Complete Plant Operator Career Guide
Plant operators are the unseen backbone of essential industries, ensuring the continuous, safe, and efficient operation of complex machinery and systems that produce everything from electricity to chemicals. You monitor and control equipment in power plants, manufacturing facilities, and water treatment centers, playing a critical role in maintaining infrastructure and daily life. This career offers a stable path for those who thrive on precision, problem-solving, and hands-on technical work, often requiring specialized training and offering competitive wages.
Key Facts & Statistics
Median Salary
$71,780 USD
(U.S. Bureau of Labor Statistics, May 2023)
Range: $45k - $100k+ USD
Growth Outlook
Annual Openings
Top Industries
Typical Education
High school diploma or equivalent, often with significant on-the-job training or a postsecondary certificate/associate's degree in a related field like industrial technology or power plant operations.
What is a Plant Operator?
A Plant Operator is a skilled professional responsible for the safe, efficient, and continuous operation of industrial facilities that produce energy, process materials, or treat substances. They monitor and control complex machinery, systems, and equipment from a central control room or by patrolling the facility. Their primary goal is to ensure that all plant processes run within specified parameters, optimizing output while adhering to strict safety, environmental, and quality standards.
This role differs significantly from a Maintenance Technician, who primarily focuses on repairing and servicing equipment, or a Process Engineer, who designs and optimizes the processes themselves. The Plant Operator is the frontline individual who executes the operational plans, reacting to real-time conditions and making immediate adjustments to keep the plant running smoothly and safely. They are critical to preventing costly shutdowns, ensuring regulatory compliance, and maintaining consistent production.
What does a Plant Operator do?
Key Responsibilities
- Monitor and control plant systems, machinery, and equipment using control panels and digital interfaces to ensure efficient and safe operation.
- Conduct regular inspections of the plant, identifying any malfunctions, leaks, or potential hazards and initiating corrective actions promptly.
- Adjust operational parameters such as temperature, pressure, and flow rates to optimize production processes and maintain product quality.
- Perform routine maintenance tasks, including cleaning equipment, lubricating machinery, and assisting with minor repairs to prevent downtime.
- Record operational data, readings, and maintenance activities accurately in logs and digital systems, ensuring compliance with safety and environmental regulations.
- Respond to alarms and emergency situations by following established protocols to mitigate risks and ensure the safety of personnel and plant assets.
- Collaborate with maintenance teams, engineers, and other operators to troubleshoot issues and coordinate activities that impact plant operations.
Work Environment
Plant Operators typically work in industrial settings such as power plants, chemical processing facilities, water treatment plants, or manufacturing plants. The environment can be loud, with machinery noise, and may involve exposure to various temperatures, from hot to cold, depending on the process. Work schedules often involve rotating shifts, including nights, weekends, and holidays, to ensure continuous operation. Collaboration with a team of other operators, supervisors, and maintenance personnel is constant, requiring clear communication and teamwork. The pace of work can range from steady monitoring to highly reactive during unexpected events or emergencies, demanding quick thinking and problem-solving skills. While some monitoring occurs in a control room, significant time is spent on the plant floor conducting inspections.
Tools & Technologies
Plant Operators routinely use specialized control systems, including Distributed Control Systems (DCS) and Supervisory Control and Data Acquisition (SCADA) systems, to monitor and manage plant processes. They operate various gauges, sensors, and meters to collect data on pressure, temperature, flow, and other critical parameters. Personal protective equipment (PPE) like hard hats, safety glasses, and hearing protection is essential for daily tasks. Communication tools such as two-way radios and intercom systems facilitate coordination. Basic hand tools are often used for minor adjustments and maintenance. Data logging software and electronic record-keeping systems are critical for compliance and operational tracking.
Plant Operator Skills & Qualifications
Plant Operators manage and monitor industrial equipment and systems in facilities such as power plants, manufacturing plants, water treatment plants, or chemical processing plants. Qualifications for this role emphasize practical experience and a strong understanding of operational procedures and safety protocols. The specific requirements vary significantly based on the industry, the complexity of the plant, and the type of equipment involved.
Entry-level positions often require a high school diploma or equivalent, coupled with vocational training or an associate's degree in a relevant technical field. More senior or specialized roles, particularly in highly regulated industries like nuclear power or chemical processing, frequently demand extensive on-the-job training, certifications, and sometimes a bachelor's degree in engineering or a related discipline. Practical experience often outweighs formal education, especially for experienced operators, but certifications demonstrate specialized knowledge and commitment to safety standards.
The skill landscape for Plant Operators is evolving with increasing automation and digital integration. Operators now need strong computer literacy to manage sophisticated control systems, in addition to traditional mechanical aptitude. Certifications from organizations like the National Institute for the Uniform Licensing of Power Engineers (NIULPE) or industry-specific associations are highly valued, indicating proficiency and adherence to industry best practices. Understanding how to interpret digital readouts and troubleshoot automated systems is becoming as critical as manual equipment operation.
Education Requirements
Technical Skills
- Process Control Systems (DCS, SCADA, PLC): Operating and monitoring automated control systems to manage plant processes, including understanding HMI interfaces and basic troubleshooting.
- Equipment Operation and Monitoring: Starting, stopping, adjusting, and continuously monitoring pumps, valves, turbines, compressors, boilers, and other industrial machinery.
- Safety Protocols and Emergency Procedures: Strict adherence to Lockout/Tagout (LOTO), confined space entry, hot work permits, and emergency response plans.
- Preventive Maintenance and Troubleshooting: Performing routine checks, identifying equipment malfunctions, and conducting basic repairs or coordinating with maintenance personnel.
- Instrumentation and Controls: Interpreting readings from gauges, meters, and sensors; understanding the function of control loops and instrumentation.
- Blueprint and P&ID Interpretation: Reading and understanding Piping and Instrumentation Diagrams (P&IDs), electrical schematics, and mechanical blueprints.
- Chemical Handling and Safety (for chemical plants): Knowledge of Material Safety Data Sheets (MSDS), safe handling, storage, and disposal of hazardous materials.
- Water Treatment Processes (for water/wastewater plants): Understanding filtration, chemical treatment, disinfection, and sludge management processes.
- Basic Electrical and Mechanical Principles: Fundamental knowledge of electrical circuits, motor operation, hydraulics, pneumatics, and mechanical systems.
- Data Logging and Reporting: Accurately recording operational data, incidents, and maintenance activities, often using computerized maintenance management systems (CMMS).
Soft Skills
- Attention to Detail: Plant Operators must meticulously monitor gauges, alarms, and system outputs to detect anomalies and prevent potential equipment failures or safety hazards.
- Problem-Solving: Quickly identifying the root cause of equipment malfunctions or process deviations and implementing effective solutions to restore normal operations is crucial.
- Adherence to Procedures: Strict compliance with safety protocols, operational guidelines, and regulatory requirements is paramount to ensure a safe and efficient working environment.
- Situational Awareness: Maintaining a constant understanding of the plant's operational status, potential risks, and the impact of actions on overall system performance is vital.
- Communication: Clearly relaying operational status, incident reports, and maintenance needs to supervisors, colleagues, and maintenance teams is essential for coordinated efforts and safety.
- Adaptability: Adjusting to changing operational conditions, emergency situations, or new technologies and procedures is necessary for continuous plant efficiency and safety.
How to Become a Plant Operator
Entering the Plant Operator field involves several pathways, ranging from vocational training to direct entry with on-the-job learning. Aspiring operators can pursue certifications or associate's degrees in process technology, which provide a strong theoretical foundation. Alternatively, many companies hire individuals with a strong mechanical aptitude and provide extensive internal training, especially for entry-level helper or trainee positions.
The timeline for becoming a Plant Operator varies significantly. A complete beginner might spend 6-12 months on vocational training, followed by 3-6 months of job searching. Someone transitioning from a related field, like mechanics or manufacturing, might secure a role faster, potentially within 3-6 months, leveraging their existing hands-on experience. Larger industrial facilities often have more structured training programs and clearer advancement paths.
Geographic location plays a crucial role; areas with heavy industry, such as petrochemicals, power generation, or manufacturing, will have more opportunities. Networking with current operators and professionals in local industrial parks or attending industry-specific job fairs can uncover hidden opportunities. While some roles prioritize formal degrees, practical experience and a demonstrated understanding of safety protocols are universally valued.
Step 1
Step 2
Step 3
Step 4
Step 5
Step 6
Education & Training Needed to Become a Plant Operator
Becoming a Plant Operator involves a blend of formal education and hands-on training. While a four-year degree is not typically required, many successful operators hold an associate's degree in process technology, industrial maintenance, or a related engineering field. These two-year programs, costing $8,000-$20,000, provide a strong theoretical foundation in plant systems, safety protocols, and operational procedures. They usually include internships, offering practical experience.
Alternatively, vocational training programs and certifications from technical colleges or industry associations offer more focused pathways. These can range from a few weeks to a year, costing $2,000-$10,000, and concentrate on specific equipment operation, safety certifications (like OSHA), and regulatory compliance. Many plant operators also begin their careers through apprenticeships, which combine paid on-the-job training with classroom instruction, often lasting 2-4 years. These apprenticeships are highly valued by employers, as they ensure practical proficiency and adherence to industry standards.
Employers generally prefer candidates with formal training or certifications, as they demonstrate a baseline understanding of complex plant operations and safety. Continuous learning is vital; operators must stay updated on new technologies, environmental regulations, and safety standards through regular professional development courses. The specific educational needs vary by the type of plant (e.g., power, chemical, water treatment) and the complexity of its operations. Practical experience, gained through internships, apprenticeships, or entry-level positions, remains crucial for career advancement, complementing theoretical knowledge by building problem-solving skills in real-world scenarios.
Plant Operator Salary & Outlook
Compensation for a Plant Operator varies significantly based on several factors, extending beyond base salary. Geographic location plays a major role; areas with a higher concentration of industrial plants or a higher cost of living, such as the Northeast or specific parts of Texas and California, typically offer higher wages. Conversely, regions with lower living costs may show more modest figures.
Years of experience dramatically influence earning potential. Entry-level operators earn less, while those with specialized certifications in areas like wastewater treatment, power generation, or chemical processing command higher salaries due to their unique skill sets. Total compensation packages often include overtime pay, which can significantly boost annual earnings, along with performance bonuses, and robust benefits such as health insurance, retirement contributions, and paid time off. Some roles in critical infrastructure may also offer shift differentials.
Industry-specific trends also shape compensation. The energy sector, particularly oil and gas, often provides premium compensation compared to water treatment or manufacturing due to higher risks and specialized equipment. Larger companies or those operating complex, high-value plants tend to offer more competitive salaries and benefits. Remote work is generally not applicable to this hands-on role, emphasizing location-specific market rates. While salary figures are presented in USD, international markets have their own distinct compensation structures influenced by local regulations, economic conditions, and industry demand.
Salary by Experience Level
Level | US Median | US Average |
---|---|---|
Junior Plant Operator | $50k USD | $55k USD |
Plant Operator | $65k USD | $70k USD |
Senior Plant Operator | $80k USD | $85k USD |
Lead Plant Operator | $90k USD | $95k USD |
Plant Operations Supervisor | $105k USD | $110k USD |
Plant Manager | $125k USD | $135k USD |
Market Commentary
The job market for Plant Operators shows steady demand, driven by the continuous need for essential services like power generation, water treatment, and manufacturing. Growth projections indicate a stable outlook, with the Bureau of Labor Statistics projecting little to no change in employment for power plant operators over the next decade, for instance, reflecting a balance between retiring workers and increased automation. However, specific sectors like renewable energy plants or advanced manufacturing facilities may see higher demand.
Emerging opportunities often involve roles in automated or smart plants, requiring operators to possess strong technical skills in monitoring complex digital control systems. The industry faces a supply and demand dynamic where an aging workforce is retiring, creating openings that require new entrants with specific certifications and technical aptitude. This creates a need for skilled operators to ensure plant efficiency and safety.
Future-proofing in this role involves continuous learning in digital controls, data analytics for predictive maintenance, and understanding sustainable operational practices. While automation can reduce the need for some manual tasks, human oversight and problem-solving skills remain crucial for complex industrial processes. The profession is generally recession-resistant due to its essential nature, ensuring consistent job availability across various economic cycles. Geographic hotspots for Plant Operators align with major industrial hubs, energy production regions, and densely populated areas requiring extensive utility infrastructure.
Plant Operator Career Path
Career progression for a Plant Operator typically involves a journey from foundational operational tasks to advanced leadership and strategic management. Professionals often begin by mastering equipment and safety protocols, gradually taking on more complex systems. This field offers distinct pathways: an individual contributor (IC) track leading to senior operational roles, and a management track culminating in supervisory or managerial positions.
Advancement speed depends on several factors, including individual performance, the complexity of the plant (e.g., power generation, chemical processing, water treatment), company size, and industry demand. Specialization in specific types of machinery or control systems can accelerate progression. Lateral movement often occurs within different plant types or into related fields like maintenance, safety, or quality control. Larger corporations may offer clearer, more structured advancement paths, while smaller operations might provide broader exposure but fewer formal steps.
Continuous learning, adherence to safety regulations, and a strong understanding of plant economics are crucial for growth. Networking within the industry and seeking mentorship from experienced operators or supervisors also significantly aids career development. Key milestones often include obtaining specific certifications (e.g., wastewater treatment licenses, boiler operator certifications), leading critical shutdowns, or successfully implementing process improvements. Some operators may pivot into training roles, engineering support, or compliance management, leveraging their deep operational knowledge.
Junior Plant Operator
0-2 yearsKey Focus Areas
Plant Operator
2-5 yearsKey Focus Areas
Senior Plant Operator
5-8 yearsKey Focus Areas
Lead Plant Operator
8-12 yearsKey Focus Areas
Plant Operations Supervisor
12-18 yearsKey Focus Areas
Plant Manager
18+ yearsKey Focus Areas
Junior Plant Operator
0-2 yearsPerform routine operational tasks under direct supervision, including monitoring gauges, recording data, and conducting basic equipment checks. Assist senior operators with adjustments and system changes. Ensure adherence to immediate safety guidelines and contribute to maintaining a clean work environment.
Key Focus Areas
Develop a strong understanding of basic plant operations, safety protocols, and emergency procedures. Focus on learning equipment identification, standard operating procedures, and basic troubleshooting. Build foundational knowledge of control room systems and data logging.
Plant Operator
2-5 yearsOperate specific plant equipment independently, monitor control panels, and respond to alarms and deviations. Implement routine operational adjustments to maintain production targets and quality standards. Participate in shift handovers, communicate operational status, and ensure compliance with environmental regulations.
Key Focus Areas
Master a wider range of plant equipment and control systems. Develop skills in diagnosing operational issues, performing routine maintenance checks, and optimizing processes for efficiency. Understand the interdependencies of various plant sections and contribute to problem-solving.
Senior Plant Operator
5-8 yearsServe as a subject matter expert for specific plant areas or complex systems. Lead operational tasks during critical periods, including startups and shutdowns. Provide guidance and training to less experienced operators. Analyze operational data to identify trends and recommend efficiency improvements.
Key Focus Areas
Deepen expertise in complex operational procedures, system optimization, and advanced troubleshooting. Develop mentoring skills to guide junior operators. Focus on improving plant efficiency, reducing downtime, and contributing to process improvement initiatives. Understand regulatory compliance in depth.
Lead Plant Operator
8-12 yearsCoordinate and oversee the activities of a shift or a specific operational unit. Assign tasks, monitor progress, and ensure all operational procedures are followed. Act as a primary point of contact for technical issues during the shift. Contribute to incident investigations and safety audits.
Key Focus Areas
Cultivate strong leadership skills, including effective communication, conflict resolution, and decision-making under pressure. Focus on coordinating shift activities, optimizing team performance, and implementing best practices. Develop a strategic understanding of overall plant goals and production targets.
Plant Operations Supervisor
12-18 yearsManage a team of plant operators, overseeing daily operations across multiple shifts or sections. Responsible for staff training, performance reviews, and disciplinary actions. Ensure compliance with all safety, environmental, and operational regulations. Collaborate with maintenance and engineering teams to resolve complex issues.
Key Focus Areas
Develop comprehensive managerial skills, including performance management, scheduling, budgeting, and project oversight. Focus on fostering a strong safety culture, enhancing team productivity, and ensuring operational excellence. Understand the business impact of operational decisions.
Plant Manager
18+ yearsHold ultimate responsibility for the entire plant's operations, including production targets, safety, environmental compliance, and financial performance. Develop and implement strategic plans for plant upgrades, efficiency improvements, and personnel development. Represent the plant in corporate meetings and with regulatory bodies.
Key Focus Areas
Acquire executive leadership skills, including strategic planning, financial management, stakeholder engagement, and risk assessment. Focus on long-term plant performance, technological advancements, and continuous improvement initiatives. Develop strong external communication and negotiation abilities.
Job Application Toolkit
Ace your application with our purpose-built resources:
Plant Operator Cover Letter Examples
Personalizable templates that showcase your impact.
View examplesPlant Operator Job Description Template
Ready-to-use JD for recruiters and hiring teams.
View examplesGlobal Plant Operator Opportunities
Plant Operators manage complex industrial machinery and systems across various sectors globally. This role translates well internationally, with demand in manufacturing, energy, and chemical industries worldwide. The global job market for Plant Operators remains stable in 2025, driven by industrial growth and infrastructure projects.
Regulatory differences impact operational standards, requiring adaptability. Professionals consider international roles for higher pay, specialized projects, and diverse experience. International certifications like OSHA or NEBOSH can enhance global mobility.
Global Salaries
Plant Operator salaries vary significantly by region and industry. In North America, particularly the U.S. and Canada, operators earn between $60,000 and $90,000 USD annually. For example, in Texas, a skilled operator might make $75,000 USD, while in Alberta, Canada, it could be around $85,000 CAD (approx. $63,000 USD). These figures often include comprehensive benefits like health insurance and retirement plans.
European salaries range from €35,000 to €60,000 (approx. $38,000-$65,000 USD). In Germany, operators could earn €45,000 (approx. $49,000 USD), while in the UK, it might be £38,000 (approx. $48,000 USD). Nordic countries might offer slightly higher compensation but come with higher living costs. Benefits packages generally include generous vacation time and public healthcare access.
Asia-Pacific markets, like Australia, offer competitive salaries from AUD $70,000 to $100,000 (approx. $46,000-$66,000 USD), reflecting a high cost of living. In Southeast Asia, salaries are lower, typically $15,000-$30,000 USD, but purchasing power can be higher. Middle Eastern countries like Saudi Arabia often provide tax-free salaries ranging from $40,000 to $70,000 USD, often with housing allowances, which significantly boosts take-home pay.
Latin American salaries are generally lower, from $10,000 to $25,000 USD, with varying benefits. Experience and specialized skills, such as PLC programming or specific machinery certifications, often increase earning potential across all regions. International pay scales are rare for this role, as compensation is highly localized.
Remote Work
International remote work opportunities for Plant Operators are extremely limited. This role requires hands-on operation, monitoring, and maintenance of physical equipment at a specific industrial site. Direct physical presence is a fundamental requirement for the job.
Some supervisory or planning aspects of a Plant Operator's role might involve remote coordination, but actual operation cannot be done remotely. Digital nomad opportunities are not applicable to this profession. Employers rarely hire Plant Operators for international remote work due to the on-site nature of the duties.
Salary expectations for Plant Operators are tied to the physical location of the plant. Geographic arbitrage is not feasible for this role. Equipment, internet, and workspace setup for remote work are irrelevant, as the job demands on-site performance and physical interaction with machinery.
Visa & Immigration
Plant Operators seeking international work typically use skilled worker visas. Popular destination countries include Canada, Australia, Germany, and the U.S. Each country has specific requirements. For instance, Canada's Express Entry system or Australia's Skilled Migration program often list Plant Operator under specific NOC or ANZSCO codes, requiring skills assessments and English language proficiency.
Education credential recognition is crucial; diplomas or certifications from your home country must often be assessed for equivalency. Professional licensing is generally not required for Plant Operators, but specific industry certifications (e.g., confined space, hazardous materials) are essential and must meet local standards. Visa timelines vary, from a few months to over a year.
Pathways to permanent residency often exist after several years of skilled employment. Language requirements for English-speaking countries include IELTS or PTE tests. For Germany, basic German language skills (A2/B1) are often beneficial or required. Family visas for dependents are usually available once the primary applicant secures their work permit.
2025 Market Reality for Plant Operators
Understanding the current market realities for plant operators is vital for successful career planning. The landscape has significantly evolved between 2023 and 2025, influenced by post-pandemic shifts and the accelerating AI revolution.
Broader economic factors directly impact industrial output and, consequently, the demand for skilled operators. These market realities vary considerably by experience level, specific industry, geographic region, and the size of the operating facility. This analysis provides an honest assessment to help plant operators navigate these complex dynamics.
Current Challenges
Plant operators face increased competition for entry-level positions due to a stable, but not rapidly expanding, market. Automation technologies, while creating new roles, also reduce the need for some manual oversight, meaning operators must adapt their skill sets.
Economic uncertainties impact plant expansion projects, which in turn slows hiring. Job seekers often encounter a mismatch between available positions and their specific certifications or experience with newer control systems, extending job search timelines.
Growth Opportunities
Despite market stability, strong demand persists for plant operators skilled in advanced control systems and data interpretation. Emerging opportunities lie in facilities adopting Industry 4.0 technologies, such as smart factories and automated power grids, where operators manage integrated digital systems.
Professionals can gain a competitive edge by pursuing certifications in SCADA systems, industrial cybersecurity, or predictive analytics. Underserved markets exist in regions with aging infrastructure requiring modernization, or in new green energy plants, including solar and wind farms, which require specialized operational oversight.
Operators with experience in diverse industrial environments or those cross-trained in maintenance and quality control are highly valued. The current market correction encourages strategic upskilling to align with future industry needs. Sectors like water treatment, pharmaceuticals, and renewable energy remain robust and actively seek qualified operators, offering stable career paths.
Current Market Trends
The market for plant operators in 2025 shows stable demand, particularly in essential sectors like utilities, manufacturing, and chemical processing. Hiring patterns reflect a need for operators skilled in modern control systems and automated processes, moving beyond traditional manual operations.
Recent industry changes include a stronger emphasis on predictive maintenance and data analysis, driven by AI and IoT integration. This means operators now monitor complex sensor outputs and respond to algorithm-driven alerts. Economic conditions, while not causing widespread layoffs, have led to more cautious hiring, focusing on replacing retiring staff or filling highly specialized roles rather than large-scale expansion.
Technology trends significantly reshape the operator's role. Generative AI assists in optimizing plant performance and troubleshooting, while automation handles routine tasks. Employers increasingly seek operators with strong IT literacy, a grasp of HMI (Human-Machine Interface) systems, and an understanding of cybersecurity protocols. Salary trends for experienced operators remain competitive, but entry-level saturation can make securing initial roles challenging without relevant certifications or vocational training.
Geographic variations are notable; regions with robust industrial bases or new infrastructure projects, such as the Gulf Coast for petrochemicals or the Midwest for advanced manufacturing, exhibit stronger demand. Remote work normalization has minimal impact, as the role inherently requires on-site presence. Seasonal hiring is not a significant factor, with demand remaining consistent year-round for critical operations.
Emerging Specializations
The role of a Plant Operator is evolving significantly due to advancements in automation, data analytics, and sustainability initiatives. These technological shifts are creating new, specialized pathways that offer substantial career growth beyond traditional operational duties. Understanding these emerging areas allows operators to strategically position themselves for higher-value roles that often command premium compensation.
Early positioning in these future-oriented specializations is critical for career advancement in 2025 and beyond. While established specializations remain vital, focusing on cutting-edge areas ensures relevance and opens doors to leadership in next-generation operational environments. These emerging fields are not merely niche interests; they are becoming mainstream, creating significant job opportunities over the next three to five years as industries adopt advanced technologies.
Pursuing these emerging specializations involves a balance of risk and reward. While they require investment in new skills and knowledge, the potential for rapid career progression and increased earning potential often outweighs the initial effort. These roles are at the forefront of industrial innovation, offering Plant Operators the chance to shape the future of their facilities rather than simply maintaining current operations.
Automated Process Optimization Operator
Renewable Energy Systems Operator
Industrial Cybersecurity Operator
Predictive Operations Analyst
Advanced Manufacturing Process Operator
Pros & Cons of Being a Plant Operator
Making informed career decisions requires a clear understanding of both the benefits and challenges associated with a profession. The experience of a plant operator can vary significantly based on the industry sector, the type of facility, company culture, and an individual's specific role within the plant. What one person considers a pro, another might see as a con, depending on their personal values, lifestyle preferences, and career stage. For example, shift work might be a benefit for some seeking non-traditional hours, while it is a major challenge for others. This assessment provides a realistic overview, helping readers set appropriate expectations for a career as a plant operator.
Pros
- Plant operators typically earn competitive wages, with good benefits and opportunities for overtime pay, especially in industries like oil and gas, chemical, or power generation.
- Job security is strong in many sectors, as essential plants require continuous operation and skilled operators are always in demand to maintain production and safety.
- Operators gain valuable hands-on experience with complex industrial machinery and processes, developing a highly specialized skill set that is transferable across various manufacturing and utility industries.
- The work often involves a clear sense of purpose, as operators play a critical role in producing essential goods or services, contributing directly to the economy and society.
- Most plant operator roles do not require a four-year degree, allowing individuals to enter the field with a high school diploma, vocational training, or an associate's degree, reducing educational debt.
- Operators work as part of a close-knit team, fostering a strong sense of camaraderie and mutual support, which can make the challenging aspects of the job more manageable.
Cons
- Plant operators often work rotating shifts, including nights, weekends, and holidays, which can significantly disrupt personal life and social schedules.
- The work environment can be physically demanding, involving long periods of standing, walking, climbing stairs, and occasional heavy lifting, leading to fatigue.
- Exposure to hazardous materials, loud machinery, and extreme temperatures is common, requiring strict adherence to safety protocols and constant vigilance to prevent accidents.
- Stress levels can be high, particularly during equipment malfunctions, emergencies, or tight production schedules, where quick and accurate decisions are critical to prevent costly shutdowns or safety incidents.
- Career advancement opportunities may be limited within a single plant, often requiring relocation or extensive additional training to move into supervisory or engineering roles.
- Continuous learning is essential as technology evolves and new processes are introduced, requiring operators to frequently update their skills and knowledge through training programs.
Frequently Asked Questions
Plant Operators manage complex machinery and systems in industrial settings. They face distinct challenges related to safety protocols, continuous monitoring, and troubleshooting equipment failures. This section addresses common questions about entering this role, from required certifications to career advancement opportunities within diverse plant environments.
What are the basic educational and certification requirements to become a Plant Operator?
Entry-level Plant Operator positions typically require a high school diploma or GED. Many employers prefer candidates with vocational training, an associate's degree in process technology, or relevant certifications. Experience in a manufacturing or industrial environment, even in a different capacity, can be highly beneficial.
How long does it typically take to become a qualified Plant Operator, especially if I'm new to the field?
The timeline to become job-ready can vary. With a vocational program or associate's degree, it usually takes 1-2 years. Some entry-level roles offer on-the-job training, which can last from a few weeks to several months, depending on the complexity of the plant. Building practical experience is crucial for career progression.
What are the typical salary expectations for a Plant Operator, both entry-level and experienced?
Salaries for Plant Operators vary significantly based on industry, location, and experience. Entry-level operators might start in the $40,000-$55,000 range, while experienced operators in specialized fields like power generation or chemical processing can earn $60,000-$90,000 or more annually. Overtime pay is often a significant component due to shift work.
What is the typical work schedule and work-life balance like for a Plant Operator?
Plant Operators often work rotating shifts, including nights, weekends, and holidays, because plants operate 24/7. This schedule can impact work-life balance, but it also often comes with shift differentials and ample opportunities for overtime. The work environment can be demanding, requiring focus and adherence to strict safety procedures.
How secure is the job market for Plant Operators, considering automation and industry changes?
Job security for Plant Operators is generally stable, as these roles are essential for industries like energy, manufacturing, and water treatment. While automation might change some tasks, the need for skilled operators to monitor, troubleshoot, and maintain complex systems remains high. Demand can fluctuate with industrial growth and technological advancements.
What are the common career advancement opportunities for an experienced Plant Operator?
Career growth for Plant Operators often involves specializing in particular types of equipment or processes, moving into supervisory roles, or becoming a trainer. Operators can also advance into maintenance, safety, or engineering support positions. Continuous learning and obtaining advanced certifications enhance long-term career prospects.
What are the biggest challenges or unique aspects of working as a Plant Operator that I should be aware of?
The main challenges involve adapting to rotating shift schedules, continuously learning new technologies, and maintaining vigilance to prevent costly errors. Operators must also handle pressure during emergencies, strictly follow safety protocols, and often work in environments that can be hot, noisy, or require personal protective equipment.
Is remote work a possibility for Plant Operators, or are all roles on-site?
Plant Operator roles are almost exclusively on-site due to the hands-on nature of monitoring and controlling physical plant equipment. Remote work is not typically an option for this role, as operators need to be physically present to respond to alarms, inspect machinery, and perform manual adjustments or emergency shutdowns.
Related Careers
Explore similar roles that might align with your interests and skills:
Operator
A growing field with similar skill requirements and career progression opportunities.
Explore career guidePlant Technician
A growing field with similar skill requirements and career progression opportunities.
Explore career guidePlant Worker
A growing field with similar skill requirements and career progression opportunities.
Explore career guidePower Plant Operator
A growing field with similar skill requirements and career progression opportunities.
Explore career guideProcess Operator
A growing field with similar skill requirements and career progression opportunities.
Explore career guideAssess your Plant Operator readiness
Understanding where you stand today is the first step toward your career goals. Our Career Coach helps identify skill gaps and create personalized plans.
Skills Gap Analysis
Get a detailed assessment of your current skills versus Plant Operator requirements. Our AI Career Coach identifies specific areas for improvement with personalized recommendations.
See your skills gapCareer Readiness Assessment
Evaluate your overall readiness for Plant Operator roles with our AI Career Coach. Receive personalized recommendations for education, projects, and experience to boost your competitiveness.
Assess your readinessSimple pricing, powerful features
Upgrade to Himalayas Plus and turbocharge your job search.
Himalayas
Himalayas Plus
Himalayas Max
Find your dream job
Sign up now and join over 100,000 remote workers who receive personalized job alerts, curated job matches, and more for free!
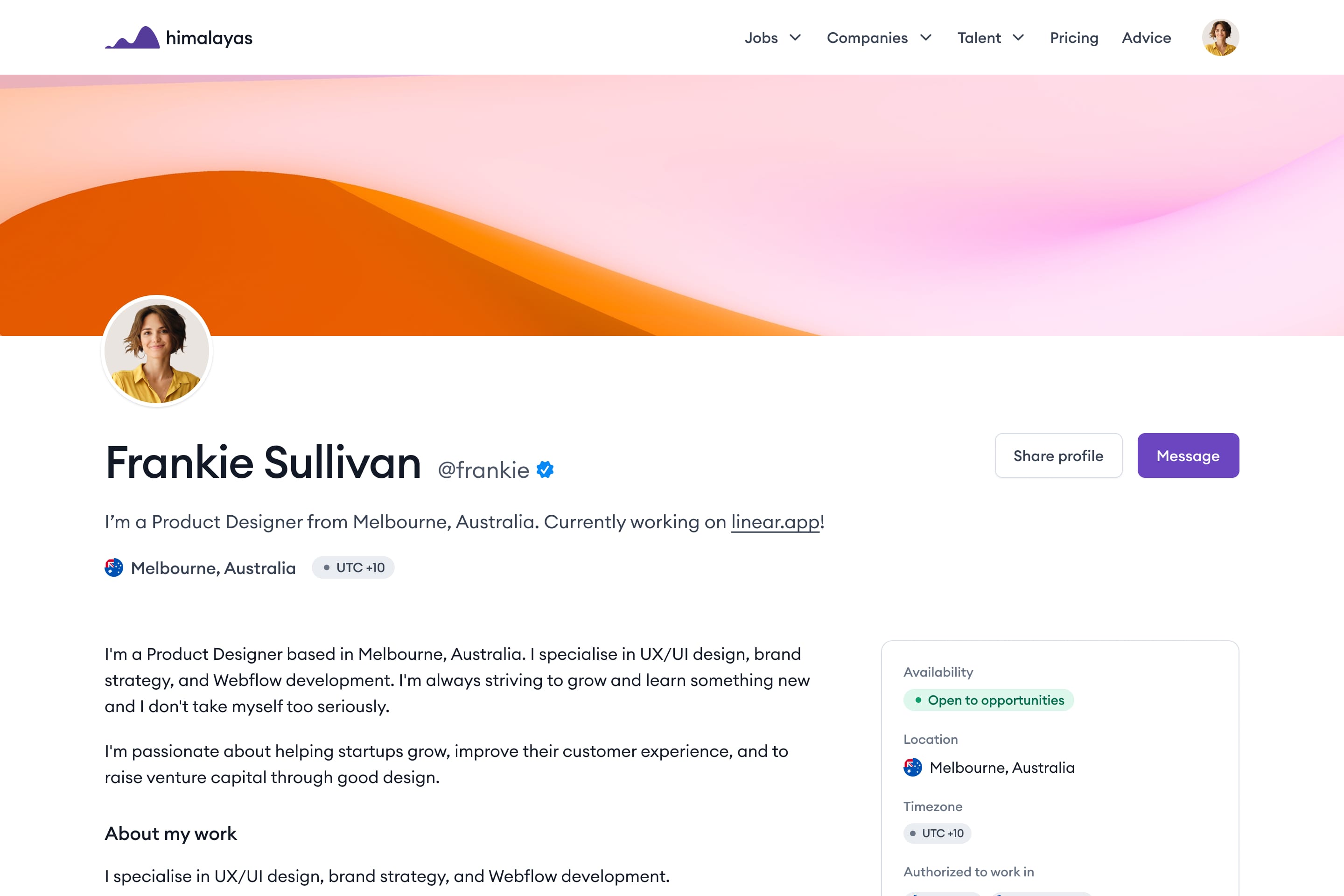