Complete Plant Controller Career Guide
Plant Controllers are the financial backbone of manufacturing and production facilities, directly impacting profitability by overseeing cost accounting, budgeting, and financial reporting at the operational level. They translate complex production data into actionable insights, ensuring efficiency and cost control crucial for a plant's success. This specialized role offers a unique blend of finance expertise and hands-on operational engagement, making it vital for companies with physical production sites.
Key Facts & Statistics
Median Salary
$156,100 USD
(U.S. national median for Financial Managers, BLS May 2023)
Range: $80k - $200k+ USD
Growth Outlook
16%
much faster than average (for Financial Managers, BLS 2022-2032)
Annual Openings
≈17,800
openings annually (for Financial Managers, BLS 2022-2032)
Top Industries
Typical Education
Bachelor's degree in Accounting, Finance, or Business; Master's degree (e.g., MBA) often preferred for advancement
What is a Plant Controller?
A Plant Controller is the chief financial officer responsible for the financial health and performance of a single manufacturing plant or production facility. This role focuses specifically on operational finance, ensuring accurate cost accounting, budgeting, forecasting, and financial reporting at the plant level. They act as a strategic business partner to the plant manager, providing critical financial insights that drive operational efficiency and profitability.
Unlike a Corporate Controller who oversees the entire organization's financial operations, or a Financial Analyst who might work across various departments, the Plant Controller's scope is confined to the specific manufacturing site. They are deeply embedded in the plant's day-to-day operations, analyzing production costs, inventory management, and variance analysis to identify and implement cost-saving measures and improve plant profitability. Their expertise bridges the gap between financial theory and practical manufacturing operations.
What does a Plant Controller do?
Key Responsibilities
- Oversee all accounting operations at the manufacturing plant, including general ledger, accounts payable, accounts receivable, and cost accounting functions.
- Prepare detailed financial reports, including monthly, quarterly, and annual statements, ensuring accuracy and compliance with accounting standards.
- Develop and implement robust internal controls to safeguard company assets and ensure the integrity of financial data within the plant.
- Analyze production costs, variances, and profitability drivers to identify areas for cost reduction and operational efficiency improvements.
- Lead the annual budgeting and forecasting processes for the plant, collaborating with operational managers to set realistic financial targets.
- Provide financial insights and strategic recommendations to plant management for decision-making regarding production, inventory, and capital expenditures.
- Manage inventory valuation and reconciliation processes, ensuring accurate reporting of stock levels and compliance with company policies. This includes overseeing cycle counts and physical inventories. This also includes analyzing inventory turns and identifying potential obsolescence issues.
Work Environment
A Plant Controller typically works in a manufacturing or production facility, often with a dedicated office space within the plant. The environment is dynamic and fast-paced, requiring close collaboration with production, operations, and supply chain teams. They regularly walk the plant floor to understand processes and observe operations firsthand. The role often involves a standard work week, but extended hours may be necessary during month-end closes, year-end audits, or budgeting cycles. While primarily on-site, some flexibility may exist for remote work on specific tasks, depending on company policy. The work demands strong communication skills and the ability to translate complex financial data into actionable insights for non-financial colleagues.
Tools & Technologies
Plant Controllers regularly use Enterprise Resource Planning (ERP) systems like SAP, Oracle, Microsoft Dynamics 365, or Infor to manage financial transactions, inventory, and production data. These systems are central to their daily operations. For data analysis and reporting, they heavily rely on Microsoft Excel, often leveraging advanced functions for financial modeling and variance analysis. Business intelligence (BI) tools such as Tableau, Power BI, or Qlik Sense are increasingly important for creating dashboards and visualizing performance metrics. Communication and collaboration tools like Microsoft Teams or Slack facilitate interaction with plant personnel and corporate finance. Knowledge of specific manufacturing software, such as Manufacturing Execution Systems (MES) or Warehouse Management Systems (WMS), is also beneficial for understanding operational data. They also work with financial reporting software and cost accounting modules within their ERP.
Plant Controller Skills & Qualifications
The Plant Controller role demands a unique blend of robust financial expertise and deep operational understanding within a manufacturing environment. This position is central to a plant's financial health, providing critical insights that drive cost control, efficiency, and strategic decision-making. Qualifications for this role vary significantly based on the company's size, industry, and the complexity of its manufacturing processes.
For entry-level Plant Controller positions, typically in smaller or less complex plants, a strong foundation in accounting principles and some exposure to manufacturing operations is sufficient. As one advances to senior or multi-plant controller roles, the emphasis shifts towards strategic financial planning, advanced cost accounting, and leadership capabilities. Larger, publicly traded companies often prioritize candidates with public accounting experience, particularly those with a CPA, due to stringent reporting requirements.
Formal education, typically a Bachelor's degree in Accounting or Finance, forms the bedrock for this career. Practical experience, especially within a manufacturing setting, is often equally, if not more, valued than advanced degrees alone. Certifications like the Certified Management Accountant (CMA) or Certified Public Accountant (CPA) significantly enhance a candidate's profile, demonstrating a commitment to professional standards and specialized knowledge in management accounting or public accounting, respectively. The skill landscape is evolving, with an increasing need for data analytics capabilities and proficiency in enterprise resource planning (ERP) systems to manage complex data sets and automate reporting processes.
Education Requirements
Technical Skills
- Advanced Cost Accounting (standard costing, activity-based costing, variance analysis)
- Financial Planning & Analysis (FP&A) including budgeting, forecasting, and long-range planning
- Enterprise Resource Planning (ERP) systems proficiency (e.g., SAP, Oracle, Microsoft Dynamics) with a focus on manufacturing modules
- Microsoft Excel (advanced functions, pivot tables, financial modeling)
- Generally Accepted Accounting Principles (GAAP) and International Financial Reporting Standards (IFRS) compliance
- Inventory Management and Valuation (FIFO, LIFO, weighted-average, obsolescence analysis)
- Capital Expenditure (CAPEX) analysis and justification (ROI, NPV, IRR)
- Manufacturing Operations knowledge (production processes, lean manufacturing, supply chain principles)
- Data Visualization Tools (e.g., Tableau, Power BI) for presenting financial performance
- Internal Controls and Compliance (Sarbanes-Oxley Act, internal audit procedures)
- Taxation principles related to manufacturing operations
- Financial Reporting and Consolidation
Soft Skills
- Analytical Thinking: Plant Controllers must dissect complex financial data, identify trends, and pinpoint areas for cost reduction or efficiency improvement within plant operations.
- Business Acumen: Understanding the end-to-end manufacturing process, supply chain, and market dynamics is crucial for providing relevant financial insights and strategic guidance.
- Communication Skills: Effective communication is essential for translating complex financial information into understandable terms for non-financial plant personnel, senior management, and operational teams.
- Leadership and Influence: This role requires leading financial planning processes, influencing operational decisions, and guiding cross-functional teams towards financial goals without direct authority over production.
- Problem-Solving: Plant Controllers frequently address unexpected financial variances, operational inefficiencies, or supply chain disruptions, requiring quick and effective solutions.
- Attention to Detail: Accuracy in financial reporting, variance analysis, and inventory management is paramount, as small errors can have significant financial implications for the plant.
- Adaptability: Manufacturing environments are dynamic; Plant Controllers must adapt to changes in production volumes, product lines, technology, and economic conditions while maintaining financial control.
How to Become a Plant Controller
Breaking into a Plant Controller role involves a blend of financial acumen, operational understanding, and strategic thinking. While a traditional accounting or finance degree is a common starting point, individuals can also transition from roles like Cost Accountant, Financial Analyst, or even Production Supervisor with a strong grasp of manufacturing financials. The timeline for entry varies; a recent graduate might spend 2-3 years in a junior accounting role gaining relevant experience, while a seasoned professional from a related field could transition in 6-12 months with targeted upskilling.
Entry strategies differ significantly by company size and industry. Smaller manufacturing plants might hire a Plant Controller directly from a senior accounting role, valuing hands-on experience over specific certifications. Larger corporations often prefer candidates with CPA or CMA certifications and experience with enterprise resource planning (ERP) systems like SAP or Oracle. Geographical location also plays a role; industrial hubs will have more opportunities, but may also have more competition. Networking within manufacturing associations and supply chain communities is crucial, as many opportunities are filled through referrals.
A common misconception is that this role is purely about number crunching; in reality, a Plant Controller acts as a strategic business partner, influencing operational decisions and driving profitability. Candidates must demonstrate not only their ability to manage financial data but also their capacity to translate financial insights into actionable operational improvements. Overcoming entry barriers often involves highlighting any experience with cost accounting, inventory management, or production variance analysis, even if gained in a non-traditional setting.
Step 1
Step 2
Step 3
Step 4
Step 5
Step 6
Education & Training Needed to Become a Plant Controller
Becoming a Plant Controller requires a strong foundation in accounting, finance, and operations management. Formal education, typically a Bachelor's degree in Accounting or Finance, is often the most common entry point. These four-year programs usually cost between $40,000 and $100,000 or more at public universities, and significantly higher at private institutions, with completion taking four years of full-time study. They provide the theoretical knowledge in financial reporting, cost accounting, and auditing crucial for the role.
Alternative pathways, such as professional certifications like the CMA (Certified Management Accountant), offer a focused approach. The CMA typically costs $2,000-$4,000, including exam fees and study materials, and can be completed in 6-18 months of dedicated self-study or bootcamp participation. While not a substitute for a degree in many cases, a CMA significantly enhances a candidate's profile, particularly for those with existing business degrees or extensive experience. Employers highly value the CMA for its emphasis on management accounting and strategic financial management, directly relevant to a Plant Controller's responsibilities.
Continuous learning is vital for Plant Controllers, as industry best practices and technology evolve. Online courses from platforms like Coursera or edX provide specialized knowledge in areas like supply chain finance, advanced Excel for finance, or ERP system proficiency. These courses range from a few hundred to a few thousand dollars and can be completed in weeks or months. Practical experience within a manufacturing environment, often starting in a cost accountant or financial analyst role, complements theoretical knowledge. The combination of formal education, professional certification, and hands-on operational finance experience forms the most robust educational background for a Plant Controller.
Plant Controller Salary & Outlook
Compensation for a Plant Controller varies significantly, influenced by numerous factors beyond just base salary. Geographic location plays a crucial role; areas with a higher cost of living or strong manufacturing sectors often offer higher pay. This includes major industrial hubs in the U.S. and extends to international markets, where local economic conditions and industry presence dictate compensation, often benchmarked against USD.
Experience, specialized industry knowledge, and specific skill sets dramatically impact earning potential. A Plant Controller with expertise in lean manufacturing, supply chain optimization, or advanced ERP systems can command a premium. Total compensation packages frequently include performance-based bonuses, which can be substantial, along with comprehensive benefits like health insurance, retirement contributions (401k matching), and professional development allowances. Some larger organizations might also offer equity or long-term incentive plans.
Industry-specific compensation trends reflect the profitability and complexity of the manufacturing sector. High-growth or highly regulated industries, such as aerospace, automotive, or pharmaceuticals, typically offer more competitive salaries. Company size also matters; larger corporations with more complex operations and higher revenue usually pay more. Salary negotiation leverage comes from demonstrating a direct impact on profitability, cost reduction, and operational efficiency.
Remote work's impact on Plant Controller roles is limited due to the inherent on-site nature of manufacturing operations. However, some corporate oversight or regional roles might offer hybrid flexibility, potentially affecting geographic arbitrage opportunities. Understanding these elements helps professionals maximize their earning potential in this vital financial leadership role.
Salary by Experience Level
Level | US Median | US Average |
---|---|---|
Assistant Plant Controller | $80k USD | $85k USD |
Plant Controller | $110k USD | $115k USD |
Senior Plant Controller | $135k USD | $140k USD |
Regional Plant Controller | $170k USD | $175k USD |
Director of Plant Controlling | $200k USD | $205k USD |
Market Commentary
The job market for Plant Controllers remains stable with consistent demand, driven by the ongoing need for robust financial oversight in manufacturing operations. As of 2025, the outlook for this role is positive, with projected growth tied to the expansion of manufacturing sectors, particularly in advanced manufacturing and automation. The U.S. Bureau of Labor Statistics projects a steady demand for financial managers, which includes roles like Plant Controllers, indicating a reliable career path.
Emerging opportunities for Plant Controllers include specializations in data analytics, where the ability to interpret complex operational data for strategic decision-making is highly valued. The increasing adoption of AI and automation in manufacturing processes means Plant Controllers must evolve their skills to integrate financial analysis with operational technology. This requires a strong understanding of ERP systems, supply chain finance, and predictive analytics.
Supply and demand dynamics show a consistent need for experienced professionals who can bridge the gap between finance and operations. Companies seek controllers who can not only manage budgets but also drive operational improvements and cost efficiencies. Geographic hotspots for these roles include states with strong manufacturing bases, such as Michigan, Ohio, Texas, and parts of the Southeast, where new plants and expansions are common.
The role of a Plant Controller is largely recession-resistant because financial control and cost management become even more critical during economic downturns. Future-proofing this career involves continuous learning in areas like digital transformation, sustainable manufacturing finance, and global supply chain risk management. While some analytical tasks may see automation, the strategic oversight, leadership, and interpretive skills of a Plant Controller are unlikely to be fully automated, ensuring long-term career viability.
Plant Controller Career Path
Career progression for a Plant Controller involves a blend of financial acumen, operational understanding, and leadership development. Professionals typically begin in analytical or assistant roles, gradually taking on more responsibility for a plant's financial health and strategic planning. Advancement can follow an individual contributor (IC) track, deepening specialization in financial analysis and operational efficiency, or a management track, leading teams and overseeing multiple facilities.
Advancement speed depends on several factors: individual performance, particularly in cost savings and process improvements; the complexity and size of the plants managed; and the overall industry's economic conditions. Lateral moves might include transitioning into corporate finance roles, supply chain finance, or even operational management, leveraging a deep understanding of manufacturing processes. Company type also shapes the path; a startup might offer faster advancement but less structured roles, while a large corporation provides more defined steps and extensive training programs.
Networking within the company and industry, seeking mentorship, and building a reputation for accurate forecasting and insightful analysis are crucial for progression. Achieving certifications like CMA or CPA can accelerate advancement. Common pivots involve moving from a single plant focus to multi-plant or regional oversight, eventually leading to strategic roles that influence overall business unit profitability and efficiency.
Assistant Plant Controller
1-3 yearsKey Focus Areas
Plant Controller
3-6 years total experience; 2-3 years in roleKey Focus Areas
Senior Plant Controller
6-10 years total experience; 3-4 years in roleKey Focus Areas
Regional Plant Controller
10-15 years total experience; 4-5 years in roleKey Focus Areas
Director of Plant Controlling
15+ years total experience; 5+ years in roleKey Focus Areas
Assistant Plant Controller
1-3 yearsSupports the Plant Controller in daily financial operations, including month-end close activities, journal entries, and reconciliations. Assists with variance analysis, budget preparation, and forecasting. Gathers and analyzes financial data to identify cost drivers and inefficiencies. Works closely with operational teams to understand production processes and their financial implications.
Key Focus Areas
Develop strong foundational accounting skills, including general ledger, accounts payable, and accounts receivable. Focus on mastering financial reporting tools and enterprise resource planning (ERP) systems. Build an understanding of manufacturing processes, cost accounting principles, and inventory valuation. Seek opportunities to participate in budgeting and forecasting cycles.
Plant Controller
3-6 years total experience; 2-3 years in roleManages the financial performance of a single manufacturing plant. Oversees all accounting functions, including cost accounting, inventory control, budgeting, and forecasting. Provides financial analysis and strategic guidance to plant management to optimize profitability and operational efficiency. Ensures compliance with company policies and financial regulations. Leads financial audits and manages a small team of accounting professionals.
Key Focus Areas
Master cost accounting, budgeting, and forecasting. Enhance analytical skills to provide actionable insights on production costs, inventory, and capital expenditures. Develop leadership skills by mentoring junior staff and leading cross-functional projects. Improve communication skills to present complex financial data clearly to non-financial stakeholders. Focus on driving financial performance and supporting operational decision-making.
Senior Plant Controller
6-10 years total experience; 3-4 years in roleOversees financial operations for a large or complex manufacturing plant, or multiple smaller plants. Provides in-depth financial analysis, strategic planning, and performance management insights to senior plant and business unit leadership. Leads major cost reduction initiatives and capital investment evaluations. Mentors and develops a team of finance professionals. Represents the plant's financial interests in broader organizational discussions.
Key Focus Areas
Refine strategic financial planning and analysis capabilities, focusing on long-term plant profitability and investment decisions. Develop advanced leadership skills, including team development, change management, and stakeholder influence. Gain expertise in supply chain finance and operational excellence methodologies. Pursue certifications like CMA or CPA for deeper financial credibility.
Regional Plant Controller
10-15 years total experience; 4-5 years in roleManages financial performance and strategic initiatives across multiple manufacturing plants within a specific geographical region. Develops and implements standardized financial reporting, budgeting, and forecasting processes across the region. Provides consolidated financial insights and strategic recommendations to corporate leadership. Leads regional financial teams, ensuring consistent application of financial controls and policies. Drives regional cost optimization and capital allocation strategies.
Key Focus Areas
Cultivate strong business acumen, understanding market dynamics, competitive landscapes, and supply chain intricacies across multiple regions. Develop executive leadership skills, including strategic communication, negotiation, and cross-cultural team management. Focus on driving standardization, best practices, and continuous improvement across all regional plants. Build a robust professional network within the industry.
Director of Plant Controlling
15+ years total experience; 5+ years in roleLeads the overall financial strategy and operations for the manufacturing division or a significant business unit with multiple plants. Sets financial policies, controls, and reporting standards across the entire plant network. Provides strategic financial guidance to the executive leadership team, influencing major investment decisions, operational improvements, and business growth initiatives. Responsible for talent development within the plant controlling function and ensures alignment with corporate financial objectives.
Key Focus Areas
Master enterprise-level financial strategy, risk management, and capital allocation. Develop exceptional executive leadership, influencing skills, and the ability to drive change across diverse business units. Focus on talent management, succession planning, and building high-performing finance organizations. Gain deep expertise in M&A financial integration and global supply chain finance.
Job Application Toolkit
Ace your application with our purpose-built resources:
Plant Controller Cover Letter Examples
Personalizable templates that showcase your impact.
View examplesPlant Controller Job Description Template
Ready-to-use JD for recruiters and hiring teams.
View examplesGlobal Plant Controller Opportunities
Plant Controllers globally manage financial operations within manufacturing facilities. This role involves cost accounting, budgeting, and performance analysis specific to production sites.
Global demand remains strong, particularly in emerging industrial markets and established manufacturing hubs, as companies seek efficiency. Regulatory differences impact tax reporting and compliance, while cultural nuances affect communication styles. International opportunities provide exposure to diverse supply chains and operational models, enhancing career growth. Professionals often benefit from certifications like CMA or CIMA for global recognition.
Global Salaries
Salaries for Plant Controllers vary significantly by region and experience. In North America, a Plant Controller in the US typically earns between $90,000 and $130,000 USD annually, while in Canada, ranges are C$80,000 to C$115,000 (approximately $58,000-$84,000 USD). These figures reflect a higher cost of living in major US cities compared to many Canadian counterparts.
European salaries differ widely. In Germany, a Plant Controller might earn €70,000 to €100,000 (around $76,000-$109,000 USD), with excellent social benefits and vacation time. The UK offers £60,000 to £90,000 (approximately $75,000-$112,000 USD), but purchasing power can be lower due to higher living costs in cities like London. Eastern Europe, like Poland, sees salaries from PLN 100,000 to PLN 180,000 (about $25,000-$45,000 USD), offering strong purchasing power relative to local expenses.
Asia-Pacific markets present diverse compensation. Australia's Plant Controllers typically earn A$100,000 to A$150,000 (about $66,000-$99,000 USD). In China, salaries range from RMB 250,000 to RMB 500,000 (roughly $35,000-$70,000 USD), with significant variations between tier-one cities and smaller industrial zones. Latin America, such as Mexico, offers MXN 400,000 to MXN 800,000 (around $22,000-$44,000 USD), where local purchasing power can be considerable. Tax implications and social security contributions vary, impacting net take-home pay, and often differ from common North American benefit structures. International experience and advanced degrees generally command higher compensation.
Remote Work
True international remote work for a Plant Controller is limited due to the inherent on-site nature of the role. This position requires direct involvement with plant operations, production lines, and inventory management. Most companies prefer or require Plant Controllers to be physically present at the manufacturing facility daily.
However, some regional or corporate Plant Controller roles may allow for hybrid models or occasional remote work, especially for reporting or strategic planning. Digital nomad opportunities are generally not feasible for this specific role. Tax implications and legal compliance for international remote work would be complex if such an arrangement existed. Companies typically hire Plant Controllers locally, expecting physical presence to oversee the plant's financial health and operational efficiency.
Visa & Immigration
Plant Controllers seeking international roles often utilize skilled worker visas. Popular destinations include Germany, Canada, and Australia, known for their industrial sectors. Germany's 'Blue Card' requires a recognized degree and a job offer meeting a salary threshold. Canada's Express Entry system assesses points for age, education, language proficiency, and work experience, often requiring an Educational Credential Assessment.
Australia's Skilled Independent Visa (subclass 189) or Employer Nominated Scheme (subclass 186) are common pathways, with specific occupation lists. Recognition of accounting and finance credentials is crucial; professional bodies like CPA Australia or Chartered Accountants ANZ often assess qualifications. Typical visa processing times range from 6 to 18 months. Language proficiency, often demonstrated through IELTS or TOEFL, is usually a requirement for non-English speaking countries. Some multinational corporations facilitate intra-company transfers for Plant Controllers, simplifying the process. Pathways to permanent residency exist in many countries after several years of skilled employment. Family visas for dependents are usually available alongside the primary applicant's visa.
2025 Market Reality for Plant Controllers
Understanding current market realities for a Plant Controller is crucial for career success. The economic landscape, post-pandemic shifts, and the rapid integration of AI tools have reshaped expectations for this vital role.
The market for Plant Controllers has seen significant evolution from 2023 to 2025. Broader economic factors like inflation, supply chain disruptions, and interest rate changes directly influence manufacturing output and, consequently, the demand for financial oversight at the plant level. Market realities also vary by company size, with larger corporations often seeking more specialized experience, and by geographic region, depending on local manufacturing hubs. This analysis provides an honest assessment of current hiring conditions.
Current Challenges
Plant Controllers face increased scrutiny on cost control and efficiency targets. Automation and AI tools demand new analytical skills, creating a knowledge gap for some. Competition remains high for experienced candidates who can drive significant operational improvements. Economic uncertainties push companies to consolidate roles or delay hiring.
Growth Opportunities
Despite challenges, strong opportunities exist for Plant Controllers who embrace operational finance. Roles focused on driving efficiency, optimizing production costs, and implementing lean manufacturing principles are in high demand. Companies are actively seeking controllers who can bridge the gap between financial data and operational performance.
Emerging opportunities lie in specializations such as sustainability reporting, where controllers analyze environmental impact costs, and in predictive analytics for supply chain optimization. Professionals who upskill in data science, advanced Excel modeling, and enterprise resource planning systems gain a significant competitive edge. Mid-sized manufacturing firms and those in niche industries like advanced materials or renewable energy often present robust opportunities.
Strategic career moves might involve targeting companies undergoing digital transformation or those expanding production lines. These situations require strong financial leadership at the plant level. Networking within manufacturing associations and pursuing certifications in lean six sigma or supply chain management can also open doors to less saturated segments of the market.
Current Market Trends
Demand for Plant Controllers remains steady, but the role has evolved significantly. Companies now seek individuals who can not only manage financial reporting but also act as strategic business partners to plant operations. This shift means a greater emphasis on operational finance, predictive analytics, and process improvement.
Generative AI and advanced analytics tools are transforming how Plant Controllers perform variance analysis, forecasting, and cost optimization. They automate routine data compilation, freeing controllers to focus on strategic insights. However, this also means employers expect higher proficiency in data visualization tools and enterprise resource planning systems like SAP and Oracle.
Economic conditions, particularly inflation and supply chain volatility, are impacting manufacturing profitability. Plant Controllers are crucial in identifying cost-saving opportunities and managing inventory effectively. Salary trends are stable, with a slight upward pressure for candidates possessing strong operational acumen and technological proficiency. Remote work remains less common for this role compared to other finance positions, given the need for on-site presence to understand plant operations deeply. Hiring generally sees peaks after budget cycles or during periods of significant capital expenditure projects.
Emerging Specializations
Technological advancements and evolving industry landscapes consistently create new specialization opportunities for financial professionals. For Plant Controllers, this means moving beyond traditional cost accounting to embrace roles at the intersection of finance, data science, and operational efficiency. Early positioning in these emerging areas, particularly from 2025 onwards, provides a distinct advantage.
These forward-looking specializations often command premium compensation and accelerate career growth. They equip professionals with unique skill sets highly valued by organizations navigating complex global markets and supply chains. While established specializations remain vital, focusing on emerging areas allows Plant Controllers to become strategic partners rather than just historical reporters.
Many of these cutting-edge specializations are already gaining traction and are expected to generate significant job opportunities within the next three to five years. Pursuing these paths involves a calculated risk, requiring investment in new skills. However, the potential rewards in terms of career advancement and influence within an organization are substantial, making it a strategic choice for ambitious Plant Controllers.
Predictive Cost & Performance Analyst
Sustainability Finance Controller
Digital Transformation Finance Lead
Financial Data Integrity & Security Specialist
Global Supply Chain Finance Manager
Pros & Cons of Being a Plant Controller
Understanding both the advantages and challenges of a career is crucial for making informed decisions. The experience of a Plant Controller can vary significantly based on the company's industry, the specific plant's size and complexity, and the prevailing corporate culture. What one individual perceives as a benefit, another might see as a drawback, depending on their personal values, work style, and career aspirations. Additionally, the demands and opportunities within this role can evolve as one progresses from an early-career professional to a more senior level. This assessment provides a realistic overview of the typical pros and cons to help set appropriate expectations.
Pros
Central role in operational decision-making by providing critical financial insights into production costs, efficiency, and profitability at the plant level.
Significant impact on the plant's financial performance, as direct oversight of budgeting, forecasting, and cost control allows for tangible contributions to the bottom line.
Exposure to diverse aspects of the business, including manufacturing processes, supply chain, and inventory management, offering a holistic understanding of industrial operations.
Strong demand for skilled professionals who can bridge the gap between finance and operations, providing good job security in manufacturing and production-heavy industries.
Opportunity for continuous learning in a dynamic environment, as the role requires adapting to new production technologies, market changes, and evolving financial regulations.
Clear career progression paths, often leading to corporate finance roles, regional controller positions, or even broader operational management roles within the organization.
Develops strong analytical and problem-solving skills through daily analysis of variances, cost drivers, and performance metrics to identify areas for improvement.
Cons
High-pressure environment during month-end and year-end close processes, requiring long hours and tight deadlines to ensure accurate financial reporting and compliance.
Exposure to operational challenges and unexpected production issues, which can directly impact financial forecasts and require quick, adaptive problem-solving.
Potential for conflict with plant operations management, as cost control measures and financial discipline may sometimes clash with production goals or departmental spending desires.
Limited direct interaction with external clients or high-level corporate strategy, as the role is primarily focused on internal plant-level financial performance and reporting.
Risk of burnout due to the demanding nature of balancing financial oversight with operational realities, especially in plants with continuous improvement initiatives or significant change.
Career progression may be slower or require relocation, as senior finance roles often consolidate at corporate headquarters, limiting advancement opportunities within a single plant.
The need for constant vigilance over inventory, scrap, and production variances means that even small operational inefficiencies can become significant financial headaches.
Frequently Asked Questions
Plant Controllers face distinct challenges balancing financial oversight with operational realities. This section addresses key questions about this role, from entry requirements and career progression to managing cost control and driving efficiency in a manufacturing environment.
What are the essential educational qualifications and certifications needed to become a Plant Controller?
Becoming a Plant Controller typically requires a bachelor's degree in accounting, finance, or a related business field. Many successful controllers also hold certifications like the CMA (Certified Management Accountant) or an MBA, which can accelerate career progression and enhance credibility. Practical experience in cost accounting within a manufacturing setting is crucial for understanding the nuances of plant operations.
How long does it typically take to become a Plant Controller, and what career steps lead to this role?
The path to becoming a Plant Controller can vary but generally takes 5-10 years of experience. You often start in roles like Staff Accountant, Cost Accountant, or Financial Analyst within a manufacturing company. Gaining exposure to different operational aspects, such as production, supply chain, and inventory management, is vital. Demonstrating strong analytical skills and leadership potential will help you advance more quickly.
What is the job security and market demand for Plant Controllers, considering economic fluctuations?
Plant Controllers play a critical role in optimizing manufacturing efficiency and profitability, making the field generally stable with good demand. As long as there are physical manufacturing operations, there will be a need for financial oversight at the plant level. Economic downturns can affect manufacturing, but the need for cost control and financial analysis often increases during such times, reinforcing the controller's value.
What is the typical work-life balance like for a Plant Controller, including hours and travel?
The work-life balance for a Plant Controller can be demanding, especially during month-end closes, budgeting cycles, and year-end audits. While it is primarily an office-based role, Plant Controllers often spend significant time on the plant floor interacting with operations teams. Some roles may require occasional travel or extended hours to meet deadlines, but it is generally a standard 40-50 hour work week outside of peak periods.
What are the realistic salary expectations for a Plant Controller, and what factors influence compensation?
A Plant Controller's salary varies based on factors like company size, industry, location, and experience. Entry-level Plant Controller roles might start around $80,000 to $100,000, while experienced professionals in larger organizations can earn well over $120,000 to $150,000 annually. Performance bonuses tied to plant profitability and efficiency are also common.
What are the common career growth paths and advancement opportunities available for a Plant Controller?
Career growth for a Plant Controller often involves moving to larger, more complex manufacturing facilities or advancing to corporate finance roles. You could become a Regional Controller, Director of Finance, or even a CFO within a manufacturing group. Specializing in areas like Lean Manufacturing or Six Sigma can also open doors to operational leadership positions, leveraging your unique blend of financial and operational insights.
What are the most significant challenges and unique responsibilities of a Plant Controller compared to other accounting roles?
The biggest challenges often include accurately forecasting costs in a dynamic production environment, effectively communicating financial performance to non-financial plant personnel, and implementing cost-saving initiatives without disrupting operations. You must balance strict financial controls with the need for operational flexibility and continuous improvement. Managing inventory valuation and reconciling production variances are also ongoing complexities.
Can someone transition into a Plant Controller role from a public accounting background, and what skills are transferable?
Yes, transitioning from public accounting to a Plant Controller role is a common and viable path. Public accounting provides a strong foundation in financial reporting, audit, and tax, which are all valuable skills. However, you will need to actively seek opportunities that offer exposure to cost accounting, inventory management, and operational finance within manufacturing to bridge the knowledge gap effectively.
Related Careers
Explore similar roles that might align with your interests and skills:
Finance Controller
A growing field with similar skill requirements and career progression opportunities.
Explore career guideFinancial Controller
A growing field with similar skill requirements and career progression opportunities.
Explore career guidePlant Manager
A growing field with similar skill requirements and career progression opportunities.
Explore career guideProduction Control Manager
A growing field with similar skill requirements and career progression opportunities.
Explore career guideProduction Controller
A growing field with similar skill requirements and career progression opportunities.
Explore career guideAssess your Plant Controller readiness
Understanding where you stand today is the first step toward your career goals. Our Career Coach helps identify skill gaps and create personalized plans.
Skills Gap Analysis
Get a detailed assessment of your current skills versus Plant Controller requirements. Our AI Career Coach identifies specific areas for improvement with personalized recommendations.
See your skills gapCareer Readiness Assessment
Evaluate your overall readiness for Plant Controller roles with our AI Career Coach. Receive personalized recommendations for education, projects, and experience to boost your competitiveness.
Assess your readinessSimple pricing, powerful features
Upgrade to Himalayas Plus and turbocharge your job search.
Himalayas
Himalayas Plus
Himalayas Max
Find your dream job
Sign up now and join over 100,000 remote workers who receive personalized job alerts, curated job matches, and more for free!
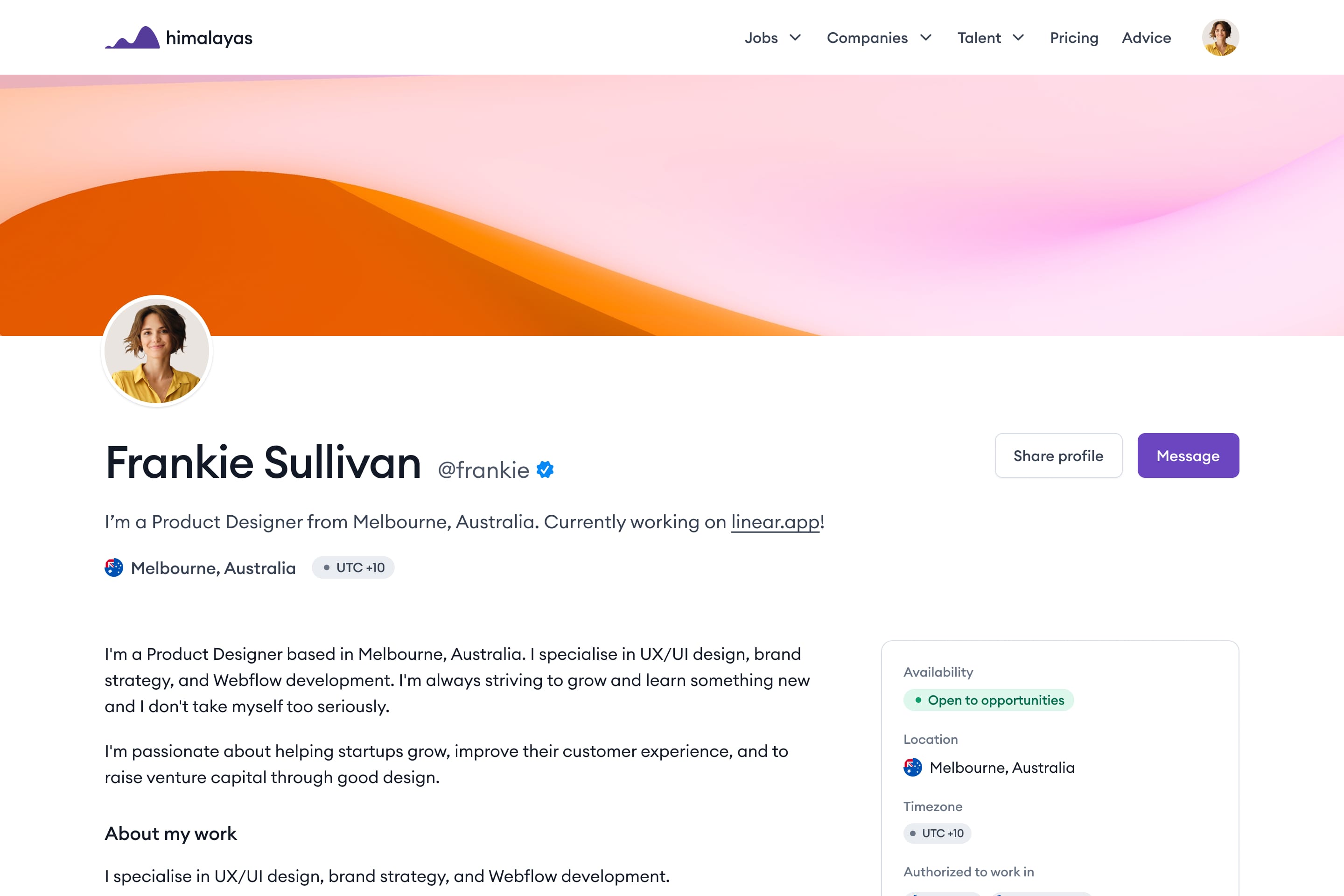