Complete Pipe Welder Career Guide
Pipe welders are the backbone of essential infrastructure, meticulously joining pipes for everything from water treatment plants to oil pipelines and HVAC systems. This specialized trade demands precision, skill, and a deep understanding of materials, offering a hands-on career with direct impact on critical systems. You'll solve complex structural challenges, ensuring the safe and efficient flow of vital resources, and be rewarded with strong earning potential.
Key Facts & Statistics
Median Salary
$48,720 USD
(U.S. Bureau of Labor Statistics, May 2023)
Range: $35k - $80k+ USD (varies by experience, specialization, and location)
Growth Outlook
2%
as fast as average (U.S. Bureau of Labor Statistics, 2022-2032)
Annual Openings
≈48,700
openings annually (U.S. Bureau of Labor Statistics, 2022-2032)
Top Industries
Typical Education
High school diploma or equivalent, plus completion of a vocational program or apprenticeship. Certifications (e.g., AWS) are highly valued.
What is a Pipe Welder?
A pipe welder is a skilled tradesperson specializing in the precise joining of pipes and tubing systems through various welding processes. This role is distinct from a general welder, as it requires specific expertise in the unique challenges of pipe welding, such as working with different pipe schedules, materials (carbon steel, stainless steel, alloys), and complex joint configurations that demand high integrity and leak-proof seals.
Pipe welders are crucial for constructing and maintaining infrastructure that transports liquids, gases, and other substances, including pipelines, chemical plants, power generation facilities, and HVAC systems. Their work ensures the safe and efficient flow of materials, preventing costly leaks and structural failures, making them indispensable to industries where fluid transport is critical.
What does a Pipe Welder do?
Key Responsibilities
- Prepare pipes for welding by cleaning, beveling, and aligning sections according to blueprints and specifications.
- Select and set up appropriate welding equipment, including arc welders, TIG welders, and MIG welders, adjusting settings for different pipe materials and thicknesses.
- Perform various welding techniques, such as shielded metal arc welding (SMAW), gas tungsten arc welding (GTAW), and gas metal arc welding (GMAW), to join pipe sections securely.
- Inspect completed welds for structural integrity, visual defects, and adherence to quality standards, often using visual inspection or non-destructive testing methods.
- Operate pipe cutting and bending machines, grinders, and other power tools to fabricate and modify pipe systems as needed.
- Adhere strictly to safety protocols, including wearing personal protective equipment and ensuring proper ventilation in confined spaces.
- Read and interpret complex isometric drawings, blueprints, and welding procedure specifications (WPS) to understand pipe routing and joint configurations.
Work Environment
Pipe welders typically work in demanding environments, which can include construction sites, industrial plants, shipyards, and manufacturing facilities. Work often involves physical labor, working in confined spaces, at heights, or in varying weather conditions. The pace of work can be fast, especially during critical project phases, requiring strong focus and attention to detail.
Collaboration with other trades, such as pipefitters, ironworkers, and engineers, is common. While some shops offer controlled environments, many projects are outdoors or in active industrial settings. Work schedules can involve standard daytime hours, but project deadlines may necessitate overtime, evening shifts, or weekend work. Travel to different job sites is a frequent requirement.
Tools & Technologies
Pipe welders use a specialized array of equipment and tools to perform their work. Core welding equipment includes arc welders (SMAW), TIG welders (GTAW), and MIG welders (GMAW), each chosen for specific pipe materials and joint requirements. They also operate plasma cutters, oxy-fuel torches, and pipe beveling machines for preparing pipe ends.
Measurement tools like calipers, micrometers, and levels ensure precise fit-up and alignment. Hand tools such as grinders, wire brushes, and pipe wrenches are essential for preparation and finishing. Welders also rely on personal protective equipment (PPE) like welding helmets, gloves, and fire-resistant clothing. Increasingly, digital welding machines offer advanced controls and data logging capabilities.
Pipe Welder Skills & Qualifications
A Pipe Welder's qualification landscape emphasizes practical, hands-on expertise over extensive formal academic degrees. Employers prioritize demonstrated welding proficiency, adherence to safety standards, and specific certifications for pipe welding processes. Entry-level positions typically require vocational training or an apprenticeship, while senior roles demand extensive experience and specialized certifications for critical applications like high-pressure systems or exotic materials.
Requirements vary significantly by industry sector. The oil and gas industry, for instance, mandates stringent certifications and often specialized experience with materials like stainless steel or chrome-moly. Commercial construction might focus on different codes and faster project turnaround times, while shipbuilding requires specific marine welding certifications. Geographic location also plays a role; some regions or states have specific licensing boards or industry associations that set local standards. Practical experience consistently holds more weight than a bachelor's degree in this trade.
Certifications from organizations like the American Welding Society (AWS) or ASME (American Society of Mechanical Engineers) are crucial for Pipe Welders. These credentials validate a welder's ability to perform specific types of welds to industry standards. While formal education like an associate's degree can provide a strong theoretical foundation, a robust portfolio of successful welds and relevant certifications often opens more doors. The skill landscape is evolving with new welding technologies and materials, requiring continuous learning and re-certification to maintain relevance.
Education Requirements
Technical Skills
- Shielded Metal Arc Welding (SMAW) - Stick Welding, especially for various pipe schedules and diameters
- Gas Tungsten Arc Welding (GTAW) - TIG Welding, particularly for stainless steel, exotic alloys, and root passes requiring high precision
- Flux-Cored Arc Welding (FCAW) - for high deposition rates on thicker pipes and outdoor conditions
- Oxy-Acetylene Cutting and Brazing for pipe preparation and minor repairs
- Blueprint Reading and Isometric Drawings interpretation for pipe routing, dimensions, and specifications
- Pipe Fitting and Fabrication techniques, including measuring, cutting, beveling, and aligning pipe sections
- Knowledge of Welding Codes and Standards (e.g., AWS D1.1, ASME Section IX, API 1104) specific to pipe welding applications
- Material Science knowledge related to various pipe metals (carbon steel, stainless steel, alloys) and their weldability
- Use and maintenance of welding equipment, including power sources, torches, electrodes, and safety gear
- Non-Destructive Testing (NDT) awareness, understanding common inspection methods like visual inspection, X-ray, and ultrasonic testing
Soft Skills
- Attention to Detail: Pipe welding demands extreme precision; even minor flaws can lead to leaks or structural failure, which is critical for safety and system integrity.
- Problem-Solving: Welders often encounter unexpected material conditions, access limitations, or alignment issues, requiring quick and effective solutions to maintain project schedules and quality.
- Physical Stamina & Dexterity: The role involves prolonged standing, kneeling, and working in awkward positions, along with fine motor control for intricate welding tasks.
- Safety Consciousness: Working with high temperatures, heavy materials, and hazardous gases requires strict adherence to safety protocols to prevent accidents and injuries.
- Adaptability: Pipe Welders must adjust to varying pipe materials, diameters, welding positions (e.g., overhead, vertical), and environmental conditions, requiring quick learning and flexibility.
- Team Collaboration: Many projects involve working closely with fitters, pipefitters, and other trades, necessitating effective communication and coordination to ensure accurate pipe alignment and installation.
How to Become a Pipe Welder
Becoming a pipe welder involves a blend of technical skill and practical experience. While some enter through formal apprenticeships, others begin with vocational training and gain on-the-job experience. The timeline to becoming proficient varies; a dedicated individual might secure an entry-level position within 6-12 months after completing a trade school program, while an apprenticeship could take 3-5 years to reach journeyman status.
Entry routes often depend on the specific industry sector. For instance, union jobs in construction or energy typically favor structured apprenticeships, which provide comprehensive training and guaranteed work hours. Non-union shops or smaller fabrication companies might be more open to candidates with a vocational certificate and a strong desire to learn, even if they lack extensive experience. Geographic location also plays a role, with industrial hubs offering more opportunities and potentially higher demand for skilled welders.
A common misconception is that a pipe welder only needs to know how to weld. In reality, precision, blueprint reading, safety protocols, and knowledge of various metals and welding processes are equally crucial. Building a strong portfolio of weld samples and demonstrating a commitment to continuous learning are vital for overcoming entry barriers and proving your capabilities to potential employers, regardless of your starting point.
Step 1
Step 2
Step 3
Step 4
Step 5
Step 6
Step 7
Education & Training Needed to Become a Pipe Welder
Becoming a successful Pipe Welder requires a blend of theoretical knowledge and extensive practical skills. Formal education options range from vocational school programs and community college associate degrees to specialized welding certifications. Vocational programs and community college degrees typically take 9-24 months and cost between $5,000 and $20,000, focusing heavily on hands-on training and various welding processes. These programs often include pipe-specific modules and prepare students for industry certifications.
Alternative pathways include apprenticeships, which combine paid on-the-job training with classroom instruction, lasting 3-5 years. Apprenticeships are often free or low-cost to the apprentice, as employers or unions cover training expenses, and they provide immediate work experience. Some welders also learn through self-study and on-the-job mentorship, though this path often takes longer and requires strong self-discipline. Employers highly value accredited certifications like those from the American Welding Society (AWS), which demonstrate proficiency in specific welding codes and procedures. These certifications are crucial for employment and typically cost $150-$500 per test, requiring prior training or experience.
The market perception for Pipe Welders heavily favors practical experience alongside certifications. While a degree can provide a strong foundation, employers prioritize demonstrable skill in various pipe welding techniques, such as TIG, MIG, and Stick welding on different materials and pipe schedules. Continuous learning is essential, as new materials, technologies, and safety standards emerge. Specialized training in areas like orbital welding or specific industry codes (e.g., ASME, API) can significantly enhance career prospects and earning potential. The cost-benefit analysis generally favors programs that offer extensive hands-on practice and lead directly to industry-recognized certifications, as these provide the most direct route to employment and career advancement in pipe welding.
Pipe Welder Salary & Outlook
Compensation for a Pipe Welder is influenced by several key factors. Geographic location significantly impacts earnings, with areas experiencing high industrial activity or a higher cost of living, such as the Gulf Coast states or major metropolitan areas, typically offering higher wages. Conversely, regions with lower demand or cost of living may see more modest compensation.
Years of experience and specialized certifications play a crucial role in salary progression. Welders with advanced skills in specific materials or welding processes, like TIG or orbital welding for critical applications, command premium rates. Total compensation often extends beyond base hourly pay, including overtime opportunities, per diem for travel, project completion bonuses, and comprehensive benefits packages covering health insurance, retirement plans, and sometimes tool allowances.
Industry-specific demands also drive salary growth; pipe welders in oil and gas, petrochemical, or power generation sectors often earn more due to the complexity and criticality of the work. Union membership can also influence pay scales and benefits. Negotiating leverage comes from proven expertise, a clean safety record, and the ability to work on specialized projects. While most pipe welding roles are on-site, some specialized fabrication roles might offer different compensation structures. International markets vary widely, but the figures provided here are in USD, reflecting the U.S. labor market.
Salary by Experience Level
Level | US Median | US Average |
---|---|---|
Apprentice Pipe Welder | $32k USD | $35k USD |
Junior Pipe Welder | $45k USD | $48k USD |
Pipe Welder | $62k USD | $65k USD |
Senior Pipe Welder | $78k USD | $80k USD |
Lead Pipe Welder | $92k USD | $95k USD |
Pipe Welding Supervisor | $105k USD | $110k USD |
Market Commentary
The job market for Pipe Welders remains robust, driven by ongoing infrastructure development, maintenance of existing industrial facilities, and new energy projects. Demand is particularly strong in the oil and gas sector, power generation (including renewable energy infrastructure), and manufacturing. Projections indicate a stable to slightly growing demand for skilled welders, with a particular need for those proficient in advanced pipe welding techniques. The Bureau of Labor Statistics projects employment for welders, cutters, solderers, and brazers to grow 2% from 2022 to 2032, which is slower than the average for all occupations, but specific demand for specialized pipe welders often outpaces this general trend.
Emerging opportunities include work on liquefied natural gas (LNG) terminals, hydrogen pipelines, and carbon capture infrastructure. The supply of highly skilled pipe welders often struggles to meet demand, creating favorable conditions for experienced professionals. Automation and AI are impacting some manufacturing welding, but the intricate, on-site, and often custom nature of pipe welding ensures a continued need for human expertise, particularly for complex joints and repairs. This profession is relatively recession-resistant due to the continuous need for infrastructure maintenance and upgrades. Geographic hotspots for pipe welding include Texas, Louisiana, Oklahoma, and the Pacific Northwest, with remote project work also common.
Pipe Welder Career Path
Career progression for a Pipe Welder involves a structured path from foundational learning to specialized expertise and leadership. This field typically offers distinct pathways: remaining an individual contributor (IC) who masters advanced welding techniques, or transitioning into a management/leadership track overseeing welding operations and teams.
Advancement speed depends on several factors, including consistent high-quality work, acquiring specialized certifications (e.g., specific pipe materials, pressure vessel codes), and demonstrating strong problem-solving abilities. Company size and industry also play a role; large industrial projects or specialized fabrication shops may offer more rapid advancement opportunities than smaller general construction firms. Lateral movement might involve specializing in exotic materials, automated welding, or moving into related fields like quality inspection or welding instruction.
Networking within professional associations, seeking mentorship from experienced welders, and maintaining a strong reputation for reliability and skill are crucial for advancement. Continuous learning through advanced training programs and adapting to new welding technologies or safety standards also marks significant progression. Common career pivots include becoming a welding inspector, a welding instructor, or an independent welding consultant for specialized projects.
Apprentice Pipe Welder
0-2 yearsKey Focus Areas
Junior Pipe Welder
2-4 years total experienceKey Focus Areas
Pipe Welder
4-7 years total experienceKey Focus Areas
Senior Pipe Welder
7-12 years total experienceKey Focus Areas
Lead Pipe Welder
10-15 years total experienceKey Focus Areas
Pipe Welding Supervisor
15+ years total experienceKey Focus Areas
Apprentice Pipe Welder
0-2 yearsWorks under direct supervision, assisting experienced welders and performing basic welding tasks. Focuses on preparation, fitting, and simple welds on non-critical pipes. Responsibilities include material handling, cleaning, and grinding. Decisions are limited to immediate task execution as instructed.
Key Focus Areas
Develop foundational welding skills and safety protocols. Understand different pipe materials and basic joint configurations. Focus on consistency in basic welding processes like SMAW or GTAW. Learn to interpret blueprints and welding symbols. Practice proper equipment setup and maintenance.
Junior Pipe Welder
2-4 years total experiencePerforms routine pipe welding tasks with moderate supervision. Handles various pipe sizes and materials under standard conditions. Responsible for producing code-compliant welds on non-critical and semi-critical piping systems. Collaborates with fitters and other trades to ensure proper alignment and joint preparation.
Key Focus Areas
Master common welding processes and pipe positions. Improve speed and efficiency while maintaining weld quality. Begin to understand stress relief and distortion control. Develop problem-solving skills for minor fit-up issues. Seek out opportunities to work on more complex pipe systems.
Pipe Welder
4-7 years total experienceIndependently performs complex pipe welding on critical and non-critical systems, often in challenging positions or environments. Responsible for ensuring welds meet stringent code requirements and specifications. Makes independent decisions on welding parameters and techniques. May provide guidance to junior welders.
Key Focus Areas
Achieve mastery in multiple welding processes (e.g., GTAW, SMAW, FCAW) across various pipe materials and positions. Acquire specialized certifications (e.g., 6G, specific alloys). Develop strong diagnostic skills for weld defects and their prevention. Understand advanced metallurgy and heat treatment.
Senior Pipe Welder
7-12 years total experienceHandles the most challenging and critical pipe welding assignments, often involving high-pressure, high-temperature, or specialized alloy systems. Provides technical guidance and expertise to other welders. Responsible for maintaining exceptionally high quality and efficiency standards. Involved in pre-fabrication and complex field installations.
Key Focus Areas
Specialize in advanced welding techniques, exotic materials (e.g., stainless steel, chrome-moly, Inconel), or specific industry codes (e.g., ASME, API). Develop expertise in troubleshooting difficult welding challenges. Mentor and train junior welders. Contribute to process improvement and quality control initiatives.
Lead Pipe Welder
10-15 years total experienceActs as the primary technical lead for a team of welders on specific projects or sections. Oversees daily welding operations, ensuring adherence to blueprints, schedules, and quality standards. Assigns tasks, monitors progress, and resolves technical issues. Provides on-the-job training and quality checks for the team.
Key Focus Areas
Develop strong leadership and communication skills. Focus on project planning, scheduling, and resource allocation for welding tasks. Understand project specifications and client requirements deeply. Improve ability to manage team dynamics and maintain a high-performing work environment.
Pipe Welding Supervisor
15+ years total experienceManages all welding activities across multiple projects or within a large fabrication shop. Responsible for overall project success related to welding, including safety, quality, budget, and schedule. Leads a team of lead welders and pipe welders. Interfaces directly with project managers, clients, and regulatory bodies. Develops and implements welding procedures.
Key Focus Areas
Cultivate advanced leadership, project management, and administrative skills. Focus on budgeting, safety compliance, and human resources management (e.g., hiring, performance reviews). Develop strategic thinking for long-term project planning and operational efficiency. Build strong client and stakeholder relationships.
Job Application Toolkit
Ace your application with our purpose-built resources:
Global Pipe Welder Opportunities
Pipe welders find strong global demand, particularly in energy, construction, and manufacturing sectors. This profession translates consistently across countries, focusing on joining pipes for various systems. Global market trends for 2025 show continued need for skilled welders in infrastructure projects and industrial maintenance. Cultural differences mostly affect safety standards and work-site etiquette. International opportunities offer diverse projects and skill development. International certifications like AWS CWI or EWF/IIW diplomas enhance global mobility.
Global Salaries
Pipe welder salaries vary significantly by region and experience. In North America, a pipe welder can expect to earn between $60,000 and $90,000 USD annually in the United States, and CAD 55,000 to CAD 85,000 in Canada. These figures often include robust benefits like health insurance and retirement plans. Europe presents a broader range: Germany offers EUR 40,000-60,000 (approx. $43,000-$65,000 USD), while Scandinavian countries like Norway can reach NOK 450,000-650,000 (approx. $42,000-$60,000 USD). These European salaries often include comprehensive public healthcare and generous vacation time.
Asia-Pacific markets, such as Australia, see salaries from AUD 70,000-100,000 (approx. $46,000-$66,000 USD), reflecting a high cost of living. In the Middle East, particularly countries like Saudi Arabia or UAE, salaries can range from AED 100,000-180,000 (approx. $27,000-$49,000 USD), often with tax-free income and housing allowances, which significantly boosts purchasing power. Latin American countries like Brazil might offer BRL 40,000-70,000 (approx. $8,000-$14,000 USD), where the lower nominal wage still provides reasonable purchasing power due to lower living costs.
Experience and specialized certifications, such as TIG or orbital welding, directly impact compensation globally. Tax implications differ greatly; for example, Nordic countries have higher income taxes but strong social welfare benefits. Understanding take-home pay requires considering local taxes, social security contributions, and the value of non-cash benefits. International pay scales are not standardized, but specific project-based rates can often be higher for skilled welders on short-term contracts.
Remote Work
Pipe welding is a hands-on trade, making traditional remote work largely impractical. The core tasks require physical presence on-site. However, some aspects of the profession can involve remote elements. These include project planning, blueprint review, material estimation, and quality control documentation.
Digital nomad opportunities are not typical for active pipe welding. Some highly experienced pipe welding consultants or instructors may offer remote training or advisory services. Companies hiring internationally for welding roles primarily seek on-site workers. Salary expectations for these limited remote roles would reflect the consultancy or instructional nature, not hands-on welding. Equipment and internet requirements for remote tasks are standard for office work, but the physical welding work demands specialized tools and a dedicated, safe workspace.
Visa & Immigration
Pipe welders commonly use skilled worker visas in many countries. Popular destinations include Canada (e.g., Express Entry), Australia (e.g., Skilled Nominated Visa Subclass 190), Germany (Skilled Immigration Act), and the UK (Skilled Worker Visa). Each country has specific requirements, often including an employer sponsor. Education credential recognition involves assessing welding certifications and diplomas from the home country. Professional licensing or trade qualification assessments are often mandatory. For instance, Canada requires a Red Seal endorsement for inter-provincial mobility.
Typical visa timelines range from a few months to over a year, depending on the country and application backlog. Pathways to permanent residency exist in countries like Canada and Australia after a few years of skilled work. Language requirements, such as English (IELTS) or German (Goethe-Zertifikat), are common for skilled worker visas. Some countries, particularly those with labor shortages in trades, may offer streamlined processing for qualified welders. Practical considerations include proving sufficient funds for relocation and understanding dependent visa options for family members.
2025 Market Reality for Pipe Welders
Understanding the current market realities for pipe welders is crucial for strategic career planning. This field has seen shifts over recent years, influenced by post-pandemic infrastructure pushes and evolving energy sector demands. Broader economic factors, such as industrial growth and investment in utilities, directly shape job availability.
Market conditions for pipe welders vary significantly by experience level, with journeymen and master welders facing different landscapes than apprentices. Geographic location, especially proximity to major industrial or energy hubs, also dictates opportunities, as does the size and specialization of contracting companies. This analysis provides an honest assessment of current hiring conditions and future prospects.
Current Challenges
Pipe welders face significant competition, especially for entry-level roles, as many seek to enter skilled trades. Economic slowdowns can delay or cancel large construction projects, directly impacting demand for their specialized skills. Maintaining up-to-date certifications for various materials and techniques remains crucial, as outdated credentials limit opportunities.
Growth Opportunities
Despite challenges, strong demand persists for pipe welders in several sectors. Infrastructure repair and upgrades, particularly in water treatment, oil and gas pipelines, and power generation, offer consistent work. Emerging opportunities exist in renewable energy projects, such as geothermal and hydrogen infrastructure, which require specialized piping systems.
Welders who specialize in exotic materials like titanium, stainless steel, or chrome-moly, or those proficient in advanced techniques like orbital welding and TIG welding for critical applications, find themselves in high demand. Obtaining certifications for these niche areas provides a significant competitive edge. Underserved markets often include remote industrial sites or specialized fabrication shops requiring immediate, highly skilled labor.
Strategic career moves involve targeting industries undergoing expansion or modernization, rather than just routine maintenance. Investing in continuous training for new welding codes or automated welding equipment integration can open doors to supervisory or quality assurance roles. Opportunities also arise from the retirement of experienced welders, creating a need for skilled replacements in critical industries.
Current Market Trends
The demand for pipe welders remains steady in 2025, driven by infrastructure projects, energy sector maintenance, and industrial construction. While some automation impacts general welding, the precision and on-site adaptability required for complex pipe systems largely protect this specific role from immediate displacement. Economic conditions, particularly interest rates affecting new construction, influence project timelines.
Generative AI and automation tools primarily assist in design, planning, and quality control, not the physical act of pipe welding itself. This means human expertise in intricate, multi-pass welds and diverse material handling remains indispensable. Employers increasingly seek welders with advanced certifications in specialized alloys and techniques like orbital welding, reflecting a shift towards higher-value, more complex projects.
Salary trends show modest growth, especially for highly skilled and certified pipe welders capable of working in challenging environments like offshore platforms or nuclear facilities. Market saturation exists at basic levels, but a shortage of master pipe welders persists. Geographic variations are significant; strong demand concentrates in regions with active oil and gas extraction, power generation, or large-scale manufacturing, while remote work is generally not feasible for this hands-on profession. Project-based hiring often creates cyclical demand throughout the year.
Emerging Specializations
The field of pipe welding is experiencing a transformative shift, driven by advancements in materials, automation, and infrastructure demands. Understanding these evolving trends is crucial for pipe welders aiming to secure future-proof careers. New specialization opportunities are continually emerging, often at the intersection of traditional welding skills and innovative technologies.
Positioning oneself early in these emerging areas provides a significant advantage, potentially leading to premium compensation and accelerated career growth by 2025 and beyond. While established specializations remain vital, exploring cutting-edge niches allows professionals to become indispensable assets in next-generation projects. These emerging areas often command higher wages due to specialized knowledge and fewer skilled practitioners.
Emerging specializations typically take several years to become mainstream and generate a substantial volume of job opportunities. Early adopters, however, gain invaluable experience and a competitive edge as the market matures. Pursuing these cutting-edge paths involves a strategic balance between risk and reward. While some areas may evolve slower than anticipated, the potential for high demand and leadership roles in a rapidly changing industry is substantial for those who invest in relevant skill development.
Advanced Material Pipe Welder
As advanced materials like duplex stainless steels, nickel alloys, and titanium become more prevalent in critical applications such as chemical processing, aerospace, and energy, demand for pipe welders proficient in these materials is rising. These materials require precise welding techniques and specialized knowledge to maintain their unique properties and ensure structural integrity. Mastery of these materials allows welders to work on high-value, complex projects.
Robotic Pipe Welding Technician
The integration of robotics and automation in welding processes is expanding, particularly for repetitive or hazardous tasks. Pipe welders specializing in robotic welding are not just operators; they program, calibrate, and troubleshoot automated welding systems, ensuring optimal performance and weld quality. This specialization combines hands-on welding expertise with programming and diagnostic skills, streamlining production and enhancing safety.
Renewable Energy Pipeline Welder
With increasing focus on sustainable energy and infrastructure, the demand for pipe welders in renewable energy sectors like offshore wind, geothermal, and hydrogen pipelines is growing. These projects often involve unique materials, extreme environmental conditions, and stringent quality requirements. Welders in this field contribute directly to green initiatives, building the infrastructure for a carbon-neutral future.
Additive Manufacturing Pipe Welder
The use of additive manufacturing, particularly for complex pipe geometries or repairs, is an emerging area. Pipe welders specializing in this technique work with metal 3D printers or directed energy deposition (DED) systems to create or repair components layer by layer. This requires a strong understanding of material science and precision control beyond traditional arc welding, opening doors to highly customized fabrication.
Pipeline Integrity & Repair Welder
The oil and gas industry is increasingly focused on integrity management and life extension for existing pipelines. This creates a demand for pipe welders specialized in advanced repair techniques, such as hot tapping, pipeline rehabilitation, and composite wrap applications. These techniques require specialized certifications and a deep understanding of pipeline operational safety, often performed under challenging live conditions to minimize downtime.
Pros & Cons of Being a Pipe Welder
Choosing a career path involves understanding both the rewarding aspects and the inherent difficulties. This is especially true for specialized roles like a Pipe Welder, where daily experiences can differ significantly from general welding or other trades. Career satisfaction and challenges vary based on the specific industry, company culture, project demands, and an individual's personal resilience and preferences. What one person considers a significant advantage, another might see as a minor inconvenience or even a challenge. Moreover, the nature of pros and cons can evolve as a career progresses, from entry-level positions to more experienced or supervisory roles. This assessment aims to provide a realistic, balanced view to help set appropriate expectations for aspiring pipe welders.
Pros
Pipe welders are highly specialized and in constant demand across diverse industries like oil and gas, manufacturing, and construction, ensuring strong job security.
The skill set commands a high earning potential, with experienced and certified pipe welders often receiving excellent wages and benefits, especially for specialized projects.
There is a significant sense of accomplishment from creating critical infrastructure; pipe welders see tangible results of their precise work in essential systems and structures.
Opportunities for travel are abundant, as major projects often require skilled welders to relocate or travel to various sites, offering diverse experiences and higher pay.
Mastering complex pipe welding techniques provides continuous intellectual stimulation and a deep sense of craftsmanship, as each joint presents a unique challenge.
Clear pathways for career advancement exist, allowing pipe welders to move into supervisory roles, quality control, inspection, or even start their own contracting businesses.
Many roles offer overtime opportunities, allowing dedicated individuals to significantly boost their income, particularly during critical project phases or tight deadlines.
Cons
Pipe welders often work in physically demanding and uncomfortable positions, requiring significant kneeling, bending, and overhead work for extended periods.
Exposure to hazardous conditions is common, including intense heat, sparks, fumes, and loud noises, which necessitates strict adherence to safety protocols and personal protective equipment.
The work environment can be unstable, with projects often located in remote areas or requiring extensive travel and time away from home for weeks or months.
Weld quality is critical and highly scrutinized; even minor imperfections can lead to costly reworks or structural failures, creating constant pressure to maintain high standards.
The job is seasonal or project-based for many, leading to potential periods of unemployment between contracts, especially in construction or oil and gas sectors.
Continuous learning and certification renewal are necessary to stay current with new welding techniques, materials, and safety regulations, requiring ongoing investment of time and resources.
There is a risk of long-term health issues from prolonged exposure to fumes and UV radiation, such as respiratory problems or vision damage, even with proper ventilation and protective gear.
Frequently Asked Questions
Pipe Welders face distinct challenges around specialized skill acquisition, physically demanding work, and safety. This section addresses the most common questions about entering this trade, from mastering specific welding techniques to understanding job site realities and career progression in a skilled craft.
How long does it take to become a certified Pipe Welder if I'm starting without experience?
Becoming a proficient Pipe Welder typically requires completing a trade school program or an apprenticeship, which can take between 6 months to 5 years. Trade schools offer focused training for 6-24 months, providing foundational skills. Apprenticeships offer hands-on experience and classroom instruction over 3-5 years, leading to journeyman status. The timeline depends on the intensity of the program and the individual's learning pace.
Do I need a college degree to become a Pipe Welder, or are there alternative paths?
No, a college degree is not a prerequisite for becoming a Pipe Welder. Most enter the field through vocational training, community college welding programs, or union apprenticeships. Employers value practical skills, certifications (like AWS certifications), and on-the-job experience far more than academic degrees. Demonstrating proficiency in various welding processes and adhering to safety standards is key.
What are the typical salary expectations for an entry-level Pipe Welder versus an experienced one?
Entry-level Pipe Welders can expect to earn a competitive hourly wage, often starting around $20-$25 per hour, but this varies significantly by region, industry, and project complexity. Experienced and certified Pipe Welders, especially those working on specialized projects like pipelines or power plants, can earn $35-$50+ per hour, with overtime opportunities significantly increasing annual income. Union membership can also impact pay scales.
What is the work-life balance like for a Pipe Welder, considering the physical demands and potential travel?
Pipe Welding is a physically demanding job that often involves working in various environments, including confined spaces, heights, and outdoors in all weather conditions. The work requires significant physical stamina, strength for lifting and maneuvering equipment, and precision in challenging positions. It is crucial to be prepared for a hands-on, often rigorous work environment that prioritizes safety.
Is there strong job security and market demand for Pipe Welders in the coming years?
The demand for skilled Pipe Welders remains strong and is projected to grow. Infrastructure projects, energy sector expansion, and maintenance of existing pipelines create consistent job opportunities. While some projects are seasonal or require travel, the specialized nature of pipe welding ensures a steady need for qualified professionals across various industries, including construction, oil and gas, and manufacturing.
What are the opportunities for career advancement and specialization as a Pipe Welder?
Career growth for Pipe Welders can involve specializing in advanced welding techniques (e.g., TIG, orbital welding), becoming a certified welding inspector (CWI), or moving into supervisory roles like a welding foreman or project manager. Many also transition into teaching at trade schools or opening their own welding businesses. Continuous learning and obtaining new certifications are crucial for advancement.
What are the biggest safety concerns for Pipe Welders, and how are they managed?
Safety is paramount in pipe welding due to exposure to fumes, intense light, heat, and heavy equipment. Welders must strictly follow safety protocols, including wearing personal protective equipment (PPE) like helmets, gloves, and fire-resistant clothing. Employers provide training on safe practices and equipment use. Adhering to these guidelines minimizes risks and ensures a safe working environment.
How much travel is typically involved in a Pipe Welder's career, and does it impact earnings?
While some shop-based pipe welding jobs might offer consistent local work, many significant pipe welding projects, especially in the energy sector or large infrastructure, require travel. Welders may work on-site for weeks or months, often relocating temporarily. This travel can be a major factor in the work-life balance and earning potential, as per diem and overtime pay are common.
Related Careers
Explore similar roles that might align with your interests and skills:
Pipefitter
A growing field with similar skill requirements and career progression opportunities.
Explore career guideWelder
A growing field with similar skill requirements and career progression opportunities.
Explore career guideWelding Inspector
A growing field with similar skill requirements and career progression opportunities.
Explore career guideWelder Fitter
A growing field with similar skill requirements and career progression opportunities.
Explore career guideWelding Machine Operator
A growing field with similar skill requirements and career progression opportunities.
Explore career guideAssess your Pipe Welder readiness
Understanding where you stand today is the first step toward your career goals. Our Career Coach helps identify skill gaps and create personalized plans.
Skills Gap Analysis
Get a detailed assessment of your current skills versus Pipe Welder requirements. Our AI Career Coach identifies specific areas for improvement with personalized recommendations.
See your skills gapCareer Readiness Assessment
Evaluate your overall readiness for Pipe Welder roles with our AI Career Coach. Receive personalized recommendations for education, projects, and experience to boost your competitiveness.
Assess your readinessSimple pricing, powerful features
Upgrade to Himalayas Plus and turbocharge your job search.
Himalayas
Himalayas Plus
Himalayas Max
Find your dream job
Sign up now and join over 100,000 remote workers who receive personalized job alerts, curated job matches, and more for free!
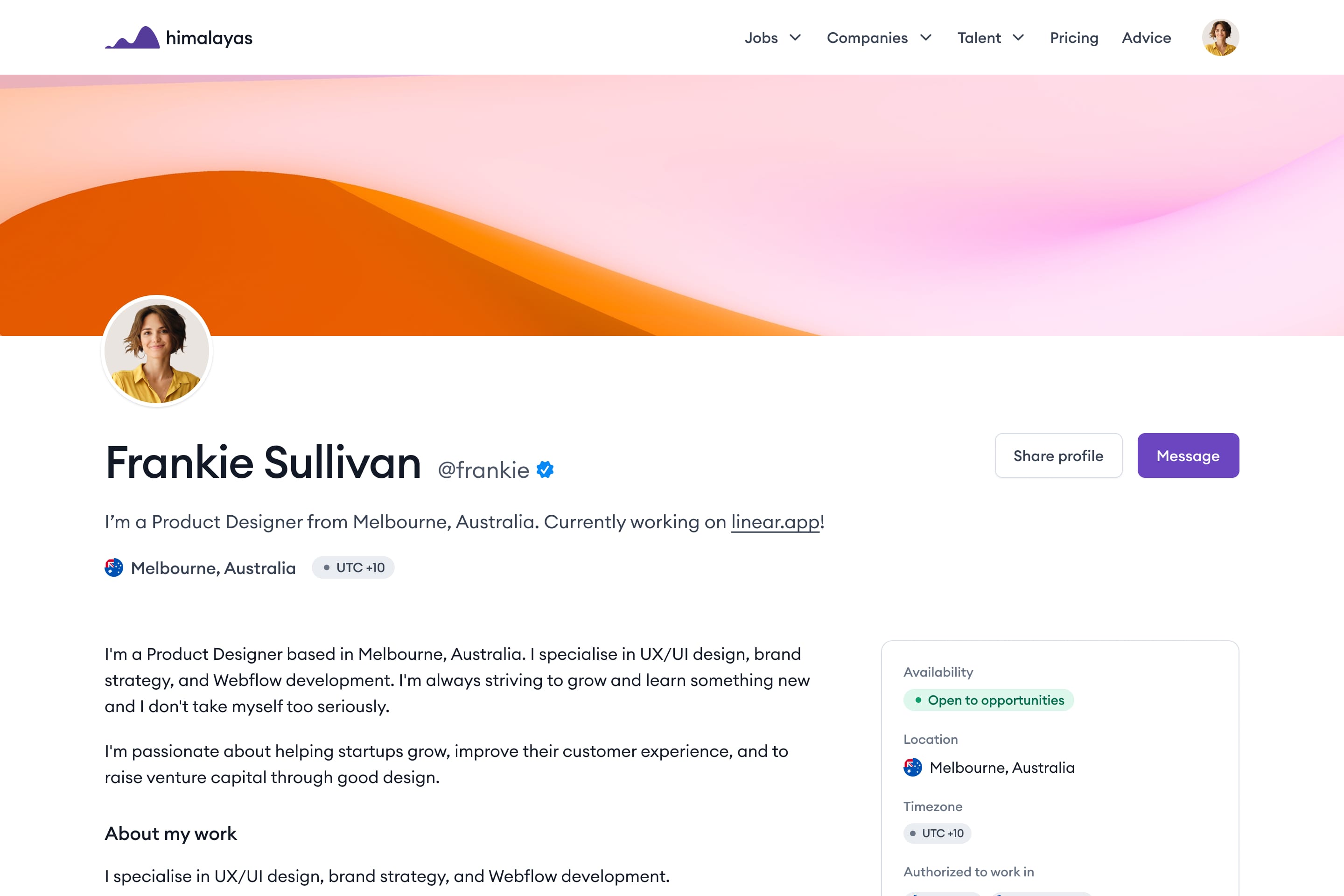