Complete Occupational Safety and Health Inspector Career Guide
Occupational Safety and Health Inspectors are crucial guardians of workplace well-being, ensuring environments are safe and compliant with regulations. They proactively identify hazards, investigate incidents, and enforce safety standards, directly preventing injuries and saving lives across diverse industries. This role combines critical thinking with a commitment to public welfare, offering a stable career path with significant impact.
Key Facts & Statistics
Median Salary
$79,280 USD
(U.S. national median, May 2023, BLS)
Range: $48k - $120k+ USD
Growth Outlook
5%
as fast as average (2022-2032)
Annual Openings
≈8,400
openings annually
Top Industries
Typical Education
Bachelor's degree in occupational health and safety, engineering, or a related scientific field; some positions may accept an associate's degree with extensive experience, or require specific certifications like CSP or CIH.
What is an Occupational Safety and Health Inspector?
An Occupational Safety and Health Inspector is a public servant responsible for enforcing government regulations related to workplace safety and health. They ensure that employers provide safe working conditions for their employees, preventing accidents, injuries, and occupational illnesses.
This role differs significantly from an internal Safety Manager or Consultant. While a Safety Manager works within a specific company to develop and implement safety programs, an Inspector acts as an external regulatory authority. They visit various workplaces, identify non-compliance with established laws (like OSHA standards in the U.S.), investigate incidents, and issue citations or penalties to compel adherence to safety regulations. They are crucial for upholding public safety standards across industries.
What does an Occupational Safety and Health Inspector do?
Key Responsibilities
- Conduct thorough on-site inspections of workplaces to identify potential safety hazards, unsafe work practices, and non-compliance with occupational safety regulations.
- Investigate workplace accidents, injuries, and fatalities to determine root causes, assess compliance failures, and recommend preventative measures.
- Prepare detailed inspection reports, documenting findings, citing violations, and outlining specific corrective actions and deadlines for employers.
- Provide technical assistance and guidance to employers and employees on best practices for hazard control, safety program development, and regulatory compliance.
- Issue citations and propose penalties for violations of occupational safety and health standards, ensuring fair and consistent enforcement.
- Follow up on previous inspections to verify that employers have implemented required corrective actions and maintained compliance standards.
- Participate in legal proceedings and enforcement actions, providing expert testimony and presenting evidence related to workplace safety investigations.
Work Environment
Occupational Safety and Health Inspectors primarily work in diverse field environments, ranging from manufacturing plants and construction sites to healthcare facilities and agricultural operations. Their work often involves exposure to various industrial settings, which can be noisy or physically demanding.
A significant portion of their time is spent conducting on-site inspections, requiring travel to different locations. They typically work independently during inspections but collaborate with legal teams, other inspectors, and agency management. The pace of work can vary from routine inspections to urgent, reactive investigations of serious incidents. While some administrative tasks occur in an office, the role demands considerable time away from a traditional desk, often involving irregular hours depending on investigation needs.
Tools & Technologies
Occupational Safety and Health Inspectors use a variety of tools to perform their duties. They rely on personal protective equipment (PPE) such as hard hats, safety glasses, and steel-toed boots for on-site visits. For documentation, they utilize digital cameras, voice recorders, and mobile devices with specialized inspection software or applications.
For analysis and reporting, inspectors work with desktop computers, laptops, and various office productivity suites like Microsoft Office (Word, Excel, PowerPoint). They frequently access and reference regulatory databases, safety standards, and legal documentation. Communication tools include email, video conferencing platforms, and agency-specific secure messaging systems.
Occupational Safety and Health Inspector Skills & Qualifications
Qualifications for an Occupational Safety and Health Inspector typically center on a blend of formal education, practical experience, and specific certifications. Entry-level positions often require a bachelor's degree in occupational health and safety or a related scientific field. As inspectors advance, practical experience conducting inspections and implementing safety protocols becomes increasingly vital. Senior roles may necessitate a master's degree or extensive specialized experience in complex industrial environments.
Requirements vary significantly by employer type. Government agencies, such as OSHA or state-level departments, often have rigid educational and experiential prerequisites, often requiring a bachelor's degree and prior inspection experience. Private sector roles, particularly in large corporations with dedicated safety departments, may prioritize certifications like the Certified Safety Professional (CSP) over a specific degree, especially for experienced hires. Smaller companies might accept a combination of relevant experience and vocational training.
Certifications play a crucial role in validating an inspector's expertise and can often compensate for a lack of a specific degree, particularly for career changers. The Certified Safety Professional (CSP) or Associate Safety Professional (ASP) certifications are highly valued across all sectors. Other specialized certifications, such as those in hazardous waste operations (HAZWOPER) or specific industry safety standards (e.g., construction safety), significantly enhance a candidate's profile. The field also evolves continuously with new regulations and technologies, requiring inspectors to engage in ongoing professional development to stay current. This ongoing learning includes understanding new machinery, chemical handling, and ergonomic principles.
Education Requirements
Technical Skills
- OSHA Regulations and Standards (29 CFR 1910 General Industry, 29 CFR 1926 Construction)
- Hazard Recognition and Risk Assessment Methodologies
- Accident Investigation and Root Cause Analysis Techniques
- Industrial Hygiene Principles (e.g., chemical exposure, noise, air quality monitoring)
- Personal Protective Equipment (PPE) Selection and Usage Guidelines
- Safety Management Systems (e.g., ANSI/ASSP Z10, ISO 45001)
- Emergency Preparedness and Response Planning
- Environmental Regulations (e.g., EPA, waste management principles relevant to workplace safety)
- Ergonomics Assessment and Control Measures
- Data Collection and Analysis Tools (e.g., spreadsheets, safety software for trend analysis)
- Confined Space Entry and Permit-Required Confined Spaces
- Fall Protection Systems and Standards
Soft Skills
- Observational Acuity: Inspectors must possess a keen eye for detail to identify subtle hazards, non-compliance, and potential risks in complex environments.
- Investigative Skills: Essential for gathering evidence, interviewing workers and management, and reconstructing incidents to determine root causes of accidents.
- Ethical Conduct: Inspectors must maintain impartiality and integrity when assessing compliance and enforcing regulations, ensuring fairness and objectivity.
- Communication and Interpersonal Skills: Critical for effectively conveying complex safety regulations, explaining findings to diverse audiences, and fostering cooperation during inspections.
- Problem-Solving and Analytical Thinking: Necessary for evaluating hazardous situations, developing practical solutions, and interpreting complex regulatory standards.
- Adaptability and Resilience: Inspectors often encounter challenging or resistant individuals, requiring them to remain composed and adjust their approach in varied and sometimes confrontational situations.
- Report Writing and Documentation: Vital for preparing clear, concise, and legally defensible reports on findings, violations, and recommended corrective actions.
- Negotiation and Persuasion: Important when discussing compliance issues and corrective actions with businesses, helping them understand the benefits of safety and agree to necessary changes without immediate punitive measures, fostering a collaborative approach to safety improvements.
How to Become an Occupational Safety and Health Inspector
Becoming an Occupational Safety and Health Inspector involves navigating various pathways, from formal education to practical experience. A bachelor's degree in occupational health and safety, environmental health, or a related scientific or engineering field is often preferred, but some roles may accept a combination of relevant experience and certifications. The timeline for entry can range from 1-2 years for those with a suitable degree and internship experience to 3-5 years for individuals transitioning from unrelated fields who need to build foundational knowledge and practical skills.
Entry strategies vary significantly by employer. Government agencies, such as OSHA, often require specific educational backgrounds and may have structured hiring processes including written exams and interviews. Private companies, consultants, or insurance firms might prioritize certifications like CSP (Certified Safety Professional) or ASP (Associate Safety Professional) alongside practical experience. Geographic location also plays a role; major industrial hubs or states with strong safety regulations may have more opportunities than rural areas.
A common misconception is that this role is purely about enforcement; it also heavily involves education, consultation, and risk assessment. Building a strong network within professional safety organizations, seeking mentorship, and demonstrating a genuine commitment to workplace safety are crucial for overcoming barriers to entry. The hiring landscape values practical problem-solving skills, regulatory knowledge, and the ability to communicate complex safety concepts effectively across all levels of an organization.
Step 1
Step 2
Step 3
Step 4
Step 5
Step 6
Education & Training Needed to Become an Occupational Safety and Health Inspector
Becoming an Occupational Safety and Health Inspector requires a blend of formal education and practical knowledge. While a four-year bachelor's degree in occupational safety and health, industrial hygiene, or a related science field is often preferred, some positions may accept candidates with an associate's degree combined with significant relevant experience. Bachelor's degrees typically cost $40,000-$100,000+ and take four years to complete, providing a strong theoretical foundation in safety regulations, hazard identification, and risk management. Shorter, specialized certificate programs or professional certifications, ranging from $2,000-$10,000 and taking 6-18 months, can supplement a technical background or serve as continuing education.
Employers, particularly government agencies like OSHA, value formal degrees for their comprehensive curriculum. However, certifications from organizations like the Board of Certified Safety Professionals (BCSP) or the American Board of Industrial Hygiene (ABIH) are highly regarded and often required for career advancement. These certifications demonstrate a commitment to professional standards and validate specialized expertise. Continuous learning is essential in this field due to evolving regulations and new technologies; inspectors must regularly update their knowledge through workshops, seminars, and advanced courses. The specific educational needs vary, with entry-level roles sometimes accepting less formal education if candidates possess extensive practical experience in a high-risk industry.
Practical experience, often gained through internships or prior roles in industrial settings, is crucial for success as an inspector, complementing theoretical knowledge. The market perceives formal degrees as a solid baseline, while certifications signify advanced competency. The cost-benefit analysis favors a degree for long-term career growth and higher earning potential, with certifications providing a cost-effective way to enhance credentials. Quality programs often hold accreditation from ABET or similar bodies, ensuring rigorous academic standards. Online learning platforms offer flexibility, allowing working professionals to pursue certifications or degrees part-time, typically over longer timeframes than full-time, in-person programs.
Occupational Safety and Health Inspector Salary & Outlook
Compensation for an Occupational Safety and Health Inspector varies significantly based on several factors. Geographic location plays a major role; areas with higher costs of living or strong industrial sectors often offer higher salaries. For instance, inspectors in metropolitan areas or states with extensive manufacturing and construction activity typically earn more than those in rural regions. Salary figures provided here are primarily for the United States, acknowledging that international markets will have different compensation structures influenced by local regulations and economic conditions.
Years of experience, specialized certifications (e.g., CSP, CIH), and the specific industry of employment also drive salary differences. Inspectors working in high-risk sectors like oil and gas, mining, or large-scale construction often command premium compensation due to the inherent complexities and liabilities. Total compensation packages extend beyond base salary to include performance bonuses, robust health and retirement benefits, and professional development allowances. Some government positions may offer defined benefit pension plans, adding significant long-term value.
Negotiating salary effectively requires understanding your value proposition, including unique skill sets in areas like industrial hygiene, ergonomics, or specific regulatory expertise. Remote work opportunities are less common for this role due to the hands-on inspection nature, but some consulting or management positions may offer more flexibility. Industry-specific trends, such as increased regulatory scrutiny in certain sectors, can also drive salary growth and demand for skilled inspectors.
Salary by Experience Level
Level | US Median | US Average |
---|---|---|
Junior Occupational Safety and Health Inspector | $60k USD | $65k USD |
Occupational Safety and Health Inspector | $75k USD | $78k USD |
Senior Occupational Safety and Health Inspector | $90k USD | $95k USD |
Lead Occupational Safety and Health Inspector | $105k USD | $110k USD |
Occupational Safety and Health Manager | $120k USD | $125k USD |
Director of Occupational Safety and Health | $148k USD | $155k USD |
Market Commentary
The job market for Occupational Safety and Health Inspectors shows steady demand, driven by ongoing regulatory compliance needs and a heightened focus on workplace safety across industries. The Bureau of Labor Statistics projects a growth of 5% for occupational health and safety specialists and technicians from 2022 to 2032, which is about as fast as the average for all occupations. This translates to approximately 2,900 new jobs over the decade, reflecting a stable, rather than rapidly expanding, market.
Demand is particularly strong in sectors with inherent safety risks, such as manufacturing, construction, healthcare, and government agencies. Emerging opportunities include specialization in areas like environmental health and safety (EHS) integration, process safety management, and the safety implications of new technologies like automation and robotics. There is a consistent need for qualified professionals to ensure adherence to OSHA standards and prevent workplace incidents, creating a relatively recession-resistant career path.
The supply of qualified candidates generally matches demand, though specialized roles or those in specific geographic hotspots (e.g., Texas, California, Pennsylvania due to industrial presence) might see more competition or higher demand. Future-proofing this career involves continuous learning in evolving regulations, new hazard identification techniques, and the integration of data analytics for proactive safety management. While automation may assist with data collection, the critical judgment and on-site presence of human inspectors remain indispensable.
Occupational Safety and Health Inspector Career Path
Career progression for an Occupational Safety and Health Inspector involves a clear path from entry-level compliance checks to strategic leadership in safety management. Professionals typically advance through a combination of on-the-job experience, continuous learning, and demonstrating a deep understanding of regulatory frameworks.
Advancement can follow individual contributor (IC) tracks, where inspectors become highly specialized experts, or management tracks, which involve leading teams and developing safety programs. Factors influencing advancement speed include performance, the complexity of industries inspected, and the ability to influence organizational safety culture. Specialization in areas like construction safety, hazardous materials, or ergonomics can also accelerate progression.
Networking within professional organizations, obtaining relevant certifications (e.g., CSP, CIH), and mentorship are crucial for navigating career opportunities. Lateral moves might involve transitioning to corporate safety roles or consulting. Career paths vary significantly between government agencies, private corporations, and consulting firms, each offering different scopes of work and advancement opportunities. Understanding these distinctions helps professionals tailor their development and achieve specific career goals.
Junior Occupational Safety and Health Inspector
0-2 yearsKey Focus Areas
Occupational Safety and Health Inspector
2-5 yearsKey Focus Areas
Senior Occupational Safety and Health Inspector
5-8 yearsKey Focus Areas
Lead Occupational Safety and Health Inspector
8-12 yearsKey Focus Areas
Occupational Safety and Health Manager
12-18 yearsKey Focus Areas
Director of Occupational Safety and Health
18+ yearsKey Focus Areas
Junior Occupational Safety and Health Inspector
0-2 yearsConduct routine safety inspections under direct supervision, focusing on compliance with basic safety standards. Document findings, assist in incident investigations, and support senior inspectors. Interact with site personnel to gather information and observe work practices. This stage involves learning the practical application of safety regulations.
Key Focus Areas
Develop a strong understanding of OSHA regulations and inspection protocols. Learn to identify common workplace hazards and proper documentation techniques. Focus on effective communication and interviewing skills for site personnel. Begin building foundational knowledge in various industrial processes and safety controls.
Occupational Safety and Health Inspector
2-5 yearsPerform independent safety inspections, identify complex hazards, and assess compliance across various industries. Conduct thorough incident investigations, issue citations, and propose corrective actions. Educate employers and employees on safety best practices and regulatory requirements. This role requires significant autonomy and judgment.
Key Focus Areas
Master a wide range of OSHA regulations and industry-specific safety standards. Enhance hazard recognition, risk assessment, and root cause analysis skills. Improve report writing, evidence collection, and enforcement procedures. Cultivate independent decision-making and problem-solving abilities.
Senior Occupational Safety and Health Inspector
5-8 yearsLead and manage complex safety investigations and compliance audits. Provide technical expertise and guidance to other inspectors on challenging cases. Review and approve inspection reports and enforcement actions. Act as a subject matter expert for specific regulatory areas or industry sectors. This role involves more strategic input.
Key Focus Areas
Develop expertise in specialized areas such as industrial hygiene, construction safety, or process safety management. Lead complex investigations and provide technical guidance to junior inspectors. Enhance negotiation and conflict resolution skills for enforcement actions. Focus on presenting findings and recommendations to diverse stakeholders.
Lead Occupational Safety and Health Inspector
8-12 yearsOversee a team of inspectors, assigning cases, reviewing work, and ensuring quality control. Develop and implement regional inspection plans and enforcement strategies. Serve as a primary point of contact for complex regulatory interpretations and appeals. Provide training and professional development to inspection staff.
Key Focus Areas
Cultivate strong leadership, mentoring, and team coordination skills. Develop programmatic oversight capabilities for inspection cycles and enforcement priorities. Enhance strategic planning and resource allocation skills. Focus on inter-agency collaboration and stakeholder engagement to improve safety outcomes.
Occupational Safety and Health Manager
12-18 yearsManage an occupational safety and health department or a significant safety program within a large organization or agency. Responsible for developing, implementing, and overseeing all safety policies, procedures, and training. Lead a team of safety professionals and ensure compliance across multiple sites or jurisdictions. This role carries significant managerial responsibility.
Key Focus Areas
Develop comprehensive safety management systems and organizational safety policies. Master budget management, performance metrics, and data analysis for safety programs. Enhance leadership, communication, and change management skills. Focus on influencing organizational culture and executive-level decision-making.
Director of Occupational Safety and Health
18+ yearsProvide executive leadership for all occupational safety and health initiatives across an entire organization or governmental department. Establish strategic direction, set overarching safety goals, and ensure regulatory compliance at the highest level. Influence corporate culture and allocate resources to achieve world-class safety performance. This role involves significant strategic and executive oversight.
Key Focus Areas
Focus on enterprise-wide risk management strategies and long-term safety vision. Develop expertise in corporate governance, legal compliance, and sustainability reporting related to safety. Cultivate executive presence, strategic partnerships, and crisis management capabilities. Drive continuous improvement in safety performance at a global or national level.
Job Application Toolkit
Ace your application with our purpose-built resources:
Occupational Safety and Health Inspector Resume Examples
Proven layouts and keywords hiring managers scan for.
View examplesOccupational Safety and Health Inspector Cover Letter Examples
Personalizable templates that showcase your impact.
View examplesTop Occupational Safety and Health Inspector Interview Questions
Practice with the questions asked most often.
View examplesOccupational Safety and Health Inspector Job Description Template
Ready-to-use JD for recruiters and hiring teams.
View examplesGlobal Occupational Safety and Health Inspector Opportunities
Occupational Safety and Health Inspectors ensure workplace compliance with safety regulations globally. This role translates well across countries, focusing on hazard identification and risk mitigation. Global demand for skilled inspectors remains strong as industries prioritize worker well-being and regulatory adherence. International job market trends for 2025 show consistent growth, driven by evolving safety standards and increased corporate accountability. Cultural differences impact safety practices, while regulatory frameworks vary significantly by region. Professionals seek international roles for diverse experiences and exposure to advanced safety methodologies. Certifications like NEBOSH or CSP enhance global mobility.
Global Salaries
Occupational Safety and Health Inspector salaries vary significantly by region and economic development. In North America, particularly the United States, an inspector can expect to earn between $65,000 and $95,000 USD annually. Canadian salaries are comparable, ranging from $60,000 to $90,000 CAD ($45,000-$68,000 USD). These figures often include comprehensive benefits packages, such as health insurance and retirement plans, which are standard.
Europe shows a wide range. In Western European countries like Germany or the UK, salaries typically fall between €45,000 and €70,000 ($48,000-$75,000 USD). Scandinavian countries may offer higher take-home pay due to robust social welfare systems, despite higher tax rates. Southern and Eastern European nations generally present lower salary figures but also a reduced cost of living, balancing purchasing power.
Asia-Pacific markets, such as Australia and Singapore, offer competitive salaries, often between $70,000 and $100,000 AUD ($46,000-$66,000 USD) or $60,000 to $85,000 SGD ($44,000-$63,000 USD) respectively, reflecting high living costs. In contrast, emerging markets like India or Malaysia might offer $15,000 to $30,000 USD, though purchasing power in local currency can be substantial. Tax implications and social security contributions differ greatly by country, impacting net income. International experience and specialized certifications, like ISO lead auditor credentials, can significantly increase compensation globally.
Remote Work
True remote work for Occupational Safety and Health Inspectors is limited due to the inherent need for on-site inspections. However, some aspects of the role, such as documentation, report writing, policy development, and virtual training, can be performed remotely. Industry trends indicate a hybrid model becoming more common, blending field visits with office-based remote tasks.
Legal and tax implications for cross-border remote work are complex, requiring adherence to both the employer's country and the employee's residence country regulations. Time zone differences can pose collaboration challenges for international teams. Digital nomad opportunities are minimal for this role, as physical presence is frequently mandatory for core duties. Employers hiring internationally for this position often prefer a local presence or a structured fly-in, fly-out arrangement.
Remote work typically does not impact salary expectations for this role, as the essential on-site component dictates compensation. Companies usually provide necessary equipment. Reliable internet is crucial for any remote components. Dedicated workspace setup is also important, even for partial remote work.
Visa & Immigration
Occupational Safety and Health Inspectors typically qualify for skilled worker visas in many countries. Popular destinations like Canada, Australia, the UK, and Germany have specific visa categories for professionals in high-demand fields. Requirements often include a relevant degree, several years of experience, and sometimes a job offer. Credential recognition is crucial; professional bodies in destination countries may require assessments or local certifications.
Visa application processes vary but generally involve online applications, document submission, and biometric appointments. Timelines can range from a few months to over a year. Some countries, like Australia, offer points-based immigration systems where OSH qualifications and experience contribute significantly. Language proficiency tests, such as IELTS or TOEFL for English-speaking countries, are often mandatory.
Pathways to permanent residency or citizenship exist through continuous skilled employment. For example, Canada's Express Entry system or Australia's skilled migration programs favor this profession. Intra-company transfers are also possible for inspectors working for multinational corporations. Family visas are available for dependents, subject to specific country regulations and the primary applicant's visa type.
2025 Market Reality for Occupational Safety and Health Inspectors
Understanding current market realities is crucial for aspiring and existing Occupational Safety and Health Inspectors. The field, while stable, has seen shifts post-pandemic, with increased emphasis on infectious disease control and mental health in the workplace, alongside the burgeoning impact of AI on industrial processes.
Broader economic factors, such as supply chain shifts and manufacturing reshoring, directly influence the types and locations of workplaces requiring inspection. Market conditions vary significantly by experience level, with senior inspectors often finding more specialized opportunities, while entry-level roles may face regional competition. This analysis provides an honest assessment of current hiring conditions.
Current Challenges
Occupational Safety and Health Inspectors face rising competition, particularly for entry-level roles, as the field attracts more candidates seeking stable government work. Economic uncertainties sometimes lead to budget constraints, impacting the number of available inspection positions. Staying current with rapidly evolving industrial processes and new safety technologies also presents an ongoing challenge for effective oversight.
Growth Opportunities
Despite challenges, strong opportunities exist for Occupational Safety and Health Inspectors specializing in emerging technologies and complex industrial environments. Demand is high for inspectors with expertise in robotics safety, cybersecurity for operational technology, and environmental health within smart factories. These specialized areas are underserved and offer competitive advantages.
Professionals can position themselves by acquiring certifications in advanced safety systems, process hazard analysis, or specific industry regulations like those for renewable energy facilities. Underserved markets include rapidly expanding logistics centers, advanced manufacturing plants, and sectors integrating significant automation where novel safety protocols are required. Market corrections can also create opportunities as companies invest more in compliance to avoid costly incidents during economic downturns. Focusing on continuous learning in AI-driven safety solutions and data analytics provides a significant competitive edge.
Current Market Trends
The market for Occupational Safety and Health Inspectors in 2025 shows steady demand, driven by ongoing regulatory enforcement and a renewed focus on workplace well-being. Hiring patterns remain consistent across federal, state, and local government agencies, with a notable increase in private sector consulting roles as companies proactively seek compliance and risk mitigation. Industry changes, particularly the integration of automation and AI into manufacturing and logistics, are reshaping the types of hazards inspectors encounter, requiring new expertise in robotic safety and data-driven risk assessment.
Economic conditions continue to support this field, as safety compliance remains non-negotiable regardless of market fluctuations. Layoffs in other sectors have not significantly impacted OSH inspector roles, given their essential regulatory function. Employer requirements now emphasize strong analytical skills, proficiency with data management software for record analysis, and a foundational understanding of emerging technologies like IoT sensors for environmental monitoring.
Salary trends for experienced inspectors show modest growth, while entry-level salaries remain competitive but stable. Market saturation is low for highly specialized inspectors in niche areas like chemical safety or construction, but generalist roles see more applicants. Geographic variations exist, with higher demand in industrial hubs and areas with new infrastructure projects, while remote work is generally not applicable given the hands-on nature of inspections.
Emerging Specializations
The field of occupational safety and health is undergoing significant transformation, driven by rapid technological advancements, evolving regulatory landscapes, and a heightened focus on holistic employee well-being. These shifts are creating entirely new specialization opportunities for Occupational Safety and Health Inspectors. Understanding these emerging areas allows professionals to strategically position themselves for the next generation of career paths.
Early positioning in these cutting-edge fields can provide a substantial advantage, often leading to premium compensation and accelerated career growth from 2025 onwards. While established specializations remain vital, exploring emerging niches ensures relevance and expanded impact. The timeline for these emerging areas to become mainstream varies, but many are already showing significant momentum, indicating a strong potential for job opportunities in the near future.
Pursuing a specialization in an emerging area involves balancing risk and reward. While it offers the chance to be at the forefront of the profession, it also requires continuous learning and adaptability. However, the potential for significant professional development and influence within the industry often outweighs these considerations, making it a compelling strategic choice for forward-thinking inspectors.
Advanced Automation & Robotics Safety Inspector
The integration of advanced robotics, automation, and AI into industrial and commercial settings introduces novel safety challenges. Inspectors specializing in this area focus on assessing risks associated with human-robot interaction, autonomous vehicle operations in workplaces, and AI-driven predictive maintenance systems that impact safety protocols. This specialization ensures that new technologies are deployed safely, preventing unforeseen hazards.
Environmental & Sustainability Safety Inspector
With increasing environmental concerns and stricter sustainability regulations, workplaces must manage their environmental impact more diligently. This specialization involves inspecting sites for compliance with environmental safety standards, assessing hazardous waste management, ensuring sustainable resource use, and evaluating the occupational health impacts of 'green' technologies and processes. It bridges traditional safety with ecological responsibility.
Remote Work & Gig Economy Safety Compliance Officer
The rise of remote work and the gig economy has blurred traditional workplace boundaries, creating new safety and health considerations. This specialization focuses on developing and inspecting safety protocols for distributed workforces, evaluating ergonomic setups in home offices, addressing psychosocial risks of isolation, and ensuring mental well-being support for non-traditional employees. It adapts safety principles to modern work models.
Cyber-Physical Systems Safety Auditor
As cyber-physical systems become more prevalent, the intersection of cybersecurity and operational safety is critical. This specialization involves assessing the safety implications of cybersecurity vulnerabilities in industrial control systems (ICS), IoT devices, and smart machinery. Inspectors ensure that digital security measures protect physical processes from malicious attacks or system failures that could lead to accidents or health hazards.
Global Supply Chain Safety Specialist
The increasing complexity of global supply chains introduces unique safety risks, from raw material sourcing to final product delivery. This specialization focuses on inspecting and ensuring safety compliance across international logistics, transportation of hazardous materials, and the safety conditions of outsourced manufacturing facilities. It requires understanding diverse regulatory frameworks and cultural safety practices.
Pros & Cons of Being an Occupational Safety and Health Inspector
Making an informed career decision requires understanding both the appealing aspects and the genuine difficulties of a profession. The experience of an Occupational Safety and Health Inspector can vary significantly based on the specific agency, the industries inspected, and the inspector's individual personality and approach. Pros and cons may also shift at different career stages; for example, the initial learning curve is a challenge, while later, the accumulated expertise becomes a significant advantage. What one person views as a benefit, such as independent work, another might see as a drawback, like limited team interaction. This assessment aims to provide a realistic overview to help set appropriate expectations for this vital role.
Pros
- Occupational Safety and Health Inspectors play a crucial role in protecting workers and the public, providing a strong sense of purpose and direct positive impact on safety and well-being.
- The role offers significant autonomy and independence, as inspectors often manage their own schedules and conduct investigations with minimal direct supervision once assigned.
- The work provides constant intellectual stimulation, requiring inspectors to analyze complex situations, apply regulations to diverse environments, and solve unique safety challenges.
- Occupational Safety and Health Inspectors typically receive comprehensive training from their agencies, covering a wide range of safety standards, investigative techniques, and legal procedures.
- The position generally offers stable employment with competitive government benefits, including good health insurance, retirement plans, and predictable work hours in many cases.
- Inspectors gain a broad understanding of various industries and processes, visiting diverse workplaces from manufacturing plants to construction sites, which offers continuous learning and prevents monotony.
- The job involves a mix of fieldwork and office work, providing a dynamic routine that balances on-site investigations with report writing, research, and communication with stakeholders.
Cons
- Occupational Safety and Health Inspectors often encounter resistance from employers or workers during inspections, which can make investigations difficult and sometimes confrontational.
- The job involves frequent travel to various worksites, often in different environments, which can be physically demanding and lead to long hours away from home.
- Inspectors must stay continuously updated on complex and evolving safety regulations and standards, requiring ongoing training and diligent study to maintain expertise.
- Investigating accidents or fatalities can be emotionally challenging, as inspectors frequently witness the aftermath of serious incidents and deal with affected individuals.
- There can be a perception of being an antagonist rather than a partner in safety, which can strain relationships with the businesses and people they regulate.
- The work environment can sometimes be hazardous, as inspectors enter sites with potential risks like chemical exposure, heights, or heavy machinery to identify safety violations.
- Career progression within governmental safety agencies can be slow, with fewer opportunities for rapid advancement compared to some private sector roles, often requiring many years of service to move up significantly in rank or responsibility levels, which can be frustrating for ambitious individuals looking for quicker career growth opportunities, especially early in their careers when they are eager to take on more leadership or specialized roles quickly, leading to a sense of stagnation if they are not prepared for a more gradual climb through the ranks within the public sector framework, where promotions are often tied to seniority and specific openings rather than rapid individual performance, making it essential for prospective inspectors to understand this slower trajectory when considering their long-term career aspirations within this field, as it differs considerably from the faster advancement paths sometimes seen in private industry, where performance and project success can lead to quicker promotions and increased responsibilities.
Frequently Asked Questions
What are the educational and certification requirements to become an Occupational Safety and Health Inspector?
Becoming an Occupational Safety and Health Inspector typically requires a bachelor's degree in occupational safety and health, environmental health, or a related scientific or engineering field. Some positions may accept extensive relevant experience in lieu of a degree, particularly if coupled with professional certifications. Strong knowledge of OSHA regulations and workplace safety standards is essential, often gained through coursework or prior safety roles.
How long does it typically take to become an Occupational Safety and Health Inspector?
The timeline to become job-ready can vary. If you are starting from a bachelor's degree, you might find an entry-level position within 6-12 months of graduation. If you need to complete a degree or gain significant experience, it could take 2-4 years. Gaining relevant experience in a safety-related role, even as a safety technician, often accelerates the process and makes you more competitive for inspector roles.
What are the typical salary expectations for an Occupational Safety and Health Inspector?
Salary expectations for Occupational Safety and Health Inspectors vary significantly based on location, employer (federal, state, or private sector), and experience. Entry-level federal positions might start around $40,000-$50,000 annually, while experienced inspectors can earn $70,000-$90,000 or more. State and local government salaries might be slightly lower, but they often come with stable benefits packages.
What is the typical work-life balance for an Occupational Safety and Health Inspector?
Occupational Safety and Health Inspectors often balance fieldwork with office-based tasks. Your work-life balance depends on your specific agency and caseload. You will conduct site visits during regular business hours, but sometimes investigations or critical incidents may require extended hours. The role often involves travel within a designated territory, which can impact personal time. Overall, it is generally a stable 40-hour work week, but flexibility is sometimes needed.
What is the job security and market demand for Occupational Safety and Health Inspectors?
The job market for Occupational Safety and Health Inspectors is stable, driven by ongoing regulatory needs and the continuous focus on workplace safety. Demand remains consistent as companies must comply with federal and state safety standards, and new industries or technologies often introduce new hazards requiring inspection. This career offers good job security because safety compliance is not optional for businesses.
What are the typical career growth opportunities for an Occupational Safety and Health Inspector?
Career growth for Occupational Safety and Health Inspectors can involve specializing in particular industries (e.g., construction, manufacturing, healthcare), becoming a senior inspector, or moving into supervisory or management roles within a safety agency. You can also transition into private sector roles as a safety consultant, safety manager, or compliance officer. Continuous professional development and additional certifications enhance advancement opportunities.
Can Occupational Safety and Health Inspectors work remotely?
This role primarily involves on-site inspections and investigations, meaning it is not typically a remote position. You will spend a significant amount of time traveling to various workplaces to assess compliance and investigate incidents. While some administrative tasks might be performed remotely, the core duties require a physical presence. The ability to travel and work in diverse environments is a key requirement for this job.
What are the biggest challenges Occupational Safety and Health Inspectors face in their daily work?
The main challenges involve dealing with non-compliant businesses, potentially hazardous environments, and sometimes adversarial interactions with employers or employees. You need strong communication skills to explain regulations, enforce compliance, and gather information effectively. The role also requires meticulous documentation and the ability to remain objective and professional under pressure. You must stay updated on evolving safety standards and technologies.
Related Careers
Explore similar roles that might align with your interests and skills:
Safety Inspector
A growing field with similar skill requirements and career progression opportunities.
Explore career guideSafety Officer
A growing field with similar skill requirements and career progression opportunities.
Explore career guideHealth and Safety Inspector
A growing field with similar skill requirements and career progression opportunities.
Explore career guideIndustrial Safety and Health Specialist
A growing field with similar skill requirements and career progression opportunities.
Explore career guideOccupational Health and Safety Technologist
A growing field with similar skill requirements and career progression opportunities.
Explore career guideAssess your Occupational Safety and Health Inspector readiness
Understanding where you stand today is the first step toward your career goals. Our Career Coach helps identify skill gaps and create personalized plans.
Skills Gap Analysis
Get a detailed assessment of your current skills versus Occupational Safety and Health Inspector requirements. Our AI Career Coach identifies specific areas for improvement with personalized recommendations.
See your skills gapCareer Readiness Assessment
Evaluate your overall readiness for Occupational Safety and Health Inspector roles with our AI Career Coach. Receive personalized recommendations for education, projects, and experience to boost your competitiveness.
Assess your readinessSimple pricing, powerful features
Upgrade to Himalayas Plus and turbocharge your job search.
Himalayas
Himalayas Plus
Himalayas Max
Find your dream job
Sign up now and join over 100,000 remote workers who receive personalized job alerts, curated job matches, and more for free!
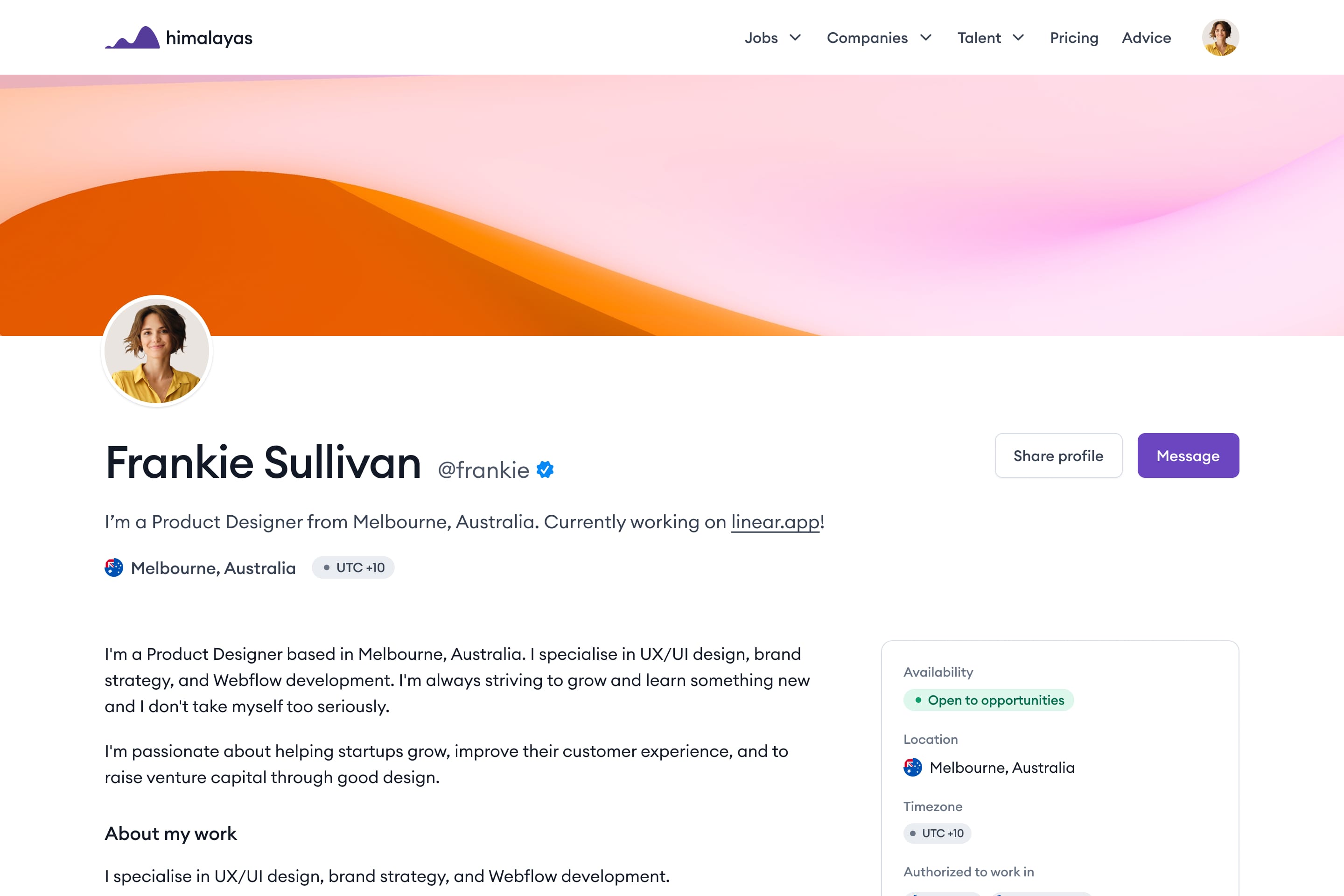