Complete Plant Manager Career Guide
Plant Managers are the strategic leaders who orchestrate the entire production lifecycle, ensuring efficiency, quality, and safety within manufacturing facilities. They bridge the gap between corporate vision and daily operations, optimizing processes to deliver products on time and within budget. This critical role demands a blend of technical expertise, leadership skills, and a keen eye for operational excellence, offering a rewarding path for those who thrive in dynamic, hands-on environments.
Key Facts & Statistics
Median Salary
$115,600 USD
(U.S. Bureau of Labor Statistics, May 2023)
Range: $70k - $180k+ USD, varying significantly by industry, company size, and location.
Growth Outlook
1%
as fast as average (U.S. Bureau of Labor Statistics, 2022-2032)
Annual Openings
≈17,200
openings annually (U.S. Bureau of Labor Statistics, 2022-2032)
Top Industries
Typical Education
Bachelor's degree in engineering, business administration, or a related field. Many positions prefer or require a Master's degree (e.g., MBA or M.S. in Operations Management) and significant experience.
What is a Plant Manager?
A Plant Manager is a senior operational leader responsible for the overall efficiency, productivity, and profitability of a manufacturing facility. This role encompasses everything from overseeing daily production processes and ensuring product quality to managing personnel, budgets, and safety standards. They serve as the central figure ensuring that a plant operates smoothly and meets its strategic objectives.
Unlike a Production Supervisor, who focuses on day-to-day line management, or a Director of Operations, who typically oversees multiple plants or broader supply chain functions, the Plant Manager holds ultimate accountability for a single facility's performance. They integrate various departments like production, maintenance, quality, and logistics, ensuring all functions work cohesively to produce goods effectively and safely.
What does a Plant Manager do?
Key Responsibilities
- Direct and coordinate daily manufacturing operations, ensuring production schedules are met efficiently and effectively.
- Implement and enforce safety protocols and quality control standards to maintain a safe working environment and high product integrity.
- Manage and mentor a team of production supervisors and line workers, fostering a culture of continuous improvement and accountability.
- Oversee budgeting and cost control initiatives, identifying opportunities to reduce waste and optimize resource utilization.
- Collaborate with supply chain and logistics teams to ensure timely delivery of raw materials and distribution of finished goods.
- Analyze production data and performance metrics to identify bottlenecks and implement corrective actions for operational improvements.
- Develop and execute strategic plans for plant growth and capacity expansion, aligning with overall company objectives and market demands.
Work Environment
Plant Managers typically work in a dynamic industrial setting, which can range from a clean room facility to a heavy manufacturing plant. The environment often involves a mix of office work for planning and analysis, and significant time on the factory floor for oversight, problem-solving, and direct team engagement. The pace is generally fast, requiring quick decision-making and adaptability to production challenges.
Collaboration is constant, involving direct reports, cross-functional teams like engineering and quality, and external vendors. Work hours are usually full-time, often extending beyond standard business hours to address operational issues or meet production deadlines. Travel is generally minimal, primarily to other company sites or for industry conferences.
Tools & Technologies
Plant Managers utilize a diverse set of tools and technologies to oversee operations. Enterprise Resource Planning (ERP) systems like SAP, Oracle, or Microsoft Dynamics are crucial for managing production planning, inventory, and supply chain logistics. Manufacturing Execution Systems (MES) track real-time production data, machine performance, and quality metrics.
Statistical Process Control (SPC) software helps monitor and improve product quality, while Computerized Maintenance Management Systems (CMMS) such as Maximo or Fiix schedule and track equipment maintenance. Communication and collaboration tools like Microsoft Teams or Slack facilitate team coordination. Data visualization tools like Tableau or Power BI are used to analyze operational performance. They also leverage various industrial automation technologies, including Programmable Logic Controllers (PLCs) and Supervisory Control and Data Acquisition (SCADA) systems, to monitor and control manufacturing processes.
Plant Manager Skills & Qualifications
The Plant Manager role demands a unique blend of technical acumen, operational leadership, and strategic business understanding. Qualification structures prioritize a strong foundation in engineering or manufacturing, often complemented by practical experience. Requirements vary significantly based on the industry sector, company size, and the complexity of the manufacturing processes involved.
For entry-level Plant Manager positions, often in smaller facilities or as an Assistant Plant Manager, a solid engineering degree combined with 5-7 years of supervisory experience in a production environment is common. Senior Plant Managers, particularly in large, multi-national corporations or highly regulated industries, usually possess a Master's degree (e.g., MBA or M.Sc. in Operations Management) and 10-15+ years of progressive leadership experience. Practical experience, including a proven track record of driving efficiency and managing large teams, often outweighs formal education alone. Certifications in lean manufacturing, Six Sigma, or project management add significant value, demonstrating a commitment to operational excellence.
The skill landscape for Plant Managers is evolving. There is a growing emphasis on digital transformation, automation, and sustainable manufacturing practices. While traditional operational skills remain crucial, understanding Industry 4.0 concepts, data analytics for decision-making, and environmental compliance are becoming "must-have" capabilities. The balance between breadth of operational knowledge and depth in specific manufacturing processes shifts with career stage; early-career managers may focus on specific production lines, while senior leaders require a holistic view of the entire plant's performance and supply chain integration.
Education Requirements
Technical Skills
- Lean Manufacturing principles (e.g., Kaizen, 5S, Value Stream Mapping, JIT)
- Six Sigma methodologies (DMAIC, statistical process control, root cause analysis)
- Production planning and scheduling software (e.g., ERP systems like SAP, Oracle)
- Supply Chain Management and Logistics optimization
- Manufacturing processes and equipment operation (e.g., CNC machining, injection molding, assembly lines)
- Quality Management Systems (e.g., ISO 9001, IATF 16949) and quality control tools
- Industrial Automation and Robotics (e.g., PLC programming, SCADA systems, HMI)
- Environmental, Health, and Safety (EHS) regulations and compliance (e.g., OSHA, EPA)
- Maintenance Management Systems (CMMS) and Predictive/Preventive Maintenance strategies
- Data analysis and reporting tools (e.g., Excel, Power BI, Tableau for operational metrics)
- Budgeting, cost control, and financial performance analysis specific to manufacturing operations
- Project Management software and methodologies (e.g., MS Project, Agile for operational improvements)
Soft Skills
- Leadership and Team Development: Essential for motivating, mentoring, and guiding diverse teams to achieve production targets and foster a culture of continuous improvement.
- Strategic Thinking and Planning: Crucial for setting long-term operational goals, optimizing resource allocation, and aligning plant operations with overall business objectives.
- Problem-Solving and Decision-Making: Necessary for quickly identifying root causes of production issues, implementing effective solutions, and making critical decisions under pressure.
- Communication and Stakeholder Management: Vital for effectively conveying operational performance, challenges, and strategies to senior management, employees, and external partners.
- Adaptability and Change Management: Important for navigating evolving market demands, technological advancements, and implementing new processes or systems within the plant.
- Safety and Quality Focus: Critical for instilling a culture of safety adherence and ensuring that all manufactured products meet stringent quality standards and regulatory compliance.
- Financial Acumen: Required for managing budgets, controlling costs, analyzing profitability, and making financially sound operational decisions to optimize plant performance.
- Negotiation and Vendor Management: Important for securing favorable terms with suppliers, resolving disputes, and maintaining strong relationships with external partners to ensure smooth supply chains and material availability for production operations and continuous improvement efforts.
How to Become a Plant Manager
Becoming a Plant Manager involves a blend of technical expertise, leadership acumen, and operational efficiency. Entry pathways vary significantly, from traditional engineering or business degrees followed by years in production roles, to transitioning from a supervisor or operations management position within manufacturing. The timeline can range from 5-7 years for someone starting as an entry-level engineer to 2-3 years for an experienced production supervisor ready for promotion.
Geographic considerations play a role; manufacturing hubs will have more opportunities, but smaller markets might offer faster advancement in smaller facilities. Company size also matters; large corporations often have structured leadership development programs, while smaller companies might offer more direct exposure to a wider range of plant operations. Many people mistakenly believe a Plant Manager only handles production, but the role also encompasses safety, quality, supply chain, and human resources oversight.
Success in this field increasingly depends on a strong understanding of lean manufacturing, automation, and data-driven decision-making. Building a professional network through industry associations and mentorship is crucial for discovering opportunities and gaining insights into best practices. Overcoming barriers like a lack of direct plant management experience often requires demonstrating leadership potential and a track record of improving processes in previous roles.
Step 1
Step 2
Step 3
Step 4
Step 5
Step 6
Step 7
Education & Training Needed to Become a Plant Manager
Becoming a Plant Manager typically involves a blend of formal education and significant practical experience. Many successful Plant Managers hold a bachelor's degree in fields like Industrial Engineering, Mechanical Engineering, Manufacturing Engineering, or Business Administration with a focus on operations. A four-year degree usually costs between $40,000 and $120,000 or more, requiring four years of full-time study. These degrees provide a strong theoretical foundation in production processes, quality control, supply chain management, and leadership principles. Some professionals also pursue a Master of Business Administration (MBA) or a Master's in Engineering Management, which can cost $30,000 to $100,000+ and take 1-2 years.
Alternative learning paths, while less common for direct entry into a Plant Manager role, can supplement a degree or provide professional development. Online courses and certifications in lean manufacturing, Six Sigma, or project management are valuable for skill enhancement. These can range from a few hundred dollars to several thousand, with completion times from a few weeks to several months. Employers highly value formal degrees and industry certifications for Plant Managers, as these roles demand a deep understanding of complex operational systems and strategic leadership. Practical experience, often gained through roles like production supervisor, operations manager, or continuous improvement specialist, is equally critical for career progression to this senior leadership position.
Continuous learning remains essential for Plant Managers to stay current with new technologies, automation, and global supply chain trends. Industry associations often offer workshops and seminars for professional development. While specific accreditation for Plant Manager programs is not common, the accreditation of the underlying engineering or business degrees by bodies like ABET (for engineering) or AACSB (for business) is important. The cost-benefit analysis favors a formal degree combined with hands-on experience, as this combination provides the most robust pathway to securing and excelling in a Plant Manager role, which requires both technical expertise and strong leadership capabilities.
Plant Manager Salary & Outlook
Compensation for a Plant Manager varies significantly based on several critical factors. Geographic location plays a major role, with higher salaries typically found in regions with a high cost of living or concentrated manufacturing activity. For instance, a Plant Manager in the Midwest might earn less than one in California, even with similar responsibilities, due to differing market demands and local industry presence.
Years of experience, the size and complexity of the plant, and specific industry specialization also drive salary variations. A Plant Manager overseeing a large, highly automated facility in the automotive sector often commands a higher salary than one in a smaller, less complex food processing plant. Advanced skill sets in lean manufacturing, supply chain optimization, and automation technologies can further enhance earning potential.
Total compensation packages extend beyond base salary. They frequently include performance-based bonuses tied to production targets, safety records, and efficiency improvements. Equity options are less common for Plant Managers than in tech roles, but some senior leadership positions may offer them. Comprehensive benefits, including health insurance, retirement contributions like 401k matching, and allowances for professional development or certifications, are standard. Salary negotiation leverage increases with a proven track record of cost savings, production increases, and effective team management. While remote work is not typical for this hands-on role, some strategic or oversight roles at the Director or VP level might offer limited flexibility. It is important to note that all salary figures provided here are in USD, recognizing that international markets will have their own distinct compensation landscapes.
Salary by Experience Level
Level | US Median | US Average |
---|---|---|
Assistant Plant Manager | $80k USD | $85k USD |
Plant Manager | $120k USD | $125k USD |
Senior Plant Manager | $150k USD | $155k USD |
Operations Manager (Plant) | $165k USD | $170k USD |
Director of Plant Operations | $200k USD | $210k USD |
VP of Plant Operations | $265k USD | $280k USD |
Market Commentary
The job market for Plant Managers is stable with steady demand, driven by the ongoing need for efficient and optimized manufacturing operations. The U.S. Bureau of Labor Statistics projects a modest growth for industrial production managers, which includes Plant Managers, around 3% over the next decade. This growth is largely influenced by the reshoring of manufacturing activities and investments in advanced manufacturing technologies.
Emerging opportunities for Plant Managers are increasingly tied to technological integration. Expertise in Industry 4.0 concepts, including automation, IoT, AI-driven predictive maintenance, and data analytics, is becoming crucial. These skills allow Plant Managers to improve operational efficiency, reduce waste, and enhance decision-making. The demand for leaders who can navigate digital transformation within manufacturing facilities is growing.
Supply and demand dynamics show a consistent need for experienced Plant Managers, particularly those with strong leadership and technical skills. There is often a gap between available positions and candidates possessing the full spectrum of required operational and technological competencies. Future-proofing this role involves continuous learning in new manufacturing technologies and supply chain resilience strategies. While some aspects of planning might see AI assistance, the core hands-on leadership, problem-solving, and human capital management aspects of the Plant Manager role are largely recession-resistant and not prone to full automation. Geographic hotspots for these roles remain concentrated in traditional manufacturing belts, but also in areas with growing high-tech manufacturing, such as parts of the Southeast and Southwest.
Plant Manager Career Path
Career progression for a Plant Manager typically involves a blend of operational excellence, leadership development, and strategic acumen. Professionals in this field often begin in supervisory or assistant roles, gaining hands-on experience in production processes and team management. Advancement often depends on demonstrating consistent performance, optimizing plant efficiency, and successfully managing complex operational challenges.
Progression can follow an individual contributor (IC) track, focusing on specialized technical expertise and process improvement across multiple plants, or a management/leadership track, which emphasizes team leadership, strategic planning, and overall operational oversight. Factors influencing advancement speed include the size and complexity of the manufacturing facility, the specific industry (e.g., automotive, food processing, chemicals), and prevailing economic conditions affecting manufacturing output and investment. Continuous learning in areas like lean manufacturing, automation, and supply chain management becomes crucial for upward mobility.
Lateral movement opportunities exist into roles such as Supply Chain Manager, Quality Assurance Director, or even corporate roles in manufacturing strategy. Plant Managers in smaller operations might transition to larger, more complex facilities or join consulting firms specializing in operational efficiency. Networking within industry associations and mentorship from experienced leaders significantly aids career development, fostering reputation and opening doors to advanced opportunities.
Assistant Plant Manager
2-4 yearsKey Focus Areas
Plant Manager
5-8 years total experienceKey Focus Areas
Senior Plant Manager
8-12 years total experienceKey Focus Areas
Operations Manager (Plant)
10-15 years total experienceKey Focus Areas
Director of Plant Operations
15-20 years total experienceKey Focus Areas
VP of Plant Operations
20+ years total experienceKey Focus Areas
Assistant Plant Manager
2-4 yearsAssists the Plant Manager in daily operations, overseeing specific production lines or shifts. Helps coordinate raw material flow, monitors output, and ensures product quality. Addresses immediate operational issues, supports team leads, and contributes to safety compliance within defined areas.
Key Focus Areas
Develop foundational skills in production scheduling, quality control, and inventory management. Learn to manage and motivate production teams, ensuring adherence to safety protocols and standard operating procedures. Focus on understanding plant-specific machinery, maintenance requirements, and basic budgeting principles.
Plant Manager
5-8 years total experienceManages all aspects of a manufacturing plant's operations, including production, quality, maintenance, and logistics. Responsible for achieving production targets, managing budgets, and ensuring compliance with safety and environmental regulations. Leads and develops a team of supervisors and manages labor relations.
Key Focus Areas
Master lean manufacturing principles, continuous improvement methodologies (e.g., Six Sigma), and advanced problem-solving techniques. Enhance leadership capabilities, including conflict resolution, performance management, and talent development for supervisory staff. Focus on optimizing overall plant performance and cost control.
Senior Plant Manager
8-12 years total experienceOversees a larger or more complex plant, or multiple smaller facilities, with increased autonomy and strategic input. Responsible for significant budget management, leading major improvement projects, and implementing corporate manufacturing strategies. Mentors other plant managers and contributes to regional operational planning.
Key Focus Areas
Drive strategic initiatives for plant optimization, including capital expenditure planning and technology upgrades. Develop cross-functional leadership, influencing supply chain, engineering, and sales teams. Focus on long-term operational planning, risk management, and fostering a culture of continuous improvement and innovation.
Operations Manager (Plant)
10-15 years total experienceResponsible for the operational performance of multiple plants or a specific large operational division, often reporting to a regional or corporate director. Ensures consistency in operational standards, drives efficiency initiatives across sites, and supports strategic planning for manufacturing networks. Involves significant travel and coordination.
Key Focus Areas
Develop a broader understanding of end-to-end supply chain dynamics, including procurement, logistics, and distribution. Focus on cross-plant standardization, sharing best practices, and implementing company-wide operational policies. Cultivate strong stakeholder management skills with corporate leadership and external partners.
Director of Plant Operations
15-20 years total experienceProvides strategic leadership for all plant operations within a specific region or business unit. Accountable for P&L performance, capital investments, and long-term operational planning across multiple facilities. Develops and implements manufacturing policies, ensures compliance, and drives continuous improvement programs at a systemic level.
Key Focus Areas
Formulate and execute multi-year operational strategies that align with overall business objectives. Develop expertise in global manufacturing trends, advanced automation, and industry 4.0 technologies. Build executive presence, lead large-scale organizational change, and manage complex stakeholder relationships at a corporate level.
VP of Plant Operations
20+ years total experienceLeads the entire manufacturing and plant operations function across the organization, often at a national or global scale. Responsible for setting the strategic direction for all plants, optimizing the manufacturing network, and driving significant cost reduction and efficiency gains. A key member of the executive leadership team, influencing overall business strategy and investment decisions.
Key Focus Areas
Shape the company's global manufacturing footprint and long-term operational vision. Focus on enterprise-level risk management, strategic partnerships, and mergers & acquisitions related to manufacturing capabilities. Cultivate advanced executive leadership, board-level communication, and talent strategy for the entire operations function.
Job Application Toolkit
Ace your application with our purpose-built resources:
Global Plant Manager Opportunities
Plant Managers oversee production and operations globally, adapting to diverse industrial landscapes. International demand remains strong, particularly in manufacturing hubs across Asia and Europe, driven by supply chain shifts and automation. Regulatory compliance and cultural leadership styles vary significantly, requiring adaptable professionals. Many consider international roles for career advancement and exposure to new technologies. Some global manufacturing certifications, like Lean Six Sigma, enhance international mobility.
Global Salaries
Salaries for Plant Managers vary widely by region, industry, and plant size. In North America, a Plant Manager in the U.S. earns between $90,000 and $150,000 USD annually, while in Canada, ranges are typically $80,000 to $130,000 CAD (approx. $58,000 - $95,000 USD). European salaries reflect strong economies; Germany offers €70,000 to €120,000 (approx. $75,000 - $130,000 USD), and the UK sees £60,000 to £100,000 (approx. $75,000 - $125,000 USD).
Asia-Pacific markets present diverse figures. China's Plant Managers earn 300,000 to 600,000 CNY (approx. $42,000 - $84,000 USD), often with housing allowances, reflecting lower cost of living. In Australia, salaries are higher, ranging from $120,000 to $180,000 AUD (approx. $80,000 - $120,000 USD). Latin America, like Mexico, typically offers $50,000 to $90,000 USD, though purchasing power can be higher locally.
Cost of living adjustments are crucial; a lower nominal salary in Southeast Asia might offer similar purchasing power to a higher one in Western Europe. International compensation packages often include benefits like housing, relocation assistance, and private healthcare, which significantly impact total remuneration. Tax implications vary by country, affecting net take-home pay. For instance, high-tax European nations may offer lower net income despite competitive gross salaries. Experience and specialized industry knowledge, such as automotive or pharmaceutical manufacturing, influence global compensation significantly.
Remote Work
Plant Managers typically require on-site presence due to the hands-on nature of managing production lines, staff, and equipment. However, some strategic or oversight aspects of the role can be managed remotely. This includes supply chain coordination, performance analysis, and virtual team meetings with global stakeholders.
Fully remote Plant Manager roles are rare, but hybrid models are emerging. These allow for some administrative tasks to be done off-site, while critical operational oversight remains on-site. Legal and tax implications for international remote work can be complex, requiring careful consideration of permanent establishment rules and dual taxation agreements. Digital nomad visas are generally not suitable for this role due to the inherent need for physical presence.
International remote collaboration often involves managing significant time zone differences. Companies hiring for global manufacturing operations may have policies supporting some remote work for regional managers or strategic roles. Salary expectations for remote components of the role might be adjusted based on the manager's geographic location. Platforms for international hiring in manufacturing support roles exist, but direct plant management remains largely location-bound.
Visa & Immigration
Plant Managers frequently utilize skilled worker visas for international assignments. Popular destinations include Germany, Canada, and Australia, all with established pathways for skilled professionals. Germany's Blue Card or skilled worker visa requires a recognized degree and a job offer meeting salary thresholds. Canada's Express Entry system prioritizes candidates with relevant work experience and qualifications.
Education credential recognition is vital; official assessments often confirm foreign degrees' equivalency. Professional licensing is generally not required for Plant Managers, but industry-specific certifications or safety training may be mandatory. Visa timelines vary, from a few months for expedited applications to over a year for complex cases. Employers often sponsor these visas, handling much of the process.
Pathways to permanent residency exist in many countries after several years of skilled employment. Language proficiency, especially in German or French for respective countries, enhances visa success. Some countries offer fast-track programs for highly skilled professionals in demand sectors like manufacturing. Family visas are typically available for dependents, allowing spouses to seek employment and children to attend local schools, making international moves more feasible.
2025 Market Reality for Plant Managers
Understanding current market realities is critical for Plant Managers seeking new roles or career advancement. The manufacturing landscape has undergone significant shifts from 2023 to 2025, driven by post-pandemic supply chain recalibrations and the rapid integration of AI and automation.
Broader economic factors like inflation and interest rates influence capital expenditure, directly impacting plant expansion and new facility construction, which affects job availability. Market conditions for Plant Managers vary significantly by industry sector, geographic manufacturing hubs, and the size of the operating plant, with larger, more technologically advanced facilities often seeking specific skill sets. This analysis provides an honest assessment of these dynamics.
Current Challenges
Plant Managers face increased competition for fewer roles as companies consolidate operations or optimize existing facilities. Automation and AI tools improve efficiency, allowing some plants to operate with leaner management structures. Economic uncertainties also lead to hiring freezes or delayed expansion plans, impacting demand for new Plant Managers.
Growth Opportunities
Despite challenges, strong demand exists for Plant Managers who can drive digital transformation and operational excellence. Emerging roles in smart factories, particularly those focused on AI-driven optimization and robotics integration, offer significant opportunities.
Plant Managers with proven experience in implementing Industry 4.0 technologies, improving sustainability metrics, and leading diverse, cross-functional teams are highly valued. Underserved markets in specialized manufacturing sectors, such as advanced materials or electric vehicle components, present growth areas. Expertise in supply chain resilience and global logistics also provides a competitive edge.
Strategic career moves might involve targeting companies investing heavily in new technologies or those expanding into new product lines. Pursuing certifications in advanced manufacturing technologies or data analytics can significantly enhance marketability. The defense, aerospace, and medical device sectors also show consistent demand for experienced Plant Managers, even during broader economic slowdowns.
Current Market Trends
Hiring for Plant Managers in 2025 shows a nuanced demand. While essential for manufacturing, the market prioritizes candidates with strong digital transformation and automation experience. Companies seek leaders who can integrate AI-driven predictive maintenance and optimize smart factory operations, moving beyond traditional operational oversight.
Economic conditions and supply chain shifts directly influence plant management roles. Nearshoring and reshoring initiatives in some sectors create new plant openings, yet overall, the emphasis remains on efficiency and cost reduction in existing facilities. This leads to a stable but not rapidly expanding job market.
Employer requirements now heavily feature expertise in lean manufacturing, Six Sigma, and advanced data analytics for process improvement. There is a growing demand for Plant Managers who understand sustainable manufacturing practices and can implement ESG (Environmental, Social, Governance) initiatives. Salary trends remain competitive for top-tier talent, but growth for mid-level managers is modest due to market saturation and a focus on internal promotions. Remote work is rarely an option; these roles require on-site presence. Seasonal hiring patterns are minimal; demand typically aligns with company growth cycles or facility openings.
Emerging Specializations
The role of a Plant Manager is evolving significantly, driven by rapid advancements in automation, data analytics, and sustainability initiatives. These technological and operational shifts are creating distinct new specialization opportunities that extend beyond traditional production oversight. Understanding these emerging niches is crucial for professionals seeking to advance their careers and command premium compensation in 2025 and beyond.
Early positioning in these cutting-edge areas allows Plant Managers to become indispensable leaders, shaping the future of manufacturing. While established specializations remain vital, focusing on emerging fields provides a strategic advantage, often leading to faster career growth and higher earning potential due to specialized skill sets. These new areas, though currently emerging, are on a clear trajectory to become mainstream within the next three to five years, creating a significant number of job opportunities.
Pursuing an emerging specialization involves a balance of risk and reward. It requires proactive learning and adapting to new paradigms, but the potential for significant impact and leadership within the industry is substantial. Plant Managers who invest in these future-oriented skills will be well-equipped to navigate complex operational challenges and drive innovation in the next generation of manufacturing.
Smart Factory Automation Lead
This specialization focuses on integrating and managing advanced automation technologies, including collaborative robots (cobots), autonomous mobile robots (AMRs), and AI-driven production lines. Plant Managers in this role oversee the strategic deployment, optimization, and maintenance of these systems to maximize efficiency and safety. They also manage the workforce transition, ensuring human-robot collaboration is seamless and productive.
Sustainable Operations Manager
This area involves leading initiatives to minimize environmental impact, optimize resource consumption, and implement circular economy principles within the plant's operations. Plant Managers specializing here drive energy efficiency projects, waste reduction programs, and sustainable material sourcing. They also ensure compliance with evolving environmental regulations and pursue certifications like ISO 14001, enhancing the plant's green credentials and operational resilience.
Data-Driven Production Optimizer
This specialization focuses on leveraging data analytics to optimize plant performance, predict maintenance needs, and improve decision-making. Plant Managers in this role oversee the collection, analysis, and interpretation of operational data from various sensors and systems. They use insights to identify bottlenecks, forecast equipment failures, and implement data-driven improvements across production, quality, and supply chain functions.
Industrial Cybersecurity Lead
This role addresses the critical need to protect industrial control systems (ICS) and operational technology (OT) networks from cyber threats. Plant Managers specializing in cybersecurity oversee the implementation of robust security protocols, conduct risk assessments, and develop incident response plans for the plant's digital infrastructure. They collaborate with IT teams to bridge the gap between enterprise IT security and plant-floor operational security, ensuring continuous, secure production.
Intra-Plant Logistics & Flow Specialist
This specialization focuses on optimizing the plant's internal logistics and material flow, from raw material reception to finished goods dispatch, often integrating advanced automation and digital twins. Plant Managers in this area design efficient layouts, implement automated guided vehicles (AGVs), and utilize simulation software to enhance throughput and reduce lead times. They ensure seamless material handling, inventory accuracy, and just-in-time delivery within the plant environment.
Pros & Cons of Being a Plant Manager
Making an informed career choice requires a thorough understanding of both the potential benefits and inherent challenges of a given profession. The experience of a Plant Manager can vary significantly based on the industry, the size of the manufacturing facility, the specific company culture, and the manager's individual leadership style. Aspects that one person considers a significant advantage, such as a fast-paced environment, might be a disadvantage for another who prefers a more predictable routine. Similarly, the demands and rewards of this role can shift as one progresses from an early-career position to a more senior leadership role within a plant. This assessment provides an honest, balanced perspective to help individuals set realistic expectations for a career as a Plant Manager.
Pros
- Plant managers hold significant authority and autonomy in decision-making regarding production processes, resource allocation, and operational improvements, leading to a strong sense of ownership and impact.
- The role offers diverse responsibilities, encompassing production, quality control, logistics, maintenance, and human resources, providing a broad skill set and continuous learning opportunities.
- Achieving production goals and implementing successful efficiency improvements provides a high level of job satisfaction and tangible results, which can be very rewarding.
- Plant managers often earn competitive salaries and benefit packages, reflecting the critical nature of their role in a company's profitability and operational success.
- The demand for skilled plant managers remains consistent across various manufacturing sectors, offering strong job security and diverse opportunities in different industries.
- This position allows for direct leadership and mentorship of a large team, fostering strong interpersonal skills and the ability to influence and develop others' careers.
- Successful plant management experience is highly valued and can open doors to executive roles in operations, supply chain, or general management within larger corporations.
Cons
- Plant managers face high pressure to meet production targets, often leading to long hours and significant stress, especially during peak seasons or equipment malfunctions.
- The role requires constant problem-solving for unexpected operational issues, such as supply chain disruptions, machinery breakdowns, or quality control failures, which can be mentally draining.
- Plant managers are responsible for a large workforce, including managing labor relations, handling disciplinary actions, and ensuring safety compliance, which can be emotionally and legally challenging.
- The work environment can be physically demanding and noisy, requiring frequent presence on the factory floor and exposure to industrial conditions, which may not suit everyone.
- Balancing competing demands from upper management (cost reduction) and employees (better conditions) often puts plant managers in difficult, no-win situations.
- Career progression can be slower for plant managers as opportunities for advancement to higher corporate roles may be limited without additional business education or experience outside of operations.
- Plant managers must stay updated on complex regulations, including environmental, health, and safety standards, which involves continuous learning and meticulous compliance efforts to avoid penalties and ensure worker well-being and environmental protection, adding a significant administrative burden to their role and requiring specialized knowledge beyond general operational management skills, which can be a steep and ongoing learning curve for those entering the field or transitioning from other management positions, and this continuous need for regulatory knowledge makes the job inherently demanding, requiring a commitment to lifelong learning and meticulous attention to detail, which can be a source of stress and a significant time investment.
Frequently Asked Questions
Plant Managers face distinct challenges balancing operational efficiency, team leadership, and strategic planning. This section addresses the most common questions about transitioning into this demanding role, from required experience and work-life balance to salary expectations and long-term career growth.
What educational background and experience do I need to become a Plant Manager?
Most Plant Manager roles require a bachelor's degree in engineering, business administration, or a related field, often coupled with 5-10 years of progressive experience in manufacturing operations. Many successful Plant Managers also hold an MBA or certifications in Lean Six Sigma, which are highly valued. Demonstrated leadership and problem-solving skills are critical.
How long does it typically take to advance into a Plant Manager role?
The timeline varies significantly based on your current experience. If you are starting in a supervisory role, it might take 5-10 years to gain the necessary operational and leadership experience for a Plant Manager position. Accelerating your career involves actively seeking leadership opportunities, pursuing advanced education, and demonstrating consistent results in production efficiency and team management.
What are the typical salary expectations for a Plant Manager?
Plant Managers typically earn between $90,000 and $180,000 annually, depending on the industry, company size, location, and complexity of the plant. Larger plants or those in specialized industries often offer higher compensation. Bonuses tied to operational performance and production targets are also common, significantly impacting total earnings.
What is the typical work-life balance like for a Plant Manager?
The work-life balance for a Plant Manager can be demanding, often requiring long hours, especially during production issues, equipment breakdowns, or audits. It is not a 9-to-5 job; flexibility and responsiveness to plant needs are essential. However, effective delegation and strong team leadership can help manage the workload and reduce constant personal presence.
Is the Plant Manager role in high demand, and is it a secure career path?
The demand for skilled Plant Managers remains strong across various manufacturing sectors. Companies consistently need experienced leaders to optimize production, manage complex operations, and ensure quality and safety. While specific industries may fluctuate, the core skillset of a Plant Manager is generally resilient to economic downturns, making it a stable career path.
What are the typical career advancement opportunities for a Plant Manager?
Career growth for a Plant Manager can lead to multi-plant management, regional operations director, or even Vice President of Manufacturing roles. Opportunities also exist to transition into corporate roles focusing on supply chain management, process improvement, or strategic operations. Continuous learning in areas like automation, supply chain optimization, and leadership development supports this progression.
What are the biggest day-to-day challenges a Plant Manager faces?
A significant challenge is balancing immediate production demands with long-term strategic initiatives like continuous improvement or new technology implementation. Managing diverse teams, ensuring safety compliance, and adapting to market changes also present daily challenges. Effective Plant Managers excel at problem-solving under pressure and fostering a collaborative environment.
Can a Plant Manager role be done remotely, or does it require on-site presence?
While some corporate aspects of the role might be performed remotely, a Plant Manager's core responsibilities require a consistent physical presence on the factory floor. Direct oversight of production, team leadership, quality control, and safety protocols necessitate being on-site. Therefore, this role offers very limited remote work flexibility.
Related Careers
Explore similar roles that might align with your interests and skills:
Manufacturing Manager
A growing field with similar skill requirements and career progression opportunities.
Explore career guideManufacturing Operations Manager
A growing field with similar skill requirements and career progression opportunities.
Explore career guidePlant Supervisor
A growing field with similar skill requirements and career progression opportunities.
Explore career guidePlant Chief
A growing field with similar skill requirements and career progression opportunities.
Explore career guidePlant Superintendent
A growing field with similar skill requirements and career progression opportunities.
Explore career guideAssess your Plant Manager readiness
Understanding where you stand today is the first step toward your career goals. Our Career Coach helps identify skill gaps and create personalized plans.
Skills Gap Analysis
Get a detailed assessment of your current skills versus Plant Manager requirements. Our AI Career Coach identifies specific areas for improvement with personalized recommendations.
See your skills gapCareer Readiness Assessment
Evaluate your overall readiness for Plant Manager roles with our AI Career Coach. Receive personalized recommendations for education, projects, and experience to boost your competitiveness.
Assess your readinessSimple pricing, powerful features
Upgrade to Himalayas Plus and turbocharge your job search.
Himalayas
Himalayas Plus
Himalayas Max
Find your dream job
Sign up now and join over 100,000 remote workers who receive personalized job alerts, curated job matches, and more for free!
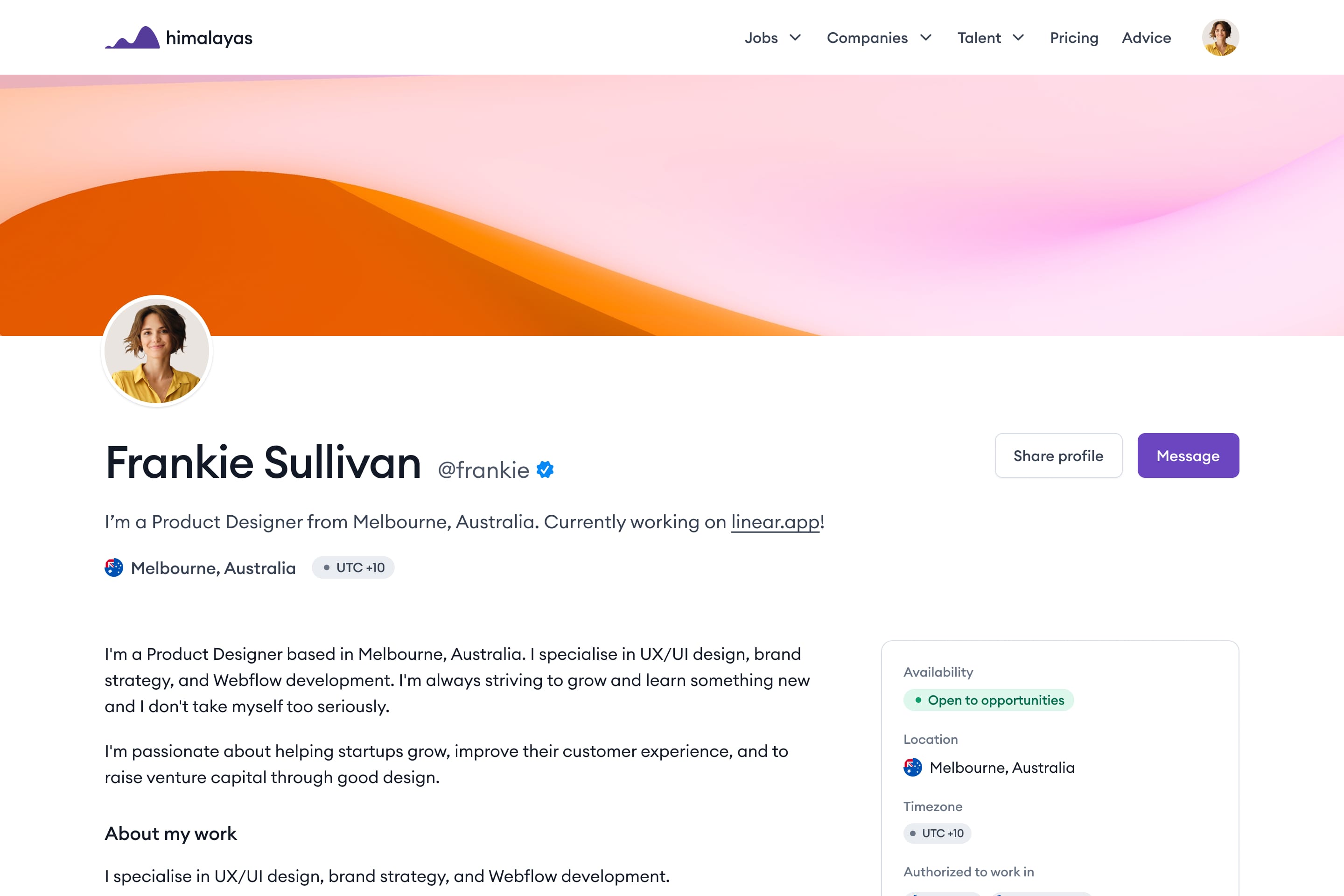