climbing, and working in various weather conditions, leading to potential strain, fatigue, and long-term joint or back issues.
- Work schedules can be irregular, with projects often requiring extended hours, early starts, or weekend work to meet tight construction deadlines, impacting personal life.
- Exposure to outdoor elements means working in extreme heat, cold, rain, or wind, which can make the job uncomfortable and physically taxing.
- Job security can fluctuate with the construction market and project availability; periods between projects might mean temporary unemployment or needing to travel for work.
- The work involves repetitive tasks like bolting and sheeting, which can lead to monotony for some individuals and increase the risk of repetitive strain injuries.
- Learning the specific techniques for assembling pre-engineered metal buildings requires specialized training and on-the-job experience, which can be a steep initial learning curve for newcomers to the trade, and specific certifications may be required to operate equipment.
Frequently Asked Questions
Pre-Engineered Metal Building (PEMB) Ironworkers face distinct challenges around specialized assembly techniques and rigorous safety protocols. This section addresses common questions about entering this specific trade, from required training and physical demands to career progression and work environment on PEMB construction sites.
What is the typical path to becoming a Pre-Engineered Metal Building Ironworker?
Becoming a Pre-Engineered Metal Building Ironworker typically involves completing an apprenticeship, which lasts 3-4 years. During this time, you gain hands-on experience and classroom instruction covering blueprint reading, welding, rigging, and specific PEMB erection techniques. Some individuals may start as helpers and learn on the job, but formal apprenticeship provides a structured path to journeyman status and certifications.
What are the core physical and mental demands of this job?
The work involves significant physical demands including lifting heavy materials, climbing, working at heights, and standing for long periods. You must have good physical stamina, balance, and strength. The job also requires mental focus for precision work and adherence to strict safety procedures, often in varying weather conditions.
What are the typical salary expectations and benefits for a Pre-Engineered Metal Building Ironworker?
Entry-level wages for PEMB Ironworkers vary by region and union affiliation, but apprentices typically start at a percentage of the journeyman rate. Experienced journeymen can earn competitive hourly wages, often with opportunities for overtime. Benefits packages, including health insurance and retirement plans, are common, especially in unionized positions.
How stable is job security for Pre-Engineered Metal Building Ironworkers?
Job security in this trade is generally stable, driven by the ongoing demand for commercial and industrial buildings. The specialized nature of PEMB construction means that skilled ironworkers are consistently needed. Economic downturns can affect construction, but infrastructure and commercial development projects continue to create opportunities.
What are the long-term career growth opportunities for a Pre-Engineered Metal Building Ironworker?
Career growth can involve advancing to foreman, superintendent, or project management roles. You can also specialize in areas like welding inspection, rigging, or become an instructor. Continuing education and acquiring additional certifications in areas like advanced welding or safety management enhance these opportunities.
What is the typical work environment like for this role?
The work environment is primarily outdoors on construction sites, exposed to various weather conditions. You will often work at heights, requiring strict adherence to fall protection and other safety protocols. The job requires teamwork and clear communication with other trades, often in noisy environments.
How different is working on Pre-Engineered Metal Buildings compared to general structural ironwork?
While some ironworker skills are transferable, PEMB construction involves specific erection sequences, specialized fasteners, and detailed plans unique to pre-engineered systems. Experience with these specific methodologies is crucial. General ironworking experience provides a strong foundation, but dedicated training in PEMB construction is highly beneficial.
What is the typical work-life balance for a Pre-Engineered Metal Building Ironworker?
The work-life balance can vary significantly, often depending on project deadlines and seasonal demand. During peak construction periods, long hours and weekend work are common. However, off-seasons or project completion can lead to more predictable schedules. Many ironworkers adjust to these fluctuating demands over their careers.
Related Careers
Explore similar roles that might align with your interests and skills:
Ironworker
A growing field with similar skill requirements and career progression opportunities.
Explore career guideConstruction Ironworker
A growing field with similar skill requirements and career progression opportunities.
Explore career guideConstruction Ironworker Helper
A growing field with similar skill requirements and career progression opportunities.
Explore career guidePrecast Concrete Ironworker
A growing field with similar skill requirements and career progression opportunities.
Explore career guideStructural Steel Erector
A growing field with similar skill requirements and career progression opportunities.
Explore career guideAssess your Pre-Engineered Metal Building Ironworker readiness
Understanding where you stand today is the first step toward your career goals. Our Career Coach helps identify skill gaps and create personalized plans.
Skills Gap Analysis
Get a detailed assessment of your current skills versus Pre-Engineered Metal Building Ironworker requirements. Our AI Career Coach identifies specific areas for improvement with personalized recommendations.
See your skills gapCareer Readiness Assessment
Evaluate your overall readiness for Pre-Engineered Metal Building Ironworker roles with our AI Career Coach. Receive personalized recommendations for education, projects, and experience to boost your competitiveness.
Assess your readinessSimple pricing, powerful features
Upgrade to Himalayas Plus and turbocharge your job search.
Himalayas
Himalayas Plus
Himalayas Max
Find your dream job
Sign up now and join over 100,000 remote workers who receive personalized job alerts, curated job matches, and more for free!
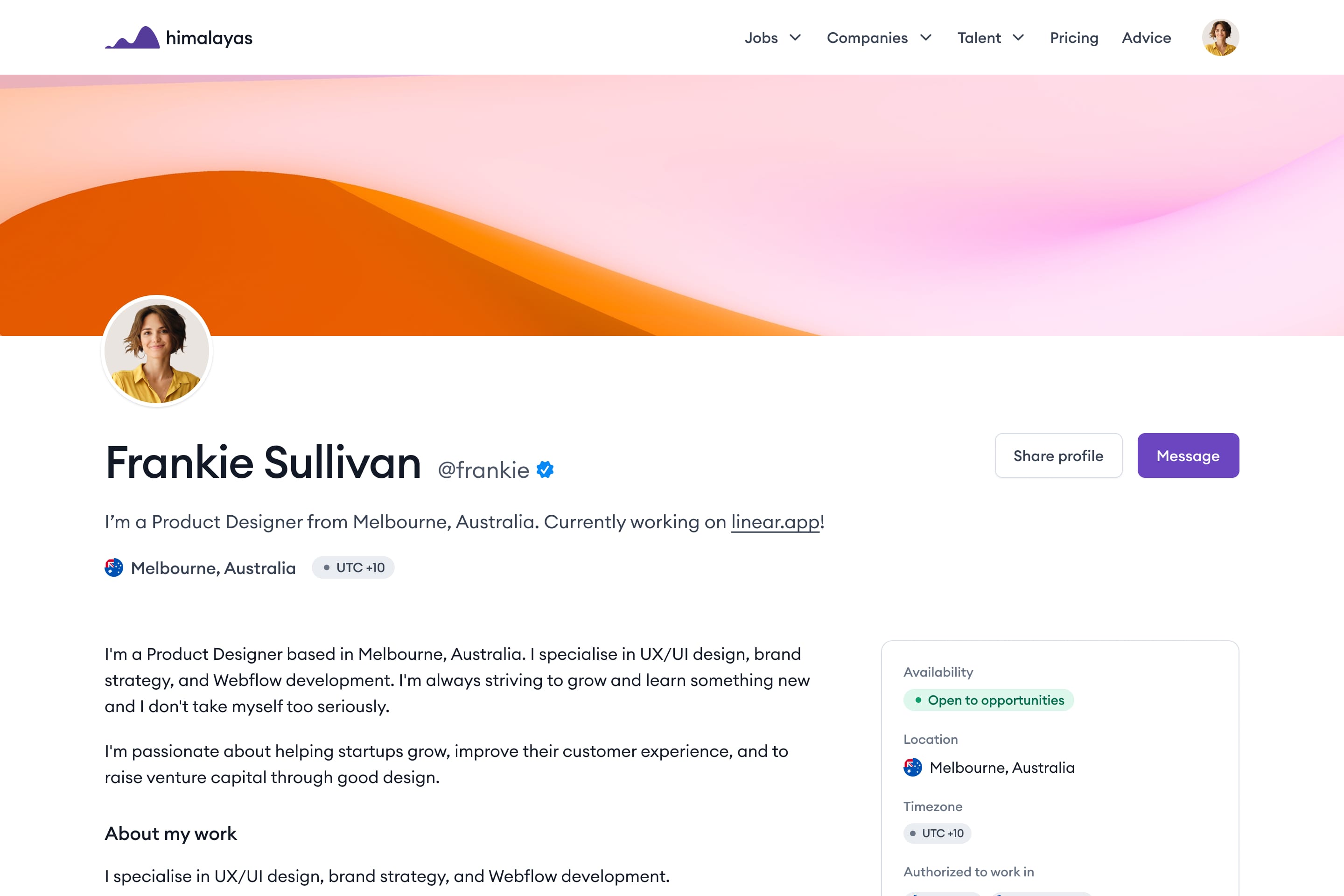